传动轴有限元分析
基于ANSYS有限元的复合材料传动轴失效分析

基于ANSYS有限元的复合材料传动轴失效分析基于ANSYS有限元的复合材料传动轴失效分析1. 引言复合材料在传动轴应用中越来越广泛,其具有较高的强度和刚度,以及较低的密度和惯性矩。
然而,由于其复杂的结构和复杂的加载条件,传动轴在运行过程中可能会发生失效。
因此,基于有限元分析的复合材料传动轴失效分析显得尤为重要。
2. 传动轴结构和材料传动轴主要有轴状结构,通常由多个复合材料组件组成,如纤维增强聚合物复合材料(FRP)和碳纤维增强复合材料(CFRP)。
这些材料的组合可以提供较高的轴向和环向强度,从而提供更好的传递力矩和转速。
3. 复合材料传动轴的失效模式复合材料传动轴的失效模式包括弯曲破坏、蠕变破坏、疲劳破坏和环剪切破坏等。
这些失效模式通常是由不同的应力和应变引起的,并在不同的加载条件下发生。
4. 有限元模型的建立基于ANSYS有限元软件,可以建立复合材料传动轴的三维有限元模型。
模型的几何形状和材料属性可以根据实际情况进行设定。
5. 材料参数的输入复合材料的性能参数需要根据实际测试数据进行输入。
这些参数包括纤维体积分数、纤维方向的弹性模量和剪切模量,基体材料的弹性模量和剪切模量等。
这些参数的准确性对于分析结果的准确性至关重要。
6. 边界条件和加载条件的设定在进行有限元分析之前,需要确定边界条件和加载条件。
边界条件通常包括固定支撑和固定约束等,以保证模型的稳定性。
加载条件通常包括径向和环向的力矩和转速等。
7. 模型分析和结果评价通过对复合材料传动轴模型进行有限元分析,可以得到应力和应变的分布图,以及轴的变形情况。
利用这些结果可以评估轴的失效模式和强度。
8. 参数敏感性分析和优化设计在分析过程中,可以对模型的几何形状和材料参数进行敏感性分析。
通过调整这些参数,可以优化设计,提高传动轴的性能和可靠性。
9. 模型验证和实验验证为了验证有限元模型的准确性,可以进行实验验证。
将有限元分析结果与实验结果进行对比和验证,以确定模型的准确性和可靠性。
基于ANSYS的传动轴受力分析

基于ANSYS的传动轴受力分析引言:传动轴是一种将动力传输到机器的旋转轴。
在实际应用中,传动轴常常承受着很大的受力。
为了确保传动轴在运行过程中的可靠性和安全性,需要对传动轴的受力进行分析和优化。
本文将基于ANSYS软件对传动轴的受力进行分析。
一、建立传动轴的有限元模型在ANSYS中,首先需要建立传动轴的有限元模型。
有限元法是一种数值计算方法,通过将实际结构离散化为有限个单元,来近似模拟连续介质的力学行为。
建立传动轴的有限元模型有助于我们分析和优化传动轴的受力。
二、给定边界条件和加载条件在进行有限元分析前,需要给定传动轴的边界条件和加载条件。
边界条件是指模型的固定部分或约束,加载条件是指施加在传动轴上的力或力矩。
在传动轴的受力分析中,常见的加载条件有转矩加载和弯曲加载。
三、进行材料属性的定义在进行有限元分析前,需要对传动轴的材料属性进行定义。
材料属性包括弹性模量、泊松比和密度等。
这些属性可以通过实验获取,也可以通过材料手册查询获得。
四、进行有限元分析在以上准备工作完成后,可以开始进行有限元分析。
有限元分析通过对传动轴模型进行网格划分,求解传动轴在加载条件下的应力和变形情况。
在ANSYS中,可以选择合适的求解算法和网格划分方式。
通过有限元分析结果,可以直观地了解传动轴承受力的情况。
五、对结果进行评估和优化有限元分析得到的结果可以用于评估传动轴的受力情况。
通过对应力分布和变形情况的分析,可以判断传动轴是否满足强度和刚度要求。
如果不满足要求,可以进行优化设计。
例如,可以调整材料的种类和尺寸,或者增加支撑结构以提高传动轴的强度和刚度。
六、验证和验证最后,需要对有限元分析的结果进行验证和验证。
验证是指将模型的计算结果与理论计算或实验数据进行对比,验证模型的准确性和可靠性。
验证可以通过比较有限元分析结果和理论分析结果来实现。
验证是指通过改变模型的一些参数或加载条件,来验证分析结果的可重复性和一致性。
结论:本文基于ANSYS软件对传动轴的受力进行了分析。
汽车传动轴临界转速的有限元法计算

汽车传动轴临界转速的有限元法计算季 钢摘要 用有限元方法分析和计算汽车传动轴的临界转速,给出了相应的计算模型,并将计算的结果与实验结果相比较,为传动轴的设计与其临界转速的测定和计算提供了一种新的方法。
关键词:汽车传动轴 临界转速 有限元汽车传动轴的临界转速直接关系到汽车的高速性与平稳性。
传动轴系统在常用转速区出现共振,会使轴系和传动齿轮承受极大的交变冲击力,发生较强的机械振动与噪声,严重时还会导致断轴或断齿,造成事故。
目前国内较注重传动轴的动平衡,但对传动轴的共振频率的分布却研究甚少。
而事实上在大多数情况下,共振问题的产生往往是由于传动系统自振频率布置不当造成的,为了避免发生共振,通常可以修正系统的动力学参数(例如转动惯量和轴段与部件的刚度等),调整自振频率。
这些工作若能在汽车动力传动轴系的设计阶段加以解决,则最为经济和方便。
计算传动轴的临界转速相当于计算它的固有频率,计算轴系的固有频率有很多方法,本文介绍有限元方法进行分析和计算。
一、有限元法动力分析有限元法是最近三四十年发展起来的一门数值分析技术,是借助高速电子计算机解场问题的近似计算方法。
它运用离散的概念,使整个问题由整体连续到分段连续,由整体解析转化为分段解析,从而使数值法与解析法互相结合,互相渗透,形成一种新的数值计算方法。
首先把连续体离散化,把连续体假想分割成数目有限的小块单元,而单元之间只在数目有限的指定点处相互连结。
其次,选择一个较简单的函数来近似地表示其位移的分布规律,并用物理学中的基本方程建立起单元上节点力与位移的关系。
最后,借助于矩阵方法集合起来,利用各种方法求解方程组,得到所要求的结果。
动力学分析是有限元法的一个重要应用范围,结构的动力方程可由节点平衡条件来导出。
节点上的作用力可分为两类,作用于节点上的外载荷与相关单元对该节点的作用力。
汇集所有的节点方程,便得到结构的动力平衡方程,用矩阵符号可表示为: [M][ ]+[C][ ]+[K][ ]=[R](1)!!!其中[ ],[],[ ]分别是结构的节点位移、节点速度、节点加速度向量;[R]是结构的整体载荷向量,是t的函数;[K]是结构的整体刚度矩阵,由各个单元刚度矩阵集合而成;[C]是结构的整体阻尼矩阵,由各个单元阻尼矩阵集合而成;[M]是结构的整体质量矩阵,由各个单元质量矩阵集合而成;式(1)是用有限元法求解结构动力问题的基本方程,它是一个大型的二阶常微分方程组,简称为动力方程。
铺层角度对无人机复合材料传动轴影响的有限元分析

铺层角度对无人机复合材料传动轴影响的有限元分析摘要目前无人机机身构件已普遍采用复合材料以减轻自重,但其传动系统仍采用金属材料,不仅自重大、传动效率低,并且随之产生振动严重的问题,影响飞行控制甚至飞行安全。
碳纤维复合材料传动轴不仅质量轻,具有比强度高、比模量大、耐疲劳性能好、且噪声小、振动衰减性好、减振性能好、安全性能好以及可设计性强等优点,解决这个问题的有效途径之一就是用轻质、高强度的复合材料代替金属材料来制备传动轴。
本文以某小型飞机传动轴为研究背景,对碳纤维复合材料传动轴连接结构受力情况进行了理论分析,确定了连接结构和碳纤维复合材料管的失效判断依据。
根据铺设角度对扭转能力的影响和复合材料层合板的一般设计原则,设计了单层厚度相同以及4种不同的铺设顺序并对其分别进行仿真分析,根据分析结果确定最终铺设方案。
通过本文研究,45°铺层角度有利于提高轴体的抗扭性能,而在仅考虑增强轴体的扭转强度时,在0°与90°之间增加45°的铺层顺序是较好的铺层方案。
所设计的连接结构和所选择的铺层方案均满足无人机传动轴的设计要求,并在一定程度上减轻了传动轴的重量,完成无人机轻量化目标。
关键词:复合材料;传动轴;有限元分析;ANSYS1.引言传动轴是飞机结构中重要的动力传输构件,承受着飞机发动机传递出去的动力,连接可移动或可转动的部件,它必须具有较高的抗扭性能力才不会失效。
因为现代飞机的主要制造材料已经从单一的材料过渡到了复合材料,并且因为其优越性能而受到青睐,但是相关的结构设计标准仍存在许多问题,这将使得复合材料的有效应用受到许多限制。
因此研究出在给定扭矩情况下复合材料传动轴的位移以及应力的失效情况并避免其发生,将会大大提高飞机飞行时的安全性。
使用碳纤维管[[1]]作为无人机的传动轴,可以显著减轻结构的质量。
本文使用ANSYS软件建立有限元几何模型,并在对其施加固定扭矩的情况下改变铺层角度。
传动轴有限元分析

汽车结构有限元分析研究报告姓名:班级:学号:盐城工学院汽车工程学院传动轴有限元分析研究报告盐城工学院汽车工程学院车辆工程专业江苏,盐城226000摘要:ANSYS软件是美国ANSYS公司研制的大型通用有限元分析(FEA)软件,是世界范围内增长最快的计算机辅助工程(CAE)软件,能与多数计算机辅助设计(CAD,computer Aided design)软件接口,实现数据的共享和交换,如,Alogor, I-DEAS,CAD等。
ANSYS 有限元软件包是一个多用途的有限元法计算机设计程序,可以用来求解结构、流体、电力、电磁场及碰撞等问题。
因此它可应用于以下工业领域:航空航天、汽车工业、生物医学、桥梁、建筑、电子产品、重型机械、微机电系统、运动器械等。
传动轴是最常件的零件,该零件结构较为简单,操作方便,加工精度高,价格低廉,因此得到了广泛的使用。
目前很多传动轴都做了适当的改进,使其适用性得到了更大的提高。
本设计是基于 ANSYS软件来汽车曲柄连杆机构行分析。
与传统的计算相比,借助于计算机有限元分析方法能更加快捷和精确的得到结果。
设置正确的模型、划分合适的网格,并合理设置求解过程,能够准确的获得分析模型各个部位的应力、变形等结果。
对零件的设计和优化有很大的参考作用。
关键词:三维建模,曲柄连杆机构,有限元,ANSYS,动静态分析引言随着发动机强化指标的不断提高,曲柄连杆机构的工作条件更加复杂。
在多种周期性变化载荷的作用下,如何在设计过程中保证曲柄连杆机构中的主要部件曲轴具有足够的疲劳强度和刚度及良好的动静态力学特性成为机构设计中的关键性问题[3]。
由于在实际工况中曲轴承受活塞、连杆传递的爆发压力的交变载荷作用,受力情况极其复杂。
采用传统的单纯有限元分析方法,很难完成对曲轴运行过程中动态变化边界条件的描述[4-5]。
为了真实全面地了解曲轴在实际运行工况下的力学特性,本课题通过运用CAD软件建立曲柄连杆机构各组成零件的几何模型,确定机构的质量特性参数,通过有限元分析软件Hyperworks和MSC.Nastran的联合仿真,对曲轴和连杆进行自由模态分析,输出振型和频率,将生成的模态中性文件导入ADAMS/View中建立曲柄连杆机构的多柔体动力学模型,应用durability 模块仿真分析曲轴和连杆在爆发压力和惯性力作用下的疲劳应力,由此可以清楚地了解曲轴和连杆在工作过程中各部分的应力,应变,迅速找到危险部位,为机构的优化设计奠定基础。
基于ANSYS有限元的复合材料传动轴失效分析
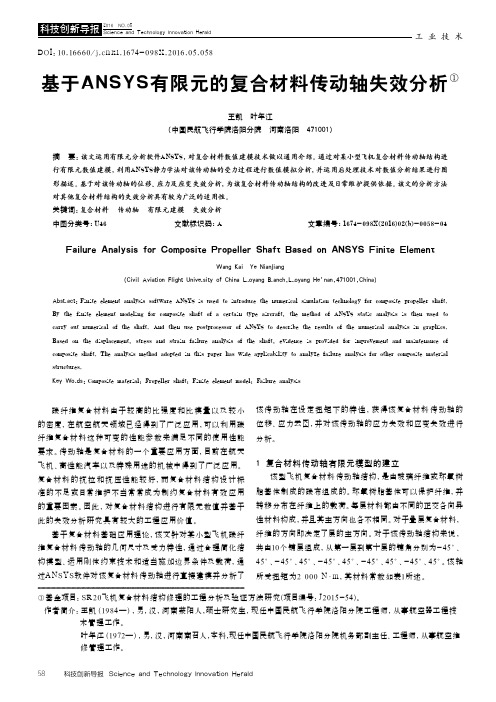
碳纤维复合材料由于较高的比强度和比模量以及较小的密度,在航空航天领域已经得到了广泛应用,可以利用碳纤维复合材料这种可变的性能参数来满足不同的使用性能要求。
传动轴是复合材料的一个重要应用方面,目前在航天飞机、高性能汽车以及特殊用途的机械中得到了广泛应用。
复合材料的抗拉和抗压性能较好,而复合材料结构设计标准的不足或日常维护不当常常成为制约复合材料有效应用的重要因素。
因此,对复合材料结构进行有限元数值并基于此的失效分析研究具有较大的工程应用价值。
基于复合材料基础应用理论,该文针对某小型飞机碳纤维复合材料传动轴的几何尺寸及受力特性,通过合理简化结构模型、运用刚体约束技术和适当施加边界条件及载荷,通过A NSYS软件对该复合材料传动轴进行直接建模并分析了该传动轴在设定扭矩下的特性,获得该复合材料传动轴的位移、应力云图,并对该传动轴的应力失效和应变失效进行分析。
1 复合材料传动轴有限元模型的建立该型飞机复合材料传动轴结构,是由玻璃纤维或环氧树脂基体制成的碳布组成的。
环氧树脂基体可以保护纤维,并转移分布在纤维上的载荷。
每层材料都由不同的正交各向异性材料构成,并且其主方向也各不相同。
对于叠层复合材料,纤维的方向即决定了层的主方向。
对于该传动轴结构来说,共由10个铺层组成,从第一层到第十层的铺角分别为-45°、45°、-45°、45°、-45°、45°、-45°、45°、-45°、45°。
该轴所受扭矩为2 000 N ·m,其材料常数如表1所述。
①基金项目:SR 20飞机复合材料结构修理的工程分析及验证方法研究(项目编号:J2015-54)。
作者简介:王凯(1984—),男,汉,河南荥阳人,硕士研究生,现任中国民航飞行学院洛阳分院工程师,从事航空器工程技 术管理工作。
叶年江(1972—),男,汉,河南南召人,本科,现任中国民航飞行学院洛阳分院机务部副主任、工程师,从事航空维 修管理工作。
装载机用万向传动轴有限元分析及结构改进
装载机用万向传动轴有限元分析及结构改进1. 引言1.1 研究背景装载机是工程机械领域常见的设备之一,广泛应用于土方工程、矿山和建筑工地等场合。
装载机用万向传动轴作为重要的传动部件,承担着将发动机的动力传递至车轮的重要功能。
在长时间的工作过程中,万向传动轴往往会受到较大的力学载荷和振动,容易出现断裂、松动等问题,导致装载机的行驶安全性和稳定性受到影响。
针对装载机用万向传动轴存在的问题,有必要对其进行有限元分析,并通过结构改进来提升其性能和可靠性。
本文将对装载机用万向传动轴进行有限元分析,并提出结构改进方案,以期达到提高装载机性能和可靠性的目的。
通过本文的研究,我们希望能够为装载机制造行业提供更加科学、合理的设计和改进方案,为装载机的发展做出贡献。
1.2 研究意义装载机作为重型机械设备,在工程施工、矿山开采等领域扮演着重要角色。
而装载机用万向传动轴作为传动系统的重要组成部分,直接影响着整机的性能和稳定性。
对装载机用万向传动轴进行有限元分析及结构改进具有重要的研究意义。
通过对万向传动轴进行有限元分析,可以深入了解其受力情况、位移变化等关键参数,为优化设计提供科学依据。
通过改进传动轴的结构,可以提高其承载能力和使用寿命,降低故障率,从而提高装载机的工作效率和可靠性。
优化设计还可以降低装载机的维护成本和使用成本,提高整体竞争力。
装载机用万向传动轴的有限元分析及结构改进不仅有助于提升装载机的性能和稳定性,还可以降低装载机的运营成本,对于推动装载机行业的发展具有积极意义。
本研究对于提升装载机制造水平、促进行业发展具有重要的现实意义和深远影响。
2. 正文2.1 万向传动轴的设计原理万向传动轴是一种用于装载机等工程机械中的重要传动装置,其设计原理主要是利用万向节的特殊结构实现传递动力和转角的功能。
万向节由两个十字轴和四个万向轴承组成,可以实现在不同方向上的传动和转动。
在装载机工作过程中,由于不同工况下对转向和传动的要求不同,因此装载机上的万向传动轴往往需要具有较高的可调性和可靠性。
基于有限元分析的输出轴的设计
基于有限元分析的输出轴的设计
由于日益提高的产品质量和性能要求,传动设计的核心在于减少系统中的振动噪声和损伤。
因此,对于输出轴的设计,有限元分析将成为设计传动系统中重要的一环。
有限元分析能够以数值形式描述模型结构的动态响应行为,从而有利于研究输出轴的结构参数的优化设计。
有限元分析的第一步是建立模型,一般可以使用三维有限元软件来建立模型,建立后的模型需要封装和装配,以模拟真实的物理过程,可以针对各种载荷、应力分布等进行模拟分析。
然后,在有限元分析中,需要使用有限元素对输出轴进行建模,一般采用有限元素建模可以提高计算速度,有利于优化输出轴的结构设计。
然后,可以结合材料参数,进行线性和非线性分析,确定应力和变形,从而推算输出轴的疲劳寿命。
再者,在传动系统中,温度变化将对输出轴产生影响,因此需要对温度变化的影响进行分析。
可以使用FEM固有温度场模型,通过数值模拟加热散热过程,从而推算温度场的变化,结果可以作为后续输出轴的应力变形分析的参数。
最后,在有限元分析中,可以考虑使用变分法,计算输出轴的最优构型,从而使输出轴拥有更高的刚性与强度,减少系统中的振动。
总之,有限元分析将为输出轴设计提供有效的帮助,可以从数值角度分析输出轴的动态行为,从而使输出轴的结构更加完善。
基于有限元分析的结果,可以准确确定输出轴的性能参数,有利于优化系统
的可靠性。
基于ANSYS workbench的汽车传动轴有限元分析和优化设计
基于ANSYS workbench的汽车传动轴有限元分析和优化设计使用ANSYS Workbench进行汽车传动轴的有限元分析和优化设计是一种常见的方法。
以下是基于ANSYS Workbench的汽车传动轴有限元分析和优化设计的一般步骤:1.创建几何模型:使用CAD软件创建传动轴的几何模型,并将其导入到ANSYS Workbench中。
确保几何模型准确、完整,并符合设计要求。
2.网格划分:对传动轴几何模型进行网格划分,将其划分为离散的单元。
选择合适的网格划分方法和单元类型,以确保模型的准确性和计算效率。
3.材料属性定义:定义传动轴所使用的材料的力学性质,如弹性模量、泊松比、密度等。
确保选择适当的材料模型,以准确模拟材料的行为。
4.载荷和约束定义:定义施加在传动轴上的载荷,如扭矩、轴向力等。
同时,定义约束条件,如固定轴承端点、自由转动等。
5.设置分析类型和求解器:根据实际情况选择适当的分析类型,如静态、动态、模态等。
配置求解器设置,选择合适的求解器类型和参数。
6.进行有限元分析:运行有限元分析,计算传动轴的应力、变形和振动等。
根据分析结果,评估传动轴的性能和强度。
7.优化设计:根据有限元分析的结果,对传动轴的结构进行优化设计。
通过调整传动轴的几何形状、材料或其他参数,以提高其性能。
8.重新进行有限元分析:对优化后的设计进行再次有限元分析,以验证优化结果。
如果需要,可以多次进行重复优化和分析的步骤。
9.结果评估和优化验证:评估优化结果的有效性,并验证传动轴在实际工况下的性能。
根据需求进行修正和改进。
请注意,基于ANSYS Workbench的有限元分析和优化设计需要一定的专业知识和技能。
基于ANSYS的汽车传动轴的有限元分析_唐良兵
空心轴受到的最大剪应力为 Max=54.246 MPa; 实心轴受到的最大剪应力为 Max=79.509 MPa。 可见在载荷相同的条件下,空心轴的重量 只为实心轴的 32.36%,并且从数据中可以看出 其安全性能更好。空心轴在减轻重量、节约材 料、提高安全性等方面效果非常明显。因此, 在保持转矩不变的条件下,空心轴可以比实心 轴少用材料,重量将会大幅减轻。
收稿日期:2012-06-18 作者简介:唐良兵(1975-),男,湖北武汉人,硕士,主要研究方向为精密机械设计、非标机械设计。
・46・
计算机应用技术 (如图 1 所示)。
机械
2013 年第 1 期 总第 40 卷
取 2E11 Pa, 泊松比 μ 取 0.27, 许用应力[τ]及许 用扭转角[θ]分别为 60 MPa 和 2°/m。 首先在三维软件 Pro/E 中建立一段直径为 90 mm、长为 150 mm、壁厚为 2.5 mm 的圆管, 传动轴的长短并不影响传动轴的强度和刚度校 核,这里取 90 mm,是考虑到进行 ANSYS 有 限元分析时所花的时间短一些。
Wt
max
( 1) ( 2)
πD3 16
可以初步确定实心轴的半径 R=26 mm。
2.1 实心传动轴有限元模型的建立
实心轴的模型建立与空心轴建立是一致 的,在 Pro/E 软件中建立一段直径为 26 mm, 长 90 mm 的实心圆筒,导入到 ANSYS 中进行 分析,采用相同的映射网格划分。
由表 1 可知,694 号节点切向位移最大, Max=-0.91217E-01,对应的转角为:
机械
2013 年第 1 期 总第 40 卷
计算机应用技术
・47・
d
d x 0.091217 2.02705E - 3 rad 45 R
- 1、下载文档前请自行甄别文档内容的完整性,平台不提供额外的编辑、内容补充、找答案等附加服务。
- 2、"仅部分预览"的文档,不可在线预览部分如存在完整性等问题,可反馈申请退款(可完整预览的文档不适用该条件!)。
- 3、如文档侵犯您的权益,请联系客服反馈,我们会尽快为您处理(人工客服工作时间:9:00-18:30)。
汽车结构有限元分析研究报告姓名:班级:学号:盐城工学院汽车工程学院传动轴有限元分析研究报告盐城工学院汽车工程学院车辆工程专业江苏,盐城226000摘要:ANSYS软件是美国ANSYS公司研制的大型通用有限元分析(FEA)软件,是世界范围内增长最快的计算机辅助工程(CAE)软件,能与多数计算机辅助设计(CAD,computer Aided design)软件接口,实现数据的共享和交换,如,Alogor, I-DEAS,CAD等。
ANSYS 有限元软件包是一个多用途的有限元法计算机设计程序,可以用来求解结构、流体、电力、电磁场及碰撞等问题。
因此它可应用于以下工业领域:航空航天、汽车工业、生物医学、桥梁、建筑、电子产品、重型机械、微机电系统、运动器械等。
传动轴是最常件的零件,该零件结构较为简单,操作方便,加工精度高,价格低廉,因此得到了广泛的使用。
目前很多传动轴都做了适当的改进,使其适用性得到了更大的提高。
本设计是基于 ANSYS软件来汽车曲柄连杆机构行分析。
与传统的计算相比,借助于计算机有限元分析方法能更加快捷和精确的得到结果。
设置正确的模型、划分合适的网格,并合理设置求解过程,能够准确的获得分析模型各个部位的应力、变形等结果。
对零件的设计和优化有很大的参考作用。
关键词:三维建模,曲柄连杆机构,有限元,ANSYS,动静态分析引言随着发动机强化指标的不断提高,曲柄连杆机构的工作条件更加复杂。
在多种周期性变化载荷的作用下,如何在设计过程中保证曲柄连杆机构中的主要部件曲轴具有足够的疲劳强度和刚度及良好的动静态力学特性成为机构设计中的关键性问题[3]。
由于在实际工况中曲轴承受活塞、连杆传递的爆发压力的交变载荷作用,受力情况极其复杂。
采用传统的单纯有限元分析方法,很难完成对曲轴运行过程中动态变化边界条件的描述[4-5]。
为了真实全面地了解曲轴在实际运行工况下的力学特性,本课题通过运用CAD软件建立曲柄连杆机构各组成零件的几何模型,确定机构的质量特性参数,通过有限元分析软件Hyperworks和MSC.Nastran的联合仿真,对曲轴和连杆进行自由模态分析,输出振型和频率,将生成的模态中性文件导入ADAMS/View中建立曲柄连杆机构的多柔体动力学模型,应用durability 模块仿真分析曲轴和连杆在爆发压力和惯性力作用下的疲劳应力,由此可以清楚地了解曲轴和连杆在工作过程中各部分的应力,应变,迅速找到危险部位,为机构的优化设计奠定基础。
曲柄连杆机构有限元分析研究报告曲轴的有限元模型的建立曲轴结构形状复杂,在实际工作中,为了减少应力集中,曲轴不同截面的结合处都有半径较小的倒角,同时为了实现曲轴和轴承间的润滑,曲轴上布置了许多油孔。
在对曲轴进行简化过程中,考虑到倒角和油孔对整体结构动力学影响较小,故在对曲轴进行离散生成柔性体之前将这些几何特征抑制掉。
用鼠标左键点选Pro/E菜单栏中的【文件】/【保存副本】命令,便出现保存副本的对话框如图。
系统默认的【文件类型】为【零件】,将文件输出的格式更改为【IGES】,选择保存路径为G盘下,输入文件名称prt0001,单击【确定】按钮。
此时出现【输出IGES】的对话框,系统默认为【曲面】,将其更改为【实体】,如下图所示。
单击【确定】按钮,将完成Pro/E输出文件的保存。
启动ANSYS,在ANSYS菜单栏中,单击【File】/【Import】/【IGES】,将出现一对话框,单击【OK】按钮,便出现如图所示的【Import IGES File】对话框。
单击【Browse】按钮,出现文件打开对话,选择文件路径G:\prt0001.igs,单击【打开】按钮,便回到【Import IGES File】对话框,单击【OK】按钮即可将实体模型调入ANSYS软件,最终生成的有限元模型如图所示。
在调入ANSYS之前,考虑到计算分析的需要,在不影响分析结果的前提下,对连杆实体模型稍微作了简化处理,例如将不关键的小圆角、小倒角删去,这样将使得结构有限元结点数和单元数目减少许多,提高计算速度。
单元选择及网格划分有限元分析的基础是单元,所以,在有限元分析之前必须将实物模型划分为等效节点和单元。
在ANSYS 单元库中有100 多种不同类型的单元,不同的单元类型决定单元的自由度、代表不同的分析领域,单元是属于二维空间还是三维空间等特性。
本文采用有限元接触分析属于非线性分析,运算量庞大,为提高运算速度,要求参与运算的节点和单元应尽可能少,但为了保证计算精度,模型网格应小到足以表述出模型的形状,否则,过粗的网格会造成较大的误差。
在有限元分析中,单元类型的选择和网格划分的精细程度决定了分析结果的准确性。
一般情况下,单元类型应尽量选择六面体和五面体,避免使用不稳定的四面体单元,这样有利于提高计算精度。
但是,连杆装配体形状很不规则,不满足六面体和五面体映射划分(mapped meshing)的拓扑结构,故选择四面体单元Solid92,采用ANSYS 自带的自由网格划分(Free meshing)方式对模型进行网格划分。
Solid92是三维10 节点四面体单元,具有二次位移(quadratic displacement)特性,适合于不规则几何体的网格划分,其每个节点有三个自由度,分别为x y z 三方向的位移。
发动机连杆有限元模型的网格化分实体模型建立后,要进行有限元分析,需要将实体模型转化为能够直接计算的网格,这种转化叫做网格划分。
再对模型进行网格划分之前,甚至在建立模型的阶段,就应同步考虑网格划分的问题,如网格划分单元属性、网格划分类型、网格划分方式、网格密度、单元形状等。
(1)定义单元类型。
在有限元分析过程中,对于不同的问题,需要应用不同特性的单元,同时每一种单元也是专门为有限元问题而设计的。
因此,在进行有限元分析之前,选择和定义适合自己问题的单元是非常必要。
单元选择不当,直接影响到计算能否进行和结果的精度。
为适应不同的分析问题,ANSYS提供了一百多种不同的单元类型。
从普通的点单元、线单元、面单元、体单元到特殊的接触单元、间隙单元和单元坐标系等。
单击【Main Menu】/【Preprocessor】/【Element Type】/【Add/Edit/Delete】,将出现一对话框。
点击【Add】进行添加,如图所示。
点击【Solid】/【10node 92】,确认【OK】,关闭【Element Type】对话框即完成单元类型的定义。
(2)定义实常数。
在进行单元特性分析时,有些单元数据可能无法从节点坐标系或材料特性中得到,这时就要定义实常数,以提供单元特性计算时使用。
常见的实常数包括厚度、横截面、高度等。
实常数的设置是依赖于单元类型的,如BEAM单元的横截面特性、SHELL 单元的厚度设置等。
对于Solid类型中的10node 92,不需要设置实常数。
(3)定义材料特性。
常见的材料特性包括:弹性模量、泊松比、密度、比热、热膨胀系数等。
每种材料特性都可以为温度的函数,可随温度的变化而变化。
材料特性的定义可以分为两个大类:线性材料定义和非线性材料定义。
单击【Main Menu】/【Preprocessor】/【Material Props】/【Material Models】,将出现一对话框,如图所示。
双击【Structural】/【Linear】/【Elastic】/【Isotropic】,即可出现一对话框如图4.7所示。
将材料的弹性模量和泊松比填入空格,即可完成材料属性的定义。
点击【Main Menu】/【Preprocessor】/【Meshing】/【MeshTool】,打开网格划分工具对话框。
选择自由划分,即点中Smart Size,在【Smart Size】中选中划分精度为“6”,然后单击【Mesh】, 便出现一个拾取框,单击【Pick All】按钮,至此,网格划分完成,如图所示。
位移边界条件边界条件的选取是分析的重要环节,其选取正确与否,不仅影响计算精度,而且对非线性分析还将影响运算是否收敛[8]。
不合理的边界条件可能使计算失败,导致计算不出结果。
对一个自由体,结构本身无约束,仅有自相平衡的外力,是无法求出定解节点位移,所以对于分析模型,要对某些节点的自由度加以限制。
本文分析模型是按如下方法进行约束:为限制模型在z 轴方向的刚体运动,在模型上半部分选几个点上加z方向上的约束;为限制模型在x轴方向的刚体运动,在模型的上半部分选几个点加x方向的约束,为限制整个分析模型在y轴方向的刚体运动,完全限制连杆大头内表面的自由度。
位移约束的操作单击【Main Menu】/【Solution】/【Define Loads】/【Apply】/【Structural】/【Displacement】/【On Areas】如图,将出现一对话框,如图所示。
此时,鼠标将变为向上的箭头进行选面,面被选中后将变亮。
对于该机体,选取连杆大头内120度的下表面施加位移约束,选中后,单击对话框中的【OK】,将自动弹出一新的对话框,如图所示。
选中【All DOF】,点击【OK】。
连杆大头被加全约束。
然后,再单击【Main Menu】/【Solution】/【Define Loads】/【Apply】/【Structural】/【Displacement】/【On Areas】选择大头孔和小头孔的四个外圆面,施加Z方向的位移约束。
加上后得道如图4.12所示图形。
载荷处理载荷可以直接施加在几何模型上,如点、线、面和体,同时也可以施加在有限元模型上,如单元和节点。
若载荷施加在有限元模型上,ANSYS在求解之前会自动将这些载荷转换到相应的节点和单元上。
连杆在工作时,承受周期性变化的外力作用。
其主要由两部分组成:一是经活塞顶传来的燃气爆发力,对连杆起压缩作用,二是活塞连杆组高速运动产生的惯性力,对连杆起拉伸作用;在分析时,认为最大燃气爆发力和惯性力均在上止点附近出现,俩者可以叠加。
另外,还有连杆小头所装的衬套、大头所装的连杆瓦作用在孔径上的过盈力,及连杆螺栓预紧力所产生附加载荷。
用有限元法可对连杆在整个7200循环中进行动态分析,会得到理想的结果,但计算过程过于复杂。
因连杆破坏大都是拉、压疲劳断裂所致。
故计算时选择了连杆在受最大拉力和最大压力这两种极端情形来计算应力的分布情况。
这样既能得到两个最危险受力工况下的应力和变形的分布情况,又能满足工程设计要求,实现计算简便,节省机时[9]。
结果分析:本文以195型柴油机连杆为研究对象,按照连杆的实际工作情况,同时考虑活塞销、曲轴连杆轴颈对连杆的影响,利用三维造型软件PRO/E 建立连杆三维有限元分析模型。
(1)建立连杆小头和大头的模型 (2)按标准尺寸创建杆身 (3)按标准尺寸对杆身和大小头连接处导圆角 (4)按标准尺寸创建小头孔 (5)按标准尺寸创建连杆大头孔 (6)按标准尺寸创建连杆工字形杆身 (7)按标准尺寸创建连杆大头螺栓座然后把连杆模型导入有限元分析软件ANSYS 中,取高阶四面体单元SOLID92,划分有限元网格;在有限元模型上加约束,加载最大拉力进行有限元分析,找出有限元模型的位移变形图和平均等效应力图,得出结论;接着再分析受最大压力时连杆的位移变形图和平均等效应力图。