模具自检表
模具结构自检表

时 间模具号Yes No 没有123456789101112131416181921备注标准及要求2022检查通项序号1517其线路安排是否顺畅且不影响模具强度?模具中心线和基准点的关系是否正确?偏移量(X/Y: -Y 20MM )加工基准面、加工基准孔是否表示?(加工中心孔、键槽、模具中心线、模具的加工平面、铸造模包含粗基准)(导板测定孔、压料板镦死窥视孔、机加工时压板夹紧用孔、配管、配线用孔)是否有防侧装置;防侧向力装置强度是否足够?气缸、气动管路走线孔画了没有?自动线模具电器盒、传感器等位置是否满足要求?是否考虑设置了压料板、顶出器、斜楔、起吊和翻转用机构?压料板重量( )直径( )侧销部位的壁厚与侧销的直径是否合理?各种铸造孔明确了没有?R/L非对称处是否有特殊注释?是否设置有C/H、C/P?C/H孔处下模是否设置型面或加强筋?C/H孔位置是否正确?是否画出前工序的制件形状?是否干涉?是否画出毛坯大小?起重棒的规格、类型是否合理?总重量( 4.9T )形状( )尺寸( )压机的T型槽和底板的加强筋设置是否合理?导滑的合入长度是否充分?导向装置是否妥当?是否要采用复合导向?(最初导向合入量至少30mm)铸件的壁厚是否按标准要求设置?模座铸件减轻孔设计是否合理?本工序加工的内容是否满足D/L图的要求?加工方向、送料方向是否正确?模具上、下模的导向防反装置是否合理?模具左右前后侧受力是否平衡?上下模是否需加直接反侧?J5LA-GV9S-70/71714G-审核结果模具文件夹命名、模具号、结构树、明细表及零部件编号是否规范;制件数模及其工艺是否为最新版本;制件名左 右后支柱内板制件编号GV9S-模具结构设计审查项目项J5LA 设 计 者装。
冲压模具检查记录表范例
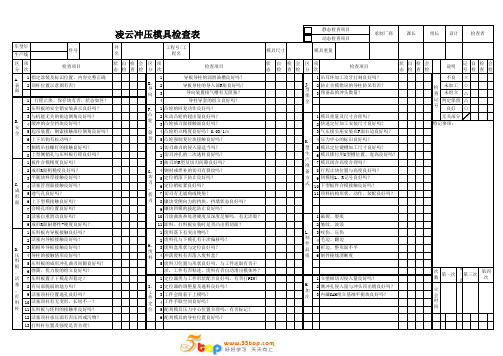
3 预备品的冲头数量?
全
1 模具重量及尺寸合理吗?
2 快速定位加工安装尺寸良好吗?
3 气压接头座安装在F面右边良好吗?
K. 4 压力中心的标识良好吗? 型 5 模具定位键槽加工尺寸良好吗?
生 6 模具锁付用U型槽位置、宽高良好吗?
产 准
7 模具闭合高度合理吗?
备 8 行程止块位置与高度良好吗?
方 9 闭模钮L、R记号良好吗? 式 10 下型板件合模接触良好吗?
12 活塞顶杆承压面有否压凹或污物?
13 打料杆位置及强度是否合理?
1 E. 2 导 向3
4
导板导柱的润滑油槽良好吗? 导板导柱的导入部R角良好吗?
导向装置排气槽有无阻塞? 导柱导套的组立良好吗?
F. 1 凸轮的回复动作良好吗?
凸 2 从动凸轮的超出量良好吗?
轮 、
3 凸轮插刀面接触面良好吗?
斜 4 凸轮组立精度良好吗?0.03/1m
凌云冲压模具检查表
静态检查项目 动态检查项目
承制厂商
课长
组长 设计
检查者
车型年 生产线
件号
件 名
工程号/工 程名
模具尺寸
模具重量
区项 分次
检查项目
状自检会 区项 态检查检 分次
检查项目
状 自 检会 区项 态 检 查检 分次
检查项目
状自检会 态检查检
说明
记自检会 号检查检
A. 1 指定涂装及标识位置、内容完整正确 表 2 顶杆位置示意图有否? 面
11 顶料机构形状、动作、装配良好吗?
1 破裂、裂痕
2 皱纹、波浪
L. 3 咬伤、压伤 制 4 毛边、翻边 件 品 5 折边、整形面不平 质 6 制件棱线清晰度
UG3D自检表
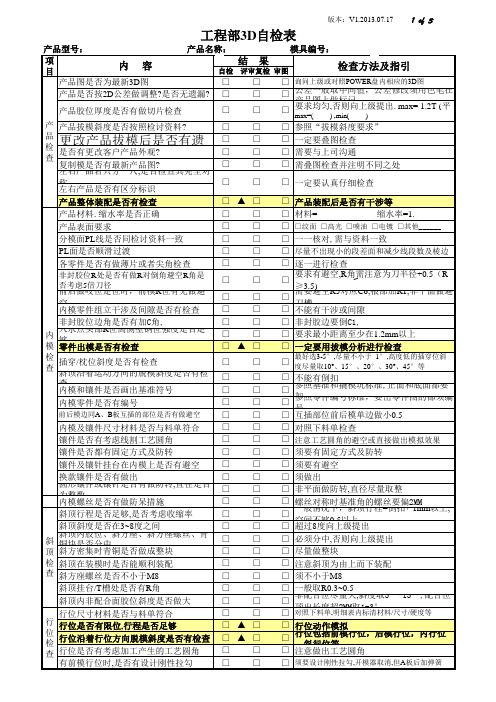
不能有干涉或间隙 非封胶边要倒C1, 要求最小距离至少在1.2mm以上 一定要用拔模分析进行检查
最好选3-5°,尽量不小于 1°,高度低的插穿位斜 度尽量取10° 、15°、20°、30° 、45°等
内模及镶件尺寸材料是否与料单符合 镶件是否有考虑线割工艺圆角 镶件是否都有固定方式及防转 镶件及镶针挂台在内模上是否有避空 换款镶件是否有做出
□ ▲ □ □ □ □ □ □ □ □ □ □ □ □ □ □ □ □ □ □ □ □ □ □ □ □ □
按最新标准
PART档需有三个产品:原始产品、乘缩水产品、浇注PART
必须检查 要求写 必须转存 要求填
设计工程师:
日期:
设计负责人:
日期:
日期
模具编号
扣分
审核
设计工时
开始时间
计划出图时间
实际出图时间
□ 要求设计分型面排气,原则上根据模流分析结果 □ 照标准做 □ 要求做 □ 需在流道处将排气断开 □ 骨位深超过15mm,宽1.0mm以下的镶件须做排气
排 大水口模胚是否有导套排气槽 气 流道末端是否有排气,排气是否排在大气中 检 查 分型面有梯形流道,排气开在另一零件时,排气有无与流道避开 骨位深的镶件是否有画排气
注意工艺圆角的避空或直接做出模拟效果
须要有固定方式及防转 须要有避空 须做出 非平面做防转,直径尽量取整 螺丝对称时基准角的螺丝要偏2MM
一般情况下,斜顶行程=倒扣+ 1mm以上,空间不够0.5以上
超过8度向上级提出 必须分中,否则向上级提出 尽量做整块 注意斜顶为由上而下装配 须不小于M8 一般取R0.3~0.5
版本:V1.2013.07.17
模具移模自检表

所有集流板和喷嘴是否采用P20材料制造。
28
在模板装配之前,所有线路是否无短路现象。
29
所有电线是否正确联接、绝缘。
30
在模板装上夹紧后,所有线路是否用万用表再次检查。
成型部分、分型面、排气槽
√
23
大型滑块(重量超过30KG)导向T形槽,是否用可拆卸的压板。
√
24
滑块用弹簧限位,若弹簧内置,弹簧孔是否全出在后模上或滑块上;若弹簧外置,弹簧固定螺栓是否两头带丝,以便滑块拆卸简单。并加防护套。
√
25
滑块的滑动距离是否大于抽芯距2-3mm,斜顶类似。
√
26
滑块下面是否都有耐磨板(滑块宽度超过80mm),耐磨板材料T8A,淬火至HRC50-55,耐磨板比大面高出0.5mm,耐磨板应加油槽。且不开通。
√
6
进出油嘴、进出气嘴是否同冷却水嘴,并在IN、OUT前空一个字符加G(气)、O(油)。
√
7
模具安装方向上的上下侧开设水嘴,必须开导流槽或下方有支撑柱加以保护。
√
8
伸出模架顶底板范围的油嘴或水嘴下方是否有支撑柱加以保护。
√
9
模架上各模板是否有基准角符号,大写英文DATUM,字高8MM,位置在离边10mm处,字迹清晰、美观、整齐、间距均匀。
√
18
斜顶、滑块抽芯成型部分若有筋位、柱等难脱模的结构,是否加反顶机构。
√
19
大的滑块不能设在模具安装方向的上方,若不能避免,是否加大弹簧或增加数量并加大抽芯距离。
√
20
21
滑块的滑动配合长度大于滑块方向长度的1.5倍,滑块完成抽芯动作后,保留在滑槽内的长度是否小于滑槽长度的2/3。
模具课钳工自检表
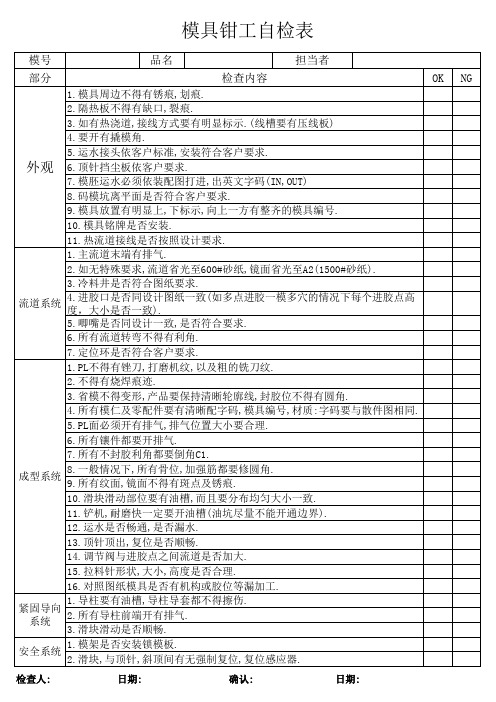
1.导柱要有油槽,导柱导套都不得擦伤.
紧固导向 系统
2.所有导柱前端开有排气.
3.滑块滑动是否顺畅.
安全系统
1.模架是否安装锁模板. 2.滑块,与顶针,斜顶间有无强制复位,复位感应器.
检查人:
日期:
确认:
日期:
8.码模坑离平面是否符合客户要求. 9.模具放置有明显上,下标示,向上一方有整齐的模具编号. 10.模具铭牌是否安装.
11.热流道接线是否按照设计要求. 1.主流道末端有排气. 2.如无特殊要求,流道省光至600#砂纸,镜面省光至A2(1500#砂纸).
ቤተ መጻሕፍቲ ባይዱ
3.冷料井是否符合图纸要求.
流道系统
4.进胶口是否同设计图纸一致(如多点进胶一模多穴的情况下每个进胶点高 度,大小是否一致).
模具钳工自检表
模号
品名
担当者
部分
检查内容
OK NG
1.模具周边不得有锈痕,划痕. 2.隔热板不得有缺口,裂痕. 3.如有热浇道,接线方式要有明显标示.(线槽要有压线板)
外观
4.要开有撬模角. 5.运水接头依客户标准,安装符合客户要求. 6.顶针挡尘板依客户要求. 7.模胚运水必须依装配图打进,出英文字码(IN,OUT)
6.所有镶件都要开排气.
7.所有不封胶利角都要倒角C1.
成型系统
8.一般情况下,所有骨位,加强筋都要修圆角. 9.所有纹面,镜面不得有斑点及锈痕.
10.滑块滑动部位要有油槽,而且要分布均匀大小一致. 11.铲机,耐磨快一定要开油槽(油坑尽量不能开通边界). 12.运水是否畅通,是否漏水.
13.顶针顶出,复位是否顺畅. 14.调节阀与进胶点之间流道是否加大. 15.拉料针形状,大小,高度是否合理. 16.对照图纸模具是否有机构或胶位等漏加工.
试模报告表格

J 产品检查 4.收缩 □
1.加强筋太厚 □ 2.产品局部料过厚 □ 3.进胶口尺寸太小 □
5.后模拖伤 □ 1.加强筋未抛光 □ 2.滑块行程不够 □ 3.斜推高出凸模表面 □ 4.后模局部倒扣 □ 前
6.前模拖伤 □ 1.前模分型线反边 □ 2.前模抛光不足 □ 3.产品贴前模 □
次
7.夹水纹明显 □
3.斜推碰贴面反边 □ 4.顶出行程不够 □ 7.取浇口困难 □
1.顶白 □
1.推杆未作防滑 □ 2.加强筋未抛光 □ 3.局部有倒扣 □
2.毛刺 □
1.分型面 □ 2.滑块碰贴面 □ 3.斜推 □ 4.斜推碰贴面 □ 5.推针 □ 6.前模分型线出圆角 □
3.阶差 □
1.分型面 □ 2.斜推,直推与凸模面不平 □ 3.推针低于凸模面大于0.1 □
1.排气不良 □
2.夹水纹处易断裂 □
3.夹水纹处不平 □
4.前模温度不够 □
8.缺胶 □
1.局部尺寸太薄 □ 2.困气 □ 3.模具漏加工 □ 4.模具未清理干净 □
工艺参数
射出时间 15 温度
热咀温度 射出位置 射出压力 射出速度 熔胶位置 熔胶压力 熔胶速度
松退 托模前位置 托模前压力 托模前速度 材料干燥时 材料干燥温
冷却时间 成型周期 型腔数 净量
模具温度 定模
动模
40
滑块 上 下 左 右 手动
一 二段 三段 四段 五段 六段 七段 八段 热流度 一段 二段 三段 四段
220 225 210 210 200
温度
300 125 85 65 35
保压压力 65
120 110 95 85 80
保压速度 15
35 85 30 25 20
模具自检表
攻芽深度==1.5倍牙距+8 mm ;螺塞沉深2mm
□ □ □ □
□ □ □ □
2)、销钉与模板(座)的有效配合长度为 15mm ≤ L≤30 mm 3)、模板或零件拆装方便,零件可快换 4)、镶件快拆(孔内攻牙或螺塞顶杆,敲击孔、压块), ø2.5及以下小孔冲头必须快换
5)、产品共模的模具换型时冲头、凹模等必须快换; 11、模板、零件强度检查 1)、凹模形状复杂易损坏的部分做镶件结构,凸凹模做镶件并要补强 2)、凹模板形状复杂时:30mm≤壁厚,30mm≤模板厚度 ,或考虑板分割 12、脱料销孔排布检查 所有连续模最后出产品脱料板需要加顶针 折弯脱料销孔边缘离折弯边距离为3~5mm,排布距离为50~80mm,脱料销大小取值为Ø4、Ø8、Ø10、Ø13 13、靠刀检查 1)、单边剪切冲头要设计靠刀或脱料板导正:单边间隙=0.02,上下导入角R1 2)、折弯侧向力大时下模要设计导向块,上模座设计挡键或与脱料板导正,单边间隙=0.02 14、防跳废料及漏料孔、堵料检查 1)、冲头防跳废料设计(顶芯、吹气)、凹模台阶式漏料 2)、下垫板及下模座漏料孔检查,垫铁避位 3)、侧冲落料要纽扣式排除废料 ,强度可靠 15、闭合成型结构检查: 1)、冲孔落料应避免为闭合成型结构,外脱板距离下垫板或下模座≥5mm;内脱板距离上垫板≥5mm 2)、折弯模、成型小凸苞模具客户无特殊要求时必须闭合成型 3)、模具必须配备限位柱,且限位柱的高度必须准确,(标注高度允许超出实际高度0.5mm) 16、工艺检查 1)、需线割型腔≤520mm(公司内线割机最大行程530mm); 2)、采用CNC加工时加工深度h=5倍刀具直径,一般型腔转角≥ R2.5; 3)、异形零件、冲头等加工成本、工艺性优化; 17、定位结构检查 1)、单工序定位前后一致,零件定位可靠 2)、连续模第一步要有初定位,中间要加误送料检测针; 3)、单工程模具定位有效直身位高出产品15mm,内定位定位直边高度原则上为3mm,该高度以定位面为 测量基准面,但模具定位实际高度必须根据零件的变形情况进行适当的调整。(有效部位需超出零件表面 5mm) 4)模具原则上不允许采用台阶定位,如果必须采用台阶定位则必须将定位上的台阶下沉5mm以上,下沉 深度以定位面为测量基准面(模具上使用的台阶定位销必须下沉2倍料厚以上) □允许
模具检验记录表
10 异型孔和非平面安装的凹模套及镶套安装孔必须加防转措 · 施 11 凹模套安装到底无悬空;凹模套与型面符型(允许凹模套高 于型面留有微量研量) 12 废料孔通畅无台阶 13 压、托料与冲头安装座无干涉现象 14 使用球锁紧凸模时,冲孔凸模周围的压料芯采用镶块式结 构,以使凸模拆卸方便
翻边、整 1 工作型面光顺无无用螺钉孔、销钉孔或其他孔;无磕伤碰伤;
4 废料滑板的板厚要符合要求,无变形,啊滑料板厚 1.8mm, 啊滑料板厚 2.5mm
5 废料盒要有防脱措施,防止模具起吊过程脱落 6 废料盒与模具型腔壁贴合,并且取放方便
7 折叠式废料滑板要用链条固定 ,不允许将链条固定在上模, 并且折叠固定后废料滑板不允许超出模具顶面
1 料厚(t)《1.5mm,刃口保留高度≧5mm 21.6mm 料厚(t)《3mm,刃口保留高度≧7mm
冲孔
7 修边镶块螺钉、销钉布局合理,螺钉、销孔不允许在一条直 线上 8 刃口镶块的材料牌号、编号需在镶块上打印清楚 1 冲头与固定座安装牢靠,无晃动 2 冲头刃口锋利无损伤 3 冲头弹料销活动自如,无卡滞现象 4 冲头安装销钉是,是否加销堵,起防止脱落保护措施 5 销钉松紧度合理,螺钉安装符合要求(冲头 10 个以下全部 拆检)
格)
3 斜楔压板与导滑面间隙《0.03mm
废料滑 板、废 盒
刃口背空 ·弹簧
键 安全
4 外漏的气缸、裸露的弹簧有安全防护措施 5 斜楔行程背板安装面铸件壁厚应在 60mm 以上,以确保安全
6 导板安装符合图纸要求 7 斜楔各部件刻印正确无误(包括镶块,冲头等与模座安装面 的对应标记刻印)
8 斜楔和挡墙间隙<0.02mm
自检
4、刃口要求锋利,不允许有过烧现象以及与刃口方向平行的 裂纹;垂直裂纹允许 100mm 内《3 个,裂纹宽度<0.05,长度 <5mm 5 上模修边镶块上螺钉、销钉有防脱落措施(螺钉加弹垫,销 钉加丝堵或弹簧销堵),特殊情况加盖板防脱 6 凸凹模刃口过渡出要有圆弧平顺连接,不允许有尖角或应力 集中
模具自检表
模具自检表
1、定位圈是否符合注塑机规格
2、模架强度是否足够
3、模架是否有锁模块
4、模架是否有吊环螺丝孔
5、模架是否有撬模空隙
6、大尺寸模架A、B板四角是否接触
7、模架上是否已将顶针、水路等剪除
8、是否将需避空的地方避空
9、模架上是否有无法加工的直角及小圆角
10、支撑柱是否足够
11、顶针、水路是否足够
12、顶针直径是否足够
13、大尺寸的模仁是否有起模螺丝孔
14、大尺寸模仁是否有压紧块
15、滑块、斜顶行程是否足够
16、滑块、斜顶强度是否足够
17、顶针板若完全顶出是否与斜顶干涉
18、滑块下有顶针时,是否有顶针先复位机构
19、CORE/CAVITY斜度是否足够
20、顶出孔是否足够
21、浇口是否足够大
22、是否有偏公差偏公差是否已做到中间值
23、产品是否有太厚或太薄的地方
24、是否有排气死角
25、弹簧是否正确,三板模拉杆上加弹簧,滑块加复位弹簧或定位
珠。
模具自检表格
8.不可以打编号的产品是否在水口上打上编号.
行 位 部 位
冷 却 系 统
顶出 系 统
制模 员:
10.攻牙孔的倒角位是否准确. 11.攻牙孔的孔径、孔距的尺寸是否准确无误. 1.行位起止位置是否正确可靠、装配合理、滑动顺畅.
2.行位润滑系统是否设立可靠.
1.冷却(运水)是否畅通.
2.料咀冷却水是否堵好,并无漏水现象.
有□ 没有 □
是□
否□
有□ 没有 □ 准确 □ 不准确 □ 准确 □ 不准确 □
是□
否□
是□
否□
是□
否□
是□
否□
正确 □ 不正确 □
正确 □ 不正确 □
审核:
注:试模前务必认真检查以上的重点,检查完将此表填好,交由文员存档.
目的:
模具自检表
鉴于模具制造周期较长,遗忘之事时有发生;模具试模前亦经常由于一些小疏忽 而导致重上压铸机、试模多次,浪费资源,为避免此类事情的发生,特针对一 些易遗忘和疏忽之处列于下表以备自检或互查。
型 号:
订 单 号:
开发日期:
项目
内容
资 1.模具与图纸尺寸是否合格(计缩水). 料
复 2.有公差的地方是否都准确无误. 核
1.顶针、司筒针的高度、方向、位置是否正确及无漏装.
2.顶针、斜顶及推板装配是否正确、伸缩顺畅,复位正确可 靠.
检查日
试模日
期:
期:
检查结果
备注
合格 □ 不合格 □
准确 □ 不准确 □
准确 □ 不准确 □
是□
否□
够□ 不够 □
有 □ 没有 □
平□ 不平 □
有□ 没有 □
有□ 没有 □
- 1、下载文档前请自行甄别文档内容的完整性,平台不提供额外的编辑、内容补充、找答案等附加服务。
- 2、"仅部分预览"的文档,不可在线预览部分如存在完整性等问题,可反馈申请退款(可完整预览的文档不适用该条件!)。
- 3、如文档侵犯您的权益,请联系客服反馈,我们会尽快为您处理(人工客服工作时间:9:00-18:30)。
模具自检表
试制模具试制模具-制造自检表
模具编号:
分类 确认项
模具名称:确认内容 自检 √/×源自NA制造:让步认可申请
审核:
符合项 √/NA
日期:
不符合项 让步认可 试模复检 ×/NA √/×/NA √/×/NA 备注
一、吊装系统
二、注塑系统
三、成型系统
四、冷却系统
五、顶出系统
备注:
1.安装在模具天侧 2.型号及安装位置符合设计要求 3.螺纹拧到底了 模锁 模具两侧都安装了 1.安装在模具地侧 支撑脚 2.长度及安装位置符合设计要求 1.已安装且无损坏及松动 定位圈 2.尺寸与选定注塑机相符 1.球半径与选定注塑机相符 浇口套 2.浇口套无损坏 1.压线板正确安装了 2.接线盒固定了 热流道 3.接线无裸露 4.能加热到要求温度 5.加热到要求温度后阀针能正常开合 抛光 影响脱模的重点部位已抛光 1.滑动顺畅 2.天侧滑块加装了弹簧限位装置 滑块 3.安装了复位开关 4.抽芯油缸前进后退动作正常 5.螺纹抽芯油马达正反转动作正常 1.无松动 导柱 2.已开油槽并润滑 1.水路接头型号符合设计要求且无缺损 2.连接回路符合设计要求 水路 3.单个回路水压8Kg测试无泄漏 4.水流自由流动,基本达到紊流状态 复位开关 针板两侧复位开关都安装了且有效 1.无转动 顶出机构 2.顶出、复位动作自如 1.油缸前进后退动作正常 油路 2.油路无泄漏 1)审核员应在模具计划试模前进行审核,一旦发现不符合项且不符合让步条件的,不允许试模并通知项目负责人。 2)试制模具前必需提供此自检表,试模员对模具进行复检并记录,一旦发现不符合项且不符合让步条件的,有权拒绝试模。 3)模具试制结束后,自检表一式两份,一份试制科留存,一份交项目负责人,项目负责人应对责令监督模具制造者整改不符合项。 吊环