正确认识纯化水系统的“死角
卫生纯水系统中针对死角的定义

GMP纯水系统设计之“死角”FDA针对6D的官方定义为:Pipelines for the transmission of purified water for manufacturing or final rinse should not have an unused portion greater in length than 6 diameters (the 6D rule) of the unused portion of pipe measured from the axis of the pipe in use.而6D是医药系统中的最低要求,厂方有时会采用更高的要求,此时3D,2D就出现了。
为了表达的比较直观我附图给大家一个认识。
可见6D和2D的测量方式是不同的。
6D是从主管路的中心开始测量,而2D是从支管开始点开始测量的。
而死角就是非使用部分超出了以上要求的尺寸。
以下是一张样图,x的值需要控制在50mm以内,否则阀门旁边的那一段区域就是死角了。
而死角并不仅仅针对阀门,管路的设计只要产生这样超出6D,3D,2D规格要求的非使用区域就是死角。
而零死角(zero-dead leg)就是上图x的长度是0。
这样的设计并不是在管路中的所有地方都是必须的(客户要求除外),它大多使用在终端的使用点的地方。
此处的水质要求应该是最高的,对于细菌的控制也是最严格的。
零死角的构成请看下图。
而满足零死角的阀门称作“零死角阀门”主要是一个零死角的阀座外加一个隔膜执行头。
见下图:现在医药用水一般对死角的问题都要求<3D!(测量的方法是从主管道的管壁到支管阀门中心的距离)楼主所说的2D一般会在什么条件下使用?再者楼主的2D测量方法为什么不是从主管道的管壁到支管阀体的中心呢?所谓2D其实就是比3D更高的要求。
当然最高的要求就是zero-dead leg.零死角。
当然在很多情况下是无法满足的,或者说代价比较昂贵。
死角检查试验报告和方案

SOP标准作业指导书NO: GT-LPS-QA-04 Version: A死角检查实验方案Page: 3 of 4Date:2013-5-1 Review Period: 2 Years1.应用范围注射水系统;纯化水系统2.目的为了完善水系统尽可能的满足死角要求,达到良好的水质3.程序3.1. 先查看U型弯下的使用点管径尺寸3.2. 在检查所使用的隔膜阀是否符合标准3.3. 把隔膜阀安装到各使用点检查是否满足3D或6D要求· 3D指U型弯下管壁到阀中心不超过使用点管径3倍·6D指U型弯中心到阀中心不超过使用点管径的6倍3.4. 用卡尺或卷尺进行实地测量4.数据表死角检查报告系统和使用点名称通过评论WFI Yes / No 符合3D WFI Yes / No 符合3D WFI Yes / No 符合3D WFI Yes / No 符合3D WFI Yes / No 符合3D WFI Yes / No 符合3D WFI Yes / No 符合3DSOP标准作业指导书NO: GT-LPS-QA-04死角检查实验方案Version: APage: 3 of 4Date:2013-5-1 Review Period: 2 YearsWFI Yes / No 符合3D WFI 符合3D WFI 符合3D WFI 符合3D WFI 符合3D WFI 符合3D WFI 符合3D WFI 符合3D WPU 符合3D WPU 符合3D WPU 符合3D WPU 符合3D WPU 符合3D WPU 符合3D WPU 符合3D WPU 符合3D WPU 符合3D WPU 符合3D WPU 符合3D WPU 符合3D WPU 符合3D WPU 符合3D 施工单位检查结果签名/日期Yes / No建设(监理)单位检查结果签名/日期Yes / No。
纯化水系统的基本知识
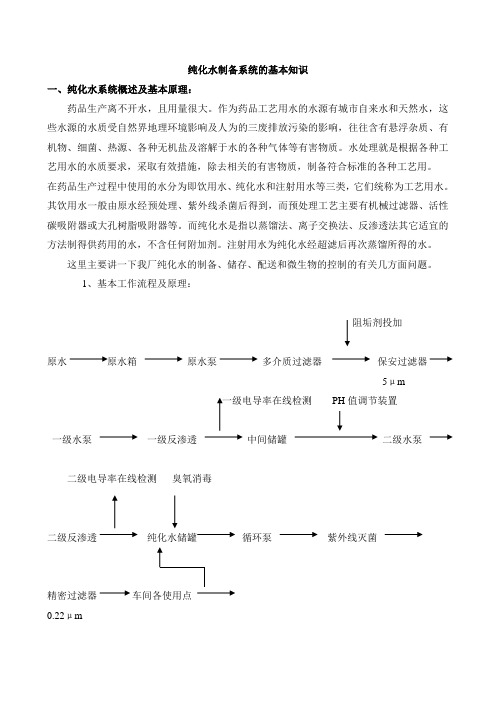
纯化水制备系统的基本知识一、纯化水系统概述及基本原理:药品生产离不开水,且用量很大。
作为药品工艺用水的水源有城市自来水和天然水,这些水源的水质受自然界地理环境影响及人为的三废排放污染的影响,往往含有悬浮杂质、有机物、细菌、热源、各种无机盐及溶解于水的各种气体等有害物质。
水处理就是根据各种工艺用水的水质要求,采取有效措施,除去相关的有害物质,制备符合标准的各种工艺用。
在药品生产过程中使用的水分为即饮用水、纯化水和注射用水等三类,它们统称为工艺用水。
其饮用水一般由原水经预处理、紫外线杀菌后得到,而预处理工艺主要有机械过滤器、活性碳吸附器或大孔树脂吸附器等。
而纯化水是指以蒸馏法、离子交换法、反渗透法其它适宜的方法制得供药用的水,不含任何附加剂。
注射用水为纯化水经超滤后再次蒸馏所得的水。
这里主要讲一下我厂纯化水的制备、储存、配送和微生物的控制的有关几方面问题。
1、基本工作流程及原理:阻垢剂投加原水原水箱原水泵多介质过滤器保安过滤器5μm一级电导率在线检测PH值调节装置一级水泵一级反渗透中间储罐二级水泵二级电导率在线检测臭氧消毒二级反渗透纯化水储罐循环泵紫外线灭菌精密过滤器车间各使用点0.22μm本工艺分为预处理、反渗透系统、储存与供水、杀菌与过滤四部分1)预处理:由于原水中含有悬浮物、有机物、细菌、胶体、微生物等,这些物质在反渗透系统浓缩分离时,会对反渗透膜造成污染,使系统不能正常工作。
所以要对原水进行初级处理,其包括原水箱和原水泵、多介质过滤器、阻垢装置、精密过滤器。
●原水箱:是为了向反渗透系统提供稳定的供水压力,不至于因外界供水压力的突变而影响整个系统的工作稳定。
●多介质过滤器:是利用几种过滤介质(如石英砂、活性碳、无烟煤等)的混合过滤作用在一定压力下把浓度较高的水通过一定厚度的粒状或非粒状过滤材料,从而有效除去原水中的悬浮物等杂质使水澄清的一种装置。
它可以减小精密过滤器的更换频率。
●阻垢装置:为了防止水中的钙、镁离子在水浓缩时在反渗透膜表面的结垢故在反渗透前加入阻垢剂。
纯化水设备工作原理及系统运行注意事项
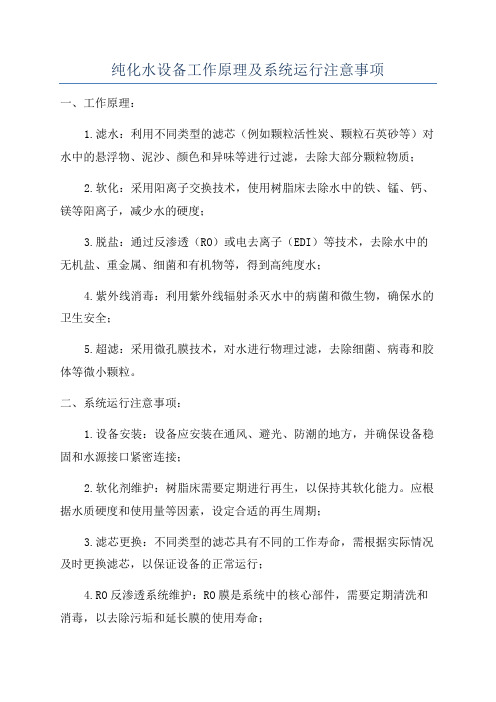
纯化水设备工作原理及系统运行注意事项一、工作原理:1.滤水:利用不同类型的滤芯(例如颗粒活性炭、颗粒石英砂等)对水中的悬浮物、泥沙、颜色和异味等进行过滤,去除大部分颗粒物质;2.软化:采用阳离子交换技术,使用树脂床去除水中的铁、锰、钙、镁等阳离子,减少水的硬度;3.脱盐:通过反渗透(RO)或电去离子(EDI)等技术,去除水中的无机盐、重金属、细菌和有机物等,得到高纯度水;4.紫外线消毒:利用紫外线辐射杀灭水中的病菌和微生物,确保水的卫生安全;5.超滤:采用微孔膜技术,对水进行物理过滤,去除细菌、病毒和胶体等微小颗粒。
二、系统运行注意事项:1.设备安装:设备应安装在通风、避光、防潮的地方,并确保设备稳固和水源接口紧密连接;2.软化剂维护:树脂床需要定期进行再生,以保持其软化能力。
应根据水质硬度和使用量等因素,设定合适的再生周期;3.滤芯更换:不同类型的滤芯具有不同的工作寿命,需根据实际情况及时更换滤芯,以保证设备的正常运行;4.RO反渗透系统维护:RO膜是系统中的核心部件,需要定期清洗和消毒,以去除污垢和延长膜的使用寿命;5.储水:纯化水应储存在无污染的容器中,避免接触灰尘、细菌等,防止二次污染;6.系统定期检测:定期对设备进行全面检测,包括水质、流量、压力等参数的监测,以及设备的维护和维修。
三、附加注意事项:1.操作人员应接受专业培训,并熟悉设备的操作规程和安全事项,以确保设备的正常运行和人员的安全;2.设备运行过程中应定期监测水质,确保其符合使用要求,并及时处理异常情况;3.设备停电或长时间不使用时,应及时关闭系统,并排空水箱,以免水质退化或设备受损;4.增加备用设备或备用滤芯供替换使用,以确保设备的连续运行和水质的可靠性。
总之,纯化水设备的工作原理是通过多种技术手段对水进行处理,去除其中的污染物和杂质。
在使用过程中,需要注意设备的安装、滤芯更换、RO膜清洗等维护工作,以及定期对水质进行监测和设备进行检修,保证设备的正常运行和水质的安全。
医药工艺用水系统设计:水管路系统设计

水管路系统设计5.1.1 纯化水、注射用水管路系统设计时,要注意流体最佳流向,使死角处于流动方向上,减少“气袋”及“水坑”(图14)。
图14 流体最佳流向示意图5.1.2 本条依据现行国家标准《洁净厂房设计规范》GB 50073作出规定。
5.1.3 管道应具有一定的坡度,避免出现使水滞流和不易清洗的部位,确保管路系统能完全排放。
ASME BPE标准要求较短管坡度大于2%,较长管道坡度为1%~0.5%,因此,本规范规定水平管道应有0.5%~1%的坡度。
为防止倒灌,排放点必须与地漏等保持空气阻断,即排放管不能与下水管道直接相连。
5.1.4 管路中使用的软管应卫生连接,设计安装时注意长度和坡度,不允许有积液。
软管的安装应保证整个软管能自动或手动排放。
5.1.5 为确保工艺用水系统的独立性,不同水质的管路间应无交叉污染的风险。
例如,有时为了操作的灵活,在不同水质的管路间设置了带阀门的旁通管,但一旦阀门失灵,其他水质的水就会进入注射用水系统,使注射用水系统遭受污染。
也不要和其他介质管道相连或共用管口。
5.1.6 用水点阀门与使用工序或设备之间应直连,就近连接至设备,否则使用点阀门后的配管会成袋型,需再增设排水阀。
例如,当洗瓶机设备布置在洗瓶间中央,循环管为布置美观而靠墙敷设时就会产生上述现象。
图15~图19为ASME BPE对工艺用水使用点的设计要求。
图15 用水点距设备管道较长做法图16 用水点与设备直接相连做法图17 用水点后设换热器做法图18 用水点下接水槽做法图19 用水点下带软管做法图20 为ISPE列举的用水点设计方式。
图20 ISPE列举的用水点设计方式图21为典型的低温用水点设计方式。
图21 典型的低温用水点设计方式。
纯化水系统安装与使用注意点
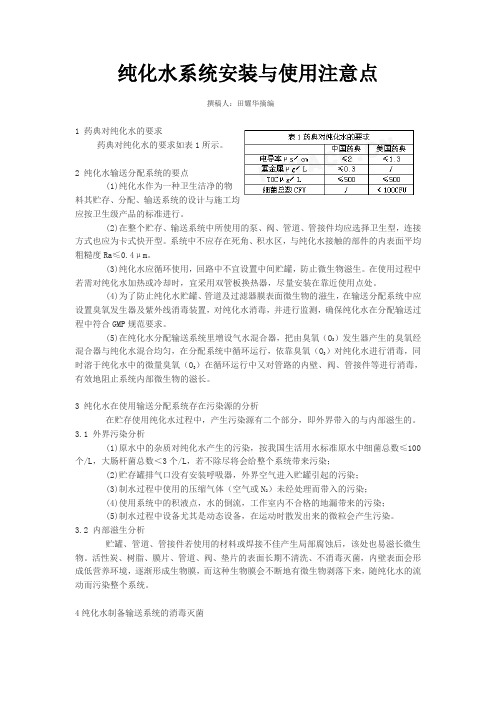
纯化水系统安装与使用注意点撰稿人:田耀华摘编1 药典对纯化水的要求药典对纯化水的要求如表1所示。
2 纯化水输送分配系统的要点(1)纯化水作为一种卫生洁净的物料其贮存、分配、输送系统的设计与施工均应按卫生级产品的标准进行。
(2)在整个贮存、输送系统中所使用的泵、阀、管道、管接件均应选择卫生型,连接方式也应为卡式快开型。
系统中不应存在死角、积水区,与纯化水接触的部件的内表面平均粗糙度Ra≤0.4μm。
(3)纯化水应循环使用,回路中不宜设置中间贮罐,防止微生物滋生。
在使用过程中若需对纯化水加热或冷却时,宜采用双管板换热器,尽量安装在靠近使用点处。
(4)为了防止纯化水贮罐、管道及过滤器膜表面微生物的滋生,在输送分配系统中应设置臭氧发生器及紫外线消毒装置,对纯化水消毒,并进行监测,确保纯化水在分配输送过程中符合GMP规范要求。
(5)在纯化水分配输送系统里增设气水混合器,把由臭氧(O3)发生器产生的臭氧经混合器与纯化水混合均匀,在分配系统中循环运行,依靠臭氧(O3)对纯化水进行消毒,同时溶于纯化水中的微量臭氧(O3)在循环运行中又对管路的内壁、阀、管接件等进行消毒,有效地阻止系统内部微生物的滋长。
3 纯化水在使用输送分配系统存在污染源的分析在贮存使用纯化水过程中,产生污染源有二个部分,即外界带入的与内部滋生的。
3.1 外界污染分析(1)原水中的杂质对纯化水产生的污染,按我国生活用水标准原水中细菌总数≤100个/L,大肠杆菌总数<3个/L,若不除尽将会给整个系统带来污染;(2)贮存罐排气口没有安装呼吸器,外界空气进入贮罐引起的污染;(3)制水过程中使用的压缩气体(空气或N2)未经处理而带入的污染;(4)使用系统中的积液点,水的倒流,工作室内不合格的地漏带来的污染;(5)制水过程中设备尤其是动态设备,在运动时散发出来的微粒会产生污染。
3.2 内部滋生分析贮罐、管道、管接件若使用的材料或焊接不佳产生局部腐蚀后,该处也易滋长微生物。
纯化水系统验证标准操作规程
文件制修订记录的适用性。
适用范围:纯化水系统验证责任者:公用工程验证小组程序:1、纯化水处理系统工艺流程图2、纯化水系统的预确认——基本要求2.1对预处理设备的要求2.1.1纯化水的预处理设备可根据水水质情况配备;2.1.2多介质机械过滤器能自动反冲或再生、排放;2.1.3活性碳过滤器为有机物集中地,为防止细菌、细菌内毒素的污染,除要求能自动反冲外,还可用蒸汽消毒或巴氏消毒(80℃的汽、水混合物喷淋灭菌2小时)。
2.2对纯化水设备的要求2.2.1 反渗透装置在进□处须安装3.0μm的水过滤器;2.2.2去离子器可采用混合床,并能连续再生;2.2.3通过混合床等去离子器后的纯化水必须循环,使水质稳定;2.2.4由于紫外消毒的穿透性较差,紫外灯应安装在过滤器的下游;2.2.5由于紫外等激发的255nm(2537埃)波长的先强与时间成反比故要求有记录紫外灯使用时间的仪表;2.2.6若采用蒸馏工艺制备纯化水,宜采用多效蒸馏水机,其材质为316L不锈钢材料电抛光并钝化处理。
2.3对贮水容器(贮罐)的基本要求2.3.1 316L不锈钢制作,内壁电抛光并作钝化处理;2.3.2贮水罐上安装0.22"m疏水性的通气过滤器(呼吸器)并可以加热消毒。
无论中间贮罐还是纯化水贮罐,均不得敞口,以防外源性污染。
2.3.3使用疏水性过滤器时,在排气,的过滤器安装温控外套,以防止蒸汽冷凝阻塞贮水罐排气管。
2.3.4能耐受121℃高温消毒或化学药剂消毒:压力容器的设计、制造,由有许可证的单位及合格人员承担,须按《钢制压力容器》 (GBl50-80)“压力容器安全技术监察规程”的有关规定办理。
2.3.5贮罐要密封、内表面要光滑、能对贮罐顶部空间进行喷淋;2.3.6排水阀采用不锈钢隔膜阀.2.4对管路及分配系统的基本要求2.4.1 316L不锈钢管材内壁电抛光并作钝化处理;2.4.2管道采用热熔式氩弧焊焊接连接,或者采用卫生夹头分段连接;2.4.3阀门采用不锈钢聚四氟乙烯隔膜阀或蝶阀,避免使用球阀、闸阀、截止阀。
制药纯化水设备系统管路死角设计标准
制药纯化水设备系统管路死角设计标准制药纯化水设备系统管路死角设计标准一、死角的定义死角的定义是:从使用的管道轴线量起,未使用部分的长度与使用管道直径的比值。
是制药纯化水设备系统管路设计中常出现的问题。
二、死角对纯化水设备系统的影响纯化水设备系统中常出现的死角是微生物繁殖的温床,并为“生物膜”的形成提供了条件,容易引起微生物指标和内毒素指标超标以及纯化水系统杀菌不彻底等现象。
同时,也增加了整个纯化水设备系统的污染风险,对企业的生产的产品质量造成不稳定因素。
此外,死角也是影响管道支路消毒清洗的关键因素。
三、GMP对纯化水设备系统死角的要求2010版中国GMP要求“制药纯化水系统的管道设计和安装应避免死角与盲管的存在”,同时,GMP建议系统应尽可能避免系统死角的存在。
四、纯化水管道死角标准目前,对纯化水设备管道的死角并没有一个标准以及硬性规定,制药行业普遍认可的是3D死角标准。
包括中国GMP、欧盟GMP和美国FDA cGMP都是以“3D”死角标准(即L<3D,其中L是指“流动侧主管网内壁到之路盲板或者用点阀门中心的举例,D 是指“非流动侧支路管道的内径”)五、洁峰纯化水设备系统符合3D死角标准ASME BPE认为用水点阀门安装方式(U行弯与两通阀门连接,T 型零死角阀门)可以满足3D死角要求,而管道焊接方式是最安全的连接方式。
洁峰制药纯化水设备系统严格遵循GMP标准,与纯化水、接触的管线均满足GMP3D要求。
在纯化水管道焊接工艺方面,洁峰采用先进的德国自动焊机记忆GF专用切管工具。
并严格规定所有纯化水管道优先采用焊接,其次卡接,杜绝丝牙的连接方式。
在纯化水设备系统管道连接方面,纯化水任何活动接口均用卫生级卡箍连接。
并配备了专用浓水隔膜调节阀,隔膜阀水平安装时为45度,循环管线安装设为0.5的坡度,设最低点为排放点。
技术资料由莱特莱德西安纯化水设备公司提供。
纯化水系统原理
纯化水系统原理
纯化水系统原理是通过一系列的物理、化学或生物过程,将水中的杂质、污染物或微生物去除,使水达到一定的纯净度或安全标准。
下面将介绍几种常见的纯化水系统原理:
1. 活性炭吸附:活性炭是一种具有很高比表面积的材料,能够有效吸附水中的有机物、氯和臭味等杂质。
水经过活性炭层时,这些杂质会被吸附到活性炭上,从而净化水质。
2. 离子交换:离子交换是一种通过树脂中的离子与水中的离子发生置换反应,去除水中的杂质的方法。
常见的离子交换器有阴离子交换器和阳离子交换器,它们可以去除水中的硬度物质、重金属离子和一些无机盐等。
3. 膜分离:膜分离技术是利用半透膜对水中的溶质进行分离的方法。
常见的膜分离技术有反渗透、超滤和微滤等。
这些膜可以有效去除水中的微生物、有机物、颗粒物和高分子物质。
4. 紫外线消毒:紫外线消毒是利用紫外线的照射杀灭水中的微生物的方法。
通过让水经过紫外线灯管的照射,紫外线可以破坏微生物的核酸结构,从而达到灭菌的目的。
5. 臭氧氧化:臭氧氧化是利用臭氧氧化反应去除水中的有机物和微生物的方法。
臭氧能够氧化降解水中的有机物,同时也具有杀灭微生物的能力。
通过以上的纯化水系统原理,可以去除水中的有机物、无机物、
微生物和其他污染物,提供符合要求的纯净水。
不同的原理可以结合使用,以达到更高的纯化效果。
纯化水设备系统死角盲管怎么排查
纯化水设备管道的死角盲管要怎么排查?首先了解下纯化水设备管路中的死角和盲管的定义:死角的定义是:从使用的管道轴线量起,未使用部分的长度与使用管道直径的比值。
盲管的定义:没有水流通过或流动的管路,比如压力表、三通(阀门关闭的一端)等,其长度不能超过6D(D管道直径)。
常见死角案例图:纯化水设备系统厂家按照GMP标准以及中国2010药典标准进行设计生产安装就不会出现死角盲管问题。
Carryclean科瑞纯化水设备系统提供专业的GMP验证文件。
相关标准:卫生级管道系统遵循6D 原则(《医药工业洁净厂房设计规范》(GB50457-2008)),ASME BPE 标准则为2D原则。
GMP对纯化水设备管路的要求1、结构设计应简单、可靠、拆装简便。
2、为便于拆装、更换、清洗零件,执行机构的设计尽量采用的标准化、通用化、系统化零部件。
3、设备内外壁表面,要求光滑平整、无死角,容易清洗、灭菌。
零件表面应做镀铬等表面处理,以耐腐蚀,防止生锈。
设备外面避免用油漆,以防剥落。
4、制备纯化水设备应采用低碳不锈钢或其他经验证不污染水质的材料。
制备纯化水的设备应定期清洗,并对清洗效果验证。
5、注射用水接触的材料必须是优质低碳不锈钢(例如316L不锈钢)或其他经验证不对水质产生污染的材料。
制备注射用水的设备应定期清洗,并对清洗效果验证。
6、纯化水储存周期不宜大于24小时,其储罐宜采用不锈钢材料或经验证无毒,耐腐蚀,不渗出污染离子的其他材料制作。
保护其通气口应安装不脱落纤维的疏水性除菌滤器。
储罐内壁应光滑,接管和焊缝不应有死角和沙眼。
应采用不会形成滞水污染的显示液面、温度压力等参数的传感器。
对储罐要定期清洗、消毒灭菌,并对清洗、灭菌效果验证。
7、制药用水的输送1)纯化水和制药用水宜采用易拆卸清洗、消毒的不锈钢泵输送。
在需用压缩空气或氮气压送的纯化水和注射用水的场合,压缩空气和氮气须净化处理。
2)纯化水宜采用循环管路输送。
管路设计应简洁,应避免盲管和死角。
- 1、下载文档前请自行甄别文档内容的完整性,平台不提供额外的编辑、内容补充、找答案等附加服务。
- 2、"仅部分预览"的文档,不可在线预览部分如存在完整性等问题,可反馈申请退款(可完整预览的文档不适用该条件!)。
- 3、如文档侵犯您的权益,请联系客服反馈,我们会尽快为您处理(人工客服工作时间:9:00-18:30)。
正确认识系统的“死角”
死角检查是系统进行安装确认(IQ)时的一项重要内容。
在制药流体工艺系统(如制药用水系统、制药工艺配液系统、CIP/SIP系统)中,任何死角的存在均可能导致整个系统的污染。
死角过大所带来的风险主要如下:
▪为微生物繁殖提供了“温床”并导致“生物膜”的形成,引起微生物指标、TOC指标或内毒素指标超标,导致水质指标不符合药典要求;
▪系统消毒或灭菌不彻底导致的二次微生物污染;
▪系统清洗不彻底导致的二次颗粒物污染或产品交叉污染。
因此,中国2010版GMP要求“管道的设计和安装应避免死角、盲管”。
《美国机械工程师协会生物加工设备标准》2014版对于死角有准确的定义,《ASMEBPE》(2014)规定:“死角”是指当管路或容器使用时,能导致产品污染
的区域(deadleg: an area of entrapment in a vessel or piping run that could lead tocontamination of the product.)。
1976年,美国FDA在CFR212法规上第一次采用量化方法进行死角的质量管理,工程上俗称“6D”规则,其含义为“当L/d<6时,证明此处无死角”,其中L指“流动侧主管网中心到支路盲板(或用点阀门中心)的距离”,d为支路的直径。
随后的研究表明,“3D”规则更符合洁净流体工艺系统的微生物控制要求,其中L的含义变更为“流动侧主管网管壁到支路盲板(或用点阀门中心)的距离”(图1)。
图1 死角的发展
更加准确的死角量化定义来自于《ASMEBPE》规范(图2),该定义明确规定:L是指“流动侧主管网内壁到支路盲板(或用点阀门中心)的距离”,D是指“非流动侧支路管道的内径”。
图2 死角的准确量化定义
死角的消毒验证:小于3D死角的支路(图中为L/D等于0,0,1.5)处很快能达到预定的消毒温度,支路垂直向下或向上的大于3D死角(图中为L/D等于4.0,5.6,9.4)在流速为0.4m/s和1.2m/s时,支路处始终无法达到预定的消毒温度,提高流速到2.0m/s,除垂直向下的4D支路能达到消毒温度外(图3),其他支路处始终无法达到预定的消毒温度(图4)。
上述实验说明,死角是影响支路清洗的关键因素,而流速是影响支路清洗的次关键因素。
图3 支路垂直向下时,死角的消毒验证
图4 支路垂直向上时,死角的消毒验证
死角的清洗验证:图5a为采用“ASMEBPE定义”模拟的死角模型,该死角处L/D 等于6,死角处预先放置105个可检测颗粒,清洗合格的标准为最终残留颗粒数<102个。
从图中可以看出,当清洗流速为0.5m/s时,死角处的残留颗粒数在清洗初期会有明显下降,但当清洗时间超过10分钟后,残留颗粒数将维持在>104个的较高水平,且颗粒数不再降低;增加清洗流速至1.0m/s,在20分钟的清洗时间内,死角处的残留颗粒数可从105个降低至接近103个;当清洗流速增加2.0m/s和2.5m/s时,其清洗验证的数据曲线基本一致,即在很短的清洗时间内(约1~2分钟),死角处的残留颗粒数可从105个降低至接近102个,但无法达到可接受的清洗标准。
图5b的死角L/D等于2.8,采用同样的工况和可接受清洗标准。
从图中可以看出,当清洗流速为0.5m/s时,死角处的残留颗粒数在清洗初期会有明显下降,但当清洗时间超过1分钟后,残留颗粒数下降幅度不大,当清洗时间超过10分钟后,残留颗粒数将维持在接近102个且未达到可接受清洗标准的水平;增加清洗流速至1.0m/s,在很短的清洗时间内,死角处的残留颗粒数会有显著下降;当清洗流速增加2.0m/s
时,在极短的清洗时间内(约10~20秒),死角处的残留颗粒数可从105个降低至可接受的清洗标准之下,之后的时间内也维持在此低水平。
上述模型进一步表明,死角是影响支路清洗的关键因素,而流速是影响支路清洗的次关键因素。
图5 死角的清洗验证
事实上,从上述的消毒验证和清洗验证的角度能有效说明3D死角规则在制药用水系统设计及加工过程中的合理性。
大多数GMP法规并未对死角标准做一个最大值的硬性规定(除了WHOGMP),部分GMP也仅仅是在其检查指南中给予了控制3D死角的建议,死角的“3D规则”还是得到了制药行业的普遍认同和推广。
中国GMP、欧盟GMP、WHOGMP和美国FDA cGMP的大多数企业均以“3D”规则(L<3D)作为安装确认的死角检查标准。
因生物发酵等制药工艺的交叉污染风险
更大,ASMEBPE标准要求生物制药企业以更加严格的“2D规则”(L<2D)作为死角的安装确认检查标准。
在制药用水系统的设计中,控制死角的设计理念有很多种。
例如,制药用水用点阀门的安装包含两种方法,第一种方式为U型弯与两通路阀门连接;第二种方式为安装T 型零死角阀门,上述方法均可满足3D死角要求(图6)。
虽然第一种安装方式比零死角阀门的安装方式节省项目投资,但其微生物污染的风险也会相应增加,因此,ISPE 推荐,如果用一个有着较大口径的两通路隔膜阀替代T型零死角阀门,则需要考虑用增加最低速度的方式来弥补其微生物污染的风险。
(a)U型弯设计(b)零死角阀设计
图6 用水点阀门的死角控制
自动氩弧焊接是最安全的不锈钢组件连接方式,采用U型弯与两通路隔膜阀自动焊接并不会影响隔膜阀膜片的更换和维修,该阀门为供应商依据工程公司或客户的实际需求特殊开发的“一端焊接、一端卡接”隔膜阀(图7)。
通过对制药行业隔膜阀标准尺寸的比对发现,采用DN25规格的两通路隔膜阀与U 型弯自动氩弧焊接组合时,可有效满足用水点的3D死角要求;采用DN25阀门与U 型弯卡箍连接会造成用点死角超过3D;理论上讲,采用DN20或DN15阀门与U型弯手工焊接也能达到3D标准,但其手工焊接的焊口质量非常不稳定,内窥镜影像质量往往不是很理想,从工程实践角度并不可取。
图7 一端焊接、一端卡接的隔膜阀
在制药工艺配液系统中,为了使工艺系统具有更好的死角控制、更好的可清洁性、更高的产品可靠性、更紧凑的空间布局和更简单的验证,工程上常使用多通道阀组。
多通路阀是指由一整块不锈钢材料锻造加工而成的阀门,它属于“多个两通路阀门组合设计”的进一步结构优化(图8),多通路阀也称为“Block阀”。
整块钢的生产工艺使得多通道阀内部没有焊缝,可实现紧凑型设计并可大大减少残液,采用独特的定制设计能够集成各种功能,例如混合、分配、开关、给料或排放。
图8多通道阀的加工过程
多通路阀最少可加工成3个通路,最多可加工成40个通路,并可加装20个执行机构的阀门,图9是一个四通道Block阀的设计示意图。
图9 四通路阀设计示例
根据不同的应用,有不同种类的多通道阀。
图10所示为一种复杂设计的注射用水用水点阀门,该阀门整合了如下功能:WFI用水点、取样、冷凝水排放、进罐、排液以及供应超纯蒸汽进行灭菌。
图10a所示为一种传统型的设计,其中包括四个T形阀并有至少六条焊缝,而采用Block型设计(图10b)可避免三条内部焊缝,此外,其所具有的阀管位置可以配置成不再需要如三通、管接头和弯头等管路部件的形式,这
使得Block型设计更为紧凑,死角最小,而且,管道的偏心设计能够确保该多通道阀更加容易排空。
(a)传统设计(b)Block设计
图10 多通道阀的设计优势
另一个控制死角的典型设计为各种常用的传感器,按设计结构划分,制药用水系统常用的传感器分为两大类,第一大类为“插入式”传感器,第二大类为“流通式”传感器。
“流通式”传感器的接触产品部分为没有任何死角的直管段,非常便于清洗与灭菌,温度传感器、压力传感器、电导率传感器及流量传感器均可设计成“流通式”,图11是典型的“插入式”电导率传感器与“流通式”电导率传感器的机构图;另一个例子是表面声波流量传感器,它也属于典型的“流通式”传感器。
(a)插入式(b)流通式
图11 电导率传感器的结构
死角的“3D”规则主要适用于RO之后需要控制微生物负荷的制药用水系统,包括纯化水系统、高纯水系统与注射用水系统。
对于新建的制药用水系统,应尽量做到全系统满足“3D死角”设计规则,这对控制整个系统的微生物污染风险将非常有益,建议在安装确认时严格执行;对于气体系统,如纯蒸汽系统、洁净氮气和洁净压缩空气系统等,因其系统中缺乏微生物繁殖的水分或系统长期处于湿热灭菌状态“3D死角”规则并非必需,GEP建议上述气体系统的死角应尽可能短。
NA卡接与Kest卡接能实现罐体附件安装无死角(图12),很好地解决了连接处可能存在的微生物滋生风险。
图12 NA卡接与Kest卡接
需要注意的是,“死角”是指当管路或容器使用时能导致产品污染的区域,超过3D 的安装点并不意味着该处一定存在“死角”,例如,注射用水回水在TOC检测仪的取样阀门常为DN8或DN15等小口径尺寸,虽然该处无法满足“3D”要求,但因其长期处于频繁自冲洗状态,其微生物的污染风险可控,并不存在死角。
与提高流速或提高管道抛光度等级相比,实现死角的“3D”规则对制药企业项目投资的影响相对较小,但其对流体工艺系统质量保证的作用却非常显著,因此,企业需将死角控制作为制药用水系统已安装确认时一个重要的检查项目对待。
同时,当系统死角控制的不够理想时(如超过3D),可采用适当增加管网流速或消毒频次加以弥补。