固体添加剂和摩擦改进剂对锂基润滑脂性能的影响
含纳米铋粉锂基润滑脂抗磨减摩性能研究
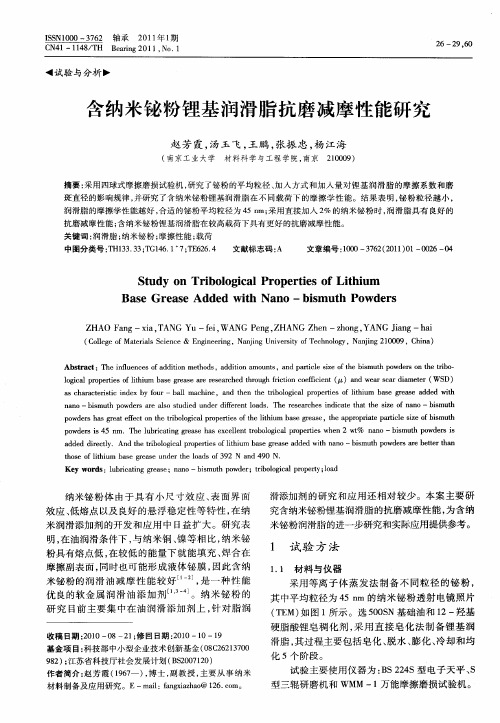
润 滑 脂 的 摩 擦 学 性 能 越 好 , 适 的铋 粉 平 均 粒 径 为 4 m; 用 直 接 加 入 2 的 纳 米 铋 粉 时 , 滑 脂 具 有 良好 的 合 5n 采 % 润
抗磨减摩性能 ; 含纳米铋粉锂基 润滑脂在 较高 载荷 下具 有更 好的抗磨 减摩性能。
关 键 词 : 滑 脂 ; 米 铋 粉 ; 擦 性 能 ; 荷 润 纳 摩 载 中图分 类 号 :H13 3 ;G 4 . 7 T 664 T 3 .3T 16 1 ;E 2 . 文 献标 志 码 : A 文章 编 号 :00— 7 2 2 1 ) l 02 0 10 36 (0 1 o 一 06— 4
( 京 工 业 大 学 材 料 科 学 与 工 程 学 院 , 京 南 南 20 0 ) 109
摘要 : 采用 四球式摩擦磨损试验机 , 研究了铋粉的平均粒径 、 加入方 式和加 入量对 锂基润 滑脂 的摩 擦系数 和磨 斑直径的影响规律 , 并研究 了含纳米铋粉锂基润滑脂 在不 同载荷下 的摩擦 学性能 。结 果表 明 , 铋粉 粒径越小 ,
l ia po etso lhu aeges r r erh dtruhfc o ofc n 肛)adw a a im t WS ) o cl r re fi im bs raeae e ace og t nce i t( g p i t s h i ri i e n er er a e r( D s d e
锂离子电池电解液中添加剂对电池性能的影响分析
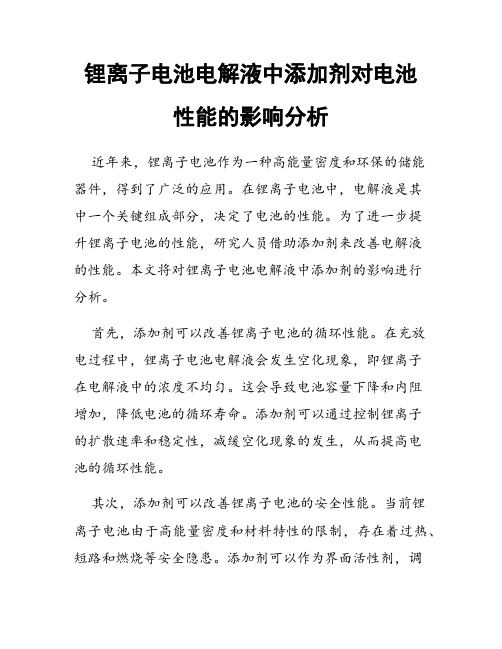
锂离子电池电解液中添加剂对电池性能的影响分析近年来,锂离子电池作为一种高能量密度和环保的储能器件,得到了广泛的应用。
在锂离子电池中,电解液是其中一个关键组成部分,决定了电池的性能。
为了进一步提升锂离子电池的性能,研究人员借助添加剂来改善电解液的性能。
本文将对锂离子电池电解液中添加剂的影响进行分析。
首先,添加剂可以改善锂离子电池的循环性能。
在充放电过程中,锂离子电池电解液会发生空化现象,即锂离子在电解液中的浓度不均匀。
这会导致电池容量下降和内阻增加,降低电池的循环寿命。
添加剂可以通过控制锂离子的扩散速率和稳定性,减缓空化现象的发生,从而提高电池的循环性能。
其次,添加剂可以改善锂离子电池的安全性能。
当前锂离子电池由于高能量密度和材料特性的限制,存在着过热、短路和燃烧等安全隐患。
添加剂可以作为界面活性剂,调节电解液与电极之间的相互作用,减少电池内部的过电位和电解液的挥发性,提高电池的安全性能,降低火灾和爆炸的风险。
第三,添加剂可以提高锂离子电池的温度性能。
在低温下,锂离子的迁移和扩散速率会降低,导致电池的性能下降。
通过加入某些添加剂,可以降低电解液的凝固温度,增加电解液的离子传导性,提高锂离子电池在低温下的工作性能。
此外,添加剂还可以改善锂离子电池的充放电性能。
添加剂可以调整电解液的PH值和电化学窗口,提高锂离子电池的电化学稳定性和电池效率。
一些添加剂还可以减少电解液中的气体生成,降低电池的内阻,提高电池的充放电效率和功率密度。
然而,锂离子电池电解液中添加剂的使用也存在一些问题。
首先,添加剂的使用可能会导致电池在高温下的稳定性下降,由于致热反应的发生,增加了电池的自发燃烧和爆炸的风险。
其次,一些添加剂的使用会导致电解液的电导率下降、电池内部结构的破坏和电极材料的腐蚀,影响电池的性能。
总结而言,锂离子电池电解液中添加剂的选择和使用对于提高锂离子电池的性能具有重要意义。
添加剂可以改善电池的循环性能、安全性能、温度性能和充放电性能。
润滑添加剂对7AO4铝合金润滑性能影响研究

3 结论
图 6 采用 T301( 14% ) 时试件表面磨损形貌图
由图可见, 试件表面磨损轻微, 只有一些分布 均匀的细小犁沟。无塑性形变, 无粘结磨损, 只发 生了磨料磨损, 相对于以上四种添加剂而言, T 301 使铝表面的磨损得到了明显改善。这主要是因为 其含有大量活性较强的氯元素, 它可以与金属 表 面发生反应, 生成氯化铝反应膜, 且反应膜内部剪 切强度远低于铝的剪切强度, 摩擦时会发生层 间 滑动, 显示出抗磨和极压作用 [ 6] 。
第 6期
李 欣等: 润 滑添加剂对 7A 04铝合金润滑性能影响研究
73
有所减少, 但其降低 的幅度 比较小, 曲线 比较 平 缓, 当浓度为 12% 、14% 时, 磨 损量分别为 4. 2mg 和 4. 24m g。由此可见添加剂 PriE co 3000对 7A04 铝合金的润滑作用要小于 RC2411和 L62LF。当 加入 T 301和 360P 时, 随着其浓度的增加磨损 量 骤降, 当浓度分别为 14% 和 5% 时, 磨损量可以减 小到 0. 59m g 和 0. 71m g, 与其它几种添加剂相 比 效果非常明显。综上可知, T301和 360P 对 7A04 铝合金具有优良的润滑性能。
图 5是采 用 12% L62LF 时 试件 的磨损 形貌 图。
图 5 采用 L62LF( 12% ) 时试件表面磨损形貌图
从图中可以看出, 试件磨损较轻, 无明显的塑 性形变, 只有一些较浅的犁沟, 犁沟边缘有少量沉 积物。此时摩擦面上主要发生了磨料磨损。这是
74
沈 阳 理工 大 学 学 报
第 29卷
图 2 采用基础油时试件表面磨损形貌图
由图 2可以看出, 只采用基础油进行实验时, 铝表面磨损严重, 产生严重塑性形变, 有很深的犁 沟且犁沟附近无沉积物。此时基础油对铝的磨损 没有起到有效的保护作用, 因为只是在金属摩 擦 面上形成了一层物理吸附膜, 当摩擦温度升高时, 吸附膜承载能力下降, 进而脱吸后失效。综上 所 述, 该非极性的基础油不能抑制两摩擦表面的 接 触和黏结, 会产生严重的磨损, 需要加入承载能力 更强的极压抗磨添加剂来改善其抗磨性。
浅谈添加剂对轴承减摩抗磨性能影响

浅谈添加剂对轴承减摩抗磨性能影响轴承系统作为旋转机械的关键部件之一,其寿命与机器寿命息息相关。
磨损是影响轴承系统寿命的重要因素之一,因此,应提高轴承系统的减摩抗磨性能,从而延长机器的使用寿命。
轴承系统采用边界润滑,对于这种润滑方式而言,其磨损主要取决于润滑油性能及摩擦表面性质和相互运动方式[1]。
在摩擦副表面性质和相互运动方式确定的情况下,提高摩擦副抗磨损性能最行之有效的方法就是改善润滑油性能,而加入少量添加剂是改善润滑油性能的有效手段。
但是,添加剂之间有时会产生互相制约作用,因此必须注意它们之间的影响和综合应用效果。
若能选择恰当的添加剂配方,能够有效提高摩擦副的抗磨损性能,然而要获得添加剂的综合效果往往是不容易的。
1、台架试验:前期曾针对润滑油添加剂的使用性能专门开展了的试样试验[2],通过比较磨斑直径和磨痕宽度已基本确定出添加剂的种类和配方。
但是试验结果还需通过台架试验进行考核验证。
台架试验在模拟实际使用条件下进行的,更接近实际工况。
通过对试验条件进行强化和控制,能够在短时间内获得试验数据,校验添加剂对轴承减摩抗磨性能设计的合理性。
由于轴承系统结构的特殊性,其磨损进程较为缓慢,为了能在较短的时间内给出添加剂对轴承减摩抗磨性能的评判结果,需要采用较实际使用条件更为恶劣的环境,同时还应保证不改变轴承系统的摩擦磨损机理,通过分析比较,确定采用增大轴承径向承载的方法。
1.1磨损机理分析:对增大轴承径向承载后轴承的磨损机理进行了分析。
轴承的磨损机理主要受:运动形式、润滑状态、磨损形式的鉴别方式和添加剂的作用机理四种因素影响。
其中,两者的润滑方式相同,均为边界润滑;添加剂的作用机理均是在摩擦副表面形成化学反应膜;在润滑状态和添加剂作用机理方面两者相同。
而在运动方式方面,运动方式主要与:运转方式、载荷方式和环境因素有关,增大径向载荷仅是在载荷方式上略有不同;磨损形式的鉴别方式方面正常状态下磨损形式仅为磨粒磨损。
锂基润滑脂常用的添加剂

由于现代技术的发展,在钢铁工业、重型机械工业中许多设备的润滑均处于边界润滑状态,机械工作部位的润滑需要使用优质极压润滑脂以满足润滑要求。锂基润滑脂是一种通用性润滑脂,与极压、抗磨添加剂的配伍性好,加入极压抗磨添加剂后可制备性能优良的极压锂基润滑脂。
极压添加剂的使用效果大致有这样的规律。磷化合物能有效地提高润滑脂的抗磨性,而硫、氯化合物能有效地提高润滑脂的耐负荷性,含硫化合物比含氯化物效果更好,同时含氯和磷的化合物或含磷和硫的化合物,既具有极压性又具有抗磨性。为了改进润滑批的抗磨性和极压性可以复合使用两种或多种极压抗磨添加剂 。以铁霸二硫化钼油脂为例,美国铁霸二硫化钼极压高温润滑脂是由深度精练的矿物油配合以二硫化钼干性极压剂经过精心调配而成的锂基脂,具有良好的抗剪切性、抗氧化性;同时具有良好的高负荷承受性和耐水性,是一种多用途润滑脂。
锂基润滑脂常用的添加剂
锂基润滑脂常用的添加剂和其他润滑脂相类似,但锂基润滑脂使用的添加剂更广泛,它对于许多添加剂有着良好的配伍性。常用的添加剂主要有抗氧剂、金属表面钝化剂、防腐剂、结构改盖剂、极压抗磨剂、色泽稳定剂、拉丝性增强剂。
1、抗氧剂
常用的锂基润滑脂的抗氧剂主要有:
(2)苯其-α-萘胺 又名防老剂甲,石油添加剂统一代号T531。无色片状结晶,暴露于日光或空气中逐渐变成黄色或紫色。有毒!相对密度1.16~1.17,熔点62℃。不溶于水,溶于乙醇、乙醚、苯等有机溶剂。主要作橡胶制品的防老剂,同时也是润滑脂最有效的氧化抑制剂之一。在合成酯类油等锂基润滑脂中常用,使用温度可达150℃。添加量一般为0.1%~1.0%。
抗氧剂在12-羟基硬脂酸锂基润滑脂中抗氧化效果的顺序下:二苯胺>苯其-α-萘胺>二戊基二硫代氨基甲酸锌。
固体添加剂在润滑脂中的应用研究
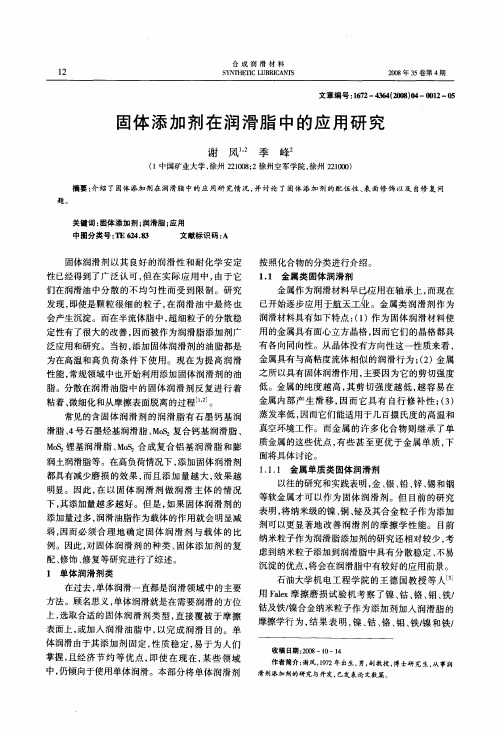
体润滑由于其添加剂 固定 , 性质稳定 , 易于为人们 掌握, 且经 济 节 约 等 优 点 , 使 在 现 在 , 些 领 域 即 某
中 , 倾 向于使 用单体 润滑 。本 部 分将单 体 润滑 剂 仍
收稿 日期 :o8一l 2o O一1 4
作者简介 : 谢凤, 7 年 出生, 副教授 , 12 9 男, 博士研究 生 从 事润 滑剂添加剂的研 究与 开发 , 已发表论 文数篇。
钨粉末的高温锂基润滑脂 在常温和高温下摩擦磨
损性 能 的研 究 认 为 , 温 下 , 础 脂 中加 入 二 硫化 常 基
数约为 3 合金纳米粒子 比金属单体 纳米粒子 的 %,
润 滑效果 好 ; 金属 纳米 粒子 的 润滑 作用 机 理是 其 在
泛应 用和研 究 。当初 , 加 固体润 滑 剂 的油脂 都是 添
其剪切强度越低 , 越容易在 脂。分散在润滑油脂 中的固体润滑剂反复进行着 低。金属的纯度越高 , 金属 内部 产 生 滑 移 , 因而 它 具 有 自行 修 补 性 ;3 () 粘着、 微细化和从摩擦表面脱离的过程l ] 1。 因而 它们能适 用于 几百摄 氏度 的高温 和 常见 的含 固体 润滑 剂 的 润 滑脂 有 石 墨 钙 基 润 蒸 发率低 ,
,
20 年 3 பைடு நூலகம்第 4 08 5 期
谢凤等 . 固体添加剂在润滑脂中的应用研 究
1 3
钴合金纳米粒子在润滑脂 中具有较好 的稳定性 , 能
够 提 高润滑 脂 的润滑 效果 , 减摩 抗磨 及 承 载 能力 其 均 比基础脂 有较 大 的改善 , 米粒 子 的最 佳 质量 分 纳
初步 的探讨 。通 过 四球 机 试 验 对 加 入 超 细 二 硫化
锂基润滑脂的运动粘度

锂基润滑脂的运动粘度引言润滑脂在机械设备中起着重要的作用,能够减少摩擦和磨损,降低设备的能耗和噪音,延长设备的使用寿命。
锂基润滑脂是一种使用广泛的润滑脂类型,其运动粘度是评价其性能的一个重要指标。
本文将对锂基润滑脂的运动粘度进行深入探讨。
锂基润滑脂的概述锂基润滑脂是以锂基油为基础油,添加多种添加剂并与稠化剂混合而成的润滑脂。
它具有良好的机械稳定性、氧化稳定性和抗水性能,适用于各种工况和温度条件下的润滑。
锂基润滑脂根据其特性和应用领域的不同,可分为多种型号,如高温型、低温型、防水型等。
运动粘度的定义和意义运动粘度是指润滑油或润滑脂在流动状态下抵抗剪切力的能力,是润滑油或润滑脂流动性的度量。
运动粘度的大小直接影响润滑膜的形成和维持,进而影响润滑效果。
因此,运动粘度是评价润滑脂性能的一个重要指标。
运动粘度的测试方法运动粘度的测试一般使用几种不同的方法,如旋转油膜厚度法、滴定法和旋转转子法等。
其中,旋转油膜厚度法是一种常用且精度较高的测试方法,它通过测量旋转带有润滑脂的滚珠轴承的厚度变化来确定润滑脂的运动粘度。
影响锂基润滑脂运动粘度的因素锂基润滑脂的运动粘度受多种因素的影响,包括温度、剪切速率、添加剂和基础油的选择等。
下面将对这些因素进行详细探讨。
温度对运动粘度的影响温度是影响锂基润滑脂运动粘度的主要因素之一。
随着温度的升高,润滑脂的分子流动能力增强,其运动粘度逐渐降低。
这是因为温度升高会导致润滑脂的稠化剂结构发生改变,使其流动性增强。
因此,在高温下,锂基润滑脂的运动粘度常常较低。
剪切速率对运动粘度的影响剪切速率是指润滑脂在流动过程中受到的剪切力大小。
剪切速率的增加会导致润滑脂分子之间的相互作用变弱,流动性增强,运动粘度降低。
因此,在高速摩擦和剪切条件下,锂基润滑脂的运动粘度往往较低。
添加剂对运动粘度的影响添加剂是指在锂基润滑脂中添加的具有特定功能的化学物质,如抗氧化剂、抗磨剂等。
添加剂的种类和含量会对润滑脂的性能产生重要影响。
锂基润滑脂流变性及摩擦学性能相关性研究

锂基润滑脂流变性及摩擦学性能相关性研究史燕;杨清香;宋宝玉;张锋【摘要】By using the lithium base grease as an example,the rheological properties and tribological properties were studied through the R/S cone and plate rheometer and four ball friction and wear tester,and the relationship between rheo-logical properties and friction and wear performance of the greases was investigated.The results show that the apparent vis-cosity is firstly decreased gradually along with increasing of shear rate and temperature,and increased gradually along with increasing of plate-cone clearance,finally it tends to a stable value.The friction coefficient of grease and wear scar diameter are increased gradually along with increasing of the load,and increased first and then decreased along with the increasing of speed and temperature.The rheological properties and tribological properties are changed in the same trend in general along with the speed,load and temperature changing,which shows certain correlation between rheology and tribological properties of lithium base grease.%以锂基润滑脂为例,通过 R/S 锥板式流变仪和四球摩擦磨损试验机,对其流变性能及摩擦磨损性能进行研究,探讨润滑脂流变性能与摩擦磨损性能的相关性。
- 1、下载文档前请自行甄别文档内容的完整性,平台不提供额外的编辑、内容补充、找答案等附加服务。
- 2、"仅部分预览"的文档,不可在线预览部分如存在完整性等问题,可反馈申请退款(可完整预览的文档不适用该条件!)。
- 3、如文档侵犯您的权益,请联系客服反馈,我们会尽快为您处理(人工客服工作时间:9:00-18:30)。
固体添加剂和摩擦改进剂对锂基润滑脂性能的影响范海粉;王瑞兴【摘要】Although the complex lithium grease is the most widely used grease,there still some problems and weakness in lubrication and equipment wear.The influence of performance was studied through different solid additive,friction modi-fier and their respective complex formulation.Result shows that solid additive has a great influence on the extreme pressure anti-wear properties of complex lithium grease;grease could has excellent EP and AW properties by compounding PTFE and MoS2,and it has synergistic effect by compounding Priolube 3986 complex ester and stearic acid,which can enhance reduce friction performance significantly.The compounding of solid additive and friction modifier has complementary advan-tage,overall raise the comprehensive properties of complex lithium grease.%针对常用复合锂基润滑脂存在的润滑极压抗磨性不足等问题,研究不同固体添加剂、摩擦改进剂对复合锂基润滑脂极压抗磨减摩性能的影响。
结果表明,固体添加剂对复合锂基润滑脂极压抗磨性能影响较大,其中PTFE和二硫化钼组成的复配剂可使润滑脂得到优异的极压和抗磨性能;摩擦改进剂Priolube 3986复酯和硬脂酸复配具有协同作用,可明显增强润滑脂的抗磨减摩性能;固体添加剂和摩擦改进剂对润滑脂的润滑作用可以优势互补,全面提升润滑脂综合性能。
【期刊名称】《润滑与密封》【年(卷),期】2016(041)012【总页数】5页(P136-140)【关键词】复合锂基润滑脂;固体添加剂;摩擦改进剂;极压抗磨性【作者】范海粉;王瑞兴【作者单位】上海禾泰特种润滑科技股份有限公司上海200331;上海禾泰特种润滑科技股份有限公司上海200331【正文语种】中文【中图分类】TE626.4;TH117.1在常用的润滑剂中,润滑脂在摩擦表面上具有比润滑油更好的保持能力和黏附性[1],可适用于更加苛刻的操作条件,广泛应用于各种机械设备的润滑。
在润滑脂中添加各种抗磨材料可以大幅提高其极压抗磨减摩性能,研究各类抗磨材料对润滑脂润滑性能的影响,从而降低设备磨损和能耗损失,对于实现十三五期间国家节能降耗目标具有重要意义。
目前锂基润滑脂在工业行业用量最大,约占总用脂量的70%[2]。
传统工艺多选用极压抗磨、抗氧抗腐蚀等添加剂,将锂基脂制备成极压多效型润滑脂。
但这些润滑脂在使用过程中往往存在润滑性特别是抗磨性不足,添加剂消耗过快,长时间使用时易表现出抗磨性能下降、品质劣化等问题。
本文作者在常规的极压型复合锂基脂工艺基础上,重点考察了不同种类固体添加剂、摩擦改进剂以及它们的复配对锂基脂的极压抗磨性、耐磨减摩等性能的影响,并初步得到一种综合性能优异的极压抗磨减摩型锂基润滑脂,符合现代机械设备对润滑脂的高承载、耐磨损的要求。
1.1 实验原料胶体石墨,粒径0.1~5 μm,青岛天盛达石墨有限公司生产;PTFE,粒径2~5 μm,美国杜邦公司生产;轻质碳酸钙,粒径1~3 μm,长兴群丰钙业有限公司生产;二硫化钼,粒径1~1.5 μm,开拓者钼业公司生产;基础油150BS和500SN,日本进口;有机无灰摩擦改进剂Perfad 3000和高黏度复酯Priolube 3986,英国禾大公司生产;癸二酸、十二羟基硬脂酸、硬脂酸、氢氧化锂、T406、TCP306、T323等均为分析纯试剂。
1.2 样品制备以150BS和500SN为基础油,加入12-羟基硬脂酸、癸二酸与一定比例的氢氧化锂,在80~90 ℃下皂化30 min,升温至120~140 ℃脱水,再在210 ℃高温炼制5 min,冷却至120 ℃,加入一定量的TCP306、T323及抗氧剂等常规添加剂,得到具有一定极压抗磨性能的复合锂基脂。
1.3 性能测试采用济南思达特测试技术有限公司生产的MRS-10W型摩擦试验机进行复合锂基脂的极压抗磨性能测试,钢球为上海钢球厂生产的一级GCr15标准钢球。
按照GB-3142方法,分别测试样品润滑脂润滑时的最小烧结负荷(pD值)和最大无卡咬负荷(pB值);按照SH/T 0189方法测试磨斑直径,并同时得到对应的摩擦因数曲线和平均摩擦因数。
本文作者重点考察不同种类的固体添加剂、固体添加剂之间的复配,以及不同种类摩擦改进剂及摩擦改进剂复配对复合锂基脂极压抗磨减摩性能的影响,并得到最优配方组合。
2.1 固体添加剂对复合锂基脂性能的影响固体添加剂以其优异的润滑性、耐化学安定性以及在润滑脂中良好的分散稳定性,在润滑脂中的应用研究较为广泛。
固体添加剂一般都是处于微米及亚微米级的载荷粒子,其在滑动面间的作用机制主要表现在:(1)粒子本身容易剪切,减少了滑动面间的摩擦;(2)减少金属面间直接接触的频度,抑制磨损的产生;(3)附着或沉积在滑动表面的较低部位,减少了相对表面的粗糙度,使油膜不易破裂[3]。
选择胶体石墨、PTFE、轻质碳酸钙、二硫化钼4种固体粉末添加剂,分别以3%质量分数添加到制备的常规极压抗磨复合锂基脂中,所得润滑脂样品分别标记为Grease-石墨、Grease-PTFE、Grease-轻质碳酸钙、Grease-二硫化钼。
试验样品以及未添加固体添加剂的空白样品在四球机上摩擦磨损试验考察结果见表1。
由表1可知,添加固体添加剂后,润滑脂样品pB和pD值都得到不同程度的提高,磨斑直径和摩擦因数也有所降低。
其中,添加PTFE的润滑脂样品的pB值最高,具有较好的抗磨性能,但其pD值较小,不适合在高载荷下使用;添加轻质碳酸钙和二硫化钼的润滑脂样品的pD值最高,极压性能相对较强,可在高载荷下对摩擦表面进行很好的保护,但pB值不如添加PTFE的润滑脂。
这可能因为PTFE颗粒随润滑脂一起进入摩擦表面后,在摩擦表面上形成PTFE颗粒与基体材料的复合层,即发生摩擦化学反应生成的金属氟化物,可与润滑脂吸附膜协同作用,有效阻止摩擦表面之间的直接接触,从而抑制摩擦表面的黏着磨损和接触疲劳,减小磨损[4]。
而添加轻质碳酸钙粉末的润滑脂的良好的极压性能主要来自于其方解石晶体结构,方解石晶体能在摩擦表面形成较厚的保护膜,耐承载能力高[5]。
二硫化钼在金属表面的附着力很强,形成的润滑膜不容易破裂,再加之二硫化钼本身的强度高,使润滑脂能承受高负荷[6]。
石墨对金属的附着力有限,因而其极压抗磨性不及二硫化钼[6],另外也可能与其加入量偏小有关,石墨一般在较高的加入量(如质量分数在10%以上)下才会表现出较高的极压性能。
图1示出了测量磨斑直径时前40 min的摩擦因数曲线。
由表1和图1可得出,虽然添加不同固体添加剂的润滑脂样品的pB和pD值有很大不同,但是磨斑直径和摩擦因数差别很小,这表明上述微米粒径级别的固体添加剂,在低载荷下所表现出的抗磨减摩性能基本相同。
摩擦因数的变化也是材料磨损机制和过程的反应。
由图1还可以看出,在摩擦开始时,各样品的摩擦因数都偏大,随后下降并趋于平稳,这可能是由于摩擦初期固体添加剂需要与摩擦表面发生磨合,并逐渐沉积,加上含磷抗磨剂在摩擦表面形成的磷化铁反应膜等多种因素的相互作用,增大了摩擦阻力;随着磨合的进行,各种因素之间作用达到平衡,摩擦表面建立起稳定的摩擦磨损状态,因而摩擦因数降低且趋于平稳。
2.2 固体添加剂复配对复合锂基脂性能的影响根据前文结论,将抗磨性能较好的PTFE分别同极压性能优异的轻质碳酸钙和二硫化钼等比例复配,以及将3种固体添加剂同时复配,以充分利用各固体添加剂性能优势。
制备的润滑脂样品的摩擦磨损试验考察结果见表2。
由表2可以看到,PTFE和二硫化钼复配效果最好,成功地将PTFE优异的抗磨性和二硫化钼超强的极压性能结合在一起;轻质碳酸钙和PTFE复配后,虽然轻质碳酸钙加入量没变,但样品pD值偏低,没有表现出预期极压性能;3种固体添加剂复配时,润滑脂极压性能较高,但pB值较其他复配润滑脂有下降趋势。
在PTFE和轻质碳酸钙组合中,可能方解石晶型碳酸钙在摩擦表面形成的保护层受到了PTFE金属氟化物摩擦反应层的影响,抗重载荷能力下降,pD值降低。
二硫化钼为切变分层晶体结构,即每个分子层的硫原子与钼原子之间的结合力很强,但分子之间的硫原子与钼原子之间的结合力很弱,因而产生了一个低剪切力的平面,当分子之间受到外来物质或外来力影响时,沿分子层很容易断裂,而形成滑移面,滑移面使原来相对滑移的两金属表面的直接接触转化为二硫化钼分子层的相对滑移,从而减少了摩擦与磨损[7],所以含有二硫化钼的复配样品pD值都较高,极压性能优异。
由表2还可看到,虽然复配后固体添加剂总量增加一倍,但是各样品的磨斑直径和摩擦因数并没有降低,且3种固体添加剂复配的样品中,摩擦因数还出现了增大趋势。
这可能因为在测量磨斑直径时载荷较低,固体添加剂主要以物理吸附沉积在磨损的凹处或摩擦表面的结构缺陷上,形成润滑保护膜,但摩擦表面积有限,再加上复配固体粉末的粒径大小相似,在润滑层中会存在吸附竞争和吸附干扰,因此减摩效果没有随着固体添加剂总量的增加而改善,尤其是在3种固体添加剂同时存在时,吸附干扰更加明显,不容易形成稳定的物理吸附膜,摩擦因数增加。
由图2可以看到,PTFE和二硫化钼虽然复配效果最好,但其摩擦曲线存在较大的波动幅度,说明摩擦过程中存在着不稳定因素,需进一步优化改进。
2.3 不同摩擦改进剂对润滑脂性能的影响摩擦改进剂一般都含有极性基团,可以强有力地吸附在金属表面形成定向吸附膜,防止金属之间接触,从而减小摩擦。
这种膜通常只能在中常温、中低速、中低负荷的情况下保持边界润滑,在高压、高温、高速情况下,吸附膜脱附,油性失效,因而摩擦改进剂主要是降低摩擦因数、减少摩擦阻力,但对润滑脂的极压性能作用甚微。