直缝埋弧焊钢管技术标准
GB9711.1与GB9711.2对比

尺寸 重量 公差
试验 /检 验
化学分析报告 购方检查 记录的保存 化学成分试验:1 元素分析、2 熔炼分析、3 产品分析。 力学性能和工艺性能试验:1 拉伸试验、2 电阻焊和连续炉焊钢管的压扁试验、弯曲试 验、埋弧焊和熔化极气体保护电弧焊焊缝工艺性能试验、焊接接头延性试验、断裂韧性 试验 静水压试验 尺寸检验及称重 外观检查. 无损检验 复验:1 化学分析、 2 拉伸试验、3 压扁试验、4 弯曲试验、5 导向弯曲试验、6 焊缝 1 元素分析 每一次要求分析的元素至少应包括碳、锰、磷、硫和硅;在炼钢时添加的妮、钒、钦 或其任一组合应进行分析;以及在炼钢时添加的用于脱氧之外的其它合金元素也应进行分 析 2 熔炼分析 钢厂应测定用于制造购方订货合同规定钢管的每熔炼批钢的化学成分。化学成分的 测定应符合7.2.1的要求。对L555级钢,熔炼分析的范围未作规定,仅规定了产品分析范 围。 3 产品分析 3 . 1 取样频数 按本标准要求,制造钢管用的每熔炼批钢,制造厂应取两个试样进行分析。 3 . 2 取样方法 无缝钢管:由制造厂选择,产品分析用试样既可以从拉伸试样上截取,也可从成品 钢管上截取。 焊接钢管:由制造厂选择,产品分析用试样既可以从成品钢管、钢板、钢带、拉伸 试样上截取也可从压扁试样上截取。对直缝焊钢管,取样位置应至少与焊缝成900 。对 螺旋焊管. 取样位置与焊缝之间的距离,从任一焊缝边缘测量,均不得小于相邻螺旋焊 缝之间距离的四分之一。对于用钢板或钢带制造的钢管,只要取样频数符合本标准的要 求,则产品分析可由钢板或钢带的供应商进行。 1.试验频数 1 . 1 拉伸试验 1 . 2 电阻焊和连续炉焊钢管的压扁试验 1 . 3 弯曲试验 1 . 4 埋弧焊和熔化极气体保护电弧焊焊缝工艺性能试验 1 . 5 焊接接头延性试验 1 . 6 断裂韧性试验( 批量的定义见附录D ( 标准的附录) S R 3 和S R 4 ) 1 . 6 . 1 对L 5 5 5 级钢管, 每次试验应从每熔炼批钢中或从每批钢管中抽一根钢管 各截取三个试样, 分别测定剪切面积百分率和冲击吸收功。 1 . 6 . 2 对所有直径的L 5 5 5 级焊接钢管, 应从订货合同提供的每熔炼批钢中抽一 根钢管, 在该钢管上截取二个试样进行落锤撕裂试验。 1 . 7 金相检验
焊接钢管国家执行标准
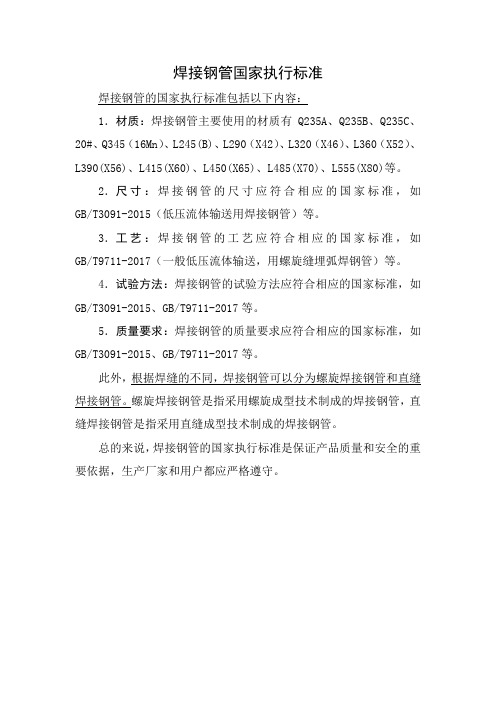
焊接钢管国家执行标准
焊接钢管的国家执行标准包括以下内容:
1.材质:焊接钢管主要使用的材质有Q235A、Q235B、Q235C、20#、Q345(16Mn)、L245(B)、L290(X42)、L320(X46)、L360(X52)、L390(X56)、L415(X60)、L450(X65)、L485(X70)、L555(X80)等。
2.尺寸:焊接钢管的尺寸应符合相应的国家标准,如GB/T3091-2015(低压流体输送用焊接钢管)等。
3.工艺:焊接钢管的工艺应符合相应的国家标准,如GB/T9711-2017(一般低压流体输送,用螺旋缝埋弧焊钢管)等。
4.试验方法:焊接钢管的试验方法应符合相应的国家标准,如GB/T3091-2015、GB/T9711-2017等。
5.质量要求:焊接钢管的质量要求应符合相应的国家标准,如GB/T3091-2015、GB/T9711-2017等。
此外,根据焊缝的不同,焊接钢管可以分为螺旋焊接钢管和直缝焊接钢管。
螺旋焊接钢管是指采用螺旋成型技术制成的焊接钢管,直缝焊接钢管是指采用直缝成型技术制成的焊接钢管。
总的来说,焊接钢管的国家执行标准是保证产品质量和安全的重要依据,生产厂家和用户都应严格遵守。
直缝电焊钢管最新标准

直缝电焊钢管最新标准直缝电焊钢管是一种常见的管材,广泛应用于建筑、石油、化工、电力、船舶等领域。
为了确保直缝电焊钢管的质量和安全,制定了一系列的标准,以规范其生产和使用。
本文将介绍直缝电焊钢管的最新标准,以便相关行业人士了解并遵守相关规定。
首先,直缝电焊钢管的最新标准主要包括以下几个方面,材料、制造工艺、质量控制、尺寸和允许偏差、外观和表面质量、试验方法等。
其中,材料是直缝电焊钢管质量的基础,制造工艺和质量控制是保证管材质量稳定的关键,尺寸和允许偏差、外观和表面质量则是直缝电焊钢管在使用过程中的重要指标,而试验方法则是验证管材质量的手段。
这些标准的制定和执行,对于保障直缝电焊钢管的质量和安全具有重要意义。
其次,直缝电焊钢管的最新标准在材料方面,要求使用优质的钢材作为原料,严格控制化学成分和机械性能,确保管材的强度和耐腐蚀性能。
在制造工艺和质量控制方面,要求严格执行相关工艺规程,加强生产过程中的质量管理,确保管材的生产工艺稳定可靠。
在尺寸和允许偏差、外观和表面质量方面,要求严格按照标准规定进行检测和评定,确保管材的尺寸精度和表面质量符合要求。
在试验方法方面,要求采用科学、严谨的试验方法对管材进行全面、系统的检测,确保管材的质量达到标准要求。
最后,为了确保直缝电焊钢管的质量和安全,相关行业人士应严格遵守直缝电焊钢管的最新标准,加强对管材质量的监督和管理,提高管材的质量和安全水平。
同时,生产企业应加强内部管理,完善质量控制体系,提高生产工艺水平,确保管材的质量稳定可靠。
使用单位应加强对管材质量的检验和验收,确保使用的管材符合标准要求,提高工程质量和安全水平。
总之,直缝电焊钢管的最新标准对于保障管材的质量和安全具有重要意义,相关行业人士应加强对标准的学习和执行,共同提高管材的质量和安全水平,推动行业的健康发展。
希望本文能够帮助相关行业人士更好地了解和遵守直缝电焊钢管的最新标准,促进行业的良性发展。
直缝埋弧焊钢管的选用

长庆气田集气干线(457)运行压力较高,考虑国内外制管水平,目前硫化氢气田管材使用现状,以及世界范围内天然气管道工业向高强度、高韧性管材发展的趋势,设计选用了进口X25直缝双面埋弧焊钢管(UOE)。
(3)加拿大S AS W钢管与LSAW钢管处于同等地位,在主干线上实际使用sSA w钢管的数量占70%左右。其主要原因是加拿大拥有SSAw钢管生产企业,在改进制造工艺后,使其生产的sswA钢管质量和性能达到UOE直缝管的水平。
(4)大量的钢管爆破实验表明,爆破点多数不在焊缝区,因此焊缝避开主应力方向而具有的优点已无多大意义。
按照DBJ08一65一97上海市标准“城市天然气管道工程技术规程”,该规程只适用于输送压力P不大于1.6 MaP(表压)的天然气管道工程。由于西气进入上海的压力将远高于1.6 PMa,同时上海的一些天然气大用户用气压力的要求也将远高于1.6 PMa的压力,因此上海天然气高压输气管网的运行压力必须考虑大于1.6 MaP。此外,由于天然气用户的发展,上海天然气的使用量在近期的目标值是每年30 x l沪扩,远期目标要超过每年5000000000立方m”。如此大量天然气的输送,必然提出要采用大于1.6 MPa压力的输气管网,选用较小口径的管道以减少建设所需的投资。由此可见,更高压力下运行的输气管网对其安全性提出了更高的要求,因而对管材的要求也相应更为严格。 天然气高压输气管的管材目前有:无缝钢管、螺旋埋弧焊钢管(Spirally Submerged Arc Welding,缩写SSAW)、电阻焊直缝钢管(Electric Resistane Welding,缩写ERW)和直缝埋弧焊钢管(Long itudinally submerged Arc welding只,缩写SLAW)。LSAW钢管按其制造工艺的不同而分为UOE管(U成型、O成型和整体扩径)、JCOE管J(成型、C成型、O成型和整体扩径)、RBE(三辊机上往复滚压成型、整体扩径)、PFP(渐进型模压成型法成型、整体扩径)等品种。由于无缝钢管和ERw钢管尺寸的限制,主输气干线的管径较大,主要采用LS AW钢管和SSAW钢管,国内外均有不同的看法,因此本文在收集近年来的国内外资料的基础上,进行客观的综述和建议,供有关领导和专家参考。
直缝埋弧焊钢管技术标准
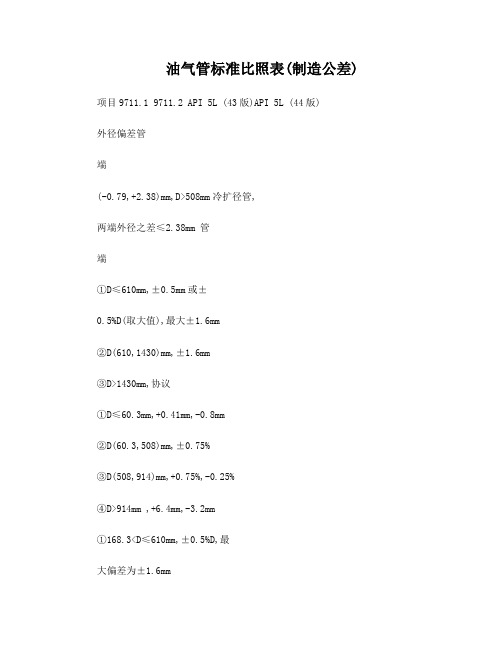
体
管
体
①D≤610mm,±0.75%D最大
±3mm
②D(610,1430】mm,±0.5%D,
最大±4mm
③D>1430mm,协议
①D≤273mm,+ 1.6mm,-0.4mm
②D(273,508)mm,+2.4mm,
-0.8mm
③D(508,1066)mm,+2.4mm,
-0.8mm
④D>1066mm ,+2.4mm,-0.8mm
有毛刺,且为清除管段内毛刺形成
的内锥角≤7°。
对接允许,两直缝应间隔(51~203)mm,焊缝余高≤3.18mm(埋弧焊)
焊缝余高3.18mm(T≤12.7);4.76mm(T>12.7)T≤15mm,内外焊缝≤3mm
T>15mm,内焊缝≤3mm,外焊缝
≤4mm T≤12.7mm,内外焊缝≤3.18mm
T>12.7mm ,内外焊缝≤4.76mm
T≤13.0mm,内外焊缝≤3.5mm
T>13mm,内焊缝≤3.5mm,外焊缝
≤4.5mm
水压试验①(L210和L245):75%,最大压力19.3MPa
②(L290~L555):85%(D≤457)、90%(D≥508)
最大压力20.7MPa①50MPa ,对外径D≤406.4mm
②L175、L175P、A25、A25P,
(+10.0% ,-5.0%)
③其他,(+10.0% ,-3.5%)
管端(30°~35°),钝边:1.59mm±0.79mm,管端切斜≤1.59mm,内锥角≤7°(8小时工
作班检验3次)。距管端101.6mm,内焊缝余
低压流体输送用焊接钢管材料标准

管体外径允许偏差
正负0.5 正负1%D 正负0.75%D 正负1%D或正负10, 两者取较小值。
管端外径允许偏差 —— —— 正2.4负0.8 正3.2负0.8
壁厚(t)允许偏差 正负10%的壁厚
03 尺寸、外形和重量
长度
• 1、通常长度 • 钢管的通常长度应为3000mm到12000mm • 2、定尺长度 • 钢管的定尺长度在通常长度范围内,直缝高频电焊
03 尺寸、外形和重量
03 尺寸、外形和重量
直径和壁厚 长度
弯曲度
不圆度 管端 重量
03 尺寸、外形和重量
公称口径 外径D系列1
直径和壁厚
外径D系列2 外径D系列3 最小公称壁厚t 不圆度不大于
15
21.3
20.8
-
2.2
0.3
20
26.9
26
-
2.2
0.35
25
33.7
33
32.5
2.5
0.4
低压流体输送用焊接钢管
GB/T3091-2015
2015-9-11发布 2016-6-1实施
目录 CONTENTS
01 范围 02 订货内容 03 尺寸、外形和重量 04 表面质量
05 钢管标志
01 范围
01 范围
A 本标准规定了低压流体
输送用焊接钢管的尺寸、 外形、重量、技术要求、 实验方法、检验规则、 包装、标志及质量证明 书。
08 弯曲度
08 弯曲度
弯曲度
• 管材弯曲度应不大于0.5%。
09 标志、运输和贮存
09 标志、运输和贮存
标志
• 每根管材上应含有至少一处完整标志,标志间距应 不大于2m,且管材上至少应有下列永久性标志:
双面埋弧焊直缝钢管订货技术条件
双面埋弧焊直缝钢管订货技术条件1.钢管名称:双面埋弧焊直缝钢管(SAWL)。
2.执行标准:GB/T3091-2008。
3.材质:Q345B且保证管材的热处理状态为正火+高温回火。
4.供货的机械性能与化学成分:机械性能和化学成分应符合低合金结构钢-GB/T1591-1994的要求,其中常温冲击功不小于34J。
5.直径、壁厚与偏差:(附订货清单)外径的偏差±0.75D;管端的直径偏差+2.4/-0.8;壁厚偏差:不大于公称壁厚*10%;管端不圆度:(直径大于400)不大于2.5mm;弯曲度:全长不大于2.5mm;坡口:壁厚大于25mm加工组合坡口,壁厚不大于25mm不开坡口。
订货清单6.长度:定尺长度12米,长度偏差0-50mm。
7.焊缝焊缝符合JGJ81-2002中1级的要求。
8.材料复验8.1钢材进场进行化学成分与机械性能的复验,复验在甲方派员监督下进行。
8.2复验按照炉批号进行,每一个检验批的管子重量不宜大于60吨,不同规格的管子不宜混为一个检验批。
8.3钢管出厂前进行弯曲性能的检验复验、检验的结果符合:GB/T3091-20089.外观表面检查:划痕和创伤深度不大于1mm;无表面裂纹(MT抽样检查);无重皮。
10.交货、标识、与验收10.1以保证长度为交验的依据;10.2以检验批为单元提供合格证和质量证明文件。
质量证明文件至少应包括:钢板的质量证明,无损检测报告、复验报告,弯曲试验报告,焊缝、外观等各项检验记录;10.3标识的内容包括(喷漆)规格、材质、检验批。
11.运输运输由甲方负责,乙方负责工厂的装车。
直缝埋弧焊钢管技术标准
油气管标准比照表(制造公差) 项目9711.1 9711.2 API 5L (43版)API 5L (44版)外径偏差管端(-0.79,+2.38)mm,D>508mm冷扩径管,两端外径之差≤2.38mm 管端①D≤610mm,±0.5mm或±0.5%D(取大值),最大±1.6mm②D(610,1430)mm,±1.6mm③D>1430mm,协议①D≤60.3mm,+0.41mm,-0.8mm②D(60.3,508)mm,±0.75%③D(508,914)mm,+0.75%,-0.25%④D>914mm ,+6.4mm,-3.2mm①168.3<D≤610mm,±0.5%D,最大偏差为±1.6mm②610<D≤1219mm,±1.6mm管体管体①D≤610mm,±0.75%D最大±3mm②D(610,1430】mm,±0.5%D, 最大±4mm③D>1430mm,协议①D≤273mm,+ 1.6mm,-0.4mm②D(273,508)mm,+2.4mm,-0.8mm③D(508,1066)mm,+2.4mm,-0.8mm④D>1066mm ,+2.4mm,-0.8mm ①168.3<D≤610mm,±0.75%D,最大偏差为±3 mm②610<D≤1219mm,±0.5%D,最大偏差为±4 mm椭圆度管端:2%D ①D≤610mm,1.5%(管端)、2%(管体)②D>610mm管端:D/T≤75时,1.0%,D/T>75时,1%(D>1430mm时协议)管体:D/T≤75时,1.5%但最大15mm,D/T>75时,2% 管端,一般至少每十根测量一次;管体,每班测量两次,开始中间各测量一根。
埋弧焊直缝钢管预焊工艺
埋弧焊直缝钢管预焊工艺答案:一、直缝埋弧焊钢管预焊工艺1、直缝埋弧焊钢管预焊工艺过程预焊时 ,先将钢管管坯进行合缝,随后进行连续气体保护焊,在焊接同时进行焊缝状态和焊接质量的监测和反馈。
具体工艺过程为:进口辊道接受管坯→调整管坯开口位置→输送装置递送管坯→管坯合缝→确认合缝质量→焊枪下降准备焊接→启动激光跟踪器进行跟踪→打开保护气体及冷却水阀→启动焊接 (管坯以焊接速度进给 )→到终端熄弧停焊→滞后关断保护气体→焊枪上升回位→管坯传往下道工序。
到此,一个预焊周期完成。
在上述工序中,调整管坯的开口位置,是指将开口缝位置调整到要求位置,此项工作可通过电控系统中摄像监视系统进行。
确认合缝质量,就是对合缝的错边量、合缝的间隙等进行确认,只有确认后才可进行合缝的跟踪和焊接。
2、直缝埋弧焊钢管预焊质量预焊质量包括合缝质量和焊缝质量。
(1)合缝 (也即成型缝)无错边或错边小于规定值, 一般规定错边量≤板厚的 8%, 最大不超过1. 5mm。
(2)要保证焊缝有适宜的熔透深度和熔敷量 ,既要保证焊后不开裂 ,不产生烧穿现象, 又要控制焊缝高度,对外焊焊缝余高不产生影响。
(3)焊道连续、成型良好,以利于保证最后的外焊质量。
(4)焊缝不存在焊偏、气孔、裂纹、夹渣、烧穿及背面焊瘤等缺陷,要求焊缝中心偏差≤1mm。
(5)无电弧灼伤、飞溅小、不影响管端坡口及表面质量。
(6)焊缝与母材匹配,焊缝金属理化性能达到质量要求。
二、直缝埋弧焊钢管预焊设备预焊设备主要包括机械系统、液压系统、焊接系统、电控系统等部分。
1、机械系统机械系统是设备的主体,包括进出口辊道、驱动装置、合缝装置、内扩导向装置等, 它实现管坯的合缝、输送。
(1)进出口辊道:进出口辊道完成管坯的接授、输送、开口缝位置调整等功能。
根据预焊工艺要求, 管坯的下底标高不变 ,因此要求进出口辊道开口能根据钢管规格进行调节。
(2)驱动装置:预焊机一般采用焊枪固定、管坯移动方式。
直缝焊管
17.4
18.2
19.5
20.7
21.6
23.3
24.1
25.7
27.8
29.9
33.9
193.7
18.7
19.6
21.0
22.4
23.3
25.1
26.0
27.8
30.0
32.2
36.6
203
22.0
23.5
2,4.4
26.3
27.3
29.1
31.5
33.8
38.5
219.1
23.8
25.4
26.4
3.70
3.93
4.27
54
1.56
1.82
1.94
2.07
2.32
2.56
2.81
3.17
3.54
3.77
4.01
4.36
60
1.74
2.02
2.16
2.30
2.58
2.86
3.14
3.54
3.95
4.22
4.48
4.88
63.5
1.84
2.14
2.29
2.44
2.74
3.03
3.33
3.76
4.19
直缝焊管
是用钢板或钢带经过弯曲成型,然后经焊接制成。按焊缝形式分为直缝焊管和螺旋焊管。按用途又分为一般焊管、镀锌焊管、吹氧焊管、电线套管、公制焊管、托辊管、深井泵管、汽车用管、变压器管、电焊薄壁管、电焊异型管和螺旋焊管。
一般焊管
一般焊管用来输送低压流体。用Q195A、Q215A、Q235A钢制造。也可采用易于焊接的其它软钢制造。钢管要进行水压、弯曲、压扁等实验,对表面质量有一定要求,通常交货长度为4-10m,常要求定尺(或倍尺)交货。焊管的规格用公称口径表示(毫米或英寸)公称口径与实际不同,焊管按规定壁厚有普通钢管和加厚钢管两种,钢管按管端形式又分带螺纹和不带螺纹两种,表6-17为焊接钢管尺寸。
- 1、下载文档前请自行甄别文档内容的完整性,平台不提供额外的编辑、内容补充、找答案等附加服务。
- 2、"仅部分预览"的文档,不可在线预览部分如存在完整性等问题,可反馈申请退款(可完整预览的文档不适用该条件!)。
- 3、如文档侵犯您的权益,请联系客服反馈,我们会尽快为您处理(人工客服工作时间:9:00-18:30)。
所有管端均应切直且不应有有害 毛刺。(30°~35°),钝边:1.59mm ±0.79mm,管端切斜≤1.6mm,内
锥角≤7° 距管端 100mm,内焊缝余高去除
油 气 管 标 准 比 照 表 (制造公差)
项目 管
外端 径 偏 差
管 体
9711.1
9711.2Байду номын сангаас
API 5L (43 版)
(-0.79,+2.38)mm,D>508mm 冷扩径管, ①D≤610mm,±0.5mm 或± ①D≤60.3mm,+0.41mm,-0.8mm
两端外径之差≤2.38mm
管 0.5%D(取大值),最大±1.6mm ②D(60.3,508)mm,±0.75%
T≤13.0mm,内外焊缝≤3.5mm T>13mm,内焊缝≤3.5mm,外焊缝 ≤4.5mm 每根钢管
无损检测 全长 100%RT 或者管端 203mmRT+其余部分 UT。冷扩径后管端至少 152.4mmMT 或 UT、 RT
焊缝全长进行 UT
无损检验方法: 要求全长 100%UT ,RT 协商。
不高于 B 级(+15.0%,-12.5%)
不低于 X42(+15.0%,-12.5%)
③ D>508mm,
不高于 B 级(+17.5%,-12.5%)
不低于 X42(+17.5%,-12.5%)
① 平端钢管,(+10.0% ,-5.0%)
② L175 、 L175P 、 A25 、 A25P ,
(+10.0% ,-5.0%)
4.0mm 。
① 公称长度为 6m,(2.74,6.86)m ⑥ 6m ,(2.74m—6.86m)平均 5.33
平均 5.33m 。
⑦ 9m ,(4.11m—10.29m)平均 8.00
② 公称长度为 12m,(4.27,13.72) ⑧ 12m ,(4.27m—13.72m)平均
m 平均 10.67m
①电弧烧伤应归为缺陷 。②电弧烧伤 可用磨削、铲除或机械加工的方法清 除,并用 10%的过硫酸铵溶液或 5% 的硝酸乙醇腐蚀液检查电弧烧伤的金 属是否完全清除 。
咬边
不需修磨:①最大深度为 0.79mm 且不 超过钢管壁厚的 12.5%,最大长度为钢 管壁厚的一半,且在任意 0.30mm 长度 焊缝上这样的咬边不超过两处。②最大 深度为 0.40mm,长度不限。 超过上述规定的咬边应视为缺陷,且应 按照下列规定处置: ①深度不超过 0.79mm,且不超过规定 壁厚 12.5%的咬边应采用修磨法去除。 ②深度超过 0.79mm 或钢管壁厚 12.5% 的咬边应补焊、切除或整根钢管拒收处 理。
由于钢管成型工艺或生产操作而造成钢 管上出现与钢管正常轮廓不一致的几何 形状(如凹陷、扁平硬块、凸起等)不得 超过下列规定: ①扁平硬块、凸起以及冷态形成的尖底凹 陷为 3mm②其他凹陷为 6mm
扩展到管端面或坡口面上,外观测 定横向尺寸超过 6.4mm 的分层或夹 杂应视为缺陷。有这种缺陷的钢管 应返切,直到没有>6.4mm 的分层 或夹杂为止。 管体上满足下列两个条件的分层应 视为缺陷: ① 最小尺寸≥19.0mm;②面积≥ 7742mm2
①168.3<D≤610mm,±0.75%D, 最大偏差为±3 mm ②610<D≤1219mm,±0.5%D,最 大偏差为±4 mm
椭圆度
管端:2%D
直线度
≤0.2%L
长度公差 6m(2.74~6.86)m ,平均 6.33m 12m(4.27~13.72)m ,平均 10.67m
①D≤610mm,1.5%(管端)、2% (管体) ②D>610mm 管端:D/T≤75 时,1.0%, D/T>75 时,1%(D>1430mm 时 协议) 管体:D/T≤75 时,1.5%但最大 15mm,
10.67
③ 公称长度为 15m,(5.33,16.76) ⑨ 15m ,(5.33m—16.76m)平均
m 平均 13.35m
13.35
④ 公称长度为 18m,(6.4,19.81) ⑩ 18m ,(6.40m—19.81m)平均
m 平均 16.00m
16.00
壁厚公差 D≤457mm,(+15%,-12.5%)T D≥508mm,(+17.5%,-10%)T(≤L245) (+19.5%,-8%)T(L290~L255)
除非合同特别要求,①在钢管外表 面上,从距钢管 450 mm—760 mm 之间的一点开始。②在钢管内表面 上,从距钢管一端至少 150 mm 的一 点开始。
油 气 管 标 准 比 照 表 (工艺质量和缺陷)
项目
9711.1
钢管上不得有深度超过 6.35mm 的摔
坑,摔坑深度是指摔坑的最低点与钢管
摔坑 原始轮廓线之间的距离。摔坑在任何方 缺
③ 其他,(+10.0% ,-3.5%)
管端
对接 焊缝余高 水压试验
(30°~35°),钝边:1.59mm±0.79mm, 管端切斜≤1.59mm,内锥角≤7°(8 小时工 作班检验 3 次)。距管端 101.6mm,内焊缝余 高去除
允许,两直缝应间隔(51~203)mm,焊缝余 高≤3.18mm(埋弧焊) 3.18mm(T≤12.7);4.76mm(T>12.7)
D/T>75 时,2% 整体直线度≤0.2%L,局部直度< 4mm/m
定尺长度:L±500mm
管端,一般至少每十根测量一次; 管体,每班测量两次,开始中间各 测量一根。 要求:管端 100m 范围内椭圆度≤ 0.8%,其余≤1.2% 。
≤0.2%L
整体直线度≤0.2%L,在每端 1000
mm 范围内对直线的局部偏离≤
向①上的长度不得超过钢管直径的一
半。所有冷态形成的深度超过 3.18mm
并带有尖底凿痕的摔坑可采用修磨法 欠
去除
9711.2 ①深度≤12.5%T,且不影响规定最 小壁厚的缺欠,应判为可接受的缺 欠,未经修补允许存在,可修磨。 ②深度>12.5%T,且不影响规定最 小壁厚的缺欠,应判为缺陷,可修 磨、补焊、切除缺陷或整根钢管判 不合格。
重量公差 L175 (+10%,-5%)其它(+10%,-3.5%)
T≤10mm 时,T(+1.0,-0.5)mm T(10,20)mm 时,(+10%,-5%)T T≥20mm 时,T(+2,-1)mm
(+10%,-3.5%)
⑤ 公称长度为 24m,(8.53,25.91) ⑪ 24m ,(8.53m—25.91m)平均
裂缝 所有裂缝、渗水和漏水均视为缺陷 漏水
③影响到规定最小壁厚的缺欠应判 为缺陷,可补焊、切除缺陷或整根 钢管判不合格。
所有裂缝、渗水和漏水均视为缺陷
焊偏 硬块
径向 错边
只要焊缝完全焊透并充分熔合,焊偏不 能作为拒收的依据
在任何方向上最小尺寸>50.8mm,且硬 度值≥35HRC(HB327)的任何硬块应拒
端 ②D(610,1430)mm,±1.6mm ③D(508,914)mm,+0.75%,-0.25%
③D>1430mm,协议
④D>914mm ,+6.4mm,-3.2mm
①D≤610mm,±0.75%D 最大 ① D≤273mm,+ 1.6mm,-0.4mm
±3mm
② D(273,508)mm,+2.4mm,
① 钢级不小于 L210 或 A 级时,直 径 D≥60.3mm 的焊接钢管对焊 缝实行全长全壁厚无损检测
② 对于 SAW ,每根钢管距管端至 少 200mm 长范围内的焊缝采用 RT 。
标识
D≤406.4mm,外表面 457~762 之间一点 D≥406.4mm,内表面≥152.4mm 处开始
① 外径 D≤48.3mm ,应在固定 于钢管捆的标签上或捆扎钢管 捆的带条上做标志。
T≤15mm,内外焊缝≤3mm T>15mm,内焊缝≤3mm,外焊缝 ≤4mm ① 50MPa ,对外径 D≤406.4mm ② 25MPa ,对外径 D>406.4mm
坡口角为 30°—35°,钝边为 1.6 ±0.8mm,尺寸大于 114mm,清除 管端内毛刺形成的内锥角不应大 于 7°。尺寸不小于 60.3mm,管端 切斜不应超过 1.6mm。
管 ②D(610,1430】mm,±0.5%D, -0.8mm
体 最大±4mm
③ D ( 508,1066 ) mm , +2.4mm ,
③D>1430mm,协议
-0.8mm
④D>1066mm ,+2.4mm,-0.8mm
API 5L (44 版) ①168.3<D≤610mm,±0.5%D,最 大偏差为±1.6mm ②610<D≤1219mm,±1.6mm
m 平均 21.34m
21.34
① D≤73mm,
① t≤5.0mm ,(+0.5,-0.5)
不高于 B 级(+20.0%,-12.5%) ② 5.0mm<t<15.0mm ,(+0.1t ,
不低于 X42(+15.0%,-12.5%)
-0.1t)
② D(73,508)mm,
③ t≥15.0mm , (+1.5 ,-1.5)
分层
电弧 烧伤
扩展到管端面或坡口面上,外观测定横 向尺寸超过 6.35mm 的分层或夹杂应视 为缺陷。有这种缺陷的钢管应返切,直 到没有>6.35mm 的分层或夹杂为止。 管体上满足下列两个条件的分层应视 为缺陷: ① 最小尺寸≥19.1mm;②面积≥ 7742mm2 有以上缺陷钢管应切除或整根钢管拒 收 电弧烧伤应视为缺陷。可用磨削、铲除 或机械加工方法清除。对清除电弧烧伤 而形成的凹坑应彻底清理,并用 10%的 过硫酸氨溶液或 5%的硝酸乙醇腐蚀液 做酸蚀以检查受损金属十分完全清除。 如受损金属已彻底清除,且修磨处得剩 余壁厚在规定范围内,则可用修磨法修 磨使凹坑与钢管原始轮廓过渡平缓。