第二章材料表面清理与精整
上篇第二章 工程材料的改性

2020年5月29日星期五
机械制造基础--上篇第二章 工程材料的改性
2、钢的淬火
淬火是将钢件加热到Ac3或Ac1以上(30~50)℃,保温 一定时间,然后以大于淬火临界冷却速度冷却获得马氏体 或贝氏体组织的热处理工艺。
淬火的目的是: 提高金属材料的强度和硬度,增加耐磨性。既要得到 马氏体组织,同时又要避免产生变形和开裂。
2020年5月29日星期五
机械制造基础--上篇第二章 工程材料的改性
正火是成本较低和生产率较高的热处理工艺。在生产中 应用如下:
• 对于要求不高的结构零件,可作最终热处理 • 改善低碳钢的切削加工性 • 作为中碳结构钢的较重要工件的预先热处理 • 消除过共析钢中二次渗碳体网,为球化退火作组织准
备
10
机械制造基础--上篇第二章 工程材料的改性
第二章 工程材料的改性
1
2020年5月29日星期五
机械制造基础--上篇第二章 工程材料的改性
一、钢的改性工艺
钢的热处理是指将钢在固态下进行加热、保温和冷却,以改变其内部 组织,从而获得所需要性能的一种工艺方法。
热处理的目的是:
•显著提高钢的力学性能,发挥钢材的潜力 •提高工件的使用性能和寿命 •还可以消除毛坯(如铸件、锻件等)中缺陷,改善
11
2020年5月29日星期五
机械制造基础--上篇第二章 工程材料的改性
3、钢的回火
将淬火钢重新加热到Acl点以下的某一温度,保温一定时 间后冷却(空冷或水冷)到室温的热处理工艺称为回火。 一般淬火件必须经过回火才能使用。
回火的目的:
•获得工件所要求的力学性能 •稳定工件尺寸 •降低脆性,消除或减少内应力
机械制造基础--上篇第二章 工程材料的改性
第四节精整和光整加工

一, 研磨
1,基本原理: ,基本原理: 研磨是利用涂敷或压嵌游离磨粒与研磨剂的混合物于一定刚 性的软质研具上,在一定压力下, 性的软质研具上,在一定压力下,通过研具与工件作复杂的 相对滑动,经过研磨剂的机械及化学作用, 相对滑动,经过研磨剂的机械及化学作用,从工件上切除很 薄的一层材料,从而达到很高的精度和很小的粗糙度. 薄的一层材料,从而达到很高的精度和很小的粗糙度. 研具:是涂敷或嵌入磨料的载体,使磨料发挥切削作用, 研具:是涂敷或嵌入磨料的载体,使磨料发挥切削作用,同 时又是研磨的成形工具. 时又是研磨的成形工具.
四 抛光 1基本原理和方法 基本原理和方法 抛光是将工件以一定压力压于涂以抛光膏, 抛光是将工件以一定压力压于涂以抛光膏,并以 高速旋转的抛光软轮上, 高速旋转的抛光软轮上,对工件表面进行光整加 工的方法. 工的方法. (2)特点与应用 特点与应用 1.方法简便经济 方法简便经济 2.易加工曲面 易加工曲面 3.仅能提高表面质量 仅能提高表面质量 4.劳动条件差 劳动条件差 应用: 应用:零件表面的装饰加工或提高零件表面的疲 劳强度. 劳强度.
根据磨料是否嵌入研具的情况, 研磨可分为嵌砂研磨和无 嵌砂研磨两种: 1.嵌砂研磨 2.无嵌砂研磨 3.超精密研磨 超精密研磨是一种加工精度达0.1微米以下,表面光 洁度在 R 0.012 以上的研磨方法.
外圆的超精加工
2特点与应用
设备简单, 1.设备简单,操作方便. 设备简单 操作方便. 2.生产效率高 生产效率高 3.表面质量好 表面质量好 4.不能提高工件的加工精度 不能提高工件的加工精度 应用: 应用:汽车内燃机零件 轴承 精密量具 等.
�
一.珩磨 加工原理:珩磨是一种用装有固结磨粒(油石) 1 . 加工原理 : 珩磨是一种用装有固结磨粒 ( 油石 ) 的磨 及压力进给切削的精加工方法. 具,及压力进给切削的精加工方法. 珩磨是一种在大批大量和成批生产中,孔的精加工方 珩磨是一种在大批大量和成批生产中 孔的精加工方 其工作原理见图4 所示. 法,其工作原理见图4-3-1所示. 珩磨的特点及应用: 2.珩磨的特点及应用 珩磨的特点及应用 特点: 生产效率高 生产效率高, 特点:1.生产效率高,珩磨头 相对工件运动速度高,刚性大, 相对工件运动速度高,刚性大, 压力大, 压力大,又有多个磨条同时连续 工作. 工作. 珩磨余量 铸铁件0 02 余量: 02- 15 15mm 珩磨余量:铸铁件0.02-0.15
第二章-典型零件的加工-套筒
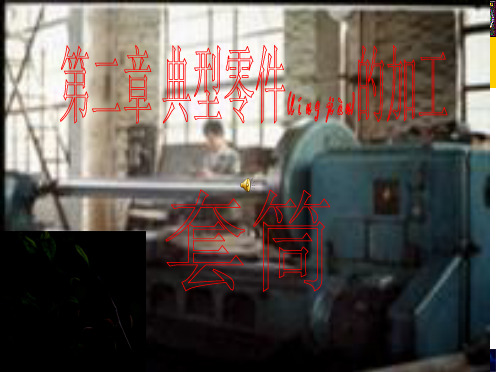
第二章 典型(diǎnxíng)零件的加工—套 筒
序号 工序名称 工 序 内 容
01 下料
Φ48×130mm(五件合一)
02 车(一刀 车端面,Ra10μm,钻、镗孔,
活)
留磨余量0.3mm,车外圆,
留磨余量0.3mm,倒角,切断;
调头,车端面,保证尺寸20mm, Ra10μm,倒角;
第二章 典型零件(línɡ jiàn)的加工—套筒
套筒类零件虽然种类众多、形态各异,但按其结构 形状来分,大体上可分为短套筒和长套筒两类。由于这两 类套筒零件结构形状上的差异,其工艺过程有很大的差 别。
长套筒类零件工艺过程分析 一、长套筒零件的加工(jiā gōng)分析
液压系统中的油缸体如图所示,是比较典型的长套 筒零件,一般结构简单,薄壁容易变形,加工面比较少, 加工方法变化不多。
第二十一页,共四十二页。
第二章 典型零件(línɡ jiàn)的加工—套
筒
2)防止套筒在加工过程中变形的措施 套筒零件孔壁较薄,加工中常因夹紧力、切削力、
残余应力和切削热等因素的影响而产生变形。为了防止 变形,应注意以下几点: (1)为减少切削力与切削热的影响:粗、精加工应分开进行,
使其变形在精加工过程中得以纠正;
(3)如图(c)所示:缸筒以一端止口定位,用螺纹与连接 盘连接在机床主轴上;另一端用中心架支承。这种方法 用螺纹传递(chuándì)扭矩,缸体基本不受径向夹紧力作用, 能保证加工精度,
但加工完毕后,须切除 螺纹部分,增加了工序
和材料的浪费,适用于
小批量生产。
第十四页,共四十二页。
第二章 典型零件(línɡ jiàn)的加工—套筒
第十六页,共四十二页。
第二章第一、二、三、四节

前角的作用
前角越大, 刀越锋利、切削轻快, 强度下降、不利散热
后角的作用
减小主后刀面与加 工表面的摩擦
刃倾角的作用
刃倾角对切屑排出方向的影响
4、刀具角度的选择
1)前角γO
(1)功用
γ
O
刀刃锋利
,切屑变形
切削力和切削功率 刀具寿命
刀刃和刀尖强度
,散热体积
影响: 1)切屑弹缩性变形 2)切屑与前刀面摩擦阻力 3)切削力、切削热 4)刀具使用寿命 5)加工质量
42
图2-19 麻花钻的几何角度
43
(4)后角α f
是在假定工作平面内测 量的切削平面与主后刀面之 间的夹角 。
为改善切削条件,并能与切削刃上变化的前 角相适应,而使各点的楔角大致相等,麻花钻的 后角刃磨时应由外缘向中心逐渐增大。
44
(5)横刃角度
横刃角度包括横刃斜角ψ、 横刃前角γoψ、和横刃后角α
1、刀具切削部分的组成 车刀:刀杆和刀头两部分 车刀的切削部分:
前刀面—切屑沿其流出的刀面 主后刀面—与工件加工面相对的刀面 副后刀面—与工件已加工面相对的刀面 主刀刃—前刀面与主后刀面的交线,它完成主要切削工作 副刀刃—前刀面与副后刀面的交线,它配合主刀刃最终形 成已加工表面 刀尖(过渡刃)—主刀刃与副刀刃的交点
(1)扩孔钻的类型
(2)扩孔钻与麻花钻的比较
1)刀齿数多(3~4个),故导向性好,切削平稳; 2)刀体强度和刚性较好; 3)没有横刃,改善了切削条件。 因此,大大提高了切削效率和加工质量。
48
高速钢整体式
镶齿套式
49
3. 铰 刀
用于中、小尺寸孔的半精 加工和精加工,IT6 ~ IT8级; 表面粗糙度1.6 ~ 0.4μm 。 图2-22
第二章冲裁教学课件

落料:以凹模为基准(即:先确定凹模尺寸),间隙取在
凸模上;
冲孔:以凸模为基准(即:先确定凸模尺寸) ,间隙取在
凹模上。
(2) 考虑冲模的磨损规律
落料模:凹模基本尺寸应取接近或等于工件的最小极限尺寸; 冲孔模:凸模基本尺寸应取接近或等于工件的最大极限尺寸。
第二章 冲裁
(3) 凸、凹模刃口制造公差
第二章 冲裁
图2.6.1 级进冲裁
第二章 冲裁
(2) 冲裁顺序的安排 (a) 级进冲裁的顺序安排 ① 先冲孔或切口,最后落料或切断; ② 采用定距侧刃时,定距侧刃切边工序应安排与首次冲孔
同时进行。
(b) 多工序工件用单工序冲裁时的顺序安排 ① 先落料,使毛坯与条料分离,再冲孔或冲缺口; ② 冲裁大小不同、相距较近的孔时,应先冲大孔再冲小孔。
形状简单的刃口制造偏差:按IT6~IT7级; 形状复杂的刃口制造偏差:取冲裁件相应部位公差的1/4; 对刃口尺寸磨损后无变化的制造偏差:取冲裁件相应部位 公差的1/8并冠以(±)。 (4) 新模具采用最小合理间隙值 凸凹模磨损到一定程度时,仍能冲出合格制件。
(5) 尺寸偏差标注原则 落料件一般标注单向负公差(上偏差为零,下偏差为负);冲 孔件一般标注单向正公差(上偏差为正,下偏差为零)。
特点:
(a)模具的间隙在配制中保证,加工基准件时可适当放宽 公差,使加工容易。根据经验,普通冲裁模具的制造偏差 p 或
d 一般可取 Δ/ 4( Δ为制件公差)。
(b)尺寸标注简单,只在基准件上标注尺寸和制造公差, 配作件只标注公称(基本)尺寸并注明配做所留的间隙值。
但该方法制造的凸模、凹模是不能互换的。
第二章 冲裁
第二章冲裁教学课件
有色金属加工技术与生产作业指导书
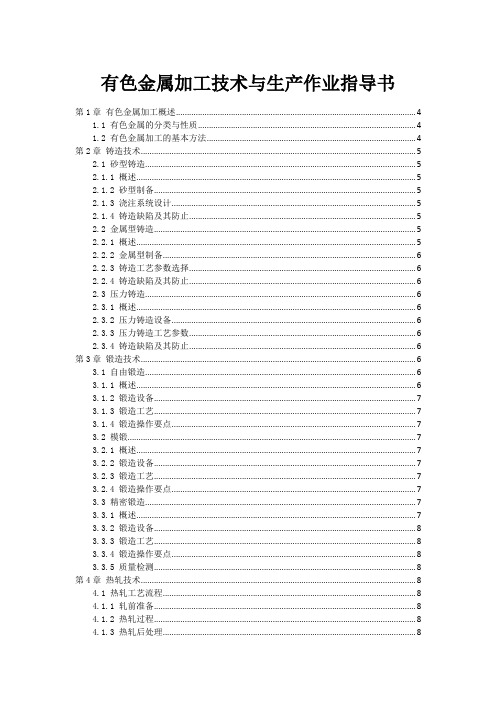
有色金属加工技术与生产作业指导书第1章有色金属加工概述 (4)1.1 有色金属的分类与性质 (4)1.2 有色金属加工的基本方法 (4)第2章铸造技术 (5)2.1 砂型铸造 (5)2.1.1 概述 (5)2.1.2 砂型制备 (5)2.1.3 浇注系统设计 (5)2.1.4 铸造缺陷及其防止 (5)2.2 金属型铸造 (5)2.2.1 概述 (5)2.2.2 金属型制备 (6)2.2.3 铸造工艺参数选择 (6)2.2.4 铸造缺陷及其防止 (6)2.3 压力铸造 (6)2.3.1 概述 (6)2.3.2 压力铸造设备 (6)2.3.3 压力铸造工艺参数 (6)2.3.4 铸造缺陷及其防止 (6)第3章锻造技术 (6)3.1 自由锻造 (6)3.1.1 概述 (6)3.1.2 锻造设备 (7)3.1.3 锻造工艺 (7)3.1.4 锻造操作要点 (7)3.2 模锻 (7)3.2.1 概述 (7)3.2.2 锻造设备 (7)3.2.3 锻造工艺 (7)3.2.4 锻造操作要点 (7)3.3 精密锻造 (7)3.3.1 概述 (7)3.3.2 锻造设备 (8)3.3.3 锻造工艺 (8)3.3.4 锻造操作要点 (8)3.3.5 质量检测 (8)第4章热轧技术 (8)4.1 热轧工艺流程 (8)4.1.1 轧前准备 (8)4.1.2 热轧过程 (8)4.1.3 热轧后处理 (8)4.2.1 设备选型 (9)4.2.2 工艺参数 (9)4.3 热轧产品质量控制 (9)4.3.1 原料质量控制 (9)4.3.2 加热质量控制 (9)4.3.3 轧制过程质量控制 (9)4.3.4 成品质量控制 (9)4.3.5 质量改进 (9)第5章冷轧技术 (10)5.1 冷轧工艺流程 (10)5.1.1 原材料准备 (10)5.1.2 热轧 (10)5.1.3 冷轧 (10)5.1.4 退火 (10)5.1.5 精整 (10)5.2 冷轧设备与工艺参数 (10)5.2.1 冷轧设备 (10)5.2.2 工艺参数 (10)5.3 冷轧产品质量控制 (10)5.3.1 原材料质量控制 (10)5.3.2 轧制过程质量控制 (11)5.3.3 退火过程质量控制 (11)5.3.4 精整过程质量控制 (11)第6章精密切削加工 (11)6.1 车削加工 (11)6.1.1 概述 (11)6.1.2 工艺参数 (11)6.1.3 切削工具 (11)6.1.4 操作要点 (12)6.2 铣削加工 (12)6.2.1 概述 (12)6.2.2 工艺参数 (12)6.2.3 切削工具 (12)6.2.4 操作要点 (12)6.3 钻削加工 (12)6.3.1 概述 (12)6.3.2 工艺参数 (12)6.3.3 切削工具 (13)6.3.4 操作要点 (13)第7章特种加工技术 (13)7.1 电化学加工 (13)7.1.1 概述 (13)7.1.2 基本原理 (13)7.1.4 应用领域 (13)7.2 高能束加工 (14)7.2.1 概述 (14)7.2.2 基本原理 (14)7.2.3 加工特点 (14)7.2.4 应用领域 (14)7.3 超声波加工 (14)7.3.1 概述 (14)7.3.2 基本原理 (14)7.3.3 加工特点 (14)7.3.4 应用领域 (15)第8章表面处理技术 (15)8.1 表面清理与预处理 (15)8.1.1 清理方法 (15)8.1.2 预处理工艺 (15)8.2 表面涂覆层制备 (15)8.2.1 涂覆方法 (15)8.2.2 涂覆材料 (15)8.2.3 涂覆工艺 (15)8.3 表面处理质量检测 (15)8.3.1 检测方法 (15)8.3.2 检测标准 (15)8.3.3 检测仪器与设备 (15)8.3.4 质量控制 (16)第9章有色金属连接技术 (16)9.1 焊接连接 (16)9.1.1 概述 (16)9.1.2 焊接方法 (16)9.1.3 焊接材料 (16)9.1.4 焊接工艺参数 (16)9.2 胶接连接 (16)9.2.1 概述 (16)9.2.2 胶粘剂 (16)9.2.3 胶接工艺 (16)9.3 机械连接 (17)9.3.1 概述 (17)9.3.2 紧固件 (17)9.3.3 连接工艺 (17)9.3.4 检验 (17)第10章生产作业管理 (17)10.1 生产计划与调度 (17)10.1.1 计划编制 (17)10.1.2 调度管理 (17)10.2.1 工艺参数控制 (17)10.2.2 设备维护与管理 (17)10.2.3 操作人员培训与管理 (18)10.3 质量管理与售后服务 (18)10.3.1 质量管理体系 (18)10.3.2 检验与检测 (18)10.3.3 售后服务 (18)10.3.4 客户满意度调查与改进 (18)第1章有色金属加工概述1.1 有色金属的分类与性质有色金属是指除了铁、锰、铬以外的所有金属,以及金属间化合物。
钢铁镀锌工艺流程
钢铁镀锌工艺流程钢铁镀锌工艺流程是将钢铁材料经过一系列处理,涂上一层锌层的工艺过程。
镀锌不仅可以保护钢材不受到氧化腐蚀,也可以延长钢材的使用寿命。
以下是一个典型的钢铁镀锌工艺流程。
第一步:预处理钢铁材料在进行镀锌之前需要先进行一系列的预处理。
首先,对钢铁材料进行清洗,将材料表面的油污、灰尘等杂质清除掉。
然后,将材料浸泡在脱脂槽中,去除材料表面的油脂。
最后,对材料进行酸洗,去除表面的氧化物和铁锈。
第二步:烘干经过预处理的钢铁材料需要进行烘干,以去除表面的水分。
烘干的方式可以是自然干燥或者采用热风炉进行加热烘干。
第三步:镀锌在烘干后,将钢铁材料浸入镀锌槽中。
镀锌槽中的溶液一般是由氯化铵、氯化锌等化学物质组成的,能够提供锌离子。
钢铁材料通过电解作用,将锌离子还原成锌金属,使其沉积在钢铁材料的表面上。
离子那边,使溶液中的锌离子不断补充,保持锌层的均匀性和密度。
第四步:冷却钢铁材料经过镀锌之后,需要进行冷却,以确保镀锌层的稳定性。
冷却的方式可以是自然冷却或者使用冷却水进行快速冷却。
第五步:除油经过冷却的钢铁材料需要进行除油处理。
这是为了去除镀锌过程中残留的油污,使得镀锌层更加牢固。
第六步:精整除油后的钢铁材料需要进行精整处理。
精整是通过机械或者化学方法,去除表面的粗糙和不平整,使得钢铁材料表面更加光滑细腻。
第七步:涂层最后一步是对钢铁材料进行涂层处理。
涂层可以起到增强防腐性能、增加美观度和保护钢铁材料等作用。
综上所述,钢铁镀锌工艺流程包括预处理、烘干、镀锌、冷却、除油、精整和涂层等主要步骤。
这一工艺流程能够有效地保护钢铁材料不受到氧化腐蚀,延长其使用寿命。
同时,还可以提高钢铁材料的美观度和装饰性,使其更加适合于各种应用领域。
第二章 锻造
材料及热加工工艺—第三篇 金属塑性加工
2) 坯料质量及尺寸计算 坯料质量的计算公式: 坯料质量的计算公式
根据: 根据:锻件图
m坯料 = m锻件 + m烧损 + m料头
其中: 取决于加热次数(火次), ),首次加热 其中:m烧损取决于加热次数(火次),首次加热 取被加热金属质量2 3%;以后每次取1.5 2%。 1.5取被加热金属质量2-3%;以后每次取1.5-2%。 m料头指锻造过程中被冲掉或切掉的那部分金属的 质量。 质量。 确定坯料的尺寸: 确定坯料的尺寸: 根据坯料重量和几何形状来确定, 根据坯料重量和几何形状来确定,还应考虑坯料 在锻造中所必需的变形程度,即锻造比的问题。 在锻造中所必需的变形程度,即锻造比的问题。
西安理工大学材料科学与工程学院 school of material science and engineering of XAUT
材料及热加工工艺—第三篇 金属塑性加工
西安理工大学材料科学与工程学院 school of material science and engineering of XAUT
西安理工大学材料科学与工程学院 school of material science and engineering of XAUT
材料及热加工工艺—第三篇 金属塑性加工
3) 选 择 锻 造 工 序
西安理工大学材料科学与工程学院 school of material science and engineering of XAUT
西安理工大学材料科学与工程学院 school of material science and engineering of XAUT
材料及热加工工艺—第三篇 金属塑性加工
材料成型概论 第三章 轧制成型2
轧机按轧辊装配形式分类
按轧辊的数目、放置、大小来区分轧机的基本型式 为:表3-2
3.4.1 轧钢生产系统
轧钢生产工艺过程: 由钢锭或钢坯轧成具有一定规格和性能的钢材的一 系列加工工序的组合。
❖ 在提高质量和产量的同时,力求降低成本是制定轧 钢生产工艺过程的总任务和总依据。
❖ 碳素钢和合金钢的基本典型生产工艺过程如下图所 示。
3.4.1 轧钢生产系统
轧钢生产工艺过程总包括六大工序: 热轧工艺系统—— 坯料准备→加热→轧制→冷却→精整→验收入库 冷轧工艺系统—— 坯料准备→酸洗→轧制→退火→精整→验收入库
材料也比较稀贵,产量不大而产品种类繁多。 ❖ 常属中型或小型的型钢生产系统或混合生产系统。
❖ 各种轧钢生产系统组成见下表。
3.4.1 轧钢生产系统
轧材生产系统的发展: ❖ 向大型化、连续化、自动化方向发展。 ❖ 工艺流程经历了“长流程”到“短流程”的发展过
程。 ❖ 目前“长流程”和“短流程”共存。 ❖ 长流程主要吃铁水,短流程主要吃废钢。
❖ 采用连铸板坯作为轧制板带钢的原料是今后发展的 必然趋势。
3.4.1 轧钢生产系统
型钢生产系统 热轧线材、热轧棒材、热轧H型钢、热轧型钢
❖ 型钢生产系统的规模往往不很大,就规模而言可分 为大型、中型和小型三种生产系统。
❖ 年产100万t以上的称大型生产系统;年产30~ 100万t称中型生产系统;年产30万t以下的称小型 生产系统。
机电设备装调与维修第二章.doc
精品文档课题序号 1 授课班级08 机电 1、 2、 3、4(五)授课课时 2 授课形式新授课第二章设备装配基础知识授课章节2.1 机器装配概述名称2.2零件的清洗使用教具课件1、掌握装配的概念和工艺过程教学目的2、掌握生产类型的概念及分类3、掌握零件的清洗方法和过程1、零件的清洗方法和过程教学重点2、生产类型的概念及分类教学难点1、装配的概念和工艺过程更新、补充、删节内容课外作业习题与思考题2— 1、 2— 2、2— 3、 2—4教学后记零件的清洗学生掌握较好,因为浅显易懂。
授课主要内容或板书设计第二章机电设备装配基本知识2.1 机器装配概述2.1.1 装配的概念机械产品是由许多零、部件组成,按照规定的技术要求,将若干个零件组装成部件或将若干个零件和部件组装成产品的过程,称作装配。
组件部件2.1.2 装配的工艺过程准备工作四装配工作步调整、检验、试运转骤喷漆、涂油、装箱等2.1.3 生产类型及组织形式2.1.4 装配工艺规程2.1.5 装配精度2.2 零件的清洗2.2.1 装配时,对零件的清理和清洗内容2.2.2 设备清洗用材料和工具清洗常用的布头、棉纱、砂布;清洗液有汽油、煤油、轻柴油和化学清洗液等。
2.2.3 装配时,对零件的清理清洗方法及步骤课堂教学安排教学过程主要教学内容及步骤[复习 ][新课 ]第二章机电设备装配基本知识2.1 机器装配概述2.1.1 装配的概念机械产品是由许多零、部件组成,按照规定的技术要求,将若干个零件组装成部件或将若干个零件和部件组装成产品的过程,称作装配。
组件部件2.1.2 装配的工艺过程准备工作四步骤装配工作调整、检验、试运转喷漆、涂油、装箱等2.1.3 生产类型及组织形式生产类型一般可分为三类: 单件生产、成批生产和大量生产。
单件生产:件数很少,甚至完全不重复生产的,单个制造的一种生产方式成批生产:每隔一定时期后,成批地制造相同的产品大量生产:产品的制造数量很庞大,各工作地点课堂教学安排教学过程主要教学内容及步骤经常重复地完成某一工序,并有严格的节奏性装配组织形式有固定式和移动式2.1.4 装配工艺规程1.规定所有的零件和部件的装配顺序。