叶轮设计计算
叶轮的设计

取:
: 8 0( n l m)
一
2 . 叶 片 螺线 平 面 图
t 一一 背 叶 片 与 涡 室 间隙 取 t = 1 mm
一
根 据 上 述 叶 轮 叶 片 曲面 螺 线 计 算 结 果 ,绘 制 叶 片 螺 线 。在
圆周 上 取 1 6 个 轴 面 ,每 两 个 轴 面 夹 角 为2 2 . 5 。 ,当 Z = O 时, 空 螺 线 在 平 面 上投 影 , 如 图 所示 :
1 9 9 7 , 2 0 ( 5 ) : 6 -1 3
3 . 叶片 厚 度 计算 确 定 叶片 厚 度 时 ,应 注 意 到 铸 造 的 可能 性 ,对 铸 铁 叶 轮 , 叶 片 最 小 厚 度 为3—4 毫 米 ,本 次 设 计 的叶 轮 材 料 选 用MT 一 4 ,叶 … 馘 拙 :
【 1 】 丁成伟 . 离心 泵 与 轴 流 泵 . 北京: 机械 工 业 出版社, 1 9 8 1
1 4 3— 1 5 8
【 2 ] A . J . 斯捷潘诺夫. 离心 泵 和 轴 流 泵 . 北京: 机 械 工 业 出 版 社
19 80: 7 4—9 3
【 3 】 劳学苏, 何希杰. 螺旋 离心泵的原理 与设计方法. 水泵技术
I
=
5. 6 8 7 (mm )
S - - 6( I T l m)
4 . 背 叶 片 的设 计
图 卜 1叶 轮 轴 面 投 影 图
背 叶片 的主 要作 用 是 减 压 ,其 减 压 程 度 决 定 了背 叶片 的 几 何 参 数 。 背 叶 片 对 于 一 般 的 泵 而 言 ,还 有 另 一 个 作 用 , 就 是 能
离心泵叶轮的设计
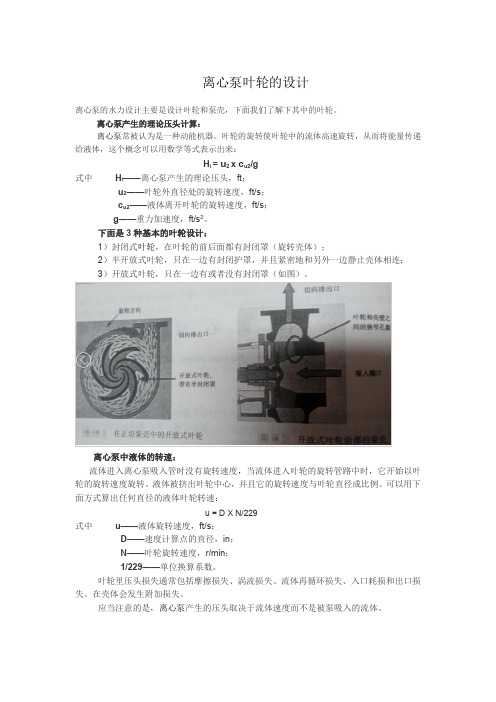
离心泵叶轮的设计
离心泵的水力设计主要是设计叶轮和泵壳,下面我们了解下其中的叶轮。
离心泵产生的理论压头计算:
离心泵常被认为是一种动能机器。
叶轮的旋转使叶轮中的流体高速旋转,从而将能量传递给液体,这个概念可以用数学等式表示出来:
H i=u2x c u2/g
式中H i——离心泵产生的理论压头,ft;
u2——叶轮外直径处的旋转速度,ft/s;
c u2——液体离开叶轮的旋转速度,ft/s;
g——重力加速度,ft/s2。
下面是3种基本的叶轮设计:
1)封闭式叶轮,在叶轮的前后面都有封闭罩(旋转壳体);
2)半开放式叶轮,只在一边有封闭护罩,并且紧密地和另外一边静止壳体相连;
3)开放式叶轮,只在一边有或者没有封闭罩(如图)。
离心泵中液体的转速:
流体进入离心泵吸入管时没有旋转速度,当流体进入叶轮的旋转管路中时,它开始以叶轮的旋转速度旋转。
液体被挤出叶轮中心,并且它的旋转速度与叶轮直径成比例。
可以用下面方式算出任何直径的液体叶轮转速:
u=D X N/229
式中u——液体旋转速度,ft/s;
D——速度计算点的直径,in;
N——叶轮旋转速度,r/min;
1/229——单位换算系数。
叶轮里压头损失通常包括摩擦损失、涡流损失、流体再循环损失、入口耗损和出口损失。
在壳体会发生附加损失。
应当注意的是,离心泵产生的压头取决于流体速度而不是被泵吸入的流体。
叶轮设计计算程序
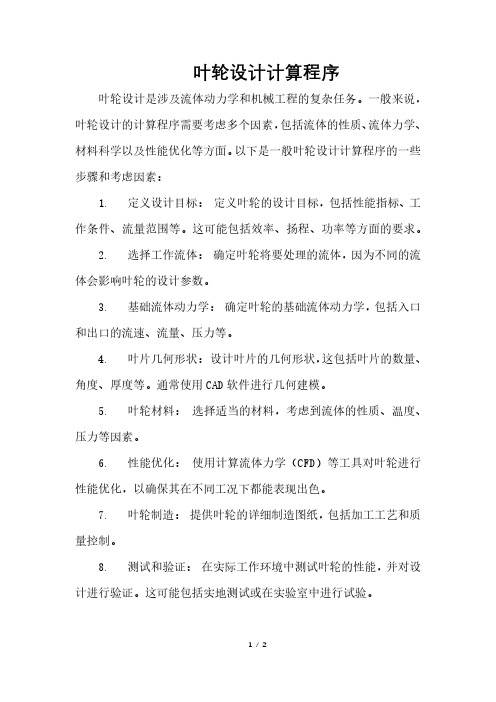
叶轮设计计算程序
叶轮设计是涉及流体动力学和机械工程的复杂任务。
一般来说,叶轮设计的计算程序需要考虑多个因素,包括流体的性质、流体力学、材料科学以及性能优化等方面。
以下是一般叶轮设计计算程序的一些步骤和考虑因素:
1. 定义设计目标:定义叶轮的设计目标,包括性能指标、工作条件、流量范围等。
这可能包括效率、扬程、功率等方面的要求。
2. 选择工作流体:确定叶轮将要处理的流体,因为不同的流体会影响叶轮的设计参数。
3. 基础流体动力学:确定叶轮的基础流体动力学,包括入口和出口的流速、流量、压力等。
4. 叶片几何形状:设计叶片的几何形状,这包括叶片的数量、角度、厚度等。
通常使用CAD软件进行几何建模。
5. 叶轮材料:选择适当的材料,考虑到流体的性质、温度、压力等因素。
6. 性能优化:使用计算流体力学(CFD)等工具对叶轮进行性能优化,以确保其在不同工况下都能表现出色。
7. 叶轮制造:提供叶轮的详细制造图纸,包括加工工艺和质量控制。
8. 测试和验证:在实际工作环境中测试叶轮的性能,并对设计进行验证。
这可能包括实地测试或在实验室中进行试验。
1/ 2
设计计算程序通常涉及使用专业的工程软件,如CAD(计算机辅助设计)、CFD(计算流体力学)等。
叶轮设计是一个高度专业化的领域,需要深厚的工程知识和经验。
设计程序的选择也取决于具体的应用和要求。
在进行叶轮设计之前,建议咨询具有相关经验的工程师或专业团队。
2/ 2。
(完整版)离心泵——叶轮设计说明书

主要设计参数本设计给定的设计参数为: 流量Q=33500.01389mmhs=,扬程H=32m ,功率P=15Kw ,转速1450minrn =。
确定比转速s n根据比转速公式343.65145046.3632s n ⨯=== 叶轮主要几何参数的计算和确定1. 轴径与轮毂直径的初步计算1.1. 泵轴传递的扭矩3159.5510955098.81450t P M N m n =⨯=⨯=⋅其中P ——电机功率。
1.2泵的最小轴径对于35号调质钢,取[]5235010Nm τ=⨯,则最小轴径0.02424d m mm ==== 根据结构及工艺要求,初步确定叶轮安装处的轴径为40B d mm =,而轮毂直径为(1.2~1.4)h B d d =,取51h d mm = 2. 叶轮进口直径jD 的初步计算取叶轮进口断面当量直径系数0 4.5K=,则0 4.50.09696D K m mm ==== 对于开式单级泵,096j D D mm == 3. 叶片进口直径1D 的初步计算由于泵的比转速为46.36,比较小,故1k 应取较大值。
不妨取10.85k =,则110.859682j D k D mm ==⨯=4. 叶片出口直径2D 的初步计算220.50.5246.369.359.3513.7310010013.730.292292s D D n K D K m mm --⎛⎫⎛⎫==⨯= ⎪⎪⎝⎭⎝⎭====5. 叶片进口宽度1b 的初步计算()002221114/4//v vm j j hvQ Q V V D D d Q b DV ηηππηπ===-=所以 220111144j j v V D D b V D K D ==其中,10v V K V =,不妨取0.8v K =,则22118535.42440.863.75jv D b mm K D ===⨯⨯6. 叶片出口宽度2b 的初步计算225/65/6246.360.640.640.33731001000.33730.00727.2s b b n K b K m mm ⎛⎫⎛⎫==⨯= ⎪⎪⎝⎭⎝⎭====7. 叶片出口角2β的确定取2β=15°8. 叶片数Z 的计算与选择取叶片数Z=8,叶片进口角0155.8β=。
叶轮设计
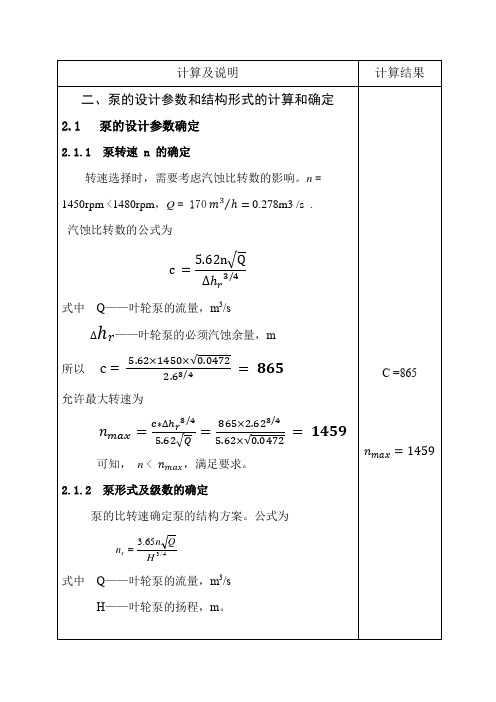
【计算过程框图】最终通过编程计算,得到D2= 325 mm四、叶轮的叶片绘型4.1. 叶轮轴面投影图的绘制1.1. 作轴面投影图图4.1 叶轮轴面投影图4.1.2 检查轴面流道过水断面的变化图10-1的作法.作出断面形成线,如图4.2。
中心的轴面液流过水断面的面积f i,公式为:计算可从进口断面开始,按断面编号列表进行。
如表4.1图4.2 过水断面积变化检查i L(mm) r c(mm) b (mm) F (mm2)1 0 79.000 48.000 238142 19.023 80.646 47.372 239923 30.575 82.154 46.603 240434 49.22 89.225 43.012 241015 50.752 96.316 40.231 243346 86.674 132.113 30.245 250937 108.967 151.764 25.33 241418 124.236 165 20 20724表4.1 过水断面面积变化检查数据轴面必须与轴面流线垂直,液体从叶轮四周流出,所以轴面液流的过水断面是以过水断面形成线为母线绕轴线旋转以后所形成的抛物面,如图4.3图4.3断面面积沿流道中线变化曲线4.3 叶片进口安放角的选择与计算4.3.1正冲角取叶片进口角大于液流角,即β′1> β1,从而在叶轮进口形成正冲角Δβ,以减少进口损失,改善空化性能,改善大流量下的工作条件。
取Δβ = 3°。
4.3.2 计算过程叶片进口处的圆周速度:u1=πD1n60= 3.14×0.12×145060=9.106式中D1---叶片进口直径,m序号i 0 1 2 3 4R i0 65表4.2进口边分点半径出口边与轴线平行,因此只需将出口边四等分即得各分点。
有了进出口点,按照流道面积相等的原则可初步大致画出各条轴面流线。
然后沿流道取7 组过水断面,不断的修改各轴面流线,直至同一过水断面上各小过水断面所包含的面积相等(相对误差在3%以内)。
泵叶轮设计计算公式

泵叶轮设计计算公式泵叶轮是泵的核心部件之一,其设计对于泵的性能和效率具有重要的影响。
在泵的设计过程中,泵叶轮的设计计算公式是至关重要的一部分。
本文将介绍泵叶轮设计计算公式的相关知识,帮助读者更好地理解泵叶轮的设计原理和计算方法。
泵叶轮的设计计算公式涉及到流体力学、动力学和材料力学等多个领域的知识,其计算过程复杂而繁琐。
但是,通过合理的公式推导和计算方法,可以有效地确定泵叶轮的结构参数,从而实现泵的高效运行和长期稳定性。
下面将介绍泵叶轮设计计算公式的相关内容。
首先,泵叶轮的设计计算公式需要考虑到泵的流体动力学特性。
泵叶轮的叶片设计应符合流体动力学的要求,以确保流体在叶轮内部的流动是稳定和均匀的。
在泵叶轮的设计计算公式中,通常会涉及到叶片的进口角、出口角、叶片数目、叶片弯曲角等参数。
这些参数的选择需要考虑到流体的流动速度、压力变化、叶轮的转速等因素,以实现泵的高效运行。
其次,泵叶轮的设计计算公式还需要考虑到泵的动力学特性。
泵叶轮的设计应符合泵的功率、扬程、流量等动力学要求,以满足不同工况下的使用需求。
在泵叶轮的设计计算公式中,通常会涉及到叶轮的直径、叶片长度、叶片厚度、叶轮的转速等参数。
这些参数的选择需要考虑到泵的工作条件、流体的物性、泵的效率等因素,以实现泵的高效运行和长期稳定性。
此外,泵叶轮的设计计算公式还需要考虑到泵的材料力学特性。
泵叶轮的设计应符合泵的强度、刚度、耐磨性等材料力学要求,以确保泵在长期运行中不会出现失效和损坏。
在泵叶轮的设计计算公式中,通常会涉及到叶轮的材料、叶片的截面形状、叶片的横截面积等参数。
这些参数的选择需要考虑到泵的工作条件、流体的物性、泵的运行环境等因素,以实现泵的长期稳定性和可靠性。
综上所述,泵叶轮的设计计算公式涉及到流体力学、动力学和材料力学等多个领域的知识,其计算过程复杂而繁琐。
但是,通过合理的公式推导和计算方法,可以有效地确定泵叶轮的结构参数,从而实现泵的高效运行和长期稳定性。
叶轮机械设计

四、 CFD分析
4后处理分析
四、 CFD分析
后处理分析
五、喘振探讨
1.喘振 2.喘振的成因 3.预防的措施
五、喘振探讨
喘振的成因
五、喘振探讨
预防的措施
(1)在轴流式压气机的第一级或前几级,装设可转动的导 叶。
(2)在压气机通流部分的某一个或若干个截面上,安装防 喘放气阀。
2.感谢毕业设计小组的其他同学,在毕业设计过程中大家相互鼓 励、相互帮助,同舟共济,共同解决了许多问题。
3.最后衷心的感谢在我大学四年中所有传授给我知识的老师们, 是他们给了我充足的营养,让我能够茁壮的成长。今后我一定会 更加努力的学习和工作,以优异的成绩来回报恩师,为母校争光!
2.通流部分各级平均直径的确定
二、气动计算
各级气动参数的选择 和平均直径的校核流 程图
二、气动计算
叶型的计算
1.截面叶型参数的计算 2.流型的选择 3.叶片的叠加
二、气动计算
1.截面叶型参数 的计算
二、气动计算
第一级流型的对比
二、气动计算
叶片的叠加
叠加的方式有两种:重心叠加和前缘叠加
一、摘要
1 压气机是燃气轮机的三大部件之一。 2设计过程复杂,要反复的迭代计算。
二、气动计算
1.首末级通流尺寸的计算以及级数确定 2.通流部分各级平均直径的确定 3.各级气动参数的选择和平均直径的校核 4.叶型的计算
二、气动计算
1.首末级通流尺寸的 计算以及级数确定流 程图
二、气动计算
四、 CFD分析
1.实体建模
四、 CFD分析
1实体建模
动叶模型
静叶模型
四、 CFD分析
整体装配模型
四、 CFD分析
风机叶轮强度计算

风机叶轮强度计算一、引言在风力发电领域,风机叶轮是将风能转化为机械能的关键部件。
叶轮的强度计算对于确保风机的安全运行至关重要。
本文将从叶轮的设计和材料选择等方面进行探讨,以提供一种有效的风机叶轮强度计算方法。
二、叶轮设计与材料选择1. 叶轮设计叶轮的设计应考虑到风力的大小、方向和速度等因素。
通常,叶轮的形状采用空气动力学原理进行优化,以确保最大限度地捕捉风能。
同时,叶轮的叶片数量和叶片角度也需要精确计算,以实现最佳的风能转换效率。
2. 材料选择叶轮的材料选择对其强度至关重要。
常见的叶轮材料包括钢、铝合金和复合材料等。
钢具有较高的强度和耐久性,但重量较大;铝合金轻巧但强度稍低;复合材料则具有较高的强度和轻量化的特点。
根据不同的设计需求和成本因素,选择适合的材料是必要的。
三、叶轮强度计算方法叶轮强度计算是确保叶轮在运行过程中不会发生破裂或变形的关键步骤。
下面介绍一种常用的叶轮强度计算方法。
1. 叶片应力计算叶片应力是叶片强度的重要指标,通常使用叶片应力公式来计算。
该公式基于叶片的几何形状、材料弹性模量和转速等参数。
通过对叶片应力进行分析,可以确定叶片的强度是否满足设计要求。
2. 叶轮强度校核叶轮强度校核主要包括静态强度和疲劳强度两个方面。
静态强度是指叶轮在额定工况下承受的最大静载荷,通过静态强度分析可以确定叶轮的材料和结构是否满足要求。
疲劳强度是指叶轮在长期运行过程中所承受的循环载荷,通过疲劳强度分析可以评估叶轮的寿命和可靠性。
3. 强度计算结果评估根据叶轮的设计要求,将强度计算结果与设计指标进行对比评估。
如果强度计算结果满足设计要求,则可以继续进行下一步的制造和测试工作;如果不满足,则需要重新进行设计或调整。
四、结论风机叶轮强度计算是确保风机安全运行的关键环节。
正确选择叶轮的设计和材料,采用合适的强度计算方法,可以保证叶轮在各种工况下的稳定性和可靠性。
本文介绍的叶轮强度计算方法为风机叶轮的设计和制造提供了一种有效的参考方式。
- 1、下载文档前请自行甄别文档内容的完整性,平台不提供额外的编辑、内容补充、找答案等附加服务。
- 2、"仅部分预览"的文档,不可在线预览部分如存在完整性等问题,可反馈申请退款(可完整预览的文档不适用该条件!)。
- 3、如文档侵犯您的权益,请联系客服反馈,我们会尽快为您处理(人工客服工作时间:9:00-18:30)。
叶轮设计
计算过程
设计参数取值
流量Q250.006944取值0.007扬程H20转速n
确定泵进出口直径
泵进口直径Ds0.054520.056
泵出口直径Dd0.0436160.044
泵进口速度vs 2.843494 2.84
泵出口速度vd 4.60599 4.6
比转数ns93.6412993
确定效率
水利效率ηh0.8436520.844
容积效率ηv0.9679350.97
圆盘损失效率η′m0.923815
机械效率ηm0.85
总效率η0.6958780.7
确定功率
轴功率P 1.962ρ1000配套功率P′ 2.4 2.4K 1.2扭矩Mn7.9034487.9
最小轴径d0.0104110.012[τ]35000000初步确定叶轮主要尺寸
进口当量直径Do0.0474860.06Ko 3.54叶轮进口直径Dj0.060.06Dh0叶轮出口宽度b20.0080810.01Kb20.602443叶轮外径D20.1300580.13KD29.695498叶片出口角β220
叶片数Z 6.0312796D10.06第一次精算叶轮外径
理论扬程Ht23.6966823.7
修正系数ψ0.8266670.83α0.62静矩0.003
有限叶片数修正系数p0.1948190.195
无穷叶片数理论扬程Ht28.321528.3
叶片出口排挤系数ψ20.7850150.785δ5出口轴面速度vm2 2.252079 2.25
出口圆周速度u220.0308620
出口直径D2(1)0.1317810.132
第二次精算叶轮外径
叶片出口排挤系数ψ20.7882720.788
出口轴面速度vm2 2.209513 2.21
出口圆周速度u219.9659320
叶轮外径D2(2)0.1317810.132
说明: Δ0
叶轮主要尺寸为:Dj60
b210
D2132
叶轮出口速度
叶片出口排挤系数ψ20.7882720.788
出口轴面速度vm2 2.209513 2.21
出口圆周速度u220.033220出口圆周分速度Vu211.61311.6无穷叶片数出口圆周分
Vu2∞13.86713.867速度
2900NPSHr3η进口流速
vs
3
g9.8
β120
λ290
填充数据
计算数据
给定数据
不确定数
据
叶轮主要
尺寸。