F(H)级低压绕组真空压力浸漆工艺守则
直流电动机绕组浸漆、烘干处理步骤

直流电动机绕组浸漆、烘干处理步骤直流电动机的浸漆处理,包括电枢绕组、励磁绕组、换向极绕组等的浸漆处理,以及其他绝缘零件的表面浸漆处理、热固性合成树脂的浇注、换向器两端面的绝缘涂封、电枢及定子有关部位的表面喷涂覆盖漆等。
在浸漆、烘干过程中,必须将电枢直立起来,使换向器端在上。
注意切勿让浸漆进入换向器内。
B、F级无溶剂漆沉浸法浸漆工艺见表1,H级硅有机漆沉浸法浸漆工艺见表2。
直流电动机的烘干处理与异步电动机的相同。
表1 B、F级无溶剂漆沉浸法浸漆工艺一例序号工序名称工艺参数B级环氧聚酯酚醛无溶剂漆F级不饱和聚酯无溶剂漆温度(℃)时间(h)热态绝缘电阻(MΩ)温度(℃)时间(h) 热态绝缘电阻(MΩ)1 预烘130 6> 201306>502第一次浸漆烘干浸漆滴漆烘干50~60室温1400.5>110 - -8 50~60室温1500.5>16 - ->103第二次浸漆烘干浸漆滴漆烘干50~60室温1403 min0.5 12 - ->2* 50~60室温1503 min0.510 - ->5注:*第二次浸漆烘干时,绕组热态绝缘电阻需连续3h稳定在同一数值,才能结束烘干。
表2 H级1053有机硅漆沉浸法浸漆工艺一例序号工序名称工艺参数温度(℃) 时间(h)热态绝缘电阻(MΩ)1 预烘1306 >502第一次浸漆烘干浸漆滴漆烘干50~60室温1301800.5>0.546---3第二次浸漆烘干浸漆滴漆烘干50~60室温1301803min0.546---4第三次浸漆烘干浸漆滴漆烘干50~60室温1301901 min> 20min414~16 - -> 10 * 注:*第三次浸漆干燥时,绕组热态绝缘电阻需连续3h稳定在同一数值,才能结束烘干。
直流电动机。
真空压力浸漆工艺流程
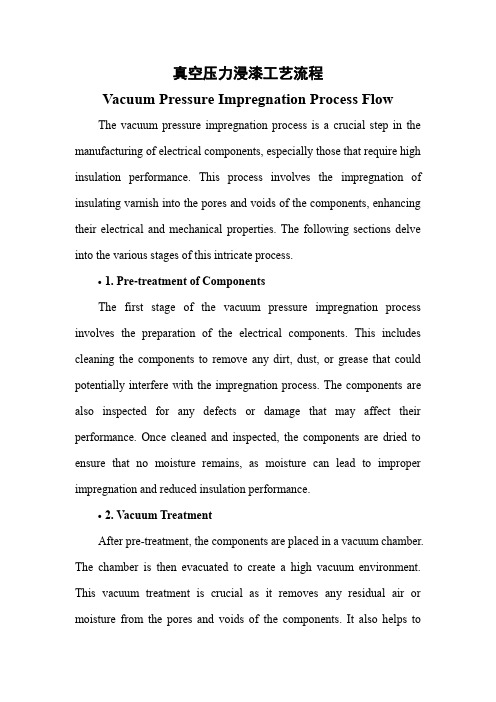
真空压力浸漆工艺流程Vacuum Pressure Impregnation Process FlowThe vacuum pressure impregnation process is a crucial step in the manufacturing of electrical components, especially those that require high insulation performance. This process involves the impregnation of insulating varnish into the pores and voids of the components, enhancing their electrical and mechanical properties. The following sections delve into the various stages of this intricate process.•1. Pre-treatment of ComponentsThe first stage of the vacuum pressure impregnation process involves the preparation of the electrical components. This includes cleaning the components to remove any dirt, dust, or grease that could potentially interfere with the impregnation process. The components are also inspected for any defects or damage that may affect their performance. Once cleaned and inspected, the components are dried to ensure that no moisture remains, as moisture can lead to improper impregnation and reduced insulation performance.•2. Vacuum TreatmentAfter pre-treatment, the components are placed in a vacuum chamber. The chamber is then evacuated to create a high vacuum environment. This vacuum treatment is crucial as it removes any residual air or moisture from the pores and voids of the components. It also helps toexpand the pores, making it easier for the varnish to penetrate and fill them during the impregnation process.•3. Varnish ImpregnationOnce the vacuum chamber has reached the desired vacuum level, the insulating varnish is introduced into the chamber. The varnish is carefully chosen based on the specific requirements of the components, such as their operating temperature, electrical performance, and environmental conditions. The varnish is then drawn into the pores and voids of the components by the vacuum pressure. This process ensures that the varnish penetrates deeply into the components, providing optimal insulation.•4. Pressure ApplicationAfter the varnish has been impregnated into the components, pressure is applied to the chamber. This pressure helps to force the varnish deeper into the pores and voids, ensuring complete impregnation. The pressure is maintained for a specific duration to allow the varnish to fully saturate the components. This step is crucial in achieving uniform and thorough impregnation, which is essential for optimal insulation performance.•5. Post-treatment and DryingOnce the pressure application is complete, the components are removed from the vacuum chamber and undergo post-treatment. Thismay include additional cleaning to remove any excess varnish or residue. The components are then dried to ensure that the varnish is fully cured and hardened. This drying process is typically done in a controlled environment to prevent any damage to the components or adverse effects on the curing process.•6. Quality Control and InspectionAfter the drying process, the components undergo strict quality control and inspection. This involves checking for any defects or imperfections in the impregnation, such as incomplete filling of pores or the presence of air bubbles. The electrical properties of the components are also tested to ensure they meet the required standards. Only components that pass this rigorous quality control are deemed suitable for further use in the manufacturing process.In conclusion, the vacuum pressure impregnation process is a meticulous and crucial step in the production of high-performance electrical components. It involves multiple stages, each designed to ensure optimal impregnation and insulation performance. From pre-treatment to post-treatment, each step contributes to the overall quality and reliability of the final product. By following this comprehensive process, manufacturers can produce electrical components that meet the highest standards of performance and safety.。
F级绝缘浸漆工艺守则

F级绝缘浸漆工艺守则1范围本标准规定了隔爆型三相异步电动机F级绝缘浸漆材料、设备与工具、工艺准备、工艺过程、质量检查和注意事项等内容。
本标准适用于机座63~355隔爆型电机绕组真空浸漆绝缘处理。
2材料2.1 浸漆材料:1140-U型不饱和聚酯无溶剂浸漆树脂(F级)或1140-E型环氧树脂无溶剂浸漆树脂(F级)。
2.2 稀释、清洗材料:苯乙烯(95%)。
3设备与工具3.1 烘房:工作温度范围可控制为50℃~150℃,最大温度不超过±5℃,设备配有强迫循环通风,控制温度及测量工件绝缘电阻的装置。
3.2 浸漆用设施:浸漆罐、贮漆罐、真空泵、调合罐、抽真空脱气保管罐、泵及过滤3.3 浸漆干燥专用工位器具。
3.4 搬运工具:平车、吊车等。
3.5 仪表:温度、测量或记录仪、粘度计(4号杯)、秒表、酒精温度计(0℃~100℃)、500V兆欧表。
3.6 净化绕组绝缘设备:吹风机(或空气压缩机、吸尘器)。
3.7 刮漆工具:铲刀、刮刀等。
4工艺准备4.1 检查所用材料、设备、装置、计量仪和有关器具应符合使用要求。
4.2 检查有绕组定子铁心其绕组端部绝缘不应有损伤和污迹,对引出线破坏、线圈碰伤、露铜、槽楔滑出、绑扎松开等工件应予以修整。
4.3 用吹风机(或空气压缩机、吸尘器)清理工件内、外表面。
4.4 配漆4.4.1 将单组份无溶剂浸渍树脂倒入漆缸,对采用双组份或多组份浸渍树脂应按规定比例将各组份搅拌均匀后再倒入漆缸,或将各组份倒入漆缸用搅拌工具搅拌,并应保证均匀。
4.4.2 测量绝缘漆的粘度:先用温度表测量漆温,然后用粘度计(4号杯)测量漆的粘度(在漆面下约100mm处取样二次,求平均值)并调节到规定的数值做好记录。
查对漆的粘温关系,对应23℃±1℃时;第一次浸漆:20s~35s第二次浸漆:30s~45s15 工艺过程5.1 白坯预烘;5.1.1 将待预烘的工件装上平车,注意每批预烘的有绕组定子铁心其规格应接近,尺寸较大的工件应堆放在干燥条件较好的位置,工件堆放的方位和数量应不防碍烘房内良好通风和温度均匀。
电机维修工艺—电机浸漆及干燥工艺规程

将一次浸漆后的电机,平稳地吊放在平车上,转子一般应竖立放在搁架上干燥,对平放的较大转 子,须将转子滴漆后,翻转 180°安放在支架上。不允许将转子外园直接放在平车上烘焙,以防结疤。 干燥温度和时间要求:
min 110~125℃
以上
10~20
s
145℃±5℃
h
滴漆和擦 4
漆
室2-K s 70~80 5~15
5
漆及干燥 D007 17~28 ℃
min
s
滴漆和擦 6
漆
室温
10~30 min
20~30
第三次浸
s 70~80
7
1032-K
漆及干燥
17~28 ℃
温度
时间
绝缘电阻
1
中小型电机水清洗干燥
120±5Ω
20~40h
5MΩ以上
2
大型电机水清洗干燥
120±5℃
32~48h
5MΩ以上
3
沥青浸胶线圈电机清洗干燥
95±5℃
24~40h
5MΩ以上
全粉云母线圈高压电机热固化处理干
4
120±5℃
燥
16~20h
5MΩ以上
5
大型电机转子无纬带端箍固化干燥
130±5℃
16~28h
D007
s
5~10 min
110~125℃ 145℃±5℃
7定子绕组真空浸漆干燥绝缘处理(VPI)工艺守则

定子绕组真空浸漆干燥绝缘处理(VPI)工艺守则1.适用范围本工艺守则适用于中、小型高低压,Y系列电机及其派生电机,定子绕组采用无溶剂浸渍漆真空干燥浸漆的绝缘处理。
2.材料准备:JF-9950-1高压电机真空压力无溶剂浸渍漆;无溶剂高压真空浸渍漆专用稀释剂、清洗剂、硅脂。
3.设备及工量具准备:真空浸漆罐、AHJ节能型高安全浸漆干燥箱、涂-4粘度计、秒表、时钟、行车、吊具、吊架、绕组铁芯搁架等。
4.工艺准备4.1工件上架4.1.1检查定子绕组、绕组绝缘、绕组引出线不应有磕碰、损伤和污染,线圈端部绑扎绳无松散和断裂,槽楔无松动、漏放,工件内外圆干净无铁屑、异物等,否则必须将工件修复、清理干净。
工件内外表面用压缩空气吹净。
4.1.2内压装定子的绕组引出线、机座的两端止口、螺孔、底脚平面必须均匀涂刷硅脂。
定子放置于八角架上,如果绕组端部高出机座端面,必须放置垫块保护绕组端部。
吊运过程中,定子绕组不允许有磕碰、变形,吊攀拧入机座端面螺孔前应涂抹硅脂。
4.1.3外压装绕组铁芯引出线涂刷硅脂,绕组铁芯非出线套入相应规格的铁芯搁架,并将绕组铁芯立放。
根据立放的高度,吊入到相应的八角架内。
吊钩外表面必须备有防护护套,在吊运及吊装过程中,绕组端部不允许有磕碰、变形及机械损伤。
4.1.4工件上架时,必须注意规格相近或立放高度相近的工件放置在用一个八角架内。
工件高度必须低于八角架上端水平面。
4.2吊架入罐4.2.1工件上架后,八角架吊入真空浸漆罐内,吊架在罐内叠放总高度应低于1800mm,使用专用四脚吊钩起吊架子。
八角架缺口或架子端面长边中心对准真空浸漆罐内进气管。
4.2.2吊架进罐位置放置:工件铁芯长度较长和工件外径较大的应放置在中、上层,最上层工件最高点必须低于出风口位置250mm.4.2.3吊架进罐时必须作如下记录:浸漆工件规格、数量、日期、班次、时间等项目,操作者必须签字。
4.2.4检查真空浸漆罐端面密封圈应全部嵌入密封槽,行车吊放罐盖于真空浸漆罐上,用专用紧定工具将真空浸漆罐和罐盖间密封压紧。
16.7F绝缘真空浸漆工艺守则
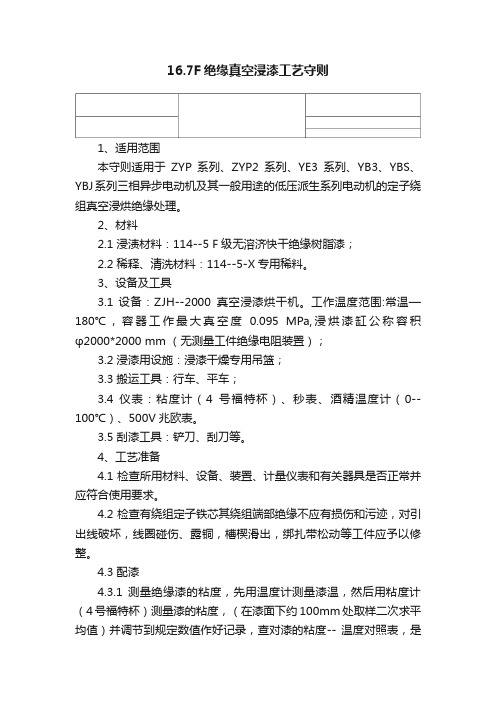
16.7F绝缘真空浸漆工艺守则1、适用范围本守则适用于ZYP系列、ZYP2系列、YE3系列、YB3、YBS、YBJ系列三相异步电动机及其一般用途的低压派生系列电动机的定子绕组真空浸烘绝缘处理。
2、材料2.1 浸渍材料:114--5 F级无溶济快干绝缘树脂漆;2.2 稀释、清洗材料:114--5-X专用稀料。
3、设备及工具3.1 设备:ZJH--2000真空浸漆烘干机。
工作温度范围:常温—180℃,容器工作最大真空度0.095 MPa,浸烘漆缸公称容积φ2000*2000 mm (无测量工件绝缘电阻装置);3.2 浸漆用设施:浸漆干燥专用吊篮;3.3 搬运工具:行车、平车;3.4 仪表:粘度计(4号福特杯)、秒表、酒精温度计(0--100℃)、500V兆欧表。
3.5 刮漆工具:铲刀、刮刀等。
4、工艺准备4.1 检查所用材料、设备、装置、计量仪表和有关器具是否正常并应符合使用要求。
4.2 检查有绕组定子铁芯其绕组端部绝缘不应有损伤和污迹,对引出线破坏,线圈碰伤、露铜,槽楔滑出,绑扎带松动等工件应予以修整。
4.3 配漆4.3.1 测量绝缘漆的粘度,先用温度计测量漆温,然后用粘度计(4号福特杯)测量漆的粘度,(在漆面下约100mm处取样二次求平均值)并调节到规定数值作好记录,查对漆的粘度-- 温度对照表,是否相符。
5、工艺过程5.1 白坯预烘5.1.1 将待预烘的工件装上吊篮,应注意每批预烘的有绕组定子,其规格应接近。
5.1.2 将装有待烘工件的吊篮分别放入浸烘罐中,将浸烘罐加盖封闭,开始加热预烘去潮,温度达到100℃开始抽真空,真空度达0.095 MPa ,抽真空时间30min 左右,停止加热保温,每隔0.5-1h用500V 兆欧表测量绝缘电阻,直到绝缘电阻升高并连续稳定为止。
绝缘电阻值和预烘时间按表1之规定。
5.2 真空压力浸漆5.2.1 待浸渍罐温度降到40-45℃时,保持最大真空度,将贮存灌中绝缘漆放入浸渍罐中(开启阀门时先小后大,以防漆冲入真空泵),待工件全部浸入漆中(漆面应高出工件表面100mm 左右)。
真空油浸工艺操作规程

真空油浸工艺操作规程本规程规定了真空油浸的工艺参数要求和操作顺序,适用于真空高压浸渍工艺的操作。
1、工艺参数及控制1.1预热窑的温度:自窑头至窑尾的温度依次为T1=50~100℃,T2=150~200℃,T3=250±30℃。
温度调节由引风机W1和排烟机W2的控制闸板来控制。
1.2导热油的温度:进油温度T4=280±20℃,回油温度T5为参考温度。
进油温度过高时可以用高位热油罐中的热油加入循环或打开全部热油循环系统,也可采用降低加热炉内温度的方法进行控制。
1.3罐体温度:浸渍罐内温度T6=180±20℃,当温度过高时可关闭该循环。
熔化罐内温度T7熔化沥青时为220±20℃,非熔化沥青过程为180±20℃,该温度可由关闭该罐三个热油循环来实现。
1.4浸渍最高压力:依浸渍制品要求,可设定范围为0.5~1.5MPa,靠电接点压力表B1设定相应压力来控制。
1.5回油压力:0.5MPa,由电接点压力表B2控制,设定为0.5MPa。
1.6真空度:100Pa,由真空数量仪显示。
1.7保压时间:依浸渍制品要求为0.5~4h。
1.8保真空时间:依浸渍制品要求为5~10分钟。
2、操作规程2.1预热系统:指加热炉、预热窑系统。
2.1.1点窑顺序:预热窑内推入待浸渍制品→打开热油泵使导热油在系统内循环→开引风机W1→开排烟机W2→点火。
2.1.2顶车:当窑尾为空位,并将摆渡车停于窑车位时,分别打开窑头及窑尾窑门,将制品顶入窑内,关闭前后窑门。
2.2导热油系统导热油系统共有七个循环,其中R代表进油,V代表回油。
七个循环分别为:2.2.1 R—V 主循环系统,加热炉与导热油分配器之间的循环。
2.2.2 R1—V1 浸渍罐导热油夹套内的循环。
2.2.3 R2—V2输油管道的导热油循环。
2.2.4 R3—V3回油管道的导热油循环。
2.2.5 R4—V4熔化罐内盘管的导热油循环。
真空浸漆烘干操作规程

真空浸漆烘干操作规程一、工艺准备1、先用棉布蘸酒精将定子外表面擦拭干净。
2、用测量杯把漆从储漆罐内取出,用温度计检测绝缘漆的温度用,4#粘度计检测粘度,粘度误差范围±2s。
对照“漆温度-粘度对照表”要求,加适量稀释剂调整。
3、检查有绕组定子铁芯,其绕组端部绝缘不应有损伤和污迹,对引出线损坏、线圈碰伤、露铜、槽楔滑出、绑扎带松开等工件,应予以修整。
4、用吹风机清理干净定子内、外表面。
二、工艺过程1、预烘:把定子放入浸漆缸内关闭缸盖,打开1号阀门和2号阀门。
启动风机,等风机运行2分钟后在启动电热器。
升温到60-80度后保温30分钟,停止加热。
2、浸漆:等缸内温度降到50度后关闭风机同时关闭1号和2号阀门。
起动真空泵抽缸内真空,待缸内真空度达到-0.08Mpa以下关闭真空泵,打开输漆阀输漆至工件上方至少50mm,关闭进漆阀,真空度-0.08Mpa以下浸漆5分钟后解除真空。
解除真空后,常压浸漆至少5分钟。
3、回漆:起动真空泵抽储漆灌抽真空打开回漆阀门,回漆完成后关闭真空泵。
4、滴干:滴净定子上的余漆,滴漆时间至少在60-90分钟,滴漆完成后将滴下余漆抽回储漆灌。
5、清洗:打开清洗灌阀门,输入稀释剂于浸漆缸底部浸泡5-10分钟,完成浸泡缸底后起动真空泵抽稀释剂储存灌真空,打开清洗阀门将稀释剂抽回稀释剂储存灌内。
抽完稀释剂后关闭真空泵。
6、固化:打开1号和2号阀门,启动风机,等风机运行2分钟后在启动电热器,浸漆缸温度达到140度,保温3.5-4小时。
保温完成后关闭电热器,待缸内温度降到100度以下后,开启缸盖取出定子。
三、注意事项1、每次浸漆前都要进行检查和调整漆的粘度。
2、定子预烘后浸漆时定子温度不能高于45度,否则引起漆的胶凝。
3、烘干过程中,不允许打开炉门。
如停电,温度降低应延长时间,保证烘干。
4、工作场地严禁烟火,保持清洁,配备消防灭火装置。
5、要严格执行工艺参数,并做好过程工艺参数监控记录。
- 1、下载文档前请自行甄别文档内容的完整性,平台不提供额外的编辑、内容补充、找答案等附加服务。
- 2、"仅部分预览"的文档,不可在线预览部分如存在完整性等问题,可反馈申请退款(可完整预览的文档不适用该条件!)。
- 3、如文档侵犯您的权益,请联系客服反馈,我们会尽快为您处理(人工客服工作时间:9:00-18:30)。
在专用平台上滴去余漆,按表1中参数操作。
16.2.9
用棉纱(棉布)蘸专用稀料拧干后,将铁心内、外圆表面、绕线转子轴表面粘附的余漆擦拭干净但决不能触到绕组。
16.2.10
将外设管路拆下,用待浸绝缘漆的专用稀释剂将外设管路内部清洗干净后并安装好。
16.3
16.3.1
16.3.1.1
16.3.1.2
16.3.4
关闭烘箱加热系统,打开炉门开出台车,趁热将每根引接线(电缆线)来回弯曲3-5次(弯曲角度不可超过90°)。在工件温度100℃时, 测量绝缘电阻,抽测1~2台,绝缘电阻不小于表1中的规定值。
16.4
如图纸规定浸两次漆的,第二次浸漆、烘干过程按5.3~6.3.4操作,但应使工件降至室温后进行。
16.5
工件出炉后,在热态下用刮刀将工件表面的余漆除净。
17
17.1
每批工件浸漆、烘干处理过程中应按规定做详细检查、测试并记录。其中出炉后,热态绝缘电阻值不小于参数表中的规定。
17.2
浸漆、烘干后定、转子绕组表面漆膜应均匀一致,手触漆膜应坚韧、不粘手、表面无裂纹、不起皱、导体之间粘结牢固。
17.3
定转子绕组不应有磕碰,引接线不应有粘连损伤;检查铁心内、外圆表面及其它部位余漆是否清理干净。
18.2
储漆罐中浸渍漆不用时应定期循环,1~2天循环一次;在用漆液每半年由车间清理和过滤一次(清理罐底过滤网),由质检员取样送到防研所绝缘室按入厂验收标准进行检验。
18.3
清理余漆时不许用毛刷蘸溶剂清理,不许把绕组表面的浸渍漆清理掉;清理用过的溶剂不许直接倒入浸漆罐中;清理余漆时使用规定的专用溶剂,不得使用其它溶剂。
用吸尘器清理工件。工件内、外表面不应有灰尘、油污、铁屑等。
16
16.1
16.1.1
将装好工件的架子吊起,在罐外离地面1.5m高处停止,用铁锤或铁棒均匀敲击架子底部,使粘连架子上的漆块落下。然后将待浸工件整架吊入浸漆罐内,移动速度控制在0.5m/min以内。摆放整齐后用长钩摘下吊环。
16.1.2
当真空度达到2500Pa~2800Pa时,开始输漆。
14
14.1
真空压力浸漆设备、高安全节能型台车自驱动式干燥箱、防爆吊车、浸漆架、接漆盘、平车、搬运圆桶小车、漆槽、外设输漆管路。
14.2
刮刀、溶剂盆、手电筒、活搬子、长钩、刷子、各种承重量的带钢丝绳的吊钩、软吊索。
14.3
秒表、Bg —4#杯、烧杯〔250ml〕、温度计 〔0~100℃〕、水银温度计〔0~250℃〕、500V兆欧表、1000V兆欧表、2500V兆欧表。
罐内滴漆
18~25
30
常压
无余漆滴下
烘干
155±1
4~10h
当U≤1140V
R≥2.5MΩ
出炉热态绝缘电阻
100
R≥2.5MΩ
16.1.4
按表1中参数操作。
16.1.5
利用罐内压力将漆打回储漆罐,按表1中参数操作。
16.1.6
在罐内滴去余漆,按表1中参数操作。
16.1.7
先排风10min,将罐内挥发气体排除,然后开罐,用长钩将吊环挂在浸漆架的吊钩上,吊出工件。在将浸漆架移至台车或专用平台时,在架子底部垫塑料布随架子移动。
15.2.4
当罐内漆量不足,需要加入新漆时,有两种方法,一是通过外设管路采用抽真空方法将漆桶内的绝缘漆抽入罐中;二是使用专用吊钩将漆桶平吊到浸漆罐的壁沿上,打开桶盖,将绝缘漆直接倒入浸漆罐中。
15.3
定、转子绕组及绝缘不应有损伤和污迹,如引出线破损、线圈碰伤、槽楔滑出及绑扎松脱等应予以修复或更换。
1பைடு நூலகம்.4
15
15.1
15.2
15.2.1
浸漆前,用专用稀释剂或新漆将罐中漆的粘度调整至30s~60s〔23
15.2.2
浸漆前,用专用稀释剂调整待用漆的粘度至30s~40s〔23±1℃ Bg — 4#杯〕,每周一次取样测凝胶时间。准备好漆槽,接好外设管路。
15.2.3
浸漆前,用专用稀释剂或新漆调整待用漆的粘度至50s~70s〔23±1℃ Bg — 4#杯〕,每周一次取样测凝胶时间。
16.2.4
打开外设管路阀门,按表1中规定值利用罐内负压将漆输入罐内糟中,使漆面高出最高层有绕组定子铁心100mm以上。
16.2.5
关闭外设管路阀门后,按表1中参数进行加压操作。
16.2.6
打开外设管路阀门,利用罐内压力将漆打回罐外漆桶内,按表1中参数操作。
16.2.7
先排风10min,将罐内挥发气体排除,然后开罐,用长钩将吊环挂在浸漆槽的吊钩上,吊出工件。在将浸漆槽移至专用平台时,在架子底部垫塑料布随浸漆槽移动。
16.1.3
按表1中规定值利用罐内负压将漆输入,并应使漆面高出最高层有绕组定子铁心100mm以上。
表1
工 序
温度(℃)
时间(min)
真空度(Pa)
压力(Pa)
备 注
抽真空
18~25
2500~2800
输漆
18~25
7300~7600
负压输漆
加压浸漆
18~25
10
300000
保压
回漆
18~25
200000
16.3.1.3
16.3.2
预先将烘箱加热升高到规定的烘焙温度,具体操作过程是:先将台车开出,关好炉门,炉门下方用3240板封好,通电升温至170℃~180℃。随后进行的操作过程要求控制在2min以内:断电、移开密封板、开炉门、进台车、关炉门、设置烘焙温度后通电。预升温过程中,有绕组定子(转子)铁心的装车、清理工作同步进行,在烘箱升高到规定的预升温度时(高安全节能型台车自驱动式干燥箱从室温到110℃,平均每分钟升温为3℃;从110℃到180℃,平均每分钟升温为2℃)。清理工作尽量同时完成(提前或滞后不能超过5min)。
16.3.3
将装有待烘工件的台车推入烘箱,选择尺寸较大的工 件(前 后各一个)接入绝缘电阻测量导线〔三相绕组对铁心〕。关闭炉门,待炉温升到规定的烘焙温度时开始计时,烘焙过程中每隔 1 h 测量并记录炉温及绝缘电阻值,直到附表规定的烘焙时间,且绝缘电阻稳定 2h 以上。烘焙过程中烘箱不得随意打开,如遇停电,其重新干燥时间应从炉温达到规定烘焙温度后,补充烘焙到规定时间(同时按规定测量绝缘电阻)。
18.1.2
JF-9801H6 F级不饱和聚酯浸渍漆的凝胶时间应控制在2~6min(140±2℃, 试管法);H9150 H级不饱和聚酯亚胺无溶剂浸渍树脂的凝胶时间为5~20min(135±1℃,试管法);H9110/35 F级不饱和聚酯亚胺无溶剂浸渍树脂的凝胶时间应控制在8±3min(试管法135±1℃)。当凝胶时间缩短到50%原值时(H9150凝胶时间缩短到5min/135℃以下时),应1~2天检测一次凝胶时间,并检查漆中有无成胶颗粒,如有应用100目铁丝网过滤,并向漆中加入0.1%稳定剂,搅匀后再测凝胶时间,直到恢复到标准规定值。当漆中反复加入稳定剂也不能使凝胶时间恢复规定值,并降至30%原值以下时,则该漆将要发生胶化,此时应立即将漆放到旧包装桶内,移到安全位置,并备有消防冷却器材,以便冷却漆桶。当凝胶时间大于标准规定值时,可加入适量固化剂调整。
F(H)级低压电机绕组真空压力浸漆、烘干工艺守则
11
本工艺守则规定了低压电机绕组进行真空压力浸漆、烘干的操作规范和设备参数的选定,适用于F(H)级低压电机有绕组定子铁心和绕线转子铁心进行真空压力浸漆、烘干的全过程。
12
0EE.629.001 生产过程中零部件存放、转序工艺规程
13
JF-9801H6 F级浸渍树脂、H9110/35F级不饱和聚酯亚胺无溶剂浸渍树脂、H9150H级不饱和聚酯亚胺无溶剂浸渍树脂、稳定剂、固化剂、专用稀释剂、棉纱、揩布、100目以上铁丝网或尼龙网、塑料布、耐油胶皮手套、棉手套、防毒面具、口罩。
18.4
浸漆场所环境温度不低于+18℃,浸漆工地清洁,勿使灰尘、污物飞落到未烘干的工件上。
18.5
浸漆场所应严禁烟火,并备有消防器材,浸漆、烘干过程中及时开动通风设施,排除有毒和易燃气体,使其在空气中的浓度不得超过有关标准规定,其它按安全操作规程;操作者应穿戴劳动保护工作服 ,戴手套,尽量不与溶剂直接接触 。
编 制:校 核:会 签:
标准化:审 定:
发放单位:
工 艺 部:1 质 保 部:2 小 型 车 间:3 产品制造部:1 防 研 所: 1
设 能 部: 1 安 技 科:1 仓 储 部 1
18
18.1
车间使用的浸渍漆每周一次由车间操作者把漆液搅拌均匀,派专人取样送到防研所绝缘室测粘度和凝胶时间。试样取出后应立即送去检验。
18.1.1
JF-9801H6 F级不饱和聚酯浸渍漆的粘度应控制在30s~60s〔23±2℃ Bg — 4#杯〕;H9150 H级不饱和聚酯亚胺无溶剂浸渍树脂的粘度应控制在50s~70s〔23±1℃ Bg — 4#杯〕;H9110/35 F级不饱和聚酯亚胺无溶剂浸渍树脂的粘度应控制在30s~40s〔23±1℃ Bg — 4#杯〕。
16.1.8
用棉纱(棉布)蘸专用稀料并拧干后,将铁心内、外圆表面、绕线转子轴表面粘附的余漆擦拭干净但决不能触到绕组。
16.2
如果需要使用其他牌号的绝缘漆进行VPI浸漆,需要通过外设管路实现。
16.2.1
将外设管路拆下,用待
16.2.2
将装有电机
16.2.3
将与外设管路连接的外部钢管插入待浸绝缘漆桶内,关闭外设管路阀门后开始抽真空。当真空度达到2500Pa~2800Pa时,保持1min。