首件确认操作指导书
首件确认作业指导书

首件确认作业指导书1.目的:规范首件产品的确认流程,使之在制造过程中流通良好。
确保首件产品质量,避免批量质量问题的发生;2.范围:适用于生产部所有生产线。
3.职责:各产线班组长负责对首件样品的制作,并依据SOP文件和基准样件进行首件确认;质量主管进行对首件确认执行工作进行监督检查。
4.流程:4.1.1所有产品每批次批量开产前(SMT班组换班时),都由产线组长或当班负责人主导,依据BOM清单、标准工艺文件、及基准样件制作出1pcs或一拼板首件产品,班组长或当班负责人依据BOM清单、SOP文件、检验文件及检验工装逐级对首件产品进行确认。
4.1.2 首件确认合格后,班组长及时填写《产前/首件确认记录表》,将首件产品放置在指定区域,并通知产线开产;如果首件确认不合格,应立即对首件产品进行自查,如果无法解决,应立即通知主管领导或质量主管进行协助处理;待问题解决后方可恢复生产,并对更正后生产的首件产品再次进行确认。
4.1.4 正式开产后,班组长应对生产线员工操作的符合性、关键工序、检验设备等生产情况进行巡查,并及时予以纠正处理,保持实际操作与SOP文件一致;质量主管对产品首件样品进行监督检查,并抽检首件确认过程的验证工作,对产线首件验证后出现不合格,立即停止生产并查找不合格原因,待问题解决后需重新进行首件确认流程。
4.1.5 正式生产后,如果出现操作人员批量人员变动或交接班时、生产设备出现异常并长时间停机时、物料型号更换时,检验工装设备做更换时,都需要重新进行首件确认,首件确认流程按照4.1.1和4.1.2条款内容确认执行,并做好相应记录;5.流程图:附件:《产前/首件确认记录表》《过程质量控制作业指导书》《产品质量异常处理办法》《产品制造工艺标准》《不合格品控制作业指导书》。
首件检验流程指导书
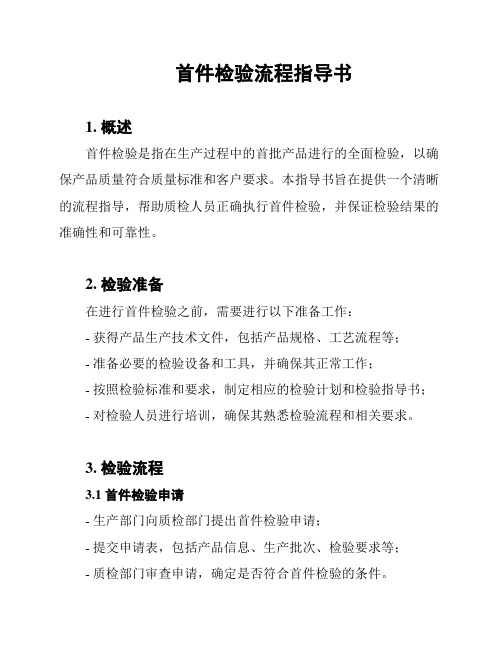
首件检验流程指导书1. 概述首件检验是指在生产过程中的首批产品进行的全面检验,以确保产品质量符合质量标准和客户要求。
本指导书旨在提供一个清晰的流程指导,帮助质检人员正确执行首件检验,并保证检验结果的准确性和可靠性。
2. 检验准备在进行首件检验之前,需要进行以下准备工作:- 获得产品生产技术文件,包括产品规格、工艺流程等;- 准备必要的检验设备和工具,并确保其正常工作;- 按照检验标准和要求,制定相应的检验计划和检验指导书;- 对检验人员进行培训,确保其熟悉检验流程和相关要求。
3. 检验流程3.1 首件检验申请- 生产部门向质检部门提出首件检验申请;- 提交申请表,包括产品信息、生产批次、检验要求等;- 质检部门审查申请,确定是否符合首件检验的条件。
3.2 首件检验计划制定- 根据产品生产技术文件和检验要求,制定首件检验计划;- 确定检验点、检验方法和抽样数量;- 制定检验记录表和检验报告格式。
3.3 首件检验实施- 生产部门按照生产工艺流程制造首批产品;- 质检人员在生产过程中,根据检验计划进行抽样检验;- 进行外观检查、尺寸测量、性能测试等必要的检验项目;- 记录检验结果,包括合格、不合格和修复情况。
3.4 首件检验评估- 根据首件检验结果,评估产品质量和生产工艺的可行性;- 分析不合格项的原因,并提出改进措施;- 对合格产品进行认可,批准生产继续进行。
4. 检验报告与记录4.1 检验报告- 根据检验记录,编制首件检验报告;- 报告内容包括产品信息、首件检验结果、不合格项等;- 报告应及时提交给相关部门和负责人。
4.2 检验记录管理- 对检验记录进行归档和保留,确保完整性和可追溯性;- 定期对检验记录进行检查和审核;- 对不合格项进行追踪处理,确保问题得到及时解决。
5. 审核和改进本首件检验流程指导书应定期进行审核,以确保其符合实际操作的要求和流程。
同时,根据持续改进的原则,不断完善和优化检验流程,提高产品质量和生产效率。
首件作业指导书
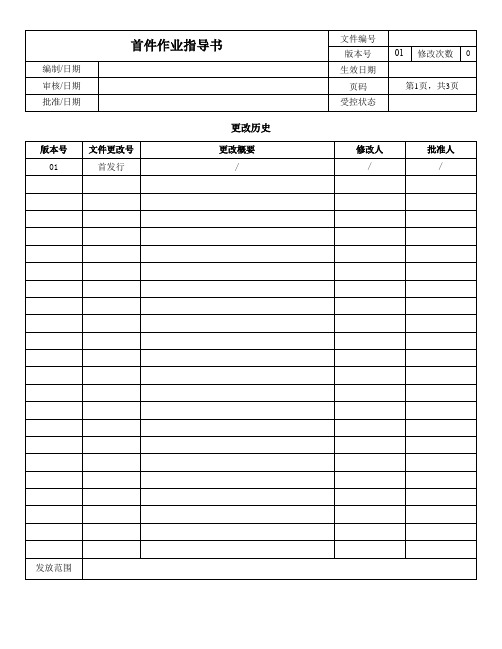
五、作业前的准备:
1、标准样品;2、制令单;
3、图纸;4、清场记录表;
六、作业步骤及方法:
1、生产班长领取标准样(返单产品标准样与初次生产订单产品标准样到品管部领取);
2、找出该订单产品的加工制令单及图纸;
3、取整模或一轮产品依制令单核对相应尺寸;
4、取整模或一轮产品依制令单测试功能性项目;
更改历史
版本号
文件更改号
更改概要
修改人
批准人
01
首发行
/
/
/
发放范围
一、目的:
对制程中的产品规格符合性验证,确保产品的各项特性能满足客户的规定要求。
二、适用范围:
适用于所有生产中的产品。
三、参考文件资料:
(一) QC工程表
(二)产品鉴别与追溯管理程序
(三)检验与试验管理程序
(四)品质瑕疵程度分类表
四、表单记录:
10、品管确认符合要求后在《首件确认表》中签名,并在首件标准样品的标签上盖章;
11、《首件确认表》、标准样品挂在机台指定位置供巡检或自检参照;
12、生产完成后,首件确认样及首件确认表一同归档保存;
七、首件时机:
1、中途机台停机4小时以上,技术员(机长)或班长需重新做首件确认;
2、同机台、同模具换不同产品时,技术员(机长)或班长需重新做首件确认;产品更换不同配套模具时,技术员(机长)或班长需重新做首件确认;
5、一种产品连续工作4个工作日时,技术员(机长)或班长需重新做首件确认;
6、首件生产现场确认完成后,品管员应在1小时内进行复核;
7、如在以上时机,生产部门无《首件确认表》,品管员应在第一次巡检或抽检前进行首件确认,并将确认结果记录于《工序巡检记录表》中;
纸箱检验首件确认作业指导书【最新版】
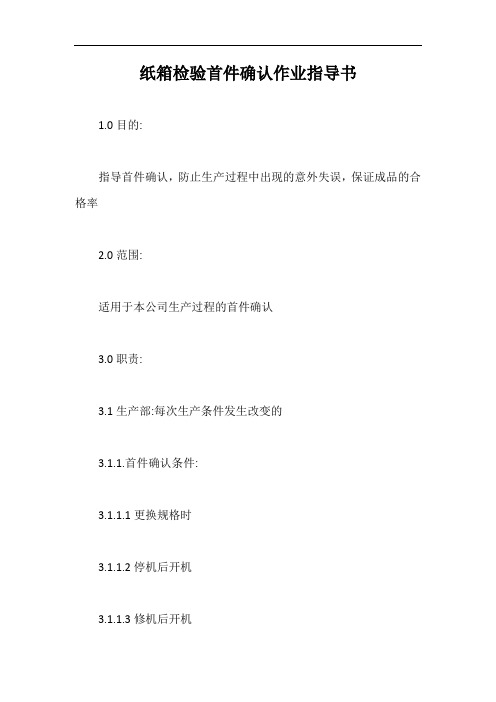
纸箱检验首件确认作业指导书
1.0目的:
指导首件确认,防止生产过程中出现的意外失误,保证成品的合格率
2.0范围:
适用于本公司生产过程的首件确认
3.0职责:
3.1生产部:每次生产条件发生改变的
3.1.1.首件确认条件:
3.1.1.1更换规格时
3.1.1.2停机后开机
3.1.1.3修机后开机
3.1.1.4交接班时
3.2品管部:对生产过程的作业方法进行监督和对产品进行检验。
4.0首件确认项目:
4.1 检验
4.1.1 检验项目
4.1.1.1 轻缺陷:标志、印刷、压痕线、刀口、箱钉、接合、裱合、摇盖耐折。
4.1.1.2 重缺:内尺寸、厚度、含水率。
4.1.2 检验方法及要求
4.1.2.1 外观检验按表1规定逐项检验。
表4
注:大、中、小型箱内综合尺寸分别为:大于或等于2000mm、小于2000mm而大于1000mm、小于或等于1000mm
5.0相关标准
5.1GB/T 6543 包装用单瓦楞纸箱和双瓦楞纸箱
6.0相关记录
6.1《首件确认单》。
首件确认作业指导书(CNC)
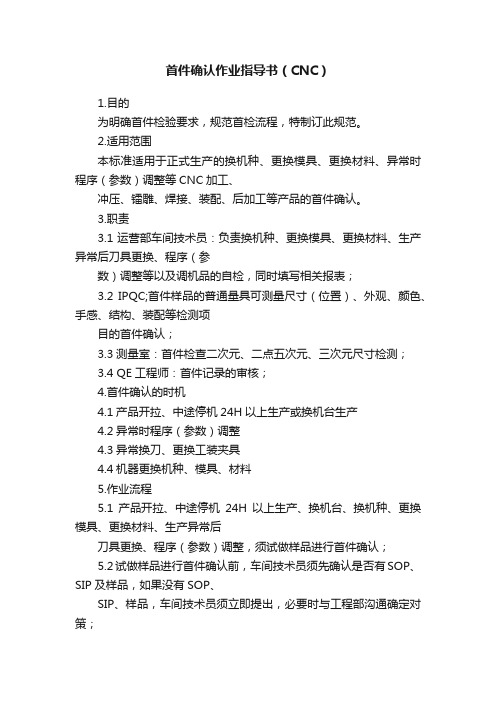
首件确认作业指导书(CNC)1.目的为明确首件检验要求,规范首检流程,特制订此规范。
2.适用范围本标准适用于正式生产的换机种、更换模具、更换材料、异常时程序(参数)调整等CNC加工、冲压、镭雕、焊接、装配、后加工等产品的首件确认。
3.职责3.1运营部车间技术员:负责换机种、更换模具、更换材料、生产异常后刀具更换、程序(参数)调整等以及调机品的自检,同时填写相关报表;3.2 IPQC;首件样品的普通量具可测量尺寸(位置)、外观、颜色、手感、结构、装配等检测项目的首件确认;3.3测量室:首件检查二次元、二点五次元、三次元尺寸检测;3.4 QE工程师:首件记录的审核;4.首件确认的时机4.1产品开拉、中途停机24H以上生产或换机台生产4.2异常时程序(参数)调整4.3异常换刀、更换工装夹具4.4机器更换机种、模具、材料5.作业流程5.1产品开拉、中途停机24H以上生产、换机台、换机种、更换模具、更换材料、生产异常后刀具更换、程序(参数)调整,须试做样品进行首件确认;5.2试做样品进行首件确认前,车间技术员须先确认是否有SOP、SIP及样品,如果没有SOP、SIP、样品,车间技术员须立即提出,必要时与工程部沟通确定对策;5.3车间技术员按照调机作业标准(CNC车间:《加工程式单》)和SIP调整好机器,安装好刀具、工装夹具后进行试调打样,样品完成后车间技术员先依据SIP 进行自检:外观,同时对卡尺、深度计等普通量具可以测量的尺寸(位置)进行测量,需要三次元、二点五次元、二次元测量的,送测量室进行检测;5.4测量室测量的结果,必须保留好电子档,生产有需要时打印并由测量员签名;5.5外观、机构、尺寸、实配OK,则交现场IPQC进行确认;如确认NG,则继续改善直至OK。
对于有改善难度和判定困难的外观问题,须请QE工程师或工程部确认,必要时升级上报。
5.6尺寸(位置)NG、外观改善有难度等问题,经过客服质量工程师或工程部确认可以生产的,必须有确认人的签名,否则车间技术员不可生产,IPQC应做不合格判定同时开出《不合格处理通知单》升级上报。
首件制作与确认流程

1.品质组长对首件与《首件确认单》上核对内 容,进行核对,并在《首件确认单》做好对 应记录 2.将首件装入PE袋中,并在上面做好对应的签 名与标示。 3.对于新产品、新订单、及特殊、订制订单的 首件,由IPQC交给业务业核对。必须经过该 订单的业务员进行核对,并签名确认。
1.核对确认好的首交还生产拉长 2.按生产计划将一个首件放置产线拉头看板指 定位置,另一个从拉头流下,每个工位的作业 人员拿起来查看与现有物料核对,无误后流入 终检位的指定位置 与拉长面对面当面交接,并在《派料 单》上备注签名确认好
1.IPQC拿对应《BOM》核对物料 2.严格按照《作业指导书》和工艺文 件进行制作 3.首件制作的数量是2个
《BOM》 《作业指导书》
拉长完成首件制作后,填写好《首件确认单》
与首件一同交IPQC核对
《首件确认单》
品质部
IPQC进行首件图档确 认
IPQC进行首件让所有的物料进行图档确认, 并在《首件确认单》做好对应记录
品质部
IPQC进行首件与MPC 样品的核对
IPQC进行首件与MPC样品的核对,确认好 作业工艺,实物对照,并在《首件确认单》 做好对应记录
品质部 业务部
生产部
IPQC将核对好的首件交品 质组长及业务员审核
3.工单完成后,首件方可投入产线包装
NO 变更日期
变更履历记录栏 变更内容
担当
承认
深圳市脉威时代科技有限公司
流程名称 序 发行部门
號 責任單位
生产部
生产部
流程图
首件制作与确认流程
发行日期
流程
物料员领完物料
SOP编号
承认
确认
确认
019-注塑首件流程作业指导书

5.1.5更换原来材料或更换材料牌号时(包含更换产品颜色);
5.1.6停机超过12小时后再次生产时;
5.2 检验流程
5.2.1注塑领班依据工艺要求或产品样品对注塑机进行调试生产出首件产品,并进行自检;
5.2.2注塑领班判定生产的产品符合要求时,填写《注塑首件单》对应栏目,提交品管员进行检验;
1.目 的:
规范首件作业流程,杜绝因首件失误或者未进行首件检验确认就进行量产,从而造成批量性质量问题的产生。
2.范 围:
适用于注塑生产制造过程管理。
3.定 义:
3.1首件:换模、换料、转色、模具结构修改、工艺较大调整、停机超过12小时后开始生产的塑胶零件均属于首件。
3.2首件检验:是指产品在连续批量生产之前,或生产过程中设备、人员等影响产品生产的因素有较大变更时,对首件加工件进行的检查确认。
5.3首件合格样板处理方式
5.3.1首件合格样板在本订单完成后,由品管员将首件样板标示擦干净,与同批次合格产品一起包装进入下一工序;
5.3.2首件合格样板如已经破坏不合格的,生产结束时品管员应及时将不合格样板送交碎料房进行破碎处理。
5.4注意事项
5.4.1对于所有检验项目以《注塑产品检验标准》和客户相关的检验图纸为准,品管员必须认真对照技术资料确认,不能漏检项目或在不确认是否合格的情况下盲目签字确认。
5.4.2注塑领班和品管员填写《注塑首件单》时,要字迹清晰;填写错误项以双横杆划掉,在边上写上正确项,并签名;不得以缩写代替全称,不得有漏项、缺项,填写数据需真实、准确,不得代行签名。
5.4.3如因首件检验有误造成产品批量不良返工(报废),品管员负主要责任,品管主管负管理责任。
首件签样作业指导书

1.0目的
建立首件签样制度,明确生产产品品质要求,保证产品质量。
2.0适用范围
适用公司各生产工序、生产制程前的首件签样确认过程。
3.0职责
3.1作业员:负责调试符合要求的首件并签名确认。
3.2各工序主管:负责指导调试符合要求的首件并签名确认,监督、指导本规定执行。
3.3品管:对作业员及部门主管确认签样进行核对并签名确认。
3.4品管经理:负责首件签样的检查及考核.
4.0名词术语
成品样:符合要求的制成品样办,可作色样、内容等方面参照依据。
5.0作业程序
5.1作业员生产前准备齐全机台、工具、样办及相关产品资料。
5.2若发现生产资料不齐全,应向相关部门索取,直到相关资料、样办备齐为止。
5.3作业员力求调试出符合品质要求的首件,若调试过程中发现异常时应立即反馈部门主
管及相关技术人员,直至首件合格为止。
5.4作业员取符合品质要求的首件3PCS签名后交主管确认签名,然后交品管核对,品管及
时回复意见。
5.5经上述三方确认合格首件签样后,便可进行批量生产,首样分别由该生产工序部门、
工艺袋处存档和品管保管。
5.6首件检验完成后,品管填写《首件检验报告》,并分类存档。
5.7本文件产生的品质记录,依据《质量记录控制程序》作业。
6.0支持文件
6.1《记录控制程序》 Q/SNK-CW-02
7.0质量记录
7.1《首件检验记录》 Q/SNK-ZJ-824.04.14。
- 1、下载文档前请自行甄别文档内容的完整性,平台不提供额外的编辑、内容补充、找答案等附加服务。
- 2、"仅部分预览"的文档,不可在线预览部分如存在完整性等问题,可反馈申请退款(可完整预览的文档不适用该条件!)。
- 3、如文档侵犯您的权益,请联系客服反馈,我们会尽快为您处理(人工客服工作时间:9:00-18:30)。
1. 目的
本指导规定了对生产部首件确认流程,防止生产过程出现批量产品错误。
2. 适用范围
本指导适用于灌/包装的首件确认。
3. 职责
3.1品质部负责该指导书的制定和修改。
3.2各产生部门配合执行该作业指导。
4 •程序
4.1首检生产
4.1.1生产部按生产指令单准备好物料。
4.1.2按作业指导书进行首检生产。
4.1.3首件正常情况下约10-20件。
4.2首件确认
4.2.1生产自检
4.2.1.1单元式机台由生产员工对首件进行自检,生产部组长复检,并在首件确认表签字确认。
4.2.1.2流水线由生产部组长自检,并在首件确认表签字确认。
4.3 IPQC 确认
4.3.1 IPQC在收到首件确认表后,应立即进行首检确认。
4.3.2 IPQC根据首件确认表信息,按产品要求对首件进行确认。
4.3.3首检确认合格后,IPQC在首件确认表上签字确认。
4.3.4首件确认不合格,将首件退回生产部重做;直至首检合格后,并在首件确认表上记录,并签字确认。
4.3.5首件完成后,将首件放置线头,随时供查。
4.3.6首件必须有IPQC人员签字才有效,否则无效
437待生产完成后,由IPQC收回首件做处理
5.相关记录
5.1《灌装首件确认表》
5.2《包装首件确认表》。