不良改善对策
尺寸不良改善方案
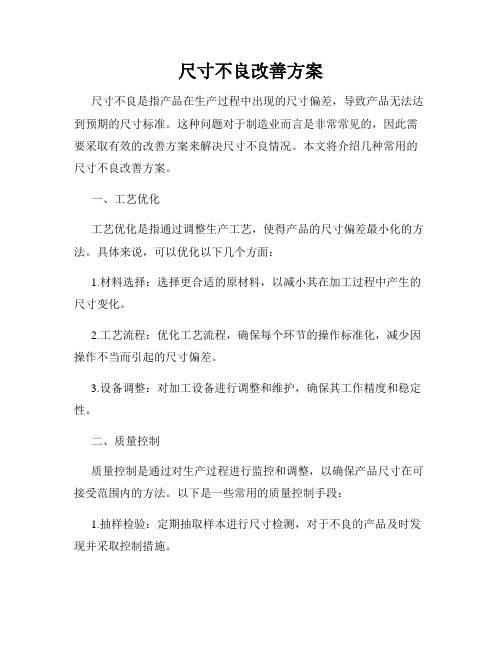
尺寸不良改善方案尺寸不良是指产品在生产过程中出现的尺寸偏差,导致产品无法达到预期的尺寸标准。
这种问题对于制造业而言是非常常见的,因此需要采取有效的改善方案来解决尺寸不良情况。
本文将介绍几种常用的尺寸不良改善方案。
一、工艺优化工艺优化是指通过调整生产工艺,使得产品的尺寸偏差最小化的方法。
具体来说,可以优化以下几个方面:1.材料选择:选择更合适的原材料,以减小其在加工过程中产生的尺寸变化。
2.工艺流程:优化工艺流程,确保每个环节的操作标准化,减少因操作不当而引起的尺寸偏差。
3.设备调整:对加工设备进行调整和维护,确保其工作精度和稳定性。
二、质量控制质量控制是通过对生产过程进行监控和调整,以确保产品尺寸在可接受范围内的方法。
以下是一些常用的质量控制手段:1.抽样检验:定期抽取样本进行尺寸检测,对于不良的产品及时发现并采取控制措施。
2.自动检测:引入自动检测设备,对产品进行实时监测,及时发现尺寸异常。
3.反馈机制:建立尺寸控制的反馈机制,及时调整工艺参数,纠正尺寸偏差。
三、员工培训员工培训是保证产品尺寸良好的关键环节。
通过培训,提高员工的专业知识和技能,确保其对尺寸控制的理解和操作能力。
以下是几个培训方面的建议:1.基础培训:包括产品尺寸标准的解读、尺寸测量方法和仪器的使用等方面的培训。
2.操作规范:制定尺寸控制的操作规范,确保员工在实际操作中能够按照标准进行。
3.技能提升:定期组织技能培训,提高员工对尺寸控制工艺的理解和应用能力。
四、持续改进尺寸控制是一个持续改进的过程,需要不断寻找和解决潜在的尺寸问题。
以下是几个持续改进的建议:1.数据分析:收集和分析生产过程中的数据,找出尺寸不良的根本原因,并采取相应的改进措施。
2.团队合作:建立跨部门的尺寸改进团队,促进各部门之间的合作和信息共享。
3.标准更新:随着技术的不断发展,及时更新产品尺寸标准,确保其与市场需求相符合。
总结:尺寸不良的改善方案包括工艺优化、质量控制、员工培训和持续改进等多个方面。
夹线的不良原因和改善对策
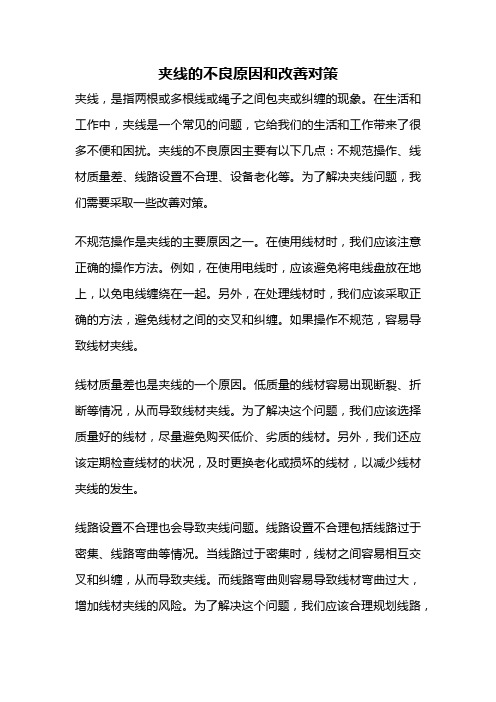
夹线的不良原因和改善对策夹线,是指两根或多根线或绳子之间包夹或纠缠的现象。
在生活和工作中,夹线是一个常见的问题,它给我们的生活和工作带来了很多不便和困扰。
夹线的不良原因主要有以下几点:不规范操作、线材质量差、线路设置不合理、设备老化等。
为了解决夹线问题,我们需要采取一些改善对策。
不规范操作是夹线的主要原因之一。
在使用线材时,我们应该注意正确的操作方法。
例如,在使用电线时,应该避免将电线盘放在地上,以免电线缠绕在一起。
另外,在处理线材时,我们应该采取正确的方法,避免线材之间的交叉和纠缠。
如果操作不规范,容易导致线材夹线。
线材质量差也是夹线的一个原因。
低质量的线材容易出现断裂、折断等情况,从而导致线材夹线。
为了解决这个问题,我们应该选择质量好的线材,尽量避免购买低价、劣质的线材。
另外,我们还应该定期检查线材的状况,及时更换老化或损坏的线材,以减少线材夹线的发生。
线路设置不合理也会导致夹线问题。
线路设置不合理包括线路过于密集、线路弯曲等情况。
当线路过于密集时,线材之间容易相互交叉和纠缠,从而导致夹线。
而线路弯曲则容易导致线材弯曲过大,增加线材夹线的风险。
为了解决这个问题,我们应该合理规划线路,避免线路过于密集和弯曲。
设备老化也是夹线的一个重要原因。
当设备老化时,线材的使用寿命会减少,容易出现断裂、折断等问题。
同时,老化的设备也容易导致线路设置不合理,从而增加线材夹线的风险。
为了解决这个问题,我们应该定期检查和维护设备,及时更换老化的设备,确保设备的正常运行。
针对夹线问题,我们可以采取一些改善对策。
首先,要加强操作规范,提高操作人员的技术水平。
通过培训和学习,提高操作人员的操作技能,减少夹线事故的发生。
其次,要选择质量好的线材和设备,确保线材和设备的使用寿命和质量。
另外,要合理规划线路,避免线路过于密集和弯曲。
最后,要定期检查和维护设备,及时更换老化的设备和线材,确保设备的正常运行。
夹线是一个常见的问题,它给我们的生活和工作带来了很多不便和困扰。
不良品改善报告范文(3篇)

不良品改善报告范文第1篇P:计划(一)制定改善计划20xx年1月P公司派训的L工程师结训回到企业后,立即深入现场进行问题调研,再结合参训前收集的现场管理问题点,然后召集改善工作筹组会议决定IE改善工作小组由工艺部工程师、生产副总、车间主管、品检工程师等8位成员共同组成,并由工艺部L 工程师担任IE改善工作小组组长,制定出每位小组成员的工作职责及IE改善小组的工作计划。
IE改善小组将IE改善工作主题聚焦于车间制程的改善及标准化。
(二)设定改善目标两周后,改善小组就改善主题对P公司的生产流程及产品的现况展开讨论,发现车间生产效率仅有61%,改善小组随即运用SMART原则来进行改善目标设定,并将改善目标设定为:1、从简化生产流程设计上入手,运用作业程序(流程)分析手法来降低产品加工成本,在现有成本基础上降低15%。
2、通过生产线工站重新部置及人员编成,运用IE手法使生产线平衡,并提高装配效率,在现有的基础提升55%。
3、改善时间为五个月(20xx年1月20xx年5月)。
改善目标确定下来,改善小组立即将主题及目标进行分解成小项目,由改善小组成员分别负责各个小项目,进行团队合作。
并定每两周召开一次改善小组会议,共同探讨实现目标的方法。
D:执行(一)执行改善对策20xx年1月下旬改善小组召开二次改善小组会议,共同探讨改善对策。
决议改善初期先设计几组新规格的模具投入生产流程中进行改善对策的尝试。
于20xx年2月上旬模具完成制作及验模后,随即将此模具投入生产流程开始进行小批量试产。
而在其试产过程中,肯定会有各式各样的问题存在,到时改善小组成员需到现场进行跟踪讨论发现的问题及解决问题的方法。
C:检查(一)改善对策执行结果验证20xx年2月中旬改善小组召开第三次改善小组会议,共同对改善对策的初期执行结果进行验证。
发现生产效率提高了,人力需求降低了2/3,表示此改善对策是可行的。
但以仅运用此改善对策的情况来看,要达成改善计划所设定的目标,仍然有许多的问题要解决。
精益生产不良品改善对策

精益生产不良品改善对策引言精益生产(Lean Production)作为一种极具竞争力的生产管理方法,旨在通过最大限度地减少资源浪费,提高生产效率和质量。
然而,不可避免地,生产过程中会出现不良品。
不良品不仅会导致生产效率下降,还会增加生产成本。
因此,实施有效的不良品改善对策对于提升企业竞争力至关重要。
本文将深入探讨精益生产中的不良品问题,并提供一些有效的改善对策,旨在帮助企业更好地应对不良品问题。
1. 不良品产生原因分析在开始制定改善对策之前,首先需要了解不良品产生的原因。
以下是一些常见的不良品产生原因:1.1 设备故障设备故障是不良品产生的主要原因之一。
设备维护不当、老化以及操作不当均可能导致设备故障,进而影响产品质量。
1.2 人为操作错误人为操作错误是不良品产生的另一个重要原因。
员工缺乏必要的培训和技能,操作不规范或疏忽大意都可能导致产品质量不合格。
1.3 原材料质量问题原材料质量问题也是导致不良品问题的常见原因。
原材料的质量不合格、存储方式不当或供应商问题都有可能导致产品质量不达标。
2. 不良品改善对策2.1 设备维护和管理设备维护和管理是减少设备故障的关键。
企业应建立完善的设备维护计划,包括定期检查、保养和清洁设备。
此外,还要加强员工对设备操作的培训,确保操作规范和正确。
2.2 员工培训和教育培训和教育是减少人为操作错误的有效途径。
企业应为员工提供必要的技能培训,使其熟悉操作流程和质量控制标准。
此外,员工还应接受质量意识和责任意识培养,以提高他们对产品质量的重视程度。
2.3 供应链管理供应链管理对于原材料质量的控制至关重要。
企业应与合格的供应商建立稳定的合作关系,并建立严格的原材料入库检查机制。
只有确保原材料的质量合格,才能避免不良品问题。
2.4 改善流程和工艺改善流程和工艺是减少不良品产生的重要手段。
通过优化生产流程,减少不必要的加工步骤和浪费,可以降低不良品的产生率。
同时,建立严格的质量控制标准,及时发现和处理问题,也是实施成功的不良品改善对策的重要环节。
喷漆常见不良现象及改进对策
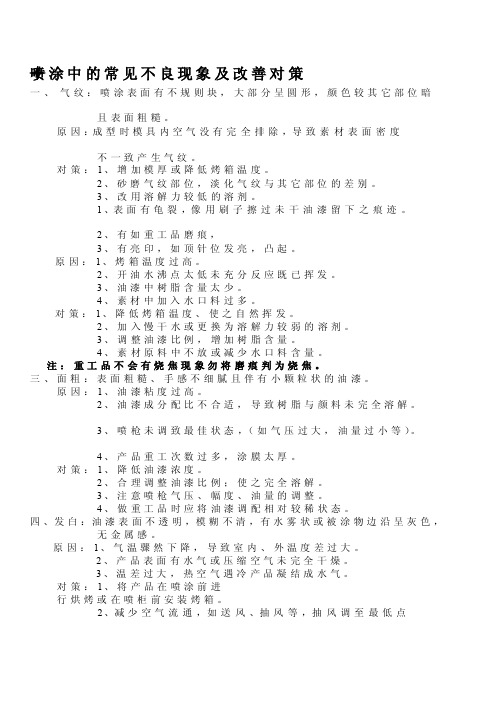
涂中的常见不良现象及改善对策一、气纹:喷涂表面有不规则块,大部分呈圆形,颜色较其它部位暗且表面粗糙。
原因:成型时模具内空气没有完全排除,导致素材表面密度不一致产生气纹。
对策:1、增加模厚或降低烤箱温度。
2、砂磨气纹部位,淡化气纹与其它部位的差别。
3、改用溶解力较低的溶剂。
1、表面有龟裂,像用刷子擦过未干油漆留下之痕迹。
2、有如重工品磨痕,3、有亮印,如顶针位发亮,凸起。
原因:1、烤箱温度过高。
2、开油水沸点太低未充分反应既已挥发。
3、油漆中树脂含量太少。
4、素材中加入水口料过多。
对策:1、降低烤箱温度、使之自然挥发。
2、加入慢干水或更换为溶解力较弱的溶剂。
3、调整油漆比例,增加树脂含量。
4、素材原料中不放或减少水口料含量。
注:重工品不会有烧焦现象勿将磨痕判为烧焦。
三、面粗:表面粗糙、手感不细腻且伴有小颗粒状的油漆。
原因:1、油漆粘度过高。
2、油漆成分配比不合适,导致树脂与颜料未完全溶解。
3、喷枪未调致最佳状态,(如气压过大,油量过小等)。
4、产品重工次数过多,涂膜太厚。
对策:1、降低油漆浓度。
2、合理调整油漆比例;使之完全溶解。
3、注意喷枪气压、幅度、油量的调整。
4、做重工品时应将油漆调配相对较稀状态。
四、发白:油漆表面不透明,模糊不清,有水雾状或被涂物边沿呈灰色,无金属感。
原因:1、气温骤然下降,导致室内、外温度差过大。
2、产品表面有水气或压缩空气未完全干燥。
3、温差过大,热空气遇冷产品凝结成水气。
对策:1、将产品在喷涂前进行烘烤或在喷柜前安装烤箱。
2、减少空气流通,如送风、抽风等,抽风调至最低点且保持相对平衡。
3、提升烤箱温度并将热量散发至生产线周围,减少生产线温差、湿度差。
4、添加防白水(先试验再加,以防影响性能)。
五、面花:被涂物同一表面颜色不均,有亮有暗。
原因:1、油漆喷涂厚薄不均。
2、底漆表面未完全烤干,(如上半部分比下半部分干)就已喷面漆。
3、喷枪雾化气压、距离等未调至最佳状态。
对策:1、调整喷枪至最佳状态。
不良品改善报告范文
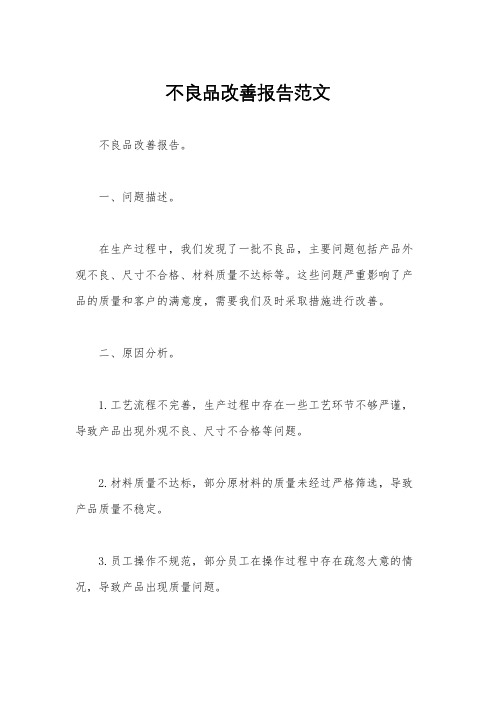
不良品改善报告范文
不良品改善报告。
一、问题描述。
在生产过程中,我们发现了一批不良品,主要问题包括产品外观不良、尺寸不合格、材料质量不达标等。
这些问题严重影响了产品的质量和客户的满意度,需要我们及时采取措施进行改善。
二、原因分析。
1.工艺流程不完善,生产过程中存在一些工艺环节不够严谨,导致产品出现外观不良、尺寸不合格等问题。
2.材料质量不达标,部分原材料的质量未经过严格筛选,导致产品质量不稳定。
3.员工操作不规范,部分员工在操作过程中存在疏忽大意的情况,导致产品出现质量问题。
三、改善措施。
1.完善工艺流程,对生产流程进行全面梳理,优化工艺环节,
加强对关键工艺环节的监控和管理,确保产品质量稳定。
2.严格把关原材料,加强对原材料的质量控制,建立严格的原
材料进货检验制度,确保原材料的质量达标。
3.加强员工培训,对员工进行质量管理方面的培训,提高员工
的质量意识和操作技能,确保产品质量符合标准。
四、改善效果。
经过以上改善措施的实施,我们对产品的质量进行了全面提升,不良品率明显下降,客户投诉情况得到了有效控制,产品质量得到
了客户的认可和好评。
同时,我们也加强了对生产过程的监控和管理,提高了生产效率和产品质量稳定性。
五、总结。
通过此次不良品改善报告,我们深刻认识到了产品质量对企业
发展的重要性,也意识到了要想提高产品质量,必须从源头抓起,
加强对生产过程的管理和控制。
我们将继续加强质量管理,不断改进工艺流程,提高产品质量,为客户提供更优质的产品和服务。
焊接不良改进报告

焊接不良改进报告
焊接不良改善报告
⼀、鱼⾻图分析
⼀、综上鱼⾻图分析,产线焊接不良主要原因如下:
1.作业随意性⼤,⽆责任⼼和质量意识;作业不作⾃检。
2.对焊锡⼯艺⽆接受标准:
3.焊锡作业员未经培训就直接上岗,是否可以胜任本岗位⼯作也监督与考核;
4.焊接⼯序没有对所使⽤的电铬铁、焊接温度进⾏明确(⽬前所⽤的均为普通电铬铁;温度没法控制)
5.作业员没有及时清理铬铁上锡渣;焊接造成连锡。
⼆、改善对策:
1.⽣产管理⼈员对作业进⾏教育培训;提⾼员⼯责任⼼和质量意识;加强对员⼯的培训与监控,⽽不是有问题只是对员⼯说⼀声:“做好⼀点”,要让员⼯养成⾃检互检的习惯。
2.由研发部拟订焊接⼯艺接受标准;与图⽚的形成明⽰可接受、不可接受,并对作业员进⾏培训,让作业掌握标准;
3.研发部对⽣产线作业员进⾏焊锡作业培训;让员⼯熟练掌握焊锡技能;以后新招进的焊锡作业员上岗必须经过培训⽅可上岗;由品质部IPQC负责监控;
4.①⽬前所⽤的均为普通电铬铁;建议公司对⽣产所⽤的电铬铁统⼀更换成恒温铬铁;
②研发部制定作业指导书时需明确该⼯位所使⽤的电铬铁规格及温度控制要求;
③品质部申购铬铁温度测试仪,对焊锡⼯位铬铁温度进⾏管控;
5.①⽣产管理⼈员需对焊接作业进⾏培训和指导;让员⼯养成电铬铁有残留锡渣时须及时清理;并成焊接进⾏⾃检;
②IPQC加强对焊锡⼯位巡检⼒度;每个焊接⼯作需抽检5-10PCS检查焊接效果;
拟定:审核:。
SMT制程不良原因及改善对策

SMT制程不良原因及改善对策SMT制程(Surface Mount Technology)是一种常用的电子组装技术,广泛应用于电子产品的制造过程中。
然而,由于各种原因所引起的不良现象在SMT制程中时有发生。
本文将讨论SMT制程不良原因以及改善对策。
1.焊接不良:焊接不良可以导致焊点虚焊、焊接断裂等问题。
常见的原因包括焊接温度不够、焊接时间不足、焊接设备不稳定等。
改善对策包括提高焊接设备的质量和稳定性、增加焊接温度和时间的控制精度等。
2.贴装不良:贴装不良可以导致元件偏移、元件漏贴等问题。
常见的原因包括贴装位置错误、贴装头磨损、胶垫损坏等。
改善对策包括提高贴装机的精度和稳定性、定期更换贴装头和胶垫等。
3.元件损坏:元件在SMT制程中容易受到机械损伤、电静电等因素的影响而受损。
改善对策包括提供合适的防护措施,如使用防静电设备、增加元件存储和运输的保护等。
4.焊盘不良:焊盘不良可以导致焊点接触不良、导致电路连通性问题。
常见的原因包括锡膏质量不佳、焊盘形状不准确等。
改善对策包括使用高质量的锡膏、提高焊盘生产过程的精度等。
5.引脚弯曲:引脚弯曲会导致元件无法正确插入或连接。
常见的原因包括元件存储和运输过程中引脚受到碰撞、搬运过程中的不当操作等。
改善对策包括提供合适的存储和运输保护措施、培训操作人员正确操作等。
改善SMT制程不良有很多对策,下面列举了其中一些常见的:1.提高设备的质量和稳定性:定期对设备进行维护和保养,确保其正常运行和精度稳定。
采用高质量的设备和工具,可大大降低不良率。
2.优化工艺参数:根据产品要求和设备特性,合理的调整焊接温度、焊接时间等工艺参数,以确保焊接效果和质量。
3.加强员工培训:提供必要的培训和指导,使操作人员熟悉SMT制程的原理和操作技巧,减少人为失误和操作不当导致的不良。
4.严格品质管理:建立完善的品质管理体系,包括设备校验、材料检测、过程控制等环节,确保产品质量稳定。
5.提供合适的存储和运输保护:对元件进行正确的存储和运输保护,避免机械损伤、静电损伤等因素导致的元件损坏。
- 1、下载文档前请自行甄别文档内容的完整性,平台不提供额外的编辑、内容补充、找答案等附加服务。
- 2、"仅部分预览"的文档,不可在线预览部分如存在完整性等问题,可反馈申请退款(可完整预览的文档不适用该条件!)。
- 3、如文档侵犯您的权益,请联系客服反馈,我们会尽快为您处理(人工客服工作时间:9:00-18:30)。
不良内容 不良数
绝缘耐压
1 日程 3.9 部署 RW
不良现象 及 原因分析 □ 不良现象
压接端内有水气, 压接端内有水气,绝缘耐压不良 □ Root Cause
3.对库存数300EA绝缘耐压进行检查,其中5EA浸泡24小 时后再进行耐压测试无不良现象.
作业指导书
1、由于新工人在操作时塑封时间较短,没 4.以后品质人员对每批产品进行抽检,抽检数为5EA/批, 对产品浸泡24小时后进行耐压测试实验. 等导线和套管完全吻合,作业员就翻面操 4. □ 管理性对策 作.导致密封性差,水渗入压接部位.
3.REF
区 发 期 工程不良 3.9 业体名 发生Line 发生Line 荣威 部品名 部品 Code 电加热 DA47-00180A 改善对策 □ 技术性对策
1.塑封时,作业标准时间单面为3秒,而新工人操作时间 单面只有1秒. 2.调整打耐压浸泡时间,由以前的浸泡时间30分钟增至 塑封作业指导书 到1小时后进行打耐压.
1、对操作人员进行培训,培训合格后方可上机操作.
薛雪珍" <xuezhen070404@>"
培训记录
2.加强品质人员质量控制意识,做到不接收不良品,不传 递不良品.
□横 开 及工 : - 类 问题 :