某公司零件加工作业指导书样本
机械加工通用作业指导书【范本模板】
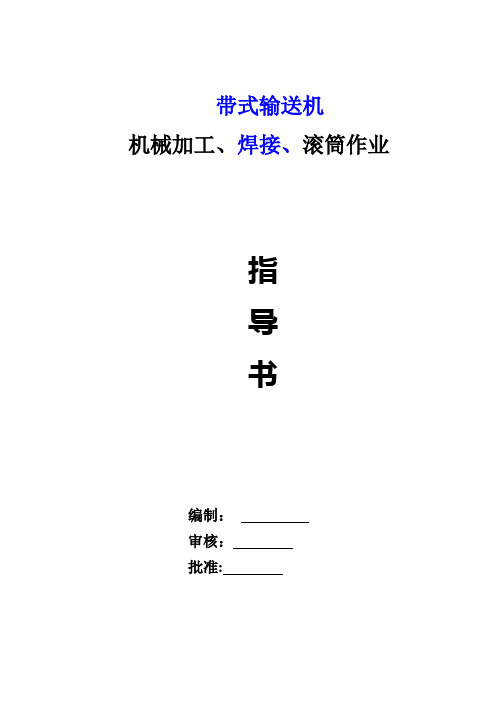
带式输送机机械加工、焊接、滚筒作业指导书编制:审核:批准:山西交城县兴星冶金设备厂机械加工通用作业指导书1、操作者应仔细看清图纸和工艺文件的各项说明,保持图纸和工艺文件的清洁与完整,并应严格按设计图纸、工艺规程和技术标准进行零部件的加工,不得随意自行更改.2、操作者按照工艺要求查看借用的工、夹、量、刀具是否符合工艺及使用要求,若有疑问,应立即与组长或车间生产管理者联系。
3、操作者应将工、夹、量、刀具分别整齐地放置在工具箱上或其它适当的地方,但不准直接放在机床上,并应妥善保管好,不得任意拆卸而改变原来尺寸或形状.4、在加工前,操作者首先应检查、抽查毛坯或经由上道工序加工并和本工序有关的尺寸,以确定余量是否符合工艺要求。
5、操作者应按照工艺规定的定位基面安装零件。
工艺未规定定位基面的,允许操作者自行选择定位基面和装夹方法,但是必须保证加工出来的工件符合图纸和工艺上的尺寸和精度要求。
在装夹工具前,应将夹具和工件清理干净,在定位基面上不得有铁屑、毛刺、污物及磕碰现象。
6、预压紧工件后,应按工艺要求进行工件的校正,若工艺未作出规定时,可按下列方法校正工件:6.1、当在本工序或本工步中加工到成品尺寸,且以后该加工面不再加工,装配时也不再调整或刮研时,可以按定位基面到加工面技术要求的1/3值校正,最后加工完成后应保证图纸中的技术要求。
6.2、在本工序或本工步中加工的加工面以后尚需加工或刮研,则按该加工面下道工序余量的1/3值校正,加工后要按此检验。
6.3、在本工序或本工步中加工的加工面到成品尺寸,以后该加工面不再加工,且图纸、工艺卡片内对该加工面与定位面无任何要求时,加工后应达到通用技术标准。
7、按工艺要求进行压紧,如工艺上无要求,零件压紧时注意压紧力的位置、大小和方向,并允许自加各种辅助支承,以增强刚性。
压紧前与压紧后都要测量,防止变形和磕碰。
8、凡加工面末到成品尺寸而工艺卡片又未规定工序的粗糙度时,粗车、粗铣、粗刨、粗镗和粗插的表面粗糙度应为Ra6.3(△4),磨削前的各种表面粗糙Z应为Rd3.2(△5),粗磨时外围的表面粗糙度应为Ra0.8(△7),平面、轴、孔互为Ral.6(△6);刮研前的加工面应为Ra3.2~Ral.6(△5~△6)。
机械加工作业指导书范例
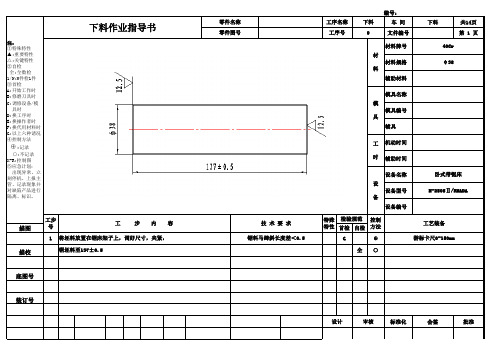
工 机动时间 时 辅助时间
设备名称
设 设备型号
备
设备编号
卧式带锯床 H-2505Ⅱ/RMADA
特殊 检验规范 控制 特性 首检 自检 方法
G
⊕
工艺装备 游标卡尺0-150mm
全○
设计
审核
标准化
会签
批准
标记 处数 更改文件号 签字 日期 标记 处数
更改文件号
签字
日期
注: ①特殊特性 ▲:重要特性 △:关键特性 ②自检
下料作业指导书
描图 描校
工步 号
工
步内容
1 将坯料放置在锯床架子上,调好尺寸,夹紧,
锯坯料至137±0.5
底图号
装订号
零件名称 零件图号
技术要求 锯料马蹄斜长度差<0.5
工序名称 工序号
下料 0
编号: 车间
文件编号
材料牌号
材 材料规格
料
辅助材料
下料
共14页 第1页
40Cr
φ38
模具名称
模 模具编号
具
全:全数检 1/N:N件检1件 ③首检 A:开始工作时 B:修磨刀具时 C:调修设备/工
装时 D:换工序时 E:换操作者时 F:换代用材料时 G:以上六种请况 ④控制方法
⊕:记录
○:不记录 X-R:控制图 ⑤应急计划:
出现异常,立 刻停机、上报主 管、记录现象并 对缺陷产品进行 隔离、标识。
机械加工作业指导书
更改文件号
签字
零件名称 零件图号
日期
工序名称 工序号
钻两孔 15
编号: 车间
文件编号
毛坯种类 材
毛坯尺寸 料
材料牌号
共14页 第4页
机加工作业指导书
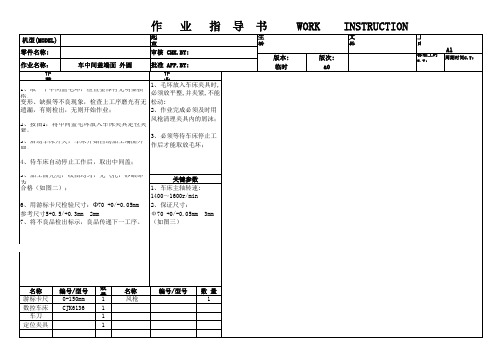
NG(不上锡) NG(上锡过量)
NG(锡尖) OK(上锡良好)
编号/型号
0-200mm 18-35mm
数量 1 1 1
NG(不上锡) NG(上锡过量)
NG(锡尖) OK(上锡良好)
作
业
指导书
WORK INSTRUCTION
机型(MODEL) 零件名称:
中间盖
起 草 审核 CHK.BY:
作业名称:
钻2-Ф3.3通孔
批准 APP.BY:
作
作
1、取一个業中间盖毛坯,检查整体有无明显损 伤、
变形、缺损等不良现象,有则检出,无则开
1、毛业坏放入台钻时,必须 放平整,并夹紧,不能松 动;
始作业;
生 效
版本: 临时
文 件
版次:
工 序
标准工时 S.T:
周期时间C.T:
2、作业完成必须及时用
2、将中间放入台钻开始攻丝;
风枪清理夹具内的屑沫;
批准 APP.BY:
作
作
1、取一个業中间盖毛坯,检查整体有无明显损 伤、
变形、缺损等不良现象,有则检出,无则开
1、毛业坏放入台钻时,必须 放平整,并夹紧,不能松 动;
始作业;
2、作业完成必须及时用
2、将中间盖放入台钻定位;
风枪清理夹具内的屑沫;
生 效
版本: 临时
版次:
文
工
件
序
标准工时
WI/TD001-SM05302A/A S.T:
关键参数 1、车床主轴转速: 1400~1600r/min 2、保证尺寸: 5+0.1/0.03mm 厚度8mm的尺寸 见图三
名称
编号/型号
数 量
机加工作业指导书模板

机加工作业指导书模板摘要:一、引言二、机加工作业概述1.加工范围2.加工方法3.加工材料三、机加工工艺流程1.工艺流程步骤2.工艺参数设置3.加工注意事项四、机加工安全操作规程1.操作规程要点2.安全防护措施3.异常情况处理五、机加质量控制与检验1.质量控制要求2.检验方法与标准3.质量改进措施六、设备维护与保养1.设备维护内容2.设备保养周期3.设备故障排除七、环境保护与职业健康1.环保措施2.职业健康要求3.培训与教育八、总结与展望正文:一、引言随着现代制造业的快速发展,机加工作业在各类工厂中得到了广泛应用。
为了规范机加工作业流程,提高工作效率,保证加工质量,特制定本指导书。
本指导书旨在为从事机加工作的人员提供一套完整的作业规范,内容包括机加工作概述、工艺流程、安全操作规程、质量控制与检验、设备维护与保养、环境保护与职业健康等方面。
二、机加工作业概述1.加工范围机加工作业主要包括金属切削、钻孔、磨削、镗孔、铣面、刨削、拉削等加工过程。
2.加工方法加工方法主要包括普通加工和数控加工。
普通加工包括手动加工和自动加工,数控加工采用数控机床、加工中心等设备进行高精度加工。
3.加工材料加工材料主要包括金属材料、非金属材料和复合材料。
金属材料包括铁、钢、铝、铜等,非金属材料包括塑料、橡胶、陶瓷等,复合材料包括碳纤维、玻璃纤维等。
三、机加工工艺流程1.工艺流程步骤(1)工艺分析与方案制定(2)设备选用与安装(3)刀具准备(4)工件装夹与定位(5)加工操作(6)加工质量检验(7)成品验收与包装2.工艺参数设置根据加工材料、刀具、设备等因素,合理设置切削速度、进给速度、切削深度等工艺参数。
3.加工注意事项(1)遵守操作规程,防止误操作(2)注意加工过程中刀具的磨损与更换(3)保持设备清洁,防止故障发生(4)定期检查加工质量,确保加工精度四、机加工安全操作规程1.操作规程要点(1)认真阅读操作手册,掌握设备性能(2)严格遵守操作规程,不得擅自变更(3)开机前检查设备完好,确认无异常(4)穿戴劳动保护用品,严禁酒后操作2.安全防护措施(1)设置安全防护装置,如防护罩、限位器等(2)定期检查电气线路,防止短路、漏电等事故(3)使用安全可靠的电源,避免触电事故3.异常情况处理遇到异常情况,如设备故障、加工质量问题等,应立即停机检查,找出原因并进行处理。
机加工作业指导书模板
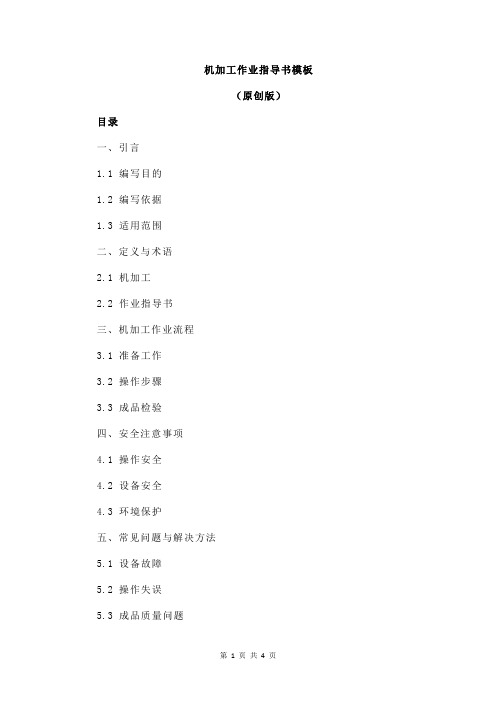
机加工作业指导书模板(原创版)目录一、引言1.1 编写目的1.2 编写依据1.3 适用范围二、定义与术语2.1 机加工2.2 作业指导书三、机加工作业流程3.1 准备工作3.2 操作步骤3.3 成品检验四、安全注意事项4.1 操作安全4.2 设备安全4.3 环境保护五、常见问题与解决方法5.1 设备故障5.2 操作失误5.3 成品质量问题六、作业指导书的管理与更新6.1 指导书的发放与归档6.2 指导书的更新与修订七、结语正文一、引言1.1 编写目的本作业指导书旨在规范机加工作业的流程和方法,确保生产效率和产品质量,降低安全事故和环境污染风险。
1.2 编写依据本指导书依据我国相关法律法规、行业标准和企业内部规定进行编写。
1.3 适用范围本指导书适用于我公司机加工车间的所有员工。
二、定义与术语2.1 机加工机加工是指通过各种机械设备,对金属、非金属等材料进行切削、成型、装配等加工过程。
2.2 作业指导书作业指导书是指对某一具体作业过程进行详细描述和指导的文件,包括作业流程、操作方法、安全注意事项等内容。
三、机加工作业流程3.1 准备工作操作人员应熟悉作业指导书内容,穿戴好劳动保护用品,检查设备状态,准备好所需工具和量具。
3.2 操作步骤根据设备操作规程和工艺文件,进行切削、成型、装配等加工操作。
3.3 成品检验成品加工完成后,应进行自检、互检和专检,确保产品质量符合要求。
四、安全注意事项4.1 操作安全操作人员应严格遵守操作规程,禁止违章作业,防止人身伤害事故发生。
4.2 设备安全定期对设备进行检查、保养和维修,发现异常情况立即停机处理,防止设备故障导致事故。
4.3 环境保护遵守环保规定,减少生产过程中产生的废气、废水等污染物排放,做好现场环境卫生。
五、常见问题与解决方法5.1 设备故障遇到设备故障,应立即停机,报告班长或主管,由专业人员进行维修。
5.2 操作失误操作过程中出现失误,应立即停止操作,分析原因,采取措施避免类似情况再次发生。
车间作业指导书
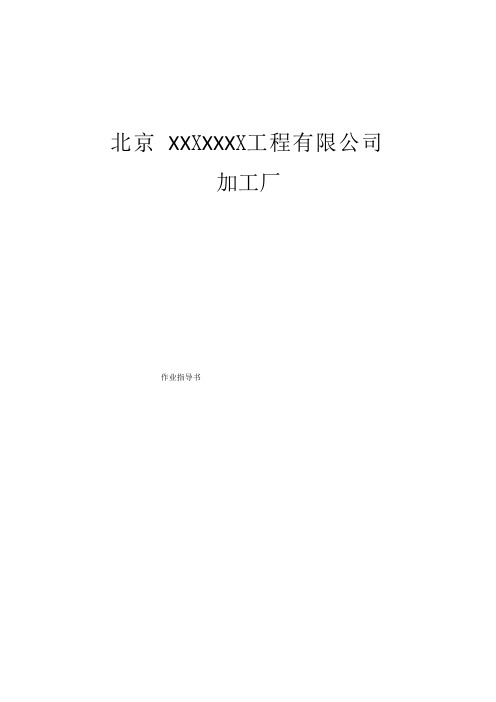
北京XX X XXX X工程有限公司加工厂作业指导书5、切割一 加工厂工作流程1。
材料进厂所需材料进厂前要有专门负责人员进行材料的分量 规格 型材尺寸进行检查并记录数据及资料,并有指定人员进行卸车。
2,加工制作图的绘制技术人员对所要进行的加工图纸进行细化 ,让操作工容易理解看懂,避免不必要的错误。
3、放样技术人员熟悉图纸,确定放样图样,放线,点焊定位板,校验尺寸,试制样品,检验尺寸,调整大样样板。
4、放线下料技术人员对所要加工的材料在熟悉掌握图纸的情况下, 进行放线,在确保准确无误时再进行下料,在划线时,考虑了焊接收缩量、变形的 余量、允许公差等。
当进行下料部份划线时要考虑剪切余量、切削余 量。
磨擦面处理 涂装编号焊接 材 料 进 厂 加工制图 放样 坡口制孔组装 划线下料 切割钢材的切割包括气割、等离子切割类高温热源的方法,也有使用剪切、切削等机械力的方法。
下料人员要考虑切割能力、切割精度、切剖面的质量及经济性。
6、坡口加工方法主要有:铲边、刨边、铣边、碳弧气刨、气割和坡口机坡口加工:普通可用气体加工和机械加工,在特殊的情况下采用手动气体切割的方法,但必须进行事后处理,如打磨等。
现在坡口加工专用机已开始普及,最近又浮现了H 型钢坡口及弧形坡口的专用机械,效率高、精度高。
焊接质量与坡口加工的精度有直接关系,如果坡口表面粗糙有尖锐且深的缺口,就容易在焊接时产生不熔部位,将在事后产生焊接裂缝。
又如,在坡口表面粘附油污,焊接时就会产生气孔和裂缝, 因此要重视坡口质量。
7、制孔加工人员在焊接结构中,不可避免地将会产生焊接收缩和变形,因此在制作过程中,把握好什么时候开孔将在很大程度上影响产品精度.特殊是对于柱及梁的工程现场连接部位的孔群的尺寸精度直接影响钢结构安装的精度,第一种方法在构件加工时顶先划上孔位,待拼装、焊接及变形矫正完成后,再划线确认进行打孔加工,第二种方法在构件一端先进行打孔加工,待拼装、焊接及变形矫正完成后,再对另一端进行打孔加工。
(完整版)机械加工通用作业指导书
机械加工通用作业指导书1、操作者应仔细看清图纸和工艺文件的各项说明,保持图纸和工艺文件的清洁与完整,并应严格按设计图纸、工艺规程和技术标准进行零部件的加工,不得随意自行更改。
2、操作者按照工艺要求查看借用的工、夹、量、刀具是否符合工艺及使用要求,若有疑问,应立即与组长或车间生产管理者联系。
3、操作者应将工、夹、量、刀具分别整齐地放置在工具箱上或其它适当的地方,但不准直接放在机床上,并应妥善保管好,不得任意拆卸而改变原来尺寸或形状。
4、在加工前,操作者首先应检查、抽查毛坯或经由上道工序加工并和本工序有关的尺寸,以确定余量是否符合工艺要求。
5、操作者应按照工艺规定的定位基面安装零件。
工艺未规定定位基面的,允许操作者自行选择定位基面和装夹方法,但是必须保证加工出来的工件符合图纸和工艺上的尺寸和精度要求。
在装夹工具前,应将夹具和工件清理干净,在定位基面上不得有铁屑、毛刺、污物及磕碰现象。
6、预压紧工件后,应按工艺要求进行工件的校正,若工艺未作出规定时,可按下列方法校正工件:6.1、当在本工序或本工步中加工到成品尺寸,且以后该加工面不再加工,装配时也不再调整或刮研时,可以按定位基面到加工面技术要求的1/3值校正,最后加工完成后应保证图纸中的技术要求。
6.2、在本工序或本工步中加工的加工面以后尚需加工或刮研,则按该加工面下道工序余量的1/3值校正,加工后要按此检验。
6.3、在本工序或本工步中加工的加工面到成品尺寸,以后该加工面不再加工,且图纸、工艺卡片内对该加工面与定位面无任何要求时,加工后应达到通用技术标准。
7、按工艺要求进行压紧,如工艺上无要求,零件压紧时注意压紧力的位置、大小和方向,并允许自加各种辅助支承,以增强刚性。
压紧前与压紧后都要测量,防止变形和磕碰。
8、凡加工面末到成品尺寸而工艺卡片又未规定工序的粗糙度时,粗车、粗铣、粗刨、粗镗和粗插的表面粗糙度应为Ra6.3(△4),磨削前的各种表面粗糙Z应为Rd3.2(△5),粗磨时外围的表面粗糙度应为Ra0.8(△7),平面、轴、孔互为Ral.6(△6);刮研前的加工面应为Ra3.2~Ral.6(△5~△6)。
关于机械加工的作业指导书范文
关于机械加工的作业指导书范文关于机械加工的作业指导书范文1、操作者应仔细看清图纸和工艺文件的各项说明,保持图纸和工艺文件的清洁与完好,并应严格按设计图纸、工艺规程和技术标准进展零部件的加工,不得随意自行更改。
2、操作者按照工艺要求查看借用的工、夹、量、刀具是否符合工艺及使用要求,假设有疑问,应立即与组长或车间消费管理者联络。
3、操作者应将工、夹、量、刀具分别整齐地放置在工具箱上或其它适当的地方,但不准直接放在机床上,并应妥善保管好,不得任意拆卸而改变原来尺寸或形状。
4、在加工前,操作者首先应检查、抽查毛坯或经由上道工序加工并和本工序有关的尺寸,以确定余量是否符合工艺要求。
5、操作者应按照工艺规定的定位基面安装零件。
工艺未规定定位基面的',允许操作者自行选择定位基面和装夹方法,但是必须保证加工出来的工件符合图纸和工艺上的尺寸和精度要求。
在装夹工具前,应将夹具和工件清理干净,在定位基面上不得有铁屑、毛刺、污物及磕碰现象。
6、预压紧工件后,应按工艺要求进展工件的校正,假设工艺未作出规定时,可按以下方法校正工件:6.1、当在本工序或本工步中加工到成品尺寸,且以后该加工面不再加工,装配时也不再调整或刮研时,可以按定位基面到加工面技术要求的1/3值校正,最后加工完成后应保证图纸中的技术要求。
6.2、在本工序或本工步中加工的加工面以后尚需加工或刮研,那么按该加工面下道工序余量的1/3值校正,加工后要按此检验。
6.3、在本工序或本工步中加工的加工面到成品尺寸,以后该加工面不再加工,且图纸、工艺卡片内对该加工面与定位面无任何要求时,加工后应到达通用技术标准。
7、按工艺要求进展压紧,如工艺上无要求,零件压紧时注意压紧力的位置、大小和方向,并允许自加各种辅助支承,以增强刚性。
压紧前与压紧后都要测量,防止变形和磕碰。
8、凡加工面末到成品尺寸而工艺卡片又未规定工序的粗糙度时,粗车、粗铣、粗刨、粗镗和粗插的外表粗糙度应为Ra6.3(△4),磨削前的各种外表粗糙Z应为Rd3.2(△5),粗磨时外围的外表粗糙度应为Ra0.8(△7),平面、轴、孔互为Ral.6(△6);刮研前的加工面应为Ra3.2~Ral.6(△5~△6)。
加工中心作业指导书
加工中心作业指导书1.目的:通过规范安全操作,防患于未然,杜绝安全隐患以达到安全生产并保证加工质量。
2.范围:适用于本公司加工中心操作及维护保养。
3。
工作流程3.1。
作业流程图3.1.1清理工作台:把工作台及工装清理干净,不同材质落料分开存放。
准备好装夹所需的螺杆、螺母、垫块等.3.1.2.核对图纸、工件是否符合:将图纸打开与工件进行核对,清楚工件的装夹位置和方向。
检查毛坯并且毛坯清理干净,去毛刺.3.1.3.拷贝程序及校对。
3。
1.4。
校表找平、拉直、分中、确定对刀参考值:先找平工件,再拉直,然后再打表确定坐标原点并在机床工件坐标系确定输入;夹紧工件后再检查工件的找平、拉直、分中.3.1。
5。
加工工件:加工前准备好所需刀具并与程序单上的刀具名称一致。
准备所有需要的刀具,在可以的情况下尽量优先用旧的刀具,盒子不要扔掉,用完后刀具放回盒子。
对好刀,开始加工,下刀后刀具离工件一段距离时要边看操作面板上的程序及余位移量进行检查,确认正常即开始加工,在加工过程中要注意检查刀具磨损,如刀具磨损要及时停机并更换刀片,然后再加工。
3.1。
6.自检:所有工件加工完以后要进行自检,譬如一些加工没有到位,R角与面没有接顺等,检验所有可以检验尺寸,表面有无压伤,有没有拆下工件后变形的情况,如有问题尽可能马上或在工件为卸下之前找技术解决.3.1.7送检:工件加工完以后要按照工艺流程进行送检。
3.2作业准备3。
2。
1仔细阅读使用手册并确实明白所有内容以能有效和安全的操作机器.3。
2。
2经常将有关安全章节及使用手册放在靠近机台的固定位置,以备必要时容易查询。
3。
2。
3机台上开关钥匙或安全保护装置的特殊工具,必须由资深工作员或主管保管。
3.2。
4确保机台周边没有任何障碍物堆置。
3.2.5在离开工作或检修机台以及基本维修工作前,务必关闭电源。
3.2。
6所有与本机维修和操作有关的人员对紧急停止按钮,各种安全开关,必须非常熟悉其所在位置、功能及操作方式。
加工厂加工车间作业指导书
2.3. 2首件检验的不良品必须做明确标识并放在不良品箱中
2. 3、1零件要按照顺序摆放,自主检查的产品必须要有标识或有区别放置,以利于追溯。
2、3、2刀具更换要记录刀具损坏原因,并且记录更换前和更换后记录。
1.1开启电源时要注意安全。
1.3作业标准书不应有手写或涂改现象
1.1检查空气压力必须符合规定,以防发生设备无法换刀。
1.1.2开启电源须按顺序。
1.2.1必须进行原点回归
1、2、2主轴逆转。
1、4工作平台必须清理干净不能有铁屑,以防止出现位置不准确问题。
2.2.1加工中心共有三轴,面对设备上下为Z轴补正方向上为+下为-,左右为X轴,补正方向左为+右为-,前后为Y轴补正方向向里为-向外为+。试加工必须要用单节执行。
2、2校刀时先用粗车刀找出Z轴0点,即总坐标值设为0,然后所有的外径内径刀的Z轴都以此点为0点,再校正X轴的数值。
2、3校正完成后就根据标准书调出程式进行首件加工,完成后送品管课进行首件检验,并将记录抄到首件检验纪录本上,如果有不合格尺寸,应将该件产品做不良标识,放不良品箱内,然后针对不良尺寸进行刀具补正,再次送品管进行检验直至所有尺寸全部合格。
制订
审核
核准
******************有限公司
标准类
文件名称
钻床攻牙床作业标准
页次
1/2
文件编号
CC-C-05
版本
A
程序
作业内容
管制点
注意事项
1.准备
2、加工
1.1将设备后面闸刀总开关置于ON位置,按押扣开关绿色键开启设备预热3分钟。
1.2领取《机械加工作业标准书》,根据标准书领取量具、钻头或丝锥、夹治具。
- 1、下载文档前请自行甄别文档内容的完整性,平台不提供额外的编辑、内容补充、找答案等附加服务。
- 2、"仅部分预览"的文档,不可在线预览部分如存在完整性等问题,可反馈申请退款(可完整预览的文档不适用该条件!)。
- 3、如文档侵犯您的权益,请联系客服反馈,我们会尽快为您处理(人工客服工作时间:9:00-18:30)。
测量
D923 表 台
6~10
2 次/ 小时
20
2 次/ 每班
首件
停机
2 Vds
≤0.05
测量
内径标准 件
6~10
2 次/ 小时
20
2 次/ 每班
记录
隔离
操作要领
(1) 操作者开机前检查工艺文件是否齐全.有效 (2) 操作者开机前认真查对标准件和被加工套圈是否一致 (3) 操作者开机需要与检查员相互校对测量仪器是否一致 (4) 加工前首先要掌握本工序加工所依据的工艺文件以及上道工序流
序
检验
号
项目
规范 公差
检查 方法
测量设备
操作者
检查员
容量 频率 容量 频率
控制 方法
日期
零部件图号
零部件名称
工序名称
工序号
共页
粗车外径 另一端
3411025-5K10
套圈
面
2
第 2页
1
倒内外工艺角
前工序名称 粗车内径一端面
工装名称
内夹具 设备名称 液压车床
后工序名称
软磨平面
工装编号
Z518-00-0
内径标准件
1
d
φ45.15-00.2 测量
L614-03 百分表
6~10
2 次/ 小时
20
2 次/ 每班
首件
(0~10/ 0.010)
记录
2B
22.70-0.15
测量
滚道宽度卡板
6~10
2 次/ 小时
20
2 次/ 每班
抽检
L617-02-01
3
(B-C)/2
4.750+0.15
测量
挡边宽度卡板
6~10
标记 处数
更改文件号 签字 日期
安徽凡尔采掘设备制造有
标记 处数 更改文件号 签字 日期
作业指导书
主轴转速 710 转/分
编制(日期)
切削规范
切削速度 98 米/分
审核(日期)
走刀量
切削深度
0.4~0.6 毫米/转 0.6~1mm
会签(日期)
批准(日期)
零部件图号
零部件名称
工序名称
工序号
共页
限公司
装夹具 (6) 首件.换砂轮所有项目要自检 (7) 在加工和搬运过程中要轻拿轻放.以防工件磕.碰.划伤 (8) 按磨削规范调整机床,正确安装并调试工装夹具 (9) 每星期更换一次切削液
磨削规范
砂轮转速
970 转/分
编制(日期)
审核(日期)
进给量
0.02mm
会签(日期)
批准(日期)
标记 处数
更改文件号 签字 日期
安徽凡尔采掘设备制造有
标记 处数 更改文件号
签字 日期
作业指导书
零部件图号
零部件名称
工序名称
工序号
共页
限公司
简 图
3411025-5K10 1
前工序名称
套圈 软磨平面
后工序名称 车档边内径
软磨外径
4
第4 页
工装名称 工装编号
托板 设备名称 无心磨床
Z519-01-0
设备型号 M1083
1
与 技 术 要 求
转下来的毛坯是否有合格标志 (5) 按切削规范要求调整机床,正确安装并调整工装夹具,导向基准的夹
具 及 主 轴 径 向 跳 动 不 大 于 0.03mm, 定 位 平 面 跳 动 不 大 于 0.03mm,夹紧力要适当,以防工件变形而造成废品 (6) 首件.换胎时对所有项目要自检 (7) 在加工和搬运过程中轻拿轻放.以防工件磕碰伤.划.伤
测量
m (±100)
6~10
2 次/ 小时
20
2 次/ 每班
记录
隔离
4 △Cir
≤0.05
测量
测量垫
6~10
2 次/ 小时
20
2 次/ 抽检 每班
调整
5
SD
≤0.06 测量
6~10
2 次/ 小时
20
2 次/ 每班
操作要领
(1) 操作者开机前检查工艺文件是否齐全.有效 (2) 操作者开机前认真查对标准件和被加工套圈是否一致 (3) 操作者开机需要与检查员相互校对测量仪器是否一致 (4) 加工前首先要掌握本工序加工所依据的工艺文件以及上道工序流
转下来的毛坯是否有合格标志
(5) 按切削规范要求调整机床,正确安装并调整工装夹具,导向基准的夹
具 及 主 轴 径 向 跳 动 不 大 于 0.03mm, 定 位 平 面 跳 动 不 大 于
0.03mm,夹紧力要适当,以防工件变形而造成废品
反应
(6) 首件. 换胎时对所有项目要自检
计划 (7) 在加工和搬运过程中轻拿轻放.以防工件磕.划.伤
工序名称
工序号
共页
粗车内径.一端面
1
第1页
工装名称 工装编号
外夹具 设备名称 液压车床
Z517-00-0
设备型号 CA7620
1
操作要领
ห้องสมุดไป่ตู้
(1) 操作者开机前检查工艺文件是否齐全.有效
(2) 操作者开机前认真查对标准件和被加工套圈是否一致
(3) 操作者开机需要与检查员相互校对测量仪器是否一致
(4) 加工前首先要掌握本工序加工所依据的工艺文件以及上道工序流
2 次/ 小时
20
2 次/ 每班
首件
3
Vdp
≤0.10
测量
(0~10/ 0.010)
6~10
2 次/ 小时
20
2 次/ 每班
记录
4
C
33.50+0.
2
测量
卡尺
(0~150/0.02)
6~10
2 次/ 小时
20
2 次/ 抽检 每班
零部件图号 3411025-5K10
1 前工序名称
零部件名称 套圈
后工序名称 粗车外径一端面
磨削规范
砂轮转速
进给量
导轮转速
中心高
1050 转/分
编制(日期)
0.02mm
审核(日期)
34 转/分
会签(日期)
320~ 330mm
批准(日期)
标记 处数
更改文件号 签字 日期
标记 处数 更改文件号 签字
日期
安徽凡尔采掘设备制造有 限公司
简 图
作业指导书
零部件图号 3411025-5K10
1 前工序名称
10 每盘
20
2 次/ 记录 每班 抽检
隔离 调整
测量垫
操作要领
(1) 操作者开机前检查工艺文件是否齐全.有效 (2) 操作者开机前认真查对标准件和被加工套圈是否一致 (3) 操作者开机需要与检查员相互校对测量仪器是否一致 (4) 加工前首先要掌握本工序加工所依据的工艺文件以及上道工序
流转下来的毛坯是否有合格标志 (5) 操作者加工第一个套圈时应重新调整机床.正确安装并调试工
2 次/ 小时
20
2 次/ 每班
L617-03-01
反应 计划
停机 隔离 调整
(1) 操作者开机前检查工艺文件是否齐全.有效 (2) 操作者开机前认真查对标准件和被加工套圈是否一致 (3) 操作者开机需要与检查员相互校对测量仪器是否一致 (4) 加工前首先要掌握本工序加工所依据的工艺文件以及上道工序流
转下来的毛坯是否有合格标志 (5) 操作者加工第一个套圈时应重新调整机床.正确安装并调试工装夹
具 (6) 首件.换砂轮所有项目要自检 (7) 在加工和搬运过程中要轻拿轻放.以防工件磕伤.碰.划伤 (8) 按磨削规范调整机床,正确安装并调试工装夹具 (9) 出现不合格品时,立即停机,隔离工件,如不能调整机床立即通知班长 (10) 每星期更换一次切削液
后工序名称
零部件名称 套圈
软磨外径 倒角
工序名称
工序号
共页
车档边内径
5
第5 页
工装名称 工装编号
外夹具 设备名称 液压车床
Z517-00-0
设备型号 CA7620
1
与 技 术 要 求
序 检验 号 项目
规范 公差
检查 方法
测量设备
操作者
检查员
控制
容量 频率 容量 频率 方法
反应 计划
1
d
φ42.90-0.15
6~10
2 次/ 小时
20
2 次/ 抽检 每班
调整
6 r外
0.5×45° 目测
6~10
2 次/ 小时
20
2 次/ 每班
主轴转速 710 转/分
编制(日期)
切削规范
切削速度 93.6 米/分
审核(日期)
走刀量
切削深度
0.5~0.8 毫米/转 0.7~1.0mm
会签(日期)
批准(日期)
标记 处数 更改文件号 签字
简 图 与
3411025-5K10 1
前工序名称
后工序名称
套圈
粗车滚道
7
第7页
倒角 精车滚道
工装名称 工装编号
外夹具 设备名称 液压车床
Z517-00-0
设备型号 CA7612
1
操作要领
技 术 要 求
序 检验 号 项目
规范 公差
检查 方法
测量设备
操作者 容量 频率
检查员
容 频率
量
控制 方法
D923 表台
3 Vdp
≤0.05
测量
L614-02
百分表 (0~10/