半挂车过程检验单
车辆检验记录表

抛、切丸规格
抛丸1.5切丸1。5
混合比例
4
抛丸机电流
当清理效果不理想时,应减慢辊道输送速度或添加钢砂
5
辊道输送速度
0。8—1。3米/秒
6
清理效果
各处的锈蚀、氧化铁、飞溅清理彻底
7
残沙清理
各死角无残余钢丸
底板焊接
1
来件检验
边梁无磕碰划伤、及烧伤烧穿
互检
3
焊接参数
焊接电流:200—245A;
焊接电压:23—27V
最后端侧位灯到车辆最后端≤900;
两灯间距≤3000;左右对称
前
后
间距
1
支架高度
按派工单要求
牵引销至中前支架距离
牵引销至中前支架拉杆孔轴线对应点距离差≤1。5(对角尺寸)
左
填写实测距离
右
前、前中支架距离
间距尺寸±2mm/对角尺寸≤3mm
左
填写实测距离
右
对角
两中支架距离
间距尺寸±2mm/对角尺寸≤3mm
气流量20—25L/min
4
牵引板焊接
厚度≤8mm时,焊缝高度等于板厚;腹板厚度≥10mm时,焊缝高度等于0。8X板厚。
药芯焊丝焊接;
专人焊接
5
加固板焊接
鹅颈部位通焊(后端圆弧部位、前端不焊),平直部位间断焊接(焊段长250mm,间隔200mm),
6
W称焊接
焊高4,
7
其他焊缝
焊高不小于板厚
8
割弧
轮胎安装处割弧与派工单要求的轴距尺寸差±2mm,无切割缺陷
合页样式:按派工单
2
后门样式
按派工单
3
帽罩
半挂车关键工艺和关键控制点检查记录

检验
时间
设备名称
压力表
工位
制动系统安装测试
检验结果
检验员
产品名称
半挂车
规格型号
TDZ9401
关键工序
操作员
气源压力/千帕
压降/千帕
制动系统安装测试
质量要求:
检验漏气:在额定气压700至720千帕下,非制动3分钟内,系统气压下降不大于10千帕
审核:日期
侧防护焊接
后防护焊接
支撑板的焊接
质量要求:
1、焊缝外观:平整均匀,无漏焊、虚焊、裂纹,以及夹渣
2、焊缝尺寸:焊角不小于较薄板板厚的1.5倍
检验
时间
设备名称
扭力钣手
工位
组装
检验结果
检验员
产品名称
半挂车
规格型号
TDZ9401
关键工序
操作员
测量扭矩力
钢板弹簧与车轴的连接
车轮的安装
质量要求:
1、钢板弹簧与车轴的连接紧固力矩:320至380N*m
半挂车关键工艺和关键控制点检查记录
编号:
车辆制造有限公司
关键工艺和关键控制点检查记录
编号:合同编号:
检验
时间
设备名称
焊机
工位
焊接
检验结果
检验员
产品名称
半挂车
规格型号
TDZ9401
关键工序
操作员
焊接电压
25--35V
电流
160---210A
焊接速度
250--300mm/min
车架焊接
悬架焊接
牵引销焊接
半挂车成品检验记录表
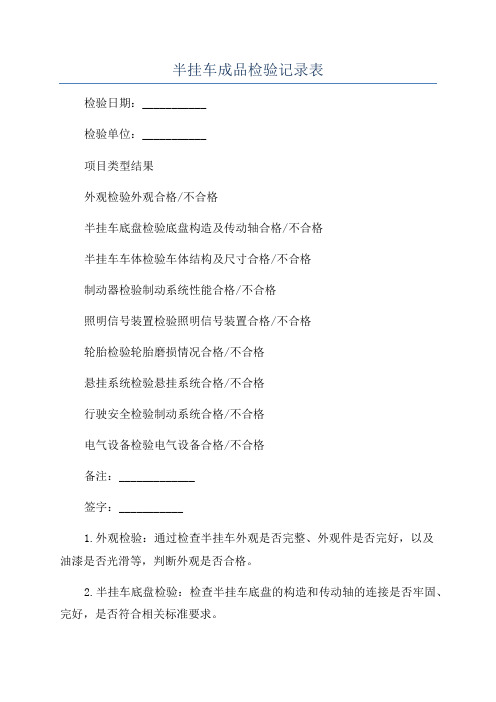
半挂车成品检验记录表检验日期:___________检验单位:___________项目类型结果外观检验外观合格/不合格半挂车底盘检验底盘构造及传动轴合格/不合格半挂车车体检验车体结构及尺寸合格/不合格制动器检验制动系统性能合格/不合格照明信号装置检验照明信号装置合格/不合格轮胎检验轮胎磨损情况合格/不合格悬挂系统检验悬挂系统合格/不合格行驶安全检验制动系统合格/不合格电气设备检验电气设备合格/不合格备注:_____________签字:___________1.外观检验:通过检查半挂车外观是否完整、外观件是否完好,以及油漆是否光滑等,判断外观是否合格。
2.半挂车底盘检验:检查半挂车底盘的构造和传动轴的连接是否牢固、完好,是否符合相关标准要求。
3.半挂车车体检验:检查半挂车车体结构及尺寸是否符合相关标准要求,以确保车体的牢固性和合理性。
4.制动器检验:对半挂车的制动系统进行测试,检查刹车性能是否正常,确保制动能力符合要求。
5.照明信号装置检验:检查半挂车的照明信号装置是否完好,是否能够正常工作,以确保行车安全。
6.轮胎检验:检查半挂车的轮胎磨损情况,是否存在严重磨损或其他异常情况,以保证行车安全。
7.悬挂系统检验:检查半挂车的悬挂系统是否牢固、完好,以确保行驶的稳定性和行驶安全。
8.行驶安全检验:对半挂车的制动系统进行更加详细的测试,以确保半挂车制动系统的性能符合标准要求。
9.电气设备检验:检查半挂车的电气设备是否完好,能否正常工作,以确保行车安全和操作的便捷性。
备注:在备注栏中可添加其他需要注意的问题,或对检验过程中发现的问题进行说明。
签字:检验单位的负责人需在签字栏签字确认该次检验的结果。
以上是半挂车成品检验记录表的范本,可以根据实际需要进行相应的调整和修改。
半挂车检验记录表

合同号VIN代号生产车间出厂编号产品型号3C标志号生产班组车架标识序号检验项目技术要求实测备注1 汽车标记(★)1.产品标牌应位于前端梁右端,铆接牢固,标牌内容齐全总质量:整备质量:2.产品标识位于后尾板上,铆接牢固,标识齐全2 车辆外廓尺寸长×宽×高(按实际尺寸)3 牵引销中心到第一轴左右轮中心距离差牵引销中心到第一轴左右轮中心距离差不大于± 3mm。
左---------------右---------------差--------------4 轴距1.相邻两轴轴距L= ±5mm。
左中右中左后右后2.整车轴距(从牵引销到轴的距离)L= ±10mm。
5 螺栓、螺母的紧固力矩1.固定牵引销紧固力矩为:130-145N.m。
2.U形螺栓、螺母紧固紧力矩:400-450N.m。
3.拉杆螺栓紧固力矩:130-145N.m。
4.支腿紧固螺栓紧固力矩:200~230N.m。
6 支承装置安装升降灵活,无卡滞现象。
7 油嘴及润滑油嘴应齐全有效,注满油脂。
8 制动系统气密性试验(★)在气压升至600KPa且不使用制动的情况下,停止空气压缩机3min后,其气压降低值不应大于10KPa。
在气压为600KPa的情况下,将制动踏板踩到底,待气压稳定后观察3min,气压降低值不应大于20KPa,汽车列车气压降低值不应大于30KPa。
9 栏板装配1.箱板与边梁、立柱间的间隙均不大于3mm。
3.各箱板高度差不大于3mm。
4.栏板开关灵活、轻便、栓钩无松旷现象。
10 防护装置防护网总成(★)1.防护网总成前缘位于支腿的中心横截面之后不大于250mm处2.防护网总成的后缘应处在轮胎周向切面之前300mm的范围之内3.防护网总成的下缘任何一点的离地高度520±20mm。
4. 防护网总成的前缘应具有一个连续的、贯穿其整个高度的垂直构件,该垂直构件的外侧面向内弯曲100mm,垂直构件的前端面向后弯曲至少100mm。
半挂车成品例行检验范表

偏差≤±3%
地磅
符合工艺规范。深浅一致,附着力好;无 变色、脱层、气泡、流痕等现象。
支承装置:操作应灵活可靠,该装置离地 间隙不得小于350mm。 螺母拧紧扭矩:182-245Nm 轮胎:螺母拧紧扭矩:570-630Nm 气压:轮胎标定±10kpa 车轴及钢板弹簧:规格尺寸及安装正确、 上下支板焊接牢靠。 U型螺栓扭力:600-650Nm
应无异响、联接松动、偏尾、偏磨等异常现象。
制动反应敏捷,无甩尾;每个轮胎都有拖痕且长度一致。 出现异常时可以检测制动力。
பைடு நூலகம்
备注
验收结论
合格接收( )
让步接收( )
返修返工( )
检验:
校对:
批准:
填写不合格处理单( )
NSJ
车轴号:
支承号:
半挂车成品例行检验记录单
表号: 日期:
牵引销号:
继动阀号:
VIN
序 检验 号 项目
依据
1 尺寸
NSJ/QW5.1-01
2
整备质量
(定期抽检)
公告参数
3 油漆
NSJ/QW5.1-01
NSJ/QW5.1-01
4 装配
GB4785 NSJ/QW5.1-01
NSJ/QW5.1-01
5 整车标识
电路布置整齐,固定牢靠,照明和信号装 置数量齐全、安装位置正确。
气路布置整齐,固定牢靠,配件齐全、安 装位置正确。
锁顶应转动(固定锁顶)或升降(升降锁 顶)灵活,位置正确,锁止可靠。
目测
卷尺测量 扭力扳手检查 压力尺检查
目测 卷尺测量
目测 卷尺测量 目测 手感
VIN 铭牌 商标 型号 厂名符合要求
目测
半挂车和全挂车符合性安全检查表

3a
4a 4b 4c
5a6a7a1a 1b 2a 2b 2c 2d
2e
3a
277808811.xlstrailer-loadbed checklist
Page 1 of 2
print date: 1
No编号 4a
Standards required要求标准 Trailer landing gear appropriate to the gross weight and which does not interfere with the 与总重配套的挂车起落装置,且在装货的情况下不会干扰拖头的摆动。两个带浮板的可伸 swing of the prime mover when stowed. Dual telescopic landing legs with flotation plates 缩式支腿,适用于软土地面,且有足够的强度支撑满载的挂车。 suitable for use on soft ground and adequate strength to support a fully loaded trailer. 4.4.3. DRAWBAR TRAILERS Specific Requirement 1. BRAKES Overrun brakes and parking brake, as a minimum, for trailers with a gross weight (trailer + load) of up to 3,500 kgs. Two- or three-line trailer brake system, for trailer with a gross weight of more than 3,500 kgs. 2. COUPLING AND CONNECTIONS Drawbar eye of the trailer to match with the trailer coupling of the towing vehicle Trailer coupling height to match the drawbar height of the trailer Drawbar to be horizontal when connected 4.4.4. REQUIREMENTS FOR LOAD BED FOR GENERAL CARGO, TUBULARS & CONTAINERS 1. GENERAL A smooth wooden cargo deck with no holes or protruding parts In case of steel decks: smooth with no holes and sufficient wooden sleepers, rubber mats or manilla type rope to provide friction area between steel cargo and load bed 4.4.3 全挂车具体要求 1. 制动器 总重(挂车+负荷)在3,500kgs以下的挂车应至少配有过速制动器和停车制动器 总重在3,500kgs以上的挂车应配有两线或三线制动系统 2. 联接器和连接 挂车的牵引杆孔应与牵引车的挂车联结器配套 挂车联结器的高度与挂车牵引杆的高度配套 连接后,牵引杆应保持水平 4.4.4 普通货物、管材和集装箱用平板车的要求 1. 概述 光滑的木制装货板,无孔洞或凸出部分 若是钢制装货板:表面光滑无孔洞,且有足够的木枕、橡胶垫或吕宋麻绳,在钢制装货板 与平板车之间提供摩擦区
半挂车过程检验单

半挂车过程检验单检验项目:1.车身外观检查2.驾驶室和底盘检查3.制动系统检查4.悬挂系统检查5.灯光系统检查6.轮胎和轮毂检查7.油箱和燃油系统检查8.管路和电器系统检查9.储藏箱和挂钩检查10.挂车制动和纵横稳定性测试检验步骤:1.车身外观检查:-检查车身是否完整,有无明显损伤、腐蚀等。
-检查车身上是否有明显的喷漆修补痕迹。
-检查车身上的镀铬饰条是否完好。
2.驾驶室和底盘检查:-检查驾驶室的底盘是否有明显的油渍或漏油现象。
-检查驾驶室的座椅、方向盘、仪表等是否正常工作。
-检查底盘是否有明显的异常噪音或震动。
3.制动系统检查:-检查制动系统的刹车片和刹车盘是否磨损严重。
-检查制动系统的制动液是否达到标准要求。
-进行制动系统的一系列测试,包括紧急制动、制动平衡等。
4.悬挂系统检查:-检查悬挂系统的悬挂弹簧和减震器是否正常。
-检查悬挂系统的螺栓、松紧带等是否松动。
-进行悬挂系统的一系列测试,包括经济速度通过坡道、过减速带等。
5.灯光系统检查:-检查车辆的前大灯、后尾灯、转向灯等是否正常工作。
-检查车辆的照明灯光是否清晰明亮。
-进行灯光系统的一系列测试,包括夜间行驶、转向信号等。
6.轮胎和轮毂检查:-检查轮胎的花纹深度是否达到要求。
-检查轮胎的胎面是否有明显的损伤或磨损。
-检查轮毂的螺栓、松紧带等是否松动。
7.油箱和燃油系统检查:-检查油箱的密封性是否良好。
-检查油箱的防爆阀和透气阀是否正常工作。
-检查燃油管路是否有泄漏现象。
8.管路和电器系统检查:-检查管路是否有明显的损坏或漏油现象。
-检查电器系统的线路是否正常连接。
-进行电器系统的一系列测试,包括转向灯信号、刹车灯信号等。
9.储藏箱和挂钩检查:-检查储藏箱的门是否完好,是否能正常开启和关闭。
-检查挂钩的锁紧装置是否可靠。
-检查挂钩、牵引装置的磨损程度。
10.挂车制动和纵横稳定性测试:-进行挂车制动和纵横稳定性的一系列测试,包括紧急制动、交织穿越等。
货车、罐式汽车、半挂车现场核查记录表

后防护横向构件截面高度(N2,≧100;N3,≧120;)(mm)
后防护装置下边缘离地高≦500(mm)
后防护装置任一端最外边缘与这一侧后轴车轮最外端水平横向距离≦100(mm)
核查地点: 核查时间: 样车核查人:
表2 罐式汽车现场核查记录表
车辆基本结构及技术参数检查表
产品型号及名称
产品生产企业
VIN
货车、罐式汽车、半挂车现场核查记录表
表1 货车现场核查记录表
车辆基本结构及技术参数检查表
产品型号及名称
产品生产企业
VIN
序号
技术参数
检查结果
1
外廓尺寸
长×宽×高(mm)
2
整备质量(kg)
3
轮胎
数量、型号规格、层级
4)(左/右)
侧防护横杆截面高度(N2,≧50;N3,≧100;)(mm)(左/右)
后防护装置任一端最外边缘与这一侧后轴车轮最外端水平横向距离≦100(mm)
7
危险品罐式运输车
圆柱罐体
罐体总长(mm)
罐体直径(mm)
椭圆罐体
罐体总长(mm)
长轴(mm)
短轴(mm)
8
混凝土搅拌运输车
罐体总长(mm)
中筒长度(mm)
中筒直径(mm)
罐体安装角度(°)
核查地点: 核查时间: 样车核查人:
侧防护下缘离地高≦550(mm)(左/右)
侧防护前缘若为超过25mm的开阔空间,应具有一个连续的贯穿整个高度的垂直构件(左/右)
前缘距支腿中心横截面的距离≦250mm(左/右)
前缘距牵引主销位于最后位置时中心横截面的距离≦2700mm(左/右)
后缘与处在最靠近它的轮胎周向铅垂切面间的距离≦300(mm)(左/右)
- 1、下载文档前请自行甄别文档内容的完整性,平台不提供额外的编辑、内容补充、找答案等附加服务。
- 2、"仅部分预览"的文档,不可在线预览部分如存在完整性等问题,可反馈申请退款(可完整预览的文档不适用该条件!)。
- 3、如文档侵犯您的权益,请联系客服反馈,我们会尽快为您处理(人工客服工作时间:9:00-18:30)。
外观
所有焊接处均牢固可靠,没有未清理之焊缝及飞溅
备注
检验人:
喷漆检验
型号 批号; 日期:
序号
检 验 项 目
检 验 标 准
检验结果
判 断
1
工件检验要求
工件表面喷丸或钢丝刷除锈,目视没有明显锈痕,无氧化皮存在
工件表面应无焊接飞溅物、焊渣、表面没有毛刺及油污
2
防锈漆
目视底漆喷涂要均匀、无滴挂、流淌等缺陷及漏喷现象
检查上下板簧座的安装位置是否符合设计要求。最大偏差小于1mm
检查板簧座与车轴是否贴紧,是否达到规定的压力。卡轴板与车桥轴管的单侧间隙不大于3mm。
板簧座与车轴之间不允许有扭曲、歪斜等缺陷
上下板簧座的孔中心线必须重合。
安装钢板弹簧后,左右钢板弹簧对角线误差小于3mm
2
车轮安装
螺栓的预紧力是否拧紧到规定的600±。且相邻轮胎螺栓的扭矩值之差不能超过5%。
2
悬挂组焊
吊耳焊接要求对角焊严禁顺序焊,焊角≥8mm。
3
打磨
三角加强块只焊接纵向焊缝,横向不焊接。焊接后不得有扭曲、歪斜现象。
4
翻转焊
按图纸要求加焊垫梁,穿线螺丝,气瓶支架。保证各部件焊接牢固。
5
平板焊
保证焊缝均匀一致,只允许有一个接头,并且打磨平整
备注
检验人:
厢体总成检验
型号 批号; 日期:
序号
检 验 项 目
半挂车过程检验单
小件制作检验
型号 批号; 日期:
序号
检验项 目
检 验 标 准
检验结果
判 断
1
剪板
确保板的材质,规格与图纸一致
折弯角度必须按图纸要求度数施工误差±3º
剪板尺寸误差±1mm
对角线±2mm
剪板刀口要整齐,无毛刺
2
下 料
确保板的材质,规格与图纸一致
下横梁.防护网保证尺寸误差±2mm
对角线误差不大于3mm。
确保无毛刺
3
做 大 架
严格按图纸下料,下料长度公差±10mm
宽度公差±2mm
横梁规格焊接位置与图纸一致,牵引板必须平整,且焊接牢固
保证左右纵梁平行度误差≤3mm,
垂直度误差≤2mm
变径前后纵梁平行度误差≤3mm。
制作大架后车架整体对角线误差≤5mm
所有焊缝外观美观,无焊接缺陷
所有焊接部位必须清渣打磨,不允许有飞溅
4
小件制作
按图施工,保证其尺寸及公差。
护栏不得出现扭曲.变形等缺陷。护栏支撑及支撑座焊接端正
工具箱,阀门箱要求门缝一致,其缝隙≤3mm
所有焊缝要求光滑美观,并其进行打磨处理。
沉淀杯两侧出料口要求平行一致,不得出现高低不平现象,罐体连接要求法兰与管子必须保持垂直,不得出现歪斜现象。(罐式)
所有小件上有孔的部位,一律不准使用手动火焰切割,要采用等离子 、钻、冲等工艺,保证孔无毛刺飞边。
5
侧防护
边缘离地高度≤550mm
6
后防护
边缘离地高度≤550mm
7
车架检验
车架应无明显扭曲,车架四角至地面理想水平面距离≤10mm,牵引板两侧至地面理想水平面距离≤5mm
8
制动系统
密封性
采用气压制动的机动车当气压升至600kPa且不使用制动的情况下,停止空气压缩机3min后,其气压的降低值≤10(kPa)在气压为600kPa的情况下,将制动踏板踩到底,待气压稳定后,观察3min,其气压的降低值≤30(kPa)
2
点梁
保证翼板.立板的规格型号与图纸一致,立板与翼板的宽度偏差≤2mm,对接立板和翼板时,须打坡口。
3
焊梁
焊缝要求均匀一致,焊角宽度≥8mm,补焊位置进行清渣打磨,接头位置无明显高低不平现象。不允许出现焊偏、漏焊、焊瘤现象。焊接成型后,上下翼板相对于立板均不能左右歪斜
4
调梁
大梁中间位置轻微起拱,严禁出现塌腰现象,保证两根大梁的直线度,不得有歪曲Байду номын сангаас象。
3
中、后立柱
材质符合图纸明细要求,无扭曲、歪斜现象
折边要到位,长度方向上不允许出现鼓肚,误差不超2mm。
4
前栏板
前栏板与车厢底板垂直度不能超过±1°
前栏板与前边梁及前加强板螺栓紧固牢靠,不得有松动现象。
侧栏板及后栏板外边缘应与边梁外边缘平齐,栏板应开启灵活,连接牢靠
栏板关闭后,相邻间隙及高度差不大于5mm。
目视表面无橘皮等固体粘接物
目测表面是否有混漆现象
面漆应喷湿两遍
漆膜厚度要求面漆干燥后用测厚仪测4点厚度取平均值,一般厚度>60微米以上。
漆膜光泽用光泽仪测出4点光泽度,取平均值,一般光泽为>80-90
备注
检验人:
制动系统安装及检验
型号 批号; 日期:
序号
检 验 项 目
检 验 标 准
检验结果
判 断
1
车轴、板簧装配
检 验 标 准
检验结果
判 断
1
前厢板:
总成无扭曲现象。蒙皮表面平整,没有凸凹不平现象
外形尺寸符合图纸要求,对角线长度之差不超过2mm。
2
侧、后厢板及仓栏
总成无扭曲现象。瓦楞板表面平整,没有凸凹不平现象,
沿栏板高度方向误差不超过1mm。。
外形尺寸符合图纸要求,长度误差±1mm,
对角线长度之差不超过2mm。
栏板关闭后,与边梁间隙不大于3mm,个别不大于5mm,但累计长度不大于460mm,连续长度不大于220mm
车厢应为矩形,对角线长度之差不大于10mm。
备注
检验人:
半挂车检验
支撑总成检验
型号 批号; 日期:
序号
检 验 项 目
检 验 标 准
检验结果
判 断
1
检查支腿与车架是否垂直,
最大偏差<2°
2
左右两支腿的高度尺寸是否相同
9
灯具安装及性能检查
灯光齐全,各总成、配件符合《产品配置单》《关键元器件名录》灯具表面印有3C标志的要求,安装位置符合图纸要求,外观无损伤,安装牢固,功能正常,厂家与一致性相符
10
VIN
打印位置正确在鹅颈前部、编码正确,字迹清晰
11
反光标识
符合国家标准和GA406的要求,产品有3c厂家与一致性相符
12
车轮轮辋与制动鼓的径向间隙≥3mm,两者绝对不能相碰。不允许留有污垢、毛刺杂物夹在其中。
牵引销到中桥两轴头的尺寸最大偏差不大于5mm
各轴距公差±3mm
3
安装要求
悬挂系统各螺栓要按规定力矩紧固,各螺栓按规定紧固牢靠,不得松动。要求各管接头安装时必须缠生料带,确保不会漏气
管布置美观,两相邻固定螺栓间气管的悬垂量不大于10mm
各气管无破皮及明显折弯痕迹,没有与钢结构件锐边直接接触;若无法避免接触,则必须用螺纹穿线管作局部保护;若管路需要弯曲时,则弯曲半径不得小于100mm。
,4
外观
供给管路、与驻车制动相关的管路颜色为红色;控制管路、与行车制动相关的管路颜色为黄色。红握手接头在右侧。
5
气密试验
安装完毕后向制动气路充入600Kpa压缩空气,检查各阀门、储气筒及管路接头,不得有漏气现象。非制动状态:不大于10kPa/3min;制动状态:不大于30kPa/3min。
目视工件表面应无漆皮等等固体粘接物
3
腻子
刮腻子时底漆应干燥,并再次检验工件表面是否有飞溅焊渣等物
工作表面凹凸不平处应刮腻子,不得有漏刮等现象
腻子干燥经打磨后应平整光滑
4
中途喷漆检验
喷漆应均匀,无流挂及漏喷
目测漆面无污染物
湿喷湿两遍
5
面漆
面漆喷涂应均匀完全覆盖中涂或底漆
目视喷涂应均匀无流挂漏喷等
目视表面无橘皮等固体粘接物
备注
检验人:
半挂车成品检验单
型号 批号; 日期:
序号
检验项目
检验要求
检测结果
判定
1
外廓尺寸
符合尺寸要求
2
汽车铭牌标志要求
内容齐全、字迹清晰、字高至少应为7mm,其它情况字高至少应为4mm位于车辆右侧车架前部、易于看到且能防止磨损或替换。
3
后悬
≤55%轴距,且≯
4
外观检查
油漆光亮,无流挂、麻点、虚漆及脱漆等缺陷。
备注
检验人:
悬挂组焊及铺底板检验
型号 批号; 日期:
序号
检 验 项 目
检 验 标 准
检验结果
判 断
1
悬挂点焊:
轴距误差±5mm,
每组吊耳误差≤3mm
对角线误差不大于5mm,
从牵引销中心到左右支座的误差不大于5mm。
两纵梁的下翼板是否在同一水平面上,如不在同一水平面上,最大允许偏差2mm。
各吊耳安装尺寸符合安装尺寸,不能出现混装现象。
最大偏差<5mm
3
转动手柄,
高低档,位应升降灵活,快慢档转换正常,
如果是联动支腿,则保证两支腿伸缩同步
4
支腿板与纵梁立板
要求全部满焊
焊角不小于6mm
必须加装三角加强板。严禁与纵梁下翼板横向焊接
5
支腿安装
支腿安装螺栓,不能少装,拧紧力矩为200±
支腿收起后,支腿鞋放水平后,距地面不小于320mm。
备注
纵梁总成的任意横截面上,上、下翼面对腹板的垂直度公差不大于1mm。
纵梁总成上凸允许的最大平面度误差为8-12mm。
纵梁腹板的纵向直线度公差,在任意1000mm长度内为2mm,在全长上为5mm。
备注
检验人:
车架总成检验
型号 批号; 日期:
序号
检 验 项 目
检 验 标 准