合成氨原料气醇烃化净化精制新工艺
净化-03-合成氨原料气醇烷化净化工艺应用探讨
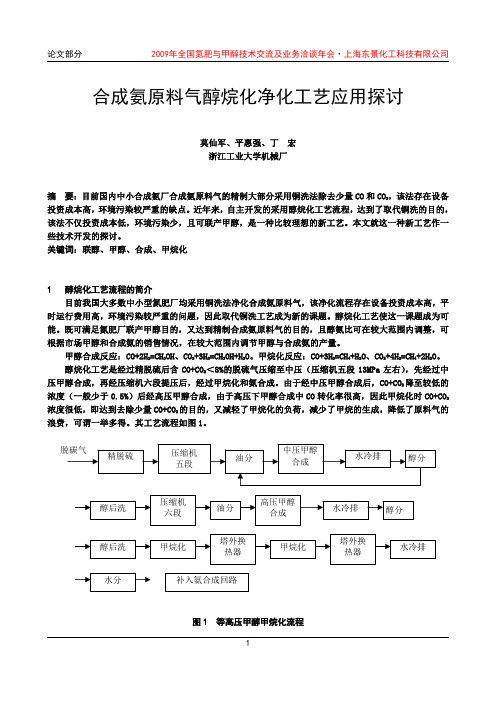
合成氨原料气醇烷化净化工艺应用探讨莫仙军、平惠强、丁 宏 浙江工业大学机械厂摘 要:目前国内中小合成氨厂合成氨原料气的精制大部分采用铜洗法除去少量CO 和CO 2,该法存在设备投资成本高,环境污染较严重的缺点。
近年来,自主开发的采用醇烷化工艺流程,达到了取代铜洗的目的,该法不仅投资成本低,环境污染少,且可联产甲醇,是一种比较理想的新工艺。
本文就这一种新工艺作一些技术开发的探讨。
关键词:联醇、甲醇、合成、甲烷化1 醇烷化工艺流程的简介目前我国大多数中小型氮肥厂均采用铜洗法净化合成氨原料气,该净化流程存在设备投资成本高,平时运行费用高,环境污染较严重的问题,因此取代铜洗工艺成为新的课题。
醇烷化工艺使这一课题成为可能。
既可满足氮肥厂联产甲醇目的,又达到精制合成氨原料气的目的,且醇氨比可在较大范围内调整,可根据市场甲醇和合成氨的销售情况,在较大范围内调节甲醇与合成氨的产量。
甲醇合成反应:CO+2H 2=CH 3OH、CO 2+3H 2=CH 3OH+H 2O。
甲烷化反应:CO+3H 2=CH 4+H 2O、CO 2+4H 2=CH 4+2H 2O。
醇烷化工艺是经过精脱硫后含CO+CO 2<8%的脱硫气压缩至中压(压缩机五段13MPa 左右),先经过中压甲醇合成,再经压缩机六段提压后,经过甲烷化和氨合成。
由于经中压甲醇合成后,CO+CO 2降至较低的浓度(一般少于0.5%)后经高压甲醇合成,由于高压下甲醇合成中CO 转化率很高,因此甲烷化时CO+CO 2浓度很低,即达到去除少量CO+CO 2的目的,又减轻了甲烷化的负荷,减少了甲烷的生成,降低了原料气的浪费,可谓一举多得。
其工艺流程如图1。
图1 等高压甲醇甲烷化流程2 醇烷化工艺的工程设计应用我单位目前该工程设计先后在3万、6万、10万和18万t/a合成氨能力的多家氮肥厂实施。
下面以年产10万t合成氨能力的设计为例进行分析:2.1 主要设备规格合成氨能力总氨为10万t/a,中压联产甲醇2万t,高压副产甲醇5千t。
合成氨精制新技术醇烃化工艺开车技术总结

合成氨精制新技术醇烃化工艺开车技术总结我公司投资建设的由湖南安淳高新技术有限公司设计的120Kt总氨/年醇烃化工艺于2009年12月投入运行,并一次开车成功,取代了物耗高、能耗高有污染的铜洗工艺,装置采用DCS系统控制,现运行正常稳定,经济及环境效益明显,下面将工艺情况介绍如下:1 工艺流程来自氢氮气压缩机五段出口13.5Mpa的净化气进入甲醇油水分离器,除去油污及压缩冷凝水后,少部分气体从大盖顶上引进气体混合分布器Ⅰ和零米冷激分布器;约占入塔总气量30%的气体进入甲醇塔的下部,内外筒环隙,由下而上进入冷束管,冷束管出来的气体进入混合分布器Ⅱ,与出上绝热层的高温气体混合进入第二绝热层反应。
约占总入塔气量70%的气体进塔前预热器,被塔前预热器加热的气体,从甲醇塔的底部进入塔内,进塔气体进入塔内换热器管内,与出塔气体换热后,经中心管进入触媒表面,依次通过上绝热层、第二绝热层、下部绝热层,从下部换热器外壳进入换热器管间,由上折流而下,与入塔气体换热后出塔,进入塔前预热器管内换热,换热后的气体进入水冷器,出水冷器气体进醇分,将生成的甲醇分离下来,送精馏工段精制。
来自醇分离器后的气体从烃化塔的下部进烃化塔的内外筒环隙,自下而上出塔,进入塔前预热器,被加热的气体二次进塔,从塔的下部进入塔内换热器管间,与出塔气体换热后经中心管进入触媒层表面反应,出上绝热层的气体,进入气体混合分布器,与极小一部分从大盖外引进混合分布器的冷气体(升温还原时用以控制下绝热层的触媒温度,正常生产不用冷激气),混合进入下绝热层,出下绝热层的气体进入塔下部换热器管内,与二次进塔气体换热以后出塔,出塔气体进入烃分离器,分离掉烃后气体进入水冷器冷却,然后进氨冷器进一步冷却,再经水分离器分离后去压缩机六进。
2 主要设备2.1甲醇塔Φ1200mm,是由一个直形异径冷管束,两个气体混合分布器,一个集气罩,把触媒层分成三轴一径,二个绝热段,一个内冷段,一个径向段组成,内装填甲醇催化剂,下部有一列管式换热器。
醇烃化精制新工艺在合成氨生产中的应用

醇烃化精制新工艺在合成氨生产中的应用摘要:介绍了醇烃化精制新工艺替代甲烷化工艺在合成氨厂的应用情况。
事实证明,利用闲置的高压设备进行醇烃化技术改造,不仅投资省,而且操作弹性大、设备维护工作量小,具有明显的经济效益和环保效益。
关键词:合成氨生产;应用一、合成氨生产工艺的探究在我国合成氨企业中,虽然生产工艺各不相同,原料采用、设备结构和操作条件也各有差异,但是实现合成氨的基本步骤则是相同的。
首先,原料经过预处理后以不同的方式制备原料气(氢氮混合气),随后经过脱硫、变换、净化等工序后,将原料气压缩至一定的压力后,引入合成系统。
然后,气体通过最终净化,并换热升温至操作温度,送入合成塔内的催化剂层,在其中进行氨的合成反应。
反应后,氢氮混合气不能全部转化成氨,必须将其中的氨分离,剩下的氢氮混合气由循环压缩机补充压力后,与压缩机送来的新鲜气混合,再次进行合成,如此连续循环操作合成氨。
合成氨生产过程较为复杂,为保证各工序有序进行,在生产过程中根据不同的反应情况,给予合适的温度、压强和相应的催化剂等。
合成氨原料气的制备过程不仅将消耗大量的能源物质(煤、碳、天然气、水蒸气)作为原料,更需要消耗大量的能源物质作为动力能源消耗。
因此,制气环节能耗和成本较大,占合成氨生产的60%~70%。
其次在变换、净化及合成过程中都需要压缩,压缩机的使用也要消耗大量的动力能源。
最后,整个工艺过程中需要大量的换热蒸汽,产生大量的余热及三废物质。
因此如果能够实现合成氨过程中的各种能源物质的有效综合利用,可降低整个过程中的能耗,减少不必要的能源损耗,实现合成氨过程中的节能减排。
二、采用醇烃化原料气精制工艺的依据醇烃化工艺即在用甲醇化、烃化(或甲烷化)反应的方法来净化精制合成氨原料气,使合成氨原料气进入氨合成工段之前的气体中CO 、CO2(俗称气体中的“微量”指标)总量小于10ppm,并联产甲醇。
它与铜洗工艺或甲烷化流程相比,流程短、精制度高,操作稳定可靠,节约能耗、物耗,经济效益显著。
合成氨工艺

合成氨工艺————————————————————————————————作者:————————————————————————————————日期:合成氨工艺流程(1)原料气制备将煤和天然气等原料制成含氢和氮的粗原料气。
对于固体原料煤和焦炭,通常采用气化的方法制取合成气;渣油可采用非催化部分氧化的方法获得合成气;对气态烃类和石脑油,工业中利用二段蒸汽转化法制取合成气。
(2)净化对粗原料气进行净化处理,除去氢气和氮气以外的杂质,主要包括变换过程、脱硫脱碳过程以及气体精制过程。
①一氧化碳变换过程在合成氨生产中,各种方法制取的原料气都含有CO,其体积分数一般为12%~40%。
合成氨需要的两种组分是H2和N2,因此需要除去合成气中的CO。
变换反应如下:CO+H2OH→2+CO2 =-41.2kJ/mol 0298HΔ由于CO变换过程是强放热过程,必须分段进行以利于回收反应热,并控制变换段出口残余CO含量。
第一步是高温变换,使大部分CO转变为CO2和H2;第二步是低温变换,将CO含量降至0.3%左右。
因此,CO变换反应既是原料气制造的继续,又是净化的过程,为后续脱碳过程创造条件。
②脱硫脱碳过程各种原料制取的粗原料气,都含有一些硫和碳的氧化物,为了防止合成氨生产过程催化剂的中毒,必须在氨合成工序前加以脱除,以天然气为原料的蒸汽转化法,第一道工序是脱硫,用以保护转化催化剂,以重油和煤为原料的部分氧化法,根据一氧化碳变换是否采用耐硫的催化剂而确定脱硫的位置。
工业脱硫方法种类很多,通常是采用物理或化学吸收的方法,常用的有低温甲醇洗法(Rectisol)、聚乙二醇二甲醚法(Selexol)等。
粗原料气经CO变换以后,变换气中除H2外,还有CO2、CO和CH4等组分,其中以CO2含量最多。
CO2既是氨合成催化剂的毒物,又是制造尿素、碳酸氢铵等氮肥的重要原料。
因此变换气中CO2的脱除必须兼顾这两方面的要求。
一般采用溶液吸收法脱除CO2。
浅谈合成氨原料气精制工艺的发展
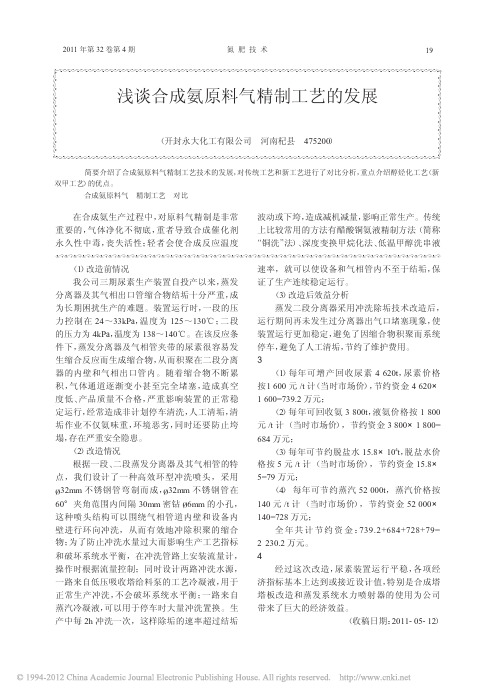
25.0
原料气精制后含 CO 的体积分数 (×10-6) 6.0 以下
原料气精制后含 CO2 的体积分数 (×10-6) 0.017 以下
蒸汽冷凝液,可以用于停车时大量冲洗置换。生 带来了巨大的经济效益。
产中每 2h 冲洗一次,这样除垢的速率超过结垢
(收稿日期:2011- 05- 12)
20
氮肥技术
2011 年第 32 卷
氮洗涤净化精制法(适应于粉煤制气和水煤浆制 气工艺)等。随着科技的不断发展,合成氨原料气 精制工艺也在不断地改进和提高,其中双甲工艺 和醇烃化工艺(也称新双甲工艺)取代传统的精 制工艺并得到了广泛的应用和发展,新工艺具有 降 低 消 耗 、节 约 成 本 、稳 定 操 作 、净 化 彻 底 的 特 点。 1 合成氨原料气传统精制工艺 1.1 醋酸铜氨液精制方法
双甲工艺的主要反应方程式: 甲醇化反应 CO+2H2=CH3OH+Q CO2+3H2=CH3OH+H2O+Q 甲醇化反应主要以 CO、CO2 与 H2 合成反应 生成甲醇产品,并去除了原料气中的一定量的 (CO+CO2),这是双甲工艺的第一步净化反应的功
合成氨原料气的精制陈诚
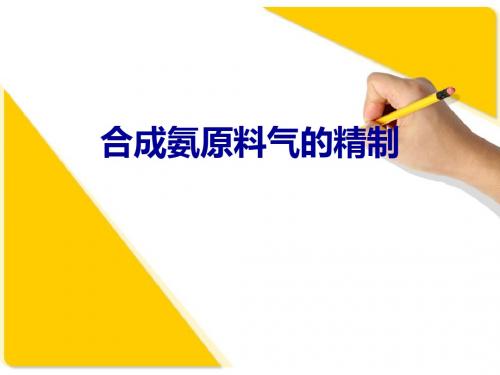
4 操作条件 (1)温度 铜液温度: 8~12℃ 回流塔进口温度:25~38 ℃ 回流塔出口温度:40~55℃ 下加热器出口温度:60~68℃ 上加热器出口温度:74~78℃ 再生器出口温度:74~78℃ 氨冷器出口温度:8~15℃ (2)压力 铜洗操作压力: 12.0~15.0 MPa 再生压力: 0.106~0.108 MPa 铜塔进出口压差≤0.5 MPa 铜泵进口压力:0.04~0.12 Mpa (3)成分 总铜2.0~2.5mol/L 总氨8.5~12.5 mol/L 总酸≥总铜10~15%,为2.2~3.0 mol/L 残存CO<0.005m3CO/ m3 残存CO2≤1.5 mol/L 铜比5~8 净氨塔氨水滴度:由生产科另行下达指标
(1)吸收CO2是依靠铜氨液中的游离氨,反应如下。 2NH3+CO2+H2O =(NH4)2CO3+Q 生成的(NH4)2CO3会继续吸收CO2而生成NH4HCO3
(NH4)2CO3+CO2+H2O2=NH4HCO3+Q
以上两个反应都是放热反应,在吸收过程中会放出大量热量,使铜液 温度上升,影响吸收能力。生成的碳酸铵和碳酸氢铵在温度较低时易 于结晶;当铜氨液中的醋酸和氨量不足时,铜液吸收CO2后又会生成 碳酸铜沉淀,所有这些,都将造成设备和管道堵塞,影响生产。所以, 进入铜洗系统的原料气中CO2的含量不可太高,并且铜液中应有足够 的氨和醋酸含量。
(3)补充所消耗的氨、醋酸和铜,冷却降温
铜氨液再生过程中,由于加热温度升高,使铜氨液中的氨、醋酸挥发 一部分,必须补充一定量的氨和醋酸。
吸收过程中,部分H2S与低价铜离子反应生成了Cu2S沉淀,降低了铜 氨液中总铜的含量,必须给铜氨液中补充铜。
合成氨原料气精制
合成氨原料气精制技术
——双甲新工艺
合成氨原料气用变换反应, 使CO降至1.5%~5%,CO2降至0.2% • (2)甲醇化 通过下述反应将CO、CO2变成 化学产品甲醇,使原料气中CO+CO2达到 0.1%~0.3%,此过程称为甲醇化 CO+2H2 → CH3OH CO2+3H2→CH3OH+H2O
•
氨经济效益为150.48万元。双甲工艺有明 显的节能效益,吨氨煤气(或天然气)消 耗降低11.24%,可少消耗汽400~600kt。 ④环境效益 减少和消除了两个污染源。因 去除了铜洗工艺,消除了因铜液“跑冒滴 漏”造成的污染。因将放空的CO、CO2 回收利用制取甲醇,消除了铜洗再生产放 空污染。
① 气体中CO+CO2净化指标 气体净化前 20~25cm3/m3,气体净化后小于等于 10cm3/m3。 ② 吨氨原材料消耗定额 采用新工艺前,铜洗 工序需消耗铜0.2kg、醋酸2kg、氨10kg、蒸 汽350kg。采用新工艺后,取消铜洗工序,消 耗摊入副粗甲醇成本。 ③ 经济效益 因取消铜洗工序,吨氨可节约物耗 (铜、冰醋酸、液氨)14元、蒸汽30元、氨 耗6.48元等。年产10kt合成氨可节约50.48万 元;副产甲烷,按氨醇比5:1计算,10kt氨副 产2000t甲醇,利润100万元。年产10kt合成
合成氨原料气醇烃化净化精制新工艺技术
合成氨原料气醇烃化净化精制新工艺技术合成氨是一种重要的化学原料,在农业、化肥生产以及其他领域有广泛的应用。
合成氨的生产过程中,醇烃化是一个关键的步骤,它将醇类原料氧化成氨气。
然而,该过程中也存在着一些问题,如氨气纯度不高、能耗大和废水处理困难等。
为了解决这些问题,研究人员提出了一种新的工艺技术,通过气醇烃化净化和精制的方法来改进合成氨的生产过程。
新工艺技术的主要步骤包括以下几个方面:首先,选择高纯度的醇类原料作为氨气的来源。
一般来说,乙醇和丙醇是合成氨生产中常用的原料,它们具有较高的氨气产率。
在这一步中,可以采用蒸馏等方法从原料中提取纯度较高的醇类化合物。
其次,将醇类化合物经过催化氧化反应得到氨气。
这个步骤的关键在于选择适当的催化剂和反应条件,以提高氨气的产率和纯度。
同时,还需控制反应中的温度、压力和氧化剂的使用量,以减少能耗和废水产生。
接下来,对产生的氨气进行净化处理。
在这一步中,可以采用吸附剂、膜分离或冷凝等方法去除气相中的杂质,如水、氧气和碳氧化物等。
通过这些净化手段,可以提高氨气的纯度,并减少对后续工艺步骤的影响。
最后,对净化后的氨气进行精制处理。
在这一步中,可以利用洗涤和吸附等方法去除氨气中的杂质,如硫化氢和二氧化碳等。
通过精制处理,可以进一步提高合成氨的纯度,并保证其达到工业生产的要求。
总的来说,合成氨原料气醇烃化净化精制新工艺技术为合成氨的生产过程提供了一种可行的改进方法。
该工艺技术通过选择高纯度的醇类化合物原料、优化催化氧化反应条件以及采用净化和精制手段,可以提高氨气的产率、纯度和质量,降低能耗并减少废水处理难题,从而实现合成氨生产过程的可持续发展。
合成氨是一种广泛用于农业、化肥生产和其他领域的化学原料。
目前,最常用的方法是通过醇烃化将醇类原料氧化成氨气。
然而,传统的合成氨工艺存在一些问题,如氨气纯度低、废水处理难题以及能耗较高。
为了解决这些问题,研究人员提出了一种新的合成氨原料气醇烃化净化精制工艺技术。
合成氨原料气醇烃化净化精制新工艺
合成氨原料气醇烃化净化精制新工艺1. 醇烃化工艺开发简况合成氨原料气醇烃化净化精制工艺,即在用甲醇化、烃化(或甲烷化)反应的方法来净化精制合成氨原料气,使合成氨原料气进入氨合成工段之前的气体中CO、CO2(俗称气体中的“微量”指标)总量小于10ppm。
此工艺还可联产甲醇,用此工艺取代传统的“醋酸铜氨液洗涤法(俗称铜洗法)”的净化精制合成氨原料气的方法。
工艺简称醇烃化工艺(或双甲工艺)。
合成氨原料气醇烃化净化工艺是双甲工艺的升级技术,双甲工艺是湖南安淳高新技术有限公司开发成功的技术,该技术于上世纪1990年提出,1991年进行工业化实施,1992年9月第一套工业化装置在湖南衡阳市氮肥厂投产成功,国际上属于首先提出,最先进行工业化生产。
1993年4月获国家发明专利权,相继又申请了可调节氨醇比的醇烃化工艺专利,美、英等权威化学文摘均作了报道。
1994年元月通过化工部科技鉴定,1994年6月国家科委将该项目列入《国家重大科技成果推广计划》项目。
第一套装置至今已正常运行13年,目前净化精制能力达到了总氨8万吨/年,副产1万吨甲醇/年,取得了很好的效益。
目前,推广的工艺最大处理合成氨能力为40万吨,在全国中、小合成氨厂推广达15家,目前正在进行工程设计的有5家。
湖南郴州桥口氮肥厂的双甲工艺工程被评为国家优秀创新工程,双甲工艺技术于2000年被授予湖南省科技进步一等奖。
双甲工艺评为1995年度原化学工业部十二大重大科技成果之一,给予重点推广。
2003年醇烃化工艺获得国家科技进步二等奖。
此工艺开发和发展可分为三个阶段,历时十多年的开发创新和竭力推广,有着超乎寻常的辛劳可谓十年磨一剑。
技术发展的第一阶段——确认了国产的甲烷化催化剂在高压条件下的运行条件。
技术发展之初,当有双甲净化这个工艺创意时,当时国内的很多厂家已经有了联醇工段,一般为联醇后再串铜洗工段进行净化精制方法,由于联醇出口的CO和CO2的指标与传统的甲烷化进口的气体成份指标不一样,且压力等级也不一样,要将铜洗去掉用甲烷化来替代必须首先解决进甲烷化炉的进口气体的气体成份问题——一定要使醇后气中的CO+CO2总量不超过0.7%,且较低为好。
合成氨生产的三个过程
合成氨生产是一个复杂的过程,包括三个主要阶段:原料气制备、净化、氨的合成。
以下是每个阶段的详细描述:一、原料气制备合成氨生产的第一步是制备原料气,即氮气和氢气的混合气体。
这个过程通常使用天然气或煤作为原料。
天然气蒸汽转化法:天然气的主要成分是甲烷,通过蒸汽转化反应,甲烷与水蒸气在催化剂的作用下反应生成一氧化碳和氢气。
然后,一氧化碳通过变换反应转化为二氧化碳,氢气则被回收利用。
煤为原料:以煤为原料时,首先通过气化炉将煤转化为煤气,煤气中含有大量的氢气和一氧化碳。
然后,一氧化碳通过变换反应转化为二氧化碳,氢气则被回收利用。
二、净化在合成氨生产中,原料气需要经过净化处理,以除去其中的杂质。
脱硫:硫化物是原料气中的主要杂质之一,必须将其除去。
通常使用催化剂或化学吸收剂将硫化物转化为硫化氢,然后通过酸碱洗涤法将其除去。
脱碳:一氧化碳是原料气中的另一种杂质,它会对氨的合成反应产生不利影响。
通过使用催化剂或化学吸收剂将一氧化碳转化为二氧化碳,然后通过碱洗法将其除去。
氢气提纯:经过脱硫和脱碳处理后,原料气中的氢气纯度仍然不够高。
因此,需要进行氢气提纯,通常使用变压吸附或低温分离等方法将氢气纯度提高到99%以上。
三、氨的合成经过净化的原料气进入氨的合成阶段。
合成反应:在高温高压下,氮气和氢气在催化剂的作用下反应生成氨气和水蒸气。
这个反应是放热反应,需要控制温度和压力以确保反应的顺利进行。
气体分离:合成反应完成后,气体混合物需要进行分离。
通常使用冷凝法将水蒸气冷凝成液体水,然后通过蒸馏法将氨气从气体中分离出来。
氨的精制:经过气体分离后得到的氨气可能含有其他杂质,如硫化氢、二氧化碳等。
因此,需要进行氨的精制,通常使用化学吸收法或物理吸附法将杂质除去,以提高氨的纯度。
产品储存和运输:经过精制后的氨可以储存在专门的储罐中,也可以通过管道输送到下游用户。
在储存和运输过程中,需要注意安全措施,防止泄漏和事故发生。
总之,合成氨生产是一个复杂的过程,包括原料气制备、净化和氨的合成三个主要阶段。
- 1、下载文档前请自行甄别文档内容的完整性,平台不提供额外的编辑、内容补充、找答案等附加服务。
- 2、"仅部分预览"的文档,不可在线预览部分如存在完整性等问题,可反馈申请退款(可完整预览的文档不适用该条件!)。
- 3、如文档侵犯您的权益,请联系客服反馈,我们会尽快为您处理(人工客服工作时间:9:00-18:30)。
合成氨原料气醇烃化净化精制新工艺合成氨原料气醇烃化净化精制新工艺合成氨原料气醇烃化净化精制新工艺作者/来源:谢定中,卢健(湖南安淳高新技术有限公司,湖南长沙410015)日期: 2006-01-10 点击率:8771 醇烃化工艺开发简况合成氨原料气醇烃化净化精制工艺是双甲工艺的升级技术。
双甲工艺是湖南安淳高新技术有限公司开发成功的原创型技术,该技术于1990年提出,1991年进行工业化,1992年9月第一套工业化装置在湖南衡阳市氮肥厂投产成功,在国际上最早提出,最先进行工业化生产。
1993年4月获国家发明专利,相继又申请了可调节氨醇比的醇烃化专利技术,美、英等权威化学文摘均作了报道。
1994年元月通过化工部科技鉴定,1994年6月国家科委将该项目列入《国家重大科技成果推广计划》项目。
第一套装置至今已正常运行15年,目前这个示范厂的净化精制能力上升到了总氨80kt/a,副产10kt/a 甲醇,工艺投用以来,取得了很好的经济和社会效益。
目前,推广的工艺最大合成氨能力达400kt/a,在全国中、小合成氨厂推广达35家之多。
湖南郴州桥口氮肥厂的双甲工艺被评为国家优秀创新工程,双甲工艺评为1995年度原化学工业部十二大重大科技成果之一,2000年被授予湖南省科技进步一等奖,给予重点推广。
2003年醇烃化工艺获得国家科技进步二等奖。
此工艺开发和发展可分为三个阶段,历时近十五年的开发创新和竭力推广,有着超乎寻常的辛劳,可谓“十年磨一剑”。
技术发展的第一阶段——确认了国产甲烷化催化剂在高压条件下的运行条件。
技术发展之初,当有双甲净化工艺这个创意时,国内的很多厂家已经有了联醇工段,一般为联醇后再串铜洗进行净化精制,由于联醇出口CO和CO2的指标与传统的甲烷化进口气体成分指标不一样,且压力等级也不一样,要将铜洗去掉用甲烷化来替代,必须首先解决进甲烷化炉的进口气体的气体成份问题——一定要使醇后气中CO+CO2总量不超过0.7%,且越低越有利于提高气体的利用率和降低气体的消耗。
另外要使甲烷化催化剂能在甲醇之后的压力级内运行必须有一套可行的工艺条件及设备等来保证。
而当时,国际、国内传统镍基甲烷化催化剂的使用压力均在0.3MPa,而当时甲醇催化剂活性压力为13MPa,按工艺布置,甲烷化只能放置在甲醇后,因此,必须要找出甲烷化催化剂在高压下的工况条件。
我公司通过改变工艺条件、流程及设备结构,进行了大量的实验,模索出了一整套甲烷化催化剂在高压条件下的运行条件,于1991年在湖南衡阳氮肥厂的40kt/a装置上投产,达到了预期的效果。
技术发展的第二阶段——确定了可调氨醇比的思维模式及工艺条件。
当流程打通后,气体的成分控制、新鲜气的消耗、副产甲醇的量及工艺长久稳定运行的条件等均需要摸索,要求有切实可行的工艺方法及操作工艺指标。
特别是当甲醇市场波动时,氨和副产甲醇的产量配合要自如,且经济性能要好、工艺指标也要先进。
为此我们摸索出了一种可调氨醇比的工艺条件和设备配置方法,达到了醇氨比可在1∶20到1∶1的范围内进行调整,且可保证工艺运行稳定,净化精制气净化指标不变的目标。
这种工艺方法的更新,使很多厂家获得了十分优厚的效益回报。
技术发展的第三阶段——开发了醇烃化净化精制工艺,代替甲醇甲烷化(双甲)工艺。
众所周知,甲烷化反应主要是将醇后气中少量的CO和CO2与气体中的H2进行合成反应,生成CH4和水,而在氨合成工段CH4为无用的惰性气体,将要在生产过程中放空掉。
因此,我们要求醇后气中CO和CO2尽量低,另外找出一种能使合成后的CH4量生成少的催化剂来替代纯甲烷化的工艺,我们开发了一种价廉的催化剂,称之为醇烃化催化剂,以此来取代甲烷化催化剂。
首次使用是在湖南衡阳氮肥厂和湖南岳阳化工股份有限公司,达到了降低新鲜气消耗约30%的效果。
换言之,利用这种催化剂可将原来采用气态的废气输出方式换成液态,且此物质可回收利用,既降低了有效气体的消耗,又使工艺操作和流程更加简化。
基于此,我们成功地将双甲工艺升级为更加先进、更加节能的醇烃化工艺,此技术一问世,得到了同行的一致认同,成功地获得了国家科技进步二等奖。
不论是双甲工艺还是醇烃化工艺净化精制原料气都比目前很多厂家在用传统的铜洗法和深度低变—甲烷化法净化精制工艺有着比较明显优点。
2 醇烃化工艺技术方案2.1 化学反应2.1.1 甲醇化反应原料气中CO、CO2与H2在一定温度、催化剂作用下生成粗甲醇,经过冷却、分离送入中间贮糟,此工艺类似于合成氨的联醇工艺,但对醇后气的指标要求高,因而要求醇塔要有更高的转化率和更好的热利用率。
本工序主要反应方程式如下主反应CO+2H2 = CH3OH +102.5kJ/molCO2+3H2 = CH3OH+H2O+59.6kJ/mol副反应4CO+8H2 = C4H9OH+3H2O +49.62kJ/mol2CO+4H2 = (CH3)2O+H2O+200.2kJ/mol2CH3OH = (CH3)2O+H2OCO+3H2 = CH4+H2O +115.6kJ/molCO2+H2=CO+H2O-42.9kJ/molnCO+2nH2=(CH2)n+nH2O+Q2.1.2 甲烷化反应经甲醇化工序后的醇后气,含CO+CO2为0.03%~0.3%,经换热后温度达到280℃,进入甲烷化工序,净化气中CO、CO2在催化剂作用下,与H2生成甲烷。
反应方程如下:主反应:CO +3H2 = CH4 + H2O +206.3kJ/molCO2 + 4H2 = CH4 + 2H2O +165.1kJ/mol副反应:O2+2H2=2H2O+C +484.0kJ/mol2CO=CO2+C+172.5kJ/molCO+H2=H2O+C+131.5kJ/molNi+4CO=Ni(CO)4(气)2.2 双甲工艺流程简图及说明2.2.1 双甲工艺的原则流程图1 双甲工艺的原则流程图造气出来的半水煤气经气柜后,进行粗脱硫,使H2S含量<0.07g/m3,加压至0.8MPa,进入中变;中变出来的气体CO含量控制在1.5%~5%,经脱碳,使CO2下降到0.2%~0.5%,再用无硫氨水进行第二次脱硫,将H2S脱除到100×10-6以下;再进行精脱硫,使气体之总硫降到0.1×10-6;气体再入高压机压缩到3.0~13MPa(压力的配置与甲醇的产量大小有关,原则上醇产量高时取较低的压力,反之可取高一点)与醇后气进行换热,温度为200℃,进入甲醇化反应。
从甲醇化塔出来的气体,与新来的气体换热,再水冷至40℃左右,进入醇分,经醇分后CO+CO2达到0.03%~0.3%;去高压机加压至与氨合成相等压力,进入甲烷化系统(或醇烃化系统),反应后的气体CO+CO2≤10×10-6,经换热冷却分离水分后,送往合成系统。
从合成氨系统排出的吹除气及液氨贮罐排出的弛放气,经脱氨后去氢回收装置,利用真空纤维或变压吸附法对气体介质的选择吸附,吸附弛放气中的H2。
H2解吸后,回到系统中,未吸附的气体则排空。
2.2.2 可控制醇氨比的联产甲醇双甲工艺流程(图2)双甲工艺的目的是以净化精制原料气为主,副产甲醇为辅。
但随着市场的变化,产品需求也有变化,即有时醇氨比要大幅度调节。
在甲醇市场好时,醇氨比要求达到1∶3或更高。
此时产醇和精制原料气都是双甲(或醇烃化)工艺的重要任务。
这种条件下我们的流程安排原则上是设置两个甲醇塔,第一个甲醇塔以产醇(尽量放在低压级)为主,第二个醇化塔的目的是净化或深度净化合成氨原料气。
经过第二个塔后CO+CO2含量≤0.3%(这种指标既使新鲜气的消耗不多、又可使热的利用率高、操作方便简捷,后面将专门论述)。
图2 可调氨醇比的双甲流程(醇产量较大)这种安排很灵活,当产甲醇为主,醇氨比很大时,原料气通过两塔,在第一塔中CO与CO2的70%转化为醇;第二塔只把剩余30%的CO与CO2 进行转化,达到既产醇又深度净化的效果,使出醇化系统的CO+CO2总量≤0.3%。
如果甲醇市场需求疲软,工艺以净化精制为主,甲醇是副产品,并使产量尽量少;例如醇氨比达1∶10到1∶20,此时可只用一个醇化塔,这一套醇化系统在运行中可以不启用循环机;以第二醇化塔作为备用塔;当第一塔催化剂活性下降、催化剂老化后,再启用第二塔,同样全过程均可十分方便地控制入甲烷化炉的CO+CO2含量≤0.3%。
第一级甲醇化采用3.0MPa或8.0MPa,第二级甲醇化及甲烷化与氨合成采用12~32MPa压力均可(因地制宜视具体情况确定配置方式)。
第一级仍以产醇为主,即90%的CO与CO2在此压力下转化为粗甲醇,剩余10%的CO与CO2在12~32MPa(或30MPa)压力下转化为甲醇,使CO+CO2含量≤0.3%进入甲烷化,甲烷化后气体中CO+CO2≤10×10-6,送入氨合成。
此流程的优点之一是在低压下合成甲醇,即有占整个原料气6%~10%的气体(CO、CO2和生成甲醇需要的H2),不需加压到更高压力,大大节约了电耗。
优点之二是在3~8MPa压力下甲醇化,可以利用甲醇化反应热副产中压蒸汽,作动力用,背压后蒸汽仍可作为工艺用汽。
优点之三由于甲烷化(或醇烃化)与氨合成等压,可免除工艺气体再过压缩机升压而污染气体这一环节,可以较方便地利用氨合成反应热,维持低成分下(CO+CO2≤0.3%)甲烷化炉(或醇烃化炉)的反应温度,而不必开电炉来维持反应。
对老厂采用醇烃化工艺,高压机没有3~5MPa这一段,而只有7.8MPa、12.5MPa和30MPa等压力段,则分别可以在7.8MPa和12.5MPa压力下进行甲醇化,然后升压至15MPa或32MPa进行甲烷化或醇烃化和氨合成。
这种流程的节能效果也很显著。
这种多级不等压的双甲工艺是我公司因地制宜既有利于生产,又有利于净化和节能的通用设计方法,均有成功的应用实例。
2.2.3 联产甲醇的醇烃化精制流程将甲烷化镍基催化剂改成我公司开发的醇烃化催化剂,则形成可调氨醇比的醇烃化精制流程(图3)。
图3 可调氨醇比的醇烃化原则流程取代双甲工艺的的醇烃化工艺中烃反应有如下几个主要的反应式(2n+1)H2 + nCO →C n H(2n+2) +nH2O (1)2nH2 + nCO →C n H2n +nH2O (2)2nH2 + nCO →CnH(2n + 2)O +(n-1)H2O (3)(3n+1)H2 + nCO2→C n H(2n+2) +2nH2O (4)从反应式可看出,醇后气中CO与CO2在醇烃化催化剂选择作用下,大部分可以生成醇类、多元醇类及非常少量的CH4。
多元醇类物质、醇烃类等物质均可在常温下冷凝为液体,有很好的分离性能,环保性能也很好。
这种物质可作为燃料使用或作为产品来提纯(将其直接送到甲醇精馏岗位提走其中35%的甲醇产品,其余可作为甲醇精馏残液进入燃烧炉内烧之)。