片剂崩解不合格的原因和解决方法
片剂崩解时限等问题总结-20190806

片剂崩解时限等问题总结20190806一、影响片剂的主要原因及解决方法主要原因原村料特性的符合性、药用赋形剂的使用比例,辅料的不一致性,不合理的配方,不合理的混合工艺、制粒工艺,压片时使用的模具及设备不佳,不良的压片工艺过程,不适宜的生产环境1)片重差异2)粘冲:有细粉枯于冲头及模圈表面致使片面不光洁、不平、有凹痕现象3)裂片4)松片5)变色及斑点6)崩解迟緩7)刻字或线条不青晰二、粉末直接压片粉末直接压片的应用方法及其注意事项由于粉末直接压片具有较明显的优点,如工艺过程比较简单,不必制粒、干燥,产品崩解或溶出快,成品质量稳定,在国外约有40%的片剂品种已采用这种工艺生产。
a)应用1).用于遇湿、热易变色、分解的药物许多药物对显、热不稳定,如头孢克肟遇湿、热易发生变色,效价降低;維生素C具有还原性,易空气氧化以致颜色变黄、含量下降,特别是受水分、温度、金属离子等向时更易造成药品变质;氮茶碱遇湿、热均易分解、变色,放出强烈氨臭;利福平对湿、热也不稳定,含量下降,溶出度不合格;维生素B1、B2、B6等对湿热、金属离子均不稳定。
这些药物若来用常拠쿄法制粒,因在生产过程中,药物与合剂中的溶接角触,并经高温干燥,必会对产品质量有景知向。
而来用粉末直接压片工艺,所制得的片剥片面光滑,无裂片和粘冲,片重差异小,崩解时限短,经加速试验、留样观察,片剂各项质量指标均无变化。
2).用于酯类、酰胺类等易水解药物因盐酸甲氯芬酯极易水解,采用常规的湿法制粒工艺,因生产过程中加入粘合剂,含有水分,在干燥的高温条件下,药物分解加快,从而影响药品的质量,不仅降低了药物的含量,而且增加了降解产物,使疗效降低,副作用增加。
而采用粉末直接压片工艺生产,避免了与水的接蝕・同时可选用引湿性小的辅料,进一步保证药物在贮藏期间的稳定性。
3).用于溶解度较小或疏水性的药物溶解度小的药物的溶出度受其比表面积和药物成品表面性质的影响较大,通过药剂学方法,选用疏水性辅料,经粉末直接压片后,药品崩解后药物直接从粉末中释放出来分散度增大,溶出加快,相对生物利用度提高4).用于低熔点及产生共熔的复方药物环扁桃酯的熔点为50C~62℃,常规湿法制粒可造成药物熔化而影响质量;盐酸麻黄素和盐酸苯海拉明的复方制剂,湿法制粒干燥时两者可产生共熔,不易烘干。
片剂崩解迟缓问题的探讨

中国现代应用药学CHINESE JOURNAL OFMODERN APPLIEDPHARMACY1999年第16卷 第3期 vol.16No.31999片剂崩解迟缓问题的探讨张文起 片剂崩解迟缓是影响片剂质量的主要因素之一,药典根据片剂作用部位与吸收不同,除了含片等不作崩解检查外,对其它片剂崩解时限均有不同要求,作者对浙江绍兴市9家药厂片剂生产调查发现片剂崩解迟缓现象时有发生,本文就片剂生产中对可能造成片剂崩解迟缓的诸因素及解决办法进行探讨。
1 影响因素1.1 主药的影响 主药的性状,理化性质,如晶形、结晶水、粘度、溶解度、粒度等及主药的稳定性对片剂的崩解时限有较大的影响。
1.2 赋形剂影响1.2.1 稀释剂影响:稀释剂本身具有一定的粘合性,且用量较大时,如糊精、糖粉或使用疏水性的稀释剂,可延长片剂的崩解时间。
1.2.2 粘合剂的影响:粘合剂对片剂的崩解时限影响较大,这可能是由于胶类物质形成的屏障延缓了水合的透入,影响了片剂溶解或分散的速度。
1.2.3 崩解剂的影响:崩解剂可促进片剂的崩解。
它可以看成是在人体胃环境中的分散剂。
理想的崩解剂不仅使药物崩解为颗粒状,而且还能将颗粒崩解为粉粒。
1.2.4 润滑剂的影响:润滑剂对片剂的崩解有显著的影响,润滑剂多为疏水性物质,可延长片剂的崩解时间,阻碍水分进入片剂内部,用量越大,影响越大。
润滑剂的品种不同,其疏水性不同所以不同润滑剂对片剂崩解有差异。
常用润滑剂影响崩解强的顺序为:硬脂铝镁>硬脂酸>矿物油>滑石粉。
1.3 生产过程的影响1.3.1 混合时间的影响:在生产操作中,湿混的时间对片剂崩解影响也有很大作用。
时间短,制出的颗粒细粉多,无法压片;时间太长,则片剂崩解得不好,一般来讲,随着混合时间的增加,崩解时间也随之增加。
因此,在操作中,对于同一品种,由于原辅料的产地不一,批号不同,季节不同,湿混时间也不一样,这就要求操作中要控制好湿混时间。
1.3.2 颗粒干燥温度的影响:颗粒干燥温度由原辅料性质而定,不可太高,颗粒如用淀粉或糖粉,过高温时能引起糊化或熔化,不但能使颗粒坚硬,而且片剂也不易崩解。
片剂崩解延长原因

崩解时限延长的原因崩解时限崩解度不合格是影响片剂质量的主要因素之一。
《中华人民共和国药典》根据片剂作用的部位与吸收度不同,除了对含片等不作崩解检查以外,对其他片剂崩解时限均有不同要求。
崩解度不合格的主要原因是在制粒过程中黏合剂用量过大,致使颗粒过硬,片子崩解时间被延长。
此外,润滑剂对片剂的崩解亦有显著的影响。
润滑剂多为疏水性物质,可延长片剂的崩解时限,阻碍水分进入片剂内部,故用量越大、影响越大。
在生产中如遇到制成的颗粒压片后崩解时限不合格,其解决方法一是加入崩解作用较强的崩解剂(如羟甲基淀粉钠);二是在保证片剂质量的前提下,按一定比例与崩解良好的颗粒混和均匀再压片;三是先加入一定量的崩解剂,然后再与崩解良好的颗粒混合。
(一)片剂的崩解机制片剂的崩解机制与所用崩解剂及所含药物的性质有关,主要有以下几点:1.毛细管作用。
片剂具有许多毛细管和孔隙,与水接触后水即从这些亲水性通道进入片剂内部,强烈的吸水性使片剂润湿而崩解。
淀粉及其衍生物和纤维素类衍生物的崩解作用多与此相关。
2.膨胀作用。
崩解剂吸水后充分膨胀,自身体积显著增大,使片剂的粘结力瓦解而崩散。
羧甲基淀粉及其钠盐的崩解作用主要即在于其强大的膨胀作用。
3.产气作用。
泡腾崩解剂遇水产生气体,借气体的膨胀而使片剂崩解。
其他机制尚有:可溶性原、辅料遇水溶解使片剂崩解或蚀解;表面活性剂因能改善颗粒的润湿性,而促进崩解;辅料中加用了相应的酶,因酶解作用而有利崩解等。
(二)片剂常用崩解剂1.干燥淀粉。
用前100℃干燥1h。
本品对易溶性药物的片剂作用较差,适用于不溶性或微溶性药物的片剂。
因淀粉的可压性较差,遇湿受热易糊化,故用量不宜过多,湿粒干燥温度亦不宜过高,否则将影响成品的硬度和崩解度。
2.羧甲基淀粉钠(CMS-Na)。
具良好的流动性和可压性;遇水后,体积可膨胀200~300倍;亦可作为直接压片的干燥粘合剂和崩解剂。
适用于可溶性和不溶性药物;用量为4%~8%,一般采用外加法。
片剂制备常见问题及解决方法

二.片剂随着中国几千年历史的发展,尤其是近年来中药及其制剂的广泛使用中药已成为独具特色的治病良药。
但是,中药片剂在生产中也存在着不少问题,现对这些问题及其解决方法作一综述。
1 生产工艺糖衣片的常规打光方法是在闷锅结束后,打蜡粉加入片子中(每万片用量3~5g),开动糖衣锅打光,一般需15min完成。
但生产时,常因一些因素掌握不好而导致打光困难,甚至被迫停止。
报道可改用“布袋-糖衣锅”法打光,该法只需5~10min,且应用广泛。
生产复方冬凌草含片,老工艺是将冬凌草提取液经减压浓缩到稠膏状后,直接与其他浸膏混合置烘箱中高温烘干,新工艺将提取液经减压浓缩至稠膏状后,溶解在乙醇中,制粒前喷入干粉中,制粒后在鼓风机中低温烘干。
通过对比发现,采用新工艺制得的含片中冬凌草甲素含量比老工艺制得者高,临床疗效更显著。
2 崩解片剂崩解迟缓是影响片剂质量的主要因素之一。
据报道片剂崩解迟缓主要是受主药!赋形剂和生产过程的影响[3]"最佳解决办法是:加入崩解作用较强的崩解剂,如2%~5%羟甲基淀粉钠;在保证片剂成品质量的前提下,可按一定比例与崩解良好的颗粒混合均匀压片;先加入一定量的崩解剂,然后再与崩解良好的颗粒混合"另外,改进制粒方法也可改善片剂的崩解性能,如紫花杜鹃片(浸膏在颗粒中占80%)分别用混合机与喷雾制粒,两种片剂的崩解时限分别为60,20~30min;感冒清片(浸膏在颗粒中占40%)用上述两方法制粒,两种片剂的崩解时限分别为55,23min。
结果表明,改用喷雾制粒压片,崩解时限明显缩短,产品质量提高。
3 包衣在气温较高的条件下,片芯易失水,且由于受热膨胀,导致片子的爆裂。
一般认为,糖衣片所发生的龟裂砚象主要是包衣层中搪层和有色搪层水份挥发引起的,然面过份干燥还会析出糖的结晶,而形成龟裂,所以当羞片水份在30%-50%时,包衣温度在50℃以下干操,不会导致片芯的膨胀,低温放置也不会龟裂。
由于包衣时衣层的厚度、颜色不均匀等原因造成片面花斑、片面高低不平、光亮度差异等外观质量问题也很常见。
片剂生产过程中常见质量问题和解决方法

工 程 技 术2008 NO.18Science and Technology Innovation Herald1 溶出超限片剂在规定的时间内未能溶出规定的药物,即为溶出超限或称为溶出度不合格。
片剂口服后,经过崩解、溶出、吸收产生药效,其中任何一个环节发生问题都将影响药的实际疗效。
未崩解的完整片剂的表面积很小,所以溶出速度慢。
崩解后所形成的小颗粒很多,表面积大幅度增加,溶出过程也随之增至最大,药物的溶出速度也最快,所以,能够使崩解加快的因素,一般也能加快溶出。
但是,也有不少药物的片剂虽可迅速崩解,而药物溶出却很慢,因此崩度合格并不一定能保证药物快速而完全的溶出,也就不能保证具有可靠的疗效。
对于许多难溶性药物来说,这种溶出加快的幅度不会很大,尚需采取一些其他的方法来改善溶出。
原因分析及解决方法。
1.1 研磨混合物疏水性药物单独粉碎时,随着粒径的减小,表面自由能增大,粒子易发生重新聚集的现象,粉碎的实际效率不高。
与此同时,这种疏水性的药物粒径减小、比表面积增大,会使片剂的疏水性增强,不利于片剂的崩解和溶出。
如果将这种疏水性的药与大量的水溶性辅料共同研磨粉碎制成混合物,则药物与辅料的粒径都可以降低到很小。
又由于辅料的量多,所以在细小的药物粒子周围吸附着大量水溶性辅料的粒子,这样就可以防止细小药物粒子的相互聚集,使其稳定地存在于混合物中。
当水溶性辅料溶解时,细小的药物粒子便直接暴露于溶出介质中,所以溶解(出)速度大大加快。
例如,将疏水性的地高辛、氢化可的松等药物与20倍的乳糖球磨混合后干法制粒压片,溶出度大大加快。
1.2 制成固体分散物将难溶性药物制成固体分散物是改善溶出速度的有效方法,例如,用1∶9的吲哚美辛与PEG6000制成的固体分散物粉碎后,加入适宜辅料压片,其溶出度呆得到很大的改善。
1.3 载体吸附将难溶性药物溶于能与小混溶的无毒溶剂(如PEG400)中,然后用硅胶一类多孔性的载体将其吸附,最后制成片剂。
微晶纤维素压片崩解
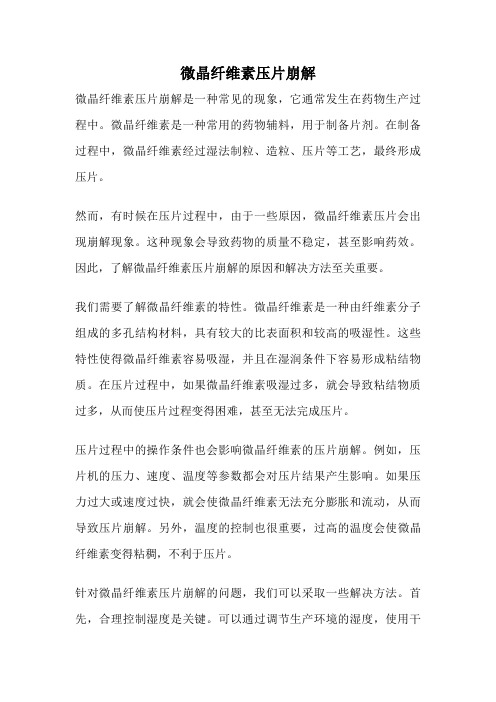
微晶纤维素压片崩解微晶纤维素压片崩解是一种常见的现象,它通常发生在药物生产过程中。
微晶纤维素是一种常用的药物辅料,用于制备片剂。
在制备过程中,微晶纤维素经过湿法制粒、造粒、压片等工艺,最终形成压片。
然而,有时候在压片过程中,由于一些原因,微晶纤维素压片会出现崩解现象。
这种现象会导致药物的质量不稳定,甚至影响药效。
因此,了解微晶纤维素压片崩解的原因和解决方法至关重要。
我们需要了解微晶纤维素的特性。
微晶纤维素是一种由纤维素分子组成的多孔结构材料,具有较大的比表面积和较高的吸湿性。
这些特性使得微晶纤维素容易吸湿,并且在湿润条件下容易形成粘结物质。
在压片过程中,如果微晶纤维素吸湿过多,就会导致粘结物质过多,从而使压片过程变得困难,甚至无法完成压片。
压片过程中的操作条件也会影响微晶纤维素的压片崩解。
例如,压片机的压力、速度、温度等参数都会对压片结果产生影响。
如果压力过大或速度过快,就会使微晶纤维素无法充分膨胀和流动,从而导致压片崩解。
另外,温度的控制也很重要,过高的温度会使微晶纤维素变得粘稠,不利于压片。
针对微晶纤维素压片崩解的问题,我们可以采取一些解决方法。
首先,合理控制湿度是关键。
可以通过调节生产环境的湿度,使用干燥剂等方法来控制微晶纤维素的湿度,从而减少崩解的概率。
其次,合理调整压片机的参数,确保压力、速度和温度等参数在合适的范围内,以保证微晶纤维素能够充分膨胀和流动。
此外,选择适当的压片机模具和压片机配件也是非常重要的。
微晶纤维素压片崩解是一种常见的问题,但通过合理控制湿度、调整压片机参数以及选择合适的压片机配件,我们可以解决这个问题,保证药物的质量稳定性和药效。
我们应该在药物生产过程中高度重视微晶纤维素压片崩解问题,并采取相应的措施来预防和解决。
只有这样,我们才能生产出质量稳定、药效可靠的药物,为人类的健康做出贡献。
松片、裂片、崩解延缓等质量问题的解决办法

生产过程中常见问题和处理方法一、质量问题制剂生产过程由于种种原因造成制剂的质量不合格,尤其是在片剂生产中,造成片剂质量问题的因素更多.现仅对片剂、胶囊剂及注射剂生产中可能产生质量问题的原因及解决方法作介绍。
(一)片剂生产过程中可能发生问题的分析及解决方法1. 松片片剂压成后,硬度不够,表面有麻孔,用手指轻轻加压即碎裂,原因分析及解决方法:①药物粉碎细度不够、纤维性或富有弹性药物或油类成分含量较多而混合不均匀。
可将药物粉碎过100目筛、选用黏性较强的黏合剂、适当增加压片机的压力、增加油类药物吸收剂充分混匀等方法加以克服。
②黏合剂或润湿剂用量不足或选择不当,使颗粒质地疏松或颗粒粗细分布不匀,粗粒与细粒分层。
可选用适当黏合剂或增加用量、改进制粒工艺、多搅拌软材、混均颗粒等方法加以克服。
③颗粒含水量太少,过分干燥的颗粒具有较大的弹性、含有结晶水的药物在颗粒干燥过程中失去较多的结晶水,使颗粒松脆,容易松裂片。
故在制粒时,按不同品种应控制颗粒的含水量。
如制成的颗粒太干时,可喷入适量稀乙醇(50%—60%),混匀后压片。
④药物本身的性质。
密度大压出的片剂虽有一定的硬度,但经不起碰撞和震摇。
如次硝酸铋片、苏打片等往往易产生松片现象;密度小,流动性差,可压性差,重新制粒。
⑤颗粒的流动性差,填入模孔的颗粒不均匀。
⑥有较大块或颗粒、碎片堵塞刮粒器及下料口,影响填充量。
⑦压片机械的因素。
压力过小,多冲压片机冲头长短不齐,车速过快或加料斗中颗粒时多时少。
可调节压力、检查冲模是否配套完整、调整车速、勤加颗粒使料斗内保持一定的存量等方法克服。
2。
裂片片剂受到震动或经放置时,有从腰间裂开的称为腰裂;从顶部裂开的称为顶裂,腰裂和顶裂总称为裂片,原因分析及解决方法:①药物本身弹性较强、纤维性药物或因含油类成分较多。
可加入糖粉以减少纤维弹性,加强黏合作用或增加油类药物的吸收剂,充分混匀后压片。
②黏合剂或润湿剂不当或用量不够,颗粒在压片时粘着力差。
片剂裂片的原因及解决方法
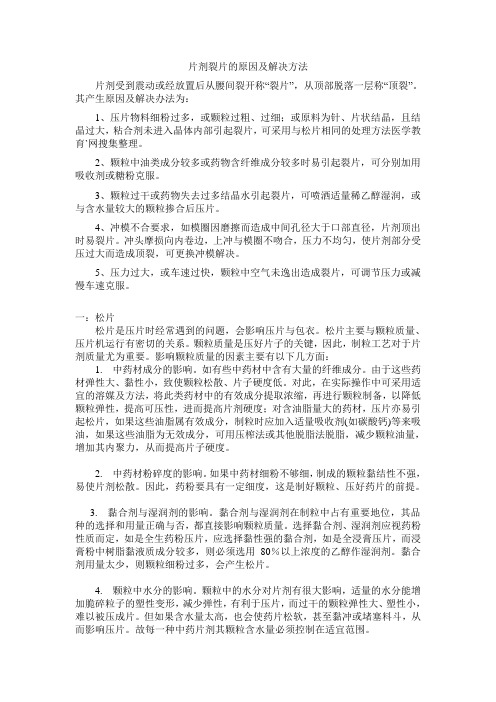
片剂裂片的原因及解决方法片剂受到震动或经放置后从腰间裂开称“裂片”,从顶部脱落一层称“顶裂”。
其产生原因及解决办法为:1、压片物料细粉过多,或颗粒过粗、过细;或原料为针、片状结晶,且结晶过大,粘合剂未进入晶体内部引起裂片,可采用与松片相同的处理方法医学教育`网搜集整理。
2、颗粒中油类成分较多或药物含纤维成分较多时易引起裂片,可分别加用吸收剂或糖粉克服。
3、颗粒过干或药物失去过多结晶水引起裂片,可喷洒适量稀乙醇湿润,或与含水量较大的颗粒掺合后压片。
4、冲模不合要求,如模圈因磨擦而造成中间孔径大于口部直径,片剂顶出时易裂片。
冲头摩损向内卷边,上冲与模圈不吻合,压力不均匀,使片剂部分受压过大而造成顶裂,可更换冲模解决。
5、压力过大,或车速过快,颗粒中空气未逸出造成裂片,可调节压力或减慢车速克服。
一:松片松片是压片时经常遇到的问题,会影响压片与包衣。
松片主要与颗粒质量、压片机运行有密切的关系。
颗粒质量是压好片子的关键,因此,制粒工艺对于片剂质量尤为重要。
影响颗粒质量的因素主要有以下几方面:1. 中药材成分的影响。
如有些中药材中含有大量的纤维成分。
由于这些药材弹性大、黏性小,致使颗粒松散、片子硬度低。
对此,在实际操作中可采用适宜的溶媒及方法,将此类药材中的有效成分提取浓缩,再进行颗粒制备,以降低颗粒弹性,提高可压性,进而提高片剂硬度;对含油脂量大的药材,压片亦易引起松片,如果这些油脂属有效成分,制粒时应加入适量吸收剂(如碳酸钙)等来吸油,如果这些油脂为无效成分,可用压榨法或其他脱脂法脱脂,减少颗粒油量,增加其内聚力,从而提高片子硬度。
2. 中药材粉碎度的影响。
如果中药材细粉不够细,制成的颗粒黏结性不强,易使片剂松散。
因此,药粉要具有一定细度,这是制好颗粒、压好药片的前提。
3. 黏合剂与湿润剂的影响。
黏合剂与湿润剂在制粒中占有重要地位,其品种的选择和用量正确与否,都直接影响颗粒质量。
选择黏合剂、湿润剂应视药粉性质而定,如是全生药粉压片,应选择黏性强的黏合剂,如是全浸膏压片,而浸膏粉中树脂黏液质成分较多,则必须选用80%以上浓度的乙醇作湿润剂。
- 1、下载文档前请自行甄别文档内容的完整性,平台不提供额外的编辑、内容补充、找答案等附加服务。
- 2、"仅部分预览"的文档,不可在线预览部分如存在完整性等问题,可反馈申请退款(可完整预览的文档不适用该条件!)。
- 3、如文档侵犯您的权益,请联系客服反馈,我们会尽快为您处理(人工客服工作时间:9:00-18:30)。
片剂崩解不合格的原因和解决方法
应将处方与工艺进行细分,一步步进行研究试验,不要轻易下结论
一、处方原因
1、崩解剂
(1)、速崩王:外加、内加或内外加(颗粒比较硬的品种可能需要内加,一般
用量4%-8%)
(2)、L-HPC:有良好的崩解效果,崩解后颗粒更细,有利于药物的溶出,难
溶性药物使用效果较好
(3)、羧甲基淀粉钠:在中药浸膏片中效果不理想,药物粘性大,溶液不容易
大量进入药片中,只有很少的崩解剂能够吸到水后膨胀,对抗
不了药物本身的粘性,需要使用大量的崩解剂分部到能吸到水
的部位产生足够的膨胀;改善的方法:加入能够改变药物粘性
的辅料和此类崩解剂配合使用(氯化钠无副作用,加入量可随
意,迅速溶解后产生大量孔隙使溶液进入药片中增大溶液与药
物的接触面积,溶解后使药片松散,有利于崩解剂发挥作用和
最终的崩解
(4)、硬度较大的品种多用一些羧甲基淀粉钠和微晶纤维素
(5)、硬度不够的品种加一些糖粉
(6)、pvpp:中药,用量比较大,10%,崩解时间可在15分钟内
用量一般在2%-5%
粒径达的,效率更高
可用于分散片、难溶片等
价格较高
(7)、微晶纤维素
(8)、崩解剂合用比单用效果好,内加和外加的用量比例也很重要
解决缓释片崩解问题,L-HPC与CMS-Na合用,PVPP与
CCMS-Na合用
(9)、pvp,微粉硅胶,应充分考虑不同的崩解剂对产品的影响,交联羧甲基淀
粉钠(价格较高)
2、粘合剂减少用量或降低浓度,HPMC
3、润滑剂(1)、滑石粉,亲水性润滑剂,用量适当不会影响崩解,润滑性不如硬
脂酸镁。
(2)、疏水性润滑剂,用量较多时会影响崩解,可加入量表面活性剂,
如十二烷基硫酸钠(0.1%左右)
(3)、月桂醇硫酸镁(十二烷基硫酸镁)水溶性润滑剂,润滑效果不及
硬脂酸镁,好于滑石粉、PEG及月桂醇硫酸钠
4、表面活性剂:分散片可适当加0.1%左右的表面活性剂
5、一般常识“崩解要求快,片重应该小”是误区,实际生产中,片重小,压力就不
会很大
6、主药的影响:难溶性主药影响崩解
含油类成分较多,加入吸有剂,吸附油类成分,不加崩解可解决
片剂疏水性较强,加入表面活性剂,改善片剂的润湿性
二、中药浸膏片
1、浸膏量过大,遇水相互粘结成团,使崩解困难,解决方法加入好的崩解剂如CMS-Na,
改变制粒工艺
2、水提半浸膏片、醇提半浸膏片,中药粉作崩解剂
3、全浸膏片粘度大,颗粒难做,制成的颗粒和成片后易吸湿,解决方法加入新型崩解剂
4、实用新型辅料解决崩解问题(1)避开淀粉、糊精糖粉等传统辅料
(2)新型辅料:微晶纤维素和低取代羟丙纤维素联合
粘合剂:交联聚维酮
润滑剂,使用水溶性润滑剂:PEG
5、原料来源复杂,特别是油类、树脂、全浸膏片造成崩解不合格最为常见,原因由于没
有孔隙和毛细管通道堵赛水分不能迅速进入片剂中
6、颗粒过于坚硬解决方法(1)适当减少膏量,增加药粉量,或增加一些崩解剂,如淀
粉、羧甲基淀粉纳等
(2)将粗颗粒破碎
(3)选择适当的粘合剂
(4)选较高浓度的酒精制粒
(5)增加崩解剂用量
7、崩解剂:品种和加入方法选择不当,用量不足,干燥不够
8、粘合剂:粘性太强,用量过多,减少用量和调换品种,水改乙醇
9、润滑剂:疏水性润滑剂(硬镁)用量过多,减少用量,更换为滑石粉,二氧化硅,
或亲水性润滑剂(如月桂醇硫酸镁)
10、填充剂:提取物粘性大,乳糖,虽压缩成型好,但不利于崩解
可选用硫酸钙,多加适当填充剂
11、不同中药提取物理化学性质差异较大,应根据性质及临床用量选择适当的填充剂、
崩解剂及其用量。
三、工艺因素
1、压片压力的影响,压力不要太大,在硬度合格的前提下,适当降低压力
素片5kg即可,包衣片可稍高,片重小于0.2g的片子,硬度应在4kg
以下
2、颗粒水分,颗粒制备工艺(采用喷雾干燥制粒),压片压力
3、制粒工艺(1)颗粒水分;
(2)粘合剂加入量过多;
(3)颗粒太紧、太硬;
(4)做软材时搅拌不均匀;
(5)颗粒粒度,容易有花斑,片子过松;太细容易导致片子太硬
4、包衣隔离层的影响,浓度,层数
5、亲水性辅料外加,主药与部分辅料制粒,整粒时再入亲水性辅料和崩解剂,崩解
剂用量在7%-10%左右
四、储存条件含胶、糖、浸膏的片剂和储存温度较高或引湿后,崩解时间会延长。