工艺流程简述 (1)
工艺流程简述
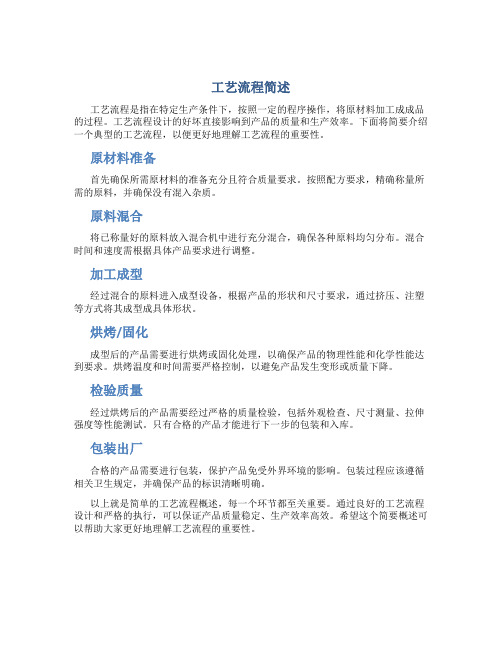
工艺流程简述
工艺流程是指在特定生产条件下,按照一定的程序操作,将原材料加工成成品的过程。
工艺流程设计的好坏直接影响到产品的质量和生产效率。
下面将简要介绍一个典型的工艺流程,以便更好地理解工艺流程的重要性。
原材料准备
首先确保所需原材料的准备充分且符合质量要求。
按照配方要求,精确称量所需的原料,并确保没有混入杂质。
原料混合
将已称量好的原料放入混合机中进行充分混合,确保各种原料均匀分布。
混合时间和速度需根据具体产品要求进行调整。
加工成型
经过混合的原料进入成型设备,根据产品的形状和尺寸要求,通过挤压、注塑等方式将其成型成具体形状。
烘烤/固化
成型后的产品需要进行烘烤或固化处理,以确保产品的物理性能和化学性能达到要求。
烘烤温度和时间需要严格控制,以避免产品发生变形或质量下降。
检验质量
经过烘烤后的产品需要经过严格的质量检验,包括外观检查、尺寸测量、拉伸强度等性能测试。
只有合格的产品才能进行下一步的包装和入库。
包装出厂
合格的产品需要进行包装,保护产品免受外界环境的影响。
包装过程应该遵循相关卫生规定,并确保产品的标识清晰明确。
以上就是简单的工艺流程概述,每一个环节都至关重要。
通过良好的工艺流程设计和严格的执行,可以保证产品质量稳定、生产效率高效。
希望这个简要概述可以帮助大家更好地理解工艺流程的重要性。
生产工艺流程简述(3篇)
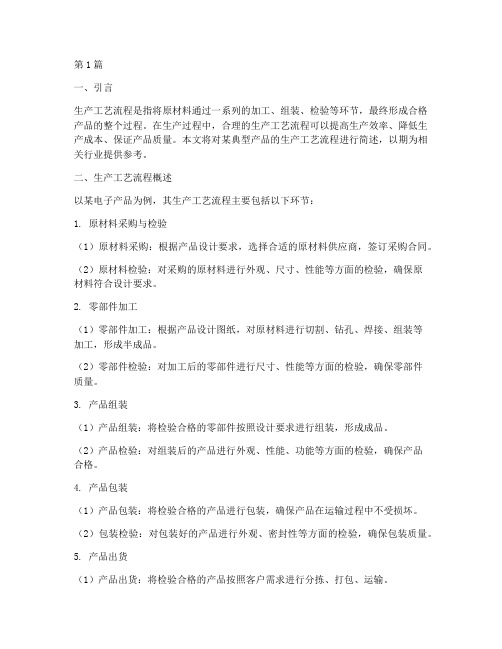
第1篇一、引言生产工艺流程是指将原材料通过一系列的加工、组装、检验等环节,最终形成合格产品的整个过程。
在生产过程中,合理的生产工艺流程可以提高生产效率、降低生产成本、保证产品质量。
本文将对某典型产品的生产工艺流程进行简述,以期为相关行业提供参考。
二、生产工艺流程概述以某电子产品为例,其生产工艺流程主要包括以下环节:1. 原材料采购与检验(1)原材料采购:根据产品设计要求,选择合适的原材料供应商,签订采购合同。
(2)原材料检验:对采购的原材料进行外观、尺寸、性能等方面的检验,确保原材料符合设计要求。
2. 零部件加工(1)零部件加工:根据产品设计图纸,对原材料进行切割、钻孔、焊接、组装等加工,形成半成品。
(2)零部件检验:对加工后的零部件进行尺寸、性能等方面的检验,确保零部件质量。
3. 产品组装(1)产品组装:将检验合格的零部件按照设计要求进行组装,形成成品。
(2)产品检验:对组装后的产品进行外观、性能、功能等方面的检验,确保产品合格。
4. 产品包装(1)产品包装:将检验合格的产品进行包装,确保产品在运输过程中不受损坏。
(2)包装检验:对包装好的产品进行外观、密封性等方面的检验,确保包装质量。
5. 产品出货(1)产品出货:将检验合格的产品按照客户需求进行分拣、打包、运输。
(2)出货检验:对出货的产品进行数量、质量等方面的检验,确保产品符合客户要求。
三、生产工艺流程优化措施1. 优化原材料采购与检验(1)建立长期稳定的原材料供应商关系,降低采购成本。
(2)采用先进的检验设备和技术,提高检验效率和质量。
2. 优化零部件加工(1)引进先进加工设备,提高加工精度和效率。
(2)优化加工工艺,降低加工成本。
3. 优化产品组装(1)采用模块化设计,提高组装效率。
(2)加强组装人员培训,提高组装质量。
4. 优化产品包装(1)采用环保、安全的包装材料,降低生产成本。
(2)优化包装设计,提高包装质量。
5. 优化产品出货(1)加强物流管理,提高运输效率。
工艺流程图
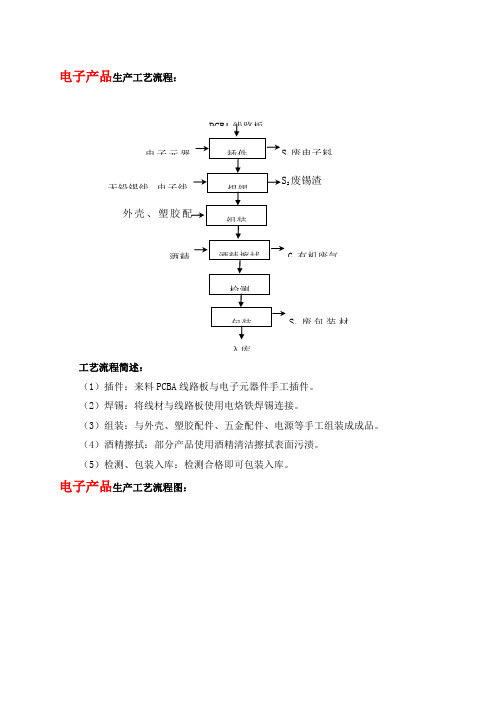
电子产品生产工艺流程:工艺流程简述:(1)插件:来料PCBA 线路板与电子元器件手工插件。
(2)焊锡:将线材与线路板使用电烙铁焊锡连接。
(3)组装:与外壳、塑胶配件、五金配件、电源等手工组装成成品。
(4)酒精擦拭:部分产品使用酒精清洁擦拭表面污渍。
(5)检测、包装入库:检测合格即可包装入库。
电子产品生产工艺流程图:废电子料 外壳、塑胶电子元S 3废包装材废锡渣 无铅锡线、电子线G 2有机废气 入库工艺流程简述:(1)点焊:项目电子产品的生产工艺较简单,首先用电烙铁将外购的PCBA 线路板与电子元件进行点焊连接。
(2)粘胶:项目部分电子元件需用黄胶进行粘贴,通过粘胶的方式将其固定在线路板上。
(3)组装:然后与外购的五金配件、塑胶配件用电批进行组装在一起。
(4)检测、包装:产品组装完成后,用测试设备对产品进行测试,检测合格后即 可将产品包装为成品。
电子元器件生产工艺流程图及污染物标识(废水:W ;废气:G ;固废:S ;噪声:N )成品2焊锡废气、S 3废锡S 5包装废料 S 4废电子料 电子元件、有机废气、S 6废胶工艺简述:(1)绕线、剪线头:来料骨架使用绕线机将漆包线绕至骨架上,然后人工剪去多余线头。
(2)浸锡、补焊:将产品骨架针脚与漆包线接合处浸锡焊接,浸锡时需按一定比例加入一定量的环保助焊剂辅助焊接,少部分浸锡不合格产品使用电烙铁补焊连接。
(3)装磁芯、包胶带:人工将磁芯安装在骨架上,部分需用手啤机压合组装,然后在骨架上用包胶带机包裹上胶带。
(4)测试:用测试仪对产品半成品性能进行测试。
(5)浸油、烘烤:将产品送至含浸机中浸绝缘油,使产品具备绝缘性质,浸油时绝缘油中需加入一定比例的天那水进行稀释,浸油后的产品送至电烤箱烘烤固定,电烤箱工作温度约95~100℃。
包装出货无铅锡条、无铅锡1废线头 3废胶带 2有机废气 5废包装材料 设备噪声 G 1焊锡废气、G 2有机废N 设备噪声(6)包装出货:产品烘烤后即可包装为成品。
工艺流程及简述

工艺流程及简述
《工艺流程简介》
工艺流程是指在生产过程中,产品从原材料开始经过一系列的加工、处理、组装等步骤,最终形成成品的整个过程。
每一个工艺流程都是为了满足产品质量、成本和交货时间等方面的要求而设计的。
工艺流程的优化和改进对于企业的生产效率和产品质量有着直接的影响。
一个典型的工艺流程通常包括以下几个步骤:
1.原材料准备:在这个阶段,原材料经过采购、检验、储藏等流程,保证原材料的质量和数量符合要求。
2.加工制造:在这个阶段,原材料通过加工、成型、组装等工序,逐步转化成中间品或成品。
3.检验质量:在每一个加工制造的环节,都需要进行质量的检验,保证产品的合格率和质量符合标准。
4.包装输送:在产品制造完成后,需要进行包装和输送,以便于产品的运输和存储。
在实际的生产过程中,工艺流程的优化可以通过如下几个方面来实现:
1.技术改进:引入新的加工工艺、设备或材料,以提高生产效
率和产品质量。
2.流程优化:通过分析生产流程中的瓶颈和低效环节,进行调整和改进,减少生产成本并提高生产效率。
3.自动化改造:引入自动化设备,降低人力成本,提高生产效率和产品一致性。
4.质量管理:通过建立严格的质量管理体系,加强质量控制,提高产品的质量和合格率。
在竞争日益激烈的市场环境中,工艺流程的优化和改进是企业不断提高竞争力的关键。
只有不断地寻求改进和创新,才能在激烈的市场竞争中脱颖而出。
工艺流程简述:

生产工艺流程图主要生产工艺流程简述:1、运检:由采购部门购进含材质单的钢管,检查人员进行外观和利用检验设备检查后、运到生产车间。
2、胀头:首先利用高频加热箱对钢管进行加热,再采用液压机将钢管两端扩径。
3、齐头:采用锯床,按照相关标准将钢管两端切齐。
4、平头:采用动力头设备将钢管端面加工平整。
5、喷砂和抛丸:利用喷砂机将钢管内表面的锈层和毛刺清洗光滑,采用抛丸机将钢管外表面的锈层和毛刺清洗光滑。
每台喷砂机和抛丸机分别配套一台布袋式除尘器。
6、包管:利用包管机将保温材料缠绕在内管上,形成保温层。
7、烘干:利用电加热炉将缠绕在保温管材料的钢管烘干。
此工序会有少量水蒸气产生,无组织排放于车间内部。
8、穿管:利用拉管机将内、外钢管穿连在一起,待用。
9、焊头:利用半自动焊机将内、外钢管两端焊接上,再利用二氧化碳气体保护焊对焊缝进行封闭,焊接材料为焊丝。
无废焊接材料产生。
本项目焊接机全部采用半自动化设备,并配备4套移动式收尘箱。
4套除尘箱为移动设备,对使用中的焊接机进行除尘。
10、探伤:采用超声波动探伤设备检验焊接处是否有缺陷。
11、加热:采用电加热炉将内、外钢管之间空隙处的湿气烘干。
此工序会有少量水蒸气产生,无组织排放于车间内部。
12、真空:首先,用台钻将钢管钻孔,再利用罗茨真空泵将内、外钢管之间空隙处抽成真空,增加保温性能。
再利用半自动点焊机将孔焊接堵住,最后用半自动小焊机补平小空隙和凸凹不平的表面。
13、螺纹:利用数控管螺纹车床,将钢管两端车上螺纹。
本工序采用切屑液、切屑液起到冷却和润滑作用,循环使用,随时添加,不外排。
14、管头:利用管头上丝机,将钢管一端接上管头。
15、喷漆:将钢管外层表面喷砂,本项目喷漆采用大型喷漆设备,利用空压机提供动力、采用喷枪喷漆。
本项目油漆主要为醇酸调和漆,松香水为稀释剂。
16、检查入库:采用水压设备检查成品管的气密性和耐压性能,经检查人员检查外观合格后,入库待销。
生产工艺流程图:S1W1S4 图例:G—大气污染物W—废水污染物N—噪声S—固体废物建设项目污染防治措施及预期治理效果大气污染物喷砂机和抛丸机工作过程中,会产生金属粉尘,项目单位为每台喷砂机和抛丸机分别配备一套YTL-9型布袋除尘器,除尘效率为99.9%。
设备制造产品生产工艺简述

设备制造产品生产工艺简述公司属于通用设备制造业,主要生产轮式装载机、农机驱动桥系列产品,每一道生产工序都要经检验合格后,方可进入下一道工序。
其中,轮式装载机生产工艺主要是将各类原材料按照施工样图用切割机进行切割下料,检验合格后,进行机加工,用焊机进行阻焊、电焊,外形尺寸无损检验后,进行磷化外协加工,运回公司内,进行喷底漆,装配,或直接采用外购件、外协件、标准件、电气件进行总装,试车,喷面漆,凉干验收合格后入库。
其中,农机驱动桥系列产品生产工艺主要是装配。
生产工艺流程图如下:下料机加工焊接磷化(外协)外购件喷底漆外协件装配(总装)标准件试车电气件喷面漆入库主要工艺流程简述:(1)机加工,外购钢材经检验后进行机械加工,机械加工的工序主要由车、铣、钻、攻丝、数控加工中心加工等工序。
①车床加工由普通车床和数控车床完成,主要加工轴、孔套等部件;②铣床加工由普通铣床和数控铣床完成,主要加工平面及精密中心距的孔,数控铣床也可镗孔和钻孔;③钻床加工由摇臂钻床完成,利用钻头和定位工装,对工件进行钻出固定孔及攻丝的底孔;④攻丝加工由攻丝机完成,主要工件上攻制螺纹孔;⑤数控加工中心加工,主要加工形状较为复杂的板簧类零件,可一次装夹定位完成铣、镗、钻、攻、铰等多个工序。
⑥抛丸处理,利用抛丸机清理工件表面,设备型号为Q3730,将表面的氧化皮及锈蚀清理干净,清理完后用角磨机手工打磨干净工件上的毛刺。
(2)半成品巡检,机械加工过程中要进行巡检,保证产品质量,检测重点、主要尺寸,防止出现批量不合格件。
(3)焊接,主要是组焊和电焊,其中组焊是将各组件依次摆放到工装上,调整工件位置,按照图纸进行装配,然后进行点固、打磨、焊接成型。
(4)磷化过程进行外协,公司只做好机罩(薄板件),联系泰安专门的磷化酸洗厂完成该工序。
(5)喷漆,主要是防锈底漆涂装和表面涂装。
在喷漆房内喷涂,人工将工件推进喷漆房,关上喷漆房大门,启动控制柜,进行喷漆作业。
工艺流程简述
工艺流程简述霍家工业树脂厂工艺流程1离子膜烧碱工艺流程说明(1)一次盐水工序来自电解的淡盐水进入化盐水贮槽,经化盐水泵被送入化盐桶,原盐由皮带输送机送入化盐桶顶部,化盐水溶解原盐后的饱和粗盐水从化盐桶溢流口流出,粗盐水流经反应器,与精制剂氯化钡,氢氧化钠,次氯酸钠混合后经前反应罐进入中间槽,再由泵将粗盐水经气水混合器送入加压溶气罐,减压后加入三氯化铁进入预处理器,除去有机物及氢氧化镁等杂质,从溢流口流出,流经反应器与碳酸钠混合后进入后反应罐,经机械搅拌后进入滤料槽,充分反应后的盐水自流进入HVM 过滤器,去除碳酸钙,硫酸钡等杂质,过滤后的盐水由过滤器上部溢流出,同时加入5%亚硫酸钠溶液除去盐水中的游离氯,后进入精盐水储槽,精盐水由精盐水泵送往二次盐水精制工序。
渣池中的盐泥浆用盐泥泵打入板框压滤机经压滤,滤饼运出界区,滤液流入滤液槽,再用泵送入后反应罐。
(2)二次盐水精制工序由一次盐水工序的精盐水泵送来的精盐水,进入精盐水储槽,由精盐水泵送入螯合树脂塔对盐水进行二次精制,装置设有三台树脂塔,正常运行期间为二塔串联运行,一塔线外再生,精制后盐水中的钙镁含量小于0.02mg/l ,然后送电解系统。
树脂塔再生时需要用的烧碱,高纯酸,纯水等,分别由装置内储罐经泵供给。
再生废液进入再生废水槽,由再生废水泵输送至废水处理,经中和后,达标后排放。
(3)离子膜电解工序通过树脂塔来的合格的二次精制盐水进入盐水高位槽,通过位差,进入离子膜电解槽的阳极室电解,生成氯气,同时使盐水浓度降低成为含氯淡盐水,淡盐水与氯气一起进入淡盐水储槽进行气液分离,氯气送至氯气处理工序,一部分淡盐水与通过树脂塔来的二次精制盐水混合,作循环盐水送入离子膜电解槽的阳极室,继续电解,一部分通过淡盐水泵送到脱氯塔。
电解槽阴极室出来的电解液,进入碱液储槽进行气液分离,分离后的氢气送至氢气处理工序,电解液通过碱液泵一部分进入碱高位槽,通过位差且经过纯水稀释后给电解槽循环使用;一部分由泵打到成品碱储槽,由成品碱泵送到液碱储运工序。
工艺流程简述范文
工艺流程简述范文工艺流程是指将原材料经过一系列的加工和处理工序,按照特定的方法和顺序,最终转化为符合特定要求的成品的过程。
不同行业和不同产品的工艺流程也会有所不同,下面以制造流程为例,对工艺流程进行简述。
工艺流程根据产品的不同特点和工艺要求而不同,但通常包括以下几个主要步骤。
1.原材料准备:这是工艺流程的第一步,主要是对原料进行检验和准备,确保原料质量合格。
同时根据产品的需求,对原料进行切割、分类等处理,为后续工序做好准备。
2.加工与成型:在这个环节中,原材料经过加工和成型工序的处理,使其逐渐转变为成品的形态。
具体工艺包括铸造、锻造、冲压、挤压、焊接、切割、热处理等。
这些工艺的目的是通过改变原材料的形状和结构,使其符合产品的设计要求。
3.表面处理:在加工与成型之后,产品的表面通常需要进行处理,以改善产品的外观和性能。
常见的表面处理工艺包括电镀、喷涂、镀膜、抛光等。
这些工艺的目的是提高产品的耐腐蚀性、耐磨性和装饰性。
4.组装与装配:该环节是将加工好的零部件进行组装和装配,形成最终的成品。
这包括零部件的组织、调试、连接、固定等工序,以确保产品的完整性和可靠性。
同时,也可能涉及到与其他配套设备或部件的连接和配合。
5.检测与质量控制:在制造过程中,需要对产品进行检测和质量控制,以确保产品质量符合要求。
这包括原材料的检验、工艺过程中的中控检测以及最终产品的成品检验。
常用的检测手段包括物理测量、化学分析、无损检测等方法。
6.包装与运输:在产品制造完成后,需要进行包装和运输工作,使得成品能够安全地送到客户手中。
包装的目的是保护产品,减少运输过程中的损坏和变形。
同时,也可以利用包装来提高产品的附加值,增加产品的市场竞争力。
运输方式则根据产品的性质和客户要求来决定,可以有陆运、海运、航空等选择。
7.售后服务:在产品交付给客户后,还需要提供售后服务,以解决产品使用过程中出现的问题,或是提供技术支持和维修等服务。
良好的售后服务可以提高客户的满意度,增加客户的忠诚度,从而促进企业的发展。
MTO工艺简述
(一)、MTO装置工艺流程简述MTO装置由甲醇制烯烃单元、烯烃分离单元组成,其中甲醇制烯烃单元包括反应再生系统,取热系统,急冷、汽提系统;烯烃分离单元包括进料气压缩、酸性气体脱除和废碱液处理系统,进料气体和凝液干燥系统,气体再生部分,脱丙烷系统,脱甲烷系统,脱乙烷系统、乙炔加氢,乙烯精馏塔,丙烯精馏塔,脱丁烷塔,丙烯制冷系统。
(1)甲醇制烯烃1)进料汽化和产品急冷区进料汽化和产品急冷区由甲醇进料缓冲罐,进料闪蒸罐,洗涤水汽提塔,急冷塔,产品分离塔和产品/水汽提塔组成。
来自于罐区的甲醇经过与汽提后的水换热,在中间冷凝器中部汽化后进入进料闪蒸罐,然后进入汽化器汽化,并用蒸汽过热后送入MTO反应器。
反应器出口物料经冷却后送入急冷塔。
闪蒸罐底部少量含水物料进入氧化物汽提塔中。
一些残留的甲醇被汽提返回到进料闪蒸罐。
急冷塔用水直接冷却反应后物料,同时也除去反应产物中的杂质。
水是MTO反应的产物之一,甲醇进料中的大部分氧转化为水。
MTO反应产物中会含有极少量的醋酸,冷凝后回流到急冷塔。
为了中和这些酸,在回流中注入少量的碱(氢氧化钠)。
为了控制回流中的固体含量,由急冷塔底抽出废水,送到界区外的水处理装置。
急冷塔顶的气相送入产品分离器中。
产品分离器顶部的烯烃产品送入烯烃回收单元,进行压缩,分馏和净化。
自产品分离器底部出来的物料送入水汽提塔,残留的轻烃被汽提出来,在中间冷凝器中与新鲜进料换热后回到产品分离器。
汽提后底部的净产品水与进料甲醇换热冷却到环境温度,被送到界区外再利用或处理。
洗涤水汽提塔底主要是纯水,送到轻烯烃回收单元以回收MTO生成气中未反应的甲醇。
水和回收的甲醇返回到氧化物汽提塔,在这里甲醇和一些被吸收的轻质物被汽提,送入进料闪蒸罐。
气体后的水返回氧化物汽提塔。
2)流化催化反应和再生区MTO的反应器是快速流化床型的催化裂化设计。
反应实际在反应器下部发生,此部分由进料分布器,催化剂流化床和出口提升器组成。
工艺流程及简述
工艺流程及简述工艺流程及简述一、简述工艺流程是指为了完成某项生产任务,按照一定的工艺路线和工艺步骤,利用一定的工艺装备和工艺条件,进行一系列工艺操作和工艺控制的过程。
它是一种合理组织和高效控制生产过程的方法。
工艺流程制定合理,可以提高生产效率,降低生产成本,提高产品质量。
二、工艺流程的组成工艺流程一般由以下几个组成部分构成:1. 前处理:包括原料采集、分选、清洗、预处理等工艺操作,以便使原料符合生产要求。
2. 加工过程:根据产品的需要,对原料进行物理、化学和生物处理等工艺操作,包括加工、混合、热处理、分离等过程。
3. 后处理:对产品进行检测、包装、贮存、运输等处理,以保证产品质量,方便使用。
4. 控制措施:在整个工艺流程中,需要有合适的控制措施进行监测和调控,以确保生产稳定进行,产品质量符合要求。
三、工艺流程的制定制定工艺流程需要考虑以下几个方面的因素:1. 原料特性:了解原料的物理、化学特性,包括成分、性质、形态等,以确定选择合适的加工工艺。
2. 产品要求:明确产品的质量要求,包括外观、性能、使用环境等,以确定制定工艺流程的重点和关键控制环节。
3. 设备条件:评估现有的设备配备情况,根据设备的性能和效率,确定工艺流程的具体操作步骤。
4. 能源消耗:优化工艺流程,减少能源消耗,提高生产效率。
5. 安全环保:考虑生产过程对环境和员工的影响,制定相应的环保和安全操作规程。
四、工艺流程的优化工艺流程制定完毕后,可以通过以下几个方面的优化来提高生产效率和产品质量:1. 设备改进:引进新的工艺设备,提高生产效率和产品质量。
2. 工艺改进:优化工艺流程,减少工艺操作环节,缩短生产周期。
3. 控制改进:引入先进的控制系统,提高生产自动化程度,降低人工操作的干预。
4. 能耗改进:优化能源消耗,改进工艺参数,提高能源利用效率。
5. 质量改进:加强质量检测和控制,提高产品的一致性和稳定性。
总之,工艺流程是对生产过程进行合理规划和控制的方式,能够提高生产效率,降低生产成本,提高产品质量。
- 1、下载文档前请自行甄别文档内容的完整性,平台不提供额外的编辑、内容补充、找答案等附加服务。
- 2、"仅部分预览"的文档,不可在线预览部分如存在完整性等问题,可反馈申请退款(可完整预览的文档不适用该条件!)。
- 3、如文档侵犯您的权益,请联系客服反馈,我们会尽快为您处理(人工客服工作时间:9:00-18:30)。
工艺流程简述
本装置由预处理净化、加热炉、催化反应及分馏四部分组成。
一、原料油预处理净化部分
青岛胶州鑫星烯烃厂独创的“催化降凝”再生基础油和燃油技术,对矿物油原料的适应性强,催化剂、吸附剂使用安全系数高,催化效果大,产品质量稳定,避免了酸碱淬洗等二次污染。
出油率83%以上,密度(20℃)0.84,十六烷值50以上,色度似啤酒色,清澈透明,无异味。
原料油由卸车台经初滤进入原料油储罐中,经预热室加热至60-80度,经管道送至沉降塔进行初期脱水、泥、沙和金属粉末等,以减少机械杂质灰分含量,再经过滤后送至换热器二次脱水、脱轻,防止加热炉炉管结焦和催化剂过早、过快失活。
二、加热炉部分
经一级预处理后原料油,由原料油换热器经换热后,换热到150度以上进行脱水脱轻后进入管式炉进行闪蒸。
闪蒸后进入初分塔经过真空泵抽负压使油气达塔顶。
初分塔底油经过初分塔底调解流出,轻重分离,加热炉辐射室温度为620度左右,操作压力为微负压,原料油进炉速度掌握在1.5t/h,加热炉出口温度在400度,送入初分塔进行分离,初分塔顶温度为360度左右,微负压。
初分塔中最下部油通过换热器、冷却水箱进入渣油缓冲罐经过渣油泵外送出装置。
三、催化反应部分
初分塔中除了塔底部分渣油排除装置外,初分塔塔顶气化出来的产物油气从初分塔顶进入催化反应器中,自下而上,进行催化吸附反应,催化塔顶压力为-0.01Mpa,催化塔中的催化剂工作温度范围在320-420度。
催化后的产物由催化反应塔上部出口进行换热器再经冷却器冷凝后,进入过滤器送入成品罐。
四、分馏部分
轻组分油经换热器换热至150度时抽出,经油水分离后送至加热炉经吸附整流至馏分油内。
初分塔底在400-420度时分馏出重油,经换热后送入重油罐。
产品方案。