福特生产系统(ppt35)
合集下载
系统思考(201X版)ppt课件

2、通用系统模型 为了更深入地认识和控制系统,以实体和连接
为基础,学者们提出了各种通用系统模型概念。学 者埃里克·特里斯特等提出的“社会技术系统”就 是一种简单的通用系统模型(如图2-1所示)。
社会技术系统的构成要素包括:
⑴ 输入:绝大多数系统都不是孤立的、自给自足
的,它们都存在或需要来自外部的各种输入(可能 包括能量、信息、物质等),以维持系统的运行;
总之,系统思考可以帮助你做出正确的决策, 以通过最严厉的检验----时间的检验。
二、系统思考的精髓和原理
系统思考也就是要顺应系统的特性,洞悉系统 的结构,从整体上对影响系统行为的各种力量与相 互关系进行思考。系统思考的精髓包括深入思考、 动态思考、全面思考和整.体思考等“四重转变”。
(一)什么是系统 系统一词包括部分组成整体的意思。诸如体系、
的相互关联,看清事物的来
龙去脉和发展
.
2、深入思考:从专注于个别事件到洞悉系统的潜 在结构
系统思考中有一个著名的“冰山模型”(如图 2-2所示),揭示了人们思维的层次。系统思考看 待世界,不是只关注一个个孤立的事件,而是主张 看到事件之间的相互关联与作用模式以及发展趋势, 更进一步地要看清影响和推动该模式与趋势发生的 潜在的“结构”----在这里,“结构”不是指逻辑 架构或组织成员之间的汇报关系,而是表示系统中 的关键影响要素(或称为“变量”)及其之间的相 互联系方式(或称为“连.接”)。
.
前言
系统思考是纵观全局、看清事件背后的结构及 要素之间的互动关系,并主动地“建构”和“解构” 的思维能力。对相同的现象,不同的人有不同的见 解和观点,有人熟视无睹,有人却看到了其中隐藏 的商机和变化的规律。如何在纷繁复杂的事件背后 抽丝拨茧地理出简单的结构,引导我们做出正确的 决定?系统思考正是帮助我们走向成功的睿智的 “慧眼”。
精益管理理念课件

执行、C(Check)检查、A(Action)标准化。 对总结检查的结果进行处理, 成
功的经验加以肯定并适当推广、 标准化;失败的教训加以总结, 未解决的问题放到下一个PDCA
P (改善计划)
A (标准化)
D (改善实施)
循环里。
C (效果验证)
四、PDCA
PDCA是一种解决问题,持续改善的工具和
生产过剩带来的危害
△生产过剩会掩盖生产过程中隐藏着的 急待改善的各种问题和不合理成分。
设计 不良
机械 故障
产品 不良
材料 不良
产 不均
资金 占用大
△生产过剩除了会滞留大量资金、产生多 余的利息支出外,还会引发新的连锁性浪 费:
l 原材料、零部件、电能、气能等过早 消耗;
l 工位器具增加;
l 搬运工、搬运设备增加;
项 目 单件生产方式 大批量生产方式
精益生产方式
产品特点
设备和工 装
作业分工 与作业内
容 对操作工
人 要求 库存水平 制造成本
完全按顾客要求 标准化,品种单一 通用、灵活、便宜 专用、高效、昂贵
粗略、丰富 细致、简单、重复
懂设计制造 有较高操作技能
不需要专业技能
高
高
高
低
品种多样化、系列 化
柔性高、效率高
结束
三、快速转换
快速转换是一种调整技术, 它可以在保证质量及 稳定性的前提下, 明显缩短机器安装及调整的转换 时间。通过快速转换, 可以减少库存量, 降低前置时 间, 提高设备使用效率, 使按计划生产的要求更容易 达到。
四、PDCA
PDCA是一种解决问题,持续改善的工具和
手段,其具体含义为: P(Plan)计划、D(Do)
FPS基础理念培训教材(中文版)
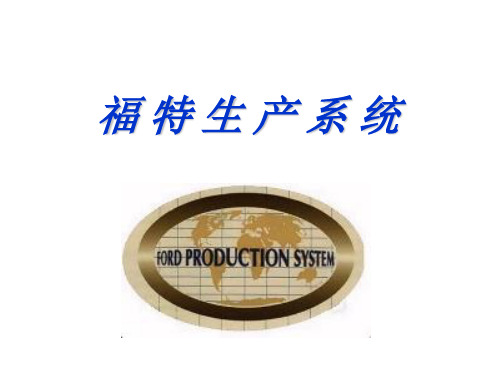
特定FPS 领导人 或协调员
工会领导
江铃指导委员会成员
组长: Bob Bax 副组长: 熊春英 组员: 周亚倬,Peter Corbett,
章海平, 汪清, 杨智勇 协调员: 万春泉
职 位 和 责 任- 指 导 委 员 会
• 制订展望和宗旨 • 定义工作组 • 确定职责关系 • 执行过程 • 制订反馈程序 • 探讨解决工作组遇到的障碍 • 指 导 委 员 会 专 门会 议
FPS = 消 灭 浪 费
浪费的定义
浪费的种种
• 缺陷 • 等候 • 超余生产 • 多余的动作和搬运 • 库存 • 低效率 • 消 除 各 种 浪 费 是 FPS 的 主 要 目 的
缺陷
WASTE 不 能 达 到 产 品 性 能 规 格 的 产 品
等候
因缺少材料、工件、辅助物、设备、上一
WASTE 工序或外协商来的信息等, 造成某工人
and return
工 位 过 程 控 制( 继 续)
目 标: 确 保 工 位 内 的 生 产 质 量 并 消 除 与 不 合 格 物 料 有 关 的 浪 费
管理变更
管理 变更
APQP
DEFINE QUALITY REQUIREMENTS
制定过程 控制
• 反应计划 • 最终的
工艺流程图
质量反馈系统
各 要 素 小 组 由 车 间, 工 会 和 管 理 层 代 表 共 同 组 成 以 帮 助 FPS 的 实 施
要素 小组
工 厂 FPS 指 导 委 员 会
委 员 会 由 工 会 和 公 司 代 表 组 成 并 对 工 厂 FPS 的 实 施 进 行 领 导 和 指 导
实施结构
要素
综合
精益的福特生产体系概述(33页)

断追求完美的境界. • 精益生产是以人为本的制度。要求每个人的投入以杜绝浪费。
2019/5/23
Michelle Gao
7
附加价值的概念
2019/5/23
Michelle Gao
8
7种浪费形式
多余动作 生产过剩 多余的流程
需要時才搬 運過去
搬运 纠错
七大浪费
等待 库存
2019/5/23
Michelle Gao
(最短的前置时间)
2019/5/23
Michelle Gao
13
FPS模式
小齿轮“人”(The People Pinion Gear)
有弹性的、有技能的、目的明确的、充 分授权的人员.
2019/5/23
人
Michelle Gao
SHARP 健康与安全 Environment环境 Leadership 领导 Work Group工作小组 Training 培训
1945
1973
1980
2019/5/23
Michelle Gao
5
2000年丰田汽车公司超越福特成为世界第 二大汽车制造商
FORD TOYOTA
1960
1970
1980
1990
2000
2010
2019/5/23
Michelle Gao
6
精益的概念
精益(Lean )
即消除我们在过程、工作方式、工程、产品制造及 任何增加复杂程度、成本和时间同时对顾客没有附 加价值的不必要的重复和浪费
14
领导要素
方针展开 时间和数据管理 参与、承诺与支持 变更管理 价值流 最佳实务 问题解决与持续改善
2019/5/23
2019/5/23
Michelle Gao
7
附加价值的概念
2019/5/23
Michelle Gao
8
7种浪费形式
多余动作 生产过剩 多余的流程
需要時才搬 運過去
搬运 纠错
七大浪费
等待 库存
2019/5/23
Michelle Gao
(最短的前置时间)
2019/5/23
Michelle Gao
13
FPS模式
小齿轮“人”(The People Pinion Gear)
有弹性的、有技能的、目的明确的、充 分授权的人员.
2019/5/23
人
Michelle Gao
SHARP 健康与安全 Environment环境 Leadership 领导 Work Group工作小组 Training 培训
1945
1973
1980
2019/5/23
Michelle Gao
5
2000年丰田汽车公司超越福特成为世界第 二大汽车制造商
FORD TOYOTA
1960
1970
1980
1990
2000
2010
2019/5/23
Michelle Gao
6
精益的概念
精益(Lean )
即消除我们在过程、工作方式、工程、产品制造及 任何增加复杂程度、成本和时间同时对顾客没有附 加价值的不必要的重复和浪费
14
领导要素
方针展开 时间和数据管理 参与、承诺与支持 变更管理 价值流 最佳实务 问题解决与持续改善
2019/5/23
精益管理知识培训
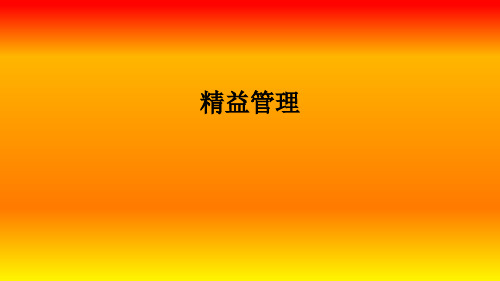
原则二
关注流程,提高总体 效益
创造价值
精益生产 精益起源、发展
精益方法
(1)流水线生产-福特模式
1、精益生产的起源与发展
流水线生产,亨利.福特(Henry Ford)于1913 年在密歇根州的Highland Park,建立的生产 系统。福特-“为世界装上轮子的人”。
亨利福特于1903年创立了福特汽车 公司。1908年生产出世界上第一辆T 型车。当时生产一辆汽车728个人工,当时汽车的年产量大约12辆。
福特的梦想是让自己的员工买得起汽车,汽车成为大众化的交通工具。
1913年,福特应用创新理念和反向思维逻辑提出在汽车组装中,即流水 线生产。第一条流水线使每辆T型汽车的组装时间由原来的12小时28分 钟缩短至10秒钟,生产效率提高了4488倍!
一年之中生产几十万辆汽车,这个新的系统既有效又经济,结果他把 汽车的价格削减了一半,降至每辆260美元,一个工人工作不到四个月 就可以买一辆T型车。
1985年,麻省理工 学院筹措了500万美
元,确定了一个国 家汽车计划(IMVP)
的研究项目,组织 了53名专家学者, 用5年时间对14个国 家近90个汽车装配 厂进行考察分析。
美国麻省理工学院教 授詹姆斯.P.沃麦 克等专家出版《改造 世界的机器》,认为 日本丰田汽车公司的 生产方式是最适用于 现代制造企业的一种 生产组织管理方式。 第一次提出了精益生 产( lean production )。
1985
1992
1996
二战后第一次石油危 机发生,西方经济受 到重大挫折,日本尤 其严重,日本产业陷 入混乱,但是日本政 府发现丰田快速盈利。 与之主办丰田生产制 度研讨会,丰田生产 方式在全日本推广。
精益生产培训讲义(PPT 77页)
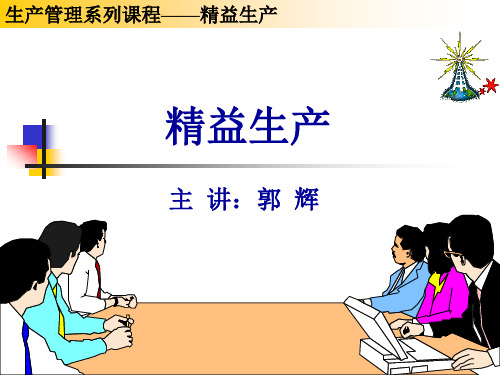
XX钢铁公司
6周预测 每周传真
生管
MRP
90/60/30d 预测
每日订货
精益生产
XX装配厂
周二+周四
每周计划
每日发运 计划
1d1次
5d卷 材
冲压
点焊#1
点焊#2
装配#1
装配#2
发运
4600左 2400右
1100左 600右
1600左 850右
1200左 640右
2700左 平台
1440右
5d 郭 辉 1s
精益生产
清洁
1
2
列队
3
4
5
列队
注塑 1 2 3 4 5
列队
装配 1 2 3 4 5
列队
检查 1 2 3 4 5
该加工车间机器的摆放是依照相同加工功能的原理,这是一个功能区平
面布局图,因此造成它的物料流动的方向是向前向后式,是无序的,存在物 料列队等候的状况。
郭辉
20:15 19
1、库存浪费的解决方法
6
……
郭辉
0 20:16 39
4、标准作业
精益生产
标准作业卡核心控制三个要素: 节拍时间、操作顺序、作业手持。
标准作业卡的目的是作为管理者观察 生产线作业状态的一种管理工具,对于发 现该生产线潜藏的问题点也很有帮助。 另一方面,该车间的监查者通过张贴标准 作业卡,表明了“自己要求工人这样作业” 的强烈意志,因而要对其内容负责。
郭辉
20:15 5
2、精益生产的的诞生
1. 成立于1937年; 2. 1949年陷入经营危机,几近破产; 3. 1957年9月,丰田汽车首次出口美国; 4. 2000年经营利润1万亿日元; 5. 2005年经营利润104亿美元; 6. 2006年成为全球最大的汽车制造商
第十二章准时化生产方式
第三种方法最有柔性。 每一种产品的生产批量为1,每一次只生产1台,
这种投产方法比第二种方法更均衡。当一种产品在 生产时,其他产品的等待生产时间更短。
如果产品A的实际需求在某时期的中后期发生了变 化时,而第三种方法调整的余地就更大。
而JIT这种小批量(甚至是一件)混流作业安排则 可避免由于市场变化带来生产的不均衡和浪费。
第一种方法最缺乏柔性。 当市场需求突发变化,就很难调整,从而造成
某些产品制造过剩,产生库存,而另一些产品失去 市场机会,生产现场忙闲不均。
另外,当第一个产品在生产时,其他的产品要 等待比较长的时间
第二种方法有部分应变能力。 每一产品的生产批量减少为5,三种产品相间地
出产,产品等待时间分配均衡了一些。
为基础,将生产过程中传统的送料制改为取料制,以看板作 为“取货命令”、“运输命令”、“生产指令”进行现场生 产控制。
从生产的最后一道工序(总装线)起,按反工艺顺序, 一步一步,一道工序一道工序向前推进,直到原材料准备部 门,都按看板要求取货、运送和生产。
(二)、实施看板管理的条件
1、必须是以流水作业为基础的作业,不适用于 单件生产。 2、企业生产秩序稳定,有均衡生产基础。 3、设备工装精良,保证加工质量稳定。 4、原材料协作伙伴供应数量、质量有保证。 5、实施标准作业,生产布局和现场平面布置合理。 无此条件,即使引进看板管理制度,也难以实现 准时化。
• 日本汽车公司以丰田汽车公司为代表,50年首先对 美国汽车工业进行了考察和学习,但他们意识到不 能照搬美国的生产方式:
• 一是资金有限(战后); • 二是美国生产方式虽然先进,但仍大有改善的余地; • 三是需要考虑采取一种更能灵活适应市场需求,尽
快提高产品竞争力的生产方式。
这种投产方法比第二种方法更均衡。当一种产品在 生产时,其他产品的等待生产时间更短。
如果产品A的实际需求在某时期的中后期发生了变 化时,而第三种方法调整的余地就更大。
而JIT这种小批量(甚至是一件)混流作业安排则 可避免由于市场变化带来生产的不均衡和浪费。
第一种方法最缺乏柔性。 当市场需求突发变化,就很难调整,从而造成
某些产品制造过剩,产生库存,而另一些产品失去 市场机会,生产现场忙闲不均。
另外,当第一个产品在生产时,其他的产品要 等待比较长的时间
第二种方法有部分应变能力。 每一产品的生产批量减少为5,三种产品相间地
出产,产品等待时间分配均衡了一些。
为基础,将生产过程中传统的送料制改为取料制,以看板作 为“取货命令”、“运输命令”、“生产指令”进行现场生 产控制。
从生产的最后一道工序(总装线)起,按反工艺顺序, 一步一步,一道工序一道工序向前推进,直到原材料准备部 门,都按看板要求取货、运送和生产。
(二)、实施看板管理的条件
1、必须是以流水作业为基础的作业,不适用于 单件生产。 2、企业生产秩序稳定,有均衡生产基础。 3、设备工装精良,保证加工质量稳定。 4、原材料协作伙伴供应数量、质量有保证。 5、实施标准作业,生产布局和现场平面布置合理。 无此条件,即使引进看板管理制度,也难以实现 准时化。
• 日本汽车公司以丰田汽车公司为代表,50年首先对 美国汽车工业进行了考察和学习,但他们意识到不 能照搬美国的生产方式:
• 一是资金有限(战后); • 二是美国生产方式虽然先进,但仍大有改善的余地; • 三是需要考虑采取一种更能灵活适应市场需求,尽
快提高产品竞争力的生产方式。
案例江铃福特供应链改进
目标
作国际汽车界的“刘翔”--有我 有我中国强
部,产品过时,老产品库存积压
22、公司管理层认为产品还在自己的仓库里,卖不
出去也是钱,不考虑仓储积压费用
23、运输部门是下属公司,赢利不赢利没关系,是
否按时送到也不重要,只要把车送出去就可以了
24、质量管理工作仅限于事后把关,以抽样检验的
方式防止缺陷产品流入市场 25、供应商数量较多,良莠不齐
结果
• • •
•
• •
生产成本增加 各部门互相推卸责任,生产效率低 整车和零部件库存积压,资金周转困难 赢利无望 质量不稳定 供应商、员工和客户不满意
请应用供应链管理思想,分析江铃
在与福特汽车合作前存在哪些问题?
这些问题如何在合作后应用JIT思
想进行改进?
诊断与下药
病症一: 病变现象--产需脱节
17.
18、至于销售货款是否收回不关心,认为是财务部门的事 19、市场变化后,销售部门通知生产部门减少产量, 但生
产部门不知道应该减产多少,为什么减产
20. 财务部门因不能收到足够的销车款,因而不能全额支付
零部件供应商,供应商供货因而有时及时,有时供应不 上。同时不清楚到底卖了多少车
21. 市场要求变化的信息没有及时反馈到计划部,产品设计
生产线柔性化(多条生产线(全顺系列商用车、JMC轻卡 系列、匹卡系列、陆风SUV越野车系列),专业化生产)
信息渠道归一化,信息手段现代化Fra bibliotek
不合格的供应商要撤换
非核心业务剥离(运输、仓储、销售、售后均可以外包)
二、内科治疗
药物调理--机制建设
(信息共享机制、协同计划机制、联合库存管理机 制、激励机制(新)、质量保障机制、供应商合 作机制、供应商选择机制、技术集成机制、 ……)
精益生产培训教材
3 Shifts TAKT Time CT = C/O Time = DT = Scrap / Rework = # Operators WIP =
# Material Handlers Max Size 2 Shifts 0 Overtime
分析当前状态 设计将来状态
C/O Time = DT = Scrap = WIP =
课程一: 课程一:
精益生产概论
精益生产的发展历史
福特生产系统 •生产线大量生产 •大批量标准化产品 •工人掌握单一技术 丰田生产系统(TPS) 丰田生产系统(TPS) (TPS •JIT生产(按客户需求品种和数量准时生产) •拉动生产 •强调生产数量和库存数量与市场匹配 •按照客户需求定制产品
精益生产的发展历史
消除浪费的四步骤
第一步: 第一步: 了解什么是浪费 了解什么是浪费
第二步: 第二步: 识别工序中哪里存在浪费 识别工序中哪里存在浪费
第四步: 第四步: 实施持续改进措施 实施持续改进措施, 持续改进措施, 重复实施上述步骤
第三步: 第三步: 使用合适的工具来消除 使用合适的工具来消除 已识别的特定浪费
精益生产既是一种以最大限度地减少企业生产所占用的资 源和降低企业管理和运营成本为主要目标的生产方式,同 源和降低企业管理和运营成本为主要目标的生产方式, 时它又是一种理念,一种文化。实施精益生产就是决心追 时它又是一种理念,一种文化。 求完美的历程,也是追求卓越的过程。 求完美的历程,也是追求卓越的过程。
1985年美国麻省理工学院组织了世界上14个国家的专家、 学者,花费了5年时间,耗资500万美元,对日本等国汽车 工业的生产管理方式进行调查研究后总结出来的生产方式, 在日本称为丰田生产方式。
精益生产教师讲义
-1928年通用公司雪佛兰汽车年产量达到120万 辆
-1896年丰田汽车的创始人丰田佐吉刚刚发明了“丰 田式木制织机” -1930年丰田喜一郎刚刚开始研究开发汽车发动机 -1933年在丰田自动织机制作所设立汽车部 -1936年丰田AA型轿车初次问世 -1937年丰田汽车正式成立,产量只有4000辆
整整落后40年
TPS
Previous Process
Subsequent Process
TPM
Buffer or Store
“Production Pull”
“Withdrawal Pull”
Flow Production in U-Line Total Efficiency
Individual Efficiency Individual Lot Production
起因: •生产计划没有均衡化 •生产换型时间长 •工作场地缺乏组织 •场地规划不合理 •物料计划不合理
七种浪费——物料搬运
七种浪费——动作
定义:对产品不产生价值任何人员和设备的动作 表现: •人找工具 •大量的弯腰,抬头和取物 •设备和物料距离过大引起的走动 •需要花时间确认或辨认 •人或机器“特别忙” 起因: •办公室,生产场地和设备规划不合理 •工作场地没有组织 •人员及设备的配置不合理 •没有考虑人机工程学 •工作方法不统一 •生产批量太大
美国和丰田汽车生产历史比较
美国 -1950年美国工业劳动生产率是日本的8-9倍
丰田 -1950年汽车制造业的差距至少相差10倍
-每年人均生产汽车11.5辆 32年后-1982年
-每年人均生产汽车54.6辆
超常规、革命性的生产方式 -1973年秋爆发了二战后最严重世界性经济危机——第一次石油危机 世界上所有工业国生产力增长都出现了减缓,日本经济出现了零增长 惟有丰田汽车例外,仍然获得了高额利润 丰田公司一定有一种抗拒风险强有力的方法
-1896年丰田汽车的创始人丰田佐吉刚刚发明了“丰 田式木制织机” -1930年丰田喜一郎刚刚开始研究开发汽车发动机 -1933年在丰田自动织机制作所设立汽车部 -1936年丰田AA型轿车初次问世 -1937年丰田汽车正式成立,产量只有4000辆
整整落后40年
TPS
Previous Process
Subsequent Process
TPM
Buffer or Store
“Production Pull”
“Withdrawal Pull”
Flow Production in U-Line Total Efficiency
Individual Efficiency Individual Lot Production
起因: •生产计划没有均衡化 •生产换型时间长 •工作场地缺乏组织 •场地规划不合理 •物料计划不合理
七种浪费——物料搬运
七种浪费——动作
定义:对产品不产生价值任何人员和设备的动作 表现: •人找工具 •大量的弯腰,抬头和取物 •设备和物料距离过大引起的走动 •需要花时间确认或辨认 •人或机器“特别忙” 起因: •办公室,生产场地和设备规划不合理 •工作场地没有组织 •人员及设备的配置不合理 •没有考虑人机工程学 •工作方法不统一 •生产批量太大
美国和丰田汽车生产历史比较
美国 -1950年美国工业劳动生产率是日本的8-9倍
丰田 -1950年汽车制造业的差距至少相差10倍
-每年人均生产汽车11.5辆 32年后-1982年
-每年人均生产汽车54.6辆
超常规、革命性的生产方式 -1973年秋爆发了二战后最严重世界性经济危机——第一次石油危机 世界上所有工业国生产力增长都出现了减缓,日本经济出现了零增长 惟有丰田汽车例外,仍然获得了高额利润 丰田公司一定有一种抗拒风险强有力的方法
- 1、下载文档前请自行甄别文档内容的完整性,平台不提供额外的编辑、内容补充、找答案等附加服务。
- 2、"仅部分预览"的文档,不可在线预览部分如存在完整性等问题,可反馈申请退款(可完整预览的文档不适用该条件!)。
- 3、如文档侵犯您的权益,请联系客服反馈,我们会尽快为您处理(人工客服工作时间:9:00-18:30)。
銷售的稅後盈餘(1954 - 1999)
Mass
Lean Culture8.2% .5%GM5.1%
0
FORD
TOYOTA
3.3%*
1954 1959
* Excl. Visteon
1964
1969
1974
1979
1984
1989
1994
1999
前十名之汽車公司興衰史
市場佔有率
Mass
Lean Culture
Training 2 (訓練 )
In-Station Process Control 3 (站內製程管制 )
Manufacturing Engineering 4 (製造工程 )
From Today and Tomorrow by Henry Ford, 1926
二.福特生產系統之概念
Mass
Lean Culture
•FPS 的願景 •FPS 的經營哲學 •FPS 的精神
何謂福特生產系統(FPS)?
Mass
Lean Culture
福特生產系統(Ford Production System)FPS是一精實(lean)及一致的生產系統, 經由整合後勤供應系統,支持FPS的目標, 促使Ford所有的生產工廠內皆能排除物料 、空間、設備及時間等浪費
Mass
Lean Culture
福特生產系統
Ford Production System
福特汽車九大品牌
Mass
Lean Culture
內容大綱
一. 企業競爭與觀念變革 二. 福特生產系統之概念 三. 精實製造設計之概念 四. FPS系統介紹與展開 五. FPS小組活動 六. FPS小組活動推行績效 七. 結語
精實製造的精神
(Lean Manufacturing)
Mass
Lean Culture
精實製造觀念是消除浪費,來縮短顧客 下訂單到交貨時的時間。
傳統製造
顧客下訂單
浪費
產品交貨
精實製造
顧客下訂單
時間
浪費
時間(縮短)
產品交貨
什麼是附加價值?
•改變作業程序來改 變產品外型,適用性 及功能來滿足客戶要 求
Lean Culture
•它是什麼?
–是一種在價值流(value stream)中藉由排除
浪費以提昇流動性,使其能獲致更短的前置 時間,從而提供高品質、低成本的製造哲學
–由產品開發、程序工程、營運管理及企業總
管理作業等所組成的一整合性系統,其能為 顧客提供價值及帶給人們尊嚴。
•它不是什麼?
–僅是裁減員額數
Mass
Lean Culture
一.企業競爭與觀念變革
Mass
Lean Culture
1. 企業競爭 2. 觀念變革 3. 解決方案 4. 精實製造
競爭
Mass
Lean Culture
The Competition
• 品質 • 生產力 • 成本與利潤 • 市場佔有率 • 企業(公民)形象
全球過剩之產能
Mass
Lean Culture
90
80
70
產 能
60
| 50
百
萬 40
台 30
20
10
0
50 5 45
1985
使用率: 90%
57 10
47
1990
82%
70 17
53
1997
76%
需求 過多的產能
79
83
83
27
27
23
52
56
60
2000
63%
2003
68%
2006
73%
激烈競爭下之利潤壓力
•所做的事客戶都願 意付錢
Mass
Lean Culture
什麼是浪費?
• 生產要素增加但並沒增加價值, 只不過增加成本與時間。
• 所做的事客戶不願意多付錢。 • 問題的表徵多於真正問題的核心
– 如何對浪費的認知與瞭解,以尋找 主要的真因
– 消除浪費,先要承認浪費
Mass
Lean Culture
浪費
GM SAAB Isuzu Suzuki
Technical Agreements
VW Audi Luxury Car Seat Skoda
Toyota Daihatsu
Hino
Mass
Lean Culture
Daimler Chrysler Mitsubishi
Renault
Nissan
變革之原由
Fiat
Nissan
Toyota
Chysler
Nissan
Fiat
Renault
Peugot
British Leyland Mitsubishi
Peugot
Renault
Honda
Mazda
持續整合之傳聞
Ford/ Jaguar / Mazda / Volvo / Land Rover / Think Lincoln / Mercury Austin Martin
Rank
1 2 3 4
5 6 7 8 9 10
1950
1970
1994
GM Ford Chrysler Studebaker
GM Ford Chrysler Volkswagen
GM Ford
Toyota
Volkswagen
Nash Kaiser-Frraze Morris Hudson Austin Renault
Mass
Lean Culture
N eed for Change 需要變革
解決方案
Mass
Lean Culture
The Solution ...
回歸到亨利福特 的起始點 =
亨利福特最初的製造哲學
Mass
Lean Culture
•標準化和持續改善 •消除浪費 •連續性製造流程 •實行源頭品質管理
,使其能
持續性的提供超越顧客在品質、成本及交期上 的期望
大批量生產文化改變為 精實生產系統
Mass
Lean Culture
Top Down
Button Up
三.精實製造基本觀念
•何謂精實製造 •精實製造的精神 •價值的觀念
Mass
Lean Culture
何謂精實製造(Lean Mfg)
Mass
福特生產系統願景(FPS Vision) Mass
Lean Culture
經由一系統性定義的原則及作業方式,使能在生 產及產品交貨過程中:
有效發揮工作小組能力,並授予員工學習及能 安心工作的
一種精實(lean)、有彈性( flexible)及具共 通紀律性(disciplined common) 的生產系統
FPS 十一個單元
FTPM ME
Training
Work Groups
Mass
Lean Culture
ISPC
ISR 3.0
IM
SHARP
Environmental
SMF
FPS系統整合要求之十一單元說明 Mass
Lean Culture
單元
名稱
Ford Total Productive Maintenance 1 (福特全面生產性維護 )
Mass
Lean Culture8.2% .5%GM5.1%
0
FORD
TOYOTA
3.3%*
1954 1959
* Excl. Visteon
1964
1969
1974
1979
1984
1989
1994
1999
前十名之汽車公司興衰史
市場佔有率
Mass
Lean Culture
Training 2 (訓練 )
In-Station Process Control 3 (站內製程管制 )
Manufacturing Engineering 4 (製造工程 )
From Today and Tomorrow by Henry Ford, 1926
二.福特生產系統之概念
Mass
Lean Culture
•FPS 的願景 •FPS 的經營哲學 •FPS 的精神
何謂福特生產系統(FPS)?
Mass
Lean Culture
福特生產系統(Ford Production System)FPS是一精實(lean)及一致的生產系統, 經由整合後勤供應系統,支持FPS的目標, 促使Ford所有的生產工廠內皆能排除物料 、空間、設備及時間等浪費
Mass
Lean Culture
福特生產系統
Ford Production System
福特汽車九大品牌
Mass
Lean Culture
內容大綱
一. 企業競爭與觀念變革 二. 福特生產系統之概念 三. 精實製造設計之概念 四. FPS系統介紹與展開 五. FPS小組活動 六. FPS小組活動推行績效 七. 結語
精實製造的精神
(Lean Manufacturing)
Mass
Lean Culture
精實製造觀念是消除浪費,來縮短顧客 下訂單到交貨時的時間。
傳統製造
顧客下訂單
浪費
產品交貨
精實製造
顧客下訂單
時間
浪費
時間(縮短)
產品交貨
什麼是附加價值?
•改變作業程序來改 變產品外型,適用性 及功能來滿足客戶要 求
Lean Culture
•它是什麼?
–是一種在價值流(value stream)中藉由排除
浪費以提昇流動性,使其能獲致更短的前置 時間,從而提供高品質、低成本的製造哲學
–由產品開發、程序工程、營運管理及企業總
管理作業等所組成的一整合性系統,其能為 顧客提供價值及帶給人們尊嚴。
•它不是什麼?
–僅是裁減員額數
Mass
Lean Culture
一.企業競爭與觀念變革
Mass
Lean Culture
1. 企業競爭 2. 觀念變革 3. 解決方案 4. 精實製造
競爭
Mass
Lean Culture
The Competition
• 品質 • 生產力 • 成本與利潤 • 市場佔有率 • 企業(公民)形象
全球過剩之產能
Mass
Lean Culture
90
80
70
產 能
60
| 50
百
萬 40
台 30
20
10
0
50 5 45
1985
使用率: 90%
57 10
47
1990
82%
70 17
53
1997
76%
需求 過多的產能
79
83
83
27
27
23
52
56
60
2000
63%
2003
68%
2006
73%
激烈競爭下之利潤壓力
•所做的事客戶都願 意付錢
Mass
Lean Culture
什麼是浪費?
• 生產要素增加但並沒增加價值, 只不過增加成本與時間。
• 所做的事客戶不願意多付錢。 • 問題的表徵多於真正問題的核心
– 如何對浪費的認知與瞭解,以尋找 主要的真因
– 消除浪費,先要承認浪費
Mass
Lean Culture
浪費
GM SAAB Isuzu Suzuki
Technical Agreements
VW Audi Luxury Car Seat Skoda
Toyota Daihatsu
Hino
Mass
Lean Culture
Daimler Chrysler Mitsubishi
Renault
Nissan
變革之原由
Fiat
Nissan
Toyota
Chysler
Nissan
Fiat
Renault
Peugot
British Leyland Mitsubishi
Peugot
Renault
Honda
Mazda
持續整合之傳聞
Ford/ Jaguar / Mazda / Volvo / Land Rover / Think Lincoln / Mercury Austin Martin
Rank
1 2 3 4
5 6 7 8 9 10
1950
1970
1994
GM Ford Chrysler Studebaker
GM Ford Chrysler Volkswagen
GM Ford
Toyota
Volkswagen
Nash Kaiser-Frraze Morris Hudson Austin Renault
Mass
Lean Culture
N eed for Change 需要變革
解決方案
Mass
Lean Culture
The Solution ...
回歸到亨利福特 的起始點 =
亨利福特最初的製造哲學
Mass
Lean Culture
•標準化和持續改善 •消除浪費 •連續性製造流程 •實行源頭品質管理
,使其能
持續性的提供超越顧客在品質、成本及交期上 的期望
大批量生產文化改變為 精實生產系統
Mass
Lean Culture
Top Down
Button Up
三.精實製造基本觀念
•何謂精實製造 •精實製造的精神 •價值的觀念
Mass
Lean Culture
何謂精實製造(Lean Mfg)
Mass
福特生產系統願景(FPS Vision) Mass
Lean Culture
經由一系統性定義的原則及作業方式,使能在生 產及產品交貨過程中:
有效發揮工作小組能力,並授予員工學習及能 安心工作的
一種精實(lean)、有彈性( flexible)及具共 通紀律性(disciplined common) 的生產系統
FPS 十一個單元
FTPM ME
Training
Work Groups
Mass
Lean Culture
ISPC
ISR 3.0
IM
SHARP
Environmental
SMF
FPS系統整合要求之十一單元說明 Mass
Lean Culture
單元
名稱
Ford Total Productive Maintenance 1 (福特全面生產性維護 )