压力铸造工艺参数的选择
压力铸造工艺介绍
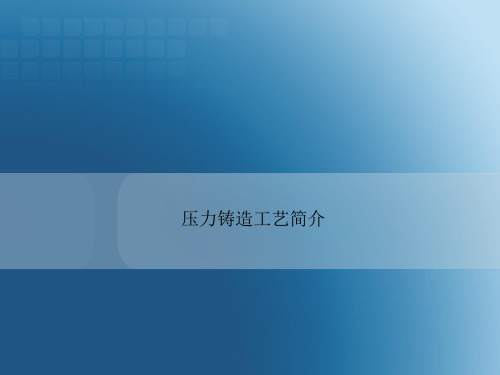
卧式压铸机
热压室压铸机
3.压铸工艺三大要素 3.2.1 卧式压铸机工作原理
3.压铸工艺三大要素 3.2.2 立式压铸机工作原理
640~680℃
200℃左右 900~980℃
1. 密度低,比强度高 2. 流动性好 3. 减震性、磁屏蔽性能好
1.熔点低,流动性好,收缩小 2.可塑性好 3.铸件表面光滑,易做各种表面处理
因熔点高,模具寿命低,应减少使用
3.2 压铸机 3.压铸工艺三大要素
压铸机一般分为冷压室压铸机和热压室压铸机两大类。 冷压室压铸机按其压室结构和布置方式分为卧式压铸机和立式压铸机两种。
3.1 压铸合金
压铸合金应具备的特性: 易于压铸:流动性、收缩性、出模性等尽可能满足压铸的要求。 机械性能:强度、延伸性、脆性等满足产品的设计要求。 机械加工性:易于加工及加工表面的质量能达到产品设计的要求。 表面处理性:抛光、电镀、喷漆、氧化等要求能达到产品设计的要求。 抗腐蚀性:产品在最终的使用环境下具有一定的抗腐蚀性。
4.1 压铸各阶段4.压铸工艺的工艺参数
t1:金属液在压室中未承受压力的时间 t2:金属液于压室中在压射冲头的作用下,通过内 浇口充填型腔的时间 t3:充填刚刚结束时的瞬间 t4.压铸工艺的工艺参数
4.2 工艺参数的选4择.压铸工艺的工艺参数
影响充型的主要因素包括:压力、速度、温度、时间,而各个因素是相互影响和制约的。调整某一 因素,其他因素也会随之变化,因此需对这些工艺参数进行正确选择和调整才能保证生产。
2.1 定义
压铸件设计与工艺资

压铸件设计与工艺资料pptxx年xx月xx日•压铸工艺简介•压铸设计原则与要求•压铸材料及性能•压铸模具设计•压铸件生产过程及控制•压铸件缺陷分析•压铸新技术与发展趋势目录01压铸工艺简介压铸是一种金属铸造工艺利用高压将金属熔液注入金属模具内形成具有特定形状和尺寸的金属零件压铸定义压铸特点快速凝固高压充型零件精度高高效生产压铸的应用范围其他需要大量金属零件的行业锁具和灯具行业家电和玩具行业汽车制造业电子和通讯行业02压铸设计原则与要求1压铸件设计原则23压铸件设计应适应压铸成型的特点,满足精度要求,避免出现不利于压铸成型的结构。
适应压铸工艺特点压铸件结构应简洁,避免过于复杂,以降低模具制造和压铸成型难度。
结构简洁设计时应考虑模具的脱模斜度,便于脱模,同时避免产生较大的侧向力。
易于脱模03圆角圆角可以改善模具的受力情况,同时还可以避免产生应力集中,提高压铸件的力学性能。
压铸件结构要素01壁厚壁厚是压铸件设计的重要结构要素之一,过薄的壁厚会导致金属填充不足,过厚的壁厚则会导致模具受力过大。
02加强筋加强筋可以增加压铸件的强度和刚度,同时还可以避免产生缩孔、缩松等缺陷。
浇口尺寸浇口的尺寸和位置应适当,以控制金属液的填充速度和填充量,避免产生冲蚀模具和填充不足等问题。
压铸件浇注系统浇口位置浇口的位置应选择在压铸件的厚壁处,以降低填充难度,同时还可以避免产生气孔、缩孔等缺陷。
溢流槽溢流槽可以收集多余的金属液,避免产生毛边和飞边等缺陷,同时还可以起到排渣和排气的作用。
03压铸材料及性能Al-Si合金是应用最广泛的压铸铝合金,具有良好的铸造性能、力学性能和抗腐蚀性能。
其中,Al-Si-Mg和Al-Si-Cu合金是常用的两种类型。
铝硅合金Al-Cu合金具有高的强度、硬度、耐磨性和耐腐蚀性,但铸造性能较差。
铝铜合金压铸铝合金力学性能压铸锌合金具有较高的强度、硬度和良好的耐磨性,但抗腐蚀性能较差。
使用范围压铸锌合金主要用于汽车、建筑、装饰等领域。
铝合金压铸技术要求
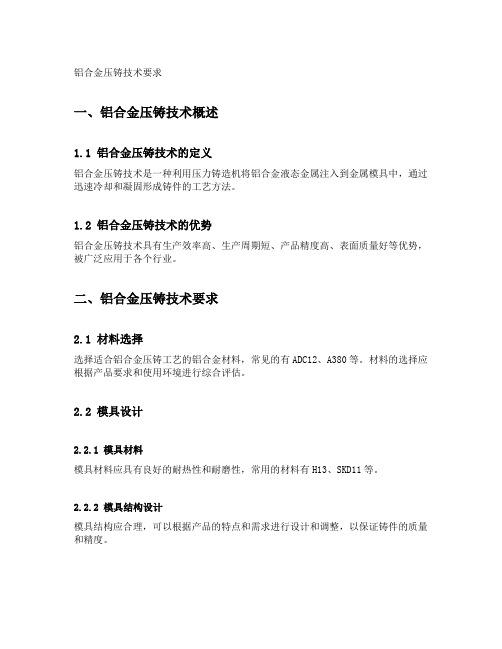
铝合金压铸技术要求一、铝合金压铸技术概述1.1 铝合金压铸技术的定义铝合金压铸技术是一种利用压力铸造机将铝合金液态金属注入到金属模具中,通过迅速冷却和凝固形成铸件的工艺方法。
1.2 铝合金压铸技术的优势铝合金压铸技术具有生产效率高、生产周期短、产品精度高、表面质量好等优势,被广泛应用于各个行业。
二、铝合金压铸技术要求2.1 材料选择选择适合铝合金压铸工艺的铝合金材料,常见的有ADC12、A380等。
材料的选择应根据产品要求和使用环境进行综合评估。
2.2 模具设计2.2.1 模具材料模具材料应具有良好的耐热性和耐磨性,常用的材料有H13、SKD11等。
2.2.2 模具结构设计模具结构应合理,可以根据产品的特点和需求进行设计和调整,以保证铸件的质量和精度。
2.3 注射设备2.3.1 压铸机选择根据产品的要求确定压铸机的型号和规格,包括锁力、注射压力等参数的选择。
2.3.2 注射系统注射系统包括注射缸、注射头、喷嘴等组成,其设计应合理,确保铝合金液态金属的注入和充填。
2.3.3 润滑系统润滑系统的设置对于铝合金压铸技术的稳定运行起着重要作用,应注意润滑剂的选择和使用。
2.4 工艺参数控制压铸工艺参数对于产品的质量和尺寸稳定性有很大的影响,应进行合理的控制和调整。
2.4.1 注射速度注射速度过快会导致铸件内部气孔、缺陷等问题,注射速度过慢会导致铝合金液态金属凝固不完全。
2.4.2 注射温度注射温度过高会导致铝合金液态金属粘度降低,流动性增强,但也会加快模具磨损。
注射温度过低则会导致液态金属凝固时间过长。
2.4.3 注射压力注射压力的控制对于铸件的密实性和表面质量有着重要影响,应根据产品要求进行精确控制。
2.4.4 注射时间注射时间应根据实际需要进行合理设置,以保证铝合金液态金属充填充实模腔。
2.5 热处理工艺铝合金压铸件在铸造成型后,经过热处理工艺可以改善其机械性能和物理性能,如固溶处理、时效处理等。
2.6 铸件表面处理铝合金压铸件的表面处理包括喷砂、喷涂、电镀等方法,以提高产品的外观质量和耐腐蚀性能。
轮毂挤压铸造数值模拟与参数优化

C A M E O 凯模C A E 案例库w w w .c a m e o .o r g .c n《热加工工艺》2013年3月第42卷第5期轮毂属于汽车的受力件,承受着汽车的全部质量。
在汽车高速运行过程中,面临着地面的摩擦、碰撞,要求有很好的强度、抗撞击能力;同时,在运行过程中,一直暴露在露天,饱受风吹雨淋,要求有一定的气密性。
总之,服役环境复杂,对其力学性能等都有很高的要求,由此选择铸造成型方法就成了关键。
1轮毂成型工艺试验方法轮毂挤压铸造成型所涉及的工艺参数很多,而每个工艺参数又有多种选择情况,工艺参数组合不同,所铸造出来的轮毂质量也不相同,如果对每种工艺参数组合都做一次试验,则试验次数繁多,甚至试验无法完成。
本文采用正交试验设计法对参数进行试验安排,通过少量试验次数,得出所需要的数据[1]。
正交试验设计,是利用规格化的正交表,恰当的设计出试验方案和有效的分析试验结果,提出最优配方和工艺条件,并进而设计出可能更优秀的试验方案的一种科学方法。
正交表则是利用“均衡搭配”与“整齐可比”这两条基本原理,从大量的全面试验中,为挑选出少量具有代表性的试验点,所制成的排列整齐的规格化表格[2]。
2轮毂成型工艺参数方案的确立挤压铸造不同于其他铸造方式之处是液态合金一直处于压力下直至凝固结束,相对于普通压铸而言,多了一个压力下补缩的过程,挤压压力是其最显著的一个工艺参数,针对38mm 铝合金汽车轮毂,已有较为成熟的挤压力取值为110MPa 。
由于在相同铸造工艺下,镁合金的压力通道阻力比铝合金要大,对于相近形状与体积铸件来说,镁合金应采用比铝合金略高的挤压力[3]。
根据轮毂“挤压压铸”的工艺特性,模具温度和合金液温度对铸件的充型和凝固过程有较大的影响。
初始加压时间以合金液充型完成开始,通过Anycasting 软件自动计算铸件体积与内浇口充型速度的比值得到,与保压时间设定为软件凝固过程模拟结束时自动结束。
3试验过程及结果分析本文针对挤压压力,合金液浇注温度,模具初始温度3个参数,选取的因素和水平表见表1。
第一节 压力铸造

各种压铸合金的浇注温度可根据下表选择:
合金 锌合金 铸件壁厚3mm 420~440 430~450 铸件壁厚>3mm 410~430 420~440 结构简单 结构复杂 结构简单 结构复杂
含硅的
铝合金 含铜的 含镁的
610~650
620~650 640~680
640~700
640~720 660~700
三、压铸种类及工艺 (一)压铸种类
1.压力和速度的选择 1)压射比压 压射比压的选择,应根据不同合金和铸件结构 特性确定,可根据下表经验数据进行选择。
合金 锌合金 铝合金 铝镁合金 镁合金 铸件壁厚3mm 30 25 30 30 40 35 40 40 铸件壁厚>3mm 50 45 50 50 60 60 65 80 结构简单 结构复杂 结构简单 结构复杂
IT11~IT13
Ra=3.2~0.8m
2)铸件的尺寸精度和表面光洁度很高。 3)铸件的强度和表面硬度较高,但伸长率较低。 4)可以压铸形状复杂的薄壁铸件。 5)生产率极高。 6)由于精度高,可简化装配操作;同时便于采用 嵌铸工艺生产复杂铸件。 7)易出现气孔,故一般压铸件不进行热处理和机 加工。 8)压铸型使用寿命短,一般用于有色金属压铸。 9)压铸只适用于大批量生产。 录像
铜合金
30
70
80
90
2)充填速度 对充填速度的选择,一般对于厚壁或内部质量 要求较高的铸件,应选择较低的充填速度和高的增 压压力;对于薄壁或表面质量要求高的铸件以及复 杂的铸件,应选择较高的比压和高的充填速度。可 根据下表经验数据进行选择。
合金 锌合金、铜合金 简单厚壁铸件 一般铸件 复杂薄壁铸件 10~15 15 15~20
录像 演示
铸造工艺学

设计铸造模具:根据铸造工艺方案和铸 件要求,设计合适的铸造模具,包括模 具结构、模具材料、模具制造工艺等。
设计铸造工艺流程:包括熔炼、浇注、冷 却、脱模等环节,以保证铸件的质量和生 产效率。
铸造工艺参数选择
浇注温度: 根据合金种 类和铸件大 小选择合适 的浇注温度
浇注速度: 根据铸件大 小和壁厚选 择合适的浇
航空航天:飞机发动机、火箭发动机 等零部件的制造
机械制造:各种机械设备的制造,如 机床、模具等
船舶行业:船舶发动机、螺旋桨等零部 件的制造
电子行业:电子元器件、集成电路等 电子产品的制造
3
铸造材料
铸造用原材料
铸铁:含碳量在 2%-4.3%之间的 铁碳合金,常用 于制造机器零件、 汽车零件等
铸钢:含碳量在 0.2%-2%之间的铁 碳合金,常用于制 造高强度、耐磨损 的零件
铸造合金材料
铸造合金的分类:铁基合金、 铝基合金、铜基合金等
铸造合金的性能:强度、硬度、 韧性、耐腐蚀性等
铸造合金的应用:汽车、船舶、 飞机、火箭等
铸造合金的发展趋势:轻量化、 高强度、耐高温、耐腐蚀等
耐火材料:用于铸造过程中的耐 高温、耐腐蚀材料
铸造用辅助材料
铸造砂:用于制造砂型和芯盒, 提供铸件形状和尺寸
感谢观看
汇报人:
浇铸设备 的设计: 包括浇铸 机、浇铸 模具等
造型设备 的设计: 包括砂箱、 砂芯盒等
制芯设备 的设计: 包括制芯 机、制芯 模具等
铸造工艺 装备的选 择:根据 铸造工艺 要求和生 产效率进 行选择
铸造工艺 装备的维 护和保养: 定期检查、 维修和更 换磨损部 件,确保 设备正常 运行。
5
铸造生产工艺
注速度
铸造技术的方法选择

铸造技术的方法选择铸造是将通过熔炼的金属液体浇注入铸型内,经冷却凝固获得所需形状和性能的零件的制作过程。
铸造是常用的制造方法,优点是:制造成本低,工艺灵活性大,可以获得复杂形状和大型的铸件,在机械制造中占有很大的比重,如机床占60~80%,汽车占25%拖拉机占50~60%。
铸件的质量直接影响着产品的质量,因此,铸造在机械制造业中占有重要的地位。
铸造是一种古老的制造方法,在我国可以追溯到6000年前。
随着工业技术的发展,铸造技术的发展也很迅速,特别是19世纪末和20世纪上半叶,出现了很多的新的铸造方法,如低压铸造、陶瓷铸造、连续铸造等,在20世纪下半叶得到完善和实用化。
由于现今对铸造质量、铸造精度、铸造成本和铸造自动化等要求的提高,铸造技术向着精密化、大型化、高质量、自动化和清洁化的方向发展,例如我国这几年在精密铸造技术、连续铸造技术、特种铸造技术、铸造自动化和铸造成型模拟技术等方面发展迅速铸造主要工艺过程包括:金属熔炼、模型制造、浇注凝固和脱模清理等。
铸造用的主要材料是铸钢、铸铁、铸造有色合金(铜、铝、锌、铅等)等。
铸造方法常用的是砂型铸造,其次是特种铸造方法,如:金属型铸造、熔模铸造、石膏型铸造......等。
而砂型铸造又可以分为粘土砂型、有机粘结剂砂型、树脂自硬砂型、消失模等等,如下图:VRH: VRH(Vacuum Replace Hardening)即真空置换硬化,其工艺过程如下:将用有机或无机粘结剂砂造好的铸型,送入真空室内抽取真空,当达到一定的真空度后,充入硬化气体;硬化气体进入砂型的砂粒间并均匀扩散,经过化学反应使砂型得到硬化。
该工艺被列为国家科技成果重点推广项目。
根据我国铸造行业的实际情况,我所于90年设计生产了第一台真空室容积为1.4立方米VRH 设备,目前我所制造的VRH设备已经被多家企业采用,其中最大容积达10立方米,产品已经形成“钟罩式”和“隧道式”两种系列。
我所竭诚欢迎全国各地客户来京考察指导。
压铸工艺参数(时间)
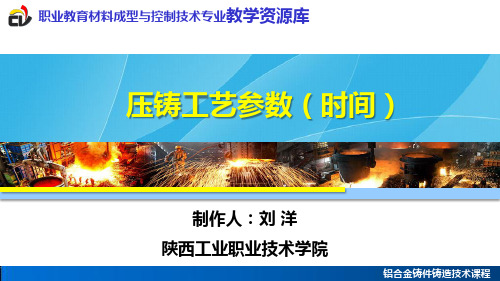
铝合金铸件铸造技术课程
职业教育材料成型与控制技术专业教学资源库
铝合金铸件铸造技术课程
职业教育材料成型与控制技术专业教学资源库
THANKS
职业教育材料成型与控制技术专业教学资源库
持压时间
从金属液充满压铸模具型腔到内浇口完全凝固,冲头压力作用在金属 液上所持续的时间称持压时间。
持压效果与余料、浇道的厚度、内浇口厚度与铸件厚度的比值有关。 持压时间的长短与合金及铸件壁厚等因素有关。熔点高、结晶温度范围大 或厚壁的铸件,持压时间需长些。反之,则可短些。
铝合金铸件铸造技术课程
职业教育材料成型与控制技术专业教学资源库
铝合金铸件铸造技术课程
职业教育材料成型与控制技术专业教学资源库
留模时间
留模时间是指持压结束到开模这段时间。 留模时间过短:铸件脱模时易引起变形或开裂,强度差的合金还可能由于 内部气体膨胀而使铸件表面鼓泡。 留模时间过长:不但影响生产率,还会因铸件温度过低收缩大,导致抽芯 及推出铸件的阻力增大,使脱模困难,热脆性合金还会引起铸件开裂。 若合金收缩率大、强度高,铸件壁薄,模具热容量大,散热快时,铸件留 模时间应短些。反之,则需长些。原则上以推出铸件不变形、不开裂的最短 时间为宜。
铝合金铸件铸造技术课程
职业教育材料成型与控制技术专业教学资源库
增压建压时间
增压建压时间是指从金属液充满型腔瞬间开始,到达预定增压压 力所需时间,也就是增压阶段比压由压射比压上升到增压比压所需的 时间。从压铸工艺角度来说,这一时间越短越好。但压铸机压射系统 的增压装置所能提供的增压建压时间是有限度的,性能较好的机器最 短建压时间也不少于0.0ls。
铝合金铸件铸造技术课程
- 1、下载文档前请自行甄别文档内容的完整性,平台不提供额外的编辑、内容补充、找答案等附加服务。
- 2、"仅部分预览"的文档,不可在线预览部分如存在完整性等问题,可反馈申请退款(可完整预览的文档不适用该条件!)。
- 3、如文档侵犯您的权益,请联系客服反馈,我们会尽快为您处理(人工客服工作时间:9:00-18:30)。
压力铸造工艺参数的选择
压力铸造high pressure die casting(简称压铸)的实质
是在高压作用下,使液态或半液态金属以较高的速度充填压
铸型(压铸模具)型腔,并在压力下成型和凝固而获得铸件的
方法。
与其它铸造方法相比,压铸有铸件尺寸精度高,产品质量好,生产效率高以及经济效益高等优势。
压力铸件的质量主要受控于压铸的填充过程中诸多因素的影响,如:压力、速度、温度、熔融金属的性质以及填充特性等等。
所以工艺参数的选择成为决定压力铸件是否成功的关
键因素。
压铸工艺是将压铸机、压铸模和压铸合金综合运用的过程。
压铸时金属填充型腔的过程,是将压力、速度、温度以及时
间等工艺因素得到有机组合的过程。
这些工艺因素既相互制约,相辅相成,只有正确选择和调整这些因素,使之协调一致,才能获得预期的结果。
压射过程中,不仅重视铸件结构
的工艺性、铸型的先进性、压铸机性能和结构优良性,压铸
合金选用的适应性和熔炼工艺的规范性。
也应重视压力、速度、温度和时间等工艺参数对铸件质量的重要作用。
这些工
艺参数的选择与合理匹配,是保证压铸件综合性能的关键。
一、压力的选择
在压力铸造的整个过程中,压射压力是压铸工艺最基本的成型参数,液态金属的充填流动和压实都是在压力和充填速
度的作用下完成的,合理选择和确定压射压力和充填速度是
压铸工艺的一个重要问题。
在压射过程中,随着冲头位置的
移动,压力也出现不同的变化,这个变化规律都会对铸件质
量产生重大影响。
1.压射力(F)
压射力是压铸机压射机构中推动压射活塞运动的力,它是反映压铸机功能的一个主要参数。
压射力的大小,由压射缸的截面积和工作液的压力所决定。
压射力的计算公式如下:
F=PπD²/4
式中:F--压射力(N);
P--压射油缸内工作液的压力(Pa);
D--压射油缸的直径(m);
π=3.1416。
2.比压(P)及其选择
比压是压室内金属液单位面积上所受的压力,填充时的比压称为压射比压。
压射后的比压称为增压比压,它决定了压铸件最终所受的压力和模具的胀型力。
比压一般是根据铸件形状、尺寸、复杂程度、壁厚、零件的要求、温度、合金特性以及浇注排气系统来选择。
比压对铸件机械性能的影响:比压增大,结晶细,表面质量提高,气孔影响减轻,从而抗拉强度提高,但延伸率有所降低。
合金熔液在高比压作用下填充型腔,合金温度升高,流动性改善,有利于铸件质量的提高。
比压的经验数据:承受轻负荷的零件的比压一般为30~40MPa;承受较大负荷的零件的比压一般为40~80MPa;气密性面和大壁薄零件的比压为80~120MPa。
拿铝合金来说,常用比压如表1所示。
表1:压铸铝合金常用比压单位:MPa
比压的计算公式:
P=4F/πD²
式中:P--压射比压(MPa);
F--压射力(N);
D--冲头直径(mm);
π=3.14。
调整比压有两种途径:调整压射力和选择不同的冲头直径。
根据压射压力与压射冲头尺寸的对应关系,使用压铸机提供
的最小压射冲头时,能够获得最大的压射压力。
压铸机的压
射力大,压射压力可调节的范围也大,压铸工艺灵活性大。
在选择压射压力时,应充分考虑压铸机能够提供的压射力及
使用的压射冲头,注意不要超出可调节的范围。
此外,高的
压射压力会加速压铸模具和机器的磨损。
所以,在保证压铸
件质量的前提下,采用较低的压力为宜。
动态压射压力及增压压射压力的选择与许多因素有关,如:压铸件结构特征、压铸合金特性、浇注系统、合金及压铸模
温度、压铸件质量标准等,选择时应该根据以上各个方面的
不同要求来综合考虑。
二、充填速度的选择
在压铸中,充填速度也是压铸工艺主要参数之一,充填速度的高低直接影响压铸件的质量,正确选用充填速度对设计
压铸模和获得合格压铸件十分重要。
充填速度过小会使压铸
件的轮廓尺寸不清晰,尺寸残缺;气孔率增加,力性能下降,但高速的金属液又会冲蚀型腔而影响压铸模的寿命。
充填速度的选择,一般应遵循的原则为:对于厚壁或内部质量要求较高的压铸件,选择较低的充填速度和高的增压比压;对于薄壁或表面质量要求高的压铸件以及复杂的压铸件,选择较高的比压和高的充填速度。
根据实际压铸设备和工艺
条件的不同,常用充填速度可参照表2。
表2 常用的充填速度 (m/s)
压射速度是指压射冲头在特定条件下运动的线速度,这一速度由压铸机的特性所决定。
压铸机所给定的压射速度一般
在0.1~7m/s范围内变动。
熔融金属在压射冲头的推动下,经过浇注系统内浇口时的速度可以认为不变或变化很小。
把流动过程看成在一封闭的
管道中进行,根据等流量连续性方程有以下关系
A₁v₁=A₂v₂
v₂=A₁v₁/A₂=πd²v₁/(4A₂)
式中:v₁为压射速度,m/s;v₂为充填速度,m/s;A₁为
压射冲头(近似压室)截面积,㎡;A₂为内浇口截面积,㎡;d为压室(压射冲头)的直径,m。
由上式可知,金属液的充填速度v₂与压室直径的平方、压射冲头的压射速度v₁成正比,而与内浇口的截面积成反比。
说明压室直径越大,充填速度也越大;压射速度越大,充填
速度相应也越大;内浇口的截面积越大,充填速度则越小。
三、温度参数的选择
这里所说的压铸温度主要是指合金浇注温度、压铸模的温度和压铸模具的的工作温度。
1、合金浇注温度
合金浇注温度是指金属液从压室进入型腔的平均温度,通常用保温炉内的温度表示,一般要求高于合金的液相线20~30℃。
浇注温度过高,合金收缩大,使压铸件容易产生裂纹,压铸件晶粒粗大,还会造成脆性;浇注温度过低,易产生冷隔、表面流纹和浇不足等缺陷。
在压力较高的情况下,应适当降
低浇注温度,这样可以有效延长压铸模使用寿命,减少产生
涡流和卷入空气,减少金属在凝固过程中的体积收缩,使缩
孔和缩松减少。
各种压铸合金的浇注温度,因其壁厚和结构
的复杂程度而不同,其值可参考表3。
表3 各种压铸合金浇注温度
2、压铸模具的的预热温度
压铸模在使用前要预热到一定的温度,压铸过程中要始终保持在一定的温度范围内。
压铸模预热的作用有三个方面:1)避免高温液体金属对冷压铸模的冲击,延长压铸模使用寿命。
压铸过程中,高温合金液直接冲击型腔,如果温差过大,会因热应力的变化而使压铸模过早疲劳失效,从而缩短使用寿命。
2)避免液体金属在模具中因激冷而过快凝固,从而失去流动性,导致压铸件不能顺利充型,造成浇不足、冷隔等铸造缺陷。
3)压铸模中,热膨胀应在生产前通过预热加以调整,否则合金液会穿入模具间隙而影响生产的正常进行。
3、压铸模具的工作温度
在连续生产中,压铸模温度会不断升高,尤其是压铸高熔点合金时,温度升高很快。
温度过高会产生液体金属粘型,还可能出现压铸件因来不及完全凝固、推出温度过高而导致变形、模具运动部件卡死等问题。
同时,过高的压铸模温度会使压铸件冷却缓慢,造成晶粒粗大而影响力学性能。
因此在压铸过程中,对压铸模温度要进行合理控制,压铸模温度过高时,应采取冷却措施。
压铸模工作温度一般可按下式计算:
t₁=⅓t₂±Δt
式中,t₁为压铸模工作温度,℃;t₂为液体金属的浇注温度,℃;Δt为温度控制公差(一般取25℃)。
例表锌合金的压铸模工作温度℃
四、时间参数的选择
压铸过程中的时间有充填时间、持压时间和留模时间三个时间段。
首先我们来看充填时间,充填时间的长短主要取决于压铸件的体积、壁厚的大小、压铸件形状的复杂程度、内浇口处的面积和充填速度等。
对大而简单的压铸件,充填时间要相对长些,对小而简单的薄壁压铸件充填时间相对短些。
压铸件的平均壁厚与充填时间的推荐值见表4。
表4 压铸件的平均壁厚与充填时间的推荐值
在压铸过程中,充填时间长,充填速度慢,有利于排气,但铸件表面粗糙度较差。
充填时间短,充填速度快,可获得良好的表面精度铸件,但铸件的致密度较差,内部的气孔量较多。
从压铸合金液充满型腔到内浇口完全凝固,在冲头压力作用下所持续的时间称为持压时间。
持压时间的作用是使压力传递给未凝固的金属,保证压铸件在压力下结晶,以获得致密的组织。
持压时间长知取决于压铸件的材料和壁薄。
对于熔点高、结晶温度范围大的厚壁压铸件,特庄时间应长些,对于熔点低、结晶温度范围小的薄壁压铸件,持压时同可以短些。
生产中常用的持压时间见表5。
表5 生产中常用的持压时间 s
从压铸终了到压铸模打开的时间,称为压铸件在模具中的留模时间。
留模时间应根据压铸件的合金性质、压铸件壁厚和结构特性来参考选择(见表6)。
以推出压铸件不变形、不开裂、保证外部尺寸和形状的最短时间为宜。
表6 各种压铸合金常用留模时间s
以上几方面的选择是压铸工艺过程中主要的参数选择,压铸件最终的参数选择主要还是需要看具体压铸件的结构、材料、形状、生产批量、质量要求以及所使用的压铸机性能等多方面因素。
当然长期生产的经验积累也是确定参数的重要一环。
参考文献:
1:《压力铸造》航空工业出版社,2018年10月;
2:《压力铸造技术与应用》天津大学出版社,2010年9月。
57。