石灰石活性分析
石灰石的消融特性讲解

石灰石的活性及其影响因素
一、石灰石的活性
? 石灰石的活性常用消溶速率来表示。 ? 在颗粒度和消溶条件相同的情况下,消溶
速率大则活性高。 ? 石灰石的活性直接影响脱硫过程中SO2的
溶解、吸收和氧化反应。 ? 石灰石的消溶速率定义为单位时间内被消
溶的石灰石的量。 ? 石灰石的消溶率定义为被消溶的石灰石的
5.SO2浓度的影响
? 当大烟幅气度中增加SO。2浓度升高时,石灰石的消溶率 ? 一方面,SO2溶于水可为浆液提供H+,浆液
pH 值降低,有利于石灰石的消溶。 ? 另可反析一进应出方一生,面步成消,氧的耗化CCaaS为S2O+O,S2溶3O和使4于2C反-,水a应SS后OO向生43沉有-和成淀利S的物O于H4从石2S-与O溶灰C3液石-a,2中+
实际烟气脱硫系统中,石灰石的消溶温 度取决于消溶时所加入水的温度。
4.pH值的影响
4.pH 值的影响
? 随着pH 值的减小,石灰石的消溶率将增大。
? 在CaCO 3的消溶过程中消溶过程中要消耗 H +,使浆液呈碱性。因此,降低浆液的 pH 值将使反应向有利于石灰石溶解的方向进 行。
5.SO2浓度的影响
? 因为F-形成了复杂的络合物覆盖在石灰石 颗粒表面,从而阻碍消溶反应的进行。
8.Cl - 浓度的影响
8.Cl - 浓度的影响
? 浆液中Cl -浓度对石灰石的消溶特性有明显 的抑制作用。浆液中微量的Cl -不利于石灰 石的消溶。
? 浆液中含有微量的Cl -,即可导致石灰石消 溶率的明显下降。
9.F- 浓度的影响
9.F- 浓度的影响
? 随着浆液中的F-的增加,石灰石消溶率略 有减小。
烟气脱硫工程用石灰石活性实验

烟气脱硫工程用石灰石活性实验总结报告南京理工大学大气污染控制课题组2008年7月22日南京1任务来源与背景目前在燃煤火电厂应用的各种烟气脱硫技术中,湿法烟气脱硫(WFGD)技术最成熟,已经工业应用了几十年,是烟气脱硫的主流技术。
在WFGD中,石灰石溶解是一个重要的速率控制步骤,对系统的正常运行、脱硫效率和运行费用等起着重要作用。
要挑选合格的石灰石,除考虑其运输费用、石灰石硬度和碳酸钙含量等外,还应根据其反应活性来选择石灰石脱硫剂。
南京理工大学大气污染控制课题组与苏源环保工程股份有限公司合作,对其在烟气脱硫工程使用的1种石灰石样品进行脱硫活性筛选实验。
课题组经过近1个星期的紧张工作,现已完成了合同书要求的各项工作,现把实验结果报告如下。
2 实验2.1 实验装置及方法实验采用酸滴定法测定石灰石溶解速率。
石灰石活性测定实验装置如图1所示。
图1 实验装置示意图(1) 玻璃釜式反应器;(2) 数字式电动搅拌器;(3) pH电极;(4) 数字式pH计;(5) 酸式滴定管;(6) 温度计;(7) 超级恒温水浴用JJ-1型精密增力电动搅拌器(常州国华电器有限公司生产)控制反应转速;用501型超级恒温水浴(上海市实验仪器厂)控制反应温度为50 ℃;溶液的pH值则由意大利HANNA INSTRUMENTS公司生产的酸度计连续测量,每次实验前酸度计用该公司生产的标准缓冲溶液(缓冲溶液pH值分别为7.00、4.01)校准。
2.2石灰石脱硫剂本实验采用苏源环保公司提供的1种石灰石试样,对石灰石试样进行研磨,然后用325目筛过筛,得到试验用石灰石粉料。
采用X 荧光衍射测定石灰石试样的化学成分,结果如表1所列。
样品1 CaCO 3含量为99.29 %,SiO 2含量为0.11 %,属正常。
表1 试验用石灰石的化学成分(%)CaCO 3 MgCO 3 SiO 2 Al 2O 3 Fe 2O 3 MnO TiO 2 烧失量 P 2O 5 K 2O 样品1 99.29 0.8367 0.11 0.07 0.09 0.003 0.006 43.53 0.02 0.00 `Q3 实验结果与讨论3.1石灰石转化率的计算本实验采硫酸溶解石灰石。
石灰石_石膏湿法烟气脱硫系统石灰石活性研究
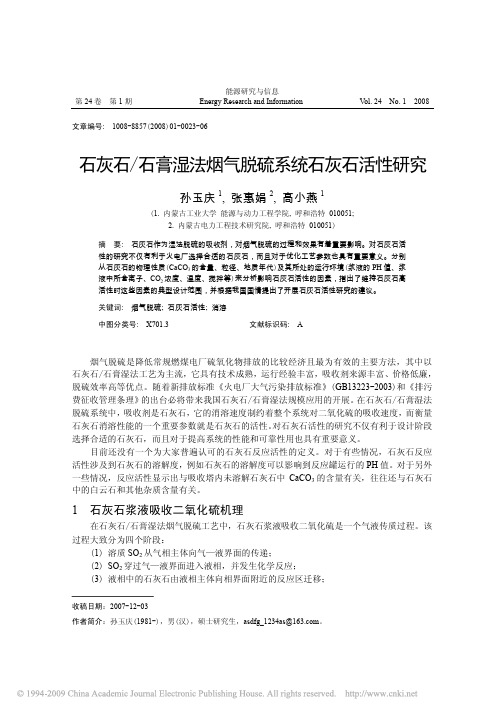
能源研究与信息第24卷 第1期 Energy Research and Information V ol. 24 No. 1 2008收稿日期:2007-12-03作者简介:孙玉庆(1981-),男(汉),硕士研究生,asdfg_1234as@ 。
文章编号: 1008-8857(2008)01-0023-06石灰石/石膏湿法烟气脱硫系统石灰石活性研究孙玉庆1, 张惠娟2, 高小燕1(1. 内蒙古工业大学 能源与动力工程学院, 呼和浩特 010051;2. 内蒙古电力工程技术研究院, 呼和浩特 010051)摘 要: 石灰石作为湿法脱硫的吸收剂,对烟气脱硫的过程和效果有着重要影响。
对石灰石活性的研究不仅有利于火电厂选择合适的石灰石,而且对于优化工艺参数也具有重要意义。
分别从石灰石的物理性质(CaCO 3的含量、粒径、地质年代)及其所处的运行环境(浆液的PH 值、浆液中所含离子、CO 2浓度、温度、搅拌等)来分析影响石灰石活性的因素,指出了维持石灰石高活性时这些因素的典型设计范围,并根据我国国情提出了开展石灰石活性研究的建议。
关键词: 烟气脱硫; 石灰石活性; 消溶中图分类号: X701.3 文献标识码: A烟气脱硫是降低常规燃煤电厂硫氧化物排放的比较经济且最为有效的主要方法,其中以石灰石/石膏湿法工艺为主流,它具有技术成熟,运行经验丰富,吸收剂来源丰富、价格低廉,脱硫效率高等优点。
随着新排放标准《火电厂大气污染排放标准》(GB13223-2003)和《排污费征收管理条理》的出台必将带来我国石灰石/石膏湿法规模应用的开展。
在石灰石/石膏湿法脱硫系统中,吸收剂是石灰石,它的消溶速度制约着整个系统对二氧化硫的吸收速度,而衡量石灰石消溶性能的一个重要参数就是石灰石的活性。
对石灰石活性的研究不仅有利于设计阶段选择合适的石灰石,而且对于提高系统的性能和可靠性用也具有重要意义。
目前还没有一个为大家普遍认可的石灰石反应活性的定义。
石灰石活性

石灰石/石膏湿法烟气脱硫系统石灰石活性研究脱硫系统一般要求CaCO3不低于90%,石灰石中往往含有少量的MgCO3,它通常以溶解形式或白云石形式存在。
在吸收塔中,白云石往往不溶解,而是随副产物离开系统。
因此含高浓度白云石的石灰石活性较低。
石灰石活性影响系统的脱硫性能及石膏的品质。
溶解石灰石为脱硫化学反应提供吸收SO2所需Ca2+及碱度,故要求活性越高越好。
1石灰石活性的研究概况石灰石/石膏湿法脱硫过程可以划分为5个阶段:(1)溶质SO2由气相主体扩散到气液两相界面气相的一侧;(2)SO2在相界面上的溶解,并转入液相;(3)SO2电离,同时剩余的SO2由液相界面扩散到液相主体;(4)石灰石的溶解、电离与扩散;(5)反应产物向液相主体的扩散及反应产物沉淀的生成。
5个阶段是同时进行的。
步骤2、3、5是快速离子反应,由化学动力学可知总化学反应速率由步骤1和4即气相中SO2的扩散(气相阻力,如式1~4所示)和石灰石固体的液相溶解(液相阻力,如式5~6所示)决定的。
降低液相阻力可以提高化学反应速率,进而提高整体系统性能,对于石灰石活性的研究都是从降低石灰石溶解的液相阻力入手的。
1.1国外石灰石活性研究情况1.1.1石灰石物理性质对活性的影响石灰石中主要有效成分是CaCO3,因此石灰石中CaCO3的含量对活性有重要影响。
石灰石中CaCO3含量越高,其活性越大。
由于白云石(MgCO3·CaCO3)比方解石(CaCO3)的溶解速率低3~l0倍,当石灰石纯度较低(CaCO3含量<85%wt)或者要求对石灰石要有较高的利用率时,白云石等杂质会大大降低石灰石的溶解。
MgCO3含量过高时,还容易产生大量可溶的MgSO3,减小SO2气相扩散的化学反应推动力,严重影响石灰石化学活性,因此设计时对石灰石中CaCO3含量一般要求高于90%。
石灰石粒径越小,比表面积越大,液固接触越充分,从而能有效降低液相阻力,故石灰石活性就越好,Chart和Rochelle1采用定pH值滴定法研究石灰石溶解特性,发现石灰石溶解速率是溶液组成、粒径分布的函数,与其表面粗糙度等无关。
第一章石灰石化学分析
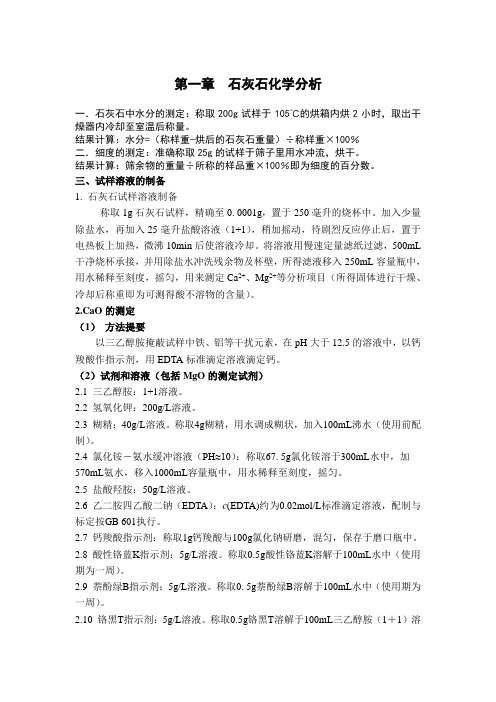
第一章石灰石化学分析一.石灰石中水分的测定:称取200g试样于105℃的烘箱内烘2小时,取出干燥器内冷却至室温后称量。
结果计算:水分=(称样重-烘后的石灰石重量)÷称样重×100%二.细度的测定:准确称取25g的试样于筛子里用水冲流,烘干。
结果计算:筛余物的重量÷所称的样品重×100%即为细度的百分数。
三、试样溶液的制备1. 石灰石试样溶液制备称取1g石灰石试样,精确至0. 0001g,置于250毫升的烧杯中。
加入少量除盐水,再加入25毫升盐酸溶液(1+1),稍加摇动,待剧烈反应停止后,置于电热板上加热,微沸10min后使溶液冷却。
将溶液用慢速定量滤纸过滤,500mL 干净烧杯承接,并用除盐水冲洗残余物及杯壁,所得滤液移入250mL容量瓶中,用水稀释至刻度,摇匀,用来测定Ca2+、Mg2+等分析项目(所得固体进行干燥、冷却后称重即为可测得酸不溶物的含量)。
2.CaO的测定(1)方法提要以三乙醇胺掩蔽试样中铁、铝等干扰元素,在pH大于12.5的溶液中,以钙羧酸作指示剂,用EDTA标准滴定溶液滴定钙。
(2)试剂和溶液(包括MgO的测定试剂)2.1 三乙醇胺:1+1溶液。
2.2 氢氧化钾:200g/L溶液。
2.3 糊精:40g/L溶液。
称取4g糊精,用水调成糊状,加入100mL沸水(使用前配制)。
2.4 氯化铵-氨水缓冲溶液(PH≈10):称取67. 5g氯化铵溶于300mL水中,加570mL氨水,移入1000mL容量瓶中,用水稀释至刻度,摇匀。
2.5 盐酸羟胺:50g/L溶液。
2.6 乙二胺四乙酸二钠(EDTA):c(EDTA)约为0.02mol/L标准滴定溶液,配制与标定按GB 601执行。
2.7 钙羧酸指示剂:称取1g钙羧酸与100g氯化钠研磨,混匀,保存于磨口瓶中。
2.8 酸性铬蓝K指示剂:5g/L溶液。
称取0.5g酸性铬蓝K溶解于100mL水中(使用期为一周)。
石灰活性度生过烧关系的探究

石灰活性度生过烧关系的探究摘要:石灰的质量指标主要有氧化钙、活性度、生过烧。
而在此所提到的氧化钙是石灰的总氧化钙,既包含石灰生烧所含的氧化钙也包括石灰过烧的氧化钙。
而生烧的氧化钙是没有活性的,实验室所出具的氧化钙指标为总氧化钙,不论是国标的化学分析方法还是荧光分析方法所测得均为总氧化钙。
总氧化钙中只有一部分氧化钙能与水发生消化反应,而这部分氧化钙称之为活性氧化钙或有效氧化钙。
关键词:石灰活性度生过烧总钙活性氧化钙1前言石灰的用途广泛,而在钢铁企业中石灰的质量等级,直接影响到炼钢的生产。
所以掌握石灰的质量等级尤为重要。
我们一般通过对石灰的氧化钙、活性度、生过烧进行检测。
从而了解石灰的质量。
一般在煅烧过程中要求对石灰石造块儿,要求其具有一定的规格。
而在造块儿过程中,不可能保证所有进入石灰窑的石灰石块儿都符合煅烧要求,从而造成了石灰石粒径大的石灰石没有烧透形成生烧。
粒径小的石灰石在石灰窑中煅烧过渡形成过烧[1]。
而生烧和过烧的石灰是没有活性的。
在我们所出具的石灰数据中,氧化钙包含了生烧和过烧氧化钙。
造成了报出的氧化钙数据比实际活性氧化钙偏高的现象。
也出现了和生过烧相关的数据解释不明的原因。
本文提出的活性氧化钙理论计算,简明的阐述了二者的关系,对石灰质量有了更直观的了解,也解释了上述总钙和生过烧的矛盾关系。
2总氧化钙和活性氧化钙的关系2.1 活性度的检测方法:活性度的具体做法是称取粒径为1.5mm--6mm50g石灰,在3000ml的烧杯放入2000ml的42±1摄氏度的水,加7-8酚酞指示剂(1%)。
用搅拌器开到250-300r/min搅拌。
用4mol/L的盐酸滴定使试样一致保持粉红色,读出其十分钟所消耗的盐酸量,则为活性度。
2.2 活性度检测原理石灰的主要成分是氧化钙,氧化钙遇水后生成氢氧化钙,氢氧化钙在与4mol/L的盐酸反应,生成氯化钙。
在检测过程中生烧石灰是不与盐酸反应的,已经通过实验证实,活性度检测原理的具体反应方程式如下:CaO + H2O = Ca(OH)2Ca(OH)2 + 2HCl =CaCl2 + 2H2O在石灰消化以后,实际上就是一个以酚酞为指示剂的酸碱中和滴定,当溶液变为乳白色时说明达到终点。
小粒度石灰石煅烧活性石灰研究

小粒度石灰石煅烧活性石灰研究石灰回转窑煅烧工艺对石灰石入窑粒度有着严格的要求,一般石灰石粒度比不宜大于3。
酒钢西沟矿供我公司石灰石粒度为10~65mm,石灰石粒度比大,如直接入窑煅烧,在煅炼过程中容易造成物料偏析,破坏物料塌落式运动轨迹;碎料被包裹在中间或和压在料层低端,影响分解速度,石灰石分解率下降,成品率降低[1];煅烧出的石灰中粉灰多,0~10mm 的粉灰占比20%~25%,石灰CaO 含量下降,不仅影响炼钢灰质量,还造成原料浪费。
为此,我们进行了小粒度石灰石煅烧试验,并在此基础上提出了三级筛分、分级煅烧的工艺方案。
一、煅烧试验试验采用西沟矿10~65mm 石灰石筛下10~20mm小粒度石灰石,其化学成分:CaO含量53%,MgO含量1.1%,SiO2含量1.3%。
(一)试验方法试验在马弗炉内进行,通过温度控制,在马弗炉内放入一定量的10~20mm 石灰石。
一般温度取1000℃、1050℃、1100℃、1150℃,煅烧时间取80min、120min、160min。
(二)试验结果及分析也随之由低到高;当温度达到1050℃并持续升高时,石灰活性度又呈下降趋势。
因此,最佳的煅烧温度在1000~1150 ℃之间,煅烧时间控制在2~2.3h,在此煅烧条件下生产出的石灰质量好、生烧率低、活性度能达到290ml 以上,完全能够满足烧结厂和炼钢厂使用要求。
试验结果表明,回转窑煅烧小粒度石灰石,进而实行石灰石分级煅烧的工艺方案是可行的。
二、原料预处理系统设备及预热器改造方案(一)原料预处理系统设备改造目前我公司上料系统配套有3台滚筒筛,滚筒筛无法实现分级筛分,故需要将滚筒筛分系统改为分级振动筛分系统。
在筛分设备的选型上,建议选择具备三级筛分效果的分级筛,将10mm以下粉料筛下入石灰石粉地仓,供烧结制粉用,10~20mm的入原料专用地仓,20~65mm 石灰石入原料专用地仓。
同时,配套安装相应的辅助设备及单机除尘、收尘管道等环保设施。
白云石、石灰石的检测分析

白云石、石灰石的全分析灼烧减量的测定一、分析方法称取干燥的试样0.25g于已恒重的瓷坩埚中,置于960度的马沸炉中灼烧1小时,取出在干燥器中冷却至室温,称重二、计算:%=(G-G1)/G*100%式中G----为干燥后试样重即0.25gG1---为烧后试样重 g三、注意事项1 温度一般为960度,时间白灰1小时,石灰石1.5小时二氧化硅的测定一、试剂:1 盐酸 1+12 动物胶 0.4%(又叫明胶)3 硝酸比重1.42的浓硝酸二、分析方法:将灼烧后的试样置于有柄瓷坩埚中,加1+1的盐酸25ml;于电热板上加热溶解,待试样完全溶解后加入1-2滴浓硝酸继续加热至体积为8-10毫升取下冷却至50-60度时,(约1分钟)加入0.4%的动物胶溶液10毫升,搅拌均匀后静止1分钟,加20毫升热蒸馏水,然后搅拌5分钟,至于电热板低温处保温15分钟取下,用热水冲洗表面皿及瓷坩埚,以快速滤纸过滤(滤前加纸浆),于400ml烧杯中,沉淀用5%的热盐酸洗涤4—5次,再用热水洗5—6次(即洗到无氯离子为止).1 将滤液作为测定R2O3的母液,如果不测R2O3,此滤液则作为测定CaO,MgO的母液.2 将沉淀连同滤纸放在瓷坩埚中灰化,然后在1000+_50度的马费炉内灼烧30分钟,取出冷却至室温后立即称重.三、计算:SiO2%=G1/G*100%式中:G1-----为沉淀重量,gG------为试样重量,即0.25g;四、注意事项:1 加入动物胶后搅拌时间必须充分,否则结果偏低.2 沉淀必须先灰化,直接灼烧易生成碳化硅.三氧化二物的测定一、试剂:1 氨水(NH4OH):比重0.9的浓氨水;2 氯化铵(NH4CL):20%,2%;二、分析方法:将测定SiO2后的母液稀释至150ml,加入20%的氯化铵20ml,用氨水中和至略有氨味后,再过量3—4滴(此时溶液的PH值=8-9),加热至沸,并至于电热板上保温至沉淀凝聚后取下,以快速滤纸(加纸浆)过滤,沉淀用2%的氯化铵溶液洗涤5-6次.1 滤液作为测定CaO,MgO的母液;2 将沉淀连同滤纸放在瓷坩埚中灰化,然后在960度的马费炉中灼烧30分钟取出,冷却至室温后立即称重.三、计算:R203=G2/G*100%式中:G2---为沉淀重量,g;G----为试样重量,g;即0.25g;氧化钙的测定一、试剂:1、氢氧化钾溶液:20%2、钙试剂:1克钙试剂与100克氯化钾研细混匀;3、EDTA标准溶液:0.01783M;4、三乙醇胺溶液:1+1;二、分析方法:吸取母液50ml,与200ml烧杯中,加盐酸羟胺0.1克,三乙醇胺10ml,氢氧化钾25ml,钙试剂约0.1克,搅拌均匀后,用0.01783M的EDTA标准溶液滴定,至溶液由粉红色变为兰色即为终点,记录所消耗EDTA标准溶液的毫升数V.三、计算:CAO%=(V*M*0.05608)/(G/5)*100%式中:V------所消耗EDTA标准溶液的毫升数,ml;M-----为EDTA标准溶液的浓度,0.01783M;0.05608------CAO毫摩尔质量G-----试样重量,即0.25克;氧化镁的测定一、试剂:1、氨水:比重0.90的浓氨水;2、镁试剂:1克铬黑T与100克氯化钾研细混匀;3、EDTA标准溶液:0.01783M;4、三乙醇胺溶液:1+1;5、氯化铵溶液:20%;二、分析方法:吸取母液50ml于200ml烧杯中,加盐酸羟胺0.1克,三乙醇胺10ml,加入氯化铵溶液(20%)5ml,氨水(密度为0.90g/ml)15ml,镁指示剂0.1克,搅拌均匀后,用EDTA标准溶液滴定至兰色为终点,记录所消耗EDTA标准溶液的毫升数V1.三、计算:MgO=(V1-V)*M*0.04032/(G/5)*100%式中:V1----为滴定钙镁时所消耗的EDTA标准溶液的毫升数ml;V-----为滴定钙时所消耗的EDTA标准溶液的毫升数ml;M-----为EDTA标准溶液的浓度,0.01783M;0.04032---为氧化镁的毫摩尔质量;G------为试样重量,即0.25克;活性度的测定一、试剂:1、0.1%的酚酞溶液(称取0.1克酚酞与100ml无水乙醇溶解)2、4M的盐酸(833ml的浓盐酸与1667ml的蒸馏水混匀,配成2500ml4M的盐酸)二、分析方法:取1000ml40度的水,加0.1%的酚酞试剂7—8滴,开动搅拌限时10分钟,把称好的试样(25克粒度大于1mm小于3mm)倒入烧杯中,用4M的盐酸中和溶液的红颜色,时间到后,记录所用盐酸的毫升数.三、计算:盐酸的毫升数*2。
- 1、下载文档前请自行甄别文档内容的完整性,平台不提供额外的编辑、内容补充、找答案等附加服务。
- 2、"仅部分预览"的文档,不可在线预览部分如存在完整性等问题,可反馈申请退款(可完整预览的文档不适用该条件!)。
- 3、如文档侵犯您的权益,请联系客服反馈,我们会尽快为您处理(人工客服工作时间:9:00-18:30)。
循环流化床锅炉干法加钙脱硫用石灰石反应活性
对脱硫效率的影响
新浦化学(泰兴)有限公司 羊文君
【摘要】:简要说明循环流化床锅炉炉内脱硫机理,分析两种矿石粉在循环流化床锅炉加钙脱硫实际运行中对脱硫效率的影响;从两种矿石粉各自物理化学特性浅析用于循环流化床锅炉脱硫优劣做出评价,对提高脱硫效率提出建议。
【关键词】:循环流化床锅炉;石灰石;脱硫;镇江船山;浙江长兴。
1、石灰石脱硫原理与影响脱硫效率的因素: 1.1 脱硫原理
循环流化床锅炉炉内脱硫是采用石灰石干法脱硫来实现的,即:将进入炉膛内的CaCO3高温煅烧分解成CaO,与烟气中的SO2发生反应生成CaSO4,随炉渣排出,从而达到脱硫目的。
石灰石脱硫过程主要分为以下三步:
1.1.1 石灰石煅烧:在常压流化床锅炉中石灰石中的CaCO3遇热煅烧分解为CaO煅烧析出CO2时,会生成并扩大CaO中的孔隙,增加其表面积,为下步的固硫反应奠定基础。
反应方程:
CaCO3→CaO +CO2
1.1.2 硫的析出与氧化:煤中的硫主要以黄铁矿、有机盐、和硫酸盐三种形式存在,有关试验表明,煤在加热并燃烧时,SO2的析出呈现明显的阶段性,黄铁矿燃烧氧化后生成SO2,有机硫在200℃分解并释放出H2S、硫醚、硫醇等,这些物质氧化后都生成SO2。
反应方
程:S+O2=SO2
1.1.3 硫的固化反应:SO2与O2克服外部的扩散阻力,到达氧化钙的表面,并扩散到微孔中,吸附在微孔的表面,最终反应生成CaSO4,以达到脱硫的效果。
反应方程:
CaO + SO2 + 1/2O2 →CaSO4
这是一个比较复杂的,涉及到反应气体在多孔氧化钙及产物层硫酸钙内扩散的复杂反应。
2、石灰石反应活性对脱硫效率的影响
2.1 石灰石反应活性:主要表现为石灰石煅烧后生成空隙的大小、分布及比表面积等。
不同石灰石的反应活性差别主要在于煅烧后微孔的结构不同,对脱硫反应来说, 直径大的孔隙有利于硫固化反应的快速进行,孔隙越小则产生扩散阻力越大,不利于脱硫反应进行,微孔很容易被CaSO4堵塞,其表面利用率更低,所使用的石灰石固有的反应活性在对炉内脱硫效率起决定性的作用。
2.2 此外,石灰石所含杂质的影响:有些杂质的存在会对石灰石的转化率产生影响,使CaO颗粒在固硫过程中孔隙被堵塞的时间推
迟,因而可以提高CaO颗粒的利用率;同样有些杂质的存在降低了石灰石的耐煅烧性,高温下CaO表面的空隙减少甚至是被烧结,比表面急剧下降,使固硫反应很难进行下去,极大程度的降低了脱硫效率。
3、试验
3.1 原材料来自镇江船山和浙江长兴两处矿石粉,为了便于比较两处石粉各项物理化学指标,均采用75微米中位粒径作为试验对象,常规分析项目见下(表 1):
H2O% CaCO3% LOI%/850℃ LOI%/950℃
镇江船山 0.38 92.94 39.99 41.53
浙江长兴 0.34 96.50 42.54 42.65 LOI%/850℃:850℃煅烧后烧失量
(表 1)
浙江长兴矿石粉钙含量高于镇江船山矿石粉,两种矿石粉在950℃下烧失量比较极近,且接近于理论值(44%),表明两种石灰石在公司当前流化床密相区温度维持950℃的运行条件下均能够有效的分解,脱硫效率则取决于分解后CaO表面的孔隙特性以及比表面积的大小,通过高压电子束扫描成像仪对样品扫描和拍照,以及对样品的比表面积进行测量,综合分析两种石灰石的反应活性,850℃和950℃煅烧后比表面积的数据(表2):
m2/g 850℃ m2/g 950℃
镇江船山 6.119 2.077
浙江长兴 10.215 8.265
(表2)
石灰石在高于770℃时开始逐步分解,在850℃附近为最佳反应温度,当温度高于900℃CaCO3晶体有部分被烧结,使孔结构减小,甚至消失,温度越高这种孔隙的烧结现象越来越严重,SO2向孔隙内部扩散变得比较困难,脱硫效率也随之急剧下降,由(表2)看出镇江船山矿石粉在高温下的烧结现象尤为严重,通过950
℃下扫描图片也能得出同样的结论:
镇江船山(图1)
浙江长兴(图2)
长兴矿石粉在同等单位质量下,能够提供高出船山矿石粉4倍之多的比表面积,但并不
意味着脱硫效率也会有同等倍率的提高,因为单位质量同等粒度样品比表面积越高则说明其微孔分布相对较广,孔直径也相对偏小,小孔径容易造成CaSO4在入口处产生堵塞,降低石灰石的利用率。
4、其他影响脱硫效率的因素:
4.1 温度对脱硫效率的影响分析
循环流化床底部的密相区处于“氧化―还原”气氛的不断更迭状态中, 并有80%左右的时间内处于还原性气氛,这主要是由于煤碳在燃烧初期产生较多的CO,以及煤的挥发分在密相区析出时产生还原性气体,CO、H2不能在密相区完全燃烧所致。
脱硫反应会有各种不同的途径和产物,在密相区还原性气氛下,可出现以下的反应:
CaSO4 +CO →CaO + SO2 + CO2
CaSO4 +4CO→CaS + 4CO2
密相区内形成的CaS在进入稀相区后与氧发生分解:
CaS +1.5 O2→SO2+CaO
尤其是在床温大于850℃时候,CaS的分解将加剧,释放出已经捕集到的SO2。
当密相区温度达到900℃以上时候,CaO孔结构被烧结,阻止SO2和O2向CaO内部扩散,使脱硫效率降低;同时,CaSO4在密相区内将发生分解反应,再次将SO2释放出来:
CaSO4 +CO →CaO + SO2 + CO2
根据当前公司流化床运行的实际情况,密相区内温度正常维持在950℃左右,该床温下的钙的利用率很低,(图3)反应了脱硫效率与床温的关系:
(图3)
4.2 Ca/S比:
在CaO与SO2 结合生成CaCO3 过程中,分子
明显加大,会堵塞气体分子进入多孔的石灰石
颗粒中的内层通道,阻碍脱硫反应进行。
因此,
加入锅炉中的石灰石不可能全部用于脱硫,在
实际生产运行中投入的钙硫比要大于理论钙
硫比,(图4)反应了Ca/S比与脱硫效率的关
系:
(图4)
4.3 石灰石的粒径分布
石灰石粒径分布对床内脱琉反应工况具有较大的影响。
较小的颗粒容易从分离器中逃逸不被捕捉送回炉膛充分利用。
CaO与SO2反应后在石灰石颗粒表面形成CaSO4,致密的CaSO4层将阻止SO2向 CaO内部扩散。
所以,石灰石颗粒越大,其相对孔容积和比表面积也越小,CaO 的有效利用率也下降。
4、结论:
实验表明:浙江长兴矿石粉含量高于镇江船山矿石粉,具有较好的耐煅烧性,在循环流化床锅炉炉内脱硫的应用中能够提供更广的反应接触面,公司CFB正常运行床温维持在950℃附近,镇江船山矿石粉在该温度下烧结现象严重,反应活性较弱。
相比之下,浙江长兴矿石粉更适用于干法炉内脱硫。
炉内喷钙脱硫反应复杂,对于锅炉燃烧工况要求较高,在Ca/S、床温、燃煤粒度、石灰石粒径分布控制良好时,脱硫效率仍然可以取得比较满意的结果。
但CFB稳定经济运行下的各项工况参数与最佳脱硫条件并不完全相符,这些影响脱硫效率因素的存在极大程度的降低了CFB锅炉的稳定脱硫效率。
根据煤灰残留活性氧化钙含量,2011年1-6月份,粉煤灰中CaO含量平均水平维持在7%左右,这部分CaO主要是由旋风分离器带出,单由粉煤灰产量推算,年累计约折合1.2万吨石灰石没有经过脱硫利用就进入灰库,综合评估全年石灰石利用率不到60%。
所以,我个人认为当前的石粉粒径要求(尤其是切割粒径)需要从有利于提高脱硫效率的角度重新加以检讨,至少要让目前的石粉浪费现象首先得到改观。
【参考文献】
[1] 赵长遂:《循环流化床锅炉炉内脱硫效率控制因素分析》。
[2] 金定安、曹子栋、俞建洪:《业锅炉原理》西安交通大学。
[3] 赵大传、徐俊贤:《行业环境学概论》中国环境科学出版社。
[4] 朱凯强、芮新红:《循环流化床锅炉设备及系统》北京:中国电力出版社
[5] 周丽:《循环流化床锅炉脱硫效率的控制能源技术与管理》
[6] 周一工:《循环流化床锅炉石灰石脱琉系统的设计初探》黑龙江电力。
[7] 史学锋、冯波:《流化床煤燃烧中的脱硫研究综述》电站系统工程
[8] 张 君、靳宗伟、刘 桐:《循环流化床锅炉炉内脱硫原理与因素分析》。