开料作业指导书
开料作业指导书

开料作业指导书一、任务背景开料作业是创造业中常见的一项工序,用于将原材料按照设计要求进行切割和加工,以制作成所需的零部件或者成品。
本指导书旨在提供详细的开料作业流程和操作要点,以确保开料作业的准确性和高效性。
二、作业准备1. 确定开料材料:根据设计要求和产品规格,选择合适的原材料进行开料作业。
2. 准备开料设备:确保开料设备的正常运行,包括切割机、钻孔机、冲压机等。
3. 检查刀具和刀片:确保刀具和刀片的完好无损,及时更换磨损的刀具。
4. 确定开料方案:根据产品图纸和工艺要求,确定开料方案,包括切割尺寸、切割顺序等。
三、开料作业流程1. 根据产品图纸,将原材料放置在开料设备上,并进行固定。
2. 根据开料方案,设置开料设备的切割参数,包括切割速度、切割深度等。
3. 启动开料设备,进行切割作业。
根据产品要求,可以使用不同的切割方式,如平面切割、曲面切割等。
4. 在切割过程中,及时清理切割产生的废料和碎屑,确保切割质量和设备的正常运行。
5. 完成切割后,进行质量检查。
检查切割尺寸是否符合要求,检查切割表面是否平整光滑。
6. 对于不合格的切割件,进行修整或者重新开料,直至符合要求为止。
7. 将合格的切割件进行分类、标记和包装,以便后续工序使用或者出库。
四、操作要点1. 安全第一:在进行开料作业前,必须佩戴好个人防护装备,如安全帽、防护眼镜、耳塞等。
严禁操作人员穿着松散的衣物或者长发。
2. 设备操作:操作人员必须熟悉开料设备的操作方法和安全规程,严禁未经培训的人员操作设备。
3. 刀具更换:及时更换磨损的刀具和刀片,避免因刀具磨损导致的切割质量下降或者设备故障。
4. 废料处理:及时清理切割产生的废料和碎屑,确保工作环境整洁,避免废料对设备和操作人员的影响。
5. 质量检查:在切割作业完成后,必须进行质量检查,确保切割尺寸和表面质量符合要求。
6. 作业记录:对每次开料作业进行记录,包括开料时间、开料材料、切割参数等,以便追溯和分析。
开料作业指导书

开料作业指导书一、任务背景开料作业是制造业中的重要环节之一,它涉及到材料的切割、裁剪和加工等工序。
正确的开料作业可以提高生产效率,减少材料浪费,保证产品质量。
为了确保开料作业的顺利进行,特编写本指导书,详细介绍了开料作业的流程和要求。
二、开料作业流程1. 准备工作a. 确定开料材料的种类和规格。
b. 准备好所需的开料工具和设备,如切割机、裁剪机等。
c. 检查开料工具和设备的状态,确保其正常工作。
d. 准备好开料作业所需的安全防护用具,如手套、护目镜等。
2. 测量和标记a. 使用测量工具(如尺子、卷尺等)对开料材料进行准确测量。
b. 根据产品的要求,在开料材料上进行标记,标明切割线、裁剪线等。
3. 切割和裁剪a. 根据标记线,使用切割工具将材料切割成所需尺寸和形状。
b. 使用裁剪工具对材料进行裁剪,确保边缘平整、无毛刺。
4. 检查和修整a. 对切割和裁剪后的材料进行检查,确保尺寸和形状符合要求。
b. 如有需要,使用修整工具对材料进行修整,使其达到更高的精度和质量要求。
5. 清理和整理a. 清理工作区域,清除切割和裁剪过程中产生的废料和碎屑。
b. 整理好开料材料,分类存放,方便后续工序的进行。
三、开料作业要求1. 安全操作a. 在进行开料作业前,必须佩戴好安全防护用具,如手套、护目镜等。
b. 使用切割和裁剪工具时,要注意操作规范,避免发生意外伤害。
2. 准确测量a. 使用准确的测量工具进行测量,确保开料材料的尺寸和形状准确无误。
b. 在标记线上进行切割和裁剪,确保开料的精度和一致性。
3. 优化利用a. 在进行开料作业时,要合理安排材料的摆放和切割方式,尽量减少材料的浪费。
b. 对于剩余材料,可以进行合理的规划和利用,减少资源的浪费。
4. 质量控制a. 在开料作业过程中,要对切割和裁剪后的材料进行严格的检查,确保质量符合要求。
b. 如发现质量问题,及时进行修整或更换材料,确保产品的质量和可靠性。
四、开料作业注意事项1. 在进行开料作业前,要对开料工具和设备进行检查,确保其正常工作。
开料作业指导书

开料作业指导书一、任务背景开料作业是制造业中的重要环节,它涉及到原材料的加工和成品的制作。
为了确保开料作业的顺利进行,提高生产效率和产品质量,制定一份详细的开料作业指导书是必要的。
二、任务目的本指导书的目的是指导工人进行开料作业,确保每一道工序的准确性和一致性,以提高产品的质量和生产效率。
三、任务内容1. 开料作业流程a. 准备工作:检查原材料的质量和数量,准备所需的工具和设备。
b. 制定开料计划:根据产品的要求和规格,制定开料计划,确定每个原材料的尺寸和数量。
c. 进行开料作业:根据开料计划,使用适当的工具和设备进行开料作业,确保每个原材料的尺寸和形状符合要求。
d. 检验开料结果:对每个开料完成的原材料进行检验,确保其尺寸和形状符合要求。
e. 记录和报告:记录每个原材料的开料结果,并及时向相关部门报告。
2. 开料作业要求a. 安全要求:在进行开料作业时,必须佩戴适当的个人防护装备,如安全眼镜、手套等。
操作过程中要注意安全,避免发生意外事故。
b. 精确度要求:开料作业要求精确度高,尺寸和形状必须与产品要求一致。
使用合适的测量工具进行测量,确保开料结果的准确性。
c. 效率要求:开料作业要求高效率,尽量减少浪费和损耗。
合理安排开料计划,合理利用原材料,提高生产效率。
d. 质量要求:开料作业的质量直接影响到产品的质量。
每个开料完成的原材料都必须经过严格的检验,确保其质量符合要求。
3. 开料作业指导a. 准备工作:i. 检查原材料的质量和数量,确保其符合要求。
ii. 准备所需的工具和设备,确保其完好无损。
b. 制定开料计划:i. 根据产品的要求和规格,制定开料计划,确定每个原材料的尺寸和数量。
ii. 考虑原材料的特性和加工工艺,合理安排开料顺序。
c. 进行开料作业:i. 使用适当的工具和设备进行开料作业,确保操作正确、安全。
ii. 根据开料计划,按照要求进行开料,确保每个原材料的尺寸和形状符合要求。
d. 检验开料结果:i. 对每个开料完成的原材料进行检验,使用测量工具进行尺寸和形状的检测。
开料作业指导书

开料作业指导书一、任务背景为了提高生产效率和产品质量,确保开料作业的准确性和一致性,制定本作业指导书,以便操作人员按照标准程序进行开料作业。
二、任务目的1. 确保开料作业的准确性和一致性;2. 提高生产效率和产品质量;3. 降低人为因素引起的错误和损失。
三、任务内容1. 开料前准备a. 确认所需开料材料和数量;b. 检查开料设备和工具的完好性;c. 准备所需的安全防护装备。
2. 开料操作步骤a. 将所需材料放置在开料设备上,并固定好;b. 根据产品要求,调整开料设备的参数,包括切割速度、切割深度等;c. 启动开料设备,确保设备运行正常;d. 按照产品图纸或者规格要求,进行开料操作;e. 定期检查开料设备的运行状态,确保设备正常运转;f. 完成开料后,及时清理工作区域,确保安全和整洁。
3. 安全注意事项a. 佩戴好安全防护装备,包括手套、护目镜等;b. 注意开料设备的运行状态,发现异常及时停机检修;c. 确保开料区域的通风良好,避免有害气体积聚;d. 禁止未经培训的人员操作开料设备;e. 禁止随意更改开料设备的参数;f. 禁止在开料过程中随意触摸切割工具。
四、数据要求1. 开料材料的规格和数量;2. 开料设备的参数设置;3. 开料设备的运行状态;4. 开料操作的时间和效率。
五、任务评估1. 根据开料作业的准确性和一致性进行评估;2. 根据生产效率和产品质量进行评估;3. 根据错误和损失的减少程度进行评估。
六、任务总结通过制定开料作业指导书,操作人员可以按照标准程序进行开料作业,提高生产效率和产品质量,降低人为因素引起的错误和损失。
同时,严格遵守安全注意事项,确保操作人员的安全和工作环境的整洁。
通过对数据的采集和评估,不断改进开料作业流程,进一步提高生产效率和产品质量。
开料作业指导书

开料作业指导书引言概述:开料作业是在制造业中常见的一项工艺,它是将原材料按照设计要求进行切割、刻划等操作,以得到所需的零部件或产品。
本指导书旨在提供开料作业的详细步骤和注意事项,帮助操作人员正确进行开料作业,确保产品质量和生产效率。
一、准备工作1.1 确定开料材料和数量在进行开料作业前,首先需要明确所需开料的材料和数量。
根据产品设计要求和生产计划,确定所需的材料种类、规格和数量,以便提前准备好。
1.2 检查设备和工具在开料作业前,需要检查开料设备和工具的工作状态,确保其正常运行和安全可靠。
检查切割机、刀具、刻划工具等设备,确保其刀片锋利、刀具固定牢固,并检查防护装置是否完好。
1.3 制定开料计划根据产品设计要求和生产计划,制定开料计划。
确定每个材料的开料尺寸、形状和数量,并合理安排开料顺序,以提高生产效率和节约材料。
二、开料操作2.1 材料测量和标记根据开料计划,使用测量工具(如卷尺、角尺等)对材料进行准确测量,并在材料上进行标记。
标记应清晰可见,包括开料尺寸、形状、数量等信息,以便后续操作。
2.2 切割操作根据开料计划和标记,使用合适的切割工具(如切割机、锯等)进行切割操作。
在切割前,要确保切割工具刀片锋利,并调整切割参数(如切割速度、切割深度等)以适应材料的不同特性。
2.3 刻划和打孔根据产品设计要求,在开料过程中可能需要进行刻划和打孔操作。
使用合适的刻划工具和打孔设备,按照标记和设计要求进行操作。
刻划应准确清晰,打孔应位置准确、孔径一致。
三、质量控制3.1 检查开料尺寸和形状在开料作业完成后,要对开料零部件进行尺寸和形状的检查。
使用测量工具对开料尺寸进行测量,并与设计要求进行对比。
同时,检查开料零部件的形状是否符合要求,如直线度、平直度等。
3.2 检查切割边缘质量切割边缘的质量直接影响产品的装配和使用。
对开料零部件的切割边缘进行检查,确保边缘平整、光滑,并无明显毛刺、裂纹等缺陷。
3.3 检查刻划和打孔质量如果开料零部件需要刻划和打孔,要对刻划线条的清晰度和打孔孔径进行检查。
开料作业指导书

开料作业指导书引言:开料作业是指在创造业中,将原材料按照设计要求进行切割、成型等加工工艺的过程。
开料作业的质量直接影响到最终产品的质量和成本。
本文将从材料准备、切割工艺、加工设备和安全注意事项四个方面,详细介绍开料作业的指导方法和注意事项。
一、材料准备1.1 材料选择:在进行开料作业前,首先要选择合适的材料。
根据产品的要求和使用环境,选择材料的种类和规格。
考虑到材料的强度、耐磨性、耐腐蚀性等特性,确保产品能够满足设计要求。
1.2 材料检查:在进行开料作业前,对材料进行子细检查。
检查材料的表面是否有明显的损伤、裂纹或者变形,以及是否符合规定的尺寸和质量要求。
如发现问题,应及时更换或者修复材料,以确保开料作业的顺利进行。
1.3 材料处理:根据不同的材料特点,进行必要的处理。
例如,对于金属材料,可以进行表面处理,如去除氧化层、涂覆保护膜等,以提高材料的耐腐蚀性和外观质量。
对于木材材料,可以进行防腐处理,以延长材料的使用寿命。
二、切割工艺2.1 切割方式:根据材料的特性和产品的要求,选择合适的切割方式。
常见的切割方式包括机械切割、激光切割、喷水切割等。
不同的切割方式有不同的优缺点,需要根据具体情况进行选择。
2.2 切割参数:在进行切割作业时,需要设置合适的切割参数。
切割参数包括切割速度、切割厚度、切割角度等。
合理的切割参数能够提高切割质量和效率,减少材料的浪费和损坏。
2.3 切割工具:选择合适的切割工具也是开料作业的关键。
根据材料的硬度和厚度,选择适当的切割刀具或者切割机械。
确保切割工具的锋利度和稳定性,以获得高质量的切割效果。
三、加工设备3.1 设备选择:根据切割工艺的要求,选择合适的加工设备。
不同的切割工艺需要不同的设备,如数控切割机、激光切割机、喷水切割机等。
选择适合的设备可以提高生产效率和产品质量。
3.2 设备调试:在使用加工设备进行开料作业前,需要进行设备的调试和检查。
确保设备的各项参数和功能正常,如切割速度、切割精度、切割深度等。
开料作业指导书

开料作业指导书一、任务描述本文档旨在为开料作业提供详细的指导和操作步骤,确保开料作业的顺利进行。
开料作业是指将原材料进行切割、加工、修整等工序,以得到符合要求的产品零部件。
二、操作流程1. 准备工作a. 确认开料所需的原材料种类、规格和数量,并进行检查。
b. 检查切割设备的工作状态,确保设备正常运行。
c. 检查安全设施,如护栏、紧急住手按钮等,确保安全操作。
2. 制定开料方案a. 根据产品设计要求和工艺要求,制定开料方案,包括切割尺寸、切割顺序等。
b. 考虑原材料的材质、硬度等特性,选择合适的切割工具和切割参数。
3. 调整切割设备a. 根据开料方案,调整切割设备的切割速度、切割深度等参数。
b. 确保切割设备的刀具锋利,切割台面平整,以确保切割质量。
4. 进行开料作业a. 将原材料放置在切割台面上,并固定好。
b. 按照开料方案,使用切割设备进行切割操作,确保切割线条准确、整齐。
c. 注意安全操作,避免手部接触切割设备。
5. 检查开料质量a. 对开料后的零部件进行检查,确保尺寸、形状等符合设计要求。
b. 检查切割表面是否平整、无毛刺等缺陷。
c. 如发现问题,及时调整切割设备或者重新进行开料作业。
6. 清理工作a. 完成开料作业后,清理切割设备和工作区域,保持整洁。
b. 对切割设备进行维护保养,如清洁切割刀具、润滑设备等。
三、注意事项1. 在进行开料作业前,必须熟悉切割设备的操作规程和安全操作要求。
2. 切割设备的刀具应定期检查和更换,确保切割质量和安全性。
3. 在进行开料作业时,应佩戴个人防护用品,如安全眼镜、手套等。
4. 如发现切割设备异常或者故障,应即将住手作业并报告相关人员进行检修。
5. 开料作业过程中,严禁随意更改开料方案,必须经过相关人员批准后方可进行调整。
6. 开料作业结束后,应及时清理切割设备和工作区域,以确保下次作业的顺利进行。
四、数据记录1. 开料作业日期:2022年1月1日2. 原材料种类:钢板3. 原材料规格:1000mm×2000mm×10mm4. 切割设备:数控切割机5. 切割工具:等离子切割刀具6. 切割速度:1000mm/min7. 切割深度:8mm8. 开料方案:按照产品设计要求,先进行长边切割,再进行短边切割。
开料作业指导书
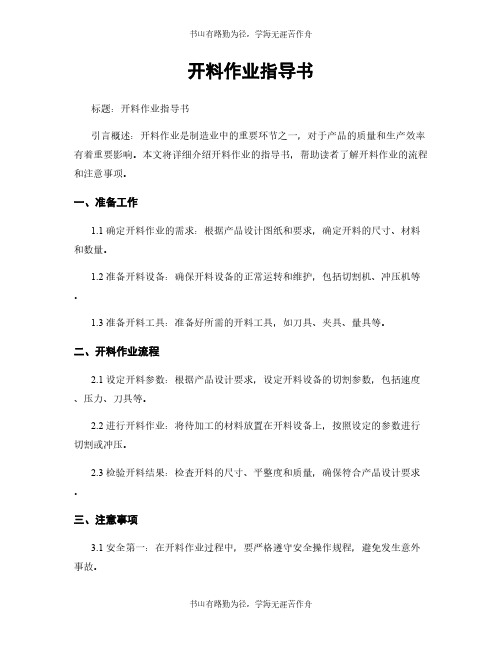
开料作业指导书标题:开料作业指导书引言概述:开料作业是制造业中的重要环节之一,对于产品的质量和生产效率有着重要影响。
本文将详细介绍开料作业的指导书,帮助读者了解开料作业的流程和注意事项。
一、准备工作1.1 确定开料作业的需求:根据产品设计图纸和要求,确定开料的尺寸、材料和数量。
1.2 准备开料设备:确保开料设备的正常运转和维护,包括切割机、冲压机等。
1.3 准备开料工具:准备好所需的开料工具,如刀具、夹具、量具等。
二、开料作业流程2.1 设定开料参数:根据产品设计要求,设定开料设备的切割参数,包括速度、压力、刀具等。
2.2 进行开料作业:将待加工的材料放置在开料设备上,按照设定的参数进行切割或冲压。
2.3 检验开料结果:检查开料的尺寸、平整度和质量,确保符合产品设计要求。
三、注意事项3.1 安全第一:在开料作业过程中,要严格遵守安全操作规程,避免发生意外事故。
3.2 材料选择:根据产品要求选择合适的材料进行开料作业,确保产品的质量和性能。
3.3 刀具维护:定期对开料刀具进行清洁和润滑,及时更换磨损严重的刀具,保持开料质量稳定。
四、质量控制4.1 抽检产品质量:对开料完成的产品进行抽检,检查尺寸、外观和质量,确保产品符合要求。
4.2 记录开料数据:记录每一次开料作业的参数和结果,建立开料作业的数据档案,便于追溯和改进。
4.3 及时处理异常:发现开料产品有质量问题时,要及时处理并找出原因,避免类似问题再次发生。
五、持续改进5.1 定期评估开料工艺:定期对开料工艺进行评估和改进,提高开料效率和质量。
5.2 培训开料操作人员:定期对开料操作人员进行培训和考核,提高其操作技能和质量意识。
5.3 借鉴他人经验:与同行业或同类产品的企业进行交流和合作,借鉴其开料经验和技术,不断提升自身的开料水平。
结语:开料作业是制造业中至关重要的一环,只有做好开料作业的每一个细节,才能确保产品质量和生产效率。
希望本文的指导书能帮助读者更好地理解开料作业的流程和注意事项,提高开料作业的质量和效率。
- 1、下载文档前请自行甄别文档内容的完整性,平台不提供额外的编辑、内容补充、找答案等附加服务。
- 2、"仅部分预览"的文档,不可在线预览部分如存在完整性等问题,可反馈申请退款(可完整预览的文档不适用该条件!)。
- 3、如文档侵犯您的权益,请联系客服反馈,我们会尽快为您处理(人工客服工作时间:9:00-18:30)。
开料作业指导书
1 目的
通过规范作业程序,使电子锯、推台锯开出的工件符合质量要求,避免因不规范操作而造成额外损失。
2 适用范围
开料作业工序
3 设备工具材料
卷尺、直角尺、中纤板、饰面板等。
4 作业准备
4.1首先根据零件生产及记录卡中规定的要求,检查应加工原材料的品种、规格、尺寸和数量。
4.2检查待加工材料翘曲度,看其表面是否有凹凸不平或划痕。
4.3用吸尘器清理工作场地,并用气管将工作台吹净,保持工作台随时清洁,不准有硬物存在,以免损伤板材表面。
4.4检查电子锯的输入系统和吸尘装置是否正常,检查推台锯的开关是否灵敏、可靠。
4.5检查锯片是否锋利,主锯和刻锯是否在一条直线上,试机约一分钟,看运行是否正常。
5 工作内容
5.1调解锯片高度。
锯片要高于待加工板厚10-15mm。
5.2向电子锯输入有关开料的具体数据,移动推台锯的靠块(条),确定加工工件的宽度。
5.3确定基准面。
确定加工工件的宽度将锯边作为准面、飞边约5—10mm。
5.4板件定位。
板件要与靠块(条)靠紧,并将卡尺卡住。
5.5电子锯的进料速度为13.5-27m/min,可加工板厚为≤100mm。
推台锯的进料速度根据板厚和硬度进行调整,加工不同厚度板材可更换不同型号的锯片。
5.6操作员在排板时应先看清图纸、木纹、板材厚度、颜色,主机手在开出第一件时要做到首检。
一米以下,正负偏差为0.5毫米;二米以上,正负偏差为1
毫米以下。
5.7加工完毕后,在“工件生产及检查记录卡”上签字,将工件摆放在指定地点,经质检确认后方可流转。
5.8作业结束时,关闭电源、气源,将工作场地和工作台清理干净。
6 技术要求
如出现划伤,磕伤,崩伤等不能修补的工件不能转入下道工序。
7 检查方法
7.1目测。
7.1.1目视开料后工件表面是否有碰伤、磕伤、砸伤和崩边等现象,工件的数量、形状是否符合图纸规定要求。
7.2 测量。
7.2.1用卷尺测量工件线形尺寸、邻边垂直度,其公差为±0.5mm。
8注意事项
8.1必须保持头脑清醒,不得酒后上岗,机电设备由专人操作。
8.2要求主机手操作,推台锯在开短小工件时要用板条向前送料,扶手开始用手去接。
8.3注意靠挡的位置,如用右靠挡开长度时,挡头不能超出主锯片的尾端,约退后1-2厘米;如用右靠挡开宽度时,挡头不得超过主锯片的1/3。
8.3.1首先检查推台锯左右靠挡是否垂直。
8.3.2电子锯首先检查气压是否正常,气压不得低于6帕斯卡,不得超出6.5帕斯卡。
8.3.3首先看清工件结构图纸,排板的过程中大小搭配,以余料最少、板材利用率最高来输入程序。
8.4开料操作过程确保“八不”:不弯曲、不斜角、不黑边、不碰坏、不爆边、不多件、不少件、不偏差。
8.5加工完毕的工件要轻摆轻放,以免散落。
8.6开钉装及异形工件时一般需比原规格开大4-5厘米。