车辆结构有限元疲劳分析
基于有限元模型的汽车车身强度分析与优化设计

基于有限元模型的汽车车身强度分析与优化设计引言:汽车车身设计是整车设计中至关重要的一环。
汽车车身不仅是汽车的“外衣”,还承担着对乘员安全和行驶稳定性的极其重要的作用。
车身的强度是确保车辆在各种复杂工况下保持结构稳定、寿命可靠的关键因素。
基于有限元模型的汽车车身强度分析与优化设计具有重要的意义。
1. 有限元分析在汽车车身设计中的应用有限元分析是一种基于力学原理和数值计算方法的数值模拟技术。
它可以将复杂的连续体结构离散为有限个单元,通过求解单元之间的相互作用力,得到结构的应力、应变等力学参数。
在汽车车身设计中,有限元分析可以有效地评估车身的强度、刚度、振动特性等。
2. 汽车车身强度分析的主要内容汽车车身强度分析主要分为静态强度分析和动态强度分析两个方面。
2.1 静态强度分析静态强度分析是对车身在静态加载条件下进行强度评估。
通过有限元分析,可以得到车身各部分的应力分布情况和最大应力值,进而判断车身是否足够强度。
在静态强度分析中,需要考虑的因素包括车身的受载状态、材料的力学性质、载荷的大小和方向等。
2.2 动态强度分析动态强度分析是对车身在动态加载条件下进行强度评估。
在实际使用中,汽车车身会受到各种道路激励和振动的影响,因此需要对车身进行动态强度分析。
通过有限元分析,可以得到车身在不同工况下的应力变化规律和疲劳寿命,进而优化车身结构设计,提升车身的抗疲劳能力。
3. 汽车车身设计的优化方法基于有限元模型的汽车车身优化设计可以通过调整车身结构和材料等手段来提升车身的强度和刚度。
3.1 结构优化在车身结构优化中,可以通过增加加强筋、设置补强板和优化焊缝位置等方式来提升车身的强度。
通过有限元分析,可以评估不同优化方案的效果,并选择最佳方案进行实施。
3.2 材料优化材料的选择对车身的强度和轻量化设计起着重要作用。
目前,高强度钢材和铝合金等轻量化材料正在被广泛应用于汽车车身设计中。
基于有限元分析,可以评估不同材料对车身强度的影响,并选择合适的材料进行使用。
有限元法进行疲劳分析

元计算科技发展有限公司是一家既年青又悠久的科技型企业。年青是因为她正处在战略重组 后的初创期,悠久是因为她秉承了中国科学院数学研究所在有限元和数值计算方面所开创的光荣 传统。元计算的目标是做强中国人自己的计算技术,做出中国人自己的CAE软件。
元计算秉承中国科学院数学与系统科学研究院有限元自动生成核心技术(曾获中科院科技进 步二等奖、国家科技进步二等奖),通过自身不懈的努力与完善,形成一系列具有高度前瞻性和 创造性的产品。
5. 评估(Evaluation) 一般来说,我们可进行下列估算: ·事件损伤(Event Damage) ·事件损伤方向(Event Damage Direction) ·损伤累积(Accumulated Damage) ·事件寿命估算(Event Life Estimate)
6. 后处理(Post Processing) 疲劳分析的后处理与静力学的后处理完全一致,此处不再重复。
有限元法进行疲劳分析
一、有限元法疲劳分析的基本思路
用有限元法进行疲劳分析,其基本思路是:首先进行静或动强度分析,然后进入到后 处理器取出相关的应力应变结果,在后处理器中再定义载荷事件,循环材料特性,接着根 据所需要的疲劳准则对每一个载荷事件进行寿命计算,最后根据累计损伤理论判断是否开 始破坏。由于结构受力状态往往是一复杂的应力状态,而在实验中测 得的结构材料S-N曲 线又常是在简单应力状态下获得的,因此常用最小能量屈服准则或其它等效准则,将所研 究的疲劳点上的复杂应力用一个等效应力替代。对有限元法而言,这一过程很容易实现。 等效替代以后,即可参照原始材料的S-N曲线进行疲劳寿命评估。上述方法称之为应力-寿 命法或S-N法,该方法不严格区 分裂纹产生和裂纹扩展,而是给出结构发生突然失效前的 全寿命估计。当然,还可以采用更加现代化的局部应变法或初始裂纹法。因篇幅所限,因 此仅讨论S-N法,且针对车辆结构疲劳分析。
重型载货汽车车架结构的有限元仿真及优化
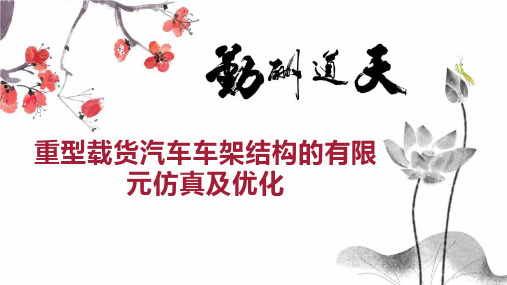
优化方案
优化方案
根据有限元仿真结果,针对重型载货汽车车架结构的薄弱环节和潜在问题, 提出以下优化方案:
优化方案
1、结构改进:对车架结构进行优化设计,减少不必要的焊接部位,增加结构 强度。例如,采用局部加强板或增加加强筋等方式对车架关键部位进行加固。
优化方案
2、材料替换:采用高强度材料替代传统钢材,如铝合金、高强度钢等,以减 轻车架重量,提高抗疲劳性能。
优化方案
3、尺寸调整:通过对车架结构的关键部位进行尺寸调整,优化结构布局,提 高承载能力。例如,调整横梁和纵梁的长度、宽度和高度等参数,以改善车架的 抗弯和抗扭性能。
优化方案
4、增加附件:如加强板、减震器等附件,提高车架的抗载荷能力和减震效果。
优化效果
优化效果
实施上述优化方案后,重型载货汽车车架结构的效果显著。以下是优化效果 的几个方面:
结论
结论
本次演示通过对重型载货汽车车架进行有限元分析,了解了车架的应力、应 变分布情况,并提出了优化建议。这些建议对于提高车架的承载能力和稳定性具 有重要意义。在实践中,可以根据具体需求和条件,综合考虑选择适合的优化措 施。有限元分析作为一种有效的数值模拟方法,可以为重型载货汽车车架的设计 和优化提供重要参考。
1、结构强度提高:通过结构改进和材料替换,车架的强度得到了显著提高, 能够有效应对各种复杂工况下的载荷。
优化效果
2、重量减轻:采用高强度材料和尺寸调整,车架重量得到了显著减轻,从而 提高整车的燃油经济性。
优化效果
3、疲劳性能改善:优化后的车架结构具有更好的抗疲劳性能,减少了车辆在 使用过程中的断裂等现象。
Байду номын сангаас
参考内容
引言
地铁车辆吊装结构强度有限元分析
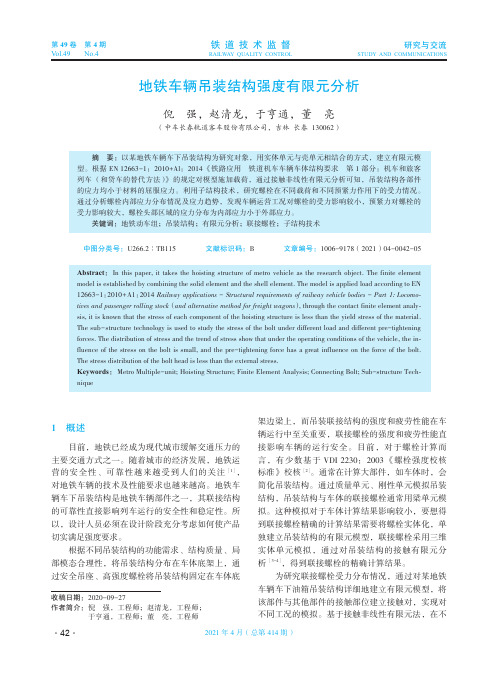
2021年4月(总第414期)·42·研究与交流STUDY AND COMMUNICATIONS第49卷Vol.49第4期No.4铁道技术监督RAILWAY QUALITY CONTROL收稿日期:2020-09-27作者简介:倪强,工程师;赵清龙,工程师;于亨通,工程师;董亮,工程师1概述目前,地铁已经成为现代城市缓解交通压力的主要交通方式之一。
随着城市的经济发展,地铁运营的安全性、可靠性越来越受到人们的关注[1],对地铁车辆的技术及性能要求也越来越高。
地铁车辆车下吊装结构是地铁车辆部件之一,其联接结构的可靠性直接影响列车运行的安全性和稳定性。
所以,设计人员必须在设计阶段充分考虑如何使产品切实满足强度要求。
根据不同吊装结构的功能需求、结构质量、局部模态合理性,将吊装结构分布在车体底架上,通过安全吊座、高强度螺栓将吊装结构固定在车体底架边梁上,而吊装联接结构的强度和疲劳性能在车辆运行中至关重要,联接螺栓的强度和疲劳性能直接影响车辆的运行安全。
目前,对于螺栓计算而言,有少数基于VDI 2230:2003《螺栓强度校核标准》校核[2]。
通常在计算大部件,如车体时,会简化吊装结构。
通过质量单元、刚性单元模拟吊装结构,吊装结构与车体的联接螺栓通常用梁单元模拟。
这种模拟对于车体计算结果影响较小,要想得到联接螺栓精确的计算结果需要将螺栓实体化,单独建立吊装结构的有限元模型,联接螺栓采用三维实体单元模拟,通过对吊装结构的接触有限元分析[3-4],得到联接螺栓的精确计算结果。
为研究联接螺栓受力分布情况,通过对某地铁车辆车下油箱吊装结构详细地建立有限元模型,将该部件与其他部件的接触部位建立接触对,实现对不同工况的模拟。
基于接触非线性有限元法,在不地铁车辆吊装结构强度有限元分析倪强,赵清龙,于亨通,董亮(中车长春轨道客车股份有限公司,吉林长春130062)摘要:以某地铁车辆车下吊装结构为研究对象,用实体单元与壳单元相结合的方式,建立有限元模型。
基于虚拟疲劳试验的铁路车辆焊接结构疲劳寿命预测

基于虚拟疲劳试验的铁路车辆焊接结构疲劳寿命预测一、本文概述随着铁路行业的快速发展,车辆的安全性和可靠性越来越受到人们的关注。
焊接结构作为铁路车辆的重要组成部分,其疲劳寿命的预测和评估对于确保车辆运行安全具有重要意义。
传统的疲劳试验方法由于周期长、成本高、对试验条件要求严格等限制,已无法满足现代铁路车辆研发的需求。
基于虚拟疲劳试验的铁路车辆焊接结构疲劳寿命预测方法应运而生,成为了当前研究的热点。
本文旨在探讨基于虚拟疲劳试验的铁路车辆焊接结构疲劳寿命预测方法。
文章将介绍虚拟疲劳试验的基本原理和关键技术,包括有限元分析、疲劳损伤累积理论等。
将详细阐述如何利用虚拟疲劳试验对铁路车辆焊接结构进行疲劳寿命预测,包括模型的建立、加载条件的设定、疲劳寿命的计算等步骤。
文章还将对虚拟疲劳试验的准确性和可靠性进行评估,并与传统疲劳试验结果进行对比分析。
文章将总结虚拟疲劳试验在铁路车辆焊接结构疲劳寿命预测中的应用前景,并提出相应的建议和改进措施。
通过本文的研究,旨在为铁路车辆焊接结构的疲劳寿命预测提供一种新的、高效的方法,为铁路车辆的安全性和可靠性提供有力保障。
也为相关领域的研究提供参考和借鉴。
二、虚拟疲劳试验技术概述虚拟疲劳试验技术是一种基于计算机模拟和数值分析的方法,旨在预测和评估铁路车辆焊接结构的疲劳寿命。
该技术结合了有限元分析(FEA)、多体动力学仿真、疲劳损伤累积理论和数据处理技术等手段,通过构建高度逼真的虚拟模型来模拟实际工作环境中的载荷条件和应力分布。
在虚拟疲劳试验中,首先需要根据实际车辆的结构特点、材料属性和焊接工艺等建立精确的有限元模型。
通过多体动力学仿真模拟车辆在不同运行条件下的动力学行为,获取各关键部位的动态载荷历程。
利用疲劳分析软件对这些载荷历程进行处理,计算各部位的应力响应和疲劳损伤累积情况。
基于疲劳损伤累积理论,预测结构的疲劳寿命,并找出潜在的疲劳薄弱环节。
虚拟疲劳试验技术具有成本低、周期短、可重复性好等优点,能够在产品设计阶段就进行疲劳性能的预测和优化,从而有效提高铁路车辆焊接结构的安全性和可靠性。
汽车底盘车架设计中的疲劳寿命分析

汽车底盘车架设计中的疲劳寿命分析汽车底盘车架作为汽车的主要部件之一,承担着车辆负荷传递和支撑车身的重要任务。
然而,在日常使用中,车架会承受各种道路条件带来的振动和冲击载荷,因此必须通过疲劳寿命分析来保证其结构的安全可靠性。
疲劳寿命分析是通过分析材料在循环载荷作用下的应力和应变历史来评估结构的使用寿命。
在汽车底盘车架设计中,疲劳寿命分析能够确保车架结构在长期使用过程中不会出现疲劳断裂,从而保证行车安全。
首先,在疲劳寿命分析中,需要进行材料的应力和应变分析。
根据车架的几何形状和所受的载荷条件,可以使用有限元分析方法对车架进行建模,并计算车架各个部位的应力和应变分布。
通过这一步骤,可以得到车架在循环载荷下的受力情况。
其次,在知晓车架的应力和应变分布后,需要进行疲劳寿命预测。
疲劳寿命预测是通过使用经验公式或材料的S-N曲线,将应力幅值和循环次数进行匹配,以确定车架在循环载荷下的寿命。
根据材料的疲劳性能和加载情况,可以预测车架在不同循环载荷下的疲劳寿命。
此外,疲劳寿命分析还需要考虑到材料的变形和应力集中情况。
材料的可塑变形会导致结构在受载过程中的局部应力升高,从而影响其疲劳寿命。
因此,在进行疲劳寿命分析时,需要对车架的变形情况进行分析,并采取适当的设计措施来降低应力集中。
在实际的车架设计过程中,还需要考虑到不同材料的选择和优化。
不同材料的抗疲劳性能不同,因此,在进行车架设计时,需要选择适当的材料并进行结构的优化,以提高车架的疲劳寿命。
此外,在进行材料选择和优化时,还需要考虑到材料的成本、加工性能以及环境要求等因素。
最后,为了确保车架结构的安全可靠性,还需要进行疲劳试验验证。
通过对车架样件进行实验加载,可以验证疲劳寿命分析的准确性,并对车架的设计进行优化。
疲劳试验还可以为车架的维修保养提供参考,预测车架在实际使用中的寿命。
综上所述,汽车底盘车架设计中的疲劳寿命分析是确保车架结构安全可靠性的重要环节。
通过对车架的应力和应变分析、疲劳寿命预测以及材料选择和优化等步骤,可以保证车架在循环载荷下的使用寿命。
有限元分析在轮胎结构设计中的应用

有限元分析在轮胎结构设计中的应用有限元分析(Finite Element Analysis,简称FEA)是一种应用数学方法和计算方法解决物理领域中的工程和科学问题的技术。
在轮胎结构设计中,有限元分析可以发挥重要作用。
本文将探讨有限元分析在轮胎结构设计中的应用。
首先,有限元分析可以用于轮胎的结构分析。
在轮胎的结构设计过程中,了解和评估轮胎的结构性能是非常重要的。
有限元分析可以帮助工程师对轮胎的不同部分进行细节分析,如轮胎的胎面、胎肩、胎侧等等。
通过有限元分析,可以模拟轮胎在不同道路条件下的受力情况,研究轮胎的应力、变形和疲劳等特性。
这有助于工程师了解轮胎的强度和刚度,为轮胎设计提供依据。
其次,有限元分析可以用于轮胎的耐久性分析。
耐久性是轮胎结构设计的一个重要指标。
有限元分析可以帮助工程师模拟轮胎在实际使用条件下的循环荷载作用下的疲劳性能。
通过有限元分析,可以评估轮胎的寿命和耐久性,预测轮胎在不同使用条件下的损坏情况。
这有助于工程师确定合适的轮胎材料和结构设计,提高轮胎的寿命和可靠性。
另外,有限元分析还可以用于轮胎的车辆动力学分析。
轮胎在车辆行驶过程中,承受着来自地面的力和转矩,对行驶稳定性和操控性起着关键作用。
有限元分析可以帮助工程师模拟轮胎和地面之间的接触力,研究轮胎的摩擦特性和动力学行为。
通过有限元分析,可以评估轮胎在转弯、制动和加速等情况下的性能,优化轮胎的设计参数,提高车辆的操控性和行驶稳定性。
此外,有限元分析还可以用于轮胎的优化设计。
通过有限元分析,工程师可以设计和评估不同的结构方案,优化轮胎的性能。
例如,可以通过有限元分析评估轮胎胎面花纹的设计对轮胎的排水性能和抓地力的影响,优化胎面花纹的形状和纹样。
此外,还可以通过有限元分析优化轮胎的结构参数,如胎压、胎宽和胎壁高度等,以获得更好的性能和经济性。
总而言之,有限元分析在轮胎结构设计中的应用十分广泛。
通过有限元分析,可以模拟轮胎的结构和性能,研究轮胎的强度、疲劳性能和动力学行为,优化轮胎的设计参数,提高轮胎的性能和可靠性。
有限元法进行疲劳分析

展望
01
随着计算机技术和数值分析方法的不断发展,有限元法在疲劳分析中 的应用将更加广泛和深入。
02
未来疲劳分析的研究将更加注重实验验证和理论建模的结合,以提高 预测精度和可靠性。
03
针对复杂结构和材料的疲劳性能研究将进一步加强,以适应各种工程 应用的需求。
04
疲劳分析将与优化设计、可靠性分析和损伤容限设计等相结合,为产 品的全寿命周期管理提供支持。
有限元法进行疲劳分析
目录
• 引言 • 有限元法基础 • 疲劳分析基础 • 基于有限元法的疲劳分析 • 有限元法进行疲劳分析的案例 • 结论与展望
01 引言
疲劳分析的重要性
01
疲劳分析是产品寿命预测的关键 环节,有助于提前发现潜在的疲 劳断裂风险,避免产品在服役过 程中发生意外断裂。
02
通过疲劳分析,可以优化产品设 计,提高产品的可靠性和安全性 ,降低产品全寿命周期成本。
02 有限元法基础
有限元法简介
有限元法是一种数值分析方法, 用于解决各种复杂的工程问题, 如结构分析、热传导、流体动力
学等。
它通过将连续的物理系统离散化 为有限个小的单元,并对这些单 元进行分析,从而实现对整个系
统的近似求解。
有限元法广泛应用于工程设计、 产品开发和科学研究等领域。
有限元法的基本原理
结构应力分析
通过有限元法计算结构的应力分布。
疲劳裂纹扩展模拟
引入裂纹扩展模型,模拟裂纹在结构中的扩 展过程。
应力集中区域识别
找出结构中的应力集中区域,这些区域往往 是疲劳裂纹萌生的地方。
结构疲劳寿命评估
结合材料的疲劳性能参数和裂纹扩展规律, 评估结构的疲劳寿命。
05 有限元法进行疲劳分析的 案例
- 1、下载文档前请自行甄别文档内容的完整性,平台不提供额外的编辑、内容补充、找答案等附加服务。
- 2、"仅部分预览"的文档,不可在线预览部分如存在完整性等问题,可反馈申请退款(可完整预览的文档不适用该条件!)。
- 3、如文档侵犯您的权益,请联系客服反馈,我们会尽快为您处理(人工客服工作时间:9:00-18:30)。
四、发动机连杆的应力疲劳分析
直接打开Conrod-fatigue.wbpj文件,导 入ConRod.x_t,并对Geometry进行编辑。
四、发动机连杆的应力疲劳分析
2.疲劳破坏的特点
1)疲劳发生的外部原因是扰动应力;
2)疲劳破坏产生于局部;
3)疲劳是一个发展的过程 从疲劳裂纹的形成到裂纹扩展,以致最后断裂,
是疲劳损伤逐渐累积的过程。 一般分为三个阶段: 裂纹萌生、裂纹扩展和最后失稳扩展断裂。
一、结构疲劳分析基础
3.疲劳分析的基本流程
材料的疲劳特性S-N曲线 E-N曲线
Gerber法 None不进行修正
Mean Stress
Curves
定义有限寿命数值 疲劳强度系数 载荷缩放系数
恒幅,比例载荷 恒幅,非比例载荷 非恒幅,比例载荷 非恒幅,非比例载荷
X方向应力/Y/Z XY平面应力 YZ平面应力 XZ平面应力
Von Mises应力 带符号的Von Mises应力
最大剪应力 最大主应力 最大主应力最大值
得到的是多轴应力。但在试验过程中得到的 一般是单轴应力。在ANSYS WB应力疲劳分析 中可以选择X、Y、Z三个方向的应力分量, Von Mises应力,带符号Von Mises应力等。 在考虑压缩平均应力对疲劳寿命的影响中, 带符号Von Mises应力是非常有用的,
二、应力疲劳分析
疲劳修正
定义有限寿命数值 疲劳强度系数 载荷缩放系数
车辆结构有限元分析
第九章 车辆结构有限元疲劳分析
结构疲劳分析基础 应力疲劳分析 典型材料试件应力疲劳分析 发动机连杆的应力疲劳分析
一、结构疲劳分析基础
车辆是运动并承载的机械,其结构承受 的载荷大部分都是交变载荷。零部件失效中, 由疲劳裂纹引起的结构失效断裂事故占总断 裂事故的70%--80%以上,约有50%--90%的 机械结构的破坏属于疲劳破坏。
二、应力疲劳分析
二、应力疲劳分析
二、应力疲劳分析
二、应力疲劳分析
9.载荷谱 通过有限元静态分析计算,得到车辆在三
种工况下的应力与循环次数的分布如下表:
二、应力疲劳分析
10.Miner线性累积损伤理论
对载荷谱(载荷时间历程)计数,得到载荷 (S)——循环次数(n)图:
构件在应力水平Si作用下,经受ni 次循环损伤为Di=ni/Ni。若在k个应力水 平Si作用下,则其总损伤为:
D=
三、典型材料试件应力疲劳分析
三、典型材料试件应力疲劳分析
三、典型材料试件应力疲劳分析
划分网格
三、典型材料试件应力疲劳分析
施加载荷和约束
三、典型材料试件应力疲劳分析
定义分析分析结果
Байду номын сангаас
三、典型材料试件应力疲劳分析
疲劳分析设置
三、典型材料试件应力疲劳分析
求解结果
四、发动机连杆的应力疲劳分析
GoodMan法 Soderberg法 Gerber法 None不进行修正 Mean Stress Curves
二、应力疲劳分析
7.应力分量的选取 在进行结构应力分析的过程中,
X方向应力/Y/Z XY平面应力 YZ平面应力 XZ平面应力
Von Mises应力 带符号的Von Mises应力
最大剪应力 最大主应力 最大主应力最大值
一、结构疲劳分析基础
人们对车辆结构疲劳的研究主要集中在车 辆的承载结构,如悬架、车轮、车架、横向 稳定杆、发动机连杆、传动轴等。
一、结构疲劳分析基础
疲劳失效的原因有哪些呢? 1)设计原因 2)材质原因 3)制造(工艺)原因
4)其他原因(安装调试、维修运转等)
一、结构疲劳分析基础
一、结构疲劳分析基础
Fully Reversed
Ratio
History
非恒定幅值比例 载荷
R=-1
指定应力比 R=X
指定载荷时 间历程
二、应力疲劳分析
6.平均应力对疲劳寿命的影响
平均应力对疲劳寿命的影响就是考虑应力 比R的变化对疲劳寿命会产生影响,从而需要 对S-N曲线进行修正。ANSYS WB提供了平均应 力修正的五个选项:
二、应力疲劳分析
9.载荷谱
进行疲劳分析时,首先必须确定零部件或 结构工作状态下所承受的载荷谱。载荷谱的 确定通常有两种方法:
1)借助已有的类似构件、结构或其模型,在使用条件或模 拟使用条件下进行测量,得到各典型工况下的载荷谱,再将 各工况组合起来得到的载荷谱,称为实测载荷谱;
2)在没有适当的类似结构或模型时,依据设计目标分析工 作状态,结合经验估计载荷谱,这样给出的是设计载荷谱。
二、应力疲劳分析
2.应力疲劳分析流程
二、应力疲劳分析
二、应力疲劳分析
定义S-N 曲线
二、应力疲劳分析
4.设置疲劳分析类型
设置疲劳 分析类型
应力疲劳分析 Stress Life 应变疲劳分析 Strain Life
高周疲劳 低周疲劳
二、应力疲劳分析
5.载荷类型
Zero-Based
R=0
载荷类型
其他设置
四、发动机连杆的应力疲劳分析
打开Model(A4),进入Mechanical界面:
按照目录树要求, 对未完成项进行补充。
四、发动机连杆的应力疲劳分析
边界条件补充
四、发动机连杆的应力疲劳分析
注意Fatigue Tool选项的设置
疲劳强度系数Kf为0.8, 代表该材料相对于光滑构 件疲劳强度下降的系数。
四、发动机连杆的应力疲劳分析
有限元静力学分析结果
载荷谱
疲劳分析方法
疲劳寿命
二、应力疲劳分析
1.S-N曲线 在ANSYS WB中S-N曲线是通过点定义
的。
二、应力疲劳分析
二、应力疲劳分析
2.应力疲劳分析流程
定义S-N 曲线
设置疲劳 分析类型
选择载 荷类型
平均应 力修正
应力分量 的选取
疲劳修正
应力疲劳分析
GoodMan法 Soderberg法