气相沉积简介
CVD简介

CVD(Chemical Vapor Deposition)原理CVD(Chemical Vapor Deposition)化学气相沉积,指把含有构成薄膜元素的气态反应剂或液态反应剂的蒸气及反应所需其它气体引入反应室,在衬底表面发生化学反应生成薄膜的过程。
CVD特点淀积温度低,薄膜成份易控,膜厚与淀积时间成正比,均匀性,重复性好,台阶覆盖性优良。
CVD制备的必要条件1) 在沉积温度下,反应物具有足够的蒸气压,并能以适当的速度被引入反应室;2) 反应产物除了形成固态薄膜物质外,都必须是挥发性的;3) 沉积薄膜和基体材料必须具有足够低的蒸气压。
CVD是Chemical Vapor Deposition的简称,是指高温下的气相反应,例如,金属卤化物、有机金属、碳氢化合物等的热分解,氢还原或使它的混合气体在高温下发生化学反应以析出金属、氧化物、碳化物等无机材料的方法。
这种技术最初是作为涂层的手段而开发的,但目前,不只应用于耐热物质的涂层,而且应用于高纯度金属的精制、粉末合成、半导体薄膜等,是一个颇具特征的技术领域。
其技术特征在于:(1)高熔点物质能够在低温下合成;(2)析出物质的形态在单晶、多晶、晶须、粉末、薄膜等多种;(3)不仅可以在基片上进行涂层,而且可以在粉体表面涂层,等。
特别是在低温下可以合成高熔点物质,在节能方面做出了贡献,作为一种新技术是大有前途的。
例如,在1000℃左右可以合成a-Al2O3、SiC,而且正向更低温度发展。
CVD工艺大体分为二种:一种是使金属卤化物与含碳、氮、硼等的化合物进行气相反应;另一种是使加热基体表面的原料气体发生热分解。
CVD的装置由气化部分、载气精练部分、反应部分和排除气体处理部分所构成。
目前,正在开发批量生产的新装置。
CVD是在含有原料气体、通过反应产生的副生气体、载气等多成分系气相中进行的,因而,当被覆涂层时,在加热基体与流体的边界上形成扩散层,该层的存在,对于涂层的致密度有很大影响。
化学气相沉积
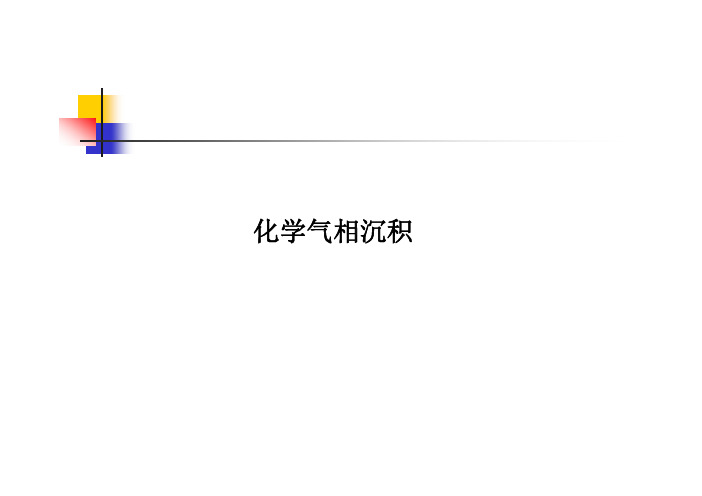
历史的简短回顾
→古人类取暖或烧烤时熏在岩洞壁或岩石上的黑色碳层 →中国古代炼丹术中的“升炼”(最早的记载) →20世纪50年代,现代CVD技术用于刀具涂层(碳化钨 为基材经CVD氧化铝、碳化钛、氮化钛) →20世纪60、70年代,半导体和集成电路技术、超纯多 晶硅。 →1990年以来我国王季陶,提出激活低压CVD金刚石生 长热力学耦合模型。第一次真正从理论和实验对比上定 量化地证实反自发方向的反应可以通过热力学反应耦合 依靠另一个自发反应提供的能量推动来完成。
化学气相沉积的反应类型 简单热分解和热分解反应沉积
通常ⅢA,ⅣA,ⅤA族的一些低周期元素的氢化物如CH4、 SiH4、GeH4、B2H6、PH3、AsH3等都是气态化合物,而且加 热后易分解出相应的元素。因此很适合用于CVD技术中作 为原料气。其中CH4,SiH4分解后直接沉积出固态的薄 膜,GeH4也可以混合在SiH4中,热分解后直接得Si—Ge 合金膜。例如:
简单热分解和热分解反应沉积
通常金属化合物往往是一些无机盐类.挥发性很低,很 难作为CVD技术的原料气;而有机烷基金属则通常是气体 或易挥发的物质,因此制备金属或金属化合物薄膜时, 常常采用这些有机烷基金属为原料,应地形成了一类金 属有机化学气相沉积(Metal—Organic Chemical Vapor Deposition简称为MOCVD)技术。 其它一些含金属的有机化合物,例如三异丙醇铝 [Al(OC3H7)3] 以及一些β—丙酮酸(或β—二酮)的金属配 合初等不包含C—M键(碳一金属键).并不真正属于金属 有机化合物,而是金属的有机配合物或含金属的有机化 合物。这些化合物也常常具有较大的挥发性,采用这些 原料的CVD技术,有时也被包含在MOCVD技术之中。
CVD的沉积反应室内部结构及工作原理变化最大,常常根 据不同的反应类型和不同的沉积物要求来专门设计。但 大体上还是可以把不同的沉积反应装置粗分为以下一些 类型。
化学气相沉积法
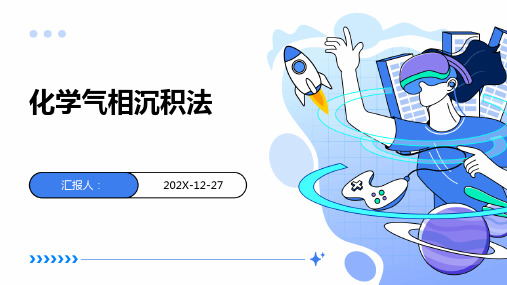
时间与速率
要点一
总结词
时间和沉积速率在化学气相沉积过程中具有重要影响,它 们决定了薄膜的厚度和均匀性。
要点二
详细描述
时间和沉积速率决定了化学气相沉积过程中气体分子在反 应器中的停留时间和沉积时间。较长的停留时间和较慢的 沉积速率有利于气体分子充分反应和形成高质量的薄膜。 然而,过长的停留时间和过慢的沉积速率可能导致副反应 或降低沉积速率。因此,选择合适的时间和沉积速率是实 现均匀、高质量薄膜的关键。
05
化学气相沉积法优 缺点
优点
适用性广
涂层性能优良
化学气相沉积法适用于各种材料表面改性 和涂层制备,如金属、陶瓷、玻璃等。
通过控制化学气相沉积的条件,可以制备 出具有高硬度、高耐磨性、高抗氧化性的 涂层。
环保
高效
化学气相沉积法使用的原料在高温下分解 ,不会对环境造成污染。
化学气相沉积法具有较高的沉积速率,可 实现快速涂层制备。
应用领域
半导体产业
用于制造集成电路、微 电子器件和光电子器件
等。
陶瓷工业
制备高性能陶瓷材料, 如氧化铝、氮化硅等。
金属表面处理
在金属表面形成耐磨、 防腐、装饰等功能的涂
层。
其他领域
在航空航天、能源、环 保等领域也有广泛应用
。
02
化学气相沉积法分 类
热化学气相沉积法
原理
在较高的温度下,使气态的化 学反应剂与固态表面接触,通 过气相反应生成固态沉积物。
缺点
高温要求
化学气相沉积法需要在高温下进行,这可能会对 基材产生热损伤或变形。
操作难度大
化学气相沉积法需要精确控制反应条件,操作难 度较大。
ABCD
设备成本高
化学气相沉积简介

• CVD Process Overview • PECVD Process Overview • PECVD Process Recipe And Clean Recipe Overview • PECVD Equipment Overview
CVD Process Overview
CVD Process Overview
PECVD中plasma的特点:
➢ Plasma组分:包括电子、离子、未电离的中性粒子,电离度小于0.01;属 于低温plasma(非平衡态的等离子体),电子温度(104K)>>粒子体温度 (300~500K);
➢ Plasma中的碰撞(collision)过程: 1)弹性碰撞(elastic collision):没有能量交换的碰撞,它是plasma 中最频繁发生的,但也是没有重要意义的碰撞; 2)非弹性碰撞(inelastic collision):发生能量交换的,有新的成分 产生的碰撞,其中三个比较重要: ➢ 离子化(Ionization) e-+A(atom\molecule)->A++2e➢ 激发与跃迁(excitation-relaxation) e-+A(atom\molecule)->A*+eA*->A+hv(photons) ➢ 离解(dissociation) e-+AB->A+B+e-
稳定性; 缺点:设备比较复杂,需要TEOS传输系统;厚膜下容易发生discolor;
wafer整体range较大;
P1E)CVDOxPirdoec(essPOEvesrivlieawne oxide and PE TEOS oxide
物理气相沉积技术

物理气相沉积技术1简介物理气相沉积(Physical Vapor Deposition,PVD)是一种表面处理技术,它基于原子、分子或离子在真空条件下从固体源“蒸发”或“剥离”,并在另外一个表面生成薄膜或涂层的过程。
PVD技术广泛应用于半导体、电子、机械、医疗等领域,可以改善材料表面的性能、延长使用寿命,也可以改变物体的颜色和外观。
2工艺流程PVD技术是在真空下完成的,因此主要工具是真空室,其次是沉积源,对于不同的应用场景,沉积源也会有所不同。
例如,如果是进行金属沉积,则沉积源可以是纯净金属,或者是通过将金属块或箔片加热,使其蒸发或溅射而得到的。
如果需要沉积金属氧化物,则需要放置源材料和氧气在沉积室中进行反应。
在PVD过程中,首先需要将材料放入真空室中,制备必要的工艺条件,使得沉积源的物质能够蒸发、溅射并扩散到目标基板上。
其中一个关键参数是真空度,PVD通常在10^-4~10^-8torr的高真空条件下进行。
另一个参数是沉积源与基板的距离,过近会导致过度热量和膜的不均匀厚度,过远影响膜的成形。
3分类根据真空沉积源材料的不同,PVD可分为四种类型:蒸发、离子镀、磁控溅射和分子束外延。
其中,蒸发和离子镀常常被用于制备功能性和装饰性薄膜涂层,磁控溅射则常被用于制备金属、半导体和陶瓷等薄膜,而分子束外延则适用于高质量、高洁净度的材料制备。
4应用PVD技术的应用涵盖了许多领域。
其中,电子和半导体产业是其中的重要应用领域之一。
在芯片制造过程中,PVD技术用于制备镀膜、金属连线等的处理;在随着显示技术的发展,PVD技术也被广泛应用于液晶显示器、有机EL显示器、柔性显示器等各种显示器领域。
此外,在航空航天、汽车、医疗、光学等领域都有PVD技术的应用。
5结论总的来说,PVD技术是一种成熟、广泛应用的表面处理技术。
它可以对各种材料表面进行处理,使其具有功能性和装饰性,可以改善产品的表面性能。
然而,由于技术的复杂性和设备的昂贵性,PVD技术在应用过程中也存在一定的限制性。
有机金属化学气相沉积法

有机金属化学气相沉积法(MOCVD, Metal-organic Chemical Vapor Deposition),是在基板上成长半导体薄膜的一种方法。
其他类似的名称如:MOVPE (Metal-organic Vapor-Phase Epitaxy)、OMVPE (Organometallic Vapor-Phase Epitaxy)及OMCVD (Organometallic Vapor-Phase Epitaxy)等等,其中的前两个字母 "MO" 或是 "OM",指的是半导体薄膜成长过程中所采用的反应源(precusor)为金属有机物 "Metal-organic" 或是有机金属"Organometallic"。
而后面三个字母 "CVD" 或是 "VPE",指的是所成长的半导体薄膜的特性是属于非晶形薄膜或是具有晶形的薄膜。
一般而言,"CVD" 所指的是非晶形薄膜的成长,这种成长方式归类于 "沉积"(Deposition);而"VPE"所指的是具有晶形的薄膜成长方式,这种方式归类于"磊晶"(Epitaxy)。
MOCVD成长薄膜时,主要将载流气体(Carrier gas)通过有机金属反应源的容器时,将反应源的饱和蒸气带至反应腔中与其它反应气体混合,然后在被加热的基板上面发生化学反应促成薄膜的成长。
一般而言,载流气体通常是氢气,但是也有些特殊情况下采用氮气(例如:成长氮化铟镓(InGaN)薄膜时)。
常用的基板为砷化镓(GaAs)、磷化镓(GaP)、磷化铟(InP)、硅(Si)、碳化硅(SiC)及蓝宝石(Sapphire,Al2O3)等等。
而通常所成长的薄膜材料主要为三五族化合物半导体(例如:砷化镓(GaAs)、砷化镓铝(AlGaAs)、磷化铝铟镓(AlGaInP)、氮化铟镓(InGaN))或是二六族化合物半导体,这些半导体薄膜则是应用在光电元件(例如:发光二极管(LED)、雷射二极管(Laser diode)及太阳能电池)及微电子元件(例如:异质接面双载子电晶体(HBT)及假晶式高电子迁移率电晶体(PHEMT))的制作。
化学气相沉积简介

PECVD Process Overview PECVD中的反应过程:
主要过程: 电子与气体发生非弹性碰撞,使的气体发生分解 (初级反应),形成离子和活性基团混合物; 活性基团向薄膜生长表面扩散输运,同时发生各 反应物之间的次级反应; 到达生长表面的各种初级、次级反应产物被吸 并与表面发生反应,同时伴随有气相分子的再放出;
TEOS-based process
plasma&heat
Si(OC2H5)4 + O2
>
USG + other volatiles
PECVD Process Overview 1) Oxide ( PE silane oxide and PE TEOS oxide )
TEOS oxide的优点: 更好的step coverage和conformity; 比SiH4更加安全;局部更平滑的表面形貌,降低寄生电容,提高器件 稳定性; 缺点:设备比较复杂,需要TEOS传输系统;厚膜下容易发生discolor; wafer整体range较大;
CVD Process Overview PECVD中plasma的特点:
Plasma组分:包括电子、离子、未电离的中性粒子,电离度小于0.01;属 于低温plasma(非平衡态的等离子体),电子温度(104K)>>粒子体温度 (300~500K); Plasma中的碰撞(collision)过程: 1)弹性碰撞(elastic collision):没有能量交换的碰撞,它是plasma 中最频繁发生的,但也是没有重要意义的碰撞; 2)非弹性碰撞(inelastic collision):发生能量交换的,有新的成分 产生的碰撞,其中三个比较重要: 离子化(Ionization) e-+A(atom\molecule)->A++2e 激发与跃迁(excitation-relaxation) e-+A(atom\molecule)->A*+eA*->A+hv(photons) 离解(dissociation) e-+AB->A+B+e-
PVD(物理气相沉积)简介

书山有路勤为径,学海无涯苦作舟
PVD(物理气相沉积)简介
1. PVD 简介PVD 是英文Physical Vapor Deposition(物理气相沉积)的缩写,是指在真空条件下,采用低电压、大电流的电弧放电技术,利用气体放
电使靶材蒸发并使被蒸发物质与气体都发生电离,利用电场的加速作用,使被
蒸发物质及其反应产物沉积在工件上。
2. PVD 技术的发展PVD 技术出现于二十世纪七十年代末,制备的薄膜具
有高硬度、低摩擦系数、很好的耐磨性和化学稳定性等优点。
最初在高速钢刀
具领域的成功应用引起了世界各国制造业的高度重视,人们在开发高性能、高
可靠性涂层设备的同时,也在硬质合金、陶瓷类刀具中进行了更加深入的涂层
应用研究。
与CVD 工艺相比,PVD 工艺处理温度低,在600℃以下时对刀具材料的抗弯强度无影响;薄膜内部应力状态为压应力,更适于对硬质合金精密复
杂刀具的涂层;PVD 工艺对环境无不利影响,符合现代绿色制造的发展方向。
目前PVD 涂层技术已普遍应用于硬质合金立铣刀、钻头、阶梯钻、油孔钻、铰刀、丝锥、可转位铣刀片、异形刀具、焊接刀具等的涂层处理。
PVD 技术不仅提高了薄膜与刀具基体材料的结合强度,涂层成分也由第
一代的TiN 发展为TiC、TiCN、ZrN、CrN、MoS2、TiAlN、TiAlCN、TiN- AlN、CNx、DLC 和ta-C 等多元复合涂层。
3. 星弧涂层的PVD 技术增强型磁控阴极弧:阴极弧技术是在真空条件下,通过低电压和高电流将靶材离化成离子状态,从而完成薄膜材料的沉积。
增强型磁控阴极弧利用电磁场的共同作用,将靶材表面的电弧加以有效地控
制,使材料的离化率更高,薄膜性能更加优异。
- 1、下载文档前请自行甄别文档内容的完整性,平台不提供额外的编辑、内容补充、找答案等附加服务。
- 2、"仅部分预览"的文档,不可在线预览部分如存在完整性等问题,可反馈申请退款(可完整预览的文档不适用该条件!)。
- 3、如文档侵犯您的权益,请联系客服反馈,我们会尽快为您处理(人工客服工作时间:9:00-18:30)。
气相沉积简介CVD(Chemical Vapor Deposition,化学气相沉积),指把含有构成薄膜元素的气态反应剂或液态反应剂的蒸气及反应所需其它气体引入反应室,在衬底表面发生化学反应生成薄膜的过程。
在超大规模集成电路中很多薄膜都是采用CVD方法制备。
经过CVD处理后,表面处理膜密着性约提高30%,防止高强力钢的弯曲,拉伸等成形时产生的刮痕。
特点沉积温度低,薄膜成份易控,膜厚与淀积时间成正比,均匀性,重复性好,台阶覆盖性优良。
制备的必要条件1)在沉积温度下,反应物具有足够的蒸气压,并能以适当的速度被引入反应室;2)反应产物除了形成固态薄膜物质外,都必须是挥发性的;3)沉积薄膜和基体材料必须具有足够低的蒸气压。
PVD是英文Physical Vapor Deposition(物理气相沉积)的缩写,是指在真空条件下,采用低电压、大电流的电弧放电技术,利用气体放电使靶材蒸发并使被蒸发物质与气体都发生电离,利用电场的加速作用,使被蒸发物质及其反应产物沉积在工件上。
涂层技术增强型磁控阴极弧:阴极弧技术是在真空条件下,通过低电压和高电流将靶材离化成离子状态,从而完成薄膜材料的沉积。
增强型磁控阴极弧利用电磁场的共同作用,将靶材表面的电弧加以有效地控制,使材料的离化率更高,薄膜性能更加优异。
过滤阴极弧:过滤阴极电弧(FCA )配有高效的电磁过滤系统,可将离子源产生的等离子体中的宏观粒子、离子团过滤干净,经过磁过滤后沉积粒子的离化率为100%,并且可以过滤掉大颗粒,因此制备的薄膜非常致密和平整光滑,具有抗腐蚀性能好,与机体的结合力很强。
磁控溅射:在真空环境下,通过电压和磁场的共同作用,以被离化的惰性气体离子对靶材进行轰击,致使靶材以离子、原子或分子的形式被弹出并沉积在基件上形成薄膜。
根据使用的电离电源的不同,导体和非导体材料均可作为靶材被溅射。
离子束DLC:碳氢气体在离子源中被离化成等离子体,在电磁场的共同作用下,离子源释放出碳离子。
离子束能量通过调整加在等离子体上的电压来控制。
碳氢离子束被引到基片上,沉积速度与离子电流密度成正比。
星弧涂层的离子束源采用高电压,因而离子能量更大,使得薄膜与基片结合力很好;离子电流更大,使得DLC膜的沉积速度更快。
离子束技术的主要优点在于可沉积超薄及多层结构,工艺控制精度可达几个埃,并可将工艺过程中的颗料污染所带来的缺陷降至最小。
金刚石电极金刚石电极是一种新型的电极,在电化学传感器,电催化中具有良好的应用前景。
他利用掺硼金刚石(boron-doped diamond BDD)薄膜作为电极材料,而掺硼金刚石薄膜特殊的sp3键结构及其具有的导电性,赋予了金刚石薄膜电极优异的电化学特性,如宽的电化学势窗、较低的背景电流、较好的物理化学稳定性以及低吸附特性等。
1.宽电化学势窗电极的析氧电位与析氢电位的电势差值,称为电极的电势窗口(Potential Window)。
电化学电位窗口是衡量一个电极材料的电催化能力的重要指标,电化学窗口越大,特别是阳极析氧过电位越高,对于在高电位下发生的氧化反应和合成具有强氧化性的中间体更有利。
另外,对于电分析性能来说,因为电极上发生氧化还原反应的同时,还存在着水电解析出氧气和氢气的竞争反应,若被研究物质的氧化电位小于电极的析氧电位或还原电位大于电极的析氢电位,在电极达到析氧或者析氢电位前,被研究物质在阳极上得以电催化氧化或者还原,可以较好的分析氧化或还原过程。
但若氧化或还原过程在电极的电势窗口以外发生,被研究物质得到的信息会受到析氢或析氧的影响,得不到最佳的研究条件甚至根本无法进行研究。
掺硼金刚石薄膜较宽的电势窗口,特别是较高的析氧电位,可以使得研究较高电位下的氧化还原反应成为可能,如可以通过分析氧化电位来进行有机物质的电分析,研究者已经成功将高析氧电位的特点应用于电分析,如茶碱,生物胺等,而用常规玻璃碳,碳纤维电极,由于高氧化电位的限制,其检测精度非常低甚至无法进行检测。
此外,由于金刚石薄膜电极较高的析氧电位,可较高效率的产生强氧化性物质如羟基自由基,羟基自由基具有非常高的活性,能对有机物进行有效“催化焚烧”。
下表列出了常用电极的析氧电位,可以看出BDD电极具有最高的析氧过电位。
2.低背景电流背景电流与电极表面形成电子双电层的电容量有关,金刚石材料电极表面的双电层为几个μF/cm2,与GC等电极相比要小2个数量级。
关于金刚石电极材料背景电流小的原因有以下几种可能:由于掺杂水平的影响,在费米能级附近具有较小的电子密度,因而对于双电层充放电的贡献较小;金刚石在生长过程中产生不同的生长取向,电极的表面由一系列“微电极”组成,这些分散的原子大小的“微电极”使得整体双电层变小;金刚石表面是sp3结构的碳元素,表面C-O功能团的贡献对双电层电容很小,没有类似于其它碳电极的法拉第电容。
利用金刚石电极的极低背景电流这一特性分析检测氧化还原反应,可得到大大高于其它常规电极的信噪比(S/N),此外,背景电流越小则对分析检测的干扰越小,有利于检出限的进一步降低。
3.高化学稳定性金刚石电极与传统碳电极相比具有很高的稳定性,金刚石为稳定的sp3 结构,通过对电极制作条件的控制,可以在非常低的sp2浓度下沉积得到金刚石薄膜,这将导致在电极有非常高的电化学稳定性。
Comninellis和他的研究组报导了使用电流密度为30mA cm-2的条件下对BDD电极进行极化,在硫酸溶液中氧化异丙醇长达400小时之久,在电极上没有发现侵蚀或失去活性的迹象。
在氢氟酸溶液中长时间的电解,金刚石的表面形貌和电化学等特性保持基本不变,O(1s)/C(1s)率只有稍微改变,电极具有很高的重现性。
4.低吸附特性金刚石对很多化学物种具有吸附惰性,这是金刚石电极又一优异性能。
常规玻碳电极由于其自身的特性,在伏安实验中电极表面经常会发生电极“中毒”污染现象,所以为了保持电极的性能须经常对电极表面进行预处理。
Swain和他的研究小组分别研究了在预处理的碳电极、高定向热解石墨电极(HOPG)和金刚石电极表面上苯醌的吸附现象,发现金刚石对苯醌的吸附性能最低。
在一些情况下,虽然检测或氧化过程不需要非常高的电位,但可能会因为在如铂等的贵金属电极的表面覆盖了一层氧化膜而对分析或氧化产生干扰。
对于排除这种干扰,使用金刚石作为分析电极也是一种较好的选择。
金刚石对于有些物质如苯酚在低电位下可能发生钝化现象,但通过提高电位的方法可以很简便的消除钝化,使电极到达最初的状态。
此外,金刚石对于羟基自由基是一种物理吸附,不与电极表面发生化学反应,因此极化过程中产生的自由基能够更高效率的催化氧化降解有机物,而较少的发生析氧副反应。
电化学势窗电极的析氧电位与析氢电位的电势差值,称为电极的电势窗口(Potential Window)。
电化学电位窗口是衡量一个电极材料的电催化能力的重要指标,电化学窗口越大,特别是阳极析氧过电位越高,对于在高电位下发生的氧化反应和合成具有强氧化性的中间体更有利。
另外,对于电分析性能来说,因为电极上发生氧化还原反应的同时,还存在着水电解析出氧气和氢气的竞争反应,若被研究物质的氧化电位小于电极的析氧电位或还原电位大于电极的析氢电位,在电极达到析氧或者析氢电位前,被研究物质在阳极上得以电催化氧化或者还原,可以较好的分析氧化或还原过程。
但若氧化或还原过程在电极的电势窗口以外发生,被研究物质得到的信息会受到析氢或析氧的影响,得不到最佳的研究条件甚至根本无法进行研究。
类金刚石薄膜的微观结构与其物理特性碳有 2 种结晶态, 即石墨和金刚石。
这2种晶态表现出 2 种不同的物理特性。
石墨结晶结构是在室温条件下热力学中优先生成的结晶结构。
它是一种层状结构, 其 C 原子紧密以共价键连接在一个平面(称为SP2 混合键) 内, 层与层之间的连接很弱。
在金刚石中, 一个C原子被另外 3 个C原子所围绕并形成共价键(称为SP3 混合键) , 表现出硬度高的特性(但其晶体需要在高温、高压条件下才能形成) 。
因此, 在温度不太高的条件(100 ℃~300 ℃) 下, 碳离子在基片上形成一种无定形碳膜, 其结构含有石墨结构成分(SP2 结构) 和金刚石结构成分(SP3 结构) ,而SP2 和SP3 含量的多少, 决定其宏观的物理特性。
因此, SP2 和SP3 含量的测试是保证类金刚石薄膜质量的关键。
Raman 光谱分析法是测试类金刚石薄膜化学结构的主要方法。
美国学者R. E. Shroder 建立了一个SP2 和SP3 成分相对比率喇曼光谱定标曲线。
分别用氮化硼(BN) 和金刚石粉末以及用石墨与金刚石粉末 2 种混合物, 在严格确定混合粉末成分比例条件下, 得到了几组喇曼光谱图。
随着石墨与金刚石粉末含量的变化, 喇曼光谱在1355cm 处的D 峰和1580cm 处的G峰有着明显的变化, 其中D峰代表SP3 成分的含量(即金刚石结构的含量) , G峰代表SP2 成分的含量。
由于类金刚石薄膜是一种无定形态的碳膜, 其SP2 键与SP3 键的杂化轨道表现在喇曼光谱在1100cm~1700cm 范围内有较宽的展宽。
因此, 用上述方法严格定量分析是困难的。
有些学者提出, 用喇曼光谱中G峰向 D 峰方向的位移量计算SP2 与SP3 含量的相对比率。
泵机械泵是指利用机械方法对被抽容器进行抽气而获得真空的设备,也被称为机械真空泵。
机械泵由电机和泵体两大部分组成。
普通型机械泵由电机通过皮带带动泵轴旋转;直连型机械泵是电机直接与泵轴连接,无中间传动环节。
机械泵是利用气体膨胀、压缩、排出的原理,把气体从容器里抽出的。
之所以称之为机械泵,是因为它是利用机械的方法,周期性地改变泵内吸气腔的容积,使容器中的气体不断地通过泵的进气口膨胀到吸气腔中,然后通过压缩经排气口排出泵外。
改变泵内吸气腔容积的方式有活塞往复式、定片式和旋片式,分别称为往复式机械泵、定片式机械泵和旋片式机械泵。
由于实际应用中,旋片式机械泵使用较多,现以旋片式机械泵为例说明其工作原理。
单级旋片式真空泵,它所能达到的极限压强为1Pa。
为提高极限压强,通常采用双级泵结构,即将两个单级泵串联起来,可使极限压强达到十的负二次方Pa数量级。
分子泵是利用高速旋转的转子把动量传输给气体分子,使之获得定向速度,从而被压缩、被驱向排气口后为前级抽走的一种真空泵。
复合式分子泵是涡轮分子泵与牵引分子泵的串联组合,集两种泵的优点于一体。
泵在很宽的压力范围内((10-6~1Pa)具有较大的抽速和较高的压缩比,大大提高了泵的出口压力。
污水指标在实际工作中一般采用生物化学需氧量(BOD)、化学需氧量(COD、OC)、总有机碳(TOC)、总需氧量(TOD)等指标来反映水中需氧有机物的含量。