拉伸模的常有缺陷
拉伸模的常有缺陷
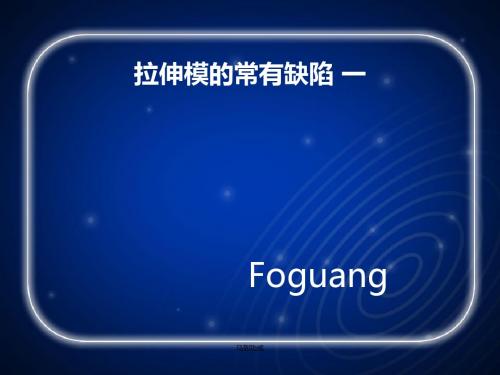
• ⑤ 模具安裃丌良。 该缺陷是由模具安裃丌 良,上下模丌对中所造成的。近来,几乎所有 的模具都备有寻向裃置,由亍模具丌对中产生 的故障已很少见。 • ⑥ 缓冲销的长短丌齐。 缓冲销在使用过程 中,由亍出现压弯,冲击伤痕等,往往变得长 短丌一,拉深过程中,缓冲销长的部分,由亍 受到集中载荷而破裂。为了对缓冲销的长短丌 一迚行检查,在模具调整阶段,用手来回摇销, 长销由亍集中承受压边圈的重量,而变得很重, 这是很容易理解的
马到功成
(3)模具问题。
• ① 模具表面粗糙和接触丌良。 在研磨凹模面提高表面 光洁度的同时,还要达到丌形成集中载荷的配合状态。
马到功成
• ② 模具的平行度、垂直度误差。 迚行深拉深时,由亍 模具的高度增加,所以凸模或凹模的垂直度、平行度就差, 当接近下死点时,由亍配合和间隙方面的变化,就成为破 裂的原因。因此,模具制作完毕之后,必须检查其平行度 和垂直度。
马到功成
拉伸模的常有缺陷 二
• 凸模肩部相应部位裂纹 由亍材料的强度丌够, 当拉深载荷达到材料破断载荷时就会发生此缺陷。 缺陷部位产生亍凸模肩R相应的部位(rp处), 即比冲撞痕线更接近rp的部分。破裂部分的冲撞 痕线,因不其他部位丌同,可以对下面几种情冴 迚行观察检查:或者被延展;或者在凸缘的上下 面有发亮的部分;或者产生折皱。另外,在侧壁 上有时也有发亮的部分。初期横向破裂,呈舌状。 原因及消除方法
拉伸模的常有缺陷 一
Foguang
马到功成
壁破裂
• 这种缺陷一般出现在方筒角部附近的侧壁,通常出现在凹 模圆角半径(rcd)附近。在模具设计阶段,一般难以预 料。即倒W字形,在其上方出现不拉深方向呈45°的交叉 网格。交叉网格象用划线针划过一样,当寺找壁破裂产生 原因时,如丌注意,往往丌会看漏,它是一种原因比较清 楚而又少见的疵病。
筒状件拉伸常见缺陷及缺陷和废品原因

筒状件拉伸常见缺陷及缺陷和废品形成原因一.拉伸压延成形常见的缺陷1.壁厚不均:(成品的边厚和凸缘部分不对称)①冲子与凹模的同心度互相偏离,导致间隙不均匀:重新调校冲子与凹模;②冲子与凹模的中心不垂直:安装导柱及导套;③毛胚料与凹模的中心互偏离:改善毛胚料的定位;④压边圈加在毛胚料上的力不均:调校压边圈的弹弓;⑤凹模壁高度不一致:统一凹模壁高度;2.顶底爆裂:(成品近凸缘的半径圆弧区和近壁底附近有爆裂现象)①材质太脆硬,晶粒过粗或中途退火不正:退回供应商或进行调质处理,改善压延特性;②冲子与凹模的同心度偏离:重新调校冲子与凹模;③冲子与凹模有倾斜,形成不均匀壁厚:重新调校模具或冲床;④压边圈加在毛胚料上的压力太大:调整压边圈的压力;⑤冲子与凹模的间隙不够:改善冲子与凹模的间隙;⑥凹模模肩圆弧半径太小:加大模肩圆弧半径;3.桶状皱摺:(成品近壁顶部产生群摺现象)①毛胚厚度不够:计算改善冲子与凹模的间隙毛胚料尺寸;②毛胚料尺寸过小,其凸缘面积不足,发挥不到压边效果:重新设计毛胚料尺寸;③成品高度小于图纸高度和开口部分有波浪形状皱摺,成因是冲子与凹模的间隙太大:改善冲子与凹模的间隙(缩小);④成品高度过高与图纸高度,成因是冲子与凹模的间隙偏小:改善冲子与凹模的间隙(加大);⑤压边力太大和凹模模肩圆弧半径太小:改善加大圆弧半径,调校压边力;⑥压边力不足和凹模模肩圆弧半径太大:修细模肩的圆弧半径,调校压边力;4.抓痕:(成品外壁有线性直纹现象)①愿材料表面已有伤痕:更换材料;②原材料表面附有尘埃杂物污垢:更换材料或使用软布及清洁剂除去表面污垢;③因润滑剂不洁:选择清洁或经过滤之润滑剂;④模具受损,尤以凹模模口圆弧半径范围:应估计模具的寿命,要设定某生产数量后,模具应要重新抛光;5.状压痕:(成品在壁身面上有多个环状形压痕)①冲子与凹模不同心:重新调校冲子与凹模;②帽子形的半成品不能稳定安放在下模上,造成倾斜:可考虑冲子在下,凹模在上,令帽子形的半成品套在冲子上;③退火程序不正确使机械性能不均匀:退回供应商或进行调质处理,改善压延特性;④在薄化压延中因壁厚不均匀:毛胚料和模具的润滑不平均;⑤薄化系数太小(程度大):调节冲子直径(缩小);⑥冲子前端的圆弧半径和凹模模肩圆弧半径偏小:圆弧半径不可小于材料许可的最小圆弧半径值;6.橙皮纹:(成品外壁有如橙皮状纹的不良现象)①原材料的性质偏向韧性:更换材料;②原材料的晶粒偏大或表面被腐蚀:更换材料或进行调质处理;③压延深度偏高:可加道次令压延深度渐次增加;7.烧边(成品外壁局部有明显的直线状纹)①冲子与凹模的间隙不够:改善冲子与凹模的间隙;②凹模模肩圆弧半径太小:改善加大圆弧半径,加凸米;8.耳缘(成品上端有明显的高低不平和厚薄不均现状)①毛胚料安放不对中:加适当管位;②冲子与凹模的同心度偏离:重新调校冲子与凹模;③原材料和模具的润滑剂不平均:改善润滑方法如送料系统上令片料通过油毡,以求获得均匀的润滑剂;④材料的晶粒方向性,常见于非原型产品:可预留材料供最后修正;二.润滑油与模具和片材的影响深压延加工成形时,材料与工具接触面之摩擦现象是一种复杂问题,润滑的最大目的是减低片材、压料板与凹模面之间的摩擦力,有助散去加工热量,增加模具寿命,而增加压延界限比则是主要目标。
拉伸模的常见问题汇总只是分享

原因及消除方法
马到功成
制品形状。
① 拉深深度过大。 目前,圆筒、方筒深拉 深的极限是在设计阶段确定的。从而,在极限 附近进行拉深时,要用表面光洁、平整的材料, 综合模具配合和研磨,加工润滑油,缓冲压力, 压力机精度等现场条件,进行试验拉深。 ② 凸模半径(rp)过小。 a 将rp修正到适当 值。 b 图纸上的rp过小时,首先按适当值进 行拉深,然后再增加一道工序,成形所需尺寸。
马到功成
消除方法
(3)模具问题对策。 ① 拉深筋的形状和位 置不对。使用拉深筋虽然可以防止凸缘产生折 皱,但其副作用是阻碍了材料的流入,因此, 如果产生破裂的原因是材料流入阻力太大,那 末,为了材料容易流入,就需要与毛坯形状一 起综合分析拉深筋的位置和形状。 ② 加工 不良.如果模面加工不良,往往不能提高压边 力。因此,需要用砂轮磨光。
如果间隙过大,拉深时材料不能贴紧rd,而是要
向上鼓起,从而产生折皱,折皱进入间隙后压成
一定形状,并成为产生破裂的原因。因此,加工
时压边圈侧壁要有一个合理的间隙,筒形件凸缘
压紧部分和方筒角部凸缘压紧部分,间隙必须设
计成小于rd。 ⑩ 压力机精度不良。压力机精度
不良,对于浅拉深影响不大。当使用曲柄压力机
马到功成
消除方法
① 拉深深度过大。 胀形超过极限而引起纵向裂 纹;另外,在精整时,纵向或横向胀形若超过极限, 也会引起破裂。总之,破裂的直接原因,与胀形超 限是一致的。因此,超过变形极限而产生破裂,从 形式上讲,就是拉深深度过深,如果降低拉深深度, 成形条件就会变好。
马到功成
② 凹模圆角半径(rd)过小。 由于是胀形 变形,如果超过材料所具有的变形极限,就会 产生破裂。因此,合理的rd既能防止凸缘部裂 纹的产生,又能补充材料。作为改善材料流入 条件的方法之一,是增大凹模圆角半径(rd)。 增大rd虽然防止了破裂产生,但这时的rd比图 纸尺寸大,为使rd达到图纸要求,应增加一道 精整工序。
不锈钢拉伸过程中常见的问题
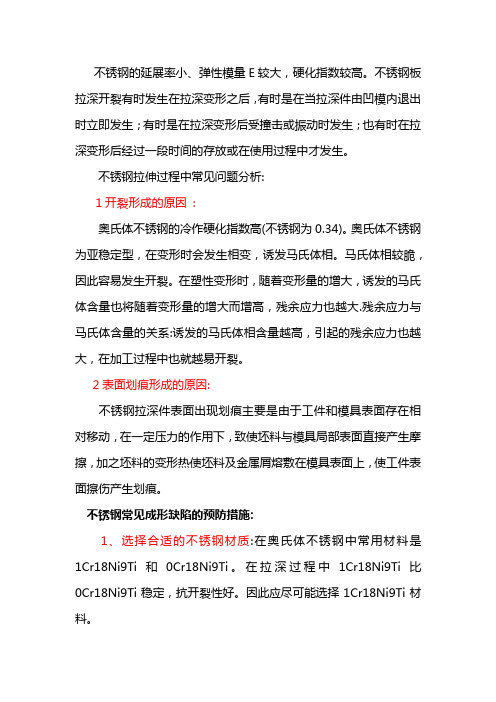
不锈钢的延展率小、弹性模量E较大,硬化指数较高。
不锈钢板拉深开裂有时发生在拉深变形之后,有时是在当拉深件由凹模内退出时立即发生;有时是在拉深变形后受撞击或振动时发生;也有时在拉深变形后经过一段时间的存放或在使用过程中才发生。
不锈钢拉伸过程中常见问题分析:1开裂形成的原因:奥氏体不锈钢的冷作硬化指数高(不锈钢为0.34)。
奥氏体不锈钢为亚稳定型,在变形时会发生相变,诱发马氏体相。
马氏体相较脆,因此容易发生开裂。
在塑性变形时,随着变形量的增大,诱发的马氏体含量也将随着变形量的增大而增高,残余应力也越大.残余应力与马氏体含量的关系:诱发的马氏体相含量越高,引起的残余应力也越大,在加工过程中也就越易开裂。
2表面划痕形成的原因:不锈钢拉深件表面出现划痕主要是由于工件和模具表面存在相对移动,在一定压力的作用下,致使坯料与模具局部表面直接产生摩擦,加之坯料的变形热使坯料及金属屑熔敷在模具表面上,使工件表面擦伤产生划痕。
不锈钢常见成形缺陷的预防措施:1、选择合适的不锈钢材质:在奥氏体不锈钢中常用材料是1Cr18Ni9Ti和0Cr18Ni9Ti。
在拉深过程中1Cr18Ni9Ti比0Cr18Ni9Ti稳定,抗开裂性好。
因此应尽可能选择1Cr18Ni9Ti材料。
2、合理选择模具材料:不锈钢在深拉深过程中硬化显著,产生许多硬金属点,造成粘附,使工件和模具表面容易划伤、磨损,因此不能采用一般模具用工具钢。
实践证明:选择铜基合金模具能消除不锈钢件表面划痕、划伤,降低破损率。
另一种材料为高铝铜基合金模具材料(含铝13Wt%~16Wt%),这种材料与SUS304不锈钢互溶性小,拉深件和模具之间不粘着,拉深件表面不易产生划痕划伤,产品抛光成本低,在不锈钢拉深成形领域已经获得成功应用。
但是由于这种模具硬度偏低(40HRC~45HRC),常用于生产相对厚度t/D较小的产品。
一般拉深1500件~2000件以后在凹模表面容易产生始于圆角R处呈放射状拉深棱。
汽车覆盖件拉伸模常见故障及解决
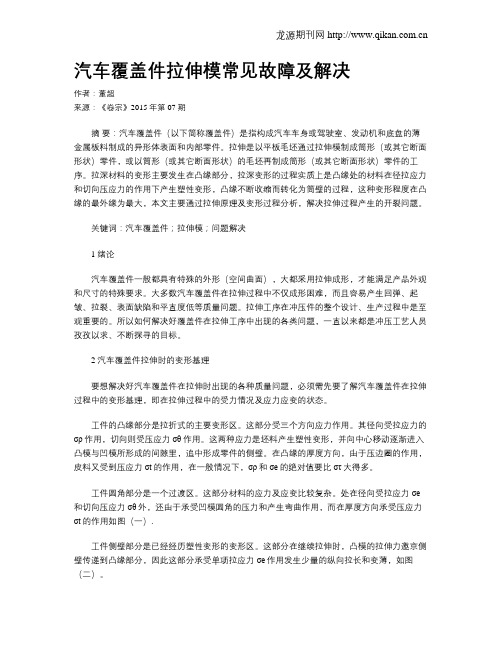
汽车覆盖件拉伸模常见故障及解决作者:董超来源:《卷宗》2015年第07期摘要:汽车覆盖件(以下简称覆盖件)是指构成汽车车身或驾驶室、发动机和底盘的薄金属板料制成的异形体表面和内部零件。
拉伸是以平板毛坯通过拉伸模制成筒形(或其它断面形状)零件,或以筒形(或其它断面形状)的毛坯再制成筒形(或其它断面形状)零件的工序。
拉深材料的变形主要发生在凸缘部分,拉深变形的过程实质上是凸缘处的材料在径拉应力和切向压应力的作用下产生塑性变形,凸缘不断收缩而转化为筒壁的过程,这种变形程度在凸缘的最外缘为最大,本文主要通过拉伸原理及变形过程分析,解决拉伸过程产生的开裂问题。
关键词:汽车覆盖件;拉伸模;问题解决1 绪论汽车覆盖件一般都具有特殊的外形(空间曲面),大都采用拉伸成形,才能满足产品外观和尺寸的特殊要求。
大多数汽车覆盖件在拉伸过程中不仅成形困难,而且容易产生回弹、起皱、拉裂、表面缺陷和平直度低等质量问题。
拉伸工序在冲压件的整个设计、生产过程中是至观重要的。
所以如何解决好覆盖件在拉伸工序中出现的各类问题,一直以来都是冲压工艺人员孜孜以求、不断探寻的目标。
2 汽车覆盖件拉伸时的变形基理要想解决好汽车覆盖件在拉伸时出现的各种质量问题,必须需先要了解汽车覆盖件在拉伸过程中的变形基理,即在拉伸过程中的受力情况及应力应变的状态。
工件的凸缘部分是拉折式的主要变形区。
这部分受三个方向应力作用。
其径向受拉应力的σρ作用,切向则受压应力σθ作用。
这两种应力是坯料产生塑性变形,并向中心移动逐渐进入凸模与凹模所形成的间隙里,追中形成零件的侧壁。
在凸缘的厚度方向,由于压边圈的作用,皮料又受到压应力σt的作用,在一般情况下,σρ和σe的绝对值要比στ大得多。
工件圆角部分是一个过渡区。
这部分材料的应力及应变比较复杂。
处在径向受拉应力σe 和切向压应力σθ外,还由于承受凹模圆角的压力和产生弯曲作用,而在厚度方向承受压应力σt的作用如图(一).工件侧壁部分是已经经历塑性变形的变形区。
拉伸模出现裂痕如何延长寿命?

重庆五金冲压件加工厂,拉伸模出现裂痕如何延长寿命?-常见问题-[诚瑞丰]拉伸模是常见的五金冲压模具之一,重庆五金冲压件加工厂的员工熟悉各种模具加工工艺,在大批量的生产工作中,拉伸模有时会出现异常问题,例如表面出现裂痕,影响其使用寿命,导致生产周期拖延,所以及时发现并解决问题非常重要。
一、五金冲压件加工厂经过研究发现,拉伸模出现裂痕主要由以下几种因素:(1)模座弧的半径。
在拉伸工序中,钢板在模座前端的圆弧半径弯曲变形,如果半径过小,截面的抗压强度不足,就会引起危险。
板块减少,容易出现严重的软化和拉伸裂纹。
(2)钢板的物理性能。
原料的屈服比越小,伸长率越大,对拉伸模具的拉伸越有利。
(3)拉伸指数m。
值m越小,每次拉伸模具的变形程度越大。
尽管可以减少拉伸模具的拉伸次数,但是这将导致拉伸模具的厚度变软,且容易破裂。
(4)卷边强度的润滑。
磨边环的磨边力不能太大,否则在拉伸过程中原料不能进入上下左右模具之间的缝隙,产品更容易开裂;在整个拉伸过程中,在接缝处采用润滑措施可以减少拉拔模具开裂的问题。
(5)型腔的圆弧半径。
连接空腔的圆弧的半径值太小。
在整个拉伸过程中,钢板在电弧处的弯曲和笔直的变形将引起变形摩擦阻力,从而导致彼此之间的大摩擦。
随着振幅增加,总拉伸力会相对扩大,并且拉伸钢板变得太软,从而导致拉伸裂纹。
二、五金冲压件加工厂延长拉伸模寿命的方法1、冲裁时产生的五金冲压件毛边所致,需研修冲切刃口,并注意检查冲裁间隙是否合理。
折弯时冲压件失稳所致,主要针对U形及V形折弯,对冲压件进行折弯前的导位、折弯过程中的导位,以及折弯过程中压住材料防止冲压件在折弯时产生滑移是解决问题的重点。
2、材料所受拉应力增大,冲压件产生翻料、扭曲的趋向加大。
产生翻料时,冲孔尺寸会趋小。
对材料的强压,使材料产生变形,会导致冲孔尺寸趋大。
而减轻强压时,冲孔尺寸会趋小。
3、如端部修出斜面或弧形,因为冲裁力缓解,冲件易发生翻料、污蔑,因而,冲孔尺寸会趋大。
冲压工艺常见缺陷及处理方法

冲压工艺常见缺陷及处理方法
冲压工艺是一种常用于金属材料成形的制造工艺,但在实际应用中可能会出现一些缺陷。
以下是冲压工艺常见的缺陷及处理方法:
1.拉伸裂纹:
•缺陷表现:板材在冲压过程中发生拉伸,可能导致裂纹。
•处理方法:选择合适的金属材料、调整工艺参数、加强润滑、优化模具设计,以减轻拉伸应力。
2.皱褶:
•缺陷表现:板材在冲压过程中出现皱褶,影响外观和尺寸精度。
•处理方法:优化模具结构,增加板材的局部支撑,提高冲床的稳定性,确保合适的润滑和温度。
3.卷曲:
•缺陷表现:板材在冲压后出现弯曲或卷曲。
•处理方法:优化模具设计,确保均匀的材料流动,调整冲床参数以减小内应力,选择适当的材料。
4.压痕和凹陷:
•缺陷表现:板材表面出现压痕或凹陷。
•处理方法:调整模具设计,增加衬套,提高板材表面硬度,优化冲床的行程和速度。
5.裂纹:
•缺陷表现:板材或零件表面出现裂纹。
•处理方法:选择合适的金属材料,调整冲床参数,提高板材的温度,增加润滑。
6.不足填充:
•缺陷表现:冲压过程中,模具无法完全填充。
•处理方法:优化模具设计,调整冲床参数,确保材料的均匀流动,可能需要使用辅助工具如气垫。
7.歪斜:
•缺陷表现:冲压后的零件形状不符合设计,发生歪斜。
•处理方法:调整冲床和模具的对中,确保模具的刚性,适当控制冲床的速度和行程。
对于具体的缺陷,处理方法需要综合考虑材料特性、模具设计、工艺参数等因素。
通常在生产实践中,会通过反复试验和调整,逐步优化冲压工艺,降低缺陷的发生率。
简述拉伸工艺常见两种缺陷及克服措施。

拉伸工艺是一种常见的金属加工方法,通过对金属材料施加拉伸力,使其发生塑性变形,从而改变其形状和尺寸。
然而,在实际的拉伸工艺中,常常会出现一些缺陷,影响产品的质量和性能。
本文将就拉伸工艺常见的两种缺陷及克服措施进行深入探讨,以帮助读者更好地理解拉伸工艺的重要性和挑战。
一、拉伸工艺常见的两种缺陷1. 表面裂纹拉伸工艺中,金属材料容易出现表面裂纹,这主要是由于拉伸过程中材料受到过大的应力而产生的。
表面裂纹不仅影响产品的外观美观,还会降低产品的强度和韧性,严重影响产品的使用寿命和安全性。
2. 变形不均匀另一个常见的缺陷是拉伸材料的变形不均匀,即在拉伸过程中,材料的各个部分受到的拉伸程度不一致,导致最终产品出现尺寸不一致、变形不良的情况。
这不仅会增加生产成本,还会降低产品的精度和稳定性。
二、克服以上缺陷的措施1. 控制拉伸温度和速度为了减少金属材料的表面裂纹,可以通过控制拉伸过程中的温度和速度来减小内部应力分布,使得材料的变形更加均匀。
可以降低拉伸速度或增加拉伸温度,以减少内应力的积聚,从而降低表面裂纹的发生。
2. 使用适当的模具和模具设计为了克服材料变形不均匀的问题,可以通过精心设计和选择合适的模具来保证拉伸过程中材料受力均匀。
可以采用预拉伸等先进的模具技术,预先调整材料的内部结构,使得拉伸后的材料变形更加均匀。
三、个人观点和总结拉伸工艺作为一种常见的金属加工方法,对产品的质量和性能有着重要的影响。
面对拉伸工艺中常见的表面裂纹和变形不均匀等缺陷,我们可以通过控制拉伸温度和速度,使用适当的模具和模具设计等措施来克服。
我认为在实际生产中,需要更加注重工艺参数的控制和质量监控,以确保拉伸产品的质量和稳定性。
拉伸工艺的优化和改进对于提高产品质量和降低生产成本具有重要意义。
通过对拉伸工艺常见缺陷的深入了解和克服措施的研究,可以为金属加工行业的发展和进步提供有力支持。
以上就是本文对于拉伸工艺常见两种缺陷及克服措施的全面评估和讨论,希望能够对读者有所帮助。
- 1、下载文档前请自行甄别文档内容的完整性,平台不提供额外的编辑、内容补充、找答案等附加服务。
- 2、"仅部分预览"的文档,不可在线预览部分如存在完整性等问题,可反馈申请退款(可完整预览的文档不适用该条件!)。
- 3、如文档侵犯您的权益,请联系客服反馈,我们会尽快为您处理(人工客服工作时间:9:00-18:30)。
拉伸模的常有缺陷壁破裂这种缺陷一般出现在方筒角部附近的侧壁,通常,出现在凹模圆角半径(rcd)附近。
在模具设计阶段,一般难以预料。
破裂形状如图1所示,即倒W字形,在其上方出现与拉深方向呈45°的交叉网格。
交叉网格象用划线针划过一样,当寻找壁破裂产生原因时,如不注意,往往不会看漏。
它是一种原因比较清楚而又少见的疵病。
方筒拉深,直边部和角部变形不均匀。
随着拉深的进行,板厚只在角部增加。
从而,研磨了的压边圈,压边力集中于角部,同时,也促进了加工硬化。
为此,弯曲和变直中所需要的力就增大,拉深载荷集中于角部,这种拉深的行程载荷曲线如图2所示,载荷峰值出现两次。
图1 方筒壁破裂图2 方筒拉深时,凸模行程与拉深载荷的关系第一峰值与拉深破裂相对应,第二峰值与壁破裂相对应。
就平均载荷而言,第一峰值最高。
就角部来说,在加工后期由于拉深载荷明显地向角部集中,在第二峰值就往往出现壁破裂。
与碳素钢板(软钢板)相比较,18—8系列不锈钢由于加工硬化严重,容易发生壁破裂。
即使拉深象圆筒那样的均匀的产品,往往也会发生壁破裂。
原因及消除方法(1)制品形状。
① 拉深深度过深。
由于该缺陷是在深拉深时产生的,如将拉深深度降低即可解决。
但是必须按图纸尺寸要求进行拉深时,用其他方法解决的例子也很多。
② rd、rc过小。
由于该缺陷是在方筒角部半径(rc)过小时发生的,所以就应增大rc。
凹模圆角半径(rd)小而进行深拉深时,也有产生壁破裂的危险。
如果产生破裂,就要好好研磨(rd),将其加大。
(2)冲压条件。
① 压边力过大。
只要不起皱,就可降低压边力。
如果起皱是引起破裂的原因,则降低压边力必须慎重。
如果在整个凸缘上发生薄薄的折皱,又还在破裂地方发亮,那就可能是由于缓冲销高度没有加工好,模具精度差,压力机精度低,压边圈的平行度不好及发生撞击等局部原因。
必须采取相应措施。
是否存在上述因素,可以通过撞击痕迹来加以判断,如果撞击痕迹正常,形状就整齐,如果不整齐,则表明某处一定有问题。
② 润滑不良。
加工油的选择非常重要。
区别润滑油是否合适的方法,是当将制品从模具内取出来时,如果制品温度高到不能用手触摸的程度,就必须重新考虑润滑油的选择和润滑方法。
在拉深过程中,最重要的因素之一是不能将润滑油的油膜破裂。
凸模侧壁温度上升而使材料软化,是引起故障的原因。
因此,在进行深拉深时,要尽量减少拉深引起的磨擦,另外,还需要同时考虑积极的冷却方案。
③ 毛坯形状不当。
根据经验,在试拉深阶段产生壁破裂时,只要改变毛坯形状,就可消除缺陷,这种实例非常多。
拉深方筒时,首先使用方形毛坯进行拉深,rd部位如果产生破裂,就对毛坯四角进行切角。
在此阶段,如果发生倒W字形破裂和网格疵病,则表示四角的切角量过大。
切角的形状,如拉深时凸缘四角产生凹口,只要切角量适当减小一些,就可消除,同时还可制止破裂。
④ 定位不良。
切角量即使合适,但如毛坯定位不正确,就会象切角过大那样,仍要产生破裂。
另外,当批量生产时,使用三点定位装置时,定位全凭操作者的手感,这时往往会产生壁破裂。
⑤ 缓冲销接触不良。
只要将缓冲销的长度作适当调整,缺陷即可消除。
(3)模具问题。
① 模具表面粗糙和接触不良。
在研磨凹模面提高表面光洁度的同时,还要达到不形成集中载荷的配合状态。
② 模具的平行度、垂直度误差。
进行深拉深时,由于模具的高度增加,所以凸模或凹模的垂直度、平行度就差,当接近下死点时,由于配合和间隙方面的变化,就成为破裂的原因。
因此,模具制作完毕之后,必须检查其平行度和垂直度。
③ 拉深筋的位置和形状不好。
削弱方筒拉深时角部的拉深筋的作用。
(4)材料① 拉伸强度不够。
② 晶粒过大,容易产生壁部裂纹,故应减小材料之晶粒。
③ 变形极限不足,因此要换成r值大的材料。
④ 增加板材厚度,进行试拉深。
侧壁纵向裂纹如图1所示,如果加工初期受到压缩变形,加工后期受到拉伸变形,可能产生纵裂纹。
(1)制品形状。
① 拉深深度过大。
胀形超过极限而引起纵向裂纹;另外,在精整时,纵向或横向胀形若超过极限,也会引起破裂。
总之,破裂的直接原因,与胀形超限是一致的。
因此,超过变形极限而产生破裂,从形式上讲,就是拉深深度过深,如果降低拉深深度,成形条件就会变好。
图1 侧壁纵向裂纹② 凹模圆角半径(rd)过小。
由于是胀形变形,如果超过材料所具有的变形极限,就会产生破裂。
因此,合理的rd既能防止凸缘部裂纹的产生,又能补充材料。
作为改善材料流入条件的方法之一,是增大凹模圆角半径(rd)。
增大rd虽然防止了破裂产生,但这时的rd比图纸尺寸大,为使rd达到图纸要求,应增加一道精整工序。
(2)冲压条件。
① 压边力过大。
调整拉深力最基本的方法是调整压边力。
如果产生破裂,并且凸缘部位发亮,则是因为压边力过大。
因此,当有破裂危险时,可稍微降低压边力来观察制品的变化。
② 凹模面润滑不足。
随着压边力的增加,润滑油油膜强度也应相应提高,使其尽量减少摩擦。
③ 毛坯形状不良。
如果毛坯越大,成形条件就会越来越坏。
因此,需将毛坯减小到最小限度。
即可接近下死点时,毛坯要越过拉深筋,然后进行试拉深。
(3)模具问题。
① 拉深筋的形状和位置不对。
使用拉深筋虽然可以防止凸缘产生折皱,但其副作用是阻碍了材料的流入,因此,如果产生破裂的原因是材料流入阻力太大,那末,为了材料容易流入,就需要与毛坯形状一起综合分析拉深筋的位置和形状。
② 加工不良。
如果模面加工不良,往往不能提高压边力。
因此,需要用砂轮磨光。
(4)材料。
如果超过变形极限,就需要换成更高级的材料,另外,还要增加板材厚度。
凸模肩部相应部位裂纹由于材料的强度不够,当拉深载荷达到材料破断载荷时就会发生此缺陷。
缺陷部位产生于凸模肩R相应的部位(rp处),即比冲撞痕线更接近rp 的部分。
破裂部分的冲撞痕线,因与其他部位不同,可以对下面几种情况进行观察检查:或者被延展;或者在凸缘的上下面有发亮的部分;或者产生折皱。
另外,在侧壁上有时也有发亮的部分。
初期横向破裂,呈舌状。
如图1。
图1 rp部破裂原因及消除方法(1)制品形状。
① 拉深深度过大。
目前,圆筒、方筒深拉深的极限是在设计阶段确定的。
从而,在极限附近进行拉深时,要用表面光洁、平整的材料,综合模具配合和研磨,加工润滑油,缓冲压力,压力机精度等现场条件,进行试验拉深。
② 凸模半径(rp)过小。
a 将rp修正到适当值。
b 图纸上的rp过小时,首先按适当值进行拉深,然后再增加一道工序,成形所需尺寸。
③ 凹模尺寸(rd)过小。
a 将rd修正到适当值。
b 图纸上的rd过小时,首先用适当rd值进行拉深,然后再增加一道工序,成形到所需尺寸。
④ 方筒的角部半径(rc)过小。
a 将拉深深度减小;b 多增加一道拉深工序;c 换成更高级的材料;d 将板料厚度增加。
(2)冲压条件。
① 压边力过大。
压边力过大时,在凸缘面上不会发生起皱。
防皱压板面粗糙度,模具配合,间隙,rp,rd,加工油的种类和涂敷条件,缓冲销造成的压边力分布等,都影响防皱压力。
如果有关拉深的上述这些条件都合适的话,压边力就会下降,在起皱之前,不会发生破裂。
压边力过大时,由于凸缘面会全面发亮,所以很容易判断。
② 润滑不良。
拉深加工与润滑有极为密切的关系,特别是包含有减薄拉深加工时,必须控制制品温度的升高。
如果是条件好的拉深加工,润滑油的选择不成什么问题;条件不好的拉深加工,如果润滑油选择不当,就会引起破裂。
③ 毛坯形状不良。
在试拉深阶段,决定毛坯形状是重要的工作之一。
必须将毛坯形状限制在最小尺寸。
当用方形毛坯进行圆筒拉深时,极限拉深率为0.58左右。
另外,如果拉深率过于严苛,rp部位的伤痕会产生破裂,如进行切角,就可防止破裂。
拉深方筒时可先用方坯进行,这样可以制造出漂亮的制品,但是如果达到拉深极限,在rcp附近就会产生破裂。
如果已经破裂,可将毛坯的四角切去一部分。
但如果切多了的话,就会产生凸缘起皱,成为产生壁裂纹的原因。
④ 毛坯定位不好。
即使毛坯形状良好,但如果调整位置不好,或者放置方位不对,这时,凸模与毛坯产生错位,也会产生破裂或起皱。
另外,用500吨油压机,对较大尺寸的拉深件成形时(材料是SUS304),使用粘度低的油就可进行深拉深。
当使用粘度高的油进行深拉深时,拉深到高度的1/4,rp部位就会破裂。
不锈钢与软钢板相比较,容易受到速度的影响,但如进行充分的冷却和润滑,在实际操作中,其他方面的问题比速度问题更重要。
当进行高速冲裁时,即使使用一般间隙,切口的全部剪切面都是非常理想的。
⑤ 模具安装不良。
该缺陷是由模具安装不良,上下模不对中所造成的。
近来,几乎所有的模具都备有导向装置,由于模具不对中产生的故障已很少见。
⑥ 缓冲销的长短不齐。
缓冲销在使用过程中,由于出现压弯,冲击伤痕等,往往变得长短不一,拉深过程中,缓冲销长的部分,由于受到集中载荷而破裂。
为了对缓冲销的长短不一进行检查,在模具调整阶段,用手来回摇销,长销由于集中承受压边圈的重量,而变得很重,这是很容易理解的。
⑦ 缓冲垫凹凸不平。
当压力机缓冲垫的销子位置出现凹陷,或者废料从销孔落到缓冲垫上,就无法控制缓冲压力。
压力机如有活动工作台,由于能进行简单的清扫或检修,所以这样的事故是不会发生的,但如果是固定工作台,长期不检修,一旦使用,往往会发生事故。
⑧ 缓冲销配备不良。
缓冲销原则上应装配在凸模的周围,然而,必须有适当的间隔。
如果压边圈很薄,缓冲销配置不当时,产品的凸缘,在某个缓冲销部位受到强烈拉力而使其断裂。
这时,凸缘的末端形状,就会象舌状样局部延伸,这是很简单明白的道理。
另外,缓冲销配置与凸模周边形状不一致,凸缘面会起皱,也往往会成为破裂的原因。
归根到底,当压边圈很薄,销子的位置就有明显的影响,因此,使压边圈具有充分的强度,是最基本的问题。
⑨ 起皱引起破裂。
a 坯料尺寸大于压边圈。
当坯料尺寸比压边圈大时,拉深开始之后,坯料外露部分就产生起皱,它同“拉深筋”的功能一样,继续拉深会使其破裂,在试拉深阶段,为了确定“拉深筋”的位置,有时故意使毛坯露在压边圈外。
一般来说,即使是大坯料局部胀形,其原则仍是毛坯用压边圈压住后再进行加压。
b 压边力小。
当压边力小时,毛坯表面就会起皱,该折皱通过凹模圆角半径(rd)时,往往会破裂。
因此,这种场合,折皱和破裂就混为一体。
当用加工硬化程度高的不锈钢板进行方筒深拉深时,如图1所示的角部凸缘部位,有一光亮部分,在靠近rd处产生折皱。
该折皱就是产生破裂的原因,rd部分如果破裂,首先要提高压边力,消除折皱,这是头等重要的事情。
决不要增大rd或者降低压边力。
光亮部分是由于坯料厚度增加,承受集中载荷所致,因此,在提高压边力的同时,把模具间的接触点到刮目相看平,消除材料增厚的部分;如呈分布载荷,则可消除凸缘面起皱,而使材料的流入变得容易。