高速铣削加工颠覆模具生成方式
模具高速铣削加工技术

高 速切 削机 床的 床身等 支
部件应具有很好 的动 、静 刚度 ,
刚度和最佳的阻尼特性。大部分
床都采用高质量 、高 刚性和 高抗
切除率提高 了3 % 4盏。切削力降 0一 0
低 了3% 0 .刀具的切 削寿命提高 了 7%,鲳于工件的切 削热 大幅度降 0 低 ,低阶切削振动几乎消失。随着 切 削速度的提高 ,单位时间毛坯材 料 的去除率增加 了。切削时 间减少
】】 C D C M 与 { 2 A /A { 岳业信 慧 讹 ・ www i do m n a o c c
性的灰铸铁作为支撑部件材料 .
的机床公 司还在底座 中添加高阻 特性的聚合物混凝 土,以增加 其 振性和热稳定性 ,这 不但可保证 床精 度稳 定,也可防 止切削时刀
维普资讯
模具 高速铣 削加工技 术
东 莞理工 学校 吴光
一
、
前曹
在 现代模 舆 生产 中 ,随 肴对 塑件 的美观度及功能要求得越来越 高 ,塑件 内部结构设计得越来越复
杂,模具 的外形设 计也 臼趋复杂 ,
引 高 的 檀 采 扪 高 次 撼 了 加 度 可㈠ 圳 也 壤 高¨ 棚 矧 度 序 磨 可 成 短画= 巷 率 蜘 电 削 多 了 舭 件 阶 潮 从 与 件 具 时 托 也 床 础 以 钳 具 小 应 由 蛳 剖 麝 少 工 模 { 少 离 商 最。 高 减一 婀 期 性。 帆 埘 舡 雠 撼¨ 州 使 低 彻 了 晃 .疵 L 邛 撼对 一光 需加 工, 剥 抛 越 № 郦 中的 扬墙 辨 用 度 德 祀 市, ㈣ 些 在一 于沮 而
高速 切削 技术 是切 削加工:
术的 主要 发展 方 向之一 .它随
模具高速铣削加工技术
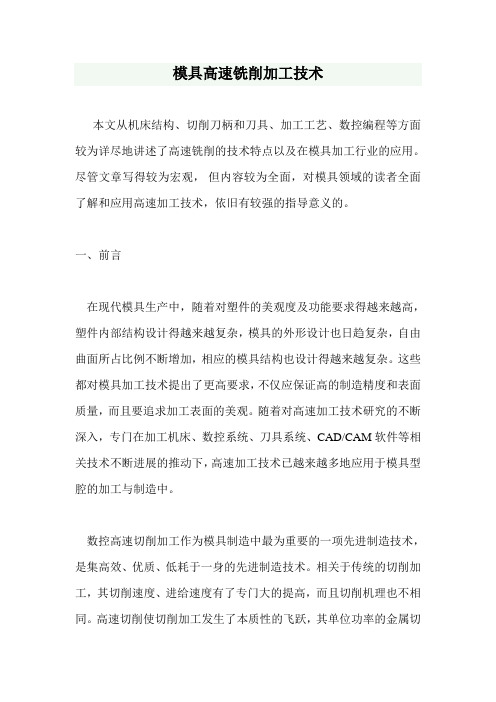
模具高速铣削加工技术本文从机床结构、切削刀柄和刀具、加工工艺、数控编程等方面较为详尽地讲述了高速铣削的技术特点以及在模具加工行业的应用。
尽管文章写得较为宏观,但内容较为全面,对模具领域的读者全面了解和应用高速加工技术,依旧有较强的指导意义的。
一、前言在现代模具生产中,随着对塑件的美观度及功能要求得越来越高,塑件内部结构设计得越来越复杂,模具的外形设计也日趋复杂,自由曲面所占比例不断增加,相应的模具结构也设计得越来越复杂。
这些都对模具加工技术提出了更高要求,不仅应保证高的制造精度和表面质量,而且要追求加工表面的美观。
随着对高速加工技术研究的不断深入,专门在加工机床、数控系统、刀具系统、CAD/CAM软件等相关技术不断进展的推动下,高速加工技术已越来越多地应用于模具型腔的加工与制造中。
数控高速切削加工作为模具制造中最为重要的一项先进制造技术,是集高效、优质、低耗于一身的先进制造技术。
相关于传统的切削加工,其切削速度、进给速度有了专门大的提高,而且切削机理也不相同。
高速切削使切削加工发生了本质性的飞跃,其单位功率的金属切除率提高了30%~40%,切削力降低了30%,刀具的切削寿命提高了70%,留于工件的切削热大幅度降低,低阶切削振动几乎消逝。
随着切削速度的提高,单位时刻毛坯材料的去除率增加了,切削时刻减少了,加工效率提高了,从而缩短了产品的制造周期,提高了产品的市场竞争力。
同时,高速加工的小量快进使切削力减少了,切屑的高速排出减少了工件的切削力和热应力变形,提高了刚性差和薄壁零件切削加工的可能性。
由于切削力的降低,转速的提高使切削系统的工作频率远离机床的低阶固有频率,而工件的表面粗糙度对低阶频率最为敏锐,由此降低了表面粗糙度。
在模具的高淬硬钢件(HRC45~HRC65)的加工过程中,采纳高速切削能够取代电加工和磨削抛光的工序,从而幸免了电极的制造和费时的电加工,大幅度减少了钳工的打磨与抛光量。
关于一些市场上越来越需要的薄壁模具工件,高速铣削也可顺利完成,而且在高速铣削CNC加工中心上,模具一次装夹可完成多工步加工。
高速铣削在模具制造中的应用

高速铣削在模具制造中的应用模具是用来制造汽车、飞机、电子和家电等产品各种构件的重要技术装备。
它作为从产品开发到成批生产构件的整个制造流程中的重要一环,在工业生产的增值链中占有十分重要的位置:模具的开发和制造,在很大程度上决定着新产品的质量、成本和投放市场的时间。
由于像锻造、铝合金压铸和塑料注塑这样的成形加工工艺和无定形材料的成形加工工艺,常常采用的是几何形状十分复杂的成形模具,有着凹、凸的自由曲面或较深的型腔,要求具有较高的精度和表面质量;另外,由于竞争促使产品品种不断增多,同时产品更新周期日益缩短,又鉴于模具主要是按单件或较小批量进行生产,这就迫使模具制造厂商必须要采用先进的加工技术,在确保工件加工精度的同时,提高生产效率和加工柔性,缩短加工时间。
例如,在汽车工业领域,汽车的开发周期已力求缩短到3年,模具的交货期需从18个月缩短到12个月。
这些成形模具通常由高性能合金模具钢制成。
模具的加工普遍采用两种工艺方法:一是采用借助于铜或石墨电极的电火花加工;二是直接采用高速铣削加工模具。
在过去,成形模的加工广泛采用电火花加工工艺。
而这种工艺的生产工艺流程较长,并缺乏柔性。
在进行电火花加工之前需要制造出石墨或铜电极。
如果由于工艺技术的原因必须变动成形模时,那就需要变动整个生产工艺流程。
由于其较低的柔性,难于进行调整或只能进行有限的调整。
此外,还有一个问题就是电火花加工的时间较长,在电火花加工后,模具还需要进行抛光处理,去除“白色层”。
近年来,尽管电火花加工技术在电源技术和石墨材料领域里取得了很大的进步,然而,上世纪90年代以来,随着高速切削技术的兴起和发展,高速铣削技术以其能显著缩短整个生产流程时间、很高的加工质量和较好的加工柔性而得到普遍接受,已成为加工成形模和注塑模的关键工艺。
高速铣削是模具制造最重要的加工工艺在模具制造中,高速铣削不仅广泛应用于加工复杂的自由曲面和型腔,而且还被用来加工电火花加工用的电极。
模具加工方法_高速切削

本章要点 挤压成形 铸造成形 合成树脂模具
一、冷挤压成形 1、原理: 原理: 在常温下,将淬硬的工艺凸模压入模坯, 在常温下,将淬硬的工艺凸模压入模坯,使坯料产生塑性 变形,以获得与工艺凸模工作表面形状相同的内成形表面。 变形,以获得与工艺凸模工作表面形状相同的内成形表面。 2、特点 可以加工形状复杂的型腔, 1)可以加工形状复杂的型腔,尤其适用于加工某些难以 进行切削加工的形状复杂的型腔。 进行切削加工的形状复杂的型腔。 挤压过程简单迅速,生产率高。 2)挤压过程简单迅速,生产率高。 加工精度高,表面粗糙度小。 3)加工精度高,表面粗糙度小。 冷挤压的型腔,材料纤维未被切断, 4)冷挤压的型腔,材料纤维未被切断,金属组织更为紧 型腔强度高。 密,型腔强度高。
快速原型
RP技术发展到今天已有 余年的历史,新的快速成型工艺 技术发展到今天已有20余年的历史 技术发展到今天已有 余年的历史, 不断产生、功能不断完善、精度不断提高、成型速度不断提高。 不断产生、功能不断完善、精度不断提高、成型速度不断提高。 例如: 例如:
随着固态激光技术的突破,高达1000mw的紫外激光器应 随着固态激光技术的突破,高达1000mw的紫外激光器应 用在SLA设备中 使其成型速度得到大大提高, 设备中, 用在SLA设备中,使其成型速度得到大大提高,激光器的 使用寿命由最初的2500小时延长到上万小时 小时延长到上万小时。 使用寿命由最初的2500小时延长到上万小时。
铣削加工中的高速铣削技术

铣削加工中的高速铣削技术现代制造业中,铣削加工技术是十分重要的一部分。
如果能够用更高效的方式进行铣削工作,将会极大提高生产效率和降低成本。
因此,高速铣削技术被越来越多地应用到了现代生产中。
高速铣削技术与传统铣削相比,最显著的不同是其搭载了更先进的高速机床和工具系统。
这些机床和工具能够高效地运作,并在短时间内完成更大量的工作。
同时,高速铣削还使用了更高级的加工参数,例如更大的切削速度、进给速度和毛坯清理速度等。
高速铣削的最大特点是其高效率,其切削速度相比于传统铣削可以提高至10倍以上,而且对切削刃的磨损及其表面质量也大有好处。
大的切削速度需求对机床特性也提出更高的要求,对其刚度、动刚性等机床特性要求更加优良,这也是高速机床设计发展的必然要求。
高速铣削一般可以分为两类:一是高速加工中的tiny 中心铣削,二是高速刀具铣削。
前者是传统铣削工艺改进的产物,主要运用于硬质度较高的材料(如钢、铁、铜等)的加工中。
因为这些材料比较脆弱,且热膨胀系数较低,所以切削时也更容易产生比较严重的变形和加热问题。
高速加工中的 tiny 中心铣削的操作将更为精细,能够使切削过程更加平稳。
同时,由于加工参数的优化,也可以减轻机床的负担,增加刀具的使用寿命。
高速刀具铣削的主要应用是在可塑性工件的加工中,例如铝合金、塑料以及一些轻金属。
这些材料具有较高的可塑性,And 切削过程时变形也不如传统的金属材料严重。
而且,高速刀具铣削可以优化加工参数,大大减少加热和变形问题,提高加工效率。
在这种情况下,高速铣削技术可以极大地提高加工质量、减少浪费、降低成本。
不过,高速铣削技术还存在一些问题要注意。
首先是刀具寿命方面的问题。
由于刀具在高速切削过程中容易变形、断裂,因此需要提出更加精准的切削参数设计。
其次是机床质量方面的要求。
由于高速铣削需要更高的动刚性及刚度要求,因此机床设计以及部件的韧性定位,变形成为了一个需要非常注意的问题。
总的来说,高速铣削技术的应用将会极大地提高加工效率、降低成本。
模具的高速铁削加工与传统铣削加工的比较

模具的高速铁削加工与传统铣削加工的比较高速铣削加工与传统的数控加工方法没有什么本质的区别,两者牵涉到同样的工艺参数一一进给量、切削速度和切削深度,也同样需要切削刀具和NC 程序。
高速铣削加工与传统数控铣削加工方法的主要区别在于进给速度、切削速度和切削深度的工艺参数值不同。
高速铣削加工采用高进给速度和小切削参数;而传统数控加工则采用低进给速度和大切削参数,如图9 一7 所示。
具体地说,从切削用量的选择看,高速铣削加工的工艺特点表现在以下几个方面:l )主轴转速(切削速度)高在高速加工中,主轴转速能够达到10000 ~30000r / min ,一般在Z000Or / min 以上。
高速加工的这个特点必须依赖于良好的机床设备,特别是高质量的机床主轴和主轴轴承。
2 )进给速度快典型的高速加工进给速度对切削钢材而言在5m / min 以上。
最近开发的数控机床的切削进给速度远远超过这个值.如德国的XHC24O 加工中心,最大进给速度可达60m / min 。
3 )切削深度小高速加工的切削深度一般在0 . 3~ 0 . 6mm 之间,在特殊情况下切削深度也可以达到0 . 1 mm 以下。
小的切削深度可以减小切削力,降低加工过程中产生的切削热,延长刀具的使用寿命。
从加工方式上讲.小的切削深度和快的进给速度能够获得加工时更好的刀具长径比L / D (其中L 指刀具长度,D 指刀具直径),使得许多深度很大的零件也能完成加工。
应该说,这是一种相当合理的加工方法。
4 )切削行距小高速铣削加工采用的刀具轨迹行距一般在0 . 2mm 以下。
一般来说,小的刀具轨迹行距可以降低加工过程中的表面粗糙度,提高加工质量,大幅度减少后续的精加工过程。
从加工的效果和经济效益看,高速铣削加工具有以下的优点:1 )加工质量好与传统的切削加工相比,用高速加工容易生产和剪断切屑。
当切屑厚度减小时,切屑温度上升,结果切屑更为碎小,而当应力和切屑都减小时,刀具负载变小,工件变形也小,产生的磨擦热降低,同时大量的切削热量被高速离去的切屑带走,所以模具和刀具的热变形很小,模具表面没有变质及微裂纹,从而大大改善工件的加工质量,并且有效地提高其加工精度。
机械加工中的高速铣削机床的设计与制造
机械加工中的高速铣削机床的设计与制造机械加工是工业领域中一项至关重要的工艺,它能够将各种材料加工成各式各样的工件,丰富着我们的生产和生活。
在机械加工的过程中,加工的效率和品质是至关重要的,因此,机床的设计和制造尤为关键。
在现代工业中,高速铣削作为一种高效、高品质的加工方法,被广泛应用。
高速铣削采用高速旋转的工具进行铣削,可以使加工速度增加几倍,同时能够获得更好的表面质量和更高的精度。
为了满足市场需求,研制高速铣削机床成为了当今机床制造业的热点。
设计一台高速铣削机床需要考虑的因素很多,其中包括机床的稳定性、运动精度、刚性、强度和生产效率等方面。
在这些因素中,机床的稳定性和刚性是至关重要的两个因素。
高速铣削机床的稳定性是指机床在运行过程中的运动稳定性。
在高速铣削中,工具在一瞬间接触工件并迅速离开,将会产生很大的惯性反作用力。
因此,一台稳定的机床能够有效地抵消这些力量,从而实现较高的铣削效率和精度。
而机床的刚性则是指机床的抗变形能力。
在高速铣削中,刀具旋转速度非常快,会产生很大的横向力,如果机床的刚性不足,就会引起机床的变形,从而影响加工精度和表面质量。
为了有效地提高机床的刚性,需要优化机床的结构、选用高强度材料和采用合理的加工工艺。
在高速铣削机床的制造过程中,材料和零部件的质量也是非常重要的,因为它们直接影响机床的稳定性和刚性。
在这方面,选用适合的材料和精密的加工工艺可以有效地提高机床的性能。
值得注意的是,在高速铣削中,切削液也非常重要。
切削液可以冷却工具和工件,减少摩擦,降低工具磨损和表面质量差异,从而提高铣削效率和加工质量。
因此,在机床的设计和制造过程中,应该考虑切削液的流动性、冷却性能和清洁性能等因素。
在现代工业中,高速铣削机床的应用已经越来越广泛,其在汽车、飞机、船舶和半导体等领域都具有重要的应用价值。
在未来,高速铣削机床的发展将越来越快,我们有理由相信,这项技术将会为机械加工带来更多的新突破。
先进制造技术-4.1高速加工
高速切削技术 3
问题的提出
从提高生产率的角度看, 从提高生产率的角度看,机床和生产过程自动化的实 归根到底, 质,归根到底,是以加快空程动作的速度和提高零件生 产过程的连续性, 产过程的连续性,从而缩短辅助工时为目的的一种技术 手段。 手段。 • 但是辅助动作速度的提高是有一定限度的。 但是辅助动作速度的提高是有一定限度的。例如目前 加工中心自动换刀时间已缩短到1S, 加工中心自动换刀时间已缩短到 ,快速空程速度已提 高到 30~50 m/min。再提高空程速度不但技术上有困难 ~ 。 经济上不合算,且对提高机床的生产率意义也不大, ,经济上不合算,且对提高机床的生产率意义也不大, 矛盾的主要方面已经转向切削工时。只有大幅度地降低 矛盾的主要方面已经转向切削工时。 切削工时(即提高切削速度和进给速度等), ),才有可能 切削工时(即提高切削速度和进给速度等),才有可能 在提高机床生产率方面出现又一次新的飞跃。 在提高机床生产率方面出现又一次新的飞跃。这就是近 20年来超高速切削技术得以迅速发展的历史背景。 年来超高速切削技术得以迅速发展的历史背景。 年来超高速切削技术得以迅速发展的历史背景 •
超高速加工是指被加工金属材料在切除过程中的剪切滑移 超高速加工是指被加工金属材料在切除过程中的剪切滑移 速度达到或超过某一阈值,使得切削力、温度、 速度达到或超过某一阈值,使得切削力、温度、磨损明显优于 传统切削速度。 传统切削速度。 铝合金>1600m/min,钛合金>150-1000m/min; ,钛合金 铝合金 ; 车削700-7000m/min,铣削300-600m/min ,铣削 车削
高速切削技术 15
高速切削技术 8
超高速切削的应用研究
• 在证实和应用萨洛蒙理论方面,美国科技界和工业界 在证实和应用萨洛蒙理论方面,美国科技界和工业界 做了许多领先的工作。 做了许多领先的工作。1977年在一台带有高频电主轴的 年在一台带有高频电主轴的 加工中心上进行超高速切削试验。 加工中心上进行超高速切削试验。其主轴转速可在 1800 范围内无级变速, ~18 000 r/min范围内无级变速,工作台的最大进给速度 范围内无级变速 为76 m/min。试验结果表明,与传统的铣削相比,其材 。试验结果表明,与传统的铣削相比, 料切除率增加了2~ 倍 主切削力减小了70%, %,而加工 料切除率增加了 ~3倍,主切削力减小了 %,而加工 的表面质量明显提高。受萨洛蒙理论的启发, 的表面质量明显提高。受萨洛蒙理论的启发,美国空军 和Lockheed飞机公司首先研究了用于轻合金材料的超高 飞机公司首先研究了用于轻合金材料的超高 速铣削。 年美国防卫高技术研究总署( 速铣削。1979年美国防卫高技术研究总署(DARPA)发 年美国防卫高技术研究总署 ) 起了一项“先进加工研究计划” 起了一项“先进加工研究计划”(Advanced Machining Research Program),研究切削速度比塑性波还要快的 ),研究切削速度比塑性波还要快的 ), 超高速切削,为快速切除金属材料提供科学依据。 超高速切削,为快速切除金属材料提供科学依据。经过 多年的努力,获得了丰硕的成果。 多年的努力,获得了丰硕的成果。
模具高速铣削加工技术及其数控编程
模具高速铣削加工技术及其数控编程【摘要】为探讨模具高速铣削加工技术及其数控编程,采用理论结合实践的方法,立足模具高速铣削加工的关键技术,分析了高速铣削数控编程的要点,并提出提升模具高速铣削加工技术应用效果的措施。
分析结果表明,模具高速铣削加工技术是一种先进的模具加工技术,但对关键技术和数控编程的应用有很高的要求,在实际生产中,需要结合模具的特点,选择好关键技术,并注重对数控编程的优化,才能提升应用效果,制作出高质量的模具产品。
【关键词】模具;高速铣削;加工;数控编程【引言】模具高速铣削工艺在机械生产制造领域中的应用显示出了优良的工艺特性,它可以简化制造工艺,缩短模具的前期准备时间,无需对模具进行精细的加工,而直接将粗制品加工成具有优良性能的模具。
此外,由于模具铣削加工的表面品质得到了极大的优化,在制造完成后无需对其进行磨光处理,降低了生产的负担。
模具高速铣削工艺具有很高的生产精度,可以达到微米级的精密加工,并通过智能的切削系统降低生产误差,并通过精加工处理后的精加工工艺,防止了模具表面的结构变形,保证了模具的表面质量。
基于此,开展模具高速铣削加工技术及其数控编程的分析研究就显得尤为必要。
1、模具高速铣削加工的关键技术1.1刀具系统目前在模具高速铣削加工中应用的主要刀具材料为金刚石、立方氮化硼、陶瓷刀具等。
常见的刀具结构有两种,一种是整体式刀具,另一种是镶齿式刀具。
前者主要为机夹机构,模具高速铣削加工中刀具在离心力的作用下,会引起夹紧机构破坏或者是刀片被甩掉,这就要求刀体夹紧机构需要有很高的强度和刚度,以保证生产的安全性。
在实际生产加工中为保证加工精度,需要合理解决好刀具刚度不足、重复精度不稳定、不方便快速换刀等问题。
1.2机床系统在模具高速铣削加工全过程中机床系统是实现高速铣削的关键结构保障系统,主要由高速主轴系统和快速进给系统组成。
其中高速主轴系统是实现模具高速铣削加工的关键之一,需要有足够的刚度和较高的回转精度,以及良好的冷却性能才能保证模具高速铣削加工的效率和质量【1】。
模具高速铣削加工技术概述
模具高速铣削加工技术概述
随着现代制造业的迅速发展,越来越多的企业开始采用模具高速铣削加工技术来提高生产效率和产品质量。
模具高速铣削加工技术是一种利用高速旋转的切削刀具来对工件进行加工的技术,具有具有加工精度高、加工效率快、精度稳定等优点,成为许多企业的首选工艺之一。
模具高速铣削加工技术的特点在于高速旋转的刀具与工件之间的相对运动速度非常快,使得在相对运动时切削力非常大,对工件进行快速加工,减少加工过程中的切削阻力,从而加快加工速度,大大提高生产效率。
在模具高速铣削加工技术中,铣床是一种非常重要的工具,铣床使用旋转刀具将工件进行加工。
在高速铣削加工过程中,铣床的结构设计、加工精度和材料的选择都是非常重要的,尤其是材料的选择,过硬的材料可以更好地提高铣床的耐磨性和使用寿命,从而更好地满足企业的生产需求。
模具高速铣削加工技术的发展历程可以追溯到20世纪80
年代,当时日本企业就开始采用该技术来加工汽车配件、电子零件等行业产品。
在90年代,模具高速铣削加工技术开始逐
渐成熟,广泛应用于制造业中,使得中国等国家也开始投入研发模具高速铣削加工技术。
在模具高速铣削加工技术的应用中,数控技术也是非常重要的一部分。
数控技术可以让操作工人根据实际生产需求来控
制铣床的运行速度、刀具的旋转速度、调整加工精度等参数,从而可以更好地满足不同客户的定制需求。
总体来说,模具高速铣削加工技术是一种重要的制造工艺,是许多行业中的不可缺少的一部分。
在未来,模具高速铣削加工技术还将继续得到改进和完善,为各行各业的企业提供更加优质的加工服务。
- 1、下载文档前请自行甄别文档内容的完整性,平台不提供额外的编辑、内容补充、找答案等附加服务。
- 2、"仅部分预览"的文档,不可在线预览部分如存在完整性等问题,可反馈申请退款(可完整预览的文档不适用该条件!)。
- 3、如文档侵犯您的权益,请联系客服反馈,我们会尽快为您处理(人工客服工作时间:9:00-18:30)。
高速铣削加工颠覆模具生成方式高速铣削加工颠覆了这家汽车零件锻造公司的十几年旧加工习惯,重新使模具制造返回到室内生产。
一位潜在的客户在Trenton锻造公司的参观访问中,看到了一个锻造的零件,非常像他要求该公司报价生产的零件。
位于密西根州的Trenton锻造公司就是在参观的前一星期收到了由这一客户邮寄来的报价材料。
然而,该客户得知这并不是类似的零件,正是他所需要的那个零件。
在收到客户打印资料的一星期内,Trenton 锻造公司模仿这一工件,加工制造了一套模具,而且试制了一批很好的锻件。
Trenton公司展示了他们的实力。
同时,也展示了他们在重点工作方面所具备的新能力。
由于在如何加工模具和谁能加工这一模具方面的情况发生了变化,现在这家汽车锻模供货商就能够向客户保证,在非常紧迫的时间内交货。
原因是适于这一工作的模具在一星期之内就完工了;Trenton公司可以承诺在两星期之内交付任何模具。
然而在一年前的这个时候,该公司根本不敢做出这样的承诺。
2000年10月,Trenton公司安装了两台转速高达18000r/min的模具铣削加工中心。
2000年9月,该公司完成了安装这两台机床的厂房建设。
建成新的车间和雇佣适当的工作人员以后,该锻模供应商就能发挥自己加工模具的潜力,使公司能承包十几年来未曾想像的加工任务。
只通过铣削加工制造模具的能力就足以说明为什么这一工作现在可以在室内完成的原因。
铣削加工的优缺点
Trenton锻造公司的模具制造主要依*EDM放电加工机床。
为什么Trenton公司的老板David Moxiow先生决定要购置两台加工中心,来替代EDM放电加工机床呢?快速而精确的加工中心,可以通过快速而轻巧的切削,直接在钢块上铣削加工出复杂的模具,而且成本效益很好。
因此,Trenton公司现在可以通过一次调试装卡,就能从硬度42 RC 的钢块上加工完成一个模具。
项目工程师Jason Van Buren先生解释了为什么在室内加工制造模具能如此吸引人的原因。
采用EDM机床加工模具需要很多加工工序和步骤,其所需的工作量一般要比锻模供货商制作模具所花费的工时更大。
其加工工序一般包括模型的制作、电极铣削加工、通过人工加工准备制作模具的钢块以及EDM机床本身的放电加工。
除了只有一个工序以外,其他全部离不开手工作业。
也就是说在执行放电加工时,只有一
个工序不需要人工参与。
正因为有如此多的原因,所以Trenton公司以前一直需要有较长时间的交货期。
采用高速铣削加工的方法,模具的加工速度较快,而且易于得到技术支持。
以前这么多的加工工序,现在只保留了模型的制作。
由于采用了新的工艺,因此大部分加工工作不需人工参与。
如果需要加工的是一个老的准备翻新的模具,那么就完全不需人工参与,因为在翻新加工一个磨损的模具时,只需采用一个经过多次实践验证的程序,就能自动完成再次铣削的加工任务。
Van Buren先生说,采用铣削加工的精度较高。
而采用EDM加工,经过多次处理会导致累积误差。
Trenton公司过去的加工公差高达0.13mm,但在采用一次性装卡铣削加工方法以后,该公司生产同样特点的模具,其公差可以缩减到0.03mm以下。
所有这些优点可以将铣削加工所存在的一大缺点平衡抵消:即其初期投资费用较高。
只将前期的投资偿还以后才能显示出铣削加工的优越性。
沉模加工的费用以及二次沉模加工
新模具加工车间所需的主要费用包括购置加工中心、刀具、CAD和CAM、。