大中型高炉技术经济指标改善的条件
1号高炉提高技术经济指标措施

柳钢1号高炉提高技术经济指标实践黄日清,王文志,黄显昌,郑镇鹏(柳州钢铁股份有限公司炼铁厂工艺技术科)摘要对柳钢1号高炉稳定顺行优化操作和强化冶炼实践进行了总结。
通过采取强化原燃料管理,合理优化操作制度,保持良好操作炉型,加强设备管理等措施,实现了高炉较长时期的稳定顺行和各项技术经济指标的进步。
关键词高炉炉型操作强化冶炼设备1 概况柳钢1号高炉于2008年5月8日建成投产,有效容积2000m3,采用串罐式无料钟炉顶,皮带上料。
6层以上采用密闭循环冷却,1~5层采用工业水冷却。
设东、西两个出铁场,储铁式大沟,明特法渣处理系统。
板壁结合炉衬技术,炉身8~14层为铜冷却板。
炉缸采用陶瓷杯技术。
从2011年4月份开始由于受上料系统设备故障等因素影响休、慢风率分别高达1.32%和1.17%,频繁的休、慢风操作导致操作炉型发生变化,气流分布不均,渣皮脱落多,炉缸出现堆积现象。
随后几个月一直进行操作炉型的纠正和消除炉缸堆积,并且烧结矿品位持续下滑至近几年的最低,只有54.91%,各项技术经济指标都较差。
到9月份焦炭热强度大幅度下降至56.28%,炉缸活跃程度进一步恶化,利用系数只有2.331t/d·m3,焦比高达435kg/tFe,炉芯温度持续下降至620℃,下跌80℃。
为此高炉采取堵风口控制冶炼强度的措施来确保炉况顺行。
10月份为适应市场变化,21日降料面至风口带停炉检修。
采用机械和人工清理的方式对炉缸堆积物进行清理,直至挖空到炉底第三层冷却壁位置,并对炉身进行喷涂造衬,形成合理操作炉型。
11月23日开炉后仅用3天便恢复炉况达产,之后经各项调整措施进行,高炉各项技术经济指标明显好转,见表1。
表1 2011~2012年1号炉技术经济指标月份产量利用系数焦比焦丁比煤比综合焦比燃料比冶炼强度综合冶强焦炭负荷t/d t/m3.d kg/tFe kg/tFe kg/tFe kg/tFe kg/tFe t/m3.d t/m3.d t/t t/t2012-2 5048.38 2.524 320 41 149 477 511 0.91 1.21 4.63 2012-1 5041.29 2.521 328 45 150 488 522 0.95 1.26 4.60 2011-12 5133.98 2.567 334 45 155 498 534 0.99 1.31 4.48 2011-11 2849.44 1.425 727 102 125 920 955 0.780.93 3.52 2011-10 4701.46 2.351 364 52 146 524 558 1.02 1.30 4.05 2011-9 4603.08 2.302 380 55 131 534 565 1.01 1.25 3.91 2011-8 4952.80 2.476 367 56 144 532 566 1.06 1.35 4.16 2011-7 4285.21 2.143 394 59 145 563 5980.97 1.22 3.98 2011-6 4905.10 2.453 372 55 165 553 592 1.06 1.39 4.13 2011-5 5062.41 2.531 324 43 160 491 527 0.94 1.26 4.89 2011-4 4993.96 2.497 348 58 161 529 567 1.02 1.35 4.28 2011-3 5214.35 2.607 340 58 154 516 553 1.06 1.38 4.32 2011-2 5044.02 2.522 344 57 162 526 564 1.01 1.34 4.27 2011-1 4807.38 2.404 437 60 142 605 639 1.02 1.34 3.85 2 炉体维护利用停炉检修时间比较长的有利时机,10月21日中班开始降料面至风口带,安全停炉后往炉内打水凝结炉缸残留渣铁矿石和未燃焦炭,拆除风口后在风口安装风扇往炉缸内鼓风,排净煤气和降低温度后在确保安全的前提下工人进入炉缸内将残留物破碎,人工清理干净。
国内外高炉炼铁技术的发展现状和趋势

国内外高炉炼铁技术的发展现状和趋势高炉炼铁技术是金属冶炼工业发展的基础,是保证金属铁质量和产量的关键技术,也是社会经济发展的重要依托。
近年来,随着金属冶炼工业的快速发展,国内外高炉炼铁技术的发展也取得了显著的成就,为保证金属铁质量、提高产量、提高经济效益发挥了重要作用。
首先,国内外高炉炼铁技术取得了重大突破,进一步提高了金属铁质量。
随着科学技术的进步,添加剂和冶炼工艺的改进,使高炉炼铁工艺取得重大进展,不仅能够有效提高铁素体组成,同时也能够改善铁水的流动性,有利于铁块的全面成型。
此外,利用新型炉料和改进的热处理技术,可以有效降低铁水的含氧量,提高铁液的液相容量,从而获得更高品质的铁。
其次,国内外高炉炼铁技术的发展,还大大提高了铁的产量。
传统的高炉炼铁工艺存在着大量的炉料损失,限制了铁的产量。
随着国内外高炉炼铁技术的发展,炉料损失大大减少,产量得到提高。
通过对炼铁工艺及其参数进行优化调整,获得合理的炉料计算和分配,进而有效提高铁的产量。
此外,结合智能技术、自动化技术和智能控制技术,还可以实现远程监控和智能化管理,可以使高炉炼铁效率更高,产量更大。
最后,国内外高炉炼铁技术的发展,对提高经济效益具有重要意义。
国内外高炉炼铁技术的发展,不仅缩短了铁的生产周期,提高了产量,而且可以减少能耗消耗和废气排放,降低了生产成本,有利于提高企业的竞争力,实现更高的经济效益。
此外,国内外高炉炼铁技术的发展还可以改善炼铁终端的工作环境,为炼铁行业的发展创造更加良好的条件。
以上是国内外高炉炼铁技术的发展现状和趋势的概述,未来的发展趋势可以简单地总结为以下几点:继续提高高炉炼铁质量和产量,推广智能技术,进一步优化炼铁工艺,合理设计炉料配比,提高炼铁效率,减少能耗和污染,改善炼铁环境,提高经济效益,实现绿色经济发展。
未来,相信国内外高炉炼铁技术将取得更好的发展,为我们社会的经济发展提供更多的依托。
高炉主要技术经济指标及有关计算

式中 t —冶炼周期,h;N —由料线到风口中
心线的料批数,批; V ' —由料线到风口中心线的
容积,m3; n —每天料批数,批; V —每批料
体积,m3/批; c —炉料在高炉内压缩率,一般
为12~15%。
7、冷却壁热流强度:
q 0.278 ctQ S
0.278=1000/3600
式中 q —冷却壁热流强度,W/m2; c —冷却 水质量热容,kJ/(kg·℃); Q —冷却壁通水量, kg/h; t —冷却壁进出水温差,℃; S —冷却壁 面积,m2。(1千卡=4186.8焦耳, 1kCal/(m2·h)=1.163W/m2)
式中 v实 —风口实际风速,m/s;v标—风口标准
风速,m/s;t—风温,℃; p —热风压力,MPa。
4、鼓风动能:
E
1 2
mV实 2
0.412
1 n
Q3 F2
(t 273)2 ( p p0 )2
m=1.29*Q /n/60
式中 E —鼓风动能,J/s; t—风温,℃;Q — 风量,m3/min; F —风口送风总面积,m2; n — 风口个数,个; p —热风压力,Pa; p0 —标准 大气压,等于101325Pa。
高炉炼铁有关计算
1、入炉风量的计算:
由于现场风量仪表有计量误差,并且送风系统有 漏风现象,造成仪表显示的风量与高炉实际的入 炉风量有较大误差,可用燃料消耗来反算入炉风 量。
(1)高炉不富氧时入炉风量:
燃烧1kgC所需风量(m3/kgC ):
VC
0.933 (0.21 0.29 f )
0.933—1kgC燃烧所需要的O2的量,22.4/24 0.21+0.29f——湿空气的含氧量,(1-f)×0.21+0.5f
高炉主要技术经济指标与有关计算
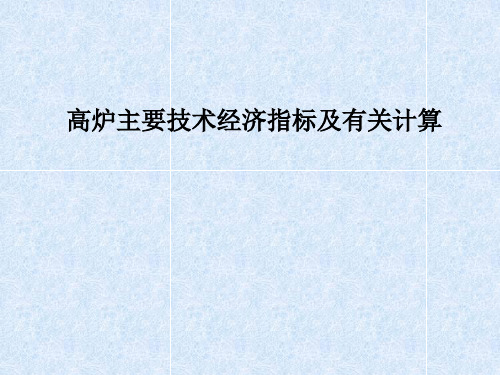
I综QK
QMBQJB Vu
式中 I 综 —综合冶炼强度,t/(m3·d); Q K —日
干焦用量,t/d;Q M —日喷吹煤量,t/d;Q J —日
焦丁量,kg; B—喷吹燃料及焦丁折干焦系数。
9、燃烧强度:
IA
QK
QMBQJB
(d2 /4)
式中 I A —燃烧强度,t/(m2·d);Q K —日干焦 用量量,k,gt;/d;B—Q喷M —吹日燃喷料吹及煤焦量丁,折t干/d焦;Q系J数—。日焦d —丁 高炉炉缸直径,m。
P —日合格生铁产量,t/d; A—生铁折合炼钢 生铁系数; d —高炉炉缸直径,m。
由于炉型的特点不同,小型高炉可允许较高的冶
炼强度因而容易获得较高的利用系数。为了对比 不同容积的高炉实际的生产率,可对比其面积利 用系数。用高炉面积利用系数衡量高炉的生产率, 更为科学。高炉的面积利用系数一般在65~70 t/ (m2·d),有的高炉达到了70 t/(m2·d)以上。
各种燃料折干焦系数
燃料名称
计算单位
折合干焦系数
焦炭(干焦)
kg/kg
1.0
焦丁
kg/kg
0.9
重油(包括原油)
kg/kg
1.2
灰分≤10%
kg/kg
1.0
10%<灰分≤12%
kg/kg
0.9
喷吹用煤粉
12%<灰分≤15%
kg/kg
0.8
15%<灰分≤20%
kg/kg
0.7
灰分>20%
kg/kg
0.6
各牌号生铁折合炼钢生铁系数(A)
生铁种类 炼钢生铁
铸造生铁
球墨铸铁用生铁 含钒生铁
《炼铁工艺》复习题及答案
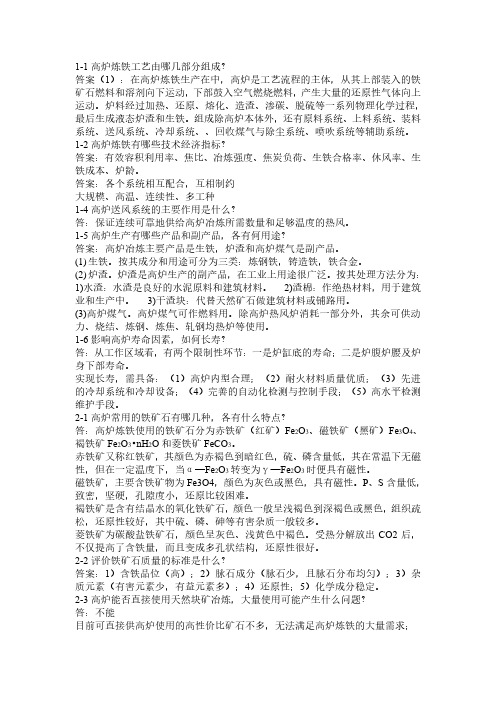
1-1高炉炼铁工艺由哪几部分组成?答案(1):在高炉炼铁生产在中,高炉是工艺流程的主体,从其上部装入的铁矿石燃料和溶剂向下运动,下部鼓入空气燃烧燃料,产生大量的还原性气体向上运动。
炉料经过加热、还原、熔化、造渣、渗碳、脱硫等一系列物理化学过程,最后生成液态炉渣和生铁。
组成除高炉本体外,还有原料系统、上料系统、装料系统、送风系统、冷却系统、、回收煤气与除尘系统、喷吹系统等辅助系统。
1-2高炉炼铁有哪些技术经济指标?答案:有效容积利用率、焦比、冶炼强度、焦炭负荷、生铁合格率、休风率、生铁成本、炉龄。
答案:各个系统相互配合,互相制约大规模、高温、连续性、多工种1-4高炉送风系统的主要作用是什么?答:保证连续可靠地供给高炉冶炼所需数量和足够温度的热风。
1-5高炉生产有哪些产品和副产品,各有何用途?答案:高炉冶炼主要产品是生铁,炉渣和高炉煤气是副产品。
(1)生铁。
按其成分和用途可分为三类:炼钢铁,铸造铁,铁合金。
(2)炉渣。
炉渣是高炉生产的副产品,在工业上用途很广泛。
按其处理方法分为:1)水渣:水渣是良好的水泥原料和建筑材料。
2)渣棉:作绝热材料,用于建筑业和生产中。
3)干渣块:代替天然矿石做建筑材料或铺路用。
(3)高炉煤气。
高炉煤气可作燃料用。
除高炉热风炉消耗一部分外,其余可供动力、烧结、炼钢、炼焦、轧钢均热炉等使用。
1-6影响高炉寿命因素,如何长寿?答:从工作区域看,有两个限制性环节:一是炉缸底的寿命;二是炉腹炉腰及炉身下部寿命。
实现长寿,需具备:(1)高炉内型合理;(2)耐火材料质量优质;(3)先进的冷却系统和冷却设备;(4)完善的自动化检测与控制手段;(5)高水平检测维护手段。
2-1高炉常用的铁矿石有哪几种,各有什么特点?答:高炉炼铁使用的铁矿石分为赤铁矿(红矿)Fe2O3、磁铁矿(黑矿)Fe3O4、褐铁矿Fe2O3•nH2O和菱铁矿FeCO3。
赤铁矿又称红铁矿,其颜色为赤褐色到暗红色,硫、磷含量低,其在常温下无磁性,但在一定温度下,当α—Fe2O3转变为γ—Fe2O3时便具有磁性。
大型高炉提高利用系数的措施

大型高炉提高利用系数的措施高炉是钢铁工业的核心设备之一,其生产效率和生产成本直接影响着钢铁企业的发展。
高炉的利用系数是衡量高炉生产效率的重要指标之一,提高高炉的利用系数对于钢铁企业来说至关重要。
本文将从高炉操作、高炉设备和高炉原料三个方面探讨提高高炉利用系数的措施。
一、高炉操作1.优化高炉操作流程高炉操作流程是高炉生产的基础,优化高炉操作流程可以提高高炉的生产效率。
优化高炉操作流程需要从高炉炉况、风温、煤气成分、风量等多个方面进行考虑,通过实时监测高炉运行状态,及时调整高炉操作参数,保持高炉正常运行,减少高炉停炉次数,提高高炉利用系数。
2.控制高炉温度高炉温度是高炉生产的重要参数之一,过高或过低的高炉温度都会影响高炉的生产效率。
控制高炉温度需要从炉况、风温、煤气成分、风量等多个方面进行考虑,通过实时监测高炉温度,及时调整高炉操作参数,保持高炉正常运行,减少高炉停炉次数,提高高炉利用系数。
二、高炉设备1.提高高炉设备的稳定性高炉设备的稳定性是高炉生产的关键之一,提高高炉设备的稳定性可以减少高炉停炉次数,提高高炉利用系数。
提高高炉设备的稳定性需要从高炉炉体、风口、渣口、煤气管道、空气预热器等多个方面进行考虑,通过对高炉设备进行定期检修和维护,及时更换损坏的设备,保持高炉设备的正常运行,提高高炉利用系数。
2.优化高炉喷吹系统高炉喷吹系统是高炉生产的重要部分,喷吹系统的优化可以提高高炉的生产效率。
优化高炉喷吹系统需要从风口、煤气管道、空气预热器等多个方面进行考虑,通过调整喷吹系统的参数,保证高炉正常喷吹,减少喷吹系统的故障次数,提高高炉利用系数。
三、高炉原料1.优化高炉原料配比高炉原料配比是高炉生产的重要参数之一,优化高炉原料配比可以提高高炉的生产效率。
优化高炉原料配比需要从铁矿石、焦炭、石灰石等多个方面进行考虑,通过调整高炉原料配比,保证高炉炉料的均匀性和稳定性,减少高炉停炉次数,提高高炉利用系数。
2.控制高炉原料粒度高炉原料粒度是高炉生产的重要参数之一,过大或过小的高炉原料粒度都会影响高炉的生产效率。
高炉炼铁对炉料质量的要求及优化配矿技术
高炉炼铁对炉料质量的要求及优化配矿技术王维兴中国金属学会一.高炉炼铁炉料质量对生产有重要意义炼铁学基本理论和高炉生产实践均证明,优化高炉炼铁原燃料的质量和冶金性能既是高炉高效化、大型化、长寿化、节能减排的前提条件,也是提高喷煤比、降低焦比和燃料比的基础条件。
所谓优化炉料质量即是提高炉料质量是入炉矿品位高,渣量少和改善原燃料性能等。
大高炉做到入炉矿品位≥58%、炉料含低SiO2、低Al2O3、低MgO,高炉渣比在300kg/t铁以下,焦炭的反应性(CRI)≤25%,反应后的强度在≥65%等,这是保证高炉生产高效、低耗和大喷煤的必要条件。
1.高炉炼铁是以精料为基础《钢铁产业发展政策》规定:“企业应积极采用精料入炉、富氧喷吹、大型高炉……先进工艺技术和装备。
精料是基础。
国内外炼铁工作者均公认,高炉炼铁是以精料为基础。
精料技术对高炉生产指标的影响率在70%,工长操作水平的影响占10%,企业现代化管理水平占10%,设备作业水平占5%,外界因素(动力、供应、上下工序等)占5%。
在高冶炼强度、高喷煤比条件下,焦炭质量变化对高炉指标的影响率在35%左右。
炼铁精料技术的内涵:精料技术的内容有:高、熟、稳、均、小、净,少,好八个方面⑴高:入炉矿含铁品位高,原燃料转鼓指数高,烧结矿碱度高。
入炉矿品位高是精料技术的核心,其作用:矿品位在57%条件下,品位升高1%,焦比降%~%,产量增加%~%,吨铁渣量减少30公斤,允许多喷煤粉15公斤.;入炉铁品位在52%左右时,品位下降1%,燃料比升高%~%。
高碱度烧结矿是碱度在~2,2(倍),其转鼓强度高、还原性好。
⑵熟:指熟料(烧结和球团矿)比要高,一般>80%。
⑶稳:入炉的原燃料质量和供应数量要稳定。
要求炉料含铁品位波动±<%,碱度波动±<(倍),FeO含量波动±≤%,合格率大于80%~98%等。
详见表4和表5。
⑷均:入炉的原燃料粒度要均匀。
高炉重点技术指标措施
1、综合焦比
①加强热风炉管理,优化烧炉工艺,保证高风温使用,合理控制风口前理论燃烧温度。
②高炉值班室精心操作,根据炉况走势及时调整布料矩阵,合理分布气流,提高煤气利用率。
③高炉日常生产中,加大对操作方针执行情况的考核力度,确保高炉长期稳定顺行及主要经济技术指标完成,为高炉长期高效运行提供管理保障。
2、喷煤比
①加强对原料筛分管理,稳定焦炭质量,改善料柱透气性。
②保证高风温使用,提高风口前理论燃烧温度。
③优化喷煤工艺管理制度,提高操作水平。
3、净铁料耗
①合理调整布料制度,保证中心气流稳定,适当抑制边缘气流的发展,降低高炉灰铁比,降低净铁料耗;
②每班对烧结矿粒度进行检测,及时掌握原料的变化情况,减少入炉粉末。
1880高炉提产增效技术的研究与应用
1880高炉提产增效技术的研究与应用发表时间:2020-07-03T15:55:42.827Z 来源:《科学与技术》2020年6期作者:安进博[导读] 随着山钢集团新旧动能转换,型钢区域需要提高高炉产量摘要:随着山钢集团新旧动能转换,型钢区域需要提高高炉产量。
型钢炼铁厂通过对影响高炉因素进行分析,采取技术措施及创新手段,使1880高炉产量有了较大幅度的提高。
实行1880高炉提产增效技术后,高炉生产稳定性提高,各项生产技术指标提升明显。
1 型钢炼铁厂1880高炉现状型钢炼铁厂拥有2座1880m3高炉,二代炉役分别是1#炉2018年1月21日开炉,2#炉2018年7月12日开炉,开炉顺利达产。
随着山钢集团新旧动能转换,根据公司要求,型钢区域高炉提高产量,1880高炉通过技术创新,按照以稳为进,以退为进,稳中求进的总体思路,采取多种技术措施,高炉的产能进一步提升。
2采取的主要技术管理措施 2.1对外购焦进行质量控制通过向公司营销采购提出铁厂对焦炭质量要求,营销采购对焦炭厂家的焦炭质量及数量实行了更为严格的管理制度,并制定外购焦技术指标(如表1)。
质量不达标,高炉车间根据外购焦质量情况对负荷做出调整,确保炉况稳定。
表1 外购焦技术指标2.2采取精准布料控制,采用时间布料法 1880高炉以前采用圈数布料法,即通过β角编码器进行圈数的读取及档位的步进,布料总时间受编码器读数的限制偏差较大,同样的布料圈数造成总布料时间不一致,影响了布料的稳定性。
1880高炉创新地采用了时间布料法,通过时间计数器的读取进行档位步进,同时根据“十字测温”中心温度的变化,及时调整总布料时间即最小档位的布料时间,进而更精密地调整气流分布。
2.3建立风量与顶压匹配量化关系模型正常炉况下高炉全风作业时顶压采用200kpa,顶压与风量匹配,按照顶压=(0.048-0.05)*风量设定炉顶压力。
提高炉顶压力后,煤气体积缩小,能降低压差,有利于顺行,流速减慢促使煤气在高炉中停留时间延长,提高了煤气利用率,降低了燃料比,有利于顺行。
高炉炼铁基本原理及工艺
30
P ↑易还原
菱
FeCO3
48.2
30~40
25
P,S↓熔烧
后易还原
精品课件
2
各类铁矿石图
磁铁矿
褐铁矿
赤铁矿
精品课件
菱铁矿
3
⑴品位:含铁量,理论上品位↑1%,焦
比↓2%,产量↑ 3%
⑵脉石成分:SiO2、Al2O3↓越好(须重
视Al2O3 ),MgO ↑越好
⑶有害杂质:S、P、Cu、Pb、Zn、As、K
(1)合理布料的意义: ①影响料柱的空隙度 ②不人为调整将产生偏析,煤气自动边缘分布
(2)影响因素: ①布料设备 ②装料制度: 包括:料线、批重、装料次序
精品课件
33
(五)高炉能量利用 1.评价方法:
(1)燃料比 (2)rd (3)C的利用程度ηco 2.煤气上升过程中的变化
精品课件
34
五、高炉强化冶炼手段与方法
②气化脱S(一定值)
③适宜的渣量
(3)炉渣脱S基本反应:
[FeS]+(CaO)=(CaS)+(FeO)
提高炉渣脱S能力的因素:
①↑温度
精品课件 ②↑还原气氛
28
(三)风口前C的燃烧
1.风口前C燃烧的意义
占总C量的70%,其它碳用于:
直接还原:(FeO)+C=[Fe]+CO
(MnO)+C=[Mn]+CO
①C的燃烧速度(一般认为影响不大)
②布料状态(中心堆积,燃烧带小;中心疏 松,燃烧带大)
③鼓风动能EK的大小 (2)影响EK的因素:
①风量↑,EK ↑ ②风温↑,体积膨胀,质量流量↓ ,EK ↓
风温↑ ,速度↑ , EK ↑ 总体EK 略有变化 ③风压↑ , EK ↓ ④风口截面积S ↓, EK ↑
- 1、下载文档前请自行甄别文档内容的完整性,平台不提供额外的编辑、内容补充、找答案等附加服务。
- 2、"仅部分预览"的文档,不可在线预览部分如存在完整性等问题,可反馈申请退款(可完整预览的文档不适用该条件!)。
- 3、如文档侵犯您的权益,请联系客服反馈,我们会尽快为您处理(人工客服工作时间:9:00-18:30)。
大中型高炉技术经济指标改善的条件和途径近一年来,我国一些大中型高炉生产不稳定,技术经济指标下滑。
这与2011年上半年全国重点钢铁企业高炉运行状况是一致的。
反应出,高炉焦比和燃料比升高,喷煤比和利用系数下降等。
这给联合企业生产带来较大的负面影响。
能耗、成本升高,产量下降,经济效益下滑,使企业生产工作量加大。
要用科学发展观去分析,问题出在哪儿?如何去解决?1. 高炉炼铁是以精料为基础国内外炼铁工作者均公认,高炉炼铁是以精料为基础。
精料技术水平,对高炉生产指标的影响率在70%,工长操作水平占10%,企业管理占10%,设备运行状态占5%,外界因素(动力、供应、上下工序等)占5%。
我们要按《高炉炼铁工艺设计规范》中提出的对不同容积高炉,焦炭、烧结矿、球团矿、块矿、喷吹煤粉等的质量要求去组织生产。
目前,炼铁原燃料供应紧张,价格高,且波动大。
造成企业采购有一定难度。
精料技术的核心是要提高入炉矿含铁品位。
含铁品位下降1%,炼铁燃料比下降1.5%,产量下降2.5%,吨铁渣量增加30kg/t,要减少喷煤粉15kg/t.目前,高品位矿价高难买,企业已不再过度追求高品位。
可以采用以下办法提高入炉矿含铁品位:将买来的矿石进行再选,提高球团矿配比,增加高品位块矿使用比例等。
《高炉炼铁工艺设计规范》中对烧结矿质量提出的要求是:铁分波动±≤0.5%,碱度波动±≤0.08%,铁分和碱度波动达标率≥80%~98%;含FeO≤9.0%,波动达标±≤1.0%.目前,一些企业达不到这个标准,严重影响了高炉正常生产。
现在,我国炼铁生产存在的最大问题是生产不稳定,其主要原因是原燃料质量不稳定(特别是焦炭质量变化)。
稳定是高炉生产的灵魂,炼铁企业应当在生产稳定上下功夫。
原燃料波动的影响:品位波动1%,产量影响3.9%~9.7%,焦比2.5%~4.6%. 碱度波动0.1,产量影响2%~4%,焦比1.2%~2.0%。
我们希望,钢铁企业有稳定的原燃料供应基地,可以使高炉炉料质量和数量均有稳定的保证。
烧结矿质量应符合表1的规定。
注:碱度为CaO/SiO2。
球团矿质量应符合表2.的规定。
注:不包括特殊矿石。
入炉块矿质量应符合表3的规定。
原料粒度应符合表4的规定。
焦炭质量应符合表5的规定。
高炉喷吹用煤应根据资源条件进行选择。
喷吹煤质量应符合表6的规定。
表6 喷吹煤质量要求入炉原料和燃料应控制有害杂质量。
其控制宜符合表7的规定。
高炉入炉原料和燃料有害杂质量控制值(kg/t)如下:K2O+Na2O≤3.0 Zn≤0.15 Pb≤0.15As≤0.1 S≤4.0 Cl-≤0.6上述表格数据表明,大型高炉就是需要有高质量的原燃料。
不能抱侥幸心理,用劣质炉料给大型高炉,高炉要是发起脾气,我们再去调整,所花的代价是很大的。
总体上还是开始时就用好炉料,是经济的。
建设大高炉、高炉扩容一定要先提高原燃料质量。
否则,高炉投产后很难达到预想的效果。
鞍钢在上世纪在这方面有过深刻的教训。
2.用生产条件论的观点去分析问题钢铁企业生产是要遵照钢铁冶金学的基本原理,是有着一定的内在规律。
任何先进的技术经济指标的实现均需要有一些技术条件的支撑。
要结合本企业的具体情况,确定影响生产的主要因素在那?这个因素是由哪些条件构成?这些条件中哪些是会产生较大的作用?大中型高炉生产的基本条件:入炉矿品位≥56%,熟料率≥80%,焦炭M40≥82%,M10≤7.5%,有害杂质含量≤3.0kg/t,热风温度≥1200℃。
在高冶炼强度、高喷煤比条件下,焦炭质量变化对高炉生产是起重大影响,对高炉指标影响率在35%左右。
不少大中型高炉生产恶化均是由焦炭重量恶化所引起的。
看焦炭质量不能只看一些数据。
有时会有假象。
鞍山热能院孟庆波副院长提出,影响焦炭质量的主要因素是煤的成因,也就是煤的G值,Y值,胶质层,反射率等。
也就是说,要用煤岩学来进行炼焦配煤。
要定期在高炉休风时,从风口把焦炭,再进行筛分,看其粒度组成,强度变化。
这是最科学判定焦炭质量的方法。
宝钢、武钢等企业就是这么做的。
3.降低燃料比是炼铁工作者得主要工作任务高炉炼铁所需能量有78%是由碳素燃烧获得的,19%是由热风提供的,3%是炉料化学反应热。
燃料比对炼铁工序能耗的影响是占80%以上。
炼铁工序能耗占钢铁联合企业总能耗的50%左右。
降低燃料比是有利于节能和降低生产成本。
表8是降低燃料比的因素。
提高精料水平是企业降低燃料比的主要工作方向。
风温提高是有利于提高喷煤比、降低焦比。
2011年上半年重点钢铁企业燃料比为520kg/t,比上年升高2 kg/t。
与2010年相比有42个企业燃料比在升高,有30个企业燃料比得到下降。
燃料比较低的企业有:宝钢469kg/t,冶钢4698kg/t,首钢472 kg/t,邯钢478 kg/t,兴澄483kg/t,太钢489 kg/t,马钢和昆缸均为491 kg/t,沙钢493 kg/t,青钢499 kg/t,韶钢和柳钢均为503 kg/t,鞍钢501 kg/t,唐钢502 kg/t,衡管504 kg/t,武钢507kg/t.燃料比降低较多的企业有:重钢降29 kg/t,邯钢降20kg/t,锡钢降17 kg/t南昌和新抚钢均降12kg/t,达钢降14kg/t,承钢和徐州均降13kg/t,衡管降11 kg/t,石横、涟钢、敬业和水钢均降8kg/t,酒钢、凌钢、武钢和太钢均降7kg/t,首钢、淮特均降6kg/t。
用生产条件论观点分析燃料比降低的原因:矿品位升高1%,燃料比下降1.5%;风温升高100℃,燃料比下降10~15kg/t;焦炭M40升高1%,燃料比下降5kg/t;M10下降0.2,燃料比下降7kg/t;烧结转鼓提高1%,燃料比下降0.5%等。
表9为部分企业燃料比下降的因素。
国际先进水平的燃料比为480kg/t以下,我国约在550kg/t(包括小块焦)。
4.提高喷煤比是炼铁技术发展的大方向,是降低炼铁成本的主要工作内容目前,我国炼铁原燃料质量在下降,高炉喷煤比也在下降。
2011年上半年重点钢铁企业煤比为147kg/t,比上年下降2kg/t;有36个企业喷煤比与上年相比在下降,下降幅度较多的企业有:水钢降22kg/t,南京降24kg/t,酒钢降21kg/t,邯钢降20kg/t,海鑫降18 kg/t,鄂缸降16kg/t,承钢降15 kg/t,冶钢和锡钢均降13 kg/t,广钢降12 kg/t.有34个企业喷煤比得到提高。
提高喷煤比是炼铁技术发展大方向,可有效低降低炼铁生产成本。
增加喷煤比后,燃料比不升高,是检验提高喷煤比效果的标准。
如果提高喷煤比,使燃料比升高,除尘灰中含碳量升高。
说明多喷的煤粉,没有起到降焦的作用。
就不应当增加喷煤比。
各企业要结合本单位具体情况(特别是原燃料质量水平),确定合理经济喷煤比数值。
现在,企业已不再片面追求高喷煤比,注重提高经济效益,寻求最佳喷煤比。
2011年上半年重点钢铁企业煤比较高的企业有:营口中板191 kg/t,太钢183 kg/t,兴澄177kg/t,青岛和合钢均为176 kg/t, 德龙175 kg/t,武钢174 kg/t,长治173 kg/t,济源、柳钢和新兴铸管均为167 kg/t,莱钢163 kg/t。
提高喷煤比要以提高风温为前提,高风温可补偿因喷煤引起的炉缸理论燃烧温度的降低。
表10是部分企业提高喷煤比和提高风温情况。
实现200kg/t喷煤比的技术条件是:渣量≤300kg/t,风温≥1200℃,富氧在3%左右,脱湿鼓风(湿度在6%左右),煤粉质量好(比焦炭灰分低,含有害杂质低,可磨性、流动性、燃烧性好等)。
目前,炼铁企业不再追求高喷煤比,寻求适合本企业情况的喷煤比,追求高经济效益。
如宝钢将喷煤比由200kg/t,降低到166kg/t,燃料比为469kg/t.5.努力提高热风温度是工作的大方向高风温是廉价的能源,是用45%高炉煤气燃烧得来的,是体现企业能源利用效率高的主要内容,是实现低燃料比的主要措施。
炼铁企业要为实现高风温,做出不断的努力。
目前,我国风温水平与国际先进水平的差距在70℃左右,且热风炉寿命大多数达不到25年。
近年来,我国热风温度不断提高,特别是一些2000M3以上容积的高炉,均实现高风温。
2011年上半年风温水平较高的企业有:太钢1219℃,首钢1217℃,宝钢1210℃,天钢1203℃,攀钢1201℃,济源1196℃,三明1191℃,津西1187℃,重钢1180℃,兴澄1178℃。
提高热风温度的技术措施是:热风炉拱顶使用耐高温的硅砖,热风炉拱顶在烧炉和送风时的温差小于100~150℃,热风炉送风时间要控制在40~60分钟,热风炉蓄热砖要用高蓄热面积的格子砖(由7孔改为19-37孔砖),并涂能吸热材料,提高热风炉废气温度(400~450℃),单烧高炉煤气的热风炉采用煤气和空气双预热技术,送风系统要能承受高风温,高炉能够使用和接受高风温等。
目前我国一些企业热风温度偏低和热风炉寿命偏低(设计规范要求大于25年)的主要原因是使用的耐火砖质量差。
为降低投资,买质量差耐火砖,使风温提达不到高风温水平,造成高炉长期得不到高风温,炼铁焦比高,其经济代价太大。
是得不偿失。
要用技术经济的方法去进行科学计算,确认合理经济的建设和改造热风炉投资原则。
要科学采购耐火砖和热风阀。
采购的原则是:性能、价格、使用寿命、维护费用等方面要综合考虑。
如少水型热风阀寿命可达8~10年,价格比普通的贵20%。
还是要买少水型热风阀。
6.建立现代化企业管理制度6.1.炼铁厂统一管理焦化厂、烧结厂、球团厂。
减少生产管理人员,实现一切为高炉服务,实现效益的最大化,不再当企业之间的裁判员,提高工作效率。
6.2.炼铁厂要参与采购,有语话权。
不能再出现,采购买来什么,炼铁厂只能用什么的现象。
要用技术经济的方法去分析,找出最佳合理矿品位采购值。
采购人员要懂得矿石的化学成分、物理性能、冶金性能对高炉冶炼的影响。
不能只看降低采购成本,而不顾高炉冶炼的效果,以及减产后对炼钢、轧钢的影响,要看企业的最终经济效益如何。
6.3.要实现高炉生产稳定,不能表扬那个工长优秀,要实现统一操作,表扬优秀高炉。
高炉要实现标准化、规范化、数字化操作。
6.4.要承认高炉炼铁有一定的生产规律,有病后,要给一定的恢复时间,不能要求太高、太急。
高炉来病如山倒,祛病如抽丝,治病是个慢功夫。
特别是恢复合理炉型是需要一定的时间。
急了,出现予速而不达的现象。
6.5.2010年部分大高炉指标。