大豆油精炼设备详细工艺流程
大豆油加工工艺流程
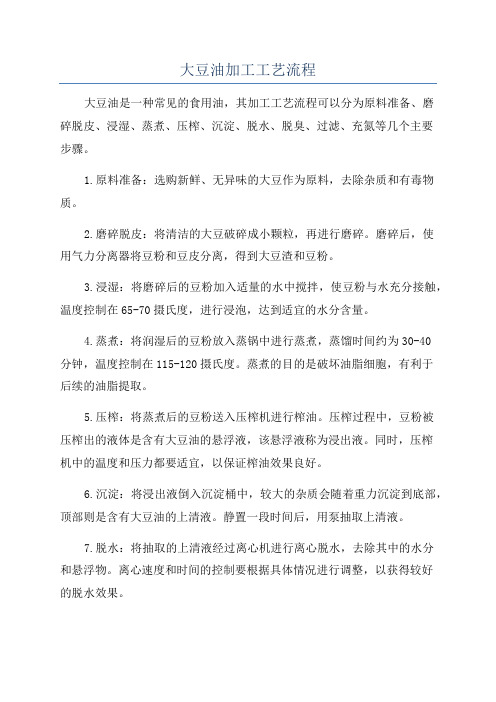
大豆油加工工艺流程大豆油是一种常见的食用油,其加工工艺流程可以分为原料准备、磨碎脱皮、浸湿、蒸煮、压榨、沉淀、脱水、脱臭、过滤、充氮等几个主要步骤。
1.原料准备:选购新鲜、无异味的大豆作为原料,去除杂质和有毒物质。
2.磨碎脱皮:将清洁的大豆破碎成小颗粒,再进行磨碎。
磨碎后,使用气力分离器将豆粉和豆皮分离,得到大豆渣和豆粉。
3.浸湿:将磨碎后的豆粉加入适量的水中搅拌,使豆粉与水充分接触,温度控制在65-70摄氏度,进行浸泡,达到适宜的水分含量。
4.蒸煮:将润湿后的豆粉放入蒸锅中进行蒸煮,蒸馏时间约为30-40分钟,温度控制在115-120摄氏度。
蒸煮的目的是破坏油脂细胞,有利于后续的油脂提取。
5.压榨:将蒸煮后的豆粉送入压榨机进行榨油。
压榨过程中,豆粉被压榨出的液体是含有大豆油的悬浮液,该悬浮液称为浸出液。
同时,压榨机中的温度和压力都要适宜,以保证榨油效果良好。
6.沉淀:将浸出液倒入沉淀桶中,较大的杂质会随着重力沉淀到底部,顶部则是含有大豆油的上清液。
静置一段时间后,用泵抽取上清液。
7.脱水:将抽取的上清液经过离心机进行离心脱水,去除其中的水分和悬浮物。
离心速度和时间的控制要根据具体情况进行调整,以获得较好的脱水效果。
8.脱臭:将脱水后的油脂转入脱臭锅中进行脱臭处理。
脱臭的目的是去除油脂中的异味和杂质,提高油的质量。
通常采用蒸汽加热和真空抽吸的方法进行脱臭。
9.过滤:经过脱臭处理的油脂需要经过过滤,以去除残留的悬浮物和杂质。
常用的过滤设备有滤布式和板框式过滤机,通过滤布或滤板来进行过滤。
10.充氮:最后,将过滤后的大豆油暴露在气体中进行充氮处理,以提高大豆油的质量和保鲜性。
以上是大豆油的加工工艺流程,通过以上步骤,大豆油可以得到较好的产量和品质。
在实际生产中,还可以根据不同的要求和技术条件进行调整和改进,以提高生产效率和产品质量。
大豆油精炼加工工艺
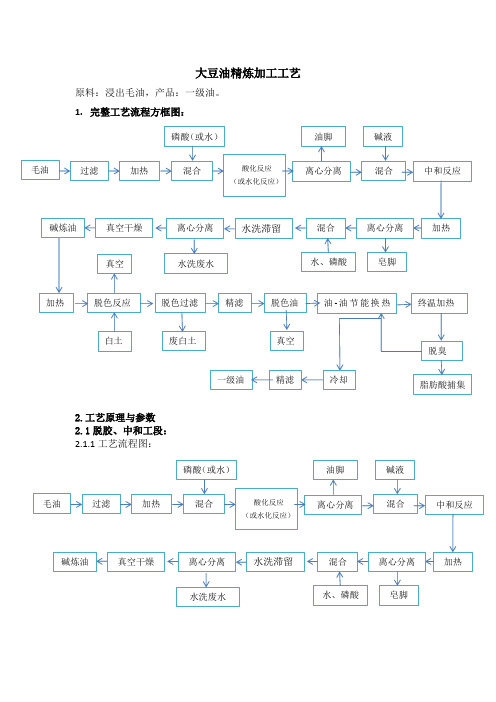
大豆油精炼加工工艺原料:浸出毛油,产品:一级油。
1. 完整工艺流程方框图:2.工艺原理与参数2.1脱胶、中和工段:2.1.1工艺流程图:油脚 碱液 磷酸(或水) 毛油 过滤 混合 加热 离心分离 酸化反应 (或水化反应) 混合 中和反应 加热离心分离 混合 水洗滞留 离心分离 真空干燥碱炼油 皂脚水洗废水 水、磷酸 油脚 碱液 磷酸(或水) 毛油 过滤混合 加热 离心分离 酸化反应 (或水化反应) 混合 中和反应加热 离心分离 混合 水洗滞留 离心分离 真空干燥 碱炼油 皂脚 水洗废水 水、磷酸 真空白土 加热 脱色反应 脱色过滤 精滤 脱色油 废白土 真空 油-油节能换热终温加热 脱臭 脂肪酸捕集冷却 精滤 一级油2.1.2工艺设备及原理大豆毛油经过滤、除杂后由泵送入生产线,经加热器加热至一定温度后进入混合器。
在混和器中,毛油与一定比例的磷酸溶液(或水)充分混合,随后进入延时罐进一步调质,油中的非水化磷脂转化为水化磷脂,然后进入脱胶离心机中进行分离,分离出油脚进入暂存罐中暂存。
酸化后的油(或脱胶油)进入混和器,与一定比例的碱液混合,使游离脂肪酸与碱发生中和反应生成钠皂,再进入延时反应罐充分反应,随后经泵送至加热器加热至一定温度,然后进入脱皂离心机中进行油皂分离,分离出皂脚进入皂脚罐中暂存。
脱皂后的油进入混和器中与一定比例的热水混合,同时添加少量的磷酸溶液(或柠檬酸水溶液),用于鳌和金属离子,利于去除残皂等杂质。
随后进入延时反应罐充分反应,再进入水洗离心机进行水洗分离,以去除残留皂脚等杂质。
水洗后的油最后进入真空干燥器中去除水分及其它挥发性物质,由泵输送至脱色工段。
2.1.3工艺参数●酸法脱胶工艺:100%磷酸(浓度75~85%)加入油量0.05~0.2 %100%柠檬酸(浓度~50%)加入油量0.05~0.2 %酸脱胶不仅对除去非水化磷脂,降低金属离子含量有利,而且对碱炼水洗除去油脂中含皂含量也有很大的益处。
大豆精炼流程及主要设备

大豆精炼流程及主要设备大豆精炼是将原始大豆中的油脂提取出来,并经过一系列的加工工艺,去除杂质、脱臭、脱酸、脱色等步骤,得到高纯度的大豆油的过程。
下面将详细描述大豆精炼的流程及主要设备。
1. 大豆精炼流程大豆精炼一般包括以下主要步骤:清洁、破碎、软化、脱皮、脱脂、脱水、脱溶剂、脱酸、脱臭、脱色、脱蜡、过滤、包装等。
1.1 清洁将原始大豆进行清洁,去除杂质、石头等。
常用的清洁设备有石磨清洁机、磁力清洁机、筛选机等。
1.2 破碎将清洁后的大豆进行破碎,使其体积变小,便于后续的加工。
常用的破碎设备有破碎机、碎米机等。
1.3 软化将破碎后的大豆进行软化处理,使其更易于脱皮和脱脂。
常用的软化设备有软化锅、软化罐等。
1.4 脱皮将软化后的大豆进行脱皮处理,去除大豆外层的皮。
常用的脱皮设备有脱皮机、脱皮筛等。
1.5 脱脂将脱皮后的大豆进行脱脂处理,将油脂从大豆中提取出来。
常用的脱脂设备有脱脂机、离心机等。
1.6 脱水将脱脂后的大豆进行脱水处理,去除其中的水分。
常用的脱水设备有脱水机、离心机等。
1.7 脱溶剂如果是采用有机溶剂提取油脂的方法,需要进行脱溶剂处理,将溶剂从油脂中蒸发出去。
常用的脱溶剂设备有脱溶剂器、蒸发器等。
1.8 脱酸将脱溶剂后的油脂进行脱酸处理,去除其中的酸。
常用的脱酸设备有脱酸器、碱炼器等。
1.9 脱臭将脱酸后的油脂进行脱臭处理,去除其中的异味。
常用的脱臭设备有脱臭锅、脱臭塔等。
1.10 脱色将脱臭后的油脂进行脱色处理,去除其中的色素。
常用的脱色设备有脱色罐、脱色塔等。
1.11 脱蜡将脱色后的油脂进行脱蜡处理,去除其中的蜡质。
常用的脱蜡设备有脱蜡器、脱蜡罐等。
1.12 过滤将经过脱蜡后的油脂进行过滤,去除其中的杂质。
常用的过滤设备有过滤机、过滤器等。
1.13 包装将过滤后的大豆油进行包装,以便储存和销售。
常用的包装设备有灌装机、封口机等。
2. 主要设备大豆精炼过程中涉及到的主要设备有清洁设备、破碎设备、软化设备、脱皮设备、脱脂设备、脱水设备、脱溶剂设备、脱酸设备、脱臭设备、脱色设备、脱蜡设备、过滤设备和包装设备等。
大豆油精炼设备工艺及要点
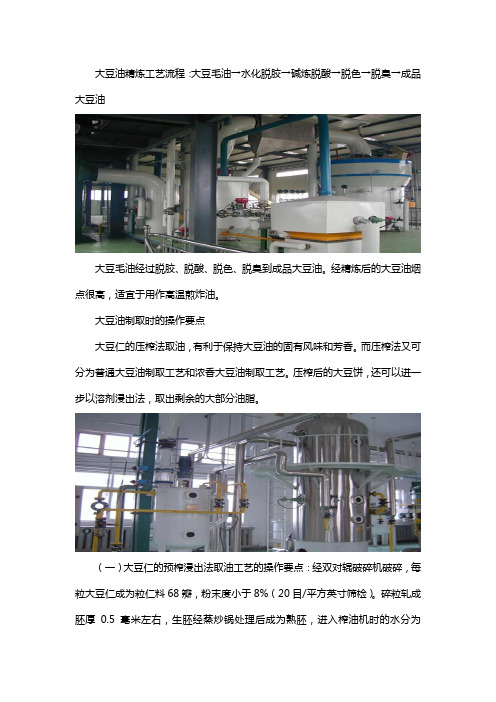
大豆油精炼工艺流程:大豆毛油→水化脱胶→碱炼脱酸→脱色→脱臭→成品大豆油大豆毛油经过脱胶、脱酸、脱色、脱臭到成品大豆油。
经精炼后的大豆油烟点很高,适宜于用作高温煎炸油。
大豆油制取时的操作要点大豆仁的压榨法取油,有利于保持大豆油的固有风味和芳香。
而压榨法又可分为普通大豆油制取工艺和浓香大豆油制取工艺。
压榨后的大豆饼,还可以进一步以溶剂浸出法,取出剩余的大部分油脂。
(一)大豆仁的预榨浸出法取油工艺的操作要点:经双对辊破碎机破碎,每粒大豆仁成为粒仁料68瓣,粉末度小于8%(20目/平方英寸筛检)。
碎粒轧成胚厚0.5毫米左右,生胚经蒸炒锅处理后成为熟胚,进入榨油机时的水分为1%2%,温度为130度上下。
如果压榨时饼不承力,并榨不成硬饼,可在熟胚中掺入少量大豆壳,以促进成饼。
压榨后的大豆饼,可以进一步进行溶剂浸出,每100千克干饼可浸出56千克的大豆油。
(二)浓香大豆油的制取工艺的操作要点:用一次压榨法生产浓香大豆油,要求用优质的新收获大豆果剥仁,除去杂质要干净彻底,浓香大豆油通常不进行精炼加工,而是经除去固体杂质后直接作为食用油。
如果获得的浓香大豆油品质差,则应进行精炼,但此时成品油的香味将大为降低。
大豆油的精炼工艺对于优质大豆仁取得的压榨大豆油,应尽量减少精炼的加工工序,以保留大豆油的天然风味。
而大豆饼经溶剂浸出所得的大豆毛油,则应进行全面精炼。
将浸出大豆毛油精炼成普通大豆油的工艺,与普通大豆油的工艺相同。
浓香大豆油加工如上所述,只需将压滤毛油沉降和冷过滤即可。
大豆油是制备食用油脂精深加工产品的良好原料。
经精炼后的大豆油烟点很高(为229.4℃),适宜于用作高温煎炸油。
毛油精炼工艺流程:过滤毛油–一次降温–加助滤剂–二次降温–沉淀48h–过滤–成品油–滤饼。
在毛油精炼工艺流程中,毛油一次降温时,由于从机榨车间送来的过滤毛油温度一般在60℃~70℃,为了节约能源,先用自来水于低速搅拌下(30rpm)散热冷却,温度降至接近室温为止。
大豆油生产工艺流程
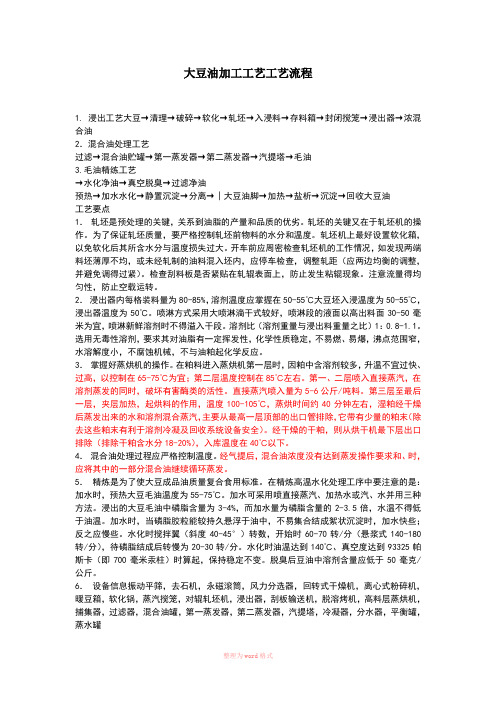
烘干机:参考价格65万元;
清洗机:参考价格65万元;破碎机:参考价格11万元;脱壳机:参考价格554万元;
调质机:参考价格11万元;压片机:参考价格32万元;浸出设备:参考价格50万元;
脱胶设备:参考价格11万元;输送设备:参考价格15万元; 厂房投资 产品描述 产品特征
1.色泽一般呈黄色或棕色;折光指数(20℃)1.4720-1.4770;比重(20℃/4℃)0.9210-0.9250。
2.卫生标准
油中的溶剂含量不得超过50毫克/公斤。
2. 浸出器内每格装料量为80-85%,溶剂温度应掌握在50-55℃大豆坯入浸温度为50-55℃,浸出器温度为50℃。喷淋方式采用大喷淋滴干式较好,喷淋段的液面以高出料面30-50毫米为宜,喷淋新鲜溶剂时不得溢入干段。溶剂比(溶剂重量与浸出料重量之比)1:0.8-1.1。选用无毒性溶剂,要求其对油脂有一定挥发性,化学性质稳定,不易燃、易爆,沸点范围窄,水溶解度小,不腐蚀机械,不与油粕起化学反应。
1. 轧坯是预处理的关键,关系到油脂的产量和品质的优劣。轧坯的关键又在于轧坯机的操作。为了保证轧坯质量,要严格控制轧坯前物料的水分和温度。轧坯机上最好设置软化箱,以免软化后其所含水分与温度损失过大。开车前应周密检查轧坯机的工作情况,如发现两端料坯薄厚不均,或未经轧制的油料混入坯内,应停车检查,调整轧距(应两边均衡的调整,并避免调得过紧)。检查刮料板是否紧贴在轧辊表面上,防止发生粘辊现象。注意流量得均匀性,防止空载运转。
大豆油生产工艺及流程
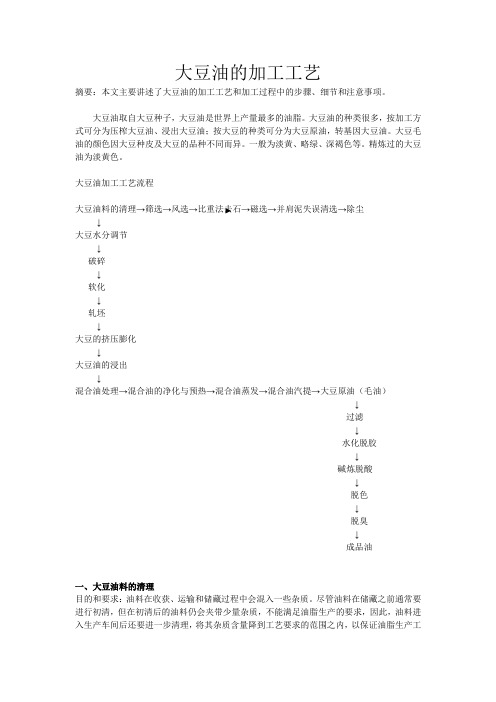
出,膨化成型。一般说来,在挤压过程中,挤压温度可达到 110 一 200℃左右,在挤压机内
的停留时间为 l 一 3min,短的只有 5 一 105。油料经高温湿热挤压处理后,可达到以下目的:(1)
使淀粉糊化、蛋白质变性,由于膨胀,能迅速彻底地破坏细胞结构,油脂均匀地扩散出来,
易于提取。(2)能钝化各种酶类,特别是脂肪水解酶、氧化酶等,在挤压后,失活率达 95%
大豆油加工工艺流程
大豆油料的清理→筛选→风选→比重法去石→磁选→并肩泥失误清选→除尘 ↓
大豆水分调节 ↓
破碎 ↓
软化 ↓
轧坯 ↓
大豆的挤压膨化 ↓
大豆油的浸出 ↓
混合油处理→混合油的净化与预热→混合油蒸发→混合油汽提→大豆原油(毛油) ↓
过滤 ↓
水化脱胶 ↓
碱炼脱酸 ↓ 脱色 ↓ 脱臭 ↓
成品油
一、大豆油料的清理 目的和要求:油料在收获、运输和储藏过程中会混入一些杂质。尽管油料在储藏之前通常要 进行初清,但在初清后的油料仍会夹带少量杂质,不能满足油脂生产的要求,因此,油料进 入生产车间后还要进一步清理,将其杂质含量降到工艺要求的范围之内,以保证油脂生产工
在大豆轧坯之前,必须对大颗粒的大豆进行破碎。其目的就是通过破碎使大豆具有一定 的粒度以符合轧坯条件,大豆破碎后的表面积增大,利于软化时温度和水分的传递,软化效 果提高。
要求大豆破碎后粒度均匀,不出油,不成团,少成粉,粒度符合要求。大豆破碎粒度为 4~6 瓣,破碎豆的粉末度控制为通过 20 目/英寸筛不超过 10%。预榨饼破碎后的最大对角线 长度为 6~10mm。为了达到破碎的要求,必须控制破碎时油料的水分含量。水分含量过高, 油料不易破碎,且容易被压扁。出油。还会造成破碎设备不宜吃料,产量降低等;水分含量 过低,破碎油料的粉末度增大,含油粉末容易粘附在一起形成团。此外,油料的温度也会对
大豆油生产工艺
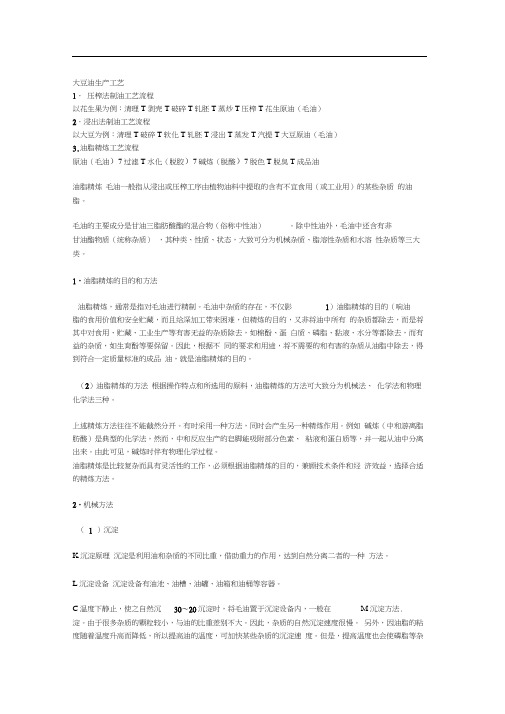
大豆油生产工艺1.压榨法制油工艺流程以花生果为例:清理T剥壳T破碎T轧胚T蒸炒T压榨T花生原油(毛油)2.浸出法制油工艺流程以大豆为例:清理T破碎T软化T轧胚T浸岀T蒸发T汽提T大豆原油(毛油)3.油脂精炼工艺流程原油(毛油)7过滤T水化(脱胶)7碱炼(脱酸)7脱色T脱臭T成品油油脂精炼毛油一般指从浸岀或压榨工序由植物油料中提取的含有不宜食用(或工业用)的某些杂质的油脂。
毛油的主要成分是甘油三脂肪酸酯的混合物(俗称中性油)。
除中性油外,毛油中还含有非甘油酯物质(统称杂质),其种类、性质、状态,大致可分为机械杂质、脂溶性杂质和水溶性杂质等三大类。
1•油脂精炼的目的和方法油脂精炼,通常是指对毛油进行精制。
毛油中杂质的存在,不仅影1)油脂精炼的目的(响油脂的食用价值和安全贮藏,而且给深加工带来困难,但精炼的目的,又非将油中所有的杂质都除去,而是将其中对食用、贮藏、工业生产等有害无益的杂质除去,如棉酚、蛋白质、磷脂、黏液、水分等都除去,而有益的杂质,如生育酚等要保留。
因此,根据不同的要求和用途,将不需要的和有害的杂质从油脂中除去,得到符合一定质量标准的成品油,就是油脂精炼的目的。
(2)油脂精炼的方法根据操作特点和所选用的原料,油脂精炼的方法可大致分为机械法、化学法和物理化学法三种。
上述精炼方法往往不能截然分开。
有时采用一种方法,同时会产生另一种精炼作用。
例如碱炼(中和游离脂肪酸)是典型的化学法,然而,中和反应生产的皂脚能吸附部分色素、粘液和蛋白质等,并一起从油中分离岀来。
由此可见,碱炼时伴有物理化学过程。
油脂精炼是比较复杂而具有灵活性的工作,必须根据油脂精炼的目的,兼顾技术条件和经济效益,选择合适的精炼方法。
2•机械方法(1 )沉淀K沉淀原理沉淀是利用油和杂质的不同比重,借助重力的作用,达到自然分离二者的一种方法。
L沉淀设备沉淀设备有油池、油槽、油罐、油箱和油桶等容器。
C温度下静止,使之自然沉30〜20沉淀时,将毛油置于沉淀设备内,一般在M沉淀方法.淀。
大豆油精炼加工工艺
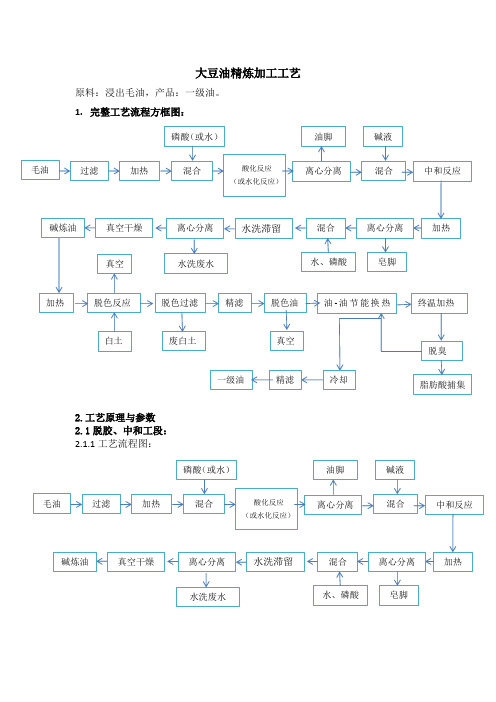
大豆油精炼加工工艺原料:浸出毛油,产品:一级油。
1. 完整工艺流程方框图:2.工艺原理与参数2.1脱胶、中和工段:2.1.1工艺流程图:油脚 碱液 磷酸(或水) 毛油 过滤 混合 加热 离心分离 酸化反应 (或水化反应) 混合 中和反应 加热离心分离 混合 水洗滞留 离心分离 真空干燥碱炼油 皂脚水洗废水 水、磷酸 油脚 碱液 磷酸(或水) 毛油 过滤混合 加热 离心分离 酸化反应 (或水化反应) 混合 中和反应加热 离心分离 混合 水洗滞留 离心分离 真空干燥 碱炼油 皂脚 水洗废水 水、磷酸 真空白土 加热 脱色反应 脱色过滤 精滤 脱色油 废白土 真空 油-油节能换热终温加热 脱臭 脂肪酸捕集冷却 精滤 一级油2.1.2工艺设备及原理大豆毛油经过滤、除杂后由泵送入生产线,经加热器加热至一定温度后进入混合器。
在混和器中,毛油与一定比例的磷酸溶液(或水)充分混合,随后进入延时罐进一步调质,油中的非水化磷脂转化为水化磷脂,然后进入脱胶离心机中进行分离,分离出油脚进入暂存罐中暂存。
酸化后的油(或脱胶油)进入混和器,与一定比例的碱液混合,使游离脂肪酸与碱发生中和反应生成钠皂,再进入延时反应罐充分反应,随后经泵送至加热器加热至一定温度,然后进入脱皂离心机中进行油皂分离,分离出皂脚进入皂脚罐中暂存。
脱皂后的油进入混和器中与一定比例的热水混合,同时添加少量的磷酸溶液(或柠檬酸水溶液),用于鳌和金属离子,利于去除残皂等杂质。
随后进入延时反应罐充分反应,再进入水洗离心机进行水洗分离,以去除残留皂脚等杂质。
水洗后的油最后进入真空干燥器中去除水分及其它挥发性物质,由泵输送至脱色工段。
2.1.3工艺参数●酸法脱胶工艺:100%磷酸(浓度75~85%)加入油量0.05~0.2 %100%柠檬酸(浓度~50%)加入油量0.05~0.2 %酸脱胶不仅对除去非水化磷脂,降低金属离子含量有利,而且对碱炼水洗除去油脂中含皂含量也有很大的益处。
- 1、下载文档前请自行甄别文档内容的完整性,平台不提供额外的编辑、内容补充、找答案等附加服务。
- 2、"仅部分预览"的文档,不可在线预览部分如存在完整性等问题,可反馈申请退款(可完整预览的文档不适用该条件!)。
- 3、如文档侵犯您的权益,请联系客服反馈,我们会尽快为您处理(人工客服工作时间:9:00-18:30)。
大豆油精炼设备详细工艺流程
一、原料处理
1.清洗:将大豆原料放入清洗机中进行清洗,去除表面的杂质和污垢。
2.脱水:将清洗过的大豆进入脱水机中进行脱水,去除大豆表面的水分。
3.磨皮:将脱水后的大豆进入磨皮机中进行磨皮,去除大豆表皮。
二、脱蜡
1.脱蜡槽加热:将磨皮后的大豆放入脱蜡槽,加热至80℃左右。
2.脱蜡:脱蜡槽中的大豆通过搅拌器进行搅拌,使蜡质与油分离。
3.分离:利用离心分离机将脱蜡后的大豆和蜡质分离。
三、脱酸
1.酸碱处理:将脱酸槽中的大豆油用碱溶液中和,使酸性物质中和为
中性。
2.脱酸:将中和后的大豆油进入脱酸槽,通过泡蚀、煮沸、抽剂等方
式去除大豆油中的酸性物质。
3.脱酸剂回收:将抽剂中的酸性物质进行分离和回收利用,减少浪费。
四、脱臭
1.脱臭塔加热:将脱酸后的大豆油加热至240℃左右。
2.蒸汽进料:将加热后的大豆油通过蒸汽进料管进入脱臭塔。
3.去除杂质:在脱臭塔中,运用物理蒸馏的原理去除大豆油中的杂质
和异味。
4.冷凝回收:蒸馏的杂质和异味通过冷凝器进行冷凝,回收回油槽。
五、成油
1.过滤:将回收的大豆油通过滤油机进行过滤,去除残留的杂质和固
体颗粒。
2.包装:将过滤后的大豆油进行包装,可以根据需要选择不同规格的
包装容器。
以上就是大豆油精炼设备的主要工艺流程,通过这些步骤可以将原料
中的杂质和有害物质去除,提高大豆油的质量。
当然,在实际生产过程中,还需要根据具体情况进行调整和优化。