2012.12 零件切削加工(思考题)(刁可春存) Microsoft Word 文档
《材料加工成型原理》思考题参考答案
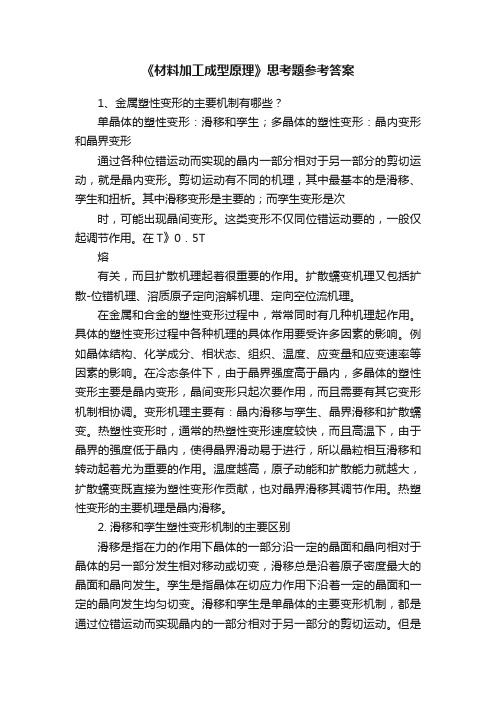
《材料加工成型原理》思考题参考答案1、金属塑性变形的主要机制有哪些?单晶体的塑性变形:滑移和孪生;多晶体的塑性变形:晶内变形和晶界变形通过各种位错运动而实现的晶内一部分相对于另一部分的剪切运动,就是晶内变形。
剪切运动有不同的机理,其中最基本的是滑移、孪生和扭析。
其中滑移变形是主要的;而孪生变形是次时,可能出现晶间变形。
这类变形不仅同位错运动要的,一般仅起调节作用。
在T》0.5T熔有关,而且扩散机理起着很重要的作用。
扩散蠕变机理又包括扩散-位错机理、溶质原子定向溶解机理、定向空位流机理。
在金属和合金的塑性变形过程中,常常同时有几种机理起作用。
具体的塑性变形过程中各种机理的具体作用要受许多因素的影响。
例如晶体结构、化学成分、相状态、组织、温度、应变量和应变速率等因素的影响。
在冷态条件下,由于晶界强度高于晶内,多晶体的塑性变形主要是晶内变形,晶间变形只起次要作用,而且需要有其它变形机制相协调。
变形机理主要有:晶内滑移与孪生、晶界滑移和扩散蠕变。
热塑性变形时,通常的热塑性变形速度较快,而且高温下,由于晶界的强度低于晶内,使得晶界滑动易于进行,所以晶粒相互滑移和转动起着尤为重要的作用。
温度越高,原子动能和扩散能力就越大,扩散蠕变既直接为塑性变形作贡献,也对晶界滑移其调节作用。
热塑性变形的主要机理是晶内滑移。
2. 滑移和孪生塑性变形机制的主要区别滑移是指在力的作用下晶体的一部分沿一定的晶面和晶向相对于晶体的另一部分发生相对移动或切变,滑移总是沿着原子密度最大的晶面和晶向发生。
孪生是指晶体在切应力作用下沿着一定的晶面和一定的晶向发生均匀切变。
滑移和孪生是单晶体的主要变形机制,都是通过位错运动而实现晶内的一部分相对于另一部分的剪切运动。
但是他们也明显的区别,如下:由孪生的变形过程可知,孪生所发生的切变均匀地波及整个孪生变形区,而滑移变形只集中在滑移面上,切变是不均匀的;孪生切变时原子移动的距离不是孪生方向原子间距的整数倍(而是几分之一原子间距),而滑移时原子移动的距离是滑移方向原子间距的整数倍;孪生变形后,孪晶面两边晶体位向不同,成镜像对称;而滑移时,滑移面两边晶体位向不变;由于孪生改变了晶体的取向,因此孪晶经抛光浸蚀后仍可观察到,而滑移所造成的台阶经抛光浸蚀后不会重现;孪生的临界分切应力要比滑移的临界分切应力大得多,常萌发于滑移受阻引起的局部应力集中区;孪生变形的速度极大,常引起冲击波,发出声响;滑移时全位错运动的结果,孪生是不全位错运动。
第四章 切削力 思考题
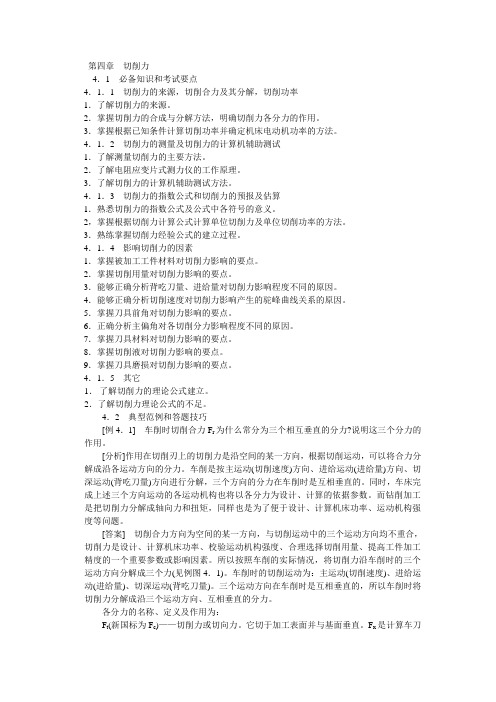
第四章切削力4.1 必备知识和考试要点4.1.1 切削力的来源,切削合力及其分解,切削功率1.了解切削力的来源。
2.掌握切削力的合成与分解方法,明确切削力各分力的作用。
3.掌握根据已知条件计算切削功率并确定机床电动机功率的方法。
4.1.2 切削力的测量及切削力的计算机辅助测试1.了解测量切削力的主要方法。
2.了解电阻应变片式测力仪的工作原理。
3.了解切削力的计算机辅助测试方法。
4.1.3 切削力的指数公式和切削力的预报及估算1.熟悉切削力的指数公式及公式中各符号的意义。
2,掌握根据切削力计算公式计算单位切削力及单位切削功率的方法。
3.熟练掌握切削力经验公式的建立过程。
4.1.4 影响切削力的因素1.掌握被加工工件材料对切削力影响的要点。
2.掌握切削用量对切削力影响的要点。
3.能够正确分析背吃刀量、进给量对切削力影响程度不同的原因。
4.能够正确分析切削速度对切削力影响产生的驼峰曲线关系的原因。
5.掌握刀具前角对切削力影响的要点。
6.正确分析主偏角对各切削分力影响程度不同的原因。
7.掌握刀具材料对切削力影响的要点。
8.掌握切削液对切削力影响的要点。
9.掌握刀具磨损对切削力影响的要点。
4.1.5 其它1.了解切削力的理论公式建立。
2.了解切削力理论公式的不足。
4.2 典型范例和答题技巧[例4.1] 车削时切削合力F r为什么常分为三个相互垂直的分力?说明这三个分力的作用。
[分析]作用在切削刃上的切削力是沿空间的某一方向,根据切削运动,可以将合力分解成沿各运动方向的分力。
车削是按主运动(切削速度)方向、进给运动(进给量)方向、切深运动(背吃刀量)方向进行分解,三个方向的分力在车削时是互相垂直的。
同时,车床完成上述三个方向运动的各运动机构也将以各分力为设计、计算的依据参数。
而钻削加工是把切削力分解成轴向力和扭矩,同样也是为了便于设计、计算机床功率、运动机构强度等问题。
[答案] 切削合力方向为空间的某一方向,与切削运动中的三个运动方向均不重合,切削力是设计、计算机床功率、校验运动机构强度、合理选择切削用量、提高工件加工精度的一个重要参数或影响因素。
数控加工技术实践课之思考题(doc 24页)
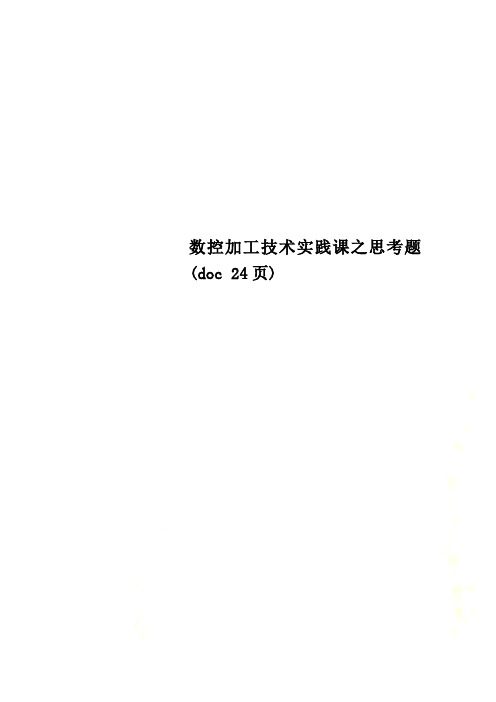
数控加工技术实践课之思考题(doc 24页)《数控加工技术》实践课思考题一.是非题(一)职业道德1.1.1(√)安全管理是综合考虑“物”的生产管理功能和“人”的管理,目的是生产更好的产品1.1.2(√)通常车间生产过程仅仅包含以下四个组成部分:基本生产过程、辅助生产过程、生产技术准备过程、生产服务过程。
1.1.3(√)车间生产作业的主要管理内容是统计、考核和分析。
1.1.4(√)车间日常工艺管理中首要任务是组织职工学习工艺文件,进行遵守工艺纪律的宣传教育,并例行工艺纪律的检查。
(二)基础知识1.2.1(×)当数控加工程序编制完成后即可进行正式加工。
1.2.2(×)数控机床是在普通机床的基础上将普通电气装置更换成CNC控制装置。
1.2.3(√)圆弧插补中,对于整圆,其起点和终点相重合,用R编程无法定义,所以只能用圆心坐标编程。
1.2.4(√)插补运动的实际插补轨迹始终不可能与理想轨迹完全相同。
1.2.5(×)数控机床编程有绝对值和增量值编程,使用时不能将它们放在同一程序段中。
1.2.6(×)用数显技术改造后的机床就是数控机床。
1.2.7(√)G代码可以分为模态G代码和非模态G代码。
1.2.8(×)G00、G01指令都能使机床坐标轴准确到位,因此它们都是插补指令。
1.2.9(√)圆弧插补用半径编程时,当圆弧所对应的圆心角大于180º时半径取负值。
1.2.10(×)不同的数控机床可能选用不同的数控系统,但数控加工程序指令都是相同的。
1.2.11(×)数控机床按控制系统的特点可分为开环、闭环和半闭环系统。
1.2.32(×)顺时针圆弧插补(G02)和逆时针圆弧插补(G03)的判别方向是:沿着不在圆弧平面内的坐标轴负方向向正方向看去,顺时针方向为G02,逆时针方向为G03。
1.2.33(√)伺服系统的执行机构常采用直流或交流伺服电动机。
[工学]加工精度的习题与思考题
![[工学]加工精度的习题与思考题](https://img.taocdn.com/s3/m/9b8aa18f50e79b89680203d8ce2f0066f4336443.png)
习题与思考题2—1 何谓加工精度、加工误差、公差?它们之间有什么区别?2—2车床床身导轨在垂直平面内及水平面内的直线度对车削轴类零件的加工误差有什么影响?影响程度各有何不同?2—3 试分析滚动轴承的外圈内滚道及内圈外滚道的形状误差(图2—64)所引起的主轴回转轴线的运动误差,它对被加工零件精度有什么影响?2—4 试分析在车床上加工时产生下述误差的原因:1)在车床上镗孔时,引起被加工孔圆度误差和圆柱度误差。
2)在车床三爪自定心卡盘上镗孔时,引起内孔与外圆不同轴度、端面与外圆的不垂直度。
2—5在车床上用两顶尖装夹工件车削细长轴时,出现图2—65所示误差是什么原因?分别采用什么办法来减少或消除?2—6 试分析在转塔车床上将车刀垂直安装加工外圆(图2-66)时,影响直径误差的因素中,导轨在垂直面内和水平面内弯曲,哪个影响大?与卧式车床比较有什么不同?为什么?2-7 在磨削锥孔时,用检验锥度的塞规着色检验,发现只在塞规中部接触或在塞规的两端接触(图2—67)。
试分析造成误差的各种因素。
2-8 如果被加工齿轮分度圆直径D=100mm,滚齿机滚切传动链中最后一个交换齿轮的分度圆直径d=200mm,分度蜗杆副的降速比为1:96,若此交换齿轮的齿距累积误差△F=0.12mm,试求由此引起的工件的齿距偏差是多少?2-9 设已知一工艺系统的误差复映系数为ε=0.25,工件在本工序前有圆柱度(椭圆度)0.45mm。
若本工序形状精度规定公差0.01mm,问至少进给几次方能使形状精度合格?2-10在车床上加工丝杠,工件总长为2650mm,螺纹部分的长度L=2000mm,工件材料和母丝杠材料都是45钢,加工时室温为20℃,加工后工件温升到45℃,母丝杠温升30℃。
试求工件全长上由于热变形引起的螺距累积误差。
2-11 横磨工件时(图2-68),设横向磨削力Fy=100N,主轴箱刚度k=5000N/mm,尾座刚度wz k=4000N/mm,加工工件zx尺寸如图2—68所示,求加工后工件的锥度。
机械零件课程设计思考题
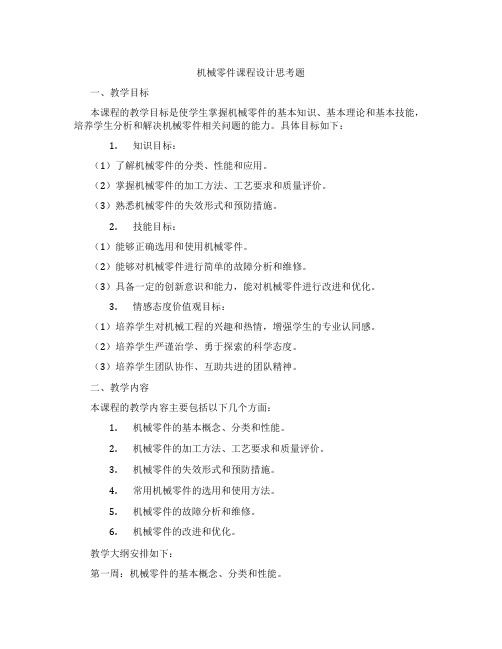
机械零件课程设计思考题一、教学目标本课程的教学目标是使学生掌握机械零件的基本知识、基本理论和基本技能,培养学生分析和解决机械零件相关问题的能力。
具体目标如下:1.知识目标:(1)了解机械零件的分类、性能和应用。
(2)掌握机械零件的加工方法、工艺要求和质量评价。
(3)熟悉机械零件的失效形式和预防措施。
2.技能目标:(1)能够正确选用和使用机械零件。
(2)能够对机械零件进行简单的故障分析和维修。
(3)具备一定的创新意识和能力,能对机械零件进行改进和优化。
3.情感态度价值观目标:(1)培养学生对机械工程的兴趣和热情,增强学生的专业认同感。
(2)培养学生严谨治学、勇于探索的科学态度。
(3)培养学生团队协作、互助共进的团队精神。
二、教学内容本课程的教学内容主要包括以下几个方面:1.机械零件的基本概念、分类和性能。
2.机械零件的加工方法、工艺要求和质量评价。
3.机械零件的失效形式和预防措施。
4.常用机械零件的选用和使用方法。
5.机械零件的故障分析和维修。
6.机械零件的改进和优化。
教学大纲安排如下:第一周:机械零件的基本概念、分类和性能。
第二周:机械零件的加工方法、工艺要求和质量评价。
第三周:机械零件的失效形式和预防措施。
第四周:常用机械零件的选用和使用方法。
第五周:机械零件的故障分析和维修。
第六周:机械零件的改进和优化。
三、教学方法本课程采用多种教学方法,以激发学生的学习兴趣和主动性:1.讲授法:用于传授基本概念、理论和方法。
2.案例分析法:通过分析实际案例,使学生更好地理解和掌握知识。
3.实验法:让学生亲自动手进行实验,培养学生的实践能力。
4.讨论法:引导学生进行分组讨论,提高学生的思考和表达能力。
四、教学资源本课程的教学资源包括:1.教材:《机械零件》,为学生提供系统、全面的知识体系。
2.参考书:提供更多的学习资料,帮助学生深入理解课程内容。
3.多媒体资料:通过图片、视频等形式,丰富学生的学习体验。
4.实验设备:为学生提供实践操作的机会,培养学生的实践能力。
机械制造技术基础课后部分习题及问题详解

12-2切削过程的三个变形区各有何特点?它们之间有什么关联?答:切削塑性金属材料时,刀具与工件接触的区域可分为3个变形区:①第一变形区(基本变形区):是切削层的塑性变形区,其变形量最大,常用它来说明切削过程的变形情况;②第二变形区(摩擦变形区):是切屑与前面摩擦的区域;③第三变形区(表面变形区):是工件已加工表面与后面接触的区域。
它们之间的关联是:这三个变形区汇集在切削刃附近,此处的应力比较集中而且复杂,金属的被切削层就在此处与工件基体发生分离,大部分变成切屑,很小的一部分留在已加工表面上。
2-3分析积屑瘤产生的原因及其对加工的影响,生产中最有效的控制积屑瘤的手段是什么?答:在中低速切削塑性金属材料时,刀—屑接触表面由于强烈的挤压和摩擦而成为新鲜表面,两接触表面的金属原子产生强大的吸引力,使少量切屑金属粘结在前刀面上,产生了冷焊,并加工硬化,形成瘤核。
瘤核逐渐长大成为积屑瘤,且周期性地成长与脱落。
积屑瘤粘结在前刀面上,减少了刀具的磨损;积屑瘤使刀具的实际工作前角大,有利于减小切削力;积屑瘤伸出刀刃之外,使切削厚度增加,降低了工件的加工精度;积屑瘤使工件已加工表面变得较为粗糙。
由此可见:积屑瘤对粗加工有利,生产中应加以利用;而对精加工不利,应以避免。
消除措施:采用高速切削或低速切削,避免中低速切削;增大刀具前角,降低切削力;采用切削液。
2-7车削时切削合力为什么常分解为三个相互垂直的分力来分析?分力作用是什么?答:(1)车削时的切削运动为三个相互垂直的运动:主运动(切削速度)、进给运动(进给量)、切深运动(背吃刀量),为了实际应用和方便计算,在实际切削时将切削合力分解成沿三个运动方向、相互垂直的分力。
(2)各分力作用:切削力是计算车刀强度、设计机床主轴系统、确定机床功率所必须的;进给力是设计进给机构、计算车刀进给功率所必需的;背向力是计算工件挠度、机床零件和车刀强度的依据,与切削过程中的振动有关。
机械切削加工课后习题答案
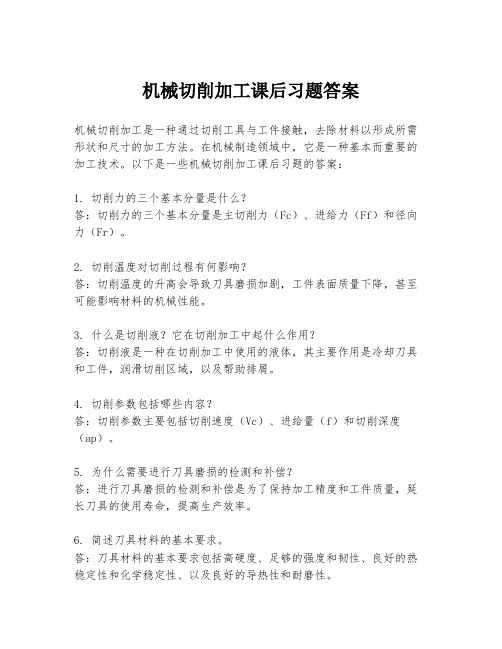
机械切削加工课后习题答案机械切削加工是一种通过切削工具与工件接触,去除材料以形成所需形状和尺寸的加工方法。
在机械制造领域中,它是一种基本而重要的加工技术。
以下是一些机械切削加工课后习题的答案:1. 切削力的三个基本分量是什么?答:切削力的三个基本分量是主切削力(Fc)、进给力(Ff)和径向力(Fr)。
2. 切削温度对切削过程有何影响?答:切削温度的升高会导致刀具磨损加剧,工件表面质量下降,甚至可能影响材料的机械性能。
3. 什么是切削液?它在切削加工中起什么作用?答:切削液是一种在切削加工中使用的液体,其主要作用是冷却刀具和工件,润滑切削区域,以及帮助排屑。
4. 切削参数包括哪些内容?答:切削参数主要包括切削速度(Vc)、进给量(f)和切削深度(ap)。
5. 为什么需要进行刀具磨损的检测和补偿?答:进行刀具磨损的检测和补偿是为了保持加工精度和工件质量,延长刀具的使用寿命,提高生产效率。
6. 简述刀具材料的基本要求。
答:刀具材料的基本要求包括高硬度、足够的强度和韧性、良好的热稳定性和化学稳定性、以及良好的导热性和耐磨性。
7. 什么是硬质合金刀具?它有哪些优点?答:硬质合金刀具是一种以碳化钨(WC)为主要成分,加入一定比例的钴(Co)作为粘合剂,通过粉末冶金工艺制成的刀具材料。
其优点包括高硬度、高耐磨性、高抗压强度和良好的热硬性。
8. 什么是数控切削?与传统切削相比有哪些优势?答:数控切削是指通过数控系统控制机床,按照预先编制的程序自动完成切削加工的过程。
与传统切削相比,数控切削具有加工精度高、加工效率高、加工范围广、适应性强等优势。
9. 简述刀具几何参数对切削过程的影响。
答:刀具几何参数包括前角、后角、刃倾角、主偏角和副偏角等。
这些参数会影响切削力的大小、切削温度的分布、切屑的形成和排出,以及工件的表面质量。
10. 如何选择切削用量以优化切削过程?答:选择切削用量时,应考虑工件材料、刀具材料、机床性能、加工精度要求等因素。
机械制造技术基础(第二版)第二章思考题

思考题1.切削用量都包含什么?车削外圆时,与工件转速和切削层参数是何关系?2.分析用麻花钻在钻床上钻孔时的主运动、进给运动、工件上的加工表面和麻花钻切削部分的基本组成。
3.在车床上切断工件,采用正交平面参考系标注切断刀的参考平面和刀具角度。
4.试述刀具的标注角度和工作角度的区别。
为什么横向切削时,进给量不能太大?5.试分析钻孔时的切削厚度、切削宽度及其与进给量、背吃刀量的关系。
6.按结构形式,刀具可分为哪几种?7.孔加工刀具分几类?都有哪些刀具?8.高速钢、硬质合金、陶瓷、金刚石、立方氮化硼各有何性能特点?适用于何处?9.试分析加工不锈钢、奥氏体钢、淬硬钢、高锰钢、钛合金时刀具材料的选择。
10.按下列条件选择刀具材料类型或牌号:1)45钢锻件粗车;2)齿轮滚刀;3)HT200铸件精车;4)低速精车合金钢蜗杆;5)高速精车调质钢长轴;6)高速精密镗削铝合金缸套;7)中速车削淬硬钢轴;8)加工65HRC冷硬铸铁;9)麻花钻;10)高速精车铜套。
11.切削过程的三个变形区各有何特点?第一变形区的变形大小可什么参数衡量?12.切屑与前刀面的摩擦对第一变形区的剪切变形有何影响?13.剪切角与前刀面摩擦角和刀具前角是何关系关系?14.前刀面上的摩擦分哪两个区域?应力如何分布?15.分析积屑瘤产生的原因及其对生产的影响。
16.切屑分哪几类?什么条件下产生?17.金属切削过程中为什么会产生切削力?18.车削时切削合力为什么常分解为三个相互垂直的分力来分析?试说明三个分力的作用。
19.如何按照单位切削力估算切削力和切削功率?20.各个因素影响切削力的原因分析,特别是背吃刀量和进给量对切削力的影响。
21.切削热是如何产生和传出的?仅从切削热产生的多少能否说明切削区温度的高低?22.切削温度的含义是什么?它在刀具上是如何分布的?它的分布和三个变形区有何联系?23.背吃刀量和进给量对切削力和切削温度的影响是否一样?为什么?如何运用这一规律指导生产实践?24.增大前角可以使切削温度降低的原因是什么?是不是前角越大切削温度越低?25.加工钢料等塑性材料和加工铸铁等脆性材料时,前刀面和后刀面上的温度哪个高?26.何谓粘结磨损与扩散磨损?影响它们的主要因素是什么?27.刀具的磨损过程可分为几个阶段?各阶段的特点是什么?刀具的磨损应限制在哪一阶段?28. 什么是刀具的磨钝标准?什么是刀具耐用度?刀具耐用度与磨钝标准有什么关系?磨钝标准确定后,刀具耐用度是否就确定了?为什么?29. 切削用量对刀具磨损有何影响?在0m vT C 关系中,指数m 的物理意义是什么?不同刀具材料的m 值为什么不同?30. 为什么最低成本耐用度会大于最高生产率耐用度?31. 工件材料切削加工性为什么是相对的?用什么指标来衡量工件材料切削加工性?怎样评价工件材料切削加工性?32. 相对加工性的大小代表什么?33. 怎样通过分析影响工件材料切削加工性的因素,来探讨改善工件材料切削加工性的途径?34. 前角、后角、主偏角的功用和选择的主要依据是什么?35. 为什么适当增大后角可提高刀具耐用度?36. 试说明在下列不同情况下刀具几何参数的选择有何不同:1)加工灰铸铁和一般碳素结构钢;2)加工不锈钢和中碳钢;3)加工高硬度高强度钢和中碳钢。
- 1、下载文档前请自行甄别文档内容的完整性,平台不提供额外的编辑、内容补充、找答案等附加服务。
- 2、"仅部分预览"的文档,不可在线预览部分如存在完整性等问题,可反馈申请退款(可完整预览的文档不适用该条件!)。
- 3、如文档侵犯您的权益,请联系客服反馈,我们会尽快为您处理(人工客服工作时间:9:00-18:30)。
思考题
1-1 什么是生产过程、工艺过程、工艺规程?工艺规程在生产是有何作用?
1-2 什么是工序、安装、工位、工步?
1-3 如何划分生产类型?各种生产类型的工艺特征是什么?
1-4 在加工中可时间定额组成有哪些?p51
1-5 什么是零件的结构工艺性?影响因素有哪些?
1-6 何谓设计基准、定位基准、工序基准、测量基准、装配基准,并举例说明。
1-7 精基准、粗基准的选择原则有哪些?
1-8 何谓六点定位原理p104、完全定位、不完全定位、欠定位、过定位,p105 p106并举例说明。
1-9夹紧装置的组成及基本要求p114。
确定夹紧力的三要素:大小、方向和作用点原则p115
1-10 试述在零件加工过程中,划分加工阶段的目的和原则。
P40
1-11 试叙述零件在机械加工工艺过程中,安排热处理工序的目的、常用的热处理方法及其在工艺过程中安排的位置。
1-12 试分析机床夹具的组成。
P102
1-14何谓机械加工精度、机械加工质量p219、分析影响加工精度的因素?p221 1-15 什么是工艺尺寸链、封闭环、增环、减环?p46
1-16 机械加工表面质量包括的内容是什么?p234
1-17 保证和提高加工精度的主要途径?p231
1-18表面质量对零件使用性能的影响是什么?p234
1-19影响表面质量的工艺因素有哪些?p236
1-20典型夹紧机构有哪些?特征是什么p117。