氰化提金工艺实践与设计探讨
全泥氰化提金工艺设计与实践

灵 湖 金矿 5td炭浆 提 金厂 投 人运 行 . 小 型炭 浆 厂 0/ 为 的设 计 和工 艺 生 产 提 供 了建 设 模 式 。 18 93年 。 家 张
口金 矿 、 陕西 西 潼 峪 金 矿 引进 全 泥 氰 化 C L工 艺 之 I
后 , 全 泥氰化 炭浆 工 艺和 规模 大 型化提 高 到一个 新 将 的水 平 。从此 以后 . 泥氰 化工 艺在 我 国黄 金选矿 厂 全
幅度 。
的经 济效 益 ; 符合 在 矿 山 的 开发 建 设 中 “ 开发 中保 在
护 , 保护中开发” 在 的原 则 . 践 环 境 、 源 、 益 协 实 资 效 调发 展 。在选 择 确定 全 泥 氰 化 工 艺 流 程设 计 中应 认
度试 验时 . 采用 的矿 浆浓 度应 与工 业生 产时 矿浆 浓度
工艺 过程 检测 控 制等方 面 也存 在着 不足 。
在设 计选 用 全泥 氰化 提金 工艺 中 . 原则 流程 的确 定是 工 艺设计 的 重要 环节 . 是选 矿 工艺设 计 成败 的关
相接 近 。例如 : 细度磨 矿 . 计 采用 旋流 器分 级 . 高 设 当
溢流 细 度 小 于 2 0 目含 量 为 9 % ~9 % 时 . 流 浓 0 0 5 溢
键 。工艺 流程 成 功 的设 计 标志 : 确定 的流程 符合 近期
矿石 特性 . 设计 的原 则 流程有 较 长时 间 的生产 稳定 使 性, 避免 选厂 投产 后 不 久 就 进 行 流程 改 造 : 设计 工 艺 流程 能够 充分 利 用矿 产资 源 . 并能 够使 企业 获得 最大
维普资讯
黄 金 GoL D
20 0 6年第 6期/ 2 第 7卷
试论氰化法提金工艺及其在我国的应用

试论氰化法提金工艺及其在我国的应用前言我国黄金资源储量丰富,分布较广,黄金冶炼方法很多。
其中包括常规的冶炼方法和新技术。
冶炼方法的改进,促进了我国黄金工业的发展。
目前我国黄金产量居世界第五位,成为产金大国之一,我国的某些冶炼黄金的技术还达到了世界先进水平。
氰化法在上世纪初就已应用于提金工艺,因其回收率高,工艺简单,单位成本低等优点,迅速普及世界各地金矿山,使人类提金技术进入新的开创阶段。
该阶段的特点是:从采矿砂金为主转变到以采脉金为主,扩大了黄金资源,拉动了内需与国际市场,黄金生产量迅速增加。
据保守估计除砂金外,人类产金的90%是在氰化法工艺中产出。
据统计国内的191个规模较大的选金厂中就有161个在使用着氰化提金工艺,实践证明:氰化法提金取得了较好经济效益。
一、氰化法提金的特点氰化提金最大特点——回收率很高,产金多,单位成本势必降低,可以实现就地产金,避免了金矿石长途运输的各种弊病,有利于提高企业的经济效益,降低成本。
但不容回避,此工艺方法也存在氰化物为剧毒药剂,工艺流程长,金的提取速度较慢,环境污染等缺点,需不断完善。
相比较而言:重洗法和混汞法都是古老的提金方法,它们仅适于从矿石中提取粗粒金,但是大多数矿石除了有粗粒金外,还有大量的细粒金。
那么从这些矿石中提取金必须借助于湿法冶金。
氰化法属于湿法冶金工艺,是一种现代化的从含金的矿石中提金的技术,从矿石中用湿法提金,主要包括两个步骤:(1)浸出——用溶剂使矿石中的金转入溶液。
(2)沉积——再从浸入液中提取金。
即从碱金属氰化物(KCN NaCH)水溶液作溶剂,浸出矿石中的金,然后从浸出液中沉积出金的工艺过程。
二、氰化法提金的原理及影响因素氰化物对金溶解作用机量的解释目前尚不一致,多数认为金在氰化溶液中有氧存在的情况下可以生成一种金的络合物而注解。
其基本反应式为:4Au+8KCN +O2+2H2O = 4KAu(CN)2 +4KOH一般认为金被氰化物溶解发生两步反应:2Au+4KCN + O2+2 H2O = 2Au(CN)2 + H2O +2KOH2Au +4KCN +H2O2 = 2KAu(CN)2 +2KOH金的表面在氰化溶液中逐渐地由表及里地溶解。
氰化法提金工艺讲解

氰化物溶液中的过程。 ②洗涤——为回收浸出后的含金溶液,
用水洗涤矿粒表面以及矿粒之间的已溶金, 以实现固液分离的过程。
③置换——用金属锌从含金溶液中使其 还原、沉淀,回收金的过程。
工艺分类
• 我国黄金矿山现有氰化厂基本采用两类提金工艺 流程,一类是以浓密机进行连续逆流洗涤,用锌 粉置换沉淀回收金的所谓常规氰化法提金工艺流 程(CCD法和CCF法);另一类则是无须过滤洗 涤,采用活性炭直接从氰化矿浆中吸附回收金的 无过滤氰化炭浆工艺流程(CIP法和CIL法)。
建厂投产,足以说明我国提金技术已发展到一个 新的水平。
氰化法提金的基本原理
• 氰化法提金是从金矿石中提取金的主要方 法之一。氰化物对金溶解作用机理的解释 目前尚不一致,多数认为金在氰化溶中有 氧存在的情况下可以生成一种金的络合而H2O=2NaAu(CN)2+2NaOH
• 黄金生产的不断发展和金矿资源的迅速开发,自20世纪80 年代起泥质高的含金氧化矿石大量增加,开发对这类矿石 进行全泥氰化搅拌浸出的研究,并在黑龙江团结沟金矿建 设一座日处理500t矿石的氰化厂,1983年投入生产。从此, 全泥氰化法提金工艺日渐推广应用,先后在河南、吉林、 河北、陕西、内蒙古等地采用此法建厂提金。与此同时, 为解决泥质氧化矿石在浓密过滤固液分离上的困难,于 1979年11月长春黄金研究所开始对团结沟金矿的矿石采 用无过滤的炭浆法提金工艺,进行了历时两年的试验研究, 获得了成功。在此基础上,于1984年8月在河南灵湖金矿 自行设计利用国产设备建成我国第一座日处理50t矿石的 炭浆法提金厂。使我国氰化法提金工艺向前迈进了一大步。 炭浆法提金工艺成为处理泥质氧化矿石的岩金矿山就地产 金的重要方法之一。此后在吉林、河南、内蒙古、陕西等 地建起了炭浆法提金厂。1984年末,冶金工业部黄金局为 推动炭浆法提金工艺在我国的应用,移植消化国外先进技 术和设备,与美国戴维麦基公司合作,在陕西省西潼峪金 矿、河北省张家口金矿,分别建起了一座日处理矿石250t (西潼峪)和一座450t(张家口)的炭浸提金厂。据调查 张家口金矿达到93.54%(1988年炭浆回收率为90.25%) 的回收率。
陕西某黄金冶炼厂焙烧氰化浸渣提金方法研究报告

陕西某黄金冶炼厂焙烧氰化浸渣提金方法研究报告本文研究了陕西某黄金冶炼厂焙烧氰化浸渣提金方法,分析了该方法的优缺点,并从工艺流程、操作技术、设备应用等方面对该方法进行了详细阐述。
一、工艺流程本研究采用的焙烧氰化浸渣提金方法主要由以下几个步骤组成:1. 氰化浸渣焙烧:将氰化浸渣送入焙炉中进行高温处理,使其得到充分焙烧,达到剥离金属的效果。
2. 氰化浸渣破碎:将焙烧后的氰化浸渣进行破碎,得到较小的颗粒状物料。
3. 搅拌:将破碎后的氰化浸渣与水一起搅拌,使其形成悬浮液。
4. 沉淀:将悬浮液静置一段时间,使其沉淀,得到含金泥浆。
5. 过滤:将含金泥浆进行过滤,去除杂质。
6. 洗涤:将过滤后的含金泥浆用水进行洗涤,使其去除残留杂质。
7. 烘干:将洗涤后的含金泥浆放入焙炉中进行烘干,得到金粉末。
二、操作技术1. 焙烧操作温度的选择:在本研究中,焙烧时采用了950℃的高温,能够使氰化浸渣得到充分焙烧,并且可以保证金属与其他杂质迅速分解。
2. 破碎操作:在氰化浸渣破碎时,应采用适当的粉碎机,能够将氰化浸渣破碎成较小的颗粒状物料。
3. 悬浮液搅拌操作:搅拌时间和强度应根据浸出效果进行调整。
4. 沉淀时间的选择:沉淀时间应根据泥浆中悬浮颗粒的大小、颗粒浓度等因素进行调整。
5. 过滤操作:过滤应选用细孔滤纸,过滤时应逐渐加压。
三、设备应用本研究采用了较新的设备,包括高温焙炉、永磁搅拌器、温度控制系统等。
这些设备的应用,不仅能够提高提金效率,而且能够保证产品质量。
四、优缺点分析本研究采用的焙烧氰化浸渣提金方法具有以下优点:1. 提金效率高:在保证产品质量的前提下,可以达到较高的提金效率。
2. 工艺流程简单:焙烧氰化浸渣提金方法的工艺流程相对简单,易于操作。
3. 环保性好:焙烧氰化浸渣提金方法的环保性好,能够减少对环境的影响。
但该方法也存在一些缺点,主要包括:1. 能源消耗大:焙烧氰化浸渣需要较高的温度,因此消耗的能源较大。
含金钼精矿氰化提金工艺试验与生产实践

图 2 浸金工艺流程
总第 5 1 1 期 2 4 浸 出金 的富集 . 2 4 1 锌 丝置换 原理 ..
现代矿 业
21 0 1 第 1 期 1年 1月 1
置换 率在 9 % 以上 , 加流 动速度 到 02 3/ 9 增 .51 h时 , 3
浸出条件 : 钼精矿加入量 10g 磨矿细度 一 0 0 , 40目
9 .6 , 出时间 4 , 固 比 6, 96% 浸 8h 液 矿浆 p >1 , H 1 氧 化 钙 加入 量 0 7 , 验结 果见 表 4 .6g试 。
表 4 氰化钠加入 量对 A u浸 出的影响
从表 4中可以看 出, 提高液固比后 , 氰化钠加入 量在 9 9l/ 以上时 , 出渣的 A . gt , 浸 u品位降低到 l 0 gt / 以下 , 出率可以达到 9 %以上 , 浸 0 气泡难以破裂
从表 3中可 以看 出 , 随着 人 料粒 度变 细 , 同磨 不
一
通过试验 , 确定的最佳氰化条件如下 : 磨矿细度 40 目 9 . 6 , 化 时 间 4 , 化 钠 量 9 9 0 9 6% 氰 8h 氰 .
矿粒度的物料浸出率差接近 5 % , 明该物料的浸 0 说
k/, 固 比 6 料 浆 p >1。根 据 浸 出试 验 结果 , gt液 , H 1
金的置换率就降低到 9 % 以下 , 0 所以最佳的含金溶
液进 入置换 箱 的流动 速度 为 0 1 I h .7I / 。 T
在 氰化 物溶 液 中 , 锌标 准 电极 电位 为 一12 .6V,
金的电位为 一 .8V 所以锌丝很容易从氰化物溶 06 , 液 中 置 换 出 金。 主 要 的 化 学 反 应 :
氰化法提金工艺
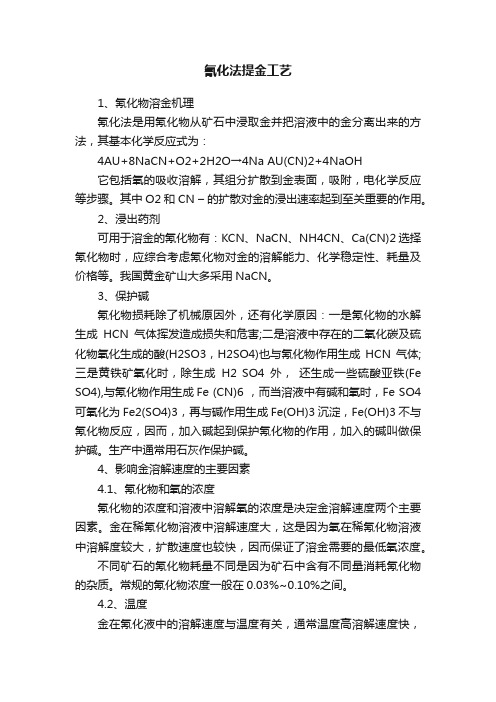
氰化法提金工艺1、氰化物溶金机理氰化法是用氰化物从矿石中浸取金并把溶液中的金分离出来的方法,其基本化学反应式为:4AU+8NaCN+O2+2H2O→4Na AU(CN)2+4NaOH它包括氧的吸收溶解,其组分扩散到金表面,吸附,电化学反应等步骤。
其中O2和CN –的扩散对金的浸出速率起到至关重要的作用。
2、浸出药剂可用于溶金的氰化物有:KCN、NaCN、NH4CN、Ca(CN)2选择氰化物时,应综合考虑氰化物对金的溶解能力、化学稳定性、耗量及价格等。
我国黄金矿山大多采用NaCN。
3、保护碱氰化物损耗除了机械原因外,还有化学原因:一是氰化物的水解生成HCN气体挥发造成损失和危害;二是溶液中存在的二氧化碳及硫化物氧化生成的酸(H2SO3,H2SO4)也与氰化物作用生成HCN气体;三是黄铁矿氧化时,除生成H2 SO4外,还生成一些硫酸亚铁(Fe SO4),与氰化物作用生成Fe (CN)6 ,而当溶液中有碱和氧时,Fe SO4可氧化为Fe2(SO4)3,再与碱作用生成Fe(OH)3沉淀,Fe(OH)3不与氰化物反应,因而,加入碱起到保护氰化物的作用,加入的碱叫做保护碱。
生产中通常用石灰作保护碱。
4、影响金溶解速度的主要因素4.1、氰化物和氧的浓度氰化物的浓度和溶液中溶解氧的浓度是决定金溶解速度两个主要因素。
金在稀氰化物溶液中溶解速度大,这是因为氧在稀氰化物溶液中溶解度较大,扩散速度也较快,因而保证了溶金需要的最低氧浓度。
不同矿石的氰化物耗量不同是因为矿石中含有不同量消耗氰化物的杂质。
常规的氰化物浓度一般在0.03%~0.10%之间。
4.2、温度金在氰化液中的溶解速度与温度有关,通常温度高溶解速度快,在无特殊工艺要求的条件下,使矿浆温度维持在150C~250C即可满足浸出的要求。
4.3、金粒的大小和形状金的溶解速度与金粒暴露的表面积成正比,因此氰化作业的磨矿粒度要比浮选更细一些。
4.4、矿浆浓度和矿泥矿浆浓度和矿泥含量直接影响溶剂的扩散速度和溶剂与金粒的接触。
野外氰化提金工艺过程中金测定的工作实践

四川地 质学报
V o 1 . 3 5 S u p p 1 . J u 1 . ,2 0 1 5
野外氰化提金工艺过程 中金测定 的工作 实践
李发铭
( 四川 省冶金地质勘查局六。 四大 队, 四川广元,6 2 8 0 1 7)
摘要 :笔者总结 了野外氰化提金 工艺过程 中金的样品分析工作 实践 ,采用碘量法测定金 ,只需简单的设备 , 即可开展金 的分析 ,较好地 满足 了野外化验和提金生产的需要 。
3 设备和分析试剂
1 )电热板 2)电阻炉 2—3 K W
3 ) 盐酸、硝酸 、氯化钾 、乙酸、氟氢化铵 、E D T A 、淀粉 ,均为分析纯。 4 ) 活性炭 ( 2 0 0目,分析纯 ) : 预先 以 2 %氟氢化铵溶液浸泡三天以上 , 过滤 , 用2 %盐酸洗 5 — 6 次, 再用水洗 5 ~ 6 次 ,烘干备用。 5)金标 准溶 液 P( A u ) =1 0 0 g / mL( 2 0 %王水 溶液 ) 。 ’ 6 ) 硫代硫酸钠标准溶液 :称取 N a S z O s ・ 5 H z O 2 5 . 2 g ,溶于新煮沸过的冷蒸馏水 中,加碳酸钠 O . 5 g , 三 氯 甲烷 l mL ,以新煮 沸过 的冷 蒸馏 水稀 释 至 1 0 L ,此 溶液 每 mL相 当于 l mg 金。 取 上述 溶液 5 0 m L于 1 0 0 0 mL容 量瓶 中 ,加碳 酸 钠 0 . 1 g ,三氯 甲烷 数滴 ,以新 煮沸 过 的冷蒸 馏水稀 释 至刻 度 ,摇匀 。配制好 放 置一周 后 ,标定 使 用 。此溶 液每 mL相 当于 5 0 g 金。 标定 :取 2 0 0 ~ 5 0 0 g 金标准溶液 ,与样品分析 4 . 4( 见下文 )同样操作 ,计算硫代硫酸钠标准溶液 对 金 的滴定 度 。
全泥氰化提金工艺设计与生产实践

全泥氰化提金工艺设计与生产实践一、工艺流程设计泥氰化提金工艺是一种常用的金属提取工艺,主要用于提取含金废物中的金属成分。
下面是一个典型的泥氰化提金工艺流程设计:1.前处理:将含金废物进行粉碎与破碎,使其颗粒大小均匀,并去除其中的杂质和有机物。
2.浸泡:将经过前处理的含金废物浸入氰化溶液中,进行化学反应。
反应时间根据废物的性质和废物含金量而定,一般为24小时至72小时。
3.沉淀:将反应后的溶液经过沉淀处理,使其中的金属成分沉淀下来。
4.过滤:将沉淀后的溶液进行过滤,去除其中的固体杂质。
5.再溶解:将过滤后的固体沉淀添加到盐酸等溶液中进行再溶解,使其中的金属成分溶解于溶液中。
6.萃取:将再溶解后的溶液进行萃取处理,利用有机溶剂提取其中的金属成分。
萃取条件为温度控制在50-70摄氏度,时间控制在2-4小时。
7.还原:将经过萃取的有机溶剂中的金属成分进行还原处理,得到金属纯度较高的金属产品。
8.精炼:将还原后的金属产品进行精炼处理,提高其纯度。
以上是一个典型的泥氰化提金工艺流程设计,根据实际情况,工艺流程中的各个环节还可以进行调整,以提高提金效率和产品的纯度。
二、生产实践在实际生产过程中,需要注意以下几个方面:1.设备选择:根据生产规模和工艺流程要求,选择合适的设备,如破碎机、浸泡槽、沉淀槽、过滤设备、萃取塔等。
设备选择要考虑生产效率、产品质量、安全性和经济性等因素。
2.溶液控制:泥氰化提金工艺中的浸泡和萃取环节涉及到溶液控制,需要严格控制溶液的温度、浓度、pH值等参数,以提高金属提取率和产品纯度。
3.杂质处理:在泥氰化提金过程中,含金废物中通常会存在一些杂质,如铜、银、铅等,需要根据具体情况采取相应的处理方法,如溶解、沉淀、萃取等,以提高产品的纯度。
4.安全保护:在泥氰化提金生产中,由于涉及到氰化物的使用,需要加强安全保护工作,严格遵守操作规程,提供足够的通风和防护设施,确保操作人员和环境的安全。
5.产品质量检测:在生产过程中,需要对产品的质量进行检测,包括金属纯度、杂质含量、产品外观等指标的检测,以确保产品符合质量要求。
- 1、下载文档前请自行甄别文档内容的完整性,平台不提供额外的编辑、内容补充、找答案等附加服务。
- 2、"仅部分预览"的文档,不可在线预览部分如存在完整性等问题,可反馈申请退款(可完整预览的文档不适用该条件!)。
- 3、如文档侵犯您的权益,请联系客服反馈,我们会尽快为您处理(人工客服工作时间:9:00-18:30)。
氰化提金工艺实践与设计探讨
摘要:文章阐述了全泥氰化提金工艺生产、设计工作中应注意把握的几个环节;全泥氰化工艺常用的几种流程;怎样合理地确定工艺、工艺参数及全泥氰化
关键词:全泥氰化提金;设计工作;工艺参数
Abstract: The paper expounds the several links should be paid attention in the production and design work of cyaniding gold extraction technology; the several processes of cyanidation techonlogy; and that how to reasonably determine the technology, technological parameters and the equipments of cyaniding gold extraction.Key words: cyaniding gold extraction; design work; technological parameters
笔者就全泥氰化提金工艺的生产实际与设计,在我国应用近三十年的历史,与设计单位认真总结近三十年的生产与设计实践。
提供给矿业同仁,供从事矿业的生产与设计部门的同行参考。
1981年吉林赤卫沟金矿75t/d全泥氰化厂及1982年黑龙江乌拉嘎金矿500t/d全泥氰化厂的建成投产为全泥氰化CCD流程在工业中的应用提供了生产和设计实例。
辽宁排山楼金矿2000t/d炭浆厂的投产,标志着我国全泥氰化炭浆工艺的科研、设计、生产水平逐步提高,成为一项技术成熟、生产可靠的提金工艺。
锦州大业金矿从CIL改为RIP的生产实践。
使我国全泥氰化提金工艺更加完善。
氧化焙烧、压热氧化、微生物浸出等对难选冶矿石予处理方法的科技创新为提金方法的应用开拓了更广泛的空间。
在矿山的开发建设中应本着“在开发中保护,在保护中开发”的原则,实践环境、资源、效益协调发展。
为了更好的遵循上述原则,应认真把握住三个环节.
一、认真委托和利用矿石可选性试验工程项目的工艺设计人员应认真作好选矿试验委托要求。
试验委托除遵照选矿试验内容和深度的有关规定提出委托内容之外,氰化工艺方案的研究委托还应明确提出以下要求,为流程方案比较、设计指标及工艺条件的确定和设备选择提供可靠的设计依据。
1、试样金品位,一般说来,地采时试样品位与地质品位比较,应下调20%~30%;露天开采时,试样品位与地质品位比较应下调10%~15%为好,力求有碍浸出的杂质含量有较强的代表性。
2、围岩及表外矿石的配入量应与开采方式可能选用的贫化率相接近,不允许大量配入围岩和表外矿进行配样,使选矿试验样品失真。
3、氰化浸出细度确定后,矿浆沉降速度的试验,其矿浆浓度应与工业生产条件相接近。
例如,高细度磨矿,设计采用旋流器分级,当溢流细度90-95%小于200目时,溢流浓度通常为20%左右,只有按此条件进行矿浆沉降试验,方能满足设计选择要求。
4、含碳的矿种进行炭浆法试验时,要委托CIP、CIL和RIP三种工艺的对比试验,以论证边浸边吸的CIL工艺,活性炭或树脂竞争吸附优势,提高浸出指标的幅度。
5、在流程试验的过程中,必须充分重视伴生有用元素的综合回收。
在研究部门提交选矿试验报告后,工艺设计人员要结合地质资源条件认真分析及审议试验内容。
二、设计流程要以生产实践为基础。
设计流程的确定,首要依据选矿试验资料。
但是,设计选择流程还必须以生产实践为基础,因为许多生产环节的工艺条件选矿试验室试验无法提供。
同时,试验室条件下完成的试验结果与生产条件有较大的差异,再者是设备能力计算是在诸多假定条件下的计算数据,虽然它是工艺设计的重要过程,是不可忽略的重要步骤,是设计的基础依据,但必须根据相类似的生产厂测定资料进行对比。
基于我国氰化厂生产实践及设计,谈几点认识。
1、实践“多碎少磨”的技术方案。
九十年代初,使用φ900旋盘细碎圆锥破碎机与深腔颚式破碎机组成“二段半”流程,破碎产品粒度降到8mm以下,提高了磨机处理能力。
φ2100×3000球磨机在磨矿细度为50%~55%小于200目时,处理能力可达到350~400t/d,比其他类似矿山同型号球磨机提高100~150t/d,经济效益极其显著。
在此应该指出,使用这种设备是有条件的,对含水份高,含泥量大的矿种不能套用蚕庄模式。
可以采用适当放大细碎设备,增加予先筛分作业,事先分出合格产品,增大闭路筛分作用的振筛面积提高筛分效率,增大圆锥破碎机的循环量,这种方法应在设计中推广采用。
2、“两浸两洗”全泥氰化流程
国内全泥氰化厂CCD流程,在柴胡栏子金矿150t/d全泥氰化厂使用“两浸两洗”流程,原设计为一浸三段洗涤,选厂建成后,生产指标较低,尤其洗涤率只有92.57%,主要原因是矿石严重氧化,含粘性矿泥多,固液分离困难,洗涤浓缩机排矿浓度仅达42%左右,排液品位高达0.31g/m3。
为提高洗涤率,该厂在不增加设备的前提下,将两台φ9m三层浓缩机改两浸两洗流程,洗涤率提高4%左右。
应当指出柴胡栏子金矿全泥氰化厂CCD工艺是1975年建成的,选矿厂设计时炭浆工艺在国内处于工业性试验阶段,因此当时无设计和生产实践可供设计者借鉴,根据该矿的矿石性质本应采用炭浆工艺,由于历史原因采用了CCD工艺,因此我认为柴胡栏子选厂CCD流程目前采用两浸两洗,是特定条件下发生的。
虽提高了洗涤率,但就工艺说不算合理。
采用CCD流程重要条件之一是矿浆沉降速度快,易固液分离,一般说洗涤流程根据规模不同,入选品位等因素的差异,也只
能使用三次或四次洗涤。
3、CCD、CIP、RIP流程
国内CCD、CIP(CIL)、RIP三种工艺在生产中均有采用,树脂法有利于含银高的矿山采用,如锦州大业金矿。
设计确定工艺时,应遵循以下原则:矿石严重风化、矿泥含量大、矿浆沉降速度慢、固液分离困难、铜及其他贱金属含量低、银金比小于5∶1的矿石,尤其地处寒冷地区的矿山,应采用CIP或CIL工艺,与此相反应使用CCD工艺。
使用CIP、CIL或RIP工艺,谁具优势,应严格比较。
4、浸出条件
选矿试验报告提供了试验室条件下的设计依据,如予处理、PH值、氰根浓度等,这些试验条件,一般说在设计中必须给予保证,其他设计条件的确定,必须依据生产实践。
A、浸出细度
试验确定的细度为“筛分分级”,与生产条件下的“沉降分级”和“离心分级”同样细度时其粒级组成生产时偏细,一般说低5%左右。
如,海沟金矿全泥氰化厂试验推荐90%小于200目,生产使用85%小于200目,浸出指标仍达到设计指标,而选厂处理能力由250t/d提高到300t/d。
研究部门多推荐高细度浸出,给设计和生产带来一系列问题,如浸前浓缩机及洗涤浓缩机的沉降面积增大,尾矿堆坝的难度加大,造成基建投资和生产费用的增加。
B、浸出时间
试验单位使用高速搅拌槽进行氰化浸出试验,和生产设备比,搅拌强度高,矿浆温度高,试验浸出时间必然偏短,而生产必须延长方能满足浸出要求,加之试验为单槽浸出,生产为多槽连续浸出,矿浆短路难免发生,又由于处理量的波动等因素,根据生产经验,其浸出时间应大于24小时。
C、浸出浓度
试验报告多推荐高浓度浸出,以求减少浸出设备容积,设计要区别对待试验条件,因为生产使用高效槽,其线速度仅为2.8-3.1m/s,精矿氰化可选用35%-40%的浸出浓度,全泥氰化40%浓度为宜。
泥质矿石由于矿浆粘度大,浸出浓度只能在30%-35%之间选定。
D、载金炭品位及载金炭解吸电解工艺
有关试验数据表明,在单一的高品位含金溶液中载金炭品位可达10kg/t以上。
国内炭浆厂载金炭品位与国外比较相对较高。
从生产实践出发,载金炭控制
在4kg/t左右为宜。
载金炭的解吸电解工艺在80年代为常温常压,解吸液用NaOH、NaCN溶液按1%配制。
现在,发展到高温高压无氰解吸电解。
温度150℃,压力在0.45~0.55MPa。
三、设备选择是实践工艺设计的保障
1、浓密设备包括浸前浓缩机和洗涤浓缩机。
以前选矿厂工艺设计浓缩机的计算一般都按生产定额计算所需面积。
全泥氰化浓缩机系主要生产设备,对工艺条件的实现和设计指标起着重要作用,因此套用以往的设计资料计算浓缩机的面积,不符合全泥氰化的工艺要求。
高效浓缩机面积国外的作法是制造厂家根据矿浆特性进行试验确定,如张家口金矿500吨/日全泥氰化炭浆厂,磨矿细度90-95%小于200目,引进高效浓缩机直径为5.18m,生产能力可达600t/d。
2、浸出及吸附设备已经形成了系列产品,最大规格为10×10.5m,可以满足不同生产能力的氰化厂选型需要。
在选型中,不能简单的套用搅拌槽的选择计算方法,要充分考虑矿浆的体重、浓度、浸出时间及波动系数。
在浸出段数的确定中,为了防止发生“短路”现象造成的影响,不应低于四段浸出来选择设备。
总之,在全泥氰化提金工艺实践与设计中,应认真总结生产实际、流程确定及设备选择,紧密结合生产实践,获得理想的生产和设计效果。