焙烧极常见外观缺陷分析
阴极焙烧炉常见问题及解决方法

阴极焙烧炉常见问题及解决方法摘要随着后金融危机到来,全球经济处于复苏期,金属铝需求回升,电解铝企业也逐步恢复生产,整个阴极炭块市场也逐渐好转,阴极焙烧炉作为阴极碳素制品重要生产工具,在生产过程中,阴极焙烧炉存在一些常见问题,需要采取一定措施进行解决,本文就针对阴极焙烧炉中常见问题进行了分析,并提出了相应的解决方法。
关键词阴极焙烧炉;常见问题;解决方法随着我国铝电解业的快速发展,阴极炭块质量与产量均获得了较大提高,我国阴极焙烧炉绝大多数为带盖环式的焙烧炉,这种焙烧炉在生产过程中,常会出现一些问题,影响阴极炭块的生产质量与数量,并且也不符合现代减排低耗要求,为增强阴极炭块质量与生产效率,采取合理方式尽心解决,可有效推动我国铝电解业发展,增强市场竞争力。
1 阴极焙烧炉常见问题阴极碳素制品原料多为沥青焦、石油焦与无烟煤等,通过破碎、煅烧与配成型后,增强机械强度,并减低电阻率,焙烧生制品,我国阴极焙烧多数是带盖式的焙烧炉,设备包含阴极焙烧炉、吸料罐、燃烧控制装置与冷却炉盖等,在整个系统中,阴极焙烧炉为主要设备,随着铝电解业不断发展,阴极的碳素制品的产量与质量要求越来越高,原有阴极焙烧炉缺点逐渐暴露,国内焙烧炉多是采用带盖的环式焙烧炉,路改多采取高铝砖与钢框架结构所砌筑城的,首先,炉盖具有砌筑时间长与施工难度大的问题,炉盖为矩形结构,由两个拱进行砌筑城的,甚至有时需要加工砖进行砌筑,一个炉盖需要4天左右时间方能完成,极大消耗了时间;其次,阴极焙烧炉砌砖厚度较大,不一般不容易烧透,在生产当中,砌砖拱顶向下塌,易出现严重变形,砌砖质量也难以得到有效保证,生产之后就容易出现收缩问题,带来生产安全隐患;再者,隔热性能非常有限,不利于散热,稳定性也不好,火焰接触部位的剥落较为严重,传统阴极焙烧炉的气孔率比较大,抗高温的气流冲刷力较弱,铝质材料的耐热耐冷性能比较差,容易出现裂纹,出现剥落状况,而带盖焙烧炉要求耐高温的同时,有需要保温,耐火砖材料是相同的,焙烧过程中,容易出现热量散失严重问题,加大了能量消耗;然后,阴极带盖焙烧炉的内部结构常会出现不合理现象,料箱装炉量比较小,料箱小又带有隔墙,整体散热面积比较大,绝热保温性能也不高,烟气的流通阻力强,负压损失比较大,对于燃烧进行控制难度大,焙烧的能耗高而周期又较长,在生产过程中,这些问题是带盖焙烧炉常见问题,采取一定措施解决这些问题是必要的。
焙烧工艺、网络结构及常见故障

排测 烟温 架测
1压 P架
燃燃 燃
零燃
零
烧烧 烧
压烧
压
架架 架
架架
架
4
54
56
6
P PP P
P
鼓
风 架
移炉后
10 P
焙烧控制及网络结构
7、自动化控制原理:
从焙烧炉各点采集的温度和负压信号经本地控制系统可编程PLC节点控制 器处理,并周期性传输至中央控制室调节站,调节站将这些信号与设定值进行对比 分析处理,并将指令通过PLC节点控制器送至燃烧器的电磁阀以调节燃料输入量 和排烟架蝶阀开度,达到温度和负压的调节。 自动控制:每个燃烧架根据各自的烟气温度实测值与设定值的对比来PID调节 喷嘴喷气量,形成温度闭环控制。
自然 冷却炉室
强制 冷却 炉室
修整 炉室
装出炉 炉室
排测
燃燃 燃 零
鼓
烟温
烧烧 烧 压
风
架测
架架 架 架
架
1压
45
6
10
P架
PP P
P
焙
风机
烧
天燃气 天燃气 天燃气
净
烟道
地
下环形烟道
化
焙烧工艺简介
6、移炉过程:
排测 烟温 架测 1压 P架
燃燃
燃
零
烧烧
烧
压
架架
架
架
45
6
PP
P
鼓
风 架
移炉前
10 P
CP343-1
CP343-1 CP343-1 CP343-1
CP343-1
CP343-1
ER34
HR31 HR32 HR33
炭素焙烧炉横墙开裂原因与对策分析
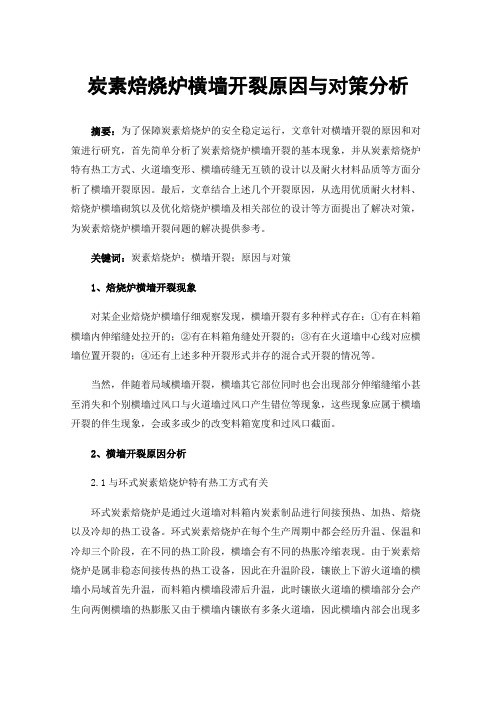
炭素焙烧炉横墙开裂原因与对策分析摘要:为了保障炭素焙烧炉的安全稳定运行,文章针对横墙开裂的原因和对策进行研究,首先简单分析了炭素焙烧炉横墙开裂的基本现象,并从炭素焙烧炉特有热工方式、火道墙变形、横墙砖缝无互锁的设计以及耐火材料品质等方面分析了横墙开裂原因。
最后,文章结合上述几个开裂原因,从选用优质耐火材料、焙烧炉横墙砌筑以及优化焙烧炉横墙及相关部位的设计等方面提出了解决对策,为炭素焙烧炉横墙开裂问题的解决提供参考。
关键词:炭素焙烧炉;横墙开裂;原因与对策1、焙烧炉横墙开裂现象对某企业焙烧炉横墙仔细观察发现,横墙开裂有多种样式存在:①有在料箱横墙内伸缩缝处拉开的;②有在料箱角缝处开裂的;③有在火道墙中心线对应横墙位置开裂的;④还有上述多种开裂形式并存的混合式开裂的情况等。
当然,伴随着局域横墙开裂,横墙其它部位同时也会出现部分伸缩缝缩小甚至消失和个别横墙过风口与火道墙过风口产生错位等现象,这些现象应属于横墙开裂的伴生现象,会或多或少的改变料箱宽度和过风口截面。
2、横墙开裂原因分析2.1与环式炭素焙烧炉特有热工方式有关环式炭素焙烧炉是通过火道墙对料箱内炭素制品进行间接预热、加热、焙烧以及冷却的热工设备。
环式炭素焙烧炉在每个生产周期中都会经历升温、保温和冷却三个阶段,在不同的热工阶段,横墙会有不同的热胀冷缩表现。
由于炭素焙烧炉是属非稳态间接传热的热工设备,因此在升温阶段,镶嵌上下游火道墙的横墙小局域首先升温,而料箱内横墙段滞后升温,此时镶嵌火道墙的横墙部分会产生向两侧横墙的热膨胀又由于横墙内镶嵌有多条火道墙,因此横墙内部会出现多个小局域的方向不同的热膨胀。
边料箱温度低于中间料箱的温度。
因此,中部横墙要向两侧低温区横墙产生热膨胀及热应力,最终形成横墙的位移。
焙烧炉在保温和冷却阶段,无论鼓风架还是冷却架鼓入的冷空气,会使火道对应的横墙段降温相对较快,而料箱对应的横墙段降温较慢(因料箱物料多,热焓大,且有填充料密封,散热差),这样在每个火道对应横墙段与相邻料箱对应的横墙段的小局域范围都会出现温差,料箱处横墙因温度高有向火道处横墙冷缩的热力学运动,会引起料箱处横墙伸缩缝加大的趋势。
论焙烧炭块水平裂纹产生的原因及控制措施郑爱平_1

论焙烧炭块水平裂纹产生的原因及控制措施郑爱平发布时间:2021-09-13T05:57:44.947Z 来源:《中国科技人才》2021年第16期作者:郑爱平[导读] 水平裂纹是现阶段焙烧出炉炭块的常见问题之一,造成这一问题出现的原因主要有生产配方、成型机运行参数、原材料质量等诸多方面。
黄河鑫业有限公司摘要:水平裂纹是现阶段焙烧出炉炭块的常见问题之一,造成这一问题出现的原因主要有生产配方、成型机运行参数、原材料质量等诸多方面。
鉴于此,本文先是阐述了焙烧炭块的主要生产工艺,又分析了现阶段焙烧生产中的常见问题及裂纹产生的主要原因,最后详细研究了如何解决焙烧炭块的水平裂纹,仅供相关人员进行借鉴与参考。
关键词:焙烧炭块;水平裂纹;控制措施随着经济社会的发展与科学技术的进步,我国的电解铝工业获得了极大的发展与进步,但与此同时也对焙烧工作的质量与安全要求逐渐提升。
一般而言,外表有水平裂纹的焙烧炭块往往会在电解的过程中产生阳极断层,严重降低了电解生产工作的安全与质量。
因此,在焙烧炭块的生产过程中采取有效措施控制水平裂纹的产生就十分必要且十分重要了,现就对其进行详细的探讨。
1 焙烧炭块的生产工艺原料石油焦粗碎后进入回转窑,经过1300℃左右的高温处理后成为煅后石油焦,送到煅后焦仓贮存。
固体沥青经过熔化、静放合格后,用沥青泵送入高位槽。
煅后焦经中碎、筛分、磨粉后分别送到各自配料仓,经电子配料秤称量后进入预热机预加热[1]。
液体沥青经配料称称量后加入已经进行一段时间干混预热的混捏机内,与加温后的混合煅后石油焦一起进行混捏。
混捏好的糊料送到成型机,在模具内振动成型。
用水冷却后的炭块进入生块库静放。
静放好的生炭块由堆垛天车经板式输送机送到焙烧,经编组后用多功能天车装入焙烧炉。
生炭块经过焙烧后成为熟块,将炭块表面粘结的填充料清理干净后送往成品库贮存。
2 焙烧炭块生产中存在的问题2.1水平裂纹的出现近两年在焙烧生产过程中出现大量带有水平方向裂纹的炭块,裂纹位置在炭块大侧面,裂纹长度在500 ~ 1000mm,宽度在1mm 左右,深度2 ~ 5mm,部分裂纹附近可见挥发分溢出时形成的黑色痕迹。
影响生阳极外观缺陷的因素

影响生阳极外观缺陷的因素为了减少成型生阳极外观缺陷而产生废品,分析生阳极生产工序中的裂纹、表面破损、表面松疏、掉棱、掉角、粘料等主要因素对生阳极外观缺陷的影响,找出解決措施,来达到减少生阳极外观缺陷的目的。
标签:生阳极、外观缺陷、影响因素前言成型是预焙阳极生产的第二道工序,其主要任务是把经过煅烧后的石油焦、预焙阳极生产及使用过程中产生的生碎、残极以及作为粘结剂用的沥青这四种原料按一定技术要求进行加工处理、生产出具有一定规格和质量要求的生阳极。
而我们生产出来的生阳极制品的合格率不是100%的,都有这样和那样的缺陷导致废块。
随着生产负荷的不断加大,加之设备的进一步老化,生阳极外观缺陷量不断增加,因此减少生阳极外观缺陷是至关重要的。
为了减少生阳极在生产过程中产生的废块,降低生产成本,对影响生阳极外观缺陷的因素进行分析,而生阳极的外观缺陷又受到该工序中产生的裂纹、表面破损、表面松疏、掉棱、掉角、粘料等诸多因素的影响。
现对主要影响因素进行分析,并找出解决措施。
1.生阳极纵裂1.1输送链板或平板小车水平度不够振动成型后的生阳极温度较高且相对比较软。
如果平板小车的钢板有变形、凹凸不平,冷却输送机链板不在同一水平面上时,推到平板小车、输送机上的生阳极,在重力作用下会使生阳极产生纵裂块。
定期对冷却输送机链板及平板小车的水平度进行检测,对链板凸起难以调整的链板进行更换,确保链板与链板之间水平基本一致。
1.2沥青用量过多,弹性膨胀较大沥青用量过多时,振动成型后的生阳极弹性膨胀较大,应力消失比较慢,导致生阳极产生纵裂。
随着沥青用量的增大,糊料的流动性较好,均匀性增强,糊料的塑性变好。
但沥青用量不宜过多,会使生阳极变形弯曲而产生裂纹。
因此,沥青配入量应控制在14.5%—17.5%之间。
1.3成型温度高,烟气排不净糊料温度高时沥青烟气排除不净,也容易产生裂纹。
糊料在较高温度下成型可有效减小糊料粘度,提高生阳极的体积密度,但成型温度过高将导致过量的沥青气相压力,此压力在成型机强压受迫振动下因气体体积压缩而进一步增大,当外部压力释放后,此气相压力在制品内部结构薄弱及存在缺陷的地方首先突破,通过水平方向微裂纹的生成扩展得以释放,并在制品内部形成拉伸应力,而产生纵裂。
砖焙烧后成品的常见问题和防治

砖焙烧后成品的常见问题和防治1炸裂当入窑砖坯的残余水分过高,预热带初期的升温速度又超过了25~35℃/h 时,坯体中迅速汽化了的蒸汽来不及排出,挤炸砖坯。
残余水分越高,情况也越严重,甚至窑顶可听到炸裂声,尤其在蹲火后刚进人预热带的砖坯。
因这时该段温度较高,更易产生炸裂。
如果只是预热带升温较急,残余水分并不太高,水汽常只挤破砖坯表层,形成蛛网般的细裂纹。
对此,除应控制人窑坯的残余水分低干8%外,还应适当延长预热带,使缓慢升温均匀脱水,以及在蹲火及轮窑烧纸挡后缓慢提远闸,慢慢加高。
2发状裂纹砖面上出现浅细而基本上没有分岔近似直线的裂纹,是保温不够急冷造成。
为此,应有10~15 排长度的保温带,轮窑不可近打窑门,隧道窑不许把保温带推到窑门上,和焙烧带后不许长时间揭火眼灌冷风。
3本来没有裂纹的砖坯烧成后大面上出现大裂纹,有时裂纹还延伸到条面或顶面。
这大多是成型时留下的隐患,焙烧又用闸不当,裂纹扩大。
为此,应适当降低原料的塑性指数,调整砖机螺旋绞刀的转速和螺旋角,采用分离式螺旋绞刀,并在泥缸上加打泥棒以减轻泥料分层;或采用热水、蒸汽搅拌、真空挤泥等措施来减少泥料中的水、气来消除分层。
另外焙烧应正确用闸,均匀排潮以及分次落实门前闸等。
4泛霜砖面上生出一层白色粉末。
这是砖体残留有硫酸镁、硫酸钠等可溶无机盐,吸水后渗出表层蒸发后的残留物。
由于坯体含有一定数量的结晶水,脱水后膨胀,因此,在泛霜时还会崩裂砖的表层。
为此,应控制泥料中氧化镁的含量低于3%。
强化粉碎,提高细度和适当延长焙烧及保温时间,使生成不溶于水的硅酸盐,减轻或杜绝危害。
5石灰爆裂原料中的石灰石焙烧后变成生石灰,出窑后吸收空气中的水分生成熟石灰,体积剧烈膨胀而破坏砖体,叫石灰爆裂。
空心砖壁薄,危害更大。
为此,除要求原料中氧化钙的含量应少于10%以外,还必须粉碎到粒径小于2mm,以化整为零减轻危害。
在焙烧时把烧结温度提高到允许的最高烧成温度,并充分保温,使生成不溶的硅酸钙。
隧道窑焙烧时常见问题产生的原因及防治_用好管好您的隧道窑之一
综合报道
COMPREHENSIVE REPORT
砖
拉条坯 t2 t1+t2+t3≈S+S S:坯垛与窑墙之间的间隙 t:坯垛之间的拉缝 t3 窑宽2500,坯垛宽500 S1=S2=50~80 t1=140;t2=t3=100
瓦世
界
论 坛
2012.2 2012 来了。 这时最怕的是底火严重超温、 坯体软化、 坯垛 倒塌, 造成焙烧带倒窑。 如果是外投煤较多, 且直落坯垛底部, 造成底 火太大应立即降低远闸, 减小炕腿风的抽力, 同时 调低首闸, 封闭焙烧带火眼, 不使冷风侵入降温。 治本的办法则是码窑时砖坯之间至少应留有 10~15mm (约一指宽) 的风道。 () 8 中火超前, 边火滞后: 焙烧带坯垛中部火势 超前于两边两排以上, 同断面上中部砖坯温度高于 两边 100℃以上。 隧道窑码坯时, 坯垛两边和顶部都必须留有 50~80mm 间隙, 形成一条通畅的风道, 而坯垛上砖 坯之间的缝隙才 15~50mm, 于是大量风从坯垛两侧 快速通过, 带走大量热能, 中部砖坯 “捂着烧” 热又 散不出去, 结果必然造成中火大, 边火弱, 看起来就 像 “中火超前, 边火滞后” 。 其治本的办法是坚持中稀边密的码窑原则, 在 整个坯垛的中部留出通风道, 其留出的通风道的宽 度之和应等于坯垛两侧与窑墙的间隙之和, 以平衡 断面风速, 坯垛断面上留出的通风道宜中间最宽, 两边渐窄, 最好是码成若干个坯垛, 使在窑车上的 坯垛形成纵横风道, 更有利于减少断面温差, 如果 窑高较高, 可以在坯垛上部用几块 “拉条坯” 把相邻 坯垛连起来以增加坯垛的稳定性。 这种分垛拉缝码法的示意图见图 1。
2012.2
论 坛
综合报道
COMPREHENSIVE REPORT
陶瓷烧成缺陷及原因分析
陶瓷烧成缺陷及原因分析发布时间:2008-8-4 15:07:14 阅读:52 次新闻来源:作者:(一)变形:产品烧成变形是陶瓷行业最常见、最严重的缺陷,如口径歪扭不圆,几何形状有不规则的改变等。
主要原因是装窑方法不当。
如匣钵柱行不正,匣钵底或垫片不平,使窑车运行发生震动,影响到产品的变形。
另外,产品在烧成中坯体预热与升温快时,温差大易发生变形。
烧成温度过高或保温时间太长也会造成大量的变形缺陷。
使用的匣钵高温强度差、或涂料抹不平时也会造成烧成品的变形。
(二)开裂:开裂指制品上有大小不同的裂纹。
其原因是坯体入窑水分太高(大于2%以上),预热升温和冷却太快,导致制品内外收缩不匀。
有的是坯体在装钵前已受到碰撞有内伤。
坯体厚薄不匀,配件(如壶把、咀等)重量过大或粘结不良也会造成制品开裂。
防止的办法是:(1)入窑坯体水分小于2%,车速适当减少冷却量。
(2)装窑时套装操作谨慎,垫片与坯体配方一致。
配件大小、重量与粘接位置恰当。
有的在粘接泥浆中加入10-15%的釉料,可以使咀、把与主体牢固熔接一体,如此可克服开裂缺陷。
(三)起泡:烧制品起泡有"坯泡"与"釉泡"两种。
坯泡分为"氧化泡"与"还原泡"两种。
氧化泡指坯泡外面覆盖釉层,断面呈灰黑色,多形成于窑内低温部位。
主要是瓷胎与釉料中的分解物未能充分氧化,烧失物未完全排除所致。
予热升温快,氧化分解阶段时间短、氧化结束时窑内温度过低,上下温度差过大。
在坯釉料中,碳酸盐。
硫酸盐及有机杂质含量较多等都是造成产品起泡的主因。
此外时装车密度不当、入窑水份高等原因亦须注意。
还原泡又称过火泡,断而发黄,多发生于高温近喷火口处的制品。
主要由于坯体内硫酸盐与高价铁还原不足,强还原气氛不足及烧成温度过高造成。
釉泡系沉积炭及分解物在釉熔前未能烧尽挥发,气体被阻于釉面层中形成。
若延长釉熔时间或适当平烧即可解决。
焙烧后产品失色分析
因为碳酸钡在水中的溶解度较小, 所以加入的量通常是原 材料中 (*# 含量的两倍, 以保证起充分反应。氯化钡也是一种 可引起泛白的物质, 因为氯化钡的溶解度很高, 其熔点也很高, 即便是在原料中的含量很少, 也能够引起泛白。但是氯化钡也 可以用来作为防止硫酸钙、 镁泛白的外加剂, 特别是硫酸钙、 镁 含量相对高时, 因氯化钡的溶解度比碳酸钡的大得多。但在实 际应用时, 氯化钡的加入量约为理论需要量的三分之二, 余量 因碳酸钡来补充和纠正, 这样做是为了防止氯化钡过量时引起 的严重泛白。氯化钡与硫酸钙、 镁的反应如下: /%$’! 7 $% ( ,-) (*. !/%(*. 7 $% ( ,-) $’! ( 1. ) 氯化钙 和 氯 化 镁 不 会 引 发 泛 白, 因它们熔点 ( $%$’! — 99!: , ,-$’! —91!: ) 低于产品的最终烧成温度。在研究外加 剂 ; 改性木质磺酸钙的过程中发现, 由于木质磺酸钙在原料中 物理、 化学上的双重作用, 可有效地抑制碱土金属硫酸 $ $ $ $ !""# 年第 % 期
探 $
$
讨
$ $
本栏编辑: 李密芳$ $
大断面吊平顶隧道窑焙烧 原理上的探讨和建议 ( 三)
湛轩业$ 黄鹏选$ 吴$ 勇$ ( 西安墙体材料研究设计院, 陕西$ 西安$ %&""’& )
#$ 焙烧过程中颜色的形成与控制 #( &$ 焙烧后产品颜色的主要机理 在绝大多数烧结砖瓦产品中氧化铁是最重要和适应性最 强的着色剂, 因为在绝大多数原材料中均存在有 &) * +) 的 ,-! .# 。在某些情况下, 可加入过量的氧化铁来增强产品的颜 色。当 ,-! .# 被 /. 还原后, ,-! .# 则可能形成磁铁矿 ( ,-# .0 ) 或方铁矿 ( ,-.) , 这两种矿物在各种温度下均呈黑色。大多数 , 其颜色随温度而 情况下所产生的最高价态的赤铁矿 ( ,-! .# ) 异。赤铁矿的颜色来自于它的晶体结构缺陷, 而每个单位体积 中缺陷的数目随温度在增加。这种缺陷的发展是一可逆反应, 但是在空气中这种缺陷消除的速度比在加热期间形成的速度 来讲大大的减缓了, 因此在冷却过程中就能够容易的保持住在 最高温度下形成的缺陷结构。在非常低的温度下, ,-! .# 几乎 是橙黄色, 随着温度的升高出现了深红色, 到 &#&’1 时则近乎 于黑色。这就是说 ,-! .# 颜色的形成和控制完全取决于坯体 到达的最高温度。另外原材料中氧化铁含量的多少也影响着 颜色出现的深浅程度。在最高温度下常使用氧化铁的还原使 本来红色的坯体产生出黄色、 褐色、 黑色的产品, 这种过程称之 为 “ 转色” ( ,2345678) 。还原气氛是由减少供给的空气量造成不 完全燃烧或减少供给的空气又引入过量的燃料来实现。在转 色之后, 立刻进入冷却阶段。如果冷却带的环境空气中氧气含 量很高, 暴露的产品表面将有被重新氧化的可能, 又显示出红 颜色。如果希望得到黑色或深色的产品, 有一些特殊的技巧可 用来在冷却期间 “ 保持这种转色” , 如在最高温度下能够使 ,-. 熔融进入玻璃相, 这种还原态的物质就能够保存下来。当然要 做到这一点, 其烧成产品的吸水率将会非常低。最好的黑色产 品是一旦通过氧化期后就调节焙烧气氛接近于理论燃烧状态, 此后在最终烧成温度下转色 &"967。在较低烧成温度下转色的 另一种方法是在整个冷却期间向窑内引入 :) 的甲醇溶液直到 温度下降到 0:"1 。还有向窑内通入煤气、 天然气等方法来营 造还原气氛的作法。加入含锰材料也可制造深色产品。 在氧化气氛下氧化铁的颜色还与原料中的粘土矿物及在 高温下生成的结晶相物质有关。如耐火粘土焙烧后的颜色是 浅黄色, 既便是氧化铁含量达到了 :) 也是如此。单从氧化铁 含量上还不能够解释耐火粘土制品形成的浅黄色, 因为合理的 控制焙烧气氛, 耐火粘土制品也能够形成粉红色或浅红色。如 在弱还原气氛下焙烧, 并在冷却中将这种气氛保持到 ;+"1 , 耐 火粘土制品就得到了红色的色调。这种在色调上的变化可从 莫来石与 ,-! .# 之间的固溶体反应方面来解释。因为 ,-# < 离 子能够进入莫来石晶格, 在莫来石中 ,-# < 起着 =2# < 离子的作 用, 从而限制了铁的扩散。当 ,-# < 离子进入莫来石晶格后, 白 色的莫来石则变成浅黄色。在 &&""1 莫来石能够吸收 &( !) 的 ,-! .( 进入这种固溶体, 在 &!""1 时可吸收 #( +) , # 重量比) 在 &#""1 可吸收 %( ’) 。莫来石与 ,-! .# 之间的固溶体反应, 从坯体中取代了红色赤铁矿物相, 当足够量的莫来石形成后则 可吸收所有存在的氧化铁, 因而就消除了氧化铁的红色特征。 上述机理可解释在某些地区的煤矸石或页岩为什么在含铁量 不低的情况下, 烧成后的颜色总是黄色色调。 以伊利石为主要矿物的原材料, 在氧化气氛中烧成后的颜 色总是红色的, 因为这样的坯体中不能形成足够量的莫来石晶 体来吸收固溶体中所有的三价铁, 并且在伊利石原料的最高烧 成温度下 ( &";"1 ) , ,-! .# 没有反应能力, 所以它依然在产品 中以红色的物相出现。 在高钙质和高镁质坯体中, 即便其主要粘土矿物是伊利 石, 焙烧后的颜色仍然是浅黄色。所以常被认为是石灰的 “漂 白作用” 所致, 这种认识是错误的。 /3.、 >8. 或是它们的硅酸 盐根本就没有改变赤铁矿红颜色的能力。事实上钙、 镁的硅酸 盐在颜色上是白色的, 也根本不吸收 ,-! .# 。因为在高钙或高 镁质坯体中的主要高温物相是钙、 镁的硅酸盐, 并且由于继续 反应和烧结, 硅酸盐晶体的生长驱使赤铁矿进入晶粒边界。显 微镜的研究结果表明, 赤铁矿处于三个硅酸盐晶体连接聚集点 的空穴中。这种进入小空穴的赤铁矿单体, 在整个产品范围内 造成了宏观可见的粉红、 浅黄或黄色的表面, 具体的颜色要视 其碱土金属硅酸盐和赤铁矿的相对含量以及硅酸盐晶粒生长 的范围而定。 #( !$ 焙烧后产品的失色 ( ?64@A2ABC3D6A7) 对烧结砖瓦产品而言, 失去本身应有颜色的最大影响因素 莫过于泛白 ( E@B9) 。所谓泛白是指在产品表面上出现的难以
电极在焙烧过程中内裂分层的分析报告
电极在焙烧过程中内裂分层的分析报告用于电解铝生产的预焙阳极炭块,在电解槽上不仅起到导电的作用,而且还要参与化学反应,因此,预焙阳极质量的好坏将直接影响铝电解的生产及经济技术指标的提高,严重的裂纹掉块会导致电解槽长包,电解质含碳,生成碳化铝,电解槽侧部漏电等技术事故,电解槽运行不平稳,影响电流效率,同时裂纹废品的产生,也会造成炭素阳极生产单位成本的升高。
在实际生产过程中,由于阳极炭块的焙烧处于全封闭的系统,从煅后焦原料的生产到生阳极的成型,以及生阳极炭块的焙烧,其化学物理变化过程非常复杂,具体造成焙烧块内裂的原因也较为复杂。
1、原料对预焙阳极的影响
通过国内外的研究数据,石油焦粉的粉末比电阻率直接反映煅后焦质量,如煅后焦煅烧程度不足,焙烧的过程中会产生二次收缩,会造成炭块内裂。
成型原料改质沥青中甲苯不溶物等指标应满足炭素制品的理化指标要求,黏度不够、糊料疏松。
生阳极制品的内部结构不均,各部位迁移程度不同,易产生内裂分层废品,造成炭块的内裂。
2、阳极焙烧过程的影响
在控制煅后焦原料的基础上,焙烧过程中降温速率也会对是否产生内裂产生很大影响,如果焙烧过程中降温冷却速度过快也会导致阳极内部裂纹。
- 1、下载文档前请自行甄别文档内容的完整性,平台不提供额外的编辑、内容补充、找答案等附加服务。
- 2、"仅部分预览"的文档,不可在线预览部分如存在完整性等问题,可反馈申请退款(可完整预览的文档不适用该条件!)。
- 3、如文档侵犯您的权益,请联系客服反馈,我们会尽快为您处理(人工客服工作时间:9:00-18:30)。
焙烧极常见外观缺陷分析摘要:本文立足于阳极焙烧几年来的生产实践及取得的经验,对焙烧块常见外观缺陷产生的原因进行简要分析,并提出了一些建议以供探索。
关键词:焙烧外观缺陷分析探索一、焙烧的目的焙烧是炭阳极生产流程中的一个重要环节、也是影响产品质量的重要工序之一。
在一定的混捏配料、振动成型工艺下形成的生块经过热处理,使之成为具有一定理化性能和外观要求的熟块,以满足铝电解生产工艺之需要.二.焙烧机理1.以粘结剂-改质沥青为载体看生块在焙烧过程中的变化:(附表格1)表-1 生块焙烧过程中性能变化表[注:本组数据取自于<<炭素工艺学>>--冶金工业出版社,仅供参考]2.石油焦煅烧温度T1 阳极焙烧温度T2 电解液温度T3 之间的内在逻辑性:T1>T2>T3 其中兼顾考虑到a。
石油焦中硫份在焙烧过程的气胀行为;b。
石油焦和沥青在电解过程中存在选择性氧化之差异(即工业术语下的掉炭渣)一般T1略大于T23。
改质沥青即高温沥青,和一般中温沥青相比,其软化点高(95-120℃),挥发份含量低、残炭率高.从以上可知焙烧过程实质上是粘结剂-沥青不同温度段的软化迁移、挥发份逸出、焦化收缩特性在工业生产中的应用.三、常见外观缺陷:焙烧阳极质量主要从理化性能和外观质量两方面进行评价、衡量。
作为外观质量更为直观地体现了阳极焙烧的过程控制状态和特征。
1998年至1999年焙烧块质量情况见表2:表-2 98-99年焙烧块外观质量统计表由表明显看出,不合格项主要为:水平裂纹、垂直裂纹、孔间裂纹及其它(包括长包、底缺、掉棱角、变形、粘料等). 四、焙烧裂纹裂纹是最常见的外观缺陷,主要体现为孔间裂纹.水平垂直裂纹.从工业生产上看,裂纹产生的主要原因有:1.前期的密度差在后期相对一致温度下因收缩不一造成的裂纹.2.前期相对均匀的密度在后期较大温差下收缩不一产生的裂纹.3.内在的气体急剧逸出造成过大的应力.然而对于同一制品裂纹,其往往是以上三种原因掺混在一起综合作用的结果.使解决实际问题的难度比理论上分析要复杂得多.这时候只有在理论指导下,通过实践摸索的经验才能进一步从中找到问题的主要矛盾和矛盾的主要方面所在。
<一>.水平、垂直裂纹从实际出炉炭块出现这种机率看:大多数表现在中层块.特别是1997年下半年至1998年上半年尤为突出.究其原因:1.挥发份的逸出.沥青中的挥发份逸出一般发生在焙烧升温过程中的中间阶段,其逸出速度过快将会造成炭块产生裂纹,这也是行业一致所要求“两头快、中间慢”的升温原则,当然这也是一个建立在特定原料性能、工艺特征等个性基础上的相对概念。
通过实测阳极温升情况并表格化如下:(1)、测量时间:2000年4-5月。
(2)、炉室采用160小时/5室运行。
(3)、测量元件:K-型热电偶。
(4)、测温点均为料箱C端尾部中心靠近隔墙处,测量深度均为120cm.表-3 阳极焙烧关键阶段温升速率表(℃/h)从出炉炭块外观情况看:在稳定目前改质沥青性能条件下,只要阳极在挥发份逸出过程中其温升速率维持在小于 8-10 ℃/h范围内.沥青本体中的挥发份逸出造成的应力不足以使炭块产生“大面积”的水平、垂直裂纹.2、硫份的气胀行为。
相反,对于煅烧工序难以排除的硫份在焙烧过程中将以H2S、C2S等形式释放出来,使焦炭气孔壁受到排除气体的压力、体积产生膨胀,在后来的收缩时制品各部分不能均匀收缩或回不到原来的位臵而产生裂纹。
从实际上看其影响住住是致命的。
特别是97年下半年至98年上半年尤为明显,从表二中可以看出。
以水平裂纹为主要外观缺陷曾一度危及生产的连续性,当时原料��石油焦的硫份含量高情况详见表4(注:原工艺设计上要求石油焦含硫≯1.5%).后来通过对当时高硫份石油焦进货源头进行积极有效地控制,在1998年的下半年由于水平裂纹得以控制使综合外观合格率明显回升并在1999年一至保持了良好的走势。
表-4 97下半年、98上半年石油焦含硫情况表(%)3、其它因素的影响。
a、火道墙的变形。
如图1所示:火道墙变形、扭曲结果会造成同一炭块的同一面上形成了温度差,从实例看:(1)、火道内A、B、C三域之间不同程度的存在着较大温度差,其温度差又将会随当时挥发份燃烧不好而进一步加大;(2)、炭块各部位至火墙间的填充料厚度不一。
从而产生炭块各部位温度相差较大。
当然这种影响实际上是很难作出定量评价的,这是因为最终是否会产生裂纹一方面要看这种温差产生的应力大小,同时还取决于糊料的混捏效果、生块的振动情况以及生产所用沥青的β树脂含量。
b、负压操作下的火道温度之间平衡情况。
c、装炉质量、料箱结焦等。
b、c的影响程度和实质基本上和a相同。
对于a~c这些因素,一般都是以一种周期性、个别形式出现,故只要对这类问题从日常运行中加强管理便可得以一定程度的控制。
至于实际生产中出现水平裂纹的频度之所以比垂直裂纹多,那是因为除了和炉型结构等因素联系在一起外,还要考虑到振动成型的炭块本身在高度方向上存在一个密度差。
<二>.孔间裂纹从我厂实际生产应用来看,这种缺陷绝大部分体现在表层块.如右图2所示:对于这种形式的阳极缺陷占有较大的频数。
分析其可能性原因:1、冷却因素的影响:阳极炭块在冷却阶段的工艺控制要求其温度下降不能过快,但从阳极炭块冷却实际温降速率(附表5:测量条件和方法同表-3)看,其速率应属于行业的正常范围.目前所出现的这种孔间裂纹基本上可以排除是整体冷却过快所致.表-5 阳极关键阶段冷却速率表[℃/h]同时为考察是否存在表层块表面相对本身下部冷却过快,特先后两次对阳极炭块从其冷却开始进行覆盖保温试验,以使孔间所在的表面冷却不致过快. 但从试验结果看并不存在某种很强的内在必然性.因为所覆盖炉室的炭块出炉后仍然体现出通常水平频度的孔间裂纹。
2、沥青的液态迁移。
由于这种缺陷是以一种普遍现象存在,故可以暂且避开随机下的个别火道墙形变。
装炉水平等因素的影响而单独考虑沥青的液态迁移。
经过长期的行业实践和有关理论都已取得共识:沥青的液态迁移和特定的阳极炭块温升速率、沥青配比(或其配比的稳定性)等联系在一起. 结合本炉型结构和工艺特征:<1>、烟气在火道内的流动特性。
由于对于炉内传热,一般认为温度在600-700℃以下以对流给热为主,700-900℃则以对流给热和辐热给热二者大体相当为特征,而900℃以上以辐射给热为主。
反映到实际上不难从现场火道内可以看出:在1-2P的炉室阶段、乃至3P前期火道温度还比较低,当然在火道内烟气流动所产生的对流给热相对于炉内的辐射传热方式明显处于主导地位,其结果必然致使火道内温度差较大。
如图3所示,原设计上分别在火道内设臵了格子砖对烟气进行分流,以增大气流的雷诺准数,其目的是为避免烟气在火道内流动存在较大的滞流区,但从实际上看:①、挥发份燃烧所产生的大部分火焰或烟气基本上直接窜过火道格子砖的C格、而A格几乎没有火焰或烟气通过。
②、在低温阶段看A、B、C格所在区,上面A区耐火砖较其紧接的下面B区特别是C区耐火砖明显要暗。
〈2〉、填充焦、阳极的导热率和温度的特性。
众所周知:填充焦、阳极的导热率两者都是随其温度的升高而增强,这样在低温阶段因为上述原因就使得料箱“OX”方向上的温度梯度难免较大。
实际定量情况如表6所示:表-6 ”OX”方向上a-b两点温差情况表备注:(1)a、b两点同在“OX”方向上并ab=8cm,(2)、测温元件为K-型热电偶且测深H=120cm, (3)、表中“2P-6”表示测量时间为阳极在2P阶段移炉后的6小时。
从以上〈1〉、〈2〉点可以综合分析液态沥青的迁移:由于“OX”和“OY”方向上同时在较大的温度梯度,这样当炭块外部及下部开始焦化并形成孔隙时,正好迎合了内部、上部沥青正以最低粘度的迁移并被填充,且由于表层块的上部因温度低、温升速率慢而致使沥青液态迁移持续时间长、迁移程度加剧。
其结果必然致使炭块在液态迁移后存在着较大的密度梯度并正比于其温度梯度。
而在后面的冷却过程中,密度大的必然收缩小,密度小的收缩相反大。
当这种收缩不一致性一旦超过当时炭块的抗拉强度时,必然产生上述有规则的孔间裂纹。
3、覆盖料的厚度。
为考察表层块的孔间裂纹是否存在很强的联系,进一步对451块表块的覆盖料进行测量,并对其出炉炭块跟踪检查。
结果如表所示:表-7 覆盖料跟踪调查结果表(块)从以上结果可以看出:虽然随着覆盖料厚度的增加其完好率有所提高,但覆盖料厚度在700mm以上的表层块仍然存在一定数量的裂2孔以下的裂纹。
从结果分析原因:a、覆盖料的厚度对表层块具有保温作用并有利于减小制品上下温差b、覆盖料越厚也意味着表层块装炉位臵越深(即越更多地处于C区域)。
这样a、b两点综合作用实际上使表层块上部的沥青液态迁移在一定程度上得以改善。
故孔间裂纹现象得以如上结果的控制,但难以从根本上消除。
4、可探索性的建议。
可在局部范围内尝试通过对格子砖合理改进以改善烟气的流动,在收效明显的基础上利用修理火道之机逐步推广应用。
同时也使表层块“发黑”(即电阻率相对较高)得以改善乃至消除成为一种可能,这是因为从实际上看:要想在火道墙可承受的条件下通过提高焙烧终温来改善表层块颜色或电阻率问题,事实上难以奏效并将会碰到因目前系统配臵下的鼓风供氧能力不足而在操作上带来“煤气过剩”的问题。
五、长包、底缺、掉棱角、变形、氧化等。
1、长包、底缺及变形都和铺料作业、料箱形变、填充料颗粒及水份紧密地联系在一起。
2、掉棱角一般都是铺料不实或不到头直接造成的。
但实际生产中常常出现类似图4的情况:其特征 A、棱角掉的尺寸大。
B、所掉部份的上面伴随水平裂纹且裂纹都呈较宽特征。
这时候不排除生块的内部裂纹在焙烧过程中扩大化的体现。
3、氧化。
一种情况是由于填充料在焙烧过程中的收缩下陷或漏料而使阳极炭块和炉室上面的空气接触产生氧化,这种情形多发生在升温过程中的表层块;另一种情况则是由于火道墙的变形致使阳极炭块和从后面鼓过来的空气接触产生氧化,此类情况常体现在冷却过程中的中层块。
参考资料:1、炭素厂97-98年《原料质量信息》。