包钢无取向硅钢生产线生产工艺解析
无取向硅钢片生产技术要点
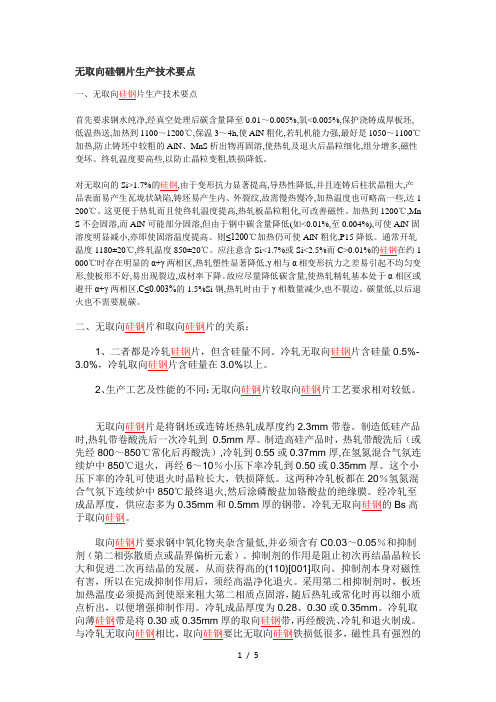
无取向硅钢片生产技术要点一、无取向硅钢片生产技术要点首先要求钢水纯净,经真空处理后碳含量降至0.01~0.005%,氧<0.005%,保护浇铸成厚板坯,低温热送,加热到1100~1200℃,保温3~4h,使AlN粗化,若轧机能力强,最好是1050~1100℃加热,防止铸坯中较粗的AlN、MnS析出物再固溶,使热轧及退火后晶粒细化,组分增多,磁性变坏。
终轧温度要高些,以防止晶粒变粗,铁损降低。
对无取向的Si>1.7%的硅钢,由于变形抗力显著提高,导热性降低,并且连铸后柱状晶粗大,产品表面易产生瓦垅状缺陷,铸坯易产生内、外裂纹,故需慢热慢冷,加热温度也可略高一些,达1 200℃。
这更便于热轧而且使终轧温度提高,热轧板晶粒粗化,可改善磁性。
加热到1200℃,Mn S不会固溶,而AlN可能部分固溶,但由于钢中碳含量降低(如<0.01%,至0.004%),可使AlN固溶度明显减小,亦即使固溶温度提高。
则≤1200℃加热仍可使AlN粗化,P15降低。
通常开轧温度1180±20℃,终轧温度850±20℃。
应注意含Si<1.7%或Si<2.5%而C>0.01%的硅钢在约1 000℃时存在明显的α+γ两相区,热轧塑性显著降低,γ相与α相变形抗力之差易引起不均匀变形,使板形不好,易出现裂边,成材率下降。
故应尽量降低碳含量,使热轧精轧基本处于α相区或避开α+γ两相区,C≤0.003%的1.5%Si钢,热轧时由于γ相数量减少,也不裂边。
碳量低,以后退火也不需要脱碳。
二、无取向硅钢片和取向硅钢片的关系:1、二者都是冷轧硅钢片,但含硅量不同。
冷轧无取向硅钢片含硅量0.5%-3.0%,冷轧取向硅钢片含硅量在3.0%以上。
2、生产工艺及性能的不同:无取向硅钢片较取向硅钢片工艺要求相对较低。
无取向硅钢片是将钢坯或连铸坯热轧成厚度约2.3mm带卷。
制造低硅产品时,热轧带卷酸洗后一次冷轧到0.5mm厚。
无取向电工钢(硅钢)生产流程[S]、[C]、[N]的控制剖析
![无取向电工钢(硅钢)生产流程[S]、[C]、[N]的控制剖析](https://img.taocdn.com/s3/m/8c62ca6ae45c3b3567ec8b28.png)
高炉顺行; 高温; 高锰; 高硅。
NERC-CCT
四、转炉工序[C]、[S]、 [N]的控制
4.1
4.2
4.3
转炉冶炼工序脱[C] 转炉冶炼工序脱[N] 转炉冶炼工序控[S]
NERC-CCT
4.1 转炉冶炼工序脱[C]
—— 转炉终点碳、氧的控制:
根据RH真空脱碳原理,要求处理前初始钢水的 [C]和[O]应达到一定的范围,以求最佳脱碳效果。
—— 改进真空脱碳效果的措施
1)提高抽气速度,实行真空快速降压,提高脱碳速度; 2)尽可能加大插入管直径,加大驱动气体流量,增大钢水循环量,提高脱碳 速度; 300 3)强制(吹氧)脱碳。 改进前 250
[C](ppm)
强制(吹氧)脱碳的特点: 可提高初始[C],达到0.04~0.06%; 可降低初始[O],降至250~ 400ppm。 脱碳速度比传统RH脱碳快。
NERC-CCT
2)影响转炉“回硫”的因素分析
——铁水脱[S]扒渣对回硫的影响 ——入炉铁水[S]对回硫的影响 ——废钢种类对回硫的影响 ——石灰中[S]对回硫的影响
12 10 8
Δ [S]*10-5
Al钢废钢方式对Δ [S] 的影响
11
7.3
7.6
6 4 2 0 1 3.2
4.8
2
3 废钢方式
4
[C],ppm
240 220 200 180 160 140 120 100 80 60 40 20 0 0 5 10 15 550mm 650mm 750mm
20
脱碳时间 ,min
不同浸渍管径下脱碳比较
300 250
650mm内径,供气流量90Nm3/h
[C](ppm)
无取向硅钢50SBW800炼钢工艺研究
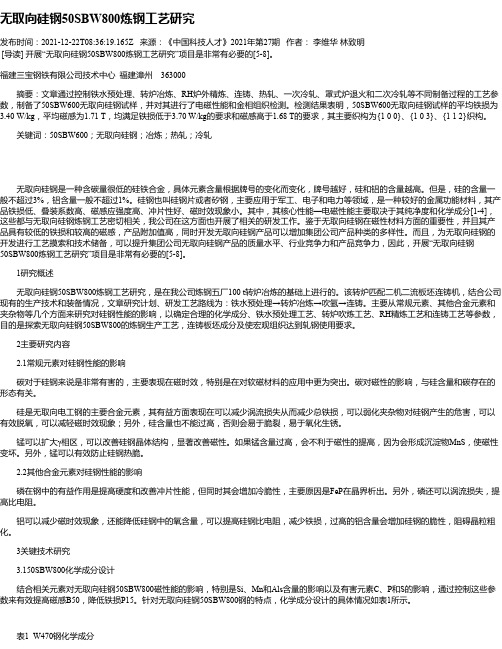
无取向硅钢50SBW800炼钢工艺研究发布时间:2021-12-22T08:36:19.165Z 来源:《中国科技人才》2021年第27期作者:李维华林致明[导读] 开展“无取向硅钢50SBW800炼钢工艺研究”项目是非常有必要的[5-8]。
福建三宝钢铁有限公司技术中心福建漳州363000摘要:文章通过控制铁水预处理、转炉冶炼、RH炉外精炼、连铸、热轧、一次冷轧、罩式炉退火和二次冷轧等不同制备过程的工艺参数,制备了50SBW600无取向硅钢试样,并对其进行了电磁性能和金相组织检测。
检测结果表明,50SBW600无取向硅钢试样的平均铁损为3.40 W/kg,平均磁感为1.71 T,均满足铁损低于3.70 W/kg的要求和磁感高于1.68 T的要求,其主要织构为{1 0 0}、{1 0 3}、{1 1 2}织构。
关键词:50SBW600;无取向硅钢;冶炼;热轧;冷轧无取向硅钢是一种含碳量很低的硅铁合金,具体元素含量根据牌号的变化而变化,牌号越好,硅和铝的含量越高。
但是,硅的含量一般不超过3%,铝含量一般不超过1%。
硅钢也叫硅钢片或者矽钢,主要应用于军工、电子和电力等领域,是一种较好的金属功能材料,其产品铁损低、叠装系数高、磁感应强度高、冲片性好、磁时效现象小。
其中,其核心性能—电磁性能主要取决于其纯净度和化学成分[1-4],这些都与无取向硅钢炼钢工艺密切相关,我公司在这方面也开展了相关的研发工作。
鉴于无取向硅钢在磁性材料方面的重要性,并且其产品具有较低的铁损和较高的磁感,产品附加值高,同时开发无取向硅钢产品可以增加集团公司产品种类的多样性。
而且,为无取向硅钢的开发进行工艺摸索和技术储备,可以提升集团公司无取向硅钢产品的质量水平、行业竞争力和产品竞争力,因此,开展“无取向硅钢50SBW800炼钢工艺研究”项目是非常有必要的[5-8]。
1研究概述无取向硅钢50SBW800炼钢工艺研究,是在我公司炼钢五厂100 t转炉冶炼的基础上进行的。
无取向硅钢 生产工艺

无取向硅钢生产工艺
无取向硅钢是一种特殊的电工钢,其具有较低的磁滞损耗和低的铁损耗,适用于制造高效率的电动机和变压器等电气设备。
无取向硅钢的生产工艺主要包括以下几个步骤:
1. 原材料准备:选用高质量的硅钢片原料,通常由硅铁合金和相关的辅助材料制成。
2. 钢液冶炼:将原料放入冶炼炉中进行冶炼,通常采用电爆炉或电弧炉等高温冶炼技术。
3. 钢液浇注:将冶炼后的钢液倒入浇注桶中,通过特定的浇注工艺将钢液注入连续浇铸机。
4. 连续浇铸:将钢液通过连续浇铸机均匀地注入狭缝状的铜板中,形成连续的钢带。
5. 热轧:使用连续热轧机将钢带进行轧制,逐渐减小钢带的厚度和宽度,并达到所需的规格和尺寸。
6. 轧制控制:通过控制轧制温度和压下力等参数,使得钢带的晶粒取向随机化,达到无取向特性。
7. 脱脂退火:将经过轧制的钢带进行退火处理,去除内部的应力和杂质,提高硅钢的磁性能和机械性能。
8. 制品加工:将退火后的钢带进一步切割、打孔、组装等,制成最终的电机或变压器的各种零部件。
9. 表面处理:对钢带进行模切、除锈、涂漆等表面处理,提高产品的外观和耐腐蚀性能。
10. 产品检验:对生产出的无取向硅钢进行严格的质量检验,包括磁性能测试、物理性能测试等。
以上是无取向硅钢的一般生产工艺流程,具体的工艺细节可能会因不同的生产厂家和产品规格有所不同。
新能源无取向硅钢 生产手册
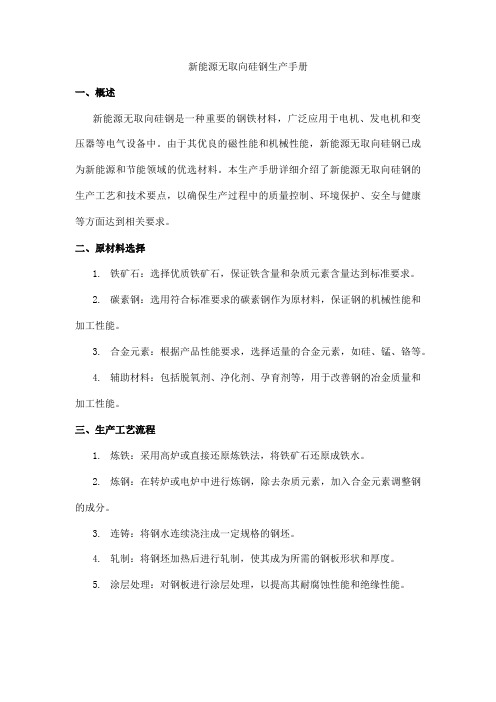
新能源无取向硅钢生产手册一、概述新能源无取向硅钢是一种重要的钢铁材料,广泛应用于电机、发电机和变压器等电气设备中。
由于其优良的磁性能和机械性能,新能源无取向硅钢已成为新能源和节能领域的优选材料。
本生产手册详细介绍了新能源无取向硅钢的生产工艺和技术要点,以确保生产过程中的质量控制、环境保护、安全与健康等方面达到相关要求。
二、原材料选择1.铁矿石:选择优质铁矿石,保证铁含量和杂质元素含量达到标准要求。
2.碳素钢:选用符合标准要求的碳素钢作为原材料,保证钢的机械性能和加工性能。
3.合金元素:根据产品性能要求,选择适量的合金元素,如硅、锰、铬等。
4.辅助材料:包括脱氧剂、净化剂、孕育剂等,用于改善钢的冶金质量和加工性能。
三、生产工艺流程1.炼铁:采用高炉或直接还原炼铁法,将铁矿石还原成铁水。
2.炼钢:在转炉或电炉中进行炼钢,除去杂质元素,加入合金元素调整钢的成分。
3.连铸:将钢水连续浇注成一定规格的钢坯。
4.轧制:将钢坯加热后进行轧制,使其成为所需的钢板形状和厚度。
5.涂层处理:对钢板进行涂层处理,以提高其耐腐蚀性能和绝缘性能。
6.质量检测与包装:对成品钢板进行质量检测,如外观、尺寸、磁性能等,符合标准要求的钢板进行包装。
四、质量控制1.成分控制:严格控制钢的化学成分,保证各合金元素含量在规定范围内。
2.冶金质量:优化炼铁和炼钢工艺,减少钢中的杂质元素和气体含量,提高钢的纯净度。
3.轧制质量控制:确保钢板在轧制过程中的温度、轧制力、轧制道次等工艺参数控制在规定范围内,以保证钢板组织和性能的稳定性。
4.涂层质量:对涂层材料和涂层工艺进行严格控制,以提高涂层的均匀性、致密性和附着力。
5.质量检测与控制:定期对生产过程中的各项工艺参数进行检测和控制,以确保产品质量稳定。
同时,对成品钢板进行严格的质量检测和控制,确保产品符合相关标准和客户要求。
五、环境保护与资源利用1.节能减排:优化炼铁和炼钢工艺,降低能耗和减少废弃物排放。
无取向硅钢片[1]
![无取向硅钢片[1]](https://img.taocdn.com/s3/m/b97c968983d049649b66587c.png)
关于“冷轧无取向硅钢相关技术情况”的介绍攀钢集团拟生产中、低牌号冷轧无取向硅钢,并有意向将冷轧后工序业务交与集团公司经营,集团公司已决定与攀钢进行战略合作开展此项业务,前期可行性研究的相关工作正在紧锣密鼓的进行。
根据集团要求,我部对冷轧无取向电工钢相关技术情况进行了调研整理,现介绍如下:一、无取向硅钢简介无取向硅钢为含碳很低的硅铁合金。
在形变和退火后的钢板中其晶粒呈无规则取向分布。
合金的硅含量为 1.5%~3.0%,或硅铝含量之和为1.8%~4.0%。
无取向硅钢中硅、铝和锰含量按规定应控制在一定范围,牌号不同,对碳、硫、氮和氧含量要求也不同,随牌号提高,这些元素的含量将进一步降低。
无取向硅钢产品通常为冷轧板材或带材,其公称厚度为0.35和0.5mm,主要用作电机和小型变压器铁芯。
二、无取向硅钢在电机的应用情况无取向硅钢因用作电机和小型变压器铁芯又叫无取向电工钢。
一般国内的高牌号无取向厚度都是 0.35mm厚;中低牌号无取向厚度是0.5mm厚。
且牌号300以上都叫高牌号;300-540叫中牌号;600-1300叫低牌号。
不同牌号冷轧无取向电工钢用途见表1所示。
三、无取向硅钢生产工艺冷轧无取向硅钢片生产工艺复杂,制造技术严格。
是将钢坯或连铸坯热轧成厚度约2.3mm带卷。
制造低硅产品(Si≤1.5%)时,热轧带卷酸洗后一次冷轧到0.5mm厚。
制造高硅产品(Si≥2.0%)时,先经800~850℃常化后再酸洗,一次冷轧到0.5或0.35mm厚, 然后在20%氢氮混合气氛下连续炉中850℃最终退火,涂半有机绝缘膜,再由剪切机切边、分条或横切成板、包装、入库。
工艺流程见图1所示。
Si≤1.5%无取向钢可以半成品状态交贷,Si≥2.0%钢都以完全退火状态交货。
表1 国产冷轧无取向硅钢片的应用中型电机√√小型电机√√√√√微型电机√√√√√密闭电机√√√√√间歇电机√√√√通用交流电机√√√√√焊接变压器√√中小型电机变压器√√√注:表达方式类似于B35A440的牌号为宝钢无取向硅钢片牌号;类似于35WW350牌号为武钢无取向硅钢片牌号;类似于50TW350牌号为太钢无取向硅钢片牌号;类似于50AW350牌号为鞍钢无取向硅钢片牌号Si ≤1.5%%图1 冷轧无取向硅钢片生产工艺流程四、无取向硅钢后工序技术要点无取向硅钢片冷轧后工序为完全退火—涂绝缘尾—剪切—成品。
本钢无取向硅钢热轧生产工艺路线的实践
本钢无取向硅钢热轧生产工艺路线的实践本钢无取向硅钢热轧生产工艺路线的实践李德君(本溪钢铁集团公司,辽宁本溪 117000)摘要:本钢拥有两条热轧生产线:一条为1700机组(传统工艺)热轧生产线;一条为薄板坯连铸连轧生产线。
通过在两条热轧生产线生产无取向硅钢试验,确定了本钢生产无取向硅钢最佳的热轧生产工艺路线。
关键词:无取向硅钢;热轧生产线;传统工艺;薄板坯连铸连轧The Practice of Non-orientation Silcon steel Hot RollingProduction Route In BX.SteelLI Dejun(Benxi Iron & Steel (Group) Co., LTD. Benxi, Liaoning Province 117000, China.)Abstract: The BX.Steel contains two Hot-Strip operations: one is the 1700-foot-long line which uses the traditional technology; the other is the BSP line (the thin-slab continuous casting and rolling production line).Through the test of producing hot-rolled non-oriented silicon steel in both lines to determine the best process to produce the hot-rolled non-oriented silicon steel in BX.Steel.Keywords: non-oriented silicon steel, Hot-Strip operations, traditional technology, FTSR前言本钢是目前我国北方地区重要的板材生产基地,在完成冶炼、连铸、热连轧、冷轧极薄带等设备的建设和现代化改造后,并从德国西马克公司引进了年产100万吨的冷轧极薄带生产线,具有无取向硅钢的生产能力。
硅钢生产线工艺说明及流程图
硅钢生产线工艺说明及流程图钢卷从钢卷库通过吊车吊运到入口钢卷存放鞍座,钢卷小车将钢卷送到1号或2号开卷机上。
入口侧钢卷输送系统设有钢卷高度对中及宽度对中系统,使钢卷能自动并顺利地插入开卷机芯轴,并保证钢卷中心线始终处于机组中心线位置。
开卷机头部设有转向夹送辊,通过开卷器将钢带引入转向夹送装置中,对带钢头部进行夹送及转向。
带钢进入双层剪切机由人工设定剪切长度和剪切次数后自动剪切。
切下的钢板通过入口切头输出装置送往废料箱。
剪切后的钢带经过3号转向夹送辊到达焊机,由焊机把两卷带钢头尾焊接起来。
为提高机组生产效率和缩短入口活套长度,焊机采用有限搭接焊机。
经过焊接后的带钢通过1号张力辊和1号纠偏辊送至入口活套。
入口活套用于贮存带钢,以保证当入口段上卷及焊接停机时工艺段连续运行。
在正常生产时入口活套通常处于满套状态,活套贮量为420米,确保机组能稳定高速地运行。
带钢从入口活套出来后,经过2号张力辊后,进入碱喷淋装置、碱刷洗装置、电解清洗装置、水刷洗装置、热水喷淋装置,将带钢表面的轧制油及杂物清洗干净。
经1号热风干燥器烘干后,通过5#纠偏辊纠偏,运行到钢结构平台上部,穿过 3号和4号张力辊及1号张力计辊,便进入退火炉内进行退火。
退火炉主要由下列部分的炉段组成:入口密封室、预热炉、无氧化加热炉、1号炉喉、辐射管加热炉、2号炉喉、均热炉、3号炉喉、循环气体喷射控冷段、4号炉喉、循环气体喷射快冷段、出口密封室。
在上述炉段预热、加热、均热、冷却,完成对带钢脱碳退火、晶粒长大、提高磁性及清除应力的工艺处理。
经过热处理之后的带钢经水喷淋冷却器调整板温,并经挤干辊挤压表面残余水份,经2号热风干燥器烘干后带钢进入6号纠偏夹送辊并输入到钢结构平台下部运行。
平台下部设6号转向辊及5号张力辊。
为了给带钢表面涂覆绝缘涂层,机组上设置了二台涂层机,并配置了绝缘涂层液供给系统及涂层液配制系统。
与此相配套设置了涂层烘干炉、涂层烧结炉及空气喷射冷却器,用以生产出合格的绝缘涂层产品。
无取向电工钢(硅钢)生产流程[S]、[C]、[N]的控制教材
NERC-CCT
—— 电工钢中[S]对磁性能的影响
钢中[S]含量增加,铁损增加,存在铁损急剧增加的[S]含 量,由此,电工钢中[S]控制成分为小于50ppm。
NERC-CCT
—— 电工钢中[N]对磁性能的影响
[N]含量在25ppm以上时,铁损急剧增加,由此,钢中[N] 含量控制应以25ppm为极限。
NERC-CCT
二、转炉流程生产无取向电工钢的关键工序
关键工序与任务: 铁水预处理工序,脱[S]、控制[N]; 转炉冶炼工序,脱[C]、脱[N]、控[S]; RH 精炼工序,脱[C]、脱[S]、控[N]; 连铸工序,控[C]、控[N]、控[S]。
NERC-CCT
—— 转炉流程脱硫工序的选择
1)铁水脱硫的优点:
—— 铁水中碳、硅含量高,提高了硫的反应能力, 从而有利于脱硫; —— 铁水中氧含量低,提高了渣-铁之间的硫分配 比,脱硫效率高; —— 铁水脱硫因其较好的动力学条件,脱硫剂利用 率高,而且脱硫速度快; —— 铁水脱硫费用低,如高炉、转炉、炉外精炼每 脱除1kg硫,其费用分别约为铁水脱硫的2.5倍、16 倍和6倍。
氮在α-Fe、γ –Fe、 δ –Fe、液态铁中的溶解度
氮在铁液中的溶解度
氮在铁中的溶解度
NERC-CCT
② 合金元素含量对氮在铁液中溶解度的影响
无取向硅钢的生产方法和无取向硅钢
无取向硅钢的生产方法和无取向硅钢下载提示:该文档是本店铺精心编制而成的,希望大家下载后,能够帮助大家解决实际问题。
文档下载后可定制修改,请根据实际需要进行调整和使用,谢谢!本店铺为大家提供各种类型的实用资料,如教育随笔、日记赏析、句子摘抄、古诗大全、经典美文、话题作文、工作总结、词语解析、文案摘录、其他资料等等,想了解不同资料格式和写法,敬请关注!Download tips: This document is carefully compiled by this editor. I hope that after you download it, it can help you solve practical problems. The document can be customized and modified after downloading, please adjust and use it according to actual needs, thank you! In addition, this shop provides you with various types of practical materials, such as educational essays, diary appreciation, sentence excerpts, ancient poems, classic articles, topic composition, work summary, word parsing, copy excerpts, other materials and so on, want to know different data formats and writing methods, please pay attention!一、无取向硅钢的生产方法。
无取向硅钢是一种广泛应用于电力、音响、汽车等行业的重要材料。
- 1、下载文档前请自行甄别文档内容的完整性,平台不提供额外的编辑、内容补充、找答案等附加服务。
- 2、"仅部分预览"的文档,不可在线预览部分如存在完整性等问题,可反馈申请退款(可完整预览的文档不适用该条件!)。
- 3、如文档侵犯您的权益,请联系客服反馈,我们会尽快为您处理(人工客服工作时间:9:00-18:30)。
包钢无取向硅钢生产线生产工艺解析硅钢是指含硅量在0. 5% ~ 4. 5% 左右的硅铁合金,是电力、电子和军事行业不可缺少的重要软磁合金,被称为钢铁产品中的“艺术品”。
经过对包钢薄板厂20万t硅钢生产工艺的探索与总结,钢板清洗质量、退火炉退火温度、涂覆膜厚度等因素,是影响硅钢成品性能的关键因素.优化前清洗段的清洗质量是降低炉辊结瘤概率的有效手段.保证退火炉的退火温度在750~950℃是细化钢板晶粒,调整组织,消除组织缺陷的核心工艺.涂覆膜均匀、厚度合理,保证在3.2~3.5 g/m2,是确保硅钢片免受各种腐蚀介质的侵蚀的重要措施。
1、硅钢生产工序铁水预脱硫处理→转炉冶炼→RH 处理→薄板坯连铸连轧→酸洗→冷轧→连续退火→涂层→卷取( 取样检验) →包装出厂在硅钢生产末段,即退火、涂层段,是直接决定硅钢成品的性能好坏及成品等级的阶段,如何管控好相应的工艺变得尤为重要。
2、退火涂层工艺解析2.1 前清洗段硅钢生产线主要控制的是退火与涂层两部分。
然而,在冷轧原料进入退火炉退火前,由于生产环境的不同,硅钢原料表面不可避免的包含一些污染物,这些污物主要包括:轧制过程中残留的乳化液、润滑油和铁粉,以及在冷硬卷存放过程中产生的锈和落上的尘土。
因此,必须对板带进行清洗,否则将严重影响最终成品表面质量,从而影响成品等级。
硅钢生产线在退火炉前专门设置了前清洗段,并且针对不同性质的杂质,设计不同种类的清洗介质,做到对症下药,有的放矢。
硅钢线前清洗段的清洗结构与清洗原因如下所述:前清洗段的布置结构依次为:碱浸洗段、碱刷洗段、电解清洗段、水刷洗段、水浸洗段、水漂洗段。
各段针对不同性质的杂质,分类清洗,主要清洗原理是:(1) 乳化液、润滑油:利用清洗液中NaOH的皂化反应初步去除板面上植物性油脂,在利用活性剂成分初步去除板面上的矿物性油脂。
结合刷洗和电解清洗深层次去除钢带表面的油脂。
(2) 铁粉:利用刷洗初步去除钢带外层的铁粉,利用电解清洗深层次去除钢带表面的铁粉。
(3) 锈:钢带表面的粘附的铁锈颗粒可以经刷洗去除。
(4) 尘土:可经脱脂清洗去除。
(5) 经过前清洗段对板带各种类型的冲洗,原板污物绝大多数已经清洗干净,能够满足后续生产工艺的要求。
2.2 连续退火退火是一种金属热处理工艺,指的是将金属缓慢加热到一定温度,保持足够时间,然后以适宜速度冷却。
目的是降低硬度,改善切削加工性;消除残余应力,稳定尺寸,减少变形与裂纹倾向;细化晶粒,调整组织,消除组织缺陷。
2.2.1 退火炉优点(1) 采用全辐射管间接方式加热带钢,改善带钢加热质量。
(2) 采用先进的保护气体循环冷却装置,采用交流变频调速,可实现带钢冷却速度、冷却温度的有效控制。
(3) 全炉均为密封炉体,既可避免带钢高温氧化,又确保炉内气氛安全可控。
(4) 采用辐射管间接加热和电阻带加热相结合的加热方式,方便控制炉内气氛,更利于保证带钢的表面质量。
(5) 采用先进的余热回收技术,可以将烟气排放温度稳定的控制在160℃左右,降低了在烟气排放过程中造成的热量损失。
(6) 采用先进的加湿系统,使炉内露点更稳定,保证产品质量的均匀性。
(7) 炉顶及侧墙耐火材料均采用轻质陶瓷纤维内衬,有效的减少了炉体散热和蓄热损失,降低炉子的控制惰性。
(8) 采用防爆泄压装置,防止发生意外爆炸时对炉体造成损害。
(9) 通过炉温检测装置和自动燃烧系统相结合的控制方式,可根据工艺设定值自动调节炉温。
(10) 设置在线氢分仪,可以连续监测炉内氢气含量。
(11) 通过设置炉压检测设备和相应的保护气体通入孔,可灵活控制各处的炉压,保证炉内气体流动稳定。
(12) 设置连续露点检测仪,自动控制炉内露点,保证炉内露点能满足工艺要求。
(13) 全炉均为密封炉体,既可避免带钢高温氧化,又确保炉内保护气体安全可控。
2.2.2 烧嘴工作原理退火炉加热段由108个W型辐射管组成,起到加热作用的主要是各辐射管的烧嘴。
只有烧嘴保持正常的工作状态,退火炉才能保证稳定运行。
烧嘴遇到的主要故障及解决方法主要有以下几方面:(1) 检查点火变压器是否点火。
检查电磁阀是否良好;检查烧嘴控制器电磁阀和点火变压器输出端子是否有输出。
(2) 检查点火电极是否漏电。
检查电极点火位置是否正确(确保火花在风盘前);梅花头离点火头2mm的间距,梅花头下面瓷管突出风盘面2~3mm。
(3) 空燃比例不好。
测烧嘴上燃气压力和空气压力,调整空燃比例阀或烧嘴前手动燃气阀和手动空气阀门。
(4) 电极损坏。
电极绝缘损坏,短路或内部断路。
电极头陶瓷或瓷管破损漏电。
(5) 烧嘴控制器损坏。
烧嘴控制器火焰检测功能损坏。
(6) 点火控制器地线未接。
检查烧嘴控制器内接地端子是否与烧嘴客体或炉壳连接。
2.2.3 退火关键控制点(1) 气氛:包钢硅钢生产线炉内气氛主要是氮氢混合气体,其中氮气的流量在350~450m3/h,氢气比例在5%~12%范围内。
混合气体的比例配比将影响退火炉运行的稳定性。
(2) 温度:硅钢生产的原料钢种有三种,分别为50W600、50W800、50W1000,不同钢种需要不同的退火温度,退火温度主要影响硅钢板的磁感应强度、铁损等性能,退火炉内设计有多个热电偶,用于时时检测炉内各区温度,保证退火温度正常。
(3) 冷却效果:退火炉内设计有18台冷却风机,其中10台是交流变频风机,可以随着板带温度自动变化风机转速。
另外8台为直流风机,保证板带冷却效果。
2.3 涂层在制造铁芯时,需要将减薄的电工钢片叠装在一起使用,为了有效的将涡流限制到各叠片内,同时使硅钢片在存储、运输和使用过程中免受各种腐蚀介质的侵蚀,防止锈蚀,需要在电工钢片表面涂覆一层电工绝缘涂层,使其具有适当的绝缘性,同时防止锈蚀。
绝缘涂层要求具有良好的绝缘性、附着性、耐蚀性等基本特性,同时要求具有良好的冲减加工性、焊接性,能经受消除应力退火的耐热性等性能。
冷轧无取向电工钢表面涂层主要包括:有机涂层、无机涂层、半无机涂层三大类,从环保角度出发,总的发展趋势是有机涂层逐渐淘汰,无机涂层逐步代替半无机涂层。
但由于受到无机涂层自身属性和各方面条件的制约,目前国际上电工钢制造厂商普遍应用仍为半无机涂层。
无取向硅钢表面绝缘涂层分成有机涂层、无机涂层和半无机涂层三大类。
无机涂层的基本成分是磷酸盐涂料和磷酸铝基涂料中添加胶态二氧化硅、氧化镁和硼酸。
无机涂层具有良好的耐热和焊接性能,但其冲制性和粘结性不佳。
半无机涂层基本成分为磷酸盐、铬酸盐、乳胶树脂溶液、弥散促进剂和表面活性剂,其中弥散促进剂和表面活性剂对涂层的质量具有重要作用。
半无机涂层具有良好的冲制性和粘结性,但其耐热性和焊接性不及无机涂层。
3、硅钢生产中常见问题3.1 炉辊结瘤在连续退火中,能够遇到的最主要也是最严重的问题就是炉辊结瘤。
炉辊结瘤,就是带钢表面的氧化物、铁屑等在辊子表面还原和粘结聚集,形成炉辊辊面结瘤。
炉辊结瘤产生的原因主要有以下几方面:(1) 钢带入退火炉前表面铁粉残留量过多,铁粉粘附在碳套上形成瘤体。
铁粉残留量过多可能是冷硬卷表面残留量过大引起的,也可能是脱脂清洗段清洗液成份不合适或清洗液未及时更换引起的。
(2) 原料卷表面生锈,氧化物被还原气氛还原成活性铁粘附在碳套上形成瘤体。
表面氧化是由于原料卷存放时间过长或存放环境湿度过大引起的。
(3) 生产线工艺段加减速幅度过大,过频繁,或炉辊转速与工艺段速度不匹配导致钢带与炉辊产生相对滑动,从而导致炉辊结瘤。
(4) 退火炉内气氛不合适,或氢气、氮气纯度过低(含氧量超标),导致部分杂质在碳套上聚集。
(5) 炉辊振动和炉辊传动控制误差使带钢和炉辊之间产生滑动,发生机械摩擦作用,在高温时,带钢表面的氧化物、铁屑等在辊子表面还原和粘结聚集,形成炉辊辊面结瘤。
(6) 由于辊子本身磨损氧化,辊子表面的氧化物附着聚集形成的。
在上述原因中,前清洗段的清洗质量和炉内气氛是否合格,是影响炉辊结瘤的最主要因素。
对此,生产线严控前清洗段各清洗介质的工艺参数,特别是电导率、介质温度、介质浓度等核心参数,并每天观测水样是否达标,在线检测钢板清洗是否干净,确保清洗质量合格。
在炉内气氛控制方面,硅钢线入口区域设置了氮气纯化装置,可以实时监控氮气的纯度,确保其氧含量低于工艺要求限度,保证炉内气氛合格。
此外,考虑到炉辊使用寿命周期,设备人员对每一根炉辊的安装时间进行登记,定期跟踪其工作状态,并定期更换,防止因本身磨损氧化,造成氧化物聚集,产生结瘤点。
3.2 冷却不均匀(1) 冷却裂纹和残余应力、组织性能不好、瓢曲和划伤等。
(2) 冷却裂纹和残余应力是由于钢板在冷却时,由于不均匀冷却所产生的热应力造成的。
(3) 钢板在冷却时,如果冷却过慢则使晶粒粗大,冷却速度过快又会产生魏氏组织、马氏体组织等,降低钢板的综合力学性能。
(4) 瓢曲是由于钢板冷却时,上下表面冷却不均以及各部位冷却不均所造成的。
4、质量控制要点(1) 前清洗段各清洗介质设定相应的工艺参数,如电导率、刷辊电流、介质温度等,并实现在线时时监控,发现参数不达标时,及时调整,保证带钢进入退火炉前的清洗质量合格。
(2) 要求退火炉各区实际温度与工艺设定温度最大温差在±20℃范围内波动,当出现温度超差时,限定在30min内消除故障,保证炉温恢复到正常温度。
(3) 设定涂层厚度标准,要求涂层厚度波动范围在±0.2g/m2以内。
优化程序,实现对涂层设备的远程控制。
当涂层厚度出现偏差时,能够及时调整,保证涂层厚度均匀稳定。
设计在线液体冷却系统,对涂层液实现低温冷却,保证涂层液质量有效。
5、结论(1) 硅钢生产中,退火环境是决定成品性能的关键,稳定的退火温度有利于降低铁损值。
(2) 涂层精度控制、涂敷膜的稳定性,将影响硅钢片的表面质量,涂层要求具有良好的绝缘性、附着性、耐蚀性等基本特性,同时要求具有良好的冲减加工性、焊接性,能经受消除应力退火的耐热性等性能。
(3) 成品表面质量需要严格控制,应保证带钢清洗质量,减少出现炉辊结瘤,保证板材表面光洁。
(4) 生产工艺按照要求调整,防止出现性能异常情况。