堆叠评审CheckList
实施项目里程碑评审checklist

通过
是否有明确的功能测试周期
有明确的功能测试周期且合理
是否有明确的测试范围
有明确的测试范围
相关开发文档是否已提交至测试组:功能需求分析说明书、概要设计说明书、网络结构拓扑图、业务流程图等
相关开发文档已提交至测试组:功能需求分析说明书、概要设计说明书、网络结构拓扑图、业务流程图等
确定行方是否有指定模板格式,优先使用行方模板,如没有使用内部模板
3
代码侵入性
开发改造对产品原功能
代码的程度
开发改造代码结构设计是否合理,侵入性是否能够剥离或优化
4
代码健壮性
异常情况考虑
对可能出现的异常情况进行了判断、捕获和处理
5
业务逻辑准确性
代码的处理逻辑、计算逻辑正确性
代码的处理逻辑、计算逻辑正确,能够符合需求需要
6
代码规范
代码抽象程度
公共代码进行了抽象
7
代码开发规范
相关开发文档已提交至测试组:性能需求分析说明书、概要设计说明书、网络结构拓扑图、业务流程图、接口设计文档等
10
性能测试方案/用例模板确定
确定行方是否有指定模板格式,优先使用行方模板,如没有使用内部模板
《性能测试方案》、
《性能测试用例》等有明确的模板
11
输出性能方案/测试用例
是否按照模板格式编写性能测试方案/测试用例
明确测试目标
有明确的测试目标
明确测试阶段
有明确的测试阶段,例如:SIT、UAT等
明确测试环
境
明确的测试环境配置情况
有明确的提交成果物
测试方案中,有写明确的成果物
2
ESI结构工艺评审点检表(checklist)[空白模板]
![ESI结构工艺评审点检表(checklist)[空白模板]](https://img.taocdn.com/s3/m/c3ac82dfb90d6c85ed3ac6a9.png)
序号类型点检项目点检人不符合项原因分析建议措施责任单位/责任人跟进反馈关闭状态改善完成时间复查情况1客户信息、项目简况、评审时间是否明确。
23D图档、CMF、工艺标准等资料客户是否提供。
3产品材质、胚料重量是否确定。
4客户特殊加工要求是否明确,是否满足我司技术能力。
5整体工艺方案和加工顺序是否合理,夹数是否过多,部分夹位能否合并。
6材料余量预留是否合理,能否进一步减少。
7定位基准是否合理可靠,尽可能避免多次转换基准,夹持方式是否牢固。
8刀具选型是否合理,有无特殊要求,刀具加工参数和寿命评估是否合理。
9工序3D有无接刀问题,如何避免接刀风险,同一夹台阶光刀尽可能用一 把刀完成。
10产品变形风险评估,如何有效解决产品加工变形导致的尺寸不稳问题。
11定位孔是否已考虑防呆,定位孔直径公差及深度是否合理,有没有考虑加倒角,加工方式是否合理,大批量生产是否可靠。
12有无放大偏位特征,如何避免。
13加工冷却方式有无特殊要求。
14外观有无特殊要求,外观面不允许出现接刀,外观刀材质选择是否合理。
15容易出现毛刺的特征如何解决毛刺问题,有没有加专门去毛刺刀具刀路。
16进刀位和退刀位是否合理,有无撞刀风险。
17是否需要断刀检测,探头,探点位选择是否合理,探点数量是否合理,变量选择是否正确。
18是否需要记版本号和机台号。
19每次飞面厚度0.30mm,飞面光刀后,接刀纹要控制在0.02以内。
20裙边宽度定义D6销钉+4mm+7mm为准,外侧壁优先考虑分夹加工;外侧壁合夹加工的裙边留料定义D6销钉+4mm+外侧壁刀具过刀直径+1.0mm。
21宽度方向以注塑前半成品尺寸(铝挤面)单边+0.5mm,长度方向以注塑前半成品尺寸(锯切面)单边+1.0mm。
22CNC1飞面,并加工一组定位孔只给CNC2使用,定位孔直径D5,方便后工序二次使用时扩孔。
23CNC2或CNC3加工内腔的工序需同时在产品内腔及外裙边加工两组定位孔作为后工序直至外侧壁工序的定位。
PCB评审CHECK LIST

SCH,PCB同步,库元件最新。走线完 成,DRC消除。 检查器件摆放是否符合结构要求 凸出PCB板边缘器件(如AudioJack) 不会和拼版工艺边干涉 项目中新增加器件的库是否正确, pcb的PartNumber与原理图是否正确 有方向的器件是否都有标示点,有极 性元件的极性是否标有正负极丝印, 是否正确。如芯片1脚、电容、二极 管、三极管、电池的极性。 丝印文字高度不得小于0.5mm,丝印 线宽不得小于0.127mm。BOT面文字需 要镜像.BGA和CSP元件都应有贴片定 NPTH孔周围0.2mm内是否禁止走线。 器件是否远离板边,保证板边有完整 铺 地(机构有特殊要求的器件除外,如天 各个器件之间的距离是否满足最 0.3mm 建议最小线宽线距为0.1mm/0.1mm, BGA pitch为0.5mm时可以在BGA内部 内层局部使用0.075mm/0.075mm的线 宽线距,表层线宽线距不得小于 0.1mm/0.1mm。 相同网络的盲孔(via1-2,via5-6)和 埋孔(via2-5),是否没有重叠,最差只 能 通孔板是否没有通孔落在BB的BGA焊 盘上 HDI板是否没有盲孔(Via1-2,Via5-6) 一半在焊盘上,一半在焊盘外 各Solder Mask开窗区域是否与导线 、过孔重叠 对于ESD器件和滤波电容,要先过器 件再进IC的PIN 表层是否没有长的高速数字走线,否则 会有辐射干扰,影响天线的灵敏度 (LCD BUS,Sensor Bus) 音频线(Speaker,Receiver,Micphone 等)是否进行了差分线、包地处理 多引脚的元器件(如SOIC、QFP 等),引脚焊盘之间的连线,应由焊 盘加引出互连线之后再短接,以免产 生桥接。 不同功能的线,特别是敏感线,是否避 免隔层平行走线 必须对BB芯片进行有效屏蔽,加屏 蔽盖 天线区域的地能否净空
结构设计评审清单
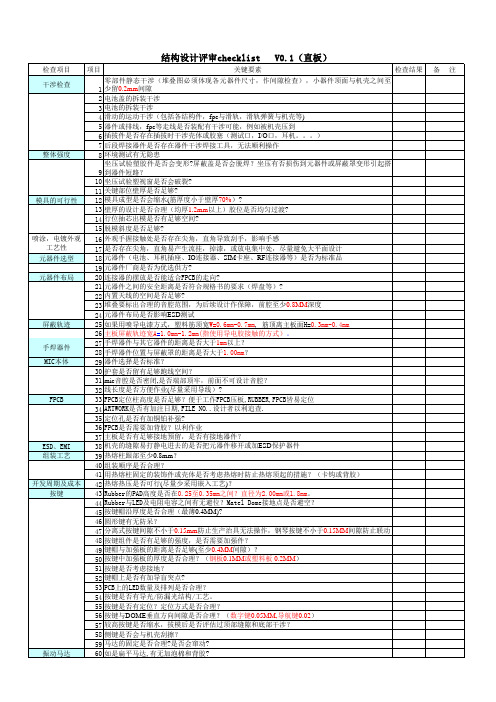
检查项目 干涉检查 项目 1 2 3 4 5 6 7 8 9 10 11 12 13 14 15 16 17 18 19 20 21 22 23 24 25 26 27 28 29 30 31 32 33 34 35 36 37 38 39 40 41 42 43 44 45 46 47 48 49 50 51 52 53 54 55 56 57 58 59 60
视窗
泡棉 壳体组合装配
61 62 63 64 65 66 67 68 69 70 71 72 73 74 75 76 77 78 79 80 81 82 84 85 86 87 89 90 91 93 94 95 96 97 98 99 100 101 102 103 104 105 106 107 108 109 110 111 112 113 114 115 116 117 118 119 120 121 122 123 124 125 126 127
电池盖开启/闭合过程是否方便? 前后左右及高度方向限位是否合理?保证装配紧凑无松动? 金属电池盖是否有单独的按扣固定电池盖,是否接地? 电池盖是否有防止左右晃动和起翘的机构? 电池盖开启/闭合过程的操作是否安全? 对于与机壳采用螺纹联接的天线配合按螺纹标准执行。 天线强度设计是否满足公司拉拔测试 对于插拔式天线,卡扣一般要一对,且成对称分布。 天线连接片的安装性能一定考虑,干涉量是否足够?(至少0.7mm) 天线组合模具及成型工艺性是否合理? 天线组合装配是否容易? 天线组合扣位装配结构是否合理,强度是否足够? 铝制件,结合工艺特点进行评审. 电铸件,结合工艺特点进行评审. 其它,结合工艺特点进行评审. 与外壳或按键配合间隙是否合理 是否有合理的备胶区域, 胶水的选择 是否需要扣位等结构加强装配强度和可靠性 是否有防静电的结构设计? 让位LED灯的设计是否合理?单边间隙是否大于0.50mm 是否有定位孔?定位孔径是否大于1.00mm? 防灰尘进入的措施是否可靠,是否有排气槽 DOME片的选择是否合适?(力度,尺寸,行程。。。) 屏蔽罩上开孔是否在1mm≤φ≤3mm的范围 (考虑RF原因) 孔间距是否满足加工工艺要求,应在3.00mm以上。 吸盘区域的设计直径是否为6mm,是否在重心范围 屏蔽的材料是否能满足要求? 屏蔽罩高度是否合理? 吸盘区域的设计直径是否为6mm,是否在重心范围 屏蔽支架的横梁设计是否便于后续的维修以及检测电子器件?(跟部要留剪断口) 屏蔽罩设计是否考虑芯片点胶需要的避让空间 屏蔽罩设计是否避免平整度不好,吸拾是否容易造成变形? 屏蔽罩盖的固定(定位)设计是否合理?底边距离PCB是否合理? LCM背胶面积及粘贴强度是否能保证拆卸不损伤?(建议中间加屏蔽纸) LCD的装配是否有合理的缓冲空间(lcd最高面到前壳面至少留0.4mm间隙) LCD建模要按最大尺寸,可视角要标出 导光板的光线设计能否把单颗LED灯均匀发散到每个地方 导光板的定位是否可靠精准 导光板的材质是否运用合理 导光板的强度设计是否合理 参照设计规范 是否容易开启/闭合 是否给插拔件提供足够的操作空间 结构/形状/厚度是否满足模具工艺及成型工艺的要求 结构/形状/厚度是否影响零件/产品强度及功能 是否有/需要操作指导标记和防呆标记 外观装饰及标记是否满足模具工艺及成型工艺的要求 零件离板边是否有合理的距离(>1.5MM) PCB板是否有合理的定位,固定 PCB板与外壳是否有合理的距离(分板筋位置至少有0.4MM间隙) PCB板强度是否足够,装配后是否容易变形 MMC卡/SD卡插拔防呆设计 摄像头/闪光灯的定位固定是否合理 摄像头工作(取景)角度内是否有干涉问题(与玻璃丝印位置等)
堆叠检讨(CHECKLIST)

3、虚拟按键灯到按键的距离不宜太近,以免亮度分布不均 1、光感到tp距离是否足够?是否有做泡棉(套)的空间? 1、要选用有压缩保护的弹片,以确保不被过量压缩 2、各馈点的距离不宜过大,中心距常做5mm,焊盘大小参考顶针和弹片封装定 3、尽可能不用高度1mm以下的弹片和顶针,高度太小预压值也会偏小,有接触不良的隐患,如不 能避免,可以更改主板厚度或调整板型结构、天线定位方式 1、堆叠上是否有fpc焊接位置的丝印线?/喇叭密封薄棉丝印线?/电池pin脚定义等丝印线? 2、是否预留了足够的接地露铜?在有外插接口的地方尽可能露铜 3、主板上须预留定位孔。以免设计公司利用骨位在板边对主板进行定位,由于邮票孔和制造误 差的存在,会使得侧键的手感不好(侧键的行程0.2或0.3) 4、副板的厚度是否合理?厚度一般不要小于0.5,以免贴片时形变 5、a、fpc焊盘长度不能少于1.5,焊盘须留0.5mm的排锡空间,焊盘宽度不小于0.7;b、在fpc的 焊接的排锡方向须预留3毫米空间,以免焊接时电烙铁碰到其它的原件 6、主板上不得两面都放置较大贴片元件,避免贴片掉下 7、要预留螺丝孔位置,如果整机是从后壳方向锁紧螺丝的,前后壳螺丝孔的位置则必须在电池 盖的投影区域内 1、屏蔽罩的不宜过大,否则容易变形,否则易变性,如由于实际情况不能更改,可以做成屏蔽 框+屏蔽罩的结构 2、屏蔽罩需要做散热孔,基带和射频屏蔽罩尽可能多开孔 3、屏蔽罩的几何中心直径6毫米内不要开孔,以方便贴片时机械手吸起屏蔽罩 4、由于不锈钢不能上锡,屏蔽框不能用不锈钢材料
1115为5毫升15为5毫升1620为67毫升3做双喇叭时两个喇叭须一样大且距离尽可能的远4喇叭尽可能远离mic距离尽可能大于10mm5喇叭下方须露铜接地6喇叭要远离地磁等传感器7弹片的喇叭尽量靠近螺丝孔1马达不能放在刀片电池连接器附近离指南针等芯片要尽可能的远2圆形扁马达的金属外壳需要接地3马达的固定必须可靠且尽可能放在整机的四个角落4转子到周围器件的距离须大于05mm1前音腔体必须密封2尽可能选用15061005等音量较小3听筒到屏的距离至少07mm弹片听筒本体到主板留03的间隙4弹片听筒的馈点的长度不小于本体的宽度馈点的宽度不小于255听筒的下方需接地13d堆叠图上的mic须附上硅胶套2mic到喇叭的位置不小于10且尽可能靠近螺丝柱3须远离2g3g天线如不能避免需更换防干扰功能的mic4做双个mic时两个mic的距离尽量的远其中一个常放在整机后面的中上部1拔插卡须要顺畅pushpush卡座须根据行程确保容易取卡2如果在出卡方向上有电池的器件须保证卡到电池等器件有05的间隙3须远离射频天线尽可能有10mm距离以免掉卡4如选用贴板的sim座在sim卡的出卡方向上的3mm内不能放原件04020201可放1电池连接器到电池须留05的间隙2须标示电池定义的01确保耳机座usbhdmidc放置的位置以免公头和外壳干涉引起接触不良2各连接器近可能的使用插脚的物料以免贴片器件因受力不当掉铜皮3固定在耳机座等上fpc器件须做好定位4堆叠图中的各公头须为通用型的5各接口的pin脚数量应满足硬件的需要6各连接器摆放的位置尽可能不要放在整机的4个角落1冲压件的披锋要避开pfc等排线以微跌免割断排线2sus304拉伸的深度尽可能不超过1mm拉伸的面尽可能是一个完整的面1电池的大小和放置位置不得影响天线2该外形尺寸的电池是否有给电池厂评估电量3电池的金手指须做下沉下沉054需要标示电池的pin脚定义1fpc的焊盘长度不得小于12x072fpc的宽度需要满足pin数的需求线宽最小01线边距最小013fpc的外形尽可能方便拼版以免在拼版时浪费4对于较大长的fpc需要做较大的接地
手机结构设计检查表

1
以内。螺丝柱加支撑筋30 MM个,螺丝间距螺丝布置是否合理?BOSS螺丝柱侧边4-6条(支撑筋条。上下压住。注意缩水,容易折断。
2
牙以上.螺丝种类尽量少。颜色区分螺丝1.4,缩合长度5
3
,H2.5牙,保证有效锁合53.4*内径1.1自攻牙:P0.5自攻螺丝柱:外径1.4H1.5牙,保证有效锁合53.8*内径2.1机械牙:P0.31.4铜螺母螺丝柱:外径,保,机械牙:P0.3内径2.4否则易裂开)*1.11.4镁合金螺丝柱:外径2.5(最小H1.5证有效锁合5牙
0.2向间隙Z
筋条
1
0.5-0.6 0.8,电池盖筋条筋厚
拔模角
1
外观面,配合面等必须拔模。
2
°,电池仓33°,反止口°,壳体内表面1.5°,止口外观面拔模3°,最小2.5°,镁合金屏框3°平行拔模,最小0.75°,前壳LENS槽1.5°,按键和壳体11°,°,镁合金电池仓2°,镁合金按键处0.5
3
1.1.结构堆叠详细设计checklist
结构堆叠设计CHECKLIST(设计要点,红色为必检)
项目名称
日期
检查清单填写要求:1、“Y,N,N/A”栏目的填写:2、“对应措施的举证/权衡考虑因素”栏目的填写:
1.1 Yes表示考虑并遵循了该项要求;2.1当标记“Yes”表示考虑并遵循了该项要求;
1.2 No.表示未考虑或未遵循该项要求;2.2当标记“No”表示未遵循该项要求时应填写原因或权衡因素;
3
0.2内部避让间隙
3
按键最多偏心0.2,否则手感不好。
4
按键四周是否都有支撑,会不会歪斜。
1°0.5-2.0°。标准拔模角其他
柱定位设计
流程规划评审Checklist

流程管理部门
时间:
评审项目
序号
评审内容
评审标准
权重
得分
扣分原因
备注
存在性
1
所描述的问题是否确实存在
前期调研确实存在问题,在运营中出现此问题或者得到反馈需要解决此问题,相应的流程规划则确实存在;
如果只是少数或者偶然出现的问题,则需要持续关注继续观察,当达到标准1时再重新进行规划及评审;
解决方案必须包含问题为什么会发生,是否还会再次产生,这种问题是否会导致其它的问题,这个问题是否侧面反映了其他的潜在问题,怎样避免这些问题,本次的解决方案有哪些经验积累等等类似的思考等。
20
4
所规划的流程目标是否可达成
流程目标在解决存在问题的基础下,既不能要求过高也不能要求太低,更不能与其他目标重复;
10
合计:
100
评审人:
评审结果
(1)91-100分:批准;
(2)81-90分:带修改建议的批准;
(3)60-80分:驳回修改;
(4)60分以下或不符合评审内容1:不需要;
如果确实不存在则中断规划评审,结束流程规划。
20
2
是否把握到了问题的关键核心
对问题的来源,定义,描述,分析及初步判断是否清晰明确;
对反馈问题影响面和严重性进行分析,判断其类别和性质。
20
有效性
3
所描述的解决方案是否能有效地解决相关问题
解决方案必须是客观的,理性的分析,尽可能掌握问题的实质,把握到每个细节要素;
规划的流程目标必须有很强的执行性,如果没有很强的执行性则需重新规划流程的目标及考核部分;
10
及时性
5
所描述的流程计划是否能及时解决相关问题
UI评审checklist、ID评审检查表

玻璃材质的TP,开孔的宽度或直径要大于1.2MM,且孔边缘距离外形边缘须2.8MM以上
5
type-c,tf卡,hdmi的位置要求与堆叠一致;
6
评估侧键与主板SWITCH或DOME的位置是否对正,如果因ID限制,按键偏心Z向需在0.2mm以内;XY方向不能偏心;
7
外观曲面评估
1
外观分型面角度小于45度时,要求分型位置有0.3mm以上直伸边或者接近直伸边,避免分型面锐边喷油锯齿和跌落壳裂等;
4
5
检查ID曲面 是否有足够的空间来满足MD设计,壳体强度是否足够: (包括LCM、camera、speaker&receiver、motor、hinge(FPC)、connector、mic、battery、audio jack、keypad、sim card、I/O、side key、SD card、pen、等);
2
出模角度检查,不同的外观纹面要求不同的拔模角度,一般不能小于3度,免喷涂的一般要求5度以上;
4
type-c,tf卡,hdmi孔等开孔是否满足设计要求;
5
防水,散热要求
6
按键/电源键突出高度是否足够,是否会影响手感;
7
金属装饰件应避免尖角;
8
对于喷涂的前壳,顶面不能是尖角,至少留0.2的直伸位,防止耐磨测试不过;
整机尺寸
1
尺寸Size(LxWxH) 是否与产品定义一致;
1
检查各零件工艺的量产可行性和可靠性,特殊工艺或颜色等需提前供应商参与评估并提供相关报告;
2
检查各零件工艺(金属装饰件,电镀件,及其它)对ESD,RF的影响;
3
检查各零件的工艺对结构设计的可行性;
4
- 1、下载文档前请自行甄别文档内容的完整性,平台不提供额外的编辑、内容补充、找答案等附加服务。
- 2、"仅部分预览"的文档,不可在线预览部分如存在完整性等问题,可反馈申请退款(可完整预览的文档不适用该条件!)。
- 3、如文档侵犯您的权益,请联系客服反馈,我们会尽快为您处理(人工客服工作时间:9:00-18:30)。
结构工程师
确认与对策1
新项目预堆叠规划评审查检表
7
马 达
马达尽量用柱状弹片式,露铜设计确认
马达焊线式焊盘及焊接工艺确认
MIC远离天线区域和天线溃点
MIC位置是否影响送话质量
马达是否通用件,3D和规格书是否一致
马达工作高度确认
6MIC MIC规格确认,接触式&焊接式&贴片式MIC焊盘设计确认
喇叭后音腔体积及密封性确认
5听筒听筒是否通用件(标准部品),3D图和规格书是否一致听筒规格确认,尽量选用外形尺寸大些的
听筒尽量用弹片式,露铜设计确认
听筒焊线式焊盘及焊接工艺确认
听筒工作高度确认
喇叭尽量用弹片式,露铜设计确认
喇叭焊线式焊盘及焊接工艺确认
喇叭工作高度确认
Camera摆放角度与屏位置成像是否OK
4喇 叭喇叭是否通用件(标准部品),3D图和规格书是否一致喇叭规格确认,是否能满足产品对音效的要求
喇叭是否考虑兼容不同规格设计(多焊盘)
3摄像头Camera是否通用件,3D和规格书是否一致Camera定位结构设计确认
Camera-FPC连接器规格及工作高度确认
2LCM
(主屏、
副屏)
LCM规格是否通用件,3D和规格书是否一致
LCM定位柱和定位孔确认
Camera-FPC焊接工艺及定位孔确认
LCM 3D图上 AA/VA区域确认
OLED规格确认
OLED连接方式确认
LCM-FPC连接器规格及工作高度确认
LCM-FPC焊接工艺及定位孔确认
LCM距离主板要留0.2以上间隙
项目型号评审日期
新项目预堆叠规划评审查检表
序号主板堆叠点检项目备注
堆叠部分
Layout整体布局layout是否好走线
16RF 测试座RF 测试座要尽量靠近天线馈点15电池连接器
电池连接器是否通用件
结构是否可靠,是否带定位机构加强连接强度
电池连接器要标明弹片工作高度和正负极电池连接器尽量远离天线区域
电池连接器本体离电池的距离03~0.4
14电 池电池规格确认,优先通用NOKIA型号
其次优先通用公司内部已有型号
容量配置是否合理
13PCB 主板螺钉孔径设计确认
主板预留接地位置是否合理
PCB 焊盘上人工焊锡需在3D 中体现
主PCB板厚度T1.05,大板尽量禁用T0.8
主板板形尽量工整,考虑共板设计
主板螺钉孔分布是否合理
USB 插头是否装配好
PCB 邮票孔在3D 中体现
12DC 座 /
耳机座DC-Jack/耳机座是否通用件
DC-Jack/耳机座工作高度确认DC-Jack/耳机座露铜设计确认
11USB USB是否通用件,尽量兼容Nokia
USB 规格是否符合国家标准
USB 焊盘及定位孔设计可靠性确认
USB 位置PCB 槽工艺孔确认
DC-Jack/耳机座插头是否装配
10T-Flash 卡 座
T-flash卡座是否通用件
尽量采用抽拉式T 卡座,非翻盖式
T-flash卡座取卡行程和取卡抠手位是否够
T-flash卡到电池的距离为0.5
9SIM卡 座SIM卡座 是否通用件
尽量采用抽拉式带横梁SIM 卡座,非翻盖式
SIM卡座取卡行程和取卡抠手位是否够
SIM卡座与天线区域的距离尽可能远,防掉卡马达要远离天线,焊盘也要远离天线
8TP 连接器主板是否带纯平TP 功能
TP 连接器规格确认
TP 连接方式--可靠性及易组装性确认
马 达
马达¢8.0圆形规格尽可能不选用
28公板测试对于公板,射频测试结果如何对于公板,基带测试结果如何对于公板,场测测试结果如何
27新部品是否有新部品需导入
新部品厂商确认
新部品导入验证测试确认
26Hall Hall中心要与磁铁中心对齐Hall位置确认
25Switch 侧键尽量采用Switch开关
侧键Switch触点凸出PCB板边0.50以上
24FPC FPC折弯形状是否合理
主板上FPC焊盘距离板边至少保证1.5mm以上
侧键FPC焊接及组装工艺确认
FPC焊盘上人工焊锡需在3D中体现
23LED灯LED规格确认
按键LED是否采用侧发光灯按键LED灯分布是否合理
22Dome Dome 形状规格-尽量用φ5的Dome
Dome铜箔距离板边至少1.0mm
主板有没有做Dome的定位孔
屏蔽框/罩的结构配合设计确认
单极双频天线高度≥4.5mm, 面积≥450mm2天线周边环境是否OK
19BT 天线BT 天线方式确认
BT 天线要远离GSM天线馈点
BT 天线接触方式(弹片、焊接、触针)确认
16RF 测试
座RF测试座的位置尽量不要影响后音腔空间设计
CPU/Flash等器件是否存在因受外力导致断路的隐患
18GSM天
线
确定GSM天线形式,是PIFA天线,还是monopole单极
天线,面积和高度是否足够
PIFA双频天线高度≥6mm, 面积≥500mm2
GSM天线接触方式(弹片、焊接、触针)确认
17屏蔽框/
屏蔽罩
屏蔽框/罩尽量公用-图纸需标明公用型号
屏蔽框/罩高度不得低于1.7mm,要注意SMT吸盘区域
屏蔽框/罩:两件或一件式设计评估。