工艺确认和工艺验证的区别
确认与验证的区别

新版GMP条款:第一百四十九条应当根据验证的结果确认工艺规程和操作规程。
问题:该条款是否混淆了确认和验证的定义?新版中的确认和验证定义是否科学?讨论:1、根据新版术语释义,确认证明厂房、设施、设备能正确运行并可达到预期结果的一系列活动。
验证是证明任何操作规程(或方法)、生产工艺或系统能够达到预期结果的一系列活动。
所以该条款将两者混为一谈,增加了大家对条款的误解。
正解是根据验证的结果确定是否批准工艺规程和操作规程。
验证只是证明工艺规程和操作规程的可靠性和重现性,而不是确认工艺参数。
2、条款对两者的定义欠妥,只是规定了对象的不同,而对其目的却表述的一模一样,都是证明达到预期结果。
两者的区别恰恰就在目的上。
确认是已经有了明确的要求或者标准,确认结果是证明对象与设计要求或标准的符合性验证是已经有了明确的目的(确保产品质量),验证结果是证明对象(过程)的可靠性和重现性看了GMP的讨论,常常谈到"验证",其实是确认(validation)的内容,觉得应该纠正过来:一不同的定义ISO9000-2000 3.8.5 验证verification通过提供客观证据对规定要求已得满足的认定注1:”已验证”一词用于表示相应的状态.注2:认定可包括下述活动,如:--变换方法进行计算;--将新设计规范与已证实的类似设计规范进行比较;--进行试验和演示;--文件发布前的评审.ISO9000-2000 3.8.6 确认validation通过提供客观证据对特定的预期用途或应用要求已得到满足的认定. 注1:”已确认”表示相应的状态.注2:确认所使用的条件可以是实际的或是模拟的.用这不同的定义来解释以下几个实例:洁净厂房的洁净度是否达到十万级,是需要验证的,可以用测试的方法来验证.但洁净度十万级的环境是否能满足生产的需要,是要通过对生产过程进行确认的.厂房熏蒸是个过程,应该用多少时间,用多少剂量可以达到预期目的,对这过程需要确认,而每次的熏蒸应该验证是否是用了这些时间和剂量.产品设计后,各技术指标是否达到(标准的)要求,要进行设计验证,一般用检测的方法,如心电监护仪的”频率响应”,超声诊断仪的”分辨率”,输液器的”连接牢固度”等等.但”频率响应”能否满足临床监护的需要/”分辨率”能否满足临床诊断的需要”连接牢固度”能否满足临床使用的需要是需要通过设计的确认来证实,二长期混淆的原因这二个定义显然是有区别的,在我们医药行业内,引入国外的GMP管理经验,但在翻译时,并没有仔细推敲,所以把validation 翻译成了”验证”,包括许多资料也是这样翻译的,如Validation of Aseptic Pharmaceutical Processes 翻译为”无菌制药工艺的验证”([美]弗里德里克.卡利登编上海医药行业协会译).这样长期以来对这二个不同的定义混淆在一起,在执行GMP中也有模糊的理解.ISO9000对这二个概念进行了不同的定义,所以GB/T19000很准确地翻译成我们现在所用的验证和确认,包括YY/T0287 所用到的这二个定义.如”设计的验证”和”设计的确认”,如”当生产和服务提供过程的输出不能有后续的监视和测量加以验证时,组织应对任何这样的过程实施确认”,都区别了这二个概念.三/在概念混淆下的现状由于概念的混淆不清,目前有些应该确认的过程用验证所替代了,如果这样,质量保证的水平大为降低.,案例:制水(工艺用水)是个过程,这过程的结果是水达到预期的要求(如纯水/注射用水),是否能够达到要求,可以用检测的方法来验证,但生产中用检测的方法是不可能的,如某个技术要求的检测(试验)需要较长的周期(无菌检测需要14天),所以这样的制水过程是个特殊的过程,需要对这过程进行确认,这确认应该通过客观证据证明这个制水过程能够在相当长的时间持续地制备出符合要求的水,这确认过程包括了设备的安装验证(IQ)/制水系统的运行验证(OQ)和制水结果的性能验证(PQ)[Qualification直译是”资格”,这里译为验证更准确],其中的”PQ”是可以用检验的方法来验证的.这样经过确认,这系统运行的结果认为是能够满足要求的不需要再经过检验而投入生产.但目前很多的企业,把这过程用验证来来取代了确认,往往只检验了某次制水过程的结果.这保证水平有局限.这样的案例很多,如无菌医疗器械包装的确认等等.另外一个说法,就是确认一个设备或者系统,(Qualification),验证一个工艺(validation)。
2-王彦忠-工艺验证和持续工艺确认

非关键工艺步骤: 如果当某个工艺阶段的任何工艺参数在操作过程中 超出规定的范围时,不会对所有的关键产品质量标准 产生潜在或实际的影响,该工艺阶段就被定义为非关 键的。在工艺性能确认时不是必须对非关键工艺阶段 进行监控。 关键但可控的工艺步骤: 如果当某个工艺阶段可以通过质量系统来控制和管 理,该工艺阶段就可以定义为关键但可控的。例如: 原辅料的化验、确认及物料平衡。在工艺性能确认时 不是必须对关键但可控的工艺阶段进行监控。
工艺验证包括产品及工艺生命周期中发生的一系 列行动,该指南将工艺验证分成了三个阶段: 第一阶段—工艺设计 第二阶段– 工艺验证/确认
第三阶段—持续的工艺验证
第一阶段—工艺设计
The commercial manufacturing process is defined during this stage based on knowledge gained through development and scale-up
定义:回顾性验证系指以历史数据的统计分析为基础 的旨在证实生产工艺条件适用性的验证。
适用条件(WHO): WHO不鼓励企业进行回顾性验证并且回顾性验证不 适用于无菌产品。 适用条件(新版GMP和欧盟GMP): 如生产工艺没有发生因原料、设备、系统、设施或生 产工艺改变而对质量有影响的重大变更时,可例外进 行回顾性验证。
在该阶段,主要目的在于基于开发和放大试验获 得知识来确定商业化生产的工艺。 Process design may be generally described as “process understanding” and “pre-qualification”. 通常称工艺设计为“理解工艺”和“预确认”。
第三阶段—持续的工艺验证
设计评审、验证、确认的区别(史上最全)

序号 项目
设计评审
设计验证
设计确认
3
时机
在本阶段结束转入下一阶ห้องสมุดไป่ตู้ 前,特别是在设计定型前
在设计形成输出时,包括阶段性设计输出
验证之后,在产品样件制造出来以后,向顾 客交付前进行(针对最终结果)
4
目的
评价设计结果满足要求的能 力,纠正设计缺陷和不足
评定设计输出是否满足输入要求,包括工艺条 件、设计参数、生产能力、检验能力
评定是否满足使用要求或预期用途要求
5
方法
设计组长召集各相关人员开评 审会议
采用计算、比较(将新设计与类似的经验证的 设计比较)试验或者演示,文档发布前评审
营销试用、临床评价或性能评价或模拟试验
各相关人员代表,其中与评审 1 参与者 对象接受者的职能代表一定要 本行当专业相关人员(PE/ME)
参加
本行当专业相关人员及其他相关人员 (PE/ME/QE/采购、计划、生产、销售、仓 储物流),必须有顾客或者顾客代表参加
9
联系 计评审和验证试验结合同时进行; 4)确认活动是验证活动的一种,或者说确认活动是一种特殊的验证; 5)评审不要求
客观证据,验证和确认要求客观证据
2
责任 设计部门
设计部门
生产部门
6
对象
设计文件、资料、样品、试验 报告
设计输出文件、图纸、规格、作业标准、设备 要求、样本等
通常是向顾客提供的产品或样品
7
性质 证明+认可
证明(正确地设计了产品)
认可(设计了正确的产品)
8
结果 评审/验证/确认结果及任何必要措施的记录应予保持
1)对关键的设计验证和设计确认的方案、结果需要加以评审; 2)设计确认前必须先通过设计验证; 3)有时,可以把设
药厂确认与验证工作流程

药厂确认与验证工作流程为了确保生产的药品符合相关监管部门的法规要求,药厂需要建立一套完善的确认与验证工作流程。
这一工作流程需要涵盖从原材料的采购到最终药品的生产和发货的全过程。
下面将介绍一份关于药厂确认与验证工作流程的范例,以便药厂生产管理人员参考。
一、原材料采购确认与验证1. 采购商确认要求:药厂应当确定采购原材料的性质、品质和规格,并编制详细的采购要求文件。
2. 供应商评估:药厂应当对潜在供应商进行评估,评估内容包括但不限于供应商的资质、生产能力和质量管理体系。
3. 试样检验:药厂应当要求供应商提供原材料的试样进行检验,以确认原材料的符合要求。
4. 验收记录:药厂应当建立原材料的验收记录,包括原材料名称、规格、数量、供应商信息等内容。
二、生产工艺确认与验证1. 工艺流程确认:药厂应当编制完整的生产工艺流程图,并进行内部确认。
2. 设备验证:药厂应当对生产所使用的设备进行验证,以保证设备符合生产要求。
3. 工艺验证:药厂应当进行生产工艺的验证,确保生产出的药品符合质量要求。
4. 记录保留:药厂应当保留工艺验证的相关记录,包括验证方案、验证结果等。
三、质量控制确认与验证1. 质量控制点确认:药厂应当确定药品生产中的关键质量控制点,并建立控制措施。
2. 质量监测验证:药厂应当对生产过程中的关键环节进行质量监测验证,以确保药品的质量稳定。
3. 不合格品处理:药厂应当对不合格品进行处理,并建立相应的记录和报告。
四、产品发货确认与验证1. 产品检验:药厂应当对生产出的产品进行检验,确保产品符合标准要求。
2. 发货记录:药厂应当建立产品发货记录,包括产品名称、批号、数量、发货日期等信息。
3. 质量跟踪:药厂应当建立产品的质量跟踪系统,对产品进行追踪和监控。
以上范例是关于药厂确认与验证工作流程的一个简要总结,具体的工作流程需要根据药厂的具体情况进行细化和规范。
希望这份范例可以对药厂生产管理人员在建立确认与验证工作流程时有所帮助。
工艺与工艺验证-

u第二十一条 采用新的生产处方或生产工艺进行首次工艺 验证应当涵盖该产品的所有规格。企业可根据风险评估的 结果采用简略的方式进行后续的工艺验证,如选取有代表 性的产品规格或包装规格、最差工艺条件进行验证,或适 当减少验证批次。
工艺与工艺验证
《确认与验证》(第六章 工艺验证 第一节 一般要求)
第二十三条 工艺验证前至少应当完成以下工作: (一)厂房、设施、设备经过确认并符合要求,分析方法经 过验证或确认。 (二)常生产操作人员应当参与工艺验证批次生产,并经过 适当的培训。 (三)用于工艺验证批次生产的关键物料应当由批准的供应 商提供,否则需评估可能存在的风险。
工艺与工艺验证
• 第二十条 企业应当有书面文件确定产品的 关键质量属性、关键工艺参数、常规生产 和工艺控制中的关键工艺参数范围,并根 据对产品和工艺知识的理解进行更新。
工艺与工艺验证
第二十五条 工艺验证方案应当至少包括以下内容: (一) 工艺的简短描述(包括批量等); (二) 关键质量属性的概述及可接受限度; (三) 关键工艺参数的概述及其范围; (四) 应当进行验证的其他质量属性和工艺参数的概述; (五) 所要使用的主要的设备、设施清单以及它们的校准状态; (六) 成品放行的质量标准; (七) 相应的检验方法清单; (八) 中间控制参数及其范围; (九) 拟进行的额外试验,以及测试项目的可接受标准,和已验证的用于测 试的分析方法; (十) 取样方法及计划; (十一)记录和评估结果的方法(包括偏差处理); (十二)职能部门和职责; (十三)建议的时间进度表。
工艺与工艺验证
性能确认 第十七条 安装和运行确认完成并符合要求后,方可进行性 能确认。在某些情况下,性能确认可与运行确认或工艺验 证结合进行。 第十八条 应当根据已有的生产工艺、设施和设备的相关知 识制定性能确认方案,使用生产物料、适当的替代品或者 模拟产品来进行试验/测试;应当评估测试过程中所需的取 样频率。
生产工艺验证及持续性工艺确认管理规定2019.3.14
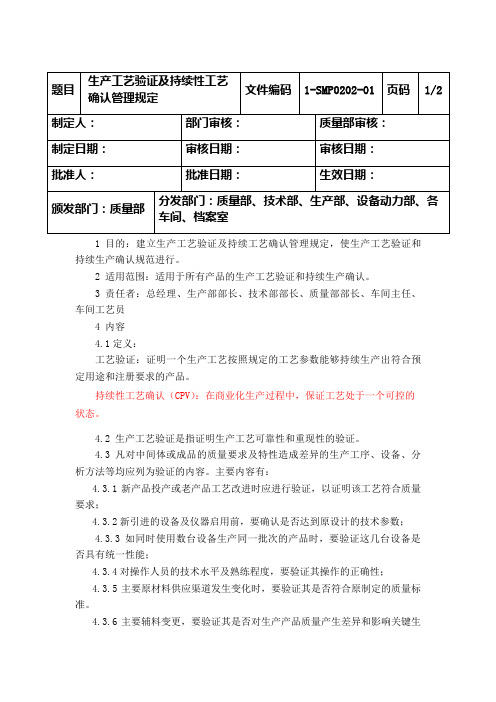
1 目的:建立生产工艺验证及持续工艺确认管理规定,使生产工艺验证和持续生产确认规范进行。
2 适用范围:适用于所有产品的生产工艺验证和持续生产确认。
3 责任者:总经理、生产部部长、技术部部长、质量部部长、车间主任、车间工艺员4 内容4.1定义:工艺验证:证明一个生产工艺按照规定的工艺参数能够持续生产出符合预定用途和注册要求的产品。
持续性工艺确认(CPV):在商业化生产过程中,保证工艺处于一个可控的状态。
4.2 生产工艺验证是指证明生产工艺可靠性和重现性的验证。
4.3凡对中间体或成品的质量要求及特性造成差异的生产工序、设备、分析方法等均应列为验证的内容。
主要内容有:4.3.1新产品投产或老产品工艺改进时应进行验证,以证明该工艺符合质量要求;4.3.2新引进的设备及仪器启用前,要确认是否达到原设计的技术参数;4.3.3如同时使用数台设备生产同一批次的产品时,要验证这几台设备是否具有统一性能;4.3.4对操作人员的技术水平及熟练程度,要验证其操作的正确性;4.3.5主要原材料供应渠道发生变化时,要验证其是否符合原制定的质量标准。
4.3.6主要辅料变更,要验证其是否对生产产品质量产生差异和影响关键生产工艺等。
4.4 生产工艺验证程序4.4.1由生产部提出验证项目申请,经验证委员会主任批准后立项。
4.4.2生产验证组组长组织小组人员,制定生产工艺验证方案,方案内容主要包括:1、验证目的;2、职责;3、概述及其相关生产工艺、质量的文件;4、风险分析;5、验证时间安排;6、生产系统要素的评价;7、生产工艺验证;8、产品成品检验及报告;9、偏差处理;10、再验证;11、验证结果评定与结论;12、验证结果的批准;13、验证证书。
4.4.3验证方案批准后,由验证小组成员对相关人员进行培训,组织力量实施,生产部收集、整理验证的记录与数据,依据生产工艺验证方案,制定并写出正式生产工艺验证报告,报验证小组。
4.4.4 验证小组负责对验证结果进行综合评审,评审内容有:4.4.4.1验证试验是否有遗漏?验证记录是否完整?4.4.4.2验证过程中验证方案有无修改?修改原因、依据以及是否经过批准?4.4.4.3验证试验是否符合标准要求?偏差及对偏差的说明是否合理?是否需要进一步补充试验?4.4.4.4生产工艺是否稳定,按此工艺生产能否得到质量均一、稳定的产品?4.4.4.5有无需要改进的设备、生产条件、操作步骤?4.4.4.6生产过程中有无需要增加的检测、控制项目?4.4.5经过评审,做出审核结论,确认再验证周期,上报验证验证委员会主任批准。
医疗器械验证及确认
3)对所验证的产品或工艺已有相当的经验。
应当注意这种验证方式,可能会带来产品质量方面的风险,须谨慎使用。
术语及验证方式的分类
3、回顾性验证 当有充分的积累数据可供使用时,可以采用回顾性验证,开展回顾性验证应 具备若干必备条件,这些条件包括:
1)有足够连续批次合格数据;
2)有以数值表示的、检验结果可以进行统计分析的、检验方法经过验证的; 3)有完整的生茶批记录,记录中工艺条件记录明确,且有关于偏差的分析说 明; 4)有关生产控制过程是标准化的,并一致处于受控状态,如原材料标准、洁 净区级别、工艺参数、检测方法、微生物控制等。 回顾性验证与前验证不同,不需要特别的事先准备验证方案,但需要一个比 较完整的生产及质量监控计划,以便能够收集足够的资料和数据,对生产和质量 进行回顾性总结。 开展回顾性验证时间,企业可根据用户投诉、偏差调查、生产控制、报废报
这一方式主要用于:
1)有特殊质量要求的产品; 2)仅靠生产过程控制及成品检查不足以确保产品重现性和产品质量的生产 工艺或过程; 3)制造产品的重要工艺或过程; 4)历史资料不足,难以进行回顾性验证的工艺或过程。 2、同步验证 同步验证是工艺运行同时进行的验证。采用这种验证方法的先决条件是: 1)有完善的取样规定,即生产机工艺条件的监控比较好; 2)有经过验证的检验方法;
械等专业知识;熟悉产品、熟悉工艺。此外负责工艺验证的管理人员还应具有微
生物及数据统计方面知识,以适应工艺验证工作的特殊要求。
当企业生产和服务提供过程通过监视或测量达到符合规定要求时,应对任何这样
一个过程实施验证。 三、验证的分类及作用 按照产品和工艺要求以及设施、设备变更,工艺制定、修订等均须通过验证 的要求,可以把验证分为四种:前验证、同步验证、回顾性验证、再验证。
确认与验证(2010版gmp培训)
证明任何操作规程(或方法)、生产工艺或系统能 够达到预期结果的一系列活动。
-SFDA 2010第十四章 附 则
(一)设计确认应当证明厂房、设施、设备的设计符合 预定用途和本规范要求; (二)安装确认应当证明厂房、设施、设备的建造 和安装符合设计标准; (三)运行确认应当证明厂房、设施、设备的运行 符合设计标准; (四)性能确认应当证明厂房、设施、设备在正常 操作方法和工艺条件下能够持续符合标准; (五)工艺验证应当证明一个生产工艺按照规定的 工艺参数能够持续生产出符合预定用途和注册要求的产 品。 -SFDA cGMP(2010 第一百四十条)
◦ 蠕动泵的喷液速度
运行测试方案应该: 介绍验证目的、项目背景、设备/系统的综述及关键功能/装置。 确认每个项目与系统的标准操作规程与维护程序以确保在规定的条件下 持续运行 设计测试包括测试方法、依据与接受标准,以确认关键功能符合用户需 求。这些测试应包括,但不局限于
◦ ◦ ◦ ◦ ◦ ◦ ◦ ◦
间接影响
◦ 该类系统是指对于产品质量没有直接影响的系统但是通常 将支持直接影响的系统,例如,冷却水。这些系统应进行 优良工程规范确认即可,然而当其可能对直接影响系统的 操作造成影响时,必须评估以决定是否附加相关的验证需 求。
-Volume 5 commissioning and qualification ISPE
◦ ◦ ◦ ◦ ◦ ◦ 定义重要级别(强制的或期望的) 对系统设计应可提供充分的基础信息 便于追溯的唯一编号 完整:已含所有有助于系统设计的必要的信息 一致:其中的任何需求应无冲突矛盾。 明确:需求应尽可能只用一种方式解释,其应是定量的,如“ 快速换线”应描述为例如“在25分钟内完成换线”。 ◦ 可理解:所有的用户与供应商应能理解需求。 ◦ 可测量:对于任何需求应可进行测试/验证。
品检中的工艺方案验证与确认方法
品检中的工艺方案验证与确认方法对于品检中的工艺方案验证与确认方法,可以通过以下几个步骤来实现:流程审核、样品制作、实验测试和数据分析。
这些步骤有助于验证和确认工艺方案的可行性和稳定性,确保产品质量满足要求。
进行流程审核。
在开始验证工艺方案之前,需要进行详尽的流程审核。
这包括审查工艺方案的流程步骤、各个环节的设置参数以及相关的标准和规范。
流程审核的目的是确保工艺方案符合质量管理体系的要求,以及能够满足产品的特定需求。
在审核过程中,应该与相关部门和工艺专家进行充分的沟通,以便识别和纠正潜在的问题。
进行样品制作。
在验证工艺方案之前,需要制作用于实验测试的样品。
样品应该按照工艺方案的要求和标准进行制作,以确保测试结果的准确性和可靠性。
样品的制作应当严格按照工艺流程进行,包括原材料的选择、配比比例、加工步骤等。
同时,应该制作足够数量的样品,以便进行多次实验测试,并获取可靠的数据。
接下来,进行实验测试。
实验测试是验证工艺方案的关键一步。
通过实验测试,可以评估工艺方案的可行性和稳定性,并确定其是否能够满足产品质量的要求。
在实验测试中,应该严格按照工艺方案进行操作,并记录实验过程中的各项参数和观测数据。
测试结果应该与预期的产品要求进行比较,并评估是否需要进一步改进或调整工艺方案。
进行数据分析。
在实验测试结束后,需要对获取的数据进行详细的分析和评估。
数据分析的目的是识别工艺方案的优点和不足之处,并提供改进的建议。
可以使用统计方法来分析数据,例如均值、方差、相关性等指标。
通过数据分析,可以得出对工艺方案的验证和确认结论,确定是否需要进一步优化或调整。
除了以上的步骤,还需要注意以下几个方面。
要确保验证和确认过程的透明度和可追溯性,以便在需要时进行审查和验证。
要充分利用现代化的检测仪器和设备,以提高测试结果的准确性和可靠性。
同时,在验证和确认过程中,要注重团队合作和跨部门协作,以确保信息的交流和共享,并做出统一的决策。
验证与确认的区别
验证(Verification)与确认(Validation)的区别验证:我们正确地构造了产品吗?(注重过程-由QA负责)确认:我们构造了正确的产品吗?(注重结果-由QC负责)说法一:(2)“验证(Verification)”的涵义通过提供客观证据对规定要求已得到满足的认定。
(2)“确认(Validation)”的涵义通过提供客观证据对特定的预期用途或应用要求已得到满足的认定。
(3)“验证”和“确认”之区别“验证”和“确认”都是认定。
但是,“验证”表明的是满足规定要求,而“确认”表明的是满足预期用途或应用要求,说简单点,“确认”就是检查最终产品是否达到顾客使用要求。
(4)“设计和开发”中“设计验证”和“设计确认”之区别在于:设计验证的目的是检查设计输出是否满足设计输入的规定要求。
设计确认的目的是检查设计形成的最终产品是否达到顾客的使用要求。
说法二:1.“确认”是要证明所提供的(或将要提供的)产品适合其预计的用途,而“验证”则是要查明工作产品是否恰当地反映了规定的要求。
换句话说,验证要保证“做得正确”,而确认则要保证“做的东西正确”。
2.验证注重“过程”,确认注重“结果”3.(Verification) ---Are we producing the product right?(Validation) ---Are we producing the right product?说法三:1.什么是验证?验证就是要用数据证明我们是不是在正确的制造产品。
注意这里强调的是过程的正确性2.什么是确认?确认就是要用数据证明我们是不是制造了正确的产品。
注意这里强调的是结果的正确性。
3.验证和确认是一个广泛的概念,感兴趣的读者可以参考IEEE Std 1012-1998 。
验证:验证检查某样东西是否符合之前已定好的标准,如:文档评审,要检查的东西是文档,检查标准就是文档的评审标准,又如:测试软件,要检查的东西就是软件,检查的标准就是软件的规格说明,包括功能说明,性能要求等。
- 1、下载文档前请自行甄别文档内容的完整性,平台不提供额外的编辑、内容补充、找答案等附加服务。
- 2、"仅部分预览"的文档,不可在线预览部分如存在完整性等问题,可反馈申请退款(可完整预览的文档不适用该条件!)。
- 3、如文档侵犯您的权益,请联系客服反馈,我们会尽快为您处理(人工客服工作时间:9:00-18:30)。
工艺确认和工艺验证的区别
工艺确认(Process Qualification)和工艺验证(Process Validation)都是在产品生产过程中进行的重要环节,旨在确保产品的制造过程能够稳定且符合设计要求。
虽然两者都是验证工艺的有效性,但它们在目标、内容、侧重点和方法上存在一些区别。
首先,工艺确认主要是为了验证工艺过程的稳定性和可行性,确保在现有设计和规范的前提下,能够稳定地生产出合格的产品。
在产品投产前或投入大规模生产之前进行,其侧重点在于验证工艺过程在实际生产中的可行性和稳定性,评估制程参数的范围,确定合理的生产工艺和设备,并进行一系列的评估、检验和测试。
工艺确认一般采用样本生产的方式,通过抽样、测试和分析等手段来确认工艺过程是否稳定和符合设计要求。
此外,工艺确认还涉及到生产工艺的标准化、工艺控制计划的制定、生产设备和工艺参数的确认等,旨在确保工艺过程的一致性和稳定性。
而工艺验证则是工艺过程的最终验证,在生产过程稳定的前提下,通过对实际生产数据的统计分析,以及对产品性能和质量的评估来验证工艺过程的有效性和符合性。
工艺验证通常发生在产品投入市场之前,通过收集大量的生产数据来验证和证明工艺过程的合理性、稳定性和可靠性,以及产品的性能和质量是否符合设计要求。
工艺验证主要包括确定合理的采样计划,制定验证规范和标准,进行数据分析和统计处理,以及对产品的功能、可靠性、耐久性、质量一致性和稳定性等进行综合评估。
在方法上,工艺确认和工艺验证主要采用的方法和手段也不完全相同。
工艺确认一般采用加速测试、缩减实验、仿真模拟等方法来验证工艺过程的可行性和稳定性;而工艺验证则主要采用实际生产过程中的数据来进行统计分析和评估。
此外,工艺验证通常需要进行多批次生产及持续的生产运行,以获取足够的数据和样本,验证和论证工艺过程的稳定性和一致性。
需要注意的是,工艺确认和工艺验证并不是一次性的工作,而是一个持续不断的过程。
在产品生命周期中,随着市场和技术的变化,工艺确认和工艺验证应该得到更新和再评估,以确保工艺过程的持续有效性和符合性。
综上所述,工艺确认和工艺验证在目标、内容、侧重点和方法等方面存在一些区别。
工艺确认主要用于验证工艺过程的可行性和稳定性,确保生产出合格的产品;工艺验证则是对工艺过程最终的验证,通过实际生产数据进行统计分析和评估,确保工艺过程的有效性和符合性。
两者都是产品生产过程中非常关键的环节,能够确保产品的质量和性能符合设计要求,提高产品的可靠性和一致性。