表面残余应力分析
压痕法残余应力测试
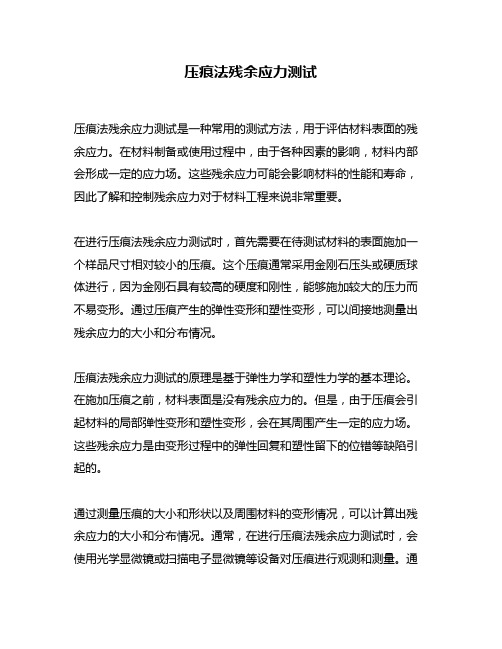
压痕法残余应力测试压痕法残余应力测试是一种常用的测试方法,用于评估材料表面的残余应力。
在材料制备或使用过程中,由于各种因素的影响,材料内部会形成一定的应力场。
这些残余应力可能会影响材料的性能和寿命,因此了解和控制残余应力对于材料工程来说非常重要。
在进行压痕法残余应力测试时,首先需要在待测试材料的表面施加一个样品尺寸相对较小的压痕。
这个压痕通常采用金刚石压头或硬质球体进行,因为金刚石具有较高的硬度和刚性,能够施加较大的压力而不易变形。
通过压痕产生的弹性变形和塑性变形,可以间接地测量出残余应力的大小和分布情况。
压痕法残余应力测试的原理是基于弹性力学和塑性力学的基本理论。
在施加压痕之前,材料表面是没有残余应力的。
但是,由于压痕会引起材料的局部弹性变形和塑性变形,会在其周围产生一定的应力场。
这些残余应力是由变形过程中的弹性回复和塑性留下的位错等缺陷引起的。
通过测量压痕的大小和形状以及周围材料的变形情况,可以计算出残余应力的大小和分布情况。
通常,在进行压痕法残余应力测试时,会使用光学显微镜或扫描电子显微镜等设备对压痕进行观测和测量。
通过分析压痕的几何形状参数,结合合适的数学模型和理论,可以得到残余应力的精确值。
压痕法残余应力测试在材料科学和工程的许多领域中得到了广泛的应用。
它可以用于评估不同材料的制备工艺对残余应力的影响,以及不同材料在使用过程中的变化情况。
压痕法残余应力测试还可以用于研究材料的应力分布和应力引起的变形行为,进一步理解材料的力学性能和行为规律。
总结回顾起来,压痕法残余应力测试是一种基于压痕的方法,用于评估材料表面的残余应力。
通过测量压痕的大小和形状,以及分析周围材料的变形情况,可以计算出残余应力的大小和分布情况。
这项测试在材料科学和工程领域具有广泛的应用,对于了解和控制材料的残余应力非常重要。
在本次的文章中,我们介绍了压痕法残余应力测试的基本原理和测试方法。
通过这项测试,可以评估材料表面的残余应力,进一步了解材料的性能和寿命。
硬态切削表面残余应力分析研究
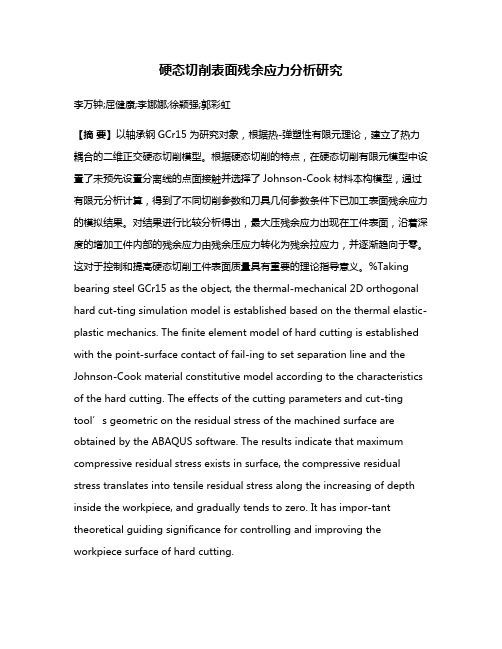
硬态切削表面残余应力分析研究李万钟;屈健康;李娜娜;徐颖强;郭彩虹【摘要】以轴承钢GCr15为研究对象,根据热-弹塑性有限元理论,建立了热力耦合的二维正交硬态切削模型。
根据硬态切削的特点,在硬态切削有限元模型中设置了未预先设置分离线的点面接触并选择了Johnson-Cook材料本构模型,通过有限元分析计算,得到了不同切削参数和刀具几何参数条件下已加工表面残余应力的模拟结果。
对结果进行比较分析得出,最大压残余应力出现在工件表面,沿着深度的增加工件内部的残余应力由残余压应力转化为残余拉应力,并逐渐趋向于零。
这对于控制和提高硬态切削工件表面质量具有重要的理论指导意义。
%Taking bearing steel GCr15 as the object, the thermal-mechanical 2D orthogonal hard cut-ting simulation model is established based on the thermal elastic-plastic mechanics. The finite element model of hard cutting is established with the point-surface contact of fail-ing to set separation line and the Johnson-Cook material constitutive model according to the characteristics of the hard cutting. The effects of the cutting parameters and cut-ting tool’s geometric on the residual stress of the machined surface are obtained by the ABAQUS software. The results indicate that maximum compressive residual stress exists in surface, the compressive residual stress translates into tensile residual stress along the increasing of depth inside the workpiece, and gradually tends to zero. It has impor-tant theoretical guiding significance for controlling and improving the workpiece surface of hard cutting.【期刊名称】《航空制造技术》【年(卷),期】2015(000)006【总页数】5页(P64-68)【关键词】硬态切削;热力耦合;温度场;残余应力;有限元【作者】李万钟;屈健康;李娜娜;徐颖强;郭彩虹【作者单位】西北工业大学机电学院;西北工业大学机电学院;西北工业大学机电学院;西北工业大学机电学院;中航光电科技股份有限公司【正文语种】中文随着切削技术的发展,尤其是超硬刀具材料陶瓷、聚晶立方氮化硼(PCBN)的出现,使得精密切削加工淬硬钢成为可能,产生了“以车带磨”的硬态切削加工技术。
x射线衍射测定表面残余应力的基本原理

x射线衍射测定表面残余应力的基本原理
X射线衍射是一种常用的非破坏性分析方法,可用于测定材料内部的残余应力。
其基本原理是利用X射线在晶体中发生衍射现象来获取有关晶体结构的信息。
当入射X射线照射到晶体表面时,其中的晶粒会发生散射。
这个散射过程中,
X射线会与晶体中的原子相互作用,导致X射线改变方向。
这种改变方向的现象
称为衍射,衍射的角度和晶体的结构以及晶格参数密切相关。
X射线衍射测定表面残余应力的原理是利用晶体中晶面的平面间距与入射X射线的衍射角度之间的关系。
当晶体受到残余应力的影响时,晶面的平面间距会发生改变。
这种改变会导致入射X射线的衍射角度产生相应的偏移。
通过测量衍射角
度的改变,可以反推出材料中的残余应力大小和分布情况。
为了获得准确的残余应力测量结果,需要选择合适的晶体材料和衍射仪器。
常
用的晶体材料包括钼、铜和钨等。
衍射仪器通常采用X射线源、衍射仪器和探测
器组成,可以实现对入射X射线的发射和检测。
测量过程中,需要准确控制入射
角度和衍射角度,并进行有效的数据分析和处理。
X射线衍射测定表面残余应力的基本原理可应用于材料工程、金属加工、航空
航天等领域,有助于了解材料的力学性能和结构变化。
通过这种非破坏性的分析方法,可以提高材料的质量控制和设计优化,从而提升产品的可靠性和性能。
钢结构焊接中的残余应力分析方法
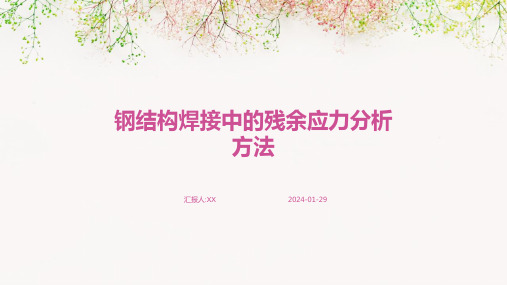
能够兼顾计算精度和计算效率,适用于大型复杂 焊接结构的残余应力分析。
03
钢结构焊接中的残余应力测量技术
X射线衍射法
01
02
03
04
原理
利用X射线在晶体中的衍射现 象,通过测量衍射角的变化来 计算残余应力。
优点
非破坏性测量,对试样无损伤 ,可测量小区域和复杂形状的 构件。
缺点
设备昂贵,操作复杂,需要专 业人员进行操作和分析。
将数值模拟得到的残余应力分布结果与实验结果 进行对比分析,验证模拟的准确性。
模拟结果优化
针对误差来源进行模拟结果的优化和改进,提高 数值模拟的精度和可靠性。
ABCD
误差来源分析
分析数值模拟中可能存在的误差来源,如模型简 化、材料参数不准确等,并提出改进措施。
工程应用探讨
探讨数值模拟在钢结构焊接残余应力分析中的工 程应用前景和局限性。
原理
利用超声波在材料中的传播速 度与应力之间的关系,通过测 量超声波传播速度的变化来计
算残余应力。
优点
设备相对简单,操作方便,可 实现在线测量。
缺点
对材料表面粗糙度和温度等因 素敏感,测量结果易受干扰。
应用范围
适用于各种金属材料和构件的 表面残余应力测量。
应变片法
原理
在构件表面粘贴应变片,通过测量应 变片电阻值的变化来计算残余应力。
求解过程
采用合适的数值方法求解边界积分方 程,得到焊接过程中的温度场和应力
场分布。
材料本构关系与热源模拟
定义材料的本构关系和焊接热源模型 ,以模拟焊接过程中的热力学行为。
结果分析与验证
对求解结果进行可视化处理和数据分 析,评估残余应力的分布和影响,并 与实验结果进行对比验证。
硬质合金表面加工 残余应力
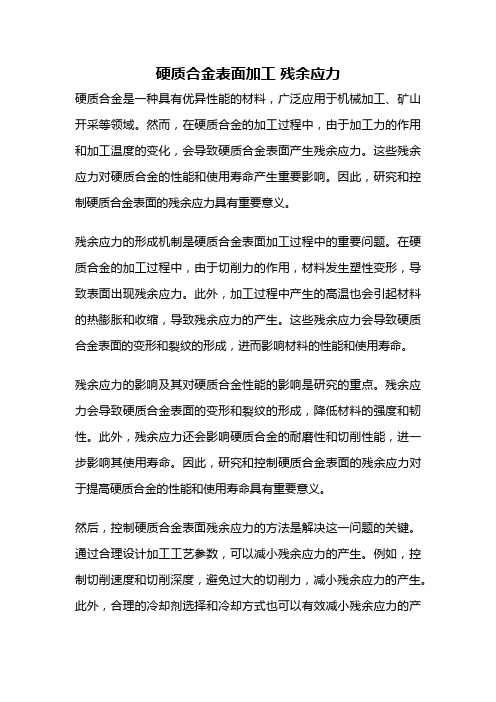
硬质合金表面加工残余应力硬质合金是一种具有优异性能的材料,广泛应用于机械加工、矿山开采等领域。
然而,在硬质合金的加工过程中,由于加工力的作用和加工温度的变化,会导致硬质合金表面产生残余应力。
这些残余应力对硬质合金的性能和使用寿命产生重要影响。
因此,研究和控制硬质合金表面的残余应力具有重要意义。
残余应力的形成机制是硬质合金表面加工过程中的重要问题。
在硬质合金的加工过程中,由于切削力的作用,材料发生塑性变形,导致表面出现残余应力。
此外,加工过程中产生的高温也会引起材料的热膨胀和收缩,导致残余应力的产生。
这些残余应力会导致硬质合金表面的变形和裂纹的形成,进而影响材料的性能和使用寿命。
残余应力的影响及其对硬质合金性能的影响是研究的重点。
残余应力会导致硬质合金表面的变形和裂纹的形成,降低材料的强度和韧性。
此外,残余应力还会影响硬质合金的耐磨性和切削性能,进一步影响其使用寿命。
因此,研究和控制硬质合金表面的残余应力对于提高硬质合金的性能和使用寿命具有重要意义。
然后,控制硬质合金表面残余应力的方法是解决这一问题的关键。
通过合理设计加工工艺参数,可以减小残余应力的产生。
例如,控制切削速度和切削深度,避免过大的切削力,减小残余应力的产生。
此外,合理的冷却剂选择和冷却方式也可以有效减小残余应力的产生。
通过对加工工艺参数的优化和改进,可以降低硬质合金表面的残余应力,提高材料的性能和使用寿命。
研究硬质合金表面残余应力的发展趋势是未来研究的方向。
随着科学技术的不断进步,研究硬质合金表面残余应力的技术也在不断发展。
例如,利用数值模拟方法可以模拟硬质合金表面加工过程中的残余应力分布和变化规律,为优化加工工艺提供理论依据。
此外,利用先进的材料表征技术可以实时监测和评估硬质合金表面的残余应力,为加工工艺的控制和改进提供指导。
硬质合金表面加工残余应力是一个重要的研究课题。
研究和控制硬质合金表面的残余应力对于提高材料的性能和使用寿命具有重要意义。
电镀的残余应力-概述说明以及解释
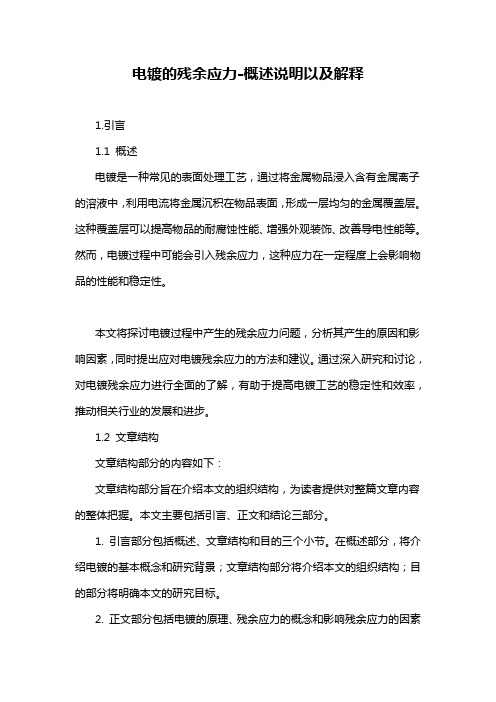
电镀的残余应力-概述说明以及解释1.引言1.1 概述电镀是一种常见的表面处理工艺,通过将金属物品浸入含有金属离子的溶液中,利用电流将金属沉积在物品表面,形成一层均匀的金属覆盖层。
这种覆盖层可以提高物品的耐腐蚀性能、增强外观装饰、改善导电性能等。
然而,电镀过程中可能会引入残余应力,这种应力在一定程度上会影响物品的性能和稳定性。
本文将探讨电镀过程中产生的残余应力问题,分析其产生的原因和影响因素,同时提出应对电镀残余应力的方法和建议。
通过深入研究和讨论,对电镀残余应力进行全面的了解,有助于提高电镀工艺的稳定性和效率,推动相关行业的发展和进步。
1.2 文章结构文章结构部分的内容如下:文章结构部分旨在介绍本文的组织结构,为读者提供对整篇文章内容的整体把握。
本文主要包括引言、正文和结论三部分。
1. 引言部分包括概述、文章结构和目的三个小节。
在概述部分,将介绍电镀的基本概念和研究背景;文章结构部分将介绍本文的组织结构;目的部分将明确本文的研究目标。
2. 正文部分包括电镀的原理、残余应力的概念和影响残余应力的因素三个小节。
将详细介绍电镀的工作原理,残余应力的概念以及影响残余应力的因素。
3. 结论部分包括总结电镀残余应力的重要性、应对电镀残余应力的方法和展望未来研究方向三个小节。
将总结本文的研究成果和对电镀残余应力的重要性进行归纳,提出应对电镀残余应力的方法,并展望未来研究的方向。
通过以上结构的安排,读者可以清晰地了解本文的内容和组织,方便其在阅读过程中更好地理解和把握文章的主要观点和结论。
1.3 目的文章的目的是探讨电镀过程中产生的残余应力对零件性能和质量的影响,以及如何有效应对这种残余应力。
通过深入分析电镀残余应力的形成机制、影响因素和表现形式,可以更好地理解电镀工艺中的问题,并提出相关的解决方法。
此外,通过对电镀残余应力的研究,可以为未来的电镀工艺改进和优化提供参考,推动该领域的发展。
因此,本文旨在从理论和实践的角度探讨电镀残余应力的问题,为相关研究和应用提供有益的参考和指导。
材料表面残余应力
材料表面残余应力
材料表面残余应力是指材料表面的应力状态,它不仅受到外界作用力的影响,还受到材料内部变形和温度变化等因素的影响。
通常情况下,材料的表面会存在着残余应力。
这种残余应力在材料使用过程中,可能会对材料的性能和寿命产生影响。
表面残余应力的产生原因比较多,主要包括材料的制备、加工、焊接等过程中受到的变形、温度变化等因素。
一般来说,材料经过加工或焊接等工艺过程中,会产生一定的塑性变形,从而导致表面残余应力的产生。
此外,材料在高温环境下的热膨胀也会导致表面残余应力的产生。
表面残余应力对材料的影响主要表现在以下几个方面。
首先,它可能会导致材料的疲劳寿命缩短,从而影响材料的使用寿命。
其次,它还可能会导致材料的强度和韧性降低,从而影响材料的性能。
此外,表面残余应力还可能会导致材料产生形变和裂纹等缺陷,从而影响材料的质量。
为了减小材料表面残余应力的影响,可以采取一些措施。
例如,在材料制备、加工和焊接等过程中,可以采用适当的工艺措施,减小塑性变形的程度,从而减小表面残余应力的产生。
此外,还可以采用热处理等方法,对材料进行退火或正火处理,从而消除表面残余应力。
- 1 -。
车铣加工表面层残余应力的研究
金属切 削加工是 一个伴 随着高温 、 高压 、 高 应变率的塑性大变形过程 ,在已加工表面 上往 往存在着较大的残余应力 ,已加 工表面层残余 应力对零件的使用性能有着重要的影响 。残余 拉应力会降低 ̄  ̄ T 的疲劳强度 , 时甚 至在切 - - 4 有 削加工后 , 会使零件表 面产生微裂纹 : 面残余压 应力却能提高零件的疲劳强度。当各部 分的残 余应力 山于分布小均 匀, 还会发生 ]件 变形 , 二 影 响工件 的形状精度 和尺寸精度。因此 , 究加工 研 表面层残余应力 ,对保证零件表面质量有重要 意义 。
作用去 除后 ,整个物体山于 内部残余应力 的作
用将发生形变。
1 . 2残余应力的分类 第一类残余应力 , 标记 为 。它在材料较 的热弹塑性 问题 。 棚 图所示1 。 大范 围内或许多 品粒 范围 内存在 并保持 平衡 , 2单 因素实验方案 3试验分析结论 在多个连续品体范围内保持常数 , 它的大小 、 方 21实验 目的 . 为 了深人研究铣 刀转速 和刀具轴 向进  ̄t AJ t 向和性 质可 用通 常 的物 理或 机 械方法 进行 测 通常 山于切削加工产生的残余应 力是指宏 对表 面层残余 应力 的影响规律 ,我们设计 了单 量。如果 第—类残余应力所 产生 的力 或力矩 的 观残余应力 , 即第一类残余应力。 也 本文从影 响 因素试验方案 , 运用金属切削原理的知识 , 详细 平衡状 态遭 到破坏 , 将导致构件宏观 尺寸的变 车铣加工工件表 面残余应力 的两个主要因素( 铣 地分析 了试验结果 , 中得出以下结论 : 从 化。通常 山于切 削加工产生 的残余应 力足指 宏 刀转速 n和轴 向进给量 D出发 , 单 因素 实 采用 1 ) 金属的热塑性变形作用对 车铣加工工件 观残余应力 。 根据加工残余应力 的性质小同 , 可 验方法 , 分别改变铣刀 转速 n和轴向进给量 £ 表面残余应力 的产生和变化大小 的影响起主导 , 分 为残余拉应力和残余压应力 ,应 力的大小 随 进行单因素正交车铣 6 # 5 钢实验 ,研究车铣加 作用 ,里层 金属的弹性恢 复和表层 金属 在切削 表层的深度面变化 。 工的切削用量 与工件表面残余应力的关 系。 热作用下发生 的相变是次要作用。 第二类残余应力称 为微 观结构应力 (,0 s- 一 t . 2 . 验 条 件 2实 2 削速 度从 15 mr n增 大 到 17 , 1切 2. /i 6 a 5r n tr r s标 记为 Il它存在于品粒 尺度 内且 u se) l a ts,  ̄I Fo r 文验机 床 : 数控车铣加 T中心 M Z K I — rn工件表 面残余应力 为拉应力但增大趋 势小 A A N a , i 0 保持平衡 , 在一个或几个 品粒 的部分 范围内保 TEGEX2 0Y。 明显 , 1 7 / i 从 5 mm n增大 到 1 8 mm n 表 面残 8A / i, 持均匀。如果第 二类残余应力平衡状 态得 到改 工 件 材料 : ,铁 素 体 ,其 硬 度 为 余 拉 应力 急剧增 大 ,但从 18 mmn 大到 6 钢 5 8. /i增 4 变 , 会造成宏观尺寸的变化 。 也 H Cl R 2 ,屈服强度 o= 8 M a L7 4 P ,抗拉强 度 盯】 29 mrn , I 1. /i时 表面残余拉应力急剧下降。 = 8 n 增大 第 三类残 余应力 称品 内亚 结构 应力(u— 9 0 a S b 8 MP ,延 伸率 6 9 = %,断 面收缩 率 _ 5 轴 向进给量 f, 3% a 对车铣 加工工 件的表面残余应 sutr t s, t c a ses标记为 “ r ul r ) 。它是在 品粒若 干 3 %, 5 化学成分见表 1 。 力影响显著。 随着轴向进给量无的增大 , 表面残 个原子范 围内存在并在 品粒 的小部分 内保持平 表 1 试验铜 的化 学成分噘 量分数) 余应力逐渐减 小。 衡, 在品体亚结构范 围内大小小均匀。 第 类残 3 刀转 速 n 为 3 0 r i  ̄ 1 8 mm n ) 铣 c 0 0/ n m ( 8. /i 4 ) 附一近是切削振动的固有一频率 ,为了工 件得 余应力平衡状态的破坏 ,小会引起宏观尺寸 的 变化。 到较好的残余应力状态 ,车铣 切削用 量应 避开 在大多数情况下 ,宏观残余应力与微观残 刀具 : 可转位立铣刀 , 直径 2 m 齿数 0 m, B 为 3 0 r n a 0 mm/的组合 。 e 0 0/ ,f 为 . r mi 8 余应力总是同时存在的 ,产生 第一类 残余应力 Z 2刀片为 Wii 公 司的 XD 0 0 0 =, da HT 9 3 8 4 比车削加 工 , 铣加工 能够 在更高 的 1 对 车 的加工过程 必须伴 随第 二 、 三类残余 应力的 第 T 5 5型 MT C N 5l — VD- i — 2 T N AI03涂 层 刀 铣 刀转速 n 和更大的轴 向进 给量 f的切削条 c a 产生。 片。 件下, 使工件得 到表 面残余压应力 以提高工件 1 - 3残余应力 的产生机理 切削条件 : 正交顺铣 , 乳化液冷却 的表面质量 。 目前 , 于残余应力 的产 生机 理 , 关 从理论 I } = 实验测量仪器 : 兰 Pn ye 公 司 , 荷 aa ta l i l 多晶 参 考 文献 定量分析还存在 困难 。下面仅从 已加工表面彤 X射线衍射仪 P 00 X射线 C K W34 , ua 【 晋烧 , l 】 诩舟. 车铣复合 开创未 来一本 刊主编刘 成过程的角度分析残余应力的产生机理。 照射 , 衍射品面(1) 于 0 5 n 衍射角 柱 与奥地利 WF 2 , 1等 . 4 m, 1 L车铣 技术公 司首席代表 李锋 1. .1机械应力引起的残余 应力 3 为 2 = 5 _ ,残余应 力的测试采用 0 -5法测 博士对话航 空制造技术. 0 .4 4 — 4 0 16 。 4  ̄ o - 4 2 7 ( 2 3 0 1 工件装夹时 , 如果夹紧力过大 , 将会使 件 量 。 贾春德 , 姜增辉. 车铣原 理. 北京: 国防土业 出版 2 035 6 发生塑性变形 , 从面使工件产生残余应力。 切削 金相显微 镜 : L MP S O Y U 公司 , 倒置 型金相 社 .0 .- 过程 中,刀刃前方 的工件材料受 到前 刀面的挤 显微镜 GX 7 。 一 1 【z素 玉扁 速铣 削加 土表 而质量的研 究. 东 3 1 【 山 压 , 面使将成 为已加工表 面层 的金属 , 削 从 在切 23实验方 案 - 大学: 博士学位论文1 0 6 56 , 0 . - 2
铣削表面残余应力产生及分析
第57卷 第11期Vol. 57 No. 112019年11月November 2019农业装备与车辆工程AGRICULTURAL EQUIPMENT & VEHICLE ENGINEERINGdoi:10.3969/j.issn.1673-3142.2019.11.007铣削表面残余应力产生及分析王琰,胡天宇,赵中华(201620 上海市 上海工程技术大学 机械与汽车工程学院)[摘要]为了减少残余应力对铣削加工零件质量的影响,避免因零件失效导致农业机械或大型器械故障,对退火H13热作模具钢做铣削后,利用盲孔法对已加工表面进行残余应力测量,对测量结果采用田口法进行优化,最终得到最优铣削加工参数,减小切削加工产生的表面残余应力,提高加工零件表面质量。
[关键词] 铣削;残余应力;盲孔法;信噪比[中图分类号] TG50 [文献标识码] B [文章编号] 1673-3142(2019)11-0028-05Generation and Analysis of Residual Stress on Milling SurfaceWang Yan, Hu Tianyu, Zhao Zhonghua(Shanghai University of Engineering Science, Shanghai 201620, China)[Abstract] In order to reduce the influence of residual stress on the quality of milling machining parts and avoid the failure of agricultural machinery or large equipment caused by the failure of parts, the residual stress of the machined surface was measured by blind hole method after milling of annealed H13 hot work die steel. The measurement results were optimized by the Taguchi method, and the optimal milling parameters were obtained, which reduced the surface residual stress produced by cutting and improved the surface quality of the machined parts. [Key words] milling; residual stress; blind hole method; signal-to-noise ratio0 引言残余应力是指外部载荷去除后,一种以平衡状态残存在于物体内部的、固有应力域中的局部内应力[1-3]。
表面残余应力产生的主要原因
表面残余应力产生的主要原因表面残余应力是指物体表面上存在的一种内应力状态,这种应力是由于物体在制造或加工过程中受到了外力的作用而产生的。
表面残余应力的产生主要有以下几个原因。
温度梯度是导致表面残余应力产生的重要原因之一。
当物体在制造或加工过程中,不同部位的温度存在差异,导致物体表面的温度与内部的温度不一致。
由于物体的热膨胀系数不同,表面和内部产生了不同的变形,从而引起了表面残余应力的产生。
机械变形也是引起表面残余应力的重要因素。
在物体的制造或加工过程中,常常需要对物体进行弯曲、拉伸、压缩等机械变形操作。
这些变形会使物体的内部产生应力,由于物体的形状复杂或变形过程中受到限制,导致应力无法完全消除,从而在表面产生了残余应力。
材料的相变也会引起表面残余应力的产生。
在材料的制造或加工过程中,常常会发生相变现象,例如固态相变、液态相变等。
这些相变过程伴随着物体内部结构的变化,使得表面和内部的应力分布不一致,从而产生了表面残余应力。
再者,物体的形状设计和工艺参数选择也会对表面残余应力产生影响。
在物体的制造或加工过程中,设计和选择合适的形状和工艺参数可以减小表面残余应力的产生。
例如,在焊接过程中,选择合适的焊接接头形状和焊接参数,可以减小残余应力的产生。
材料的性质和组织结构也会对表面残余应力产生影响。
不同材料具有不同的力学性能和内部结构,这些因素会导致材料在制造或加工过程中产生不同的应力分布。
例如,金属材料具有较好的可塑性,可以通过塑性变形消除应力,而陶瓷材料则具有较差的可塑性,容易产生残余应力。
表面残余应力的产生主要是由于物体在制造或加工过程中受到了温度梯度、机械变形、材料相变、形状设计和工艺参数选择以及材料性质和组织结构等因素的影响。
了解和控制这些影响因素,可以有效减小表面残余应力的产生,提高物体的性能和可靠性。
- 1、下载文档前请自行甄别文档内容的完整性,平台不提供额外的编辑、内容补充、找答案等附加服务。
- 2、"仅部分预览"的文档,不可在线预览部分如存在完整性等问题,可反馈申请退款(可完整预览的文档不适用该条件!)。
- 3、如文档侵犯您的权益,请联系客服反馈,我们会尽快为您处理(人工客服工作时间:9:00-18:30)。
表面残余应力胡宏宇(浙江工业大学机械工程学院,浙江杭州 310032)摘要:残余应力主要是由构件内部不均匀的塑性变形引起的。
各种工程材料和构件在毛坯的制备、零件的加工、热处理和装配的过程中都会产生不同程度的残余应力。
残余应力因其直观性差和不易检测等因素往往被人们忽视。
残余应力严重影响构件的加工精度和尺寸稳定性、静强度、疲劳强度和腐蚀开裂。
特别是在承力件和转动件上,残余应力的存在易导致突发性破坏且后果往往十分严重。
因此,研究残余应力的产生机理、检测手段、消除方法以及残余应力对构件的影响[1]。
关键词:残余应力;切削变形;磁测法;喷丸强化;Surface residual stress(S chool of mechanical engineering,Zhejiang University of Technology,Hangzhou 310032,China)Abstract:Residual stress is mainly caused by the uneven plastic deformation of component. All kinds of engineering materials in the preparation of blank, parts and components processing, heat treatmentand assembly process will produce different degree of residual stress. Residual stress because of itsintuitive factors such as poor and difficult to detect is often neglected. Seriously affect the residualstress of component machining precision and dimension stability, static strength, fatigue strength andcorrosion cracking. Especially on the bearing and rotating parts, the existence of the residual stresscan lead to sudden destruction and the consequences are often very serious. Therefore, to study themechanism of residual stress, detection means, elimination method and the influence of residual stressof components。
Key words:Residual stress;machining deflection;magnetic method;Shot peening strengthening;前言随着现代制造技术的发展,大飞机、高铁、核设施等大型设备相继出现;这些设备具有高速、重载和长时间运行的特点,其零部件工作环境恶劣、复杂,且往往对安全性有着极其苛刻的要求,因而对这些设备的关键部件,如轴承、曲轴、传动轴的疲劳寿命和可靠性也有很高的要求,对它们的疲劳寿命预测和分析成为研究的重点.金属切削加工是一个伴随着高温、高压、高应率的塑性大变形过程, 在已加工表面上存在着相当大的残余应力; 同时又由于切削过程切削力和切削热作用及刀具与工件的摩擦等综合因素的影响, 使得零件内部初始的残余应力重新分布并与表面层残余应力耦合作用形成新的残余应力分布规律。
残余应力以平衡状态存在于物体内部, 是固有应力域中局部内应力的一种。
残余应力是一种不稳定的应力状态, 当物体受到外力作用时, 作用应力与残余应力相互作用, 使其某些局部呈现塑性变形, 截面内应力重新分配; 当外力作用去除后, 整个物体由于内部残余应力的作用将发生形变。
根据理论分析和实验研究的结果,工件的疲劳寿命和加工表面的残余应力状态有重要的关系:残余压应力能抑制工件的疲劳破坏,延长疲劳寿命;残余拉应力则相反,会加速疲劳破坏的出现[2].因此,了解和控制工件已加工表面的残余应力,使零件已加工表面呈现稳定而较大的压应力状态,已成为加工出高质量和高可靠性零件的关键.1 残余应力的定义1.1 残余应力的定义构件在制造过程中,将受到来自各种工艺等因素的作用与影响;当这些因素消失之后,若构件所受到的上述作用与影响不能随之而完全消失,仍有部分作用与影响残留在构件内,则这种残留的作用与影响称为残留应力或残余应力。
残余应力是当物体没有外部因素作用时,在物体内部保持平衡而存在的应力。
凡是没有外部作用,物体内部保持自相平衡的应力,称为物体的固有应力,或称为初应力,亦称为内应力。
残余应力是指在没有外力作用于物体时,物体内部保持平衡的应力。
在没有外力的作用下,物体内部保持平衡的应力称为固有应力,残余应力是固有应力的一种[3]。
1.2 残余应力的分类残余应力的存在状态是多种多样的, 随材料的性能、产生条件不同而不同, 分类的方法也不一致。
1925 年格·马辛、Mura T、达维金科夫H.H 分别提出了残余应力的界定方法。
根据残余应力的相互影响范围大小可将残余应力分为宏观残余应力(Macrresidual stress) 和微观残余应力(Micro residualstress) 。
1973 年德国学者E.Macherauch 又将宏观残余应力称为第一类残余应力, 将微观残余应力划归为第二类、第三类残余应力。
第一类残余应力称为宏观残余应力它在材料较大范围内或许多晶粒范围内存在并保持平衡, 在多个连续晶体范围内保持常数, 它的大小、方向和性质可用切削加工表面残余应力研究的现状与进展通常的物理或机械方法进行测量。
如果第一类残余应力所产生的力或力矩的平衡状态遭到破坏, 将导致构件宏观尺寸的变化。
通常由于切削加工产生的残余应力是指宏观残余应力。
根据加工残余应力的性质不同, 可分为残余拉应力和残余压应力, 应力的大小随表层的深度而变化。
第二类残余应力称为微观结构应力( Structurasstress) ,它存在于晶粒尺度内并且保持平衡, 在一个或几个晶粒的部分范围内保持均匀。
如果第二类残余应力平衡状态得到改变, 也会造成宏观尺寸的变化。
第三类残余应力称晶内亚结构应力( Substructural stress)标记为σrⅢ它是在晶粒若干个原子范围内存在并在晶粒的小部分内保持平衡,在晶体亚结构范围内大小不均匀。
第三类残余应力平衡状态的破坏, 不会引起宏观尺寸的变化。
在大多数情况下, 宏观残余应力与微观残余应力总是同时存在的, 产生第一类残余应力的加工过程必须伴随第二、第三类残余应力的产生。
2 切屑形成过程及变形区的划分2.1切削变形金属的切削过程与金属的挤压过程很相似。
金属材料受到刀具的作用以后,开始产生弹性变形;虽着刀具继续切入,金属内部的应力、应变继续加大,当达到材料的屈服点时,开始产生塑性变形,并使金属晶格产生滑移;刀具再继续前进,应力进而达到材料的断裂强度,便会产生挤裂。
2.2变形区的划分大量的实验和理论分析证明,塑性金属切削过程中切屑的形成过程就是切削层金属的变形过程。
切削层的金属变形大致划分为三个变形区:第一变形区(剪切滑移)、第二变形区(纤维化)、第三变形区(纤维化与加工硬化)。
图1 切削变形区2.3切屑的形成及变形特点第一变形区(近切削刃处切削层内产生的塑性变形区)金属的剪切滑移变形切削层受刀具的作用,经过第一变形区的塑性变形后形成切屑。
切削层受刀具前刀面与切削刃的挤压作用,使近切削刃处的金属先产生弹性变形,继而塑性变形,并同时使金属晶格产生滑移。
第一变形区就是形成切屑的变形区,其变形特点是切削层产生剪切滑移变形。
第二变形区(与前刀面接触的切屑层产生的变形区)内金属的挤压磨擦变形经过第一变形区后,形成的切屑要沿前刀面方向排出,还必须克服刀具前刀面对切屑挤压而产生的摩擦力。
此时将产生挤压摩擦变形。
应该指出,第一变形区与第二变形区是相互关联的。
前刀面上的摩擦力大时,切屑排出不顺,挤压变形加剧,以致第一变形区的剪切滑移变形增大。
第三变形区(近切削刃处已加工表面内产生的变形区)金属的挤压磨擦变形已加工表面受到切削刃钝圆部分和后刀面的挤压摩擦,造成纤维化和加工硬化。
图2 切削过程2 切削加工表面残余应力的产生机理目前, 关于残余应力的产生机理, 从理论上定量分析还存在困难。
下面仅从已加工表面形成过程的角度分析残余应力的产生机理。
(1)机械应力引起的残余应力工件装夹时, 如果夹紧力过大, 将会使工件发生塑性变形, 从而使工件产生残余应力。
切削过程中,刀刃前方的工件材料受到前刀面的挤压, 从而使将成为已加工表面层的金属, 在切削方向产生压缩的塑性变形; 而在与已加工表面垂直方向产生拉伸塑性变形; 切削后受到与之连成一体的里层未变形金属的牵制, 从而产生残余应力。
在已加工表面形成过程中, 刀具的后刀面与已加工表面产生很大的挤压和摩擦, 使表层金属产生拉伸塑性变形, 刀具离开后, 里层金属的弹性变形趋向恢复, 但受到表层金属的牵制,因而也产生残余应力。
(2)热应力引起的残余应力切削时, 由于强烈的塑性变形与摩擦, 使已加工表面层的温度很高; 而里层温度很低, 形成不均匀的温度分布, 因此, 当热应力超过材料的屈服极限时,将使表层金属产生压缩变形, 切削后冷却至室温时,表层金属体积的收缩又受到里层金属的牵制, 因而产生残余应力。
(3)相变引起的残余应力切削时, 若表层温度大于相变温度, 则表层组织可能发生相变, 由于各种金相组织的体积不同, 从而产生残余应力。
在切削过程中, 引起不均匀塑性变形的机械应力和热应力是同时存在的, 所以残余应力的计算是一个热- 力耦合的热弹塑性问题。
3 影响切削残余应力的因素工件已加工表面残余应力的性质和大小受很多因素的影响。
掌握这些因素的影响规律并合理选择,对于降低残余应力和优化切削过程是很有必要的。
3.1工件材料的影响工件材料本身状态及其物理机械性能对加工表面残余应力产生直接影响。
实验表明:塑性好的材料切削加工后通常产生残余拉应力;塑性差的材料则产生残余压应力。
根据工件材料的具体初始应力状态,切削加工可能使工件内残余应力值“增大”或“减小”[4]。
3.2切削参数的影响切削速度的影响一般是通过“温度因素”来进行的[5]。
切削速度较低时,易产生残余拉应力;切削速度较高时,由于切削温度升高,易产生残余压应力。