铝合金铸件气孔
铝合金铸件气孔标准
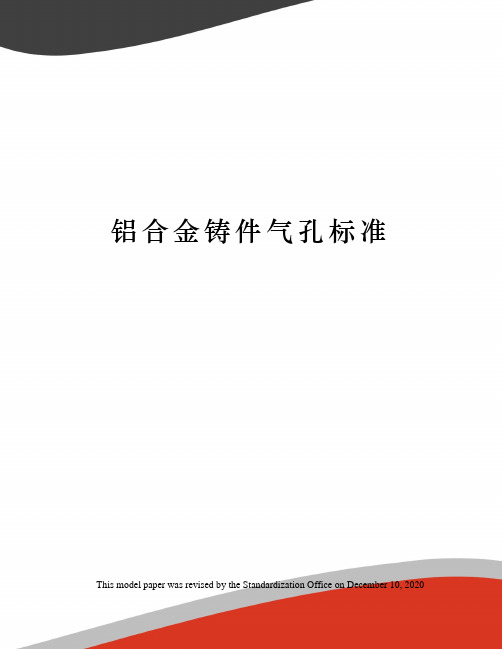
铝合金铸件气孔标准This model paper was revised by the Standardization Office on December 10, 2020铝合金铸件气孔、针孔检验标准一.适用范围本标准规定了铸件气孔、针孔允许存在的范围、大小、数量等技术要求。
本标准规定了铸造铝合金低倍针孔度的分级原则和评级方法。
本标准适用于铝合金的砂型铸造。
适用于评定铸件外表面及需要加工面经加工后的表面气孔、针孔。
二.引用标准GB1173-86铸造铝合金技术条件GB9438-88铝合金铸件技术条件GB10851-89铸造铝合金针孔三.气孔、针孔等孔洞类特征1.位于铸件内部而不延伸到铸件外部的气眼。
(1)气孔、针孔内壁光滑,大小不等的圆形孔眼,单个或成组无规则的分布在铸件的各个部位。
(2)气渣孔其特征同气孔、针孔相似,但伴随有渣子。
2.表面或近表面的孔眼,大部分暴露或与外表面相连。
(1)表面或皮下气孔大小不等的单个或成组的孔眼,位于铸件表面或近表面的部位,其内壁光滑。
(2)表面针孔铸件表面上细小的孔洞,呈现在较大的区域上。
四.具体条件1.砂型、金属型铸件的非加工表面和加工表面,在清整干净后允许存在下列孔洞:(1)单个孔洞的最大直径不大于3mm,深度不超过壁厚1/3,在安装边上不超过壁厚的1/4,且不大于1.5mm,在上述缺陷的同一截面的反面对称部位不得有类似的缺陷。
(2)成组孔洞最大直径不大于2mm,深度不超过壁厚的1/3,且不大于1.5mm。
(3)上述缺陷的数量及边距应符合表一规定表一非加工表面或加工表面总面积小于1000cm2 单个孔洞成组孔洞在10cm×10cm单位面积上孔洞数不多于4个孔洞边距不小于10mm一个铸件的非加工表面或加工面上孔洞总数不多于6个,孔洞边缘距铸件或距内孔边缘的距离不小于孔洞最大直径的2倍以3cm×3cm单位面积为一组,其孔洞数不多于3个在一个铸件上组的数量不多于2组孔洞边缘距铸件边缘或距内孔边缘的距离不小于孔洞最大直径的2倍2.液压、气压件的加工表面上,铸件以3级针孔作为验收基础,要求2级针孔占受检面积的25%以上,局部允许4级针孔,但一般不得超过受检面积的25%,当满足用户对致密性的技术要求时或对其它砂型、金属型铸件允许按低一级的针孔度验收。
气孔类别

本文从铝合金铸件气孔类别分析入手,指出铝合金铸件气孔可分为点状针孔、网状针孔、综合性针孔三类;氢是造成铝合金铸件针孔的主要原因,而氢的主要来源则是由于水蒸气分解所产生的。
因此,铝合金在熔炼过程中造成水蒸气产生的原因,也就是直接影响针孔形成的主要因素。
由于铝合金铸件气孔对铸件的品质尤其是对其力学性能产生不良的影响,作者在文中论述了铝合金铸件气孔形成的主要因素,并针对铝合金铸件气孔形成的主要因素提出了相应的预防措施,文章最后扼要总结了预防铝合金铸件针孔必须遵守的“防”、“排”、“溶”工艺原则。
引言:在纯铝中加入一些金属或非金属元素所熔制的铝合金是一种新型的合金材料,由于其比重小,比强度高,具有良好的综合性能,因此被广泛用于航空工业、汽车制造业、动力仪表、工具及民用器具制造等方面。
随着国民经济的发展以及经济一体化进程的推进,其生产量和耗用量大有超过钢铁之势。
加强对铝合金材料性能的研究,保证铝合金铸件具有优良品质,既是我们每一个科技工作者义不容辞的责任,也是同我们的日常生活息息相关的头等大事。
本文结合作者铝合金铸件生产实践经验谈谈铝合金铸件气孔与预防问题。
1.气孔类别由于铝合金具有严重的氧化和吸气倾向,熔炼过程中又直接与炉气或外界大气相接触,因此,如熔炼过程中控制稍许不当,铝合金就很容易吸收气体而形成气孔,最常见的是针孔。
针孔(gas porosity/pin-hole),通常是指铸件中小于1mm的析出性气孔,多呈圆形,不均匀分布在铸件整个断面上,特别是在铸件的厚大断面和冷却速度较小的部位。
根据铝合金析出性气孔的分布和形状特征,针孔又可以分为三类①,即:(1) 点状针孔:在低倍组织中针孔呈圆点状,针孔轮廓清晰且互不连续,能数出每平方厘米面积上针孔的数目,并能测得出其直径。
这种针孔容易与缩孔、缩松等予以区别开来。
(2) 网状针孔:在低倍组织中针孔密集相连成网状,有少数较大的孔洞,不便清查单位面积上针孔的数目,也难以测出针孔的直径大小。
铝压铸件产生气孔的可能原因精选版

铝压铸件产生气孔的可能原因Document serial number【KKGB-LBS98YT-BS8CB-BSUT-BST108】铝压铸件产生气孔的可能原因(供参考)一.人的因素:1.脱模剂是否喷得太多因脱模济发气量大,用量过多时,浇注前未燃尽,使挥发气体被包在铸件表层。
所以在同一条件下,某些工人操作时会产生较多的气孔的原因之一。
选用发气量小的脱模济,用量薄而均匀,燃净后合模。
2未经常清理溢流槽和排气道3开模是否过早是否对模具进行了预热各部位是否慢慢均匀升温,使型腔、型芯表面温度为150℃~200℃。
4刚开始模温低时生产的产品有无隔离5如果无预热装置时是否使用铝合金料慢速推入型腔预热或用其它方法加热6是否取干净的铝液,有无将氧化层注入压室7倒料时,是否将勺子靠近压室注入口,避免飞溅、氧化或卷入空气降温等。
8金属液一倒入压室,是否即进行压射,温度有无降低了。
9冷却与开模,是否根据不同的产品选择开模时间10有无因怕铝液飞出(飞水),不敢采用正常压铸压力更不敢偿试适当增加比压。
11操作员有无严格遵守压铸工艺12有无采用定量浇注如何确定浇注量二.机(设备、模具、工装)的因素:主要是指模具质量、设备性能。
1压铸模具设计是否合理,会否导致有气孔压铸模具方面的原因:1.浇口位置的选择和导流形状是否不当,导致金属液进入型腔产生正面撞击和产生旋涡。
(降低压射速度,避免涡流包气)2.浇道形状有无设计不良3.内浇口速度有无太高,产生湍流4.排气是否不畅5.模具型腔位置是否太深6.机械加工余量是否太大穿透了表面致密层,露出皮下气孔压铸件的机械切削加工余量应取得小一些,一般在左右,既可减轻铸件重量、减少切削加工量以降低成本,又可避免皮下气孔露出。
余量最好不要大于,这样加工出来的面基本看不到气孔的,因为有硬质层的保护。
2排气孔是否被堵死,气排不出来3?冲头润滑剂是否太多,或被烧焦这也是产生气体的来源之一。
4?浇口位置和导流形状,有无金属液先封闭分型面上的排溢系统5内浇口位置是否不合理,通过内浇口后的金属立即撞击型壁、产生涡流,气体被卷入金属流中6?排气道位置不对,造成排气条件不良5?溢气道面积是否够大,是否被阻塞,位置是否位於最后充填的地方模具排气部位是否经常清理避免因脱模剂堵塞而失去排气作用。
压铸件气孔的成因和解决办法
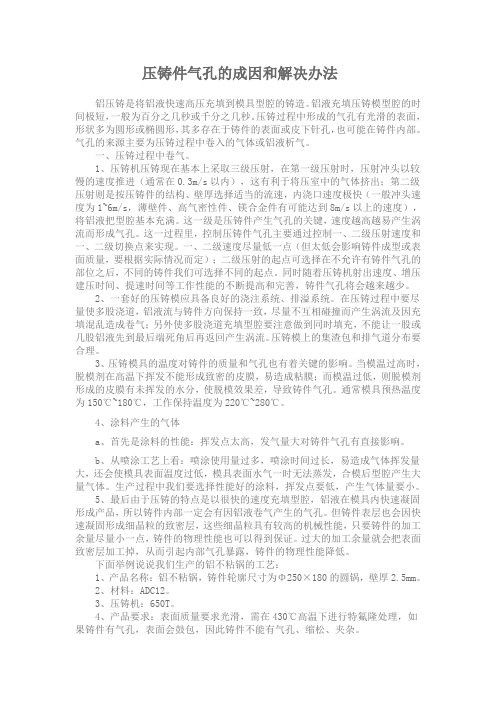
压铸件气孔的成因和解决办法铝压铸是将铝液快速高压充填到模具型腔的铸造。
铝液充填压铸模型腔的时间极短,一般为百分之几秒或千分之几秒。
压铸过程中形成的气孔有光滑的表面,形状多为圆形或椭圆形,其多存在于铸件的表面或皮下针孔,也可能在铸件内部。
气孔的来源主要为压铸过程中卷入的气体或铝液析气。
一、压铸过程中卷气。
1、压铸机压铸现在基本上采取三级压射,在第一级压射时,压射冲头以较慢的速度推进(通常在0.3m/s以内),这有利于将压室中的气体挤出;第二级压射则是按压铸件的结构、壁厚选择适当的流速,内浇口速度极快(一般冲头速度为1~6m/s,薄壁件、高气密性件、镁合金件有可能达到8m/s以上的速度),将铝液把型腔基本充满。
这一级是压铸件产生气孔的关键,速度越高越易产生涡流而形成气孔。
这一过程里,控制压铸件气孔主要通过控制一、二级压射速度和一、二级切换点来实现。
一、二级速度尽量低一点(但太低会影响铸件成型或表面质量,要根据实际情况而定);二级压射的起点可选择在不允许有铸件气孔的部位之后,不同的铸件我们可选择不同的起点。
同时随着压铸机射出速度、增压建压时间、提速时间等工作性能的不断提高和完善,铸件气孔将会越来越少。
2、一套好的压铸模应具备良好的浇注系统、排溢系统。
在压铸过程中要尽量使多股浇道,铝液流与铸件方向保持一致,尽量不互相碰撞而产生涡流及因充填混乱造成卷气;另外使多股浇道充填型腔要注意做到同时填充,不能让一股或几股铝液先到最后端死角后再返回产生涡流。
压铸模上的集渣包和排气道分布要合理。
3、压铸模具的温度对铸件的质量和气孔也有着关键的影响。
当模温过高时,脱模剂在高温下挥发不能形成致密的皮膜,易造成粘膜;而模温过低,则脱模剂形成的皮膜有未挥发的水分,使脱模效果差,导致铸件气孔。
通常模具预热温度为150℃~180℃,工作保持温度为220℃~280℃。
4、涂料产生的气体a、首先是涂料的性能:挥发点太高,发气量大对铸件气孔有直接影响。
铝合金压铸件中产生气孔的原因分析

铝合金压铸件中产生气孔的原因分析摘要:铝合金压铸件中气孔是比较常见的缺陷问题,不仅对压铸件的美观造成不良影响,也会导致压铸件质量受到影响,为此需要合理分析铝合金压铸件中气孔产生的主要原因,并采取有效的措施进行控制。
铝合金压铸件气孔产生与原材料的选择、压铸工艺的控制、压铸机选择和涂料因素等密切相关,因此需要格外重视其压铸时的原材料、压铸工艺合理控制,挑选性能优质合格的压铸机和涂料,更好的保证其压铸质量。
关键词:铝合金压铸件;气孔;原因气孔是铝合金压铸件中最常出现的缺陷问题,大多出现在铝合金压铸件的表面或者皮下针孔,也有部分气孔可能在铸件内部。
气孔对铝合金压铸件的质量具有一定负面影响,不仅影响了构件的美观,同时过多的气孔也会使其质量大打折扣,不利于铝合金压铸件在后续使用中发挥良好的作用,甚至可能导致安全问题。
因此,分析其气孔产生原因,并探讨有效的处理对策是比较重要的内容。
一、铝合金压铸件产生气孔原因1、原材料因素原材料因素是铝合金压铸件产生气体的重要因素之一。
铝合金压铸件的原材料质量和性能会在一定程度上影响其气孔产生,研究显示,铝合金压铸件的合金液在加工中很容易受到原材料自身含氢量因素的影响从而析出气体,进而导致气孔出现,影响其质量。
在铝液中有85%的气体含量为氢气,因此含氢量较高的合金锭也比较容易在加工中出现气孔问题。
原材料的气孔问题不仅受到其内部性质的影响,导致合金锭表面潮湿的水蒸气,加工回炉料脏且油污较多,以及溶剂潮湿等,也都是原材料处理阶段气孔出现的主要原因,应该结合实际情况进行客观分析[1]。
图1 铝合金压铸件气孔2、压铸过程产生气孔压铸过程产生气孔是铝合金压铸件气孔产生的主要条件。
铝合金压铸件在压铸过程中的工艺技术会在很大程度上影响到其气孔的产生,研究显示气孔的产生通常与压铸工艺的参数有关,与模具的结构也有一定关联,此外在压铸过程中由于管控不当卷入气体,也会导致气孔出现。
铝合金压铸件在压铸过程中产生的气体,多由于压室、浇注系统、型腔与大气相通,并且在压铸时金属液以高压、高速填充相关。
铝合金铸件气孔的影响和形成原理

铝合⾦铸件⽓孔的影响和形成原理在纯铝中加⼊⼀些⾦属或⾮⾦属元素所熔制的铝合⾦是⼀种新型的合⾦材料,由于其⽐重⼩,⽐强度⾼,具有良好的综合性能,因此被⼴泛⽤于航空⼯业、汽车制造业、动⼒仪表、⼯具及民⽤器具制造等⽅⾯。
随着国民经济的发展以及经济⼀体化进程的推进,其⽣产量和耗⽤量⼤有超过钢铁之势。
加强对铝合⾦材料性能的研究,保证铝合⾦铸件具有优良品质,既是我们每⼀个科技⼯作者义不容辞的责任,也是同我们的⽇常⽣活息息相关的头等⼤事。
本⽂结合作者铝合⾦铸件⽣产实践经验谈谈铝合⾦铸件⽓孔与预防问题。
1.⽓孔类别由于铝合⾦具有严重的氧化和吸⽓倾向,熔炼过程中⼜直接与炉⽓或外界⼤⽓相接触,因此,如熔炼过程中控制稍许不当,铝合⾦就很容易吸收⽓体⽽形成⽓孔,最常见的是针孔。
针孔(gas porosity/pin-hole),通常是指铸件中⼩于1mm的析出性⽓孔,多呈圆形,不均匀分布在铸件整个断⾯上,特别是在铸件的厚⼤断⾯和冷却速度较⼩的部位。
根据铝合⾦析出性⽓孔的分布和形状特征,针孔⼜可以分为三类①,即:(1) 点状针孔:在低倍组织中针孔呈圆点状,针孔轮廓清晰且互不连续,能数出每平⽅厘⽶⾯积上针孔的数⽬,并能测得出其直径。
这种针孔容易与缩孔、缩松等予以区别开来。
(2) ⽹状针孔:在低倍组织中针孔密集相连成⽹状,有少数较⼤的孔洞,不便清查单位⾯积上针孔的数⽬,也难以测出针孔的直径⼤⼩。
(3) 综合性⽓孔:它是点状针孔和⽹状针孔的中间型,从低倍组织上看,⼤针孔较多,但不是圆点状,⽽呈多⾓形。
铝合⾦⽣产实践证明,铝合⾦因吸⽓⽽形成⽓孔的主要⽓体成分是氢⽓,并且其出现⽆⼀定的规律可循,往往是⼀个炉次的全部或多数铸件均存在有针孔现象;材料也不例外,各种成分的铝合⾦都容易产⽣针孔。
2.针孔的形成铝合⾦在熔炼和浇注时,能吸收⼤量的氢⽓,冷却时则因溶解度的下降⽽不断析出。
有的资料介绍②,铝合⾦中溶解的较多的氢,其溶解度随合⾦液温度的升⾼⽽增⼤,随温度的下降⽽减少,由液态转变成固态时,氢在铝合⾦中的溶解度下降19倍。
铝合金压铸件砂孔通用规范
POROSITY SPECIFICATION FOR ALUMINUM-ALLOY DIE CASTING铝合金压铸件气孔检验标准1. SCOPE(范围):This specification covers aluminum-alloy die casting porosity application. This specification based on original spec of ASTM E505, but not to replace original spec, only to provide more comprehensive interpretion, so has to be used with original spec. The requirement would override the original spec when conflict. 本规范涵盖了所有铝合金压铸气孔的要求。
本规范参照美国材料实验协会标准ASTM E505的原始规范,但不取代原规范,仅提供更全面的说明,所以原规范必须使用。
当本规范和原规范的内容矛盾时,本规范要求取代原规范内容。
2. SPECIFICATION(说明):Reference radiographs for aluminum-alloy die casting3. POROSITY LEVEL(气孔等级):Radiographs : Scale 1:1 射线照片:比例1:1Level 33级Radiographs : Scale 1:1X射线照片:比例Level 44级Radiographs : Scale 1:1X射线照片:比例1:0.25~0.40mm 5个/10cm20.25~0.40mm 7个/10cm20.40~0.70mm 3个/10cm20.7~1. 0mm 1个/10cm21.0以上0个/10cm20.25~0.40mm 10个/10cm20.40~0.70mm 5个/10cm20.7~1. 0mm 5个/10cm21.0~4.0mm 1个/10cm20.25~0.40mm 20个/10cm20.40~0.70mm 10个/10cm20.7~1. 0mm 10个/10cm21.0~4.0mm 3个/10cm24.0~10mm 1个/10cm2Unless special elucidation, 0.25mm and below porosity does not be controlled, and this request covers inside porosity and surface porosity of aluminum-alloy die casting!如果没有特别说明,0.25mm及以下的气孔不作为气孔的评估控制范围内,此要求适用于铝合金压铸件的内部和加工表面。
铝合金的铸造缺陷及其解决方案
铝合金的铸造缺陷及其解决方案关键信息项:1、铝合金铸造缺陷的类型名称:____________________________描述:____________________________2、造成铸造缺陷的原因因素:____________________________详细解释:____________________________3、解决方案的具体措施方法:____________________________实施步骤:____________________________4、预防铸造缺陷的策略策略:____________________________执行要点:____________________________11 铝合金铸造缺陷的类型111 气孔气孔是铝合金铸造中常见的缺陷之一。
气孔通常呈圆形或椭圆形,其尺寸大小不一。
112 缩孔和缩松缩孔是由于铸件在凝固过程中,金属液补缩不足而形成的较大孔洞。
缩松则是分散的细小缩孔。
113 夹渣夹渣指在铸件内部或表面存在的非金属夹杂物。
114 裂纹裂纹分为热裂纹和冷裂纹。
热裂纹在凝固末期高温下形成,冷裂纹则在较低温度下产生。
12 造成铸造缺陷的原因121 熔炼工艺不当熔炼过程中,如果温度控制不合理、熔炼时间过长或过短、搅拌不均匀等,都可能导致合金成分不均匀,气体和夹杂物含量增加。
122 浇注系统设计不合理浇注系统的结构和尺寸如果设计不当,可能导致金属液的流动不畅,产生卷气、冲砂等问题,从而形成气孔、夹渣等缺陷。
123 模具问题模具的温度不均匀、模具的排气不畅、模具的表面粗糙度不合适等,都可能影响铸件的质量,导致缺陷的产生。
124 铸造工艺参数不合理包括浇注温度、浇注速度、冷却速度等参数,如果选择不当,会直接影响铸件的凝固过程,从而引发各种缺陷。
13 解决方案的具体措施131 优化熔炼工艺严格控制熔炼温度和时间,采用合适的搅拌方式,确保合金成分均匀,减少气体和夹杂物的含量。
铝压铸件检验及气孔标准
铝压铸件检验及气孔标准铝压铸件是一种常见的铝合金铸件制造工艺,具有高强度、轻量化、良好的工艺性能等优点,在航空、汽车、电子等领域得到广泛应用。
为了保证铝压铸件的质量和性能,需要进行严格的检验,其中气孔是铝压铸件中常见的缺陷之一,因此有关铝压铸件检验及气孔标准的研究十分重要。
一、铝压铸件检验铝压铸件的检验是为了确保其质量和性能符合设计和规范要求,主要包括外观检查、尺寸检测、力学性能检验、化学成分分析和非破坏性检验。
具体的检验项目如下:1.外观检查:观察铸件的表面是否平整、无裂纹、气孔、砂眼等缺陷,以及是否满足图纸要求的形状和尺寸。
2.尺寸检测:测量铸件的各个尺寸,包括长度、宽度、高度、孔径、螺纹等,与图纸要求进行比较,判断是否合格。
3.力学性能检验:对铝压铸件进行拉伸、弯曲、冲击等力学性能测试,以评估其强度、硬度、韧性等性能是否满足要求。
4.化学成分分析:采用光谱分析等方法检测铝压铸件的化学成分,确保其合金成分符合规定的范围。
5.非破坏性检验:利用X射线探伤、超声波检测等方法对铝压铸件进行无损检测,发现内部缺陷如气孔、夹杂物、裂纹等。
二、铝压铸件气孔标准气孔是铝压铸件中常见的缺陷,对于外观要求较高的铝压铸件,气孔的控制尤为重要。
以下是铝压铸件气孔标准的一般要求:1.外观性气孔:不允许有明显的孔洞、气孔、疤痕和破损等缺陷,对于表面精加工要求高的铝压铸件尤其重要。
2.内部气孔:用X射线或CT扫描等方法检测,按照GB/T6414-1999标准评定内部气孔的数量和尺寸。
3.气孔位置:气孔应尽量分布在铝压铸件边缘或结构薄弱部位,而不应位于重要的强度位置。
4. 气孔尺寸:气孔直径一般应小于5mm,深度应小于铝压铸件壁厚的1/25.气孔数量:气孔数量应控制在一定的范围内,具体根据铝压铸件的几何形状和尺寸大小来确定,一般要求每平方厘米内的气孔数量不得超过3个。
综上所述,铝压铸件的检验工作是确保其质量和性能符合要求的重要环节,其中对气孔的控制是关键。
铝合金铸造出现气孔的原因分析及解决办法
铝合金铸造出现气孔的原因分析与解决办法核心提示:简单来说,气孔分两类,一类是析出性气孔,即铝液在凝固过程中因气体溶解度的变化而析出,老大在这方面说的很详细;另一类就是卷入性气孔,与铝液无关,主要是铝液填充过程中因紊流包卷在产品中的空气及涂料或型腔内未干的水分。
卷入性气孔主要与浇排系统的合理性密切相关,只有涂料和水,纯属操作不当。
至于说在喷丸后出现,应该主要与高速转换点的位置关联密切。
问题1:材料ACD12铝合金压铸件在机加工或喷砂后出现较多气孔的问题,这一技术上问题困扰着我们回复:1 设备抽真空设备是什么设备啊?压铸件的气孔问题好像还没有办法解决只能通过调节压铸参数,模温和修改相关的模具温度使气孔在一个合理的等级范围2 一.人的因素:1.脱模剂是否噴得太多? 因脱模济发气量大,用量过多时,浇注前未燃尽,使挥发气体被包在铸件表层。
所以在同一条件下,某些工人操作时会产生较多的气孔的原因之一。
选用发气量小的脱模济,用量薄而均匀,燃净后合模。
2未经常清理溢流槽和排气道?3开模是否过早? 是否对模具进行了预热?各部位是否慢慢均匀升温,使型腔、型芯表面温度为150℃~200℃。
4刚开始模温低时生产的产品有无隔离?5如果无预热装置时是否使用铝合金料慢速推入型腔预热或用其它方法加热?6是否取干净的铝液,有无将氧化层注入压室?7倒料时,是否将勺子靠近压室注入口,避免飞溅、氧化或卷入空气降温等。
8金属液一倒入压室,是否即进行压射,温度有无降低了?。
9冷却与开模,是否根据不同的产品选择开模时间?10有无因怕铝液飞出(飞水),不敢采用正常压铸压力?更不敢偿试适当增加比压。
?11操作员有无严格遵守压铸工艺?12有无采用定量浇注?如何确定浇注量?二.机(设备、模具、工装)的因素: 主要是指模具质量、设备性能。
1压铸模具设计是否合理,会否导致有气孔?压铸模具方面的原因:1.浇口位置的选择和导流形状是否不当,导致金属液进入型腔产生正面撞击和产生旋涡。
- 1、下载文档前请自行甄别文档内容的完整性,平台不提供额外的编辑、内容补充、找答案等附加服务。
- 2、"仅部分预览"的文档,不可在线预览部分如存在完整性等问题,可反馈申请退款(可完整预览的文档不适用该条件!)。
- 3、如文档侵犯您的权益,请联系客服反馈,我们会尽快为您处理(人工客服工作时间:9:00-18:30)。
铝合金铸件气孔与预防湖南江雁机械厂增压器公司邓益中摘要:本文从铝合金铸件气孔类别分析入手,指出铝合金铸件气孔可分为点状针孔、网状针孔、综合性针孔三类;氢是造成铝合金铸件针孔的主要原因,而氢的主要来源则是由于水蒸气分解所产生的。
因此,铝合金在熔炼过程中造成水蒸气产生的原因,也就是直接影响针孔形成的主要因素。
由于铝合金铸件气孔对铸件的品质尤其是对其力学性能产生不良的影响,作者在文中论述了铝合金铸件气孔形成的主要因素,并针对铝合金铸件气孔形成的主要因素提出了相应的预防措施,文章最后扼要总结了预防铝合金铸件针孔必须遵守的“防”、“排”、“溶”工艺原则。
关键词:铝合金;铸件;气孔;针孔;氢;力学性能;金属型铸造;预防措施。
引言:在纯铝中加入一些金属或非金属元素所熔制的铝合金是一种新型的合金材料,由于其比重小,比强度高,具有良好的综合性能,因此被广泛用于航空工业、汽车制造业、动力仪表、工具及民用器具制造等方面。
随着国民经济的发展以及经济一体化进程的推进,其生产量和耗用量大有超过钢铁之势。
加强对铝合金材料性能的研究,保证铝合金铸件具有优良品质,既是我们每一个科技工作者义不容辞的责任,也是同我们的日常生活息息相关的头等大事。
本文结合作者铝合金铸件生产实践经验谈谈铝合金铸件气孔与预防问题。
1.气孔类别由于铝合金具有严重的氧化和吸气倾向,熔炼过程中又直接与炉气或外界大气相接触,因此,如熔炼过程中控制稍许不当,铝合金就很容易吸收气体而形成气孔,最常见的是针孔。
针孔(gas porosity/pin-hole),通常是指铸件中小于1mm的析出性气孔,多呈圆形,不均匀分布在铸件整个断面上,特别是在铸件的厚大断面和冷却速度较小的部位。
根据铝合金析出性气孔的分布和形状特征,针孔又可以分为三类①,即:(1) 点状针孔:在低倍组织中针孔呈圆点状,针孔轮廓清晰且互不连续,能数出每平方厘米面积上针孔的数目,并能测得出其直径。
这种针孔容易与缩孔、缩松等予以区别开来。
(2) 网状针孔:在低倍组织中针孔密集相连成网状,有少数较大的孔洞,不便清查单位面积上针孔的数目,也难以测出针孔的直径大小。
(3) 综合性气孔:它是点状针孔和网状针孔的中间型,从低倍组织上看,大针孔较多,但不是圆点状,而呈多角形。
铝合金生产实践证明,铝合金因吸气而形成气孔的主要气体成分是氢气,并且其出现无一定的规律可循,往往是一个炉次的全部或多数铸件均存在有针孔现象;材料也不例外,各种成分的铝合金都容易产生针孔。
2.针孔的形成铝合金在熔炼和浇注时,能吸收大量的氢气,冷却时则因溶解度的下降而不断析出。
有的资料介绍②,铝合金中溶解的较多的氢,其溶解度随合金液温度的升高而增大,随温度的下降而减少,由液态转变成固态时,氢在铝合金中的溶解度下降19倍。
(氢在纯铝中的溶解度与温度的关系见图1③)。
因此铝合金液在冷却的凝固过程中,氢的某一时刻,氢的含量超过了其溶解度即以气泡的形式析出。
因过饱和的氢析出而形成的氢气泡,来不及上浮排出的,就在凝固过程中形成细小、分散的气孔,即平常我们所说的针孔(gas porosity)。
在氢气泡形成前达到的过饱和度是氢气泡形核的数目的函数,而氧化物和其他夹杂物则在起气泡核心的作用在一般生产条件下,特别是在厚大的砂型铸件中很难避免针孔的产生。
在相对湿度大的气氛中溶炼和浇注铝合金,铸件中的针孔尤其严重。
这就是我们在生产中常常有人纳闷干燥的季节总比多雨潮湿的时节铝合金铸件针孔缺陷少些的原因。
一般说来,对铝合金而言,如果结晶温度范围较大,则产生网状针孔的机率也就大得多③。
这是因为在一般铸造生产条件下,铸件具有宽的凝固温度范围,使铝合金容易形成发达的树枝状结晶。
在凝固后期,树枝状结晶间隙部分的残留铝液可能相互隔绝,分别存在于近似封闭的小小空间之中,由于它们受到外界大气压力和合金液体的静压作用较小,当残留铝液进一步冷却收缩时能形成一定程度的真空(即补缩通道被阻塞),从而使合金中过饱和的氢气析出而形成针孔。
3.形成气孔的氢气的来源与析出铝合金中气孔的产生,是由于铝合金吸气而形成的,但气体分子状态的气体一般不能溶解于合金液中,只有当气体分子分解为活性原子时,才有可能溶解。
合金液中气体能溶解的数量多少,不仅与分子是否容易分解为活性原子有关,还直接与气体原子类别有关。
在铝合金熔炼过程中,通常接触的炉气有:氢气、氧气、水蒸气、二氧化碳、二氧化硫等,这些气体主要是由燃料燃烧后产生的,而耐火材料、金属炉料及熔剂、与气体接触的工具等也可以带入一定量的气体,如新砌的炉衬、炉子的耐火材料、坩埚等,通常需要使用几天或几周的时间,其化学结合的氢才能充分从粘结剂中释放出来。
一般而言,炉气成分是由燃料种类以及空气量来决定的。
普通焦炭坩埚炉,炉气成分主要为二氧化碳、二氧化硫和氮气;煤气、重油坩埚炉主要为水蒸气、氮气;而对目前大多数熔炼厂家使用的电炉熔炼来说,炉气成分主要是氢气。
因此,采用不同的熔炼炉熔炼时,铝合金的吸气量和产生气孔的程度是不同的。
铝合金生产实践证明,氢是唯一能大量溶解于铝或铝合金中的气体,是导致铝合金形成气孔的主要原因,是铝合金中最有害的气体,也是铝合金中溶解度最大的气体。
在铸件凝固过程中由于氢的析出而产生的孔隙,不仅减少了铸件的实际截面积而且是裂纹源。
惰性气体不能溶于铝或铝合金,其他气体一般与铝或铝合金反应形成铝的化合物,如Al2O3、AlCl3、AlN、Al4C3等等。
由图1可知,氢在液态铝或铝合金中的溶液解度很大,而几乎不溶解于固态铝(在室温条件下,其溶解度约在0.003﹪以下)。
在铝合金熔炼时,周围空气中的氢气含量并不多,氢的最通常的来源是铝和水蒸气的反应,而水蒸气主要来源于炉气中的水分、设备及工具吸附的水分、一些材料的结晶水与铝锈Al(OH)2分解出来的水分等,其反应式如下:3H2O(水蒸气)+2Al=Al2O3+6[H](1)含镁铝合金由于还发生下列反应,更容易吸收氢:H2O(水蒸气)+ Mg=MgO+2[H](2)另外,金属炉料或回炉料带入的油污、有机物、盐类熔剂等与铝液反应也能生成氢:4mAl+3CmHn=mAl4C3+3n[H] (3)镁、钠、锂可以改变铝的表面的氧化膜,使活性氢原子容易进入;金属氟和铍则能在铝的表面形成更致密的氧化膜,降低氢向铝液或铝合金中扩散的速度,对铝合金起到保护作用。
形成氢化物的元素,如钙、钛、锂、铯等金属均能强烈地扩大氢在铝液中的溶解度。
不同温度下活性氢原子在铝液或铝合金中的溶解度见表1。
4.气孔对铝合金铸件性能的影响针孔对铝合金性能的影响主要表现在能使铸件组织致密度降低,力学性能下降。
为此,在铝合金铸件生产实践中,加强对气孔等级对力学性能的影响研究,通过控制针孔等级来保证铝合金铸件品质是非常重要的。
针孔等级评定,低倍检验按GB10851-89进行,当有争议时按表2规定执行;X射线照相按GB11346-89铝合金铸件针孔分级标准执行,该标准选用目前工业生产中常用的两种合金ZL101(Al-Si-Mg系)和ZL201(Al-Cu-Mn系), 并在T4状态测定бb和σ5的试验结果表明(ZL101T4、ZL201ST4各种针孔试样的力学性能分别见表3、表4):铸件力学性能与针孔等级之间是线性相关关系,随着针孔等级级别增加,力学性能逐步下降;针孔等级每增加一级,力学性бb下降3%左右,σ5下降5%左右。
对铝合金铸件切取性能试样要求,铸件允许存在的针孔级别详见GB9438-8这里应当指出的是,由于铸件壁厚效应的影响,即使针孔严重程度相同,壁厚大的部位力学性能下降,壁厚小的则较高。
由于铸件的力学性能取决于多种因素,不仅与针孔等级有关,还与合金的化学成分的波动、铸件的凝固速度、热处理效果、其他缺陷的存在因素有关,所以同一级别的针孔试样,力学性能将在一个相当大的范围内波动。
5.铝合金铸件针孔形成的主要因素综上所述,针孔是铝合金铸件中容易出现的且对铸件品质造成一定影响的一种铸造缺陷,氢是造成针孔的主要原因(有的资料介绍,铝液中所溶解的气体中80%-90%是氢),而氢的主要来源是水蒸气分解所产生的。
因此,铝合金在熔炼过程中造成水蒸气产生的原因,也就是直接影响针孔形成的主要因素。
影响针孔形成的主要因素有:5.1 原材料、辅助材料的影响在铝合金熔炼浇注过程中,所使用的原材料、辅助材料、一些材料中的结晶水和铝锈AL(OH)2分解会产生水分,造型材料中有多种有机和无机辅料带有的水分,铸型材料中的辅料、涂料等因为预热不良含有的水分等等,在铝合金熔炼浇注时,会因水蒸气的分解而产生大量的气体,这些气体都有可能导致铸件产生气孔。
涂料中粘结剂,虽然可以增加涂层厚度,但也相应增大了发气量。
5.2 熔炼设备及工具的影响不同熔炼设备熔化铝合金时,铝合金的吸气量和形成气孔的程度是不同的。
新坩埚及有锈蚀、污物的旧坩埚,使用前应吹砂或用其他方法清除干净,并加热至700℃-800℃,保温2h-4 h,以去除坩埚所吸附的水分和其它化学物质,否则会因含有水分而在熔炼浇注时产生水蒸气而导致形成气孔。
新砌的炉子,通常也需要使用几天或几周的时间进行烘炉干燥处理,否则耐火材料中含有的水分及化学结合的氢就无法释放而导致熔炼时形成气孔。
熔炼用的工具如浇包、除气用的钟罩等,使用前应将表面残余的金属、氧化皮等污物清除干净;铝镁合金使用的工具,使用前则要求放在光卤石等熔剂中洗涤干净。
然后涂上防护涂料并进行预热烘干。
如果预热不良,表面吸咐的水分,会在熔炼浇注过程因加热形成水蒸气而产生大量的气体,导致铸件针孔的形成。
5.3 气候的影响一般情况下,周围空气中的氢气含量并不多,但空气中如果相对湿度大,则会增加合金液中气体的溶解度,形成季节性气孔,如在雨季,由于空气湿度大,铝合金熔炼时针孔产生的现象就严重些。
当然,空气湿度大时,铝合金锭、熔炼设备、工具等也会因空气潮湿而增加表面水分的吸附量,因此更应注意采取有力预热烘干防护措施,以减少气孔的产生。
5.4 熔化操作的影响铝合金熔炼时,由于氢气溶解到铝液中需要一个过程,因此加强熔炼过程的控制,对控制铝合金吸气量是大有文章可做的。
生产实践表明,铝液吸氢是在表面进行的,它不仅与铝液表面的分压有关,还与合金熔炼温度、熔炼时间等有较大的关系。
合金熔化温度越高,熔化时间和熔化后铝液保持时间越长,氢在铝液中扩散就越充分,铝液吸氢量就越大,出现针孔的几率就越大。
有人曾做试验,铝液存放时间越长,铝合金内含气量近似成比例增加。
因此,我们在大量生产条件下,为了减少铝合金熔炼时吸收氢气,一定要严格执行铝合金熔炼工艺规程,一般铝合金熔化后保持时间不能超过3h-5h,铝合金熔化温度也不能过高,一般控制在760℃以下,最高初始熔炼温度不应超过920℃。