渣孔&气孔
压铸件渣孔和气孔的分析和对策

3、形成原因
★铝水在熔炼过程中加入的熔剂和形成的熔渣被混入。 ★铝水在浇注之前的二次氧化,例如铝水在输送、飞溅、 使硅、铁、锰等二次氧化,产生的氧化物一起上浮到 铸件上表面或滞留在铸件内的死角和型芯下表面等处。 ★铝水由于除气不良,含有大量气体(H2),压注后在铸 件内形成渣孔。
★合金化学成分中各元素(Si、Cu、Fe、Zn、My、Mn 等) 之间或这些元素之间发生化学反应,铝水及其氧化物 与涂料之间发生界面反应。 ★压铸工艺不合理。
4、防止方法
★熔炼时,炉料要干燥、清洁,加强脱气、除渣,净化 铝水,提高铝水的出炉温度和处理温度。 ★运送铝水的吊包要干燥、清洁。铝水在浇包内应静置 一段时间以利于渣上浮和清除。 ★给汤时应充满料勺,防止铝水在料勺中温度下降过大。
★浇注系统不合理,充型(快速压射)速度过快,金属型 排气不良,使金属液在浇注和充型过程中产生紊流、涡 流或断流而卷入气体,在铸件中形成卷入气孔。
★料筒填充(慢速压射)速度太高,铝水在导入内浇口之
前已卷入气体,在铸件中形成卷入气孔。 ★铝水易吸气,在熔炼和浇注过程中未采取有效的精炼、 保护和净化措施,使金属液中含有大量夹渣、气体和产 气成分,在充型和凝固过程中形成析出气孔和反应气孔。 ★涂料成分不当,与金属液发生界面反应,形成表面针孔 和皮下气孔。
★浇注温度过低,模型的温度过低,金属液除渣不良,粘度 过高,使在压注充型过程中卷入的气体及由金属液中析出 的气体来不及排出铸型或集渣包或排气槽中去。 ★合金在气候潮湿季节熔炼易吸气,合金液大量吸气,造成 铸件成批报废。 ★冲头润滑剂的加入量过多,含油量过高,与金属液发生反 应,形成析出气孔和反应气孔。 ★型腔表面局部有油(如插芯油缸漏油造成的),在压铸时 产生高温气化,形成表面气孔或凹陷。
消失模铸件常见缺陷发生原因

消失模铸件常见缺陷发生原因(造型浇注)一:渣孔1:浇口杯强度不合格2:浇口杯内壁未清理干净3:浇口杯与直浇道对接时浇口杯内耐火胶泥未处理干净4:浇口杯与直浇道对接时没有把掉落在直浇道上的涂料清理干净5:直浇道与横浇道连接处没有把掉落在横浇道上的涂料清理干净6:震实力过大或振动时间过长导致涂料层震裂7:浇注前打渣不到位8:浇注时挡渣不到位9:浇注时压头太高(包嘴距离浇口杯太远)10:浇注温度太高,浇注时间太长(冲刷涂料)二:砂眼1:模型在搬运,埋箱过程中发生磕碰造成涂料层损坏2:震实力过大或振动时间过长导致涂料层震裂3:浇口杯强度不合格4:浇口杯与直浇道连接处、直浇道与横浇道连接处、内浇口与铸件连接处松动,有裂纹或粘接不牢靠5:浇道被掰弯导致涂料层破裂或被掰断6:浇注前浇口杯内部有砂三:变形1:底砂不平2:震实力过大3:振动时间不够或过长4:模型埋箱位置不合理5:负压过大四:冷隔1:负压太小2:浇注温度低,浇注速度慢3:浇注时断流五:粘砂起瘤!:涂料祈面有裂缝2:型砂杂质过多3:底砂不平4:手动填砂不到位5:震实力小或振动时间不够6:负压过大六:气孔1:型砂杂质过多2:负压太小3:浇注速度慢4:浇注时断流5:模型在造型现场摆放时间过长未埋箱造成吸潮6:浇包太凉七:多肉1:用于绑型固定的材料未全部取出2:手动填砂不到位3:砂箱跑火八:缩凹、缩孔1:埋箱时冒口上平面不水平2:埋箱时冒口未放置于最高处3:直浇道与模型距离太近4:浇注温度高5:未按要求放置冷铁九:浇不足1:浇注温度低2:浇注速度慢3:负压太小4:砂箱跑火十:塌箱1:震实力小或振动时间不够2:负压太小3:砂箱排气不畅4:浇注速度慢5:模型在造型现场摆放时间过长未埋箱造成吸潮6:砂箱顶部吃砂量不够7:密封塑料薄膜被烧穿编制:审核:批准:。
铜合金重力铸造常见表面不良分析与对策

y创新性研究铜合金重力铸造常见表面王毅不良分析与对引言长期以来,困扰铜合金重力铸造件表面质量的主要问题有:渣孔、裂纹、硬质点以及气孔等。
而这种缺陷往往要到抛光或电镀工序才能够发现,属于微观缺陷。
前道生产,如成型、机加工序不容易发现,造成较大的报废损失。
本文从铜合金重力铸造件的生产流程入手,分别从原材料检验、生产工艺、设备保养与维护等方面,分析研究品质问题产生的原因和改善措施。
重力铸造生产工艺流程在重力作用下,将熔融的金属液注入铸型而获得所需铸件的工艺方法,即为重力铸造。
一般分为手工浇注、半自动浇注以及全自动浇注。
本文主要以半自动重力铸造工艺为研究对象。
重力铸造工艺流程如图1所示。
图1重力铸造工艺流程重力铸造件常见不良原因分析与改善措施1.硬质点(1)表现形式主要表现为铸件表面抛光后出现孤立或弥散分布的硬质凸点。
在抛光过程中因为硬质颗粒阻挡,经常伴随有尾巴状拉痕存在。
此类不良电镀后愈发明显,导致产品报废。
(2)原因分析对铸件表面硬质点做扫描电镜分析如图2,铸件表面明显可见有硬质凸点缺陷。
图2对铸件表面硬质点扫描电镜分析对铸件表面硬质点进行能谱分析后发现,其 主要成份为O、Al、C、Si、Fe,以及少量Ti、B、S、V、Ca等元素。
新性研究结合重力铸造实际生产工艺及设备特点,做进一步研究分析认为,铸件表面硬质点是以上元素的氧化物,如表1o铸件表面的氧化物与黄铜的物理性质有很大区别,见表1o表1氧化物特性名称密度硬度(莫氏)黄铜&5 3.0AL2O3 4.08.8SiO2 2.67.0SiC 3.29.5Fe2O3 4.9 6.5从表1可见,与铸件基体材料黄铜相比较,AI2O3、S1O2、S1C、Fe2O3、等相关氧化物的密度明显偏低,而硬度非常大。
由于氧化物的硬度比黄铜高很多,在铸件抛光过程中,软的黄铜基体材料首先被抛下,硬的氧化物较难抛平,形成残留凸起的硬质点。
进一步研究分析发现,这些氧化物源自以下途径。
消失模铸件表面孔眼、凹陷和网纹及防止

消失模铸件表面孔眼、凹陷和网纹及防止铸造工业网今天进铸造行业群,加微信:132****1807消失模铸件表面除上述的气孔、皱皮、积碳、亮碳、粘砂等外,也会出现同砂型铸造一样的孔眼(渣孔、砂孔、缩孔)、缩坑(凹陷)等缺陷和特有的网纹和较深的龟纹等缺陷。
(1)产生原因1.渣孔。
液体金属带入熔渣及模样裂解的固相产物不能排出而积存,漂浮在铸件表面,喷丸清理后,铸件表面仍会有渣痕的不规则的孔洞。
2.砂孔。
浇注时,干砂粒进入液体金属中,最后积集到铸件表面,其颗粒状分布,抛丸清理后,砂子未清除掉,则铸件表面形成砂粒镶嵌物,若喷掉砂粒,则表面留下眼孔。
3.缩松、缩孔及缩坑(凹陷)。
铸件与内浇道及冒口连接处的热区,由于补缩不良,形成缩孔、缩松缺陷。
铸件厚大部分由于补缩不足形成缩坑(凹陷),往往出现在最后凝固较大表面上。
4.网纹、龟纹。
模样表面珠粒间融合不良,连接处的凹沟间隙和细小珠粒纹路粗而深的龟纹(严重时形成粒珠状表面)。
细小如网状纹的为网纹,主要是因模样珠粒质量不好、粘接不良,尤其是取用泡沫塑料板(型)材加工成模样时,表面粗糙涂料渗入其间,其表面龟纹、网统复印在涂料层上,浇注后铸件表面也出现这些缺陷。
(2)防止措施1.渣孔防止措施。
金属液熔炼除渣要干净,严格挡渣操作,浇冒口系统设计应便于排渣、集渣,提高浇注温度以便渣浮集,也可选用除渣滓性能较好的浇包及设置过滤网挡渣。
2.砂孔防止措施。
模样组合粘接处必须严密,中空直浇道必须密封好;模样避免在砂箱内组合粘接,浇冒口连接处和模样转角处要圆滑过度(避免角缝而夹干砂)。
3.缩孔、缩松及缩坑(凹陷)防止措施。
提高金属液的浇冒口补缩能力,液流从冒口处经过,保持冒口最后凝固;采用发热、保温冒口;充分利用直浇道补缩(组串铸件);合理的浇冒口系统。
4.网纹、龟纹的防止措施。
改善模样表面质量,选用细小的珠粒;合适的发泡剂含量;改进发泡成型的工艺;模样干燥工艺合理,防止局部急剧过热;对模样表面修饰,在模样表面涂料上光洁材料如塑料、浸挂一层薄薄的石蜡、涂上一层硝酸纤维素涂层等都可以改善模样的表面粗糙度,使浇注出的铸件没有晶粒网状及龟纹。
消失模工艺铸件气孔、渣孔缺陷,是怎么形成的?该如何防止?

消失模工艺铸件气孔、渣孔缺陷,是怎么形成的?该如何防止?本次疫情期间,罗通老师写了一篇关于铸件气孔、渣孔缺陷的文章,洲际铸造平台授权转载!许多消失模铸造厂在生产加工件时特别是碳钢不锈钢件,虽然抛丸后没有什么问题外观也比较理想,可是一加工就出现渣孔气孔,而产生的位置一般在产品的中上部及侧边和浇注系统的对面,夹渣是夹杂缺陷的铁液熔渣和模样残渣。
铸件上二者一般都呈黑色,大小不一,形状很不规则,有块状、片状、线条状等。
一般存在于铸件内部,多见于铸件上表面的皮下和拐角处。
那么泡沫模型气化分解生成大量的气体及残留物不能及时排出铸型,泡沫、涂料层填充干砂的干燥不良,在高温包围下,裂解出大量的氢气和氧气侵入铸件而形成气孔。
产生气孔渣孔的原因一般有以下几种:1,泡沫的水分干燥不透彻就去上涂料,涂料第一遍没干透就去上第二遍,在高温的液体浇注时产生的气孔,2,泡沫的密度过于太大使浇注时来不及气化而吐食泡沫产生的泡沫渣形成渣孔3,钢水脱氧不良、炉台、炉内、包内除渣不净,熔化铁水时,或多或少要产生熔渣,特别是炉料锈蚀严重或采用铁屑熔炼时,产生大量的金属熔渣。
在浇注时熔渣很容易随着铁水进入型腔,留在铸件内部,凝固后就形成黑色夹渣。
由于夹渣的密度比铁水小,一般要浮在铸件上面,铸件拐角处对熔渣有阻碍作用,熔渣上浮时易产生滞留,所以该部位也多见夹渣缺陷。
镇静时间过短,浇注过程中挡渣不力,浇注工艺不合理造成渣孔。
4,由于浇注系统设计不合理,大件小件混合搭配在一个砂型形成了纵横交错,钢水的充型速度大于泡沫气化退让及气体排出速度,造成充型前沿将气化残留物包夹在钢水中再次气化形成内壁烟黑色的分解气孔。
5,浇注温度低,充型前沿钢水不能使泡沫充分气化,未分解的残余物质来不及浮集到冒口而凝固在铸件中形成气孔。
5、内浇道开设位置不合理,充型时形成死角区,由于型腔内气体压力作用,使气化残留物积聚在死角处形成气孔,内浇道截面积过大,而且少使充型速度大于泡沫气化退让速度,吞食泡沫,在合金内部分解气化,而气体无法排出形成气孔。
六种铸件常见缺陷的产生原因及防止方法
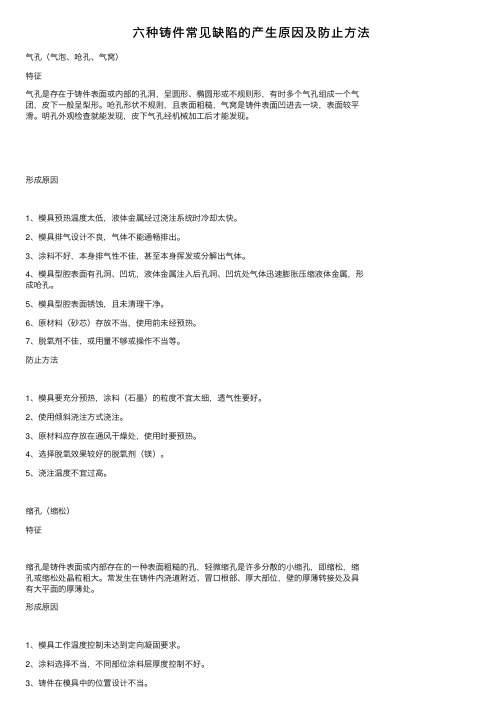
六种铸件常见缺陷的产⽣原因及防⽌⽅法⽓孔(⽓泡、呛孔、⽓窝)特征⽓孔是存在于铸件表⾯或内部的孔洞,呈圆形、椭圆形或不规则形,有时多个⽓孔组成⼀个⽓团,⽪下⼀般呈梨形。
呛孔形状不规则,且表⾯粗糙,⽓窝是铸件表⾯凹进去⼀块,表⾯较平滑。
明孔外观检查就能发现,⽪下⽓孔经机械加⼯后才能发现。
形成原因1、模具预热温度太低,液体⾦属经过浇注系统时冷却太快。
2、模具排⽓设计不良,⽓体不能通畅排出。
3、涂料不好,本⾝排⽓性不佳,甚⾄本⾝挥发或分解出⽓体。
4、模具型腔表⾯有孔洞、凹坑,液体⾦属注⼊后孔洞、凹坑处⽓体迅速膨胀压缩液体⾦属,形成呛孔。
5、模具型腔表⾯锈蚀,且未清理⼲净。
6、原材料(砂芯)存放不当,使⽤前未经预热。
7、脱氧剂不佳,或⽤量不够或操作不当等。
防⽌⽅法1、模具要充分预热,涂料(⽯墨)的粒度不宜太细,透⽓性要好。
2、使⽤倾斜浇注⽅式浇注。
3、原材料应存放在通风⼲燥处,使⽤时要预热。
4、选择脱氧效果较好的脱氧剂(镁)。
5、浇注温度不宜过⾼。
缩孔(缩松)特征缩孔是铸件表⾯或内部存在的⼀种表⾯粗糙的孔,轻微缩孔是许多分散的⼩缩孔,即缩松,缩孔或缩松处晶粒粗⼤。
常发⽣在铸件内浇道附近、冒⼝根部、厚⼤部位,壁的厚薄转接处及具有⼤平⾯的厚薄处。
形成原因1、模具⼯作温度控制未达到定向凝固要求。
2、涂料选择不当,不同部位涂料层厚度控制不好。
3、铸件在模具中的位置设计不当。
4、浇冒⼝设计未能达到起充分补缩的作⽤。
5、浇注温度过低或过⾼。
防⽌⽅法1、提⾼磨具温度。
2、调整涂料层厚度,涂料喷洒要均匀,涂料脱落⽽补涂时不可形成局部涂料堆积现象。
3、对模具进⾏局部加热或⽤绝热材料局部保温。
4、热节处镶铜块,对局部进⾏激冷。
5、模具上设计散热⽚,或通过⽔等加速局部地区冷却速度,或在模具外喷⽔,喷雾。
6、⽤可拆缷激冷块,轮流安放在型腔内,避免连续⽣产时激冷块本⾝冷却不充分。
7、模具冒⼝上设计加压装置。
8、浇注系统设计要准确,选择适宜的浇注温度。
铸件“渣眼”缺陷分析及其应对措施

铸件“渣眼”缺陷分析及其应对措施浇注的时候,熔渣随液体金属进入型腔,形成了铸件的“渣眼”缺陷。
在铸造生产中,有很多铸件(如图1)都是因为出现“渣眼”而报废的,尤其是在一些要求较高的机床液压件的生产上。
铸件出现渣眼的原因很多,有熔炼、浇注操作、造型工艺方面的原因,也有浇注系统设置方面的因素等。
下文分析一下原因以及应对措施。
1.熔炼过程中除渣措施铸铁在熔炼过程会有许多渣子产生,人们总希望在铁液进入浇包之前能彻底地实现渣、铁分离。
一方面,渣子进入浇包也就增加了被冲入型腔的危险,另一方面在浇包中进行扒渣操作会降低铁液的温度,因此铸铁熔炼过程中的放渣操作就显得特别重要。
在冲天炉内,由焦炭的灰分、砂粒及炉衬剥落耐火材料等熔成黏度很大的熔渣,不易排出。
在熔炼时加入适量的石灰石造渣剂,在炉内遇热分解为CaO后,与炉渣反应生成低熔点的盐类物质即熔渣,这些熔渣会随着铁液一起流到前炉中,由于密度不同,会发生分层,铁液在下,熔渣漂在上部,熔炼一段时间后应及时打开前炉上的出渣孔进行放渣,实现渣、铁分离。
如果造渣剂不足,渣子会变得粘稠,不易流出。
熔炼过程中,应适当提高铁液温度。
铁液温度低,渣子粘稠不易放出;另外,铁液的温度太低,悬浮在金属液中的渣子,要上浮至金属液的上部而遇到的阻力较大,也难去除掉。
2.浇注前及浇注过程的中除渣措施铁液由前炉流入浇包,部分渣子难免会随之而入。
那么浇注前,必须把浇包中的熔渣全部除尽,以免熔渣进入铸型造成渣眼缺陷。
具体地说就是在浇包中进行“扒渣”作业。
进行扒渣操作时,比较有效的办法是首先要在浇包金属液的表面撒集渣剂,使渣子与半熔的集渣剂粘在一起,即可用铁棍挑出或扒出。
常用的集渣剂主要是珍珠岩或火山灰。
珍珠岩是较理想的集渣剂,我国南方一些工厂习惯用稻草灰作集渣剂,稻草灰对金属液有保温作用,但对炉渣的集渣效果较差(对炉渣有轻微的激冷作用)。
北方的某些小厂习惯在浇包内金属液表面撒干砂,干砂虽然对漂浮的熔渣有一定的激冷作用,使渣子开始凝结,但干砂完全不熔,对炉渣的集渣作用甚小。
消失模铸件常见缺陷发生原因(白区)

消失模铸件常见缺陷发生原因(白区)一:渣孔
1:浇注时泡沫燃烧不充分(白模密度超标)
2:涂料脱落,浇注过程中钢铁水冲刷掉涂料(涂料强度不合格或涂料烘干程度不合格
3:浇注系统对接处冲进涂料(直浇道与横浇道连接处,横浇道与内浇口连接处,内浇口与铸件连接处在对接时有间隙或是没有把掉落的涂料清理干净)
二:砂眼
1:涂挂好的模型在组装、搬运过程中发生磕碰造成涂料层损坏
2:浇注系统对接处涂料层有裂缝
直浇道与横浇道连接处
横浇道与内浇口连接处
内浇口与铸件连接处
三:变形
1:白模密度(重量)不够,
2:白模自身变形
3:白模在粘接过程尺寸不合格(包括固定用筷子的位置和长短)
4:涂料涂刷不均匀
5:涂挂好的模型放置方式不合理
四:皱皮
1:涂料透气性差
2:白模密度(重量)超标
五:粘砂
1:涂层厚度不够
2:涂料涂刷不均匀
3:涂料表面有裂缝
六:气孔
1:白模密度(重量)超标
2:白模烘干程度不够(烘干室温度不够,湿度超标)
3:涂料烘干程度不够(烘干室温度不够,湿度超标)
4:白模在粘接时用胶过多
七:缺肉
1:白模表面缺肉
2:白模表面有裂纹未用胶带纸粘接导致涂挂时裂纹处进涂料
3:内浇口粘接位置不对导致铸件敲击时带肉
八:缩孔
1:冒口的大小,粘接位置不对
2:浇道与模型距离太近
编制:审核:批准:
铸造部。
- 1、下载文档前请自行甄别文档内容的完整性,平台不提供额外的编辑、内容补充、找答案等附加服务。
- 2、"仅部分预览"的文档,不可在线预览部分如存在完整性等问题,可反馈申请退款(可完整预览的文档不适用该条件!)。
- 3、如文档侵犯您的权益,请联系客服反馈,我们会尽快为您处理(人工客服工作时间:9:00-18:30)。
FUJIWA MACHINERY INDUSTRY (KUNSHAN) CO., LTD.
c、反应气孔:由铁水内部某些成分之间或由铁水型、 反应气孔: 芯在界面上发生化学反应而形成的成 群分部的气孔。 群分部的气孔。位于铸件表层的针头 型或腰圆形反应气孔称为表面气孔或 皮下气孔,由铁水与型、芯涂料发生 皮下气孔,由铁水与型、 界面反应所致; 界面反应所致;分散或成群分布在铸 件整个断面上或某个局部区域的针头 形反应气孔称为针孔, 形反应气孔称为针孔,由铁水内部某 些成分之间发生化学反应所引起。 些成分之间发生化学反应所引起。位 于铸件上部的反应气孔常拌有夹渣。 于铸件上部的反应气孔常拌有夹渣。
FUJIWA MACHINERY INDUSTRY (KUNSHAN) CO., LTD.
6、防止方法
★非铁合金熔炼时,炉料、熔剂、工具、坩埚和浇包要充 非铁合金熔炼时,炉料、熔剂、工具、 分预热和烘干,去锈去油污, 分预热和烘干,去锈去油污,多次重熔炉料的加入量要 适当限制。 适当限制。 ★防止金属液在熔炼过程中过度氧化和吸气,加强脱氧、 防止金属液在熔炼过程中过度氧化和吸气,加强脱氧、 除气和除渣。在坩埚和浇包内的金属熔池表面加覆盖熔 除气和除渣。 剂,防止金属液二次氧化、吸气和有害杂质返回熔池。 防止金属液二次氧化、吸气和有害杂质返回熔池。 对球墨铸铁,应加强脱硫,降低原铁液的含硫量, 对球墨铸铁,应加强脱硫,降低原铁液的含硫量,在保 证球化前提下,尽量减少球化剂加入量, 证球化前提下,尽量减少球化剂加入量,降低铸铁的残 留镁量,并加强孕育处理。 留镁量,并加强孕育处理。
二、渣孔分析对策
1、渣孔的定义及特征
铸件表面或内部由熔渣引起的非金属夹杂物。 铸件表面或内部由熔渣引起的非金属夹杂物。形状不 规则,通常位于铸件上表面或铸件死角处, 规则,通常位于铸件上表面或铸件死角处,在内浇口附 近,内部伴有白色的物体。夹渣经常与气孔、缩孔共 内部伴有白色的物体。夹渣经常与气孔、 生,伴有气孔的夹渣称为渣气孔。 伴有气孔的夹渣称为渣气孔。
FUJIWA MACHINERY INDUSTRY (KUNSHAN) CO., LTD.
★浇注温度过低,金属型温度过低,金属液除渣不良,粘度 浇注温度过低,金属型温度过低,金属液除渣不良, 过高, 过高,使在浇注和充型过程中卷入的气体及由金属液中析 出的气体来不及排出铸型或上浮到冒口或出气口中去。 出的气体来不及排出铸型或上浮到冒口或出气口中去。 ★在气候潮湿季节熔炼易吸气的合金时,合金液大量吸气, 在气候潮湿季节熔炼易吸气的合金时,合金液大量吸气, 造成铸件成批报废。 造成铸件成批报废。 ★树脂砂的树脂和固化剂加入量过多,树脂含氮量过高,原 树脂砂的树脂和固化剂加入量过多,树脂含氮量过高, 砂和再生砂的角形系数过高、粒度过细、 砂和再生砂的角形系数过高、粒度过细、灼减量和微粉含 量过高,使型砂的发气量过高,透气性过低。 量过高,使型砂的发气量过高,透气性过低。
铸件内部的气孔采用超声检验或射线检验, 铸件内部的气孔采用超声检验或射线检验,铸件表层的气 孔采用渗透液。各类气孔的鉴别,除应根据它们的形状、 孔采用渗透液。各类气孔的鉴别,除应根据它们的形状、 大小和分布特征外,有时还须根据它们的形成原因, 大小和分布特征外,有时还须根据它们的形成原因,辅以 测定合金的化学成分及溶解在金属液内的各种气体和杂质 的含量, 的含量,型、芯、涂料的成分、水分和发气性,以及检查 涂料的成分、水分和发气性, 和分析铸型的浇注系统和排气条件,方能确定。必要时, 和分析铸型的浇注系统和排气条件,方能确定。必要时, 还应进行金相、和透射电镜检验,以及X射线分析等, 还应进行金相、和透射电镜检验,以及X射线分析等,才能 准确鉴别气孔的类型和成因。 准确鉴别气孔的类型和成因。
FUJIWA MACHINERY INDUSTRY (KUNSHAN) CO., LTD.
2、气孔的分类
气孔依据形成的原因可以分成四类: 气孔依据形成的原因可以分成四类: 卷入气孔: a、卷入气孔:铁水在充型过程中因卷入气体而在铸 件内形成的气孔, 件内形成的气孔,多呈孤立存在的圆 形或椭圆形大气孔,位置不定, 形或椭圆形大气孔,位置不定,一般 偏在铸件的中上部。 偏在铸件的中上部。 b、侵入气孔:型、芯、涂料、芯撑、冷铁产生的气 侵入气孔: 涂料、芯撑、 体侵入铸件表层而形成的气孔,多呈 侵入铸件表层而形成的气孔, 梨形或椭圆形,尺寸较大, 梨形或椭圆形,尺寸较大,孔壁光滑 ,表面多呈氧化色。 表面多呈氧化色。
FUJIWA MACHINERY INDUSTRY (KUNSHAN) CO., LTD.
★浇注系统不合理,浇注和充型速度过快,金属型排气不 浇注系统不合理,浇注和充型速度过快, 良,使金属液在浇注和充型过程中产生紊流、涡流或断 使金属液在浇注和充型过程中产生紊流、 流而卷入气体,在铸件中形成卷入气孔。 流而卷入气体,在铸件中形成卷入气孔。 ★合金液易吸气,在熔炼和浇注过程中未采取有效的精炼、 合金液易吸气,在熔炼和浇注过程中未采取有效的精炼、 保护和净化措施,使金属液中含有大量夹渣、气体和产 保护和净化措施,使金属液中含有大量夹渣、 气成分,在充型和凝固过程中形成析出气孔和反应气孔。 气成分,在充型和凝固过程中形成析出气孔和反应气孔。 ★型砂、芯砂和涂料成分不当,与金属液发生界面反应, 型砂、芯砂和涂料成分不当,与金属液发生界面反应, 形成表面针孔和皮下气孔。 形成表面针孔和皮下气孔。
FUJIWA MACHINERY INDUSTRY (KUNSHAN) CO., LTD.
2、检验与鉴别
铸件表面的夹渣用肉眼即可发现;铸件内部的的夹渣、 铸件表面的夹渣用肉眼即可发现;铸件内部的的夹渣、 渣气孔一般用射线检验, 渣气孔一般用射线检验,有时暴露在经机械加工后的 铸件表面上,铸件清理后,表面夹渣可能会脱落, 铸件表面上,铸件清理后,表面夹渣可能会脱落,在 铸件表面留下形状不规则的孔洞。 铸件表面留下形状不规则的孔洞。在渣气孔中经常伴 有无色的SiO 颗粒的非金属夹杂物, 有无色的SiO2 颗粒的非金属夹杂物,切勿将其误判为 砂孔。 砂孔。
富士和机械工业 昆山 昆山)有限公司 富士和机械工业(昆山 有 CO., LTD.
气孔、渣孔分析对策
FUJIWA MACHINERY INDUSTRY (KUNSHAN) CO., LTD.
一、气孔分析对策
1、气孔的定义及特征
FUJIWA MACHINERY INDUSTRY (KUNSHAN) CO., LTD.
★浇注时金属液不得断流,充型速度不宜过高,铸件浇注 浇注时金属液不得断流,充型速度不宜过高, 位置和浇注系统的设置应保证金属液平稳地充满型腔, 位置和浇注系统的设置应保证金属液平稳地充满型腔, 并利于型腔内气体能畅通地排出。 并利于型腔内气体能畅通地排出。 ★砂型铸造时,应保证型和芯排气畅通。砂芯内要开排气 砂型铸造时,应保证型和芯排气畅通。 通道,合型时要填补芯头间隙, 通道,合型时要填补芯头间隙,以免钻人金属液堵塞通 气道;型腔最高处及易窝气的部位应设置出气冒口; 气道;型腔最高处及易窝气的部位应设置出气冒口;大 平面铸件可倾斜浇注.并在型腔最商处设置出气冒口; 平面铸件可倾斜浇注.并在型腔最商处设置出气冒口; 芯撑和冷铁应干燥、无锈、无油污; 芯撑和冷铁应干燥、无锈、无油污;砂型要扎足够多的 出气孔;型砂中不得混人铁豆、煤粒、粘土等杂物, 出气孔;型砂中不得混人铁豆、煤粒、粘土等杂物,并 控制水分及碳质材料的含量,减少粘土含量, 控制水分及碳质材料的含量,减少粘土含量,提高型砂 的透气性;涂料要烘干并不含易发气物质。 的透气性;涂料要烘干并不含易发气物质。
FUJIWA MACHINERY INDUSTRY (KUNSHAN) CO., LTD.
3、形成原因
★铁水在浇注过程中加入的熔剂和形成的熔渣被一起带 入型腔。 入型腔。 ★铁水在浇注过程中二次氧化,例如球墨铸铁在输送、 铁水在浇注过程中二次氧化,例如球墨铸铁在输送、 飞溅、使镁、稀土、 飞溅、使镁、稀土、硅、锰、铁等二次氧化,产生的 铁等二次氧化, 金属氧化物与硫化物、 金属氧化物与硫化物、游离石墨一起上浮到铸件上表 面或滞留在铸件内的死角和砂芯下表面等处。 面或滞留在铸件内的死角和砂芯下表面等处。 ★铸铁由于含硫量过高,锰硫比不当,除渣、除气不良 铸铁由于含硫量过高,锰硫比不当,除渣、 使铁水内含有大量硫化物、二次氧化物和气体, 使铁水内含有大量硫化物、二次氧化物和气体,浇注 后在铸件内形成渣孔。 后在铸件内形成渣孔。
FUJIWA MACHINERY INDUSTRY (KUNSHAN) CO., LTD.
5、形成原因
★由于炉料潮湿、锈蚀、油污,气候潮湿,坩埚、熔炼 由于炉料潮湿、锈蚀、油污,气候潮湿,坩埚、 工具和浇包未烘干,金属液成分不当, 工具和浇包未烘干,金属液成分不当,合金液未精炼 或精炼不足,使金属液中含有大量气体或产气物质, 或精炼不足,使金属液中含有大量气体或产气物质, 导致在铸件中形成析出气孔和反应气孔。 导致在铸件中形成析出气孔和反应气孔。 ★型、芯未充分烘干,透气性差,通气不良,含水分和 芯未充分烘干,透气性差,通气不良, 发气物质过多,涂料未烘干或含发气成分过多,冷铁、 发气物质过多,涂料未烘干或含发气成分过多,冷铁、 芯撑有锈斑、油污或未烘干,或冷凝有水珠, 芯撑有锈斑、油污或未烘干,或冷凝有水珠,金属型 排气不良,在铸件中形成侵入气孔。 排气不良,在铸件中形成侵入气孔。
FUJIWA MACHINERY INDUSTRY (KUNSHAN) CO., LTD.
d、析出气孔:熔解在铁水中的气体在铸件成形过程 析出气孔: 中析出而形成的气孔。 中析出而形成的气孔。多呈细小圆形 、椭圆形或针头形,成群分布在铸件 椭圆形或针头形, 整个断面上或某个局部区域内, 整个断面上或某个局部区域内,孔壁 光亮。 光亮。
FUJIWA MACHINERY INDUSTRY (KUNSHAN) CO., LTD.
3、气孔的图片