航空铝合金薄壁件铣削加工变形的预测模型_王光宇
航空铝合金薄壁件铣削变形预测分析
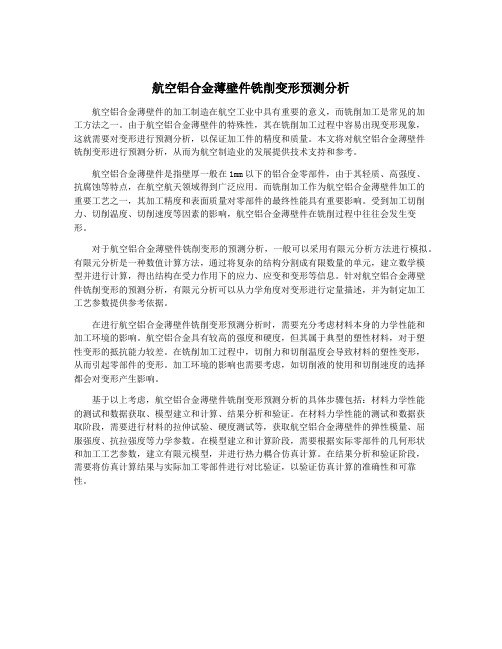
航空铝合金薄壁件铣削变形预测分析航空铝合金薄壁件的加工制造在航空工业中具有重要的意义,而铣削加工是常见的加工方法之一。
由于航空铝合金薄壁件的特殊性,其在铣削加工过程中容易出现变形现象,这就需要对变形进行预测分析,以保证加工件的精度和质量。
本文将对航空铝合金薄壁件铣削变形进行预测分析,从而为航空制造业的发展提供技术支持和参考。
航空铝合金薄壁件是指壁厚一般在1mm以下的铝合金零部件,由于其轻质、高强度、抗腐蚀等特点,在航空航天领域得到广泛应用。
而铣削加工作为航空铝合金薄壁件加工的重要工艺之一,其加工精度和表面质量对零部件的最终性能具有重要影响。
受到加工切削力、切削温度、切削速度等因素的影响,航空铝合金薄壁件在铣削过程中往往会发生变形。
对于航空铝合金薄壁件铣削变形的预测分析,一般可以采用有限元分析方法进行模拟。
有限元分析是一种数值计算方法,通过将复杂的结构分割成有限数量的单元,建立数学模型并进行计算,得出结构在受力作用下的应力、应变和变形等信息。
针对航空铝合金薄壁件铣削变形的预测分析,有限元分析可以从力学角度对变形进行定量描述,并为制定加工工艺参数提供参考依据。
在进行航空铝合金薄壁件铣削变形预测分析时,需要充分考虑材料本身的力学性能和加工环境的影响。
航空铝合金具有较高的强度和硬度,但其属于典型的塑性材料,对于塑性变形的抵抗能力较差。
在铣削加工过程中,切削力和切削温度会导致材料的塑性变形,从而引起零部件的变形。
加工环境的影响也需要考虑,如切削液的使用和切削速度的选择都会对变形产生影响。
基于以上考虑,航空铝合金薄壁件铣削变形预测分析的具体步骤包括:材料力学性能的测试和数据获取、模型建立和计算、结果分析和验证。
在材料力学性能的测试和数据获取阶段,需要进行材料的拉伸试验、硬度测试等,获取航空铝合金薄壁件的弹性模量、屈服强度、抗拉强度等力学参数。
在模型建立和计算阶段,需要根据实际零部件的几何形状和加工工艺参数,建立有限元模型,并进行热力耦合仿真计算。
铝合金薄壁件铣削变形的有限元分析

2020 年 09 月 Journal of Jiamusi University ( Natural Science Edition)
Vol. 38
Sep.
No. 5
2020
文章编号:1008 - 1402(2020)05 - 0082 - 03
铝合金薄壁件铣削变形的有限元分析
①
程婷婷ꎬ 徐小飞
( 安徽机电职业技术学院机械工程学院ꎬ安徽 芜湖 241000)
摘 要: 为了解决航空薄壁件铣削加工中变形过程运算的复杂性问题ꎬ借助目前计算机技术的
发展ꎬ利用有限元法( FEM) 对金属切削过程进行仿真ꎮ 再通过 ABAQUS 软件对薄壁件铣削的有
加工结束后使用三坐标测量仪对四块板件进
行检测ꎮ 对比结果如图 6 所示:
限元仿真过程ꎬ省去大量复杂的计算过程ꎬ得出仿真结果与实验验证结果对比后误差较小ꎬ对解
决航空薄壁件变形问题具有实际意义ꎮ
关键词: 薄壁件ꎻ加工变形ꎻ有限元仿真
中图分类号: TP391 文献标识码: A
0 引 言
航空、航天领域中薄壁件以其特殊的综合性能
优势而被广泛应用ꎮ 在薄壁件铣削加工过程中ꎬ由
通过将加工表面的节点转成集合ꎬ同时以加工
变形的集合作为输出量ꎬ通过数据( . dat) 文件中节
点坐标、坐标值和变形量得到所需的数据ꎮ 绘制出
铣削薄壁件水平薄壁的位置的变形量如图 3 所示:
图 3 铣削水平方向节点变形量
( a) 对 1 / 2 块铝板加工 ( b) 整体铣削过程
图 5 铝板铣削过程
①
最终模型建立工作ꎮ 在研究薄壁件切削变形时ꎬ考
激光加热辅助车削高温合金薄壁件变形仿真及试验研究
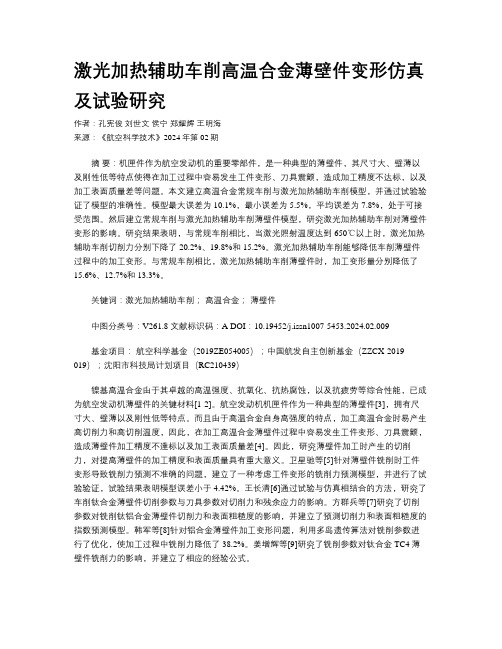
激光加热辅助车削高温合金薄壁件变形仿真及试验研究作者:孔宪俊刘世文侯宁郑耀辉王明海来源:《航空科学技术》2024年第02期摘要:机匣件作为航空发动机的重要零部件,是一种典型的薄壁件,其尺寸大、壁薄以及刚性低等特点使得在加工过程中容易发生工件变形、刀具震颤,造成加工精度不达标,以及加工表面质量差等问题。
本文建立高温合金常规车削与激光加热辅助车削模型,并通过试验验证了模型的准确性。
模型最大误差为10.1%,最小误差为5.5%,平均误差为7.8%,处于可接受范围。
然后建立常规车削与激光加热辅助车削薄壁件模型,研究激光加热辅助车削对薄壁件变形的影响。
研究结果表明,与常规车削相比,当激光照射温度达到650℃以上时,激光加热辅助车削切削力分别下降了20.2%、19.8%和15.2%。
激光加热辅助车削能够降低车削薄壁件过程中的加工变形。
与常规车削相比,激光加热辅助车削薄壁件时,加工变形量分别降低了15.6%、12.7%和13.3%。
关键词:激光加热辅助车削;高温合金;薄壁件中图分类号:V261.8 文献标识码:A DOI:10.19452/j.issn1007-5453.2024.02.009基金项目:航空科学基金(2019ZE054005);中国航发自主创新基金(ZZCX-2019-019);沈阳市科技局计划项目(RC210439)镍基高温合金由于其卓越的高温强度、抗氧化、抗热腐蚀,以及抗疲劳等综合性能,已成为航空发动机薄壁件的关键材料[1-2]。
航空发动机机匣件作为一种典型的薄壁件[3],拥有尺寸大、壁薄以及刚性低等特点。
而且由于高温合金自身高强度的特点,加工高温合金时易产生高切削力和高切削温度,因此,在加工高温合金薄壁件过程中容易发生工件变形、刀具震颤,造成薄壁件加工精度不達标以及加工表面质量差[4]。
因此,研究薄壁件加工时产生的切削力,对提高薄壁件的加工精度和表面质量具有重大意义。
卫星驰等[5]针对薄壁件铣削时工件变形导致铣削力预测不准确的问题,建立了一种考虑工件变形的铣削力预测模型,并进行了试验验证,试验结果表明模型误差小于4.42%。
题目-制造业自动化

收稿日期:.基金项目:国家863计划(SQ2008AA10XK1468859),江苏省高校自然科学研究计划(08KJD460002)资助 作者简介:尹飞鸿(1969—),男,副教授,主要从事机械工装结构优化设计与有限元分析、加工过程建模与仿真研究,E-mail:铝合金航空薄壁框铣削变形预测研究Prediction Research into Milling Stress and Deformation of theThin-Walled Aviation Box of Aluminum Alloy尹飞鸿1、2, 唐国兴2,陈志伟1,干为民 2YIN Fei-hong 1、2, T ANG Guo-xing 1, CHEN Zhi-wei 1, GAN Wei-ming 2(1. 常州工学院机电工程学院,江苏常州213002;2. 常州市特种加工重点实验室,江苏常州213002)摘 要:铝合金航空薄壁框刚性差,铣削加工过程中极易产生加工变形,影响工件加工精度和生产成本。
本文利用有限元方法,模拟分析了铣削力对航空薄壁框类零件加工变形的影响,从控制航空薄壁框铣削加工变形的角度出发,分析了不同框体尺寸航空薄壁框的铣削应力与加工变形情况,得到了加工变形规律。
本研究可为预测和控制航空薄壁框类零件的加工变形提供方法和依据,对航空薄壁框类零件的结构设计、缩短研制周期和进一步提高生产率等都具有重要意义。
关键词:铝合金;薄壁框;铣削力;铣削变形;有限元分析 中图分类号: TG4 文献标识码: A 文章编号:随着现代飞机性能要求的不断提高,越来越多的铝合金整体结构件在航空制造业中被广泛采用,如整体薄壁框、梁、壁板及接头等,这是由于铝合金结构件具有整体性能优越、密度低、强度接近或超过优质钢且塑性好等特性。
从制造角度看,整体薄壁框零件刚性差,切削力对加工精度的影响较为显著,加工时在铣削力的作用下极易发生加工变形,影响工件加工精度和成本。
航空铝合金薄壁件铣削变形预测分析

航空铝合金薄壁件铣削变形预测分析【摘要】本文针对航空铝合金薄壁件铣削变形进行了预测分析。
引言部分从背景介绍和研究意义两个方面入手,指出了研究的重要性。
正文部分详细分析了航空铝合金薄壁件铣削变形的机理,并提出了一种预测方法。
通过实验设计与结果分析,深入探讨了影响因素,并对变形预测模型进行了优化。
结论部分总结了航空铝合金薄壁件铣削变形预测分析的成果,并展望未来研究方向。
本文的研究对提高航空铝合金薄壁件铣削加工质量具有积极意义,对于航空制造领域具有一定的借鉴意义。
【关键词】航空铝合金、薄壁件、铣削、变形、预测、机理分析、实验设计、结果分析、影响因素、预测模型优化、总结、未来展望1. 引言1.1 背景介绍航空铝合金薄壁件是航空器结构中常见的零部件,其精度要求高、加工难度大。
在航空制造领域,铣削是一种常用的加工方式,但由于铣削过程中材料的削除和内部残余应力的释放,会导致薄壁件发生变形。
对航空铝合金薄壁件铣削变形进行预测分析具有重要意义。
航空铝合金薄壁件的变形问题不仅会影响零部件的装配精度和性能,还可能导致加工后的产品无法投入使用,造成不可挽回的经济损失。
研究航空铝合金薄壁件铣削变形的机理和预测方法,有助于提高航空零部件的加工质量,降低生产成本,提高航空器的整体性能。
本文将对航空铝合金薄壁件铣削变形进行深入分析和研究,探讨影响变形的因素及其机制,建立变形预测模型,并对模型进行优化,为航空铝合金薄壁件的加工提供理论支持和实际指导。
1.2 研究意义航空铝合金薄壁件是飞机制造中广泛使用的一种零部件,其质量和形状精度对飞机的性能和安全起着至关重要的作用。
在航空铝合金薄壁件的生产加工过程中,铣削是一种常用的加工方法。
铣削过程中会产生变形,影响零件的质量和精度。
对航空铝合金薄壁件铣削变形进行预测分析具有重要意义。
预测变形可以帮助优化加工工艺,减小变形,提高零件的精度和质量。
通过分析变形机理和影响因素,可以指导工程师采取有效的措施来减少变形,提高加工效率。
航空铝合金7075_T7451薄壁件铣削加工模拟及变形预测

( 南京工艺装备制造有限公司, 江苏 南京 $%"""& ) 摘# 要: 介绍了成形磨削的加工机理、 成形修整技术的应用及磨削效率的控制, 解决了滚动导轨副零件高精 度、 复杂形状的加工困难问题, 并通过研究磨削效率降低砂轮用量, 提高了产品质量及加工经济性。 关键词: 金刚滚轮# 成形修整# 修整速比# 磨削效率
航空铝合金 !"!# $ %!&#’ 薄壁件铣削加工 ! 模拟及变形预测
王聪康( 彭承明( 路( 冬( 钟晓宏
( 南昌航空大学航空制造工程学院, 江西 南昌 $$%%&$ ) 摘! 要: 在考虑刀具变形、 工件及刀具材料性能参数的基础上, 建立了三维斜角切削力有限元模型, 利用有限 元分析软件 "#"$%&’( ) 对航空铝合金 *+*, - .*/,0 材料进行了铣削仿真模拟, 获得了切削力、 工 件变形情况、 上层材料对下层材料切削力的影响、 切屑形状与大小等规律。其次, 针对航空铝合金 *+*, - .*/,0 材料铣削过程进行了切削试验, 结果表明所提出的切削力有限元模型具有可行性, 可 以有效地预测薄壁件的铣削加工变形。 关键词: 残余应力! 铣削力! 有限元模型! 切屑
分别取一系列节点, 形成路径 $%&’ ( ) , 如图 * 白线所 示。
作用, 使工件靠近边缘 1 2 / 33 处产生较大位移。
! + !# 切屑分析 图 4 为航空铝合金 414, ( 54*,) 材料有限元模拟 的切屑和实验切屑的对比, 可知两种切屑的形状和大 小都很相近, 都是螺旋卷起来, 直径为 ) 2 / 33。
表 *# 合金刀具材料参数
密度 % ( . 4B @ ’( ) &; %## 弹性模量 2 . FGH %!# )0 . 泊松比 0. [ .( @ 4B・A ) ] & [ ?( @ ’・ A ) ] #$ ( --# &&-
大型薄壁铝合金壳体数控加工变形模拟分析与控制(下)
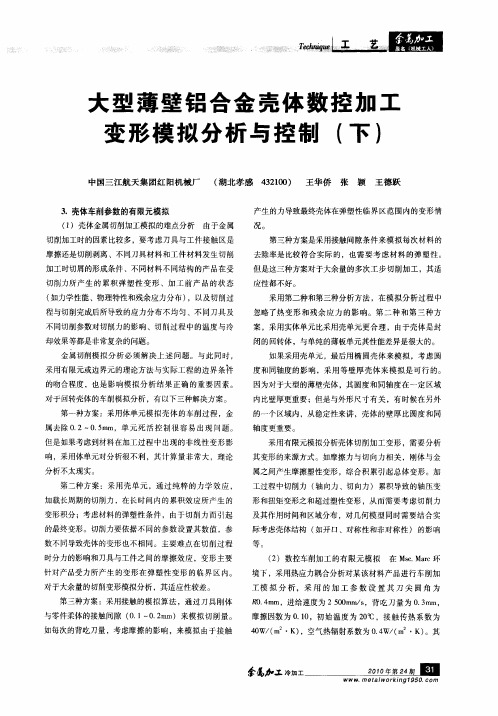
的最终变形 。切削力要依据不 同的参 数设置其 数值 ,参 数不同导致壳体的变形也不相 同。主要 难点在切 削过 程 时分力的影响和刀具 与工件之 间的摩擦效应 ,变形 主要 针对产 品受力所产生 的变形在 弹塑性 变形 的临界 区内。
( )数控车削加 工的有 限元模拟 2
在 M cMa s. r c环
境下,采用热应力耦合分析对某该材料产品进行车削加
工模 拟 分 析 ,采 用 的 加 工 参 数 设 置 其 刀 尖 圆 角 为
/ .m t 4 m,进给速度为 25 0 m s O 0 m / ,背吃刀量为 0 3 m, .m
对 于大余量的切削变形模拟分 析 , 其适应性较差。
第三种方案 :采用接触的模拟算法 ,通 过刀具刚体 与零件柔体的接触 间隙 ( . ~0 2 m)来模拟切 削量 。 0 1 .r a 如每次的背吃刀量 ,考虑摩擦 的影响 ,来模拟 由于接触
切削力所产 生 的累积 弹塑 性变 形 、加 工前 产 品的状 态
张
颖
王德跃
产生的力导致最终壳体在弹塑性临界 区范 围内的变形情
况。
第三种方案是采用接触间隙条件来模拟 每次材料的
去除率是 比较符合实 际的 ,也需 要考 虑材料 的弹塑性 。
但是这三种方案对于大余量的多次工步切 削加工 , 适 其
余应力 , 控制变形的作用 明显 。③切削加工 过程 中的工
序余量分配和工序组合 。由于加工过程 中存在加 工余 量 小 ,而所有的面均需要进行加工 ,各特征加工余量分 配 本身存在较大差异 ,从而对 导致 变形 的因素变得 复杂 ;
忽略了热变 形和残 余应 力 的影 响。第二 种 和第 三种方
航空铝合金薄壁件铣削变形预测分析
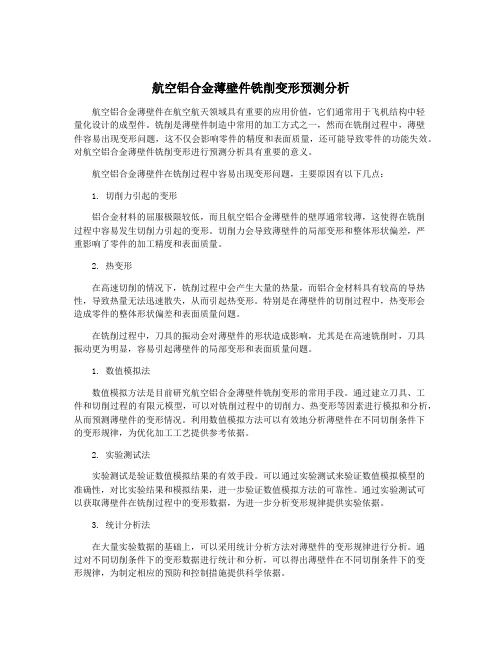
航空铝合金薄壁件铣削变形预测分析航空铝合金薄壁件在航空航天领域具有重要的应用价值,它们通常用于飞机结构中轻量化设计的成型件。
铣削是薄壁件制造中常用的加工方式之一,然而在铣削过程中,薄壁件容易出现变形问题,这不仅会影响零件的精度和表面质量,还可能导致零件的功能失效。
对航空铝合金薄壁件铣削变形进行预测分析具有重要的意义。
航空铝合金薄壁件在铣削过程中容易出现变形问题,主要原因有以下几点:1. 切削力引起的变形铝合金材料的屈服极限较低,而且航空铝合金薄壁件的壁厚通常较薄,这使得在铣削过程中容易发生切削力引起的变形。
切削力会导致薄壁件的局部变形和整体形状偏差,严重影响了零件的加工精度和表面质量。
2. 热变形在高速切削的情况下,铣削过程中会产生大量的热量,而铝合金材料具有较高的导热性,导致热量无法迅速散失,从而引起热变形。
特别是在薄壁件的切削过程中,热变形会造成零件的整体形状偏差和表面质量问题。
在铣削过程中,刀具的振动会对薄壁件的形状造成影响,尤其是在高速铣削时,刀具振动更为明显,容易引起薄壁件的局部变形和表面质量问题。
1. 数值模拟法数值模拟方法是目前研究航空铝合金薄壁件铣削变形的常用手段。
通过建立刀具、工件和切削过程的有限元模型,可以对铣削过程中的切削力、热变形等因素进行模拟和分析,从而预测薄壁件的变形情况。
利用数值模拟方法可以有效地分析薄壁件在不同切削条件下的变形规律,为优化加工工艺提供参考依据。
2. 实验测试法实验测试是验证数值模拟结果的有效手段。
可以通过实验测试来验证数值模拟模型的准确性,对比实验结果和模拟结果,进一步验证数值模拟方法的可靠性。
通过实验测试可以获取薄壁件在铣削过程中的变形数据,为进一步分析变形规律提供实验依据。
3. 统计分析法在大量实验数据的基础上,可以采用统计分析方法对薄壁件的变形规律进行分析。
通过对不同切削条件下的变形数据进行统计和分析,可以得出薄壁件在不同切削条件下的变形规律,为制定相应的预防和控制措施提供科学依据。
- 1、下载文档前请自行甄别文档内容的完整性,平台不提供额外的编辑、内容补充、找答案等附加服务。
- 2、"仅部分预览"的文档,不可在线预览部分如存在完整性等问题,可反馈申请退款(可完整预览的文档不适用该条件!)。
- 3、如文档侵犯您的权益,请联系客服反馈,我们会尽快为您处理(人工客服工作时间:9:00-18:30)。
1698
中南大学学报(自然科学版)
第 43 卷
应力场引起零件加工变形的机理。 层削法是一种目前常用的用于测量铝合金厚板内 应力的方法[19]。 本文使用层削法测量尺寸(长×宽×厚) 为 155 mm×155 mm×40 mm 的 7075 铝合金厚板的内 应力分布。 当没有任何外在载荷作用时,零件的内应力场应 该是自平衡的,即工件内任意截面内的合力和合力矩 应满足:
随着现代航空工业的发展,在飞机零部件中广泛 使用具有复杂结构的薄壁件,如整体框﹑整体梁和整
收稿日期:2011−05−03;修回日期:2011−08−26 基金项目:国家重点基础研究发展计划 (“973”计划)项目 (2010CB731703)
体壁板等。 这类零件的共同特点是尺寸大﹑结构复杂、 薄壁和精度要求高。由于这类零件的薄壁特性,极易
通信作者: 吴运新 (1963−) ,男,广东兴宁人,教授,博士生导师,从事有限元仿真,铝合金机加工研究;电话 : 0731-88830813 ; E-mail: wuyunxin@
第5期
王光宇,等:航空铝合金薄壁件铣削加工变形的预测模型
1697
在加工过程中产生翘曲变形。翘曲变形主要由初始残 余应力的释放﹑零件结构的不对称和加工工艺的缺陷 引起。有时,零件的翘曲变形甚至超过装配许可的误 差范围。为此,有时不得不在零件加工完成之后增加 校正程序。这不仅降低生产率,而且增加零件的废品 率,给制造商和零件的使用者带来巨大的经济损 失[1−3]。 为分析加工变形的机理并提出合适的策略以控 制加工变形,研究人员进行了相关的仿真和实验。He 等[4]将有限元方法用于分析和选择薄壁件加工变形的 控制策略。 Ratchev 等[5]研究薄壁件铣削加工时的误差 补偿策略。Weinert 等[6−8]将有限元方法用于铝合金结 构加工过程的计算分析和薄壁件周铣过程中静态误差 的预测。Li 等[9]建立端铣仿真模型。Rai 等[10]提出加 工仿真包以分析加工变形的根本原因和选择合适的加 工策略。虽然这些有限元模型考虑铣削力的作用,但 该有限元模型在仿真过程中不能进行网格自适应细 化,因此该模型不适合大尺寸薄壁件的铣削仿真。Liu 等 [11−14] 研究夹具— 工件的完整模型以补偿变形误差 和进行夹具的优化设计。Zaghbani 等[15]研究铝合金高 速干铣过程的力—温度模型以及相关的本构模型。但 是它只是一个数学模型,不适合用于预测加工变形。 Guo 等[16]建立用于预测航空铝合金薄壁件铣削变形的 有限元模型,但在仿真过程中,该有限元模型的网格 无法进行自适应细化,因此,为获得高精度的仿真结 果,必须把网格细分,这导致在进行大尺寸薄壁件的 铣削仿真时计算成本较高。本文的目的在于建立同时 考虑仿真结果的精度和计算成本的三维铣削加工模 型,应用自适应网格细化(AMR)技术,并考虑铣削力 对薄壁件的加工变形的影响。 AMR 技术同时保证加工 变形的有效预测和较低的计算成本。在仿真过程中, 位于铣刀附近的有限元网格将被细化。考虑铣削力影 响的模型,与未考虑铣削力影响的模型相比,其仿真 结果更加准确。
1
铣削加工的有限元模型
1.1 有限元模型的网格划分 用于铣削的 7075 铝合金厚板的尺寸为(长×宽× 厚)155 mm×155 mm×40 mm。通过铣削,在该厚板 上挖去尺寸为 145 mm×145 mm×20 mm 的方形块, 留下四周壁厚为 5 mm、 底部厚度 20 mm 的薄壁零件。 选用六面体单元对模型进行网格划分,使用刚性 面模拟夹具。为模拟真实的零件铣削过程,在划分网 格之前,通过铣刀直径、铣削宽度、铣削深度和进给
为满足式(1)和(2), 将测得的厚板轧向和横向沿厚 度方向分布的残余应力曲线进行了离散和自平衡处 理,得到用于有限元模型的残余应力曲线。图 2 所示 为经离散和自平衡处理后的残余应力曲线。为将离散 和自平衡之后的残余应力数据添加到有限元模型中, 编制了 MARC 子程序。 该子程序的功能是根据每个单 元的空间位置将初始残余应力数据添加到模型的所有 单元中。 1.4 铣削力的施加 对薄壁件进行铣削加工时,铣削力对零件变形的 影响不可忽略。在铣削过程中,由于铣削力的挤压作 用,切削刃附近的局部区域将产生大应变﹑高应变率 等现象。由于大应变﹑高应变率等现象的产生过程十 分复杂,因此,在仿真中完全模拟这些现象的产生几 乎是不可能的。基于此,本文对铣削力的产生和施加 过程进行了一定程度的简化。
摘要:为预测航空铝合金薄壁件的铣削加工变形,建立三维有限元模型。通过有限元软件 MSC.MARC,向有限 元模型添加初始应力场、对节点施加铣削力、控制铣刀路径和对模型的网格进行自适应网格细化。使用该模型进 行薄壁零件的铣削仿真。仿真结果表明:铣削之后,薄壁零件呈中间凹陷、四周翘起的盆形。同时,零件的薄壁 向内部凹陷。 为检验仿真结果的正确性, 设计验证实验以测量加工后零件的变形。 实验的结果与仿真结果相吻合, 证明本文提出的有限元模型可有效预测航空铝合金薄壁件的加工变形。该有限元模型可用来选择合适的加工策略 以减小航空铝合金薄壁件的加工变形。 关键词:铝合金;薄壁零件;子程序;铣削加工;有限元模型 中图分类号:TG501;V261 文献标志码:A 文章编号:1672−7207(2012)05−1696−07
真实铣削过程中铣刀的运动是由 2 种运动合成 的:一种是铣刀绕自身的轴线旋转,另一种是铣刀的 进给运动。这 2 种运动的叠加使得铣刀铣削刃的运动 轨迹成为 1 条摆线。铣削刃的这种运动方式导致铣削 层的厚度是非均匀变化的。在真实铣削过程中,铣削 力的大小与铣削层的厚度有关。因此,以铣刀旋转 1 周所需的时间为周期,在这个周期内,铣刀的铣削刃 微段产生的铣削力是非均匀变化的,即铣削力将随着 铣削刃微段的位置的变化而变化。而铣刀产生的总体 铣削力则呈周期变化。 直接模拟铣削刃绕自身轴线的旋转和铣刀的进给 运动是困难的。为此,将铣刀的运动进行简化。图 3 显示真实的铣削刃运动轨迹与简化后的铣削刃运动轨 迹的对比。简化后,认为铣削刃在 1 个分析步中的运
速度等多个参数确定六面体单元的尺寸。图 1 给出铣 削前和铣削后的零件有限元模型。 仿真过程中,零件由刚性面固定。通过静态应变 仪测得夹具的夹持应力约为 20 MPa。 将夹持力作为边 界条件加入有限元模型中。
(a) 铣削之前的有限元模型;(b) 铣削之后的有限元模型 图1 铣削前和铣削后的零件的有限元模型 milling Fig.1 Comparison of finite element models before and after
第 43 卷第 5 期 2012 年 5 月
中南大学学报(自然科学版) Journal of Central South University (Science and Technology)
Vol.43
No.5
May 2012
航空铝合金薄壁件铣削加工变形的预测模型
王光宇,吴运新,闫鹏飞,胡永会 (中南大学 机电工程学院,湖南 长沙,410083)
r dA 0 dM 0
其中: r 为残余应力;M 为力矩;A 为截面积。
Байду номын сангаас
(1) (2)
1—轧向残余应力;2—横向残余应力 图2 离散和自平衡处理后的厚板内应力曲线 thick plate Fig.2 Discretized and self-balanced curve of internal stress of
Prediction model for machining deformation of aeronautical aluminum alloy thin-walled workpiece
WANG Guang-yu, WU Yun-xin, YAN Peng-fei, HU Yong-hui
(School of Mechanical and Electrical Engineering, Central South University, Changsha 410083, China) Abstract: In order to predict machining deformation of aeronautical thin-walled workpiece, a three-dimensional finite element model was built. By use of finite element software MSC.MARC, the initial stress to the model was added, milling force on nodes was imposed, tool path was controlled and adaptive mesh refinement (AMR) method to the model was developed for the model. Milling simulation of aeronautical thin-walled workpiece was conducted by use of the model. Simulation result shows that after machining, the workpiece presents the shape of basin, which means that the central region of the workpiece is concave and lower than the peripheral region around. In addition, the thin walls are dented toward inside of the workpiece. To test the validity of the simulation results, a verification experiment to measure the deformation of machined workpiece was conducted. The experimental result coincides with simulation result. It is proved that the proposed finite element model can effectively predict machining deformation of aeronautical aluminum alloy thin-walled workpiece. The proposed finite element model can be applied to select appropriate machining strategies to reduce machining deformation of aeronautical aluminum alloy thin-walled workpiece. Key words: aluminum alloy; thin-walled workpiece; subroutine; milling; finite element model