有效的车身尺寸控制方法
白车身制造过程尺寸控制方法PPT课件
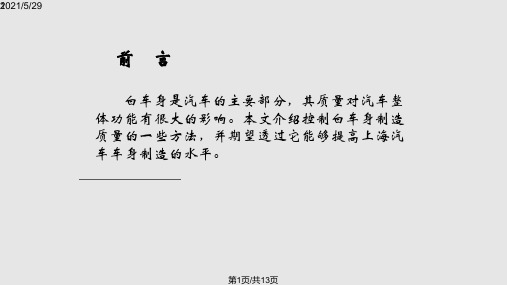
6
2021/5/29
第6页/共13页
6σ,是对一定数量的样本数据波动状况进行评价的阶段评价指 标。样本一般为20~30台。对于小样本离线检测,通常要求通 过数据分离提取出数据的波动项。须使数据具有平稳的统计特 性(近似正态分布)才可以进行6σ的计算。单点6σ计算每个点 波动标准差σ的6倍。从统计意义上讲,代表该点的实际尺寸有 99.73%的可能落在名义值的±3σ以内,因此可以认为表明了该 点数据的变动范围。整车6σ将全部测点的6σ从大到小进行排序, 取95百分位的点的6σ值作为该白车身的6σ值(如图)。
12
2021/5/29
第12页/共13页
感谢您的观看!
2021/5/29
13
第13页/共13页
4
2021/5/29
第4页/共13页
这两种典型的过程控制方法虽然都很有效,但是由于 车身制造工艺的复杂性使得车身上的产品过程监控测点数 多达几百个,这就给判断制造过程的稳定性带来了一定难 度。
5
2021/5/29
第5页/共13页
车身尺寸质量评价指标2mm工程
所谓的“2mm”指的是所有白车身的关键测点的波动(6σ) 值小于2mm。该技术对白车身尺寸质量的评定是以关键 测点的6σ表示,包括单个测点的6σ以及整车的6σ,并以 CII指数(持续质量改进指数)反映尺寸质量的长期变化 趋势。由于车身的测点数据主要是由三坐标测量机采集 的,受硬件条件的限制,采样频次较低,故不适合用 SPC的方法评价尺寸质量的稳定性。目前样板采用 “2mm工程”作为白车身尺寸质量评价的主要指标。
9
2021/5/29
第9页/共13页
车身车间在以先进 的2mm工程所提出 的6σ和CII指数作为 主要指标的同时, 结合尺寸通过率对 白车身尺寸整体水 平进行即时的评估, 并在此基础上建立 了相应的尺寸控制 流程。
车身尺寸控制方法
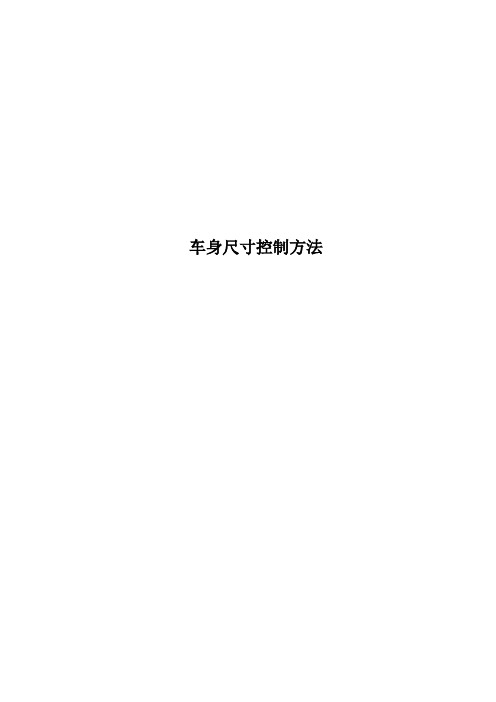
车身尺寸控制方法车身尺寸控制方法汽车车身尺寸控制是汽车生产的重要质量控制项目,也是一个系统工程,其控制能力综合反映了一个企业的产品开发和质量控制水平,因此是汽车制造企业的关注焦点。
江铃全顺工厂结合自身产品的特点,通过不断地总结和探索找到了一个适合自己的车身尺寸控制方法,即抓住根本,控制车身的变差源。
汽车制造四大工艺中冲压和焊接是基础,是整车质量的保证。
在冲压焊装的前期工艺规划中,零件模具和车身焊接夹具以及生产线的设计又是车身尺寸控制的关键环节。
设计工装模夹具时,不仅要考虑生产纲领,还必须要熟悉产品结构,了解钣金件变形特点,掌握冲压、涂装以及总装工艺的诸多要求,通晓零部件装配精度及公差分配。
只有做到这些,才能对模夹具进行全方位的设计,满足生产制造要求,达到车身尺寸质量要求。
下面结合全顺工厂的经验谈谈车身尺寸的控制方法。
图1 车身尺寸变差鱼骨分析变差的来源由于所有制造过程在人员、机器、材料、方法、环境以及测量方面都存在变动因素(如图1所示),所以车身尺寸的变差不可避免,在制造上也就有了公差的概念,公差的大小、过程能力的高低取决于控制变差能力的大小,这也具体反映了车身制造的质量水平。
经历过多次新产品开发流程,我们总结了6方面造成车身尺寸变差的权重:材料占45%,机器占30%,人员和方法占20%,环境和测量占5%。
冲压件在投产阶段对车身尺寸影响非常大,具体如表1所示。
控制变差源在车身开发阶段,有4个阶段会对车身尺寸产生较大影响,分别为产品设计、工艺开发、试生产及批量生产,各阶段产生的影响程度和侧重点不同。
要控制变差源,开发阶段控制占70%,过程控制占30%。
在开发阶段,产品设计和工艺开发尤为重要。
首先,要建立车身统一基准系统,用于统一从冲压件、零件检具、焊接总成、白车身装配,到总装装配的主定位基准原则,建立MCP(Master Control Point)清单,便于冲压、焊接、总装工艺在开发定位工装时协调一致,避免因工序定位选择不同而产生偏差。
车身尺寸质量的控制方法
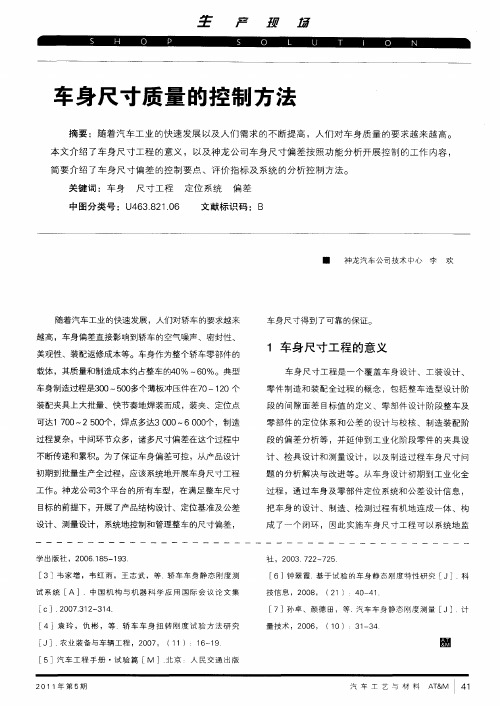
车 身尺 寸 质 量 的控 制 方法
摘要 :随着汽车 工业 的快速 发展 以及人们 需求 的不断提高 ,人们 对车身质量 的要求越来越高 。 本 文介绍 了车 身尺寸工程 的意义 ,以及神 龙公司车 身尺 寸偏差按 照功 能分析开展控 制的工作 内容 , 简 要介绍 了车 身尺寸偏差 的控制要点 、评 价指标及 系统 的分析控 制方法。
(1)车 身焊 接 夹具 是 保证 车 身焊 接精 度 的重 要 因 素
焊 接夹具 的作 用是 保证所 要焊 接零 件 之间 的相 对 位 置和焊 接 件 的尺 寸精 度 ,减 少焊 接过程 中的变形 以 提 高焊 装效 率。 因此 ,车 身焊 接夹具 是 保证车 身焊 接 精度 的最 重 要 的因素 。不 同 的夹具 结构 对零部 件尺 寸 稳定 性 的影 响是不 同 的 ,应 尽早 参 与夹具 方案 设计 , 提 出夹具所 涉及 尺 寸的要 求如 下。
关键 词 :车身 尺寸工程 定 位 系统 偏差 中图分 类号 :U463.821.06 文献标识 码 :B
一 神 龙汽 车公 司技 术中 心 李 欢
随着汽车 工业 的快速发展 ,人们对轿车 的要 求越来 越 高 ,车身偏差直接影 响到轿车 的空气噪声、密封性 、 美观 性、装配返修成本 等。车身作 为整个轿车零部件 的 载体 ,其质量和 制造成 本约 占整车 的40% ~60%。典型 车 身制造过程是300~500多个薄板冲压件在70~1 20个 装配 夹具 上大批量 、快 节奏地焊装而成 ,装夹、定位点 可达 1 700—2 500个 ,焊点 多达3 000~6 000个 ,制造 过程 复杂 ,中间环节众 多 ,诸多尺寸偏差 在这个过程 中 不断传递和 累积。 为了保证 车身偏差可控 ,从产品设计 初期到批量 生产全过程 ,应 该系统地开展 车身尺寸工程 工作 。神龙 公司3个平 台 的所 有车型 ,在 满足整车 尺寸 目标 的前 提下 ,开展 了产 品结构设计 、定位 基准及公差 设计 、测量 设计 ,系统地控 NSn管理整车 的尺寸偏差 ,
试制白车身关键尺寸精度控制方法
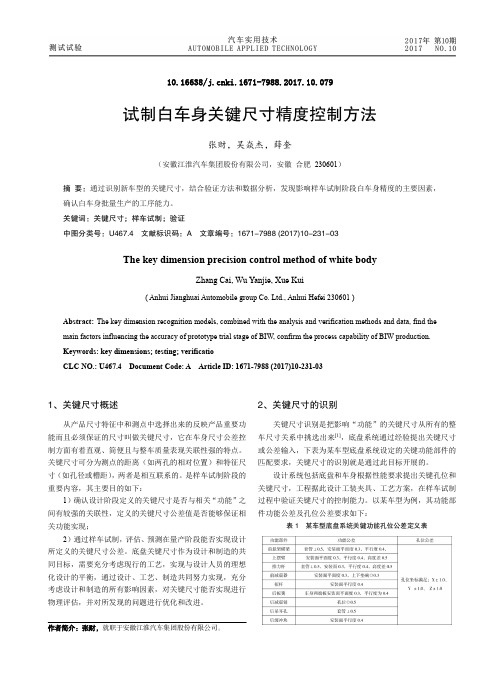
10.16638/ki.1671-7988.2017.10.079试制白车身关键尺寸精度控制方法张财,吴焱杰,薛奎(安徽江淮汽车集团股份有限公司,安徽合肥230601)摘要:通过识别新车型的关键尺寸,结合验证方法和数据分析,发现影响样车试制阶段白车身精度的主要因素,确认白车身批量生产的工序能力。
关键词:关键尺寸;样车试制;验证中图分类号:U467.4 文献标识码:A 文章编号:1671-7988 (2017)10-231-03The key dimension precision control method of white bodyZhang Cai, Wu Yanjie, Xue Kui( Anhui Jianghuai Automobile group Co. Ltd., Anhui Hefei 230601 )Abstract:The key dimension recognition models, combined with the analysis and verification methods and data, find the main factors influencing the accuracy of prototype trial stage of BIW, confirm the process capability of BIW production. Keywords: key dimensions; testing; verificatioCLC NO.: U467.4 Document Code: A Article ID: 1671-7988 (2017)10-231-031、关键尺寸概述从产品尺寸特征中和测点中选择出来的反映产品重要功能而且必须保证的尺寸叫做关键尺寸,它在车身尺寸公差控制方面有着直观、简便且与整车质量表现关联性强的特点。
关键尺寸可分为测点的距离(如两孔的相对位置)和特征尺寸(如孔径或槽距),两者是相互联系的。
车身尺寸质量控制技术
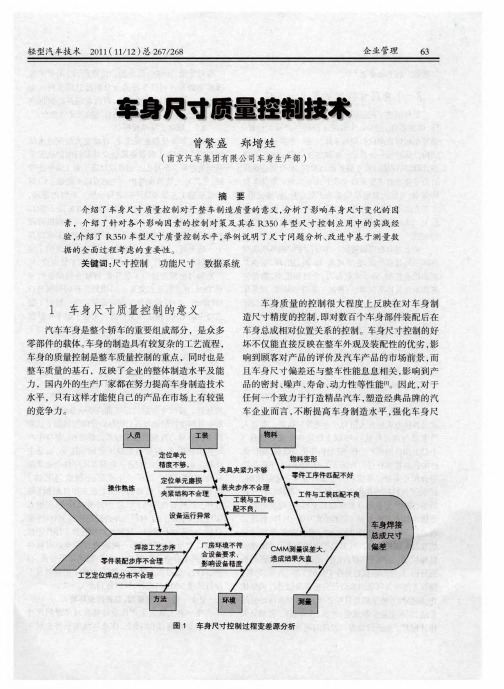
项 T M, P 并进行互相交叉 。3 维修工程师每周进行 )
P M检 查 。4 样板 测量 工程 师每 年 至少一 轮 对工 装 ) 进 行全 面 C MM 精 度测 量检 查 ,关 键 工装 半 年甚 至
三个月一次测量。5 重点加强工装精度管理 , ) 对于 需要到精度改变的工装 , 其精度调整过程必须依据 “ 工装精度调整流程” 进行 , 对调整 、 试制 、 批量验 证全过程控制 , 并留存记录备查。
23 完善 物料质 量监 控及 过程检 查 .
上百个 冲压或焊接小总成件是 车身装配总成 的基 础 ,其 尺寸 质量 的好 坏 直接 影 响 总成 的 质量 , 是车身精度控制的基石。物料质量 的控制除了依靠 供货商 自身力量及质量工程师监督维护 , 车身生产 部作为使用方 , 对物料质量 不是被动接受 , 而是主
21 提 升人员 技能 、 . 认识及 全员 参与 度 人员 质量 意识及 素 质在尺 寸质 量控 制各 环节 发 挥 了关键 作 用 。车身生 产部通 过学 习 、 培训 、 技能 比 武 等各种 方式 提升人 员对 尺寸 质量 的认识 ,提升 人
标测量 , 保持对数据 的监控 , 出现偏差 的数据 向 对 尺寸工艺工程师报警 , 并主持每周的尺寸分析会。
车身制造工艺过程复杂 ,车身总成 由数百个冲
压、 焊接零件 , 10 近 0 个装配工位 的生产线大批量 、 快节奏地焊接而成 ;同时车体又是一个多层次体系 结构 , 从冲压一分总成一车体焊接总成 中间环节众 多, 因此其焊接后尺寸偏差难以控制。 车身制造过程 的尺寸变差源主要来 自于以下几个方面 :零件本身 的偏差、 工装夹具定位偏差或不稳定性 、 焊接变形 、 工艺方法不合理 、操作不 当等各方面 闭 如图 1 ( 所 示) ,以上任何 因素的变动都有可能导致尺寸控制 的失败 。 从上述分析可以看出,车身尺寸控制体现在对 各 环节 的过程 控制 , 于对人 、 、 、 、 、 各 方 在 机 料 法 环 测 面的综合控制 , 需要全员参与 , 全过程覆盖 , 需要完 善的流程及体系保障 , 完善的工装管理制度 、 规范化 的操作 、 合理高效的工艺方法 、 优异的物料质量保障 及一致性控制 , 同样还有高效的数据测量采集系统 , 合理有效的数据处理方法及问题改进方法与流程 。 南汽车身生产部在 R 5 车型车身尺寸控制 、提升 30 尺寸质量水平工作 中, 通过探索与创新 , 总结经验 , 形成了一套有效的车身尺寸控制策略。
试析汽车白车身尺寸精度控制方法

车辆工程技术14车辆技术1 引言 随着国内经济的快速发展,人民生活水平普遍提高,汽车保有量稳步增长。
为了吸引消费者的注意力,汽车制造商正在积极更新汽车外观,但在大多数情况下,这是车身结构的变化,而其余组件并未发生重大变化。
如果车身设计不合适且尺寸不合适,则会对车辆产生巨大影响。
车身尺寸精度是确保汽车零件组装的基础。
车身制造包括冲压和焊接工艺,尺寸和表面质量控制等,车身制造技术水平已经成为衡量汽车公司制造水平的重要指标。
影响车身制造过程复杂性的因素很多,整个汽车制造的尺寸精度取决于各种因素的综合作用。
2 车身尺寸精度影响因素2.1 测量过程 测量过程对尺寸精度的影响与其他几个因素无关。
该测量和分析系统可以分析和测量车身尺寸数据,以有效地确定被测零件是否存在尺寸质量问题。
CMM是悬臂、龙门和多关节臂坐标测量机等现代汽车制造中常用的车身尺寸测量设备,这些设备的高测量精度和可编程控制功能使其适用于车身和子装配零件的高频测量。
测量分析系统会自动绘制出车身尺寸质量的线性分布图,并生成分析报告,从而使技术人员可以方便地进行分析。
2.2 零件偏差 车身焊接件基本上是冲压件,主要分为两类:一种是表面的外壳,另一种是冲压内部结构。
其形状都特别复杂,以至于它们都必须满足标准精度要求。
零件需要经历各种过程,例如冲压、剪切、弯曲、拉伸、膨胀、翻边等,必须根据图纸标准进行设计。
在包装和运输过程中由于冲压零件而引起的变形是尺寸偏差的一个因素,并且外观检查无法识别变形,即使进行了修理,也无法完全恢复到设计尺寸。
因此,应根据零件的特性设计包装和运输方式,以消除这种偏差。
冲压件的回弹是影响冲压件尺寸的最大因素,冲压后,产生应力和应变,形状和尺寸发生变化。
上述所有原因均是由于冲压模、人造工件或冲压机的问题所致。
为了保证冲压件的尺寸精度,应使用三坐标测量机参照零件图进行例行检查,以确保冲压件符合图纸的设计要求。
2.3 操作过程 在非自动化生产线中控制过程偏差的最有效方法是实施操作程序的标准化,并且在实施标准化操作后,可以最大程度地减少手动操作中的不一致、不稳定和不确定性。
培训材料1-白车身尺寸匹配控制
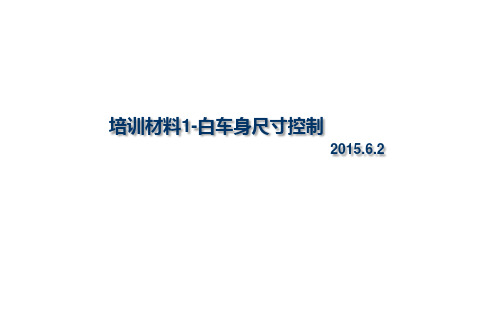
底盘RPS点的Z向平顺性 疑问——底盘不平顺有哪些危害?
答:主要两种危害。(此处强调一下:下部总成的刚度与骨架总成的刚度是不同的)
1.前后端Z向尺寸不稳定
2.整车的Y向对中性不稳定
Y
Z
18
底盘RPS点的Z向平顺性 保证地盘平顺的三步骤: 1.排查前后左右4根纵梁单件→分总成,是否存在扭曲; 2.检查后地板总成的4个Z向RPS点是否在一个平面上; 3.用移动三坐标测量关键夹具,并优化夹具。
30
辅助RPS点的Y向平顺性 建议:应优先保证Y向平顺性。 如下图红色圆圈均为Y向辅助RPS,测量支架上有夹具将侧围夹持到理论平面。 在测量支架上,完成夹紧后,应逐一单独打开某一Y向辅助加紧,观察是否有较大回弹 (回弹量大于5mm且夹紧块吃力很大)
如果回弹较大,会影响侧围报告可读性,并导致主焊骨架尺寸不稳定(因为主焊定位夹 具无法克服侧围总成较大的变形,夹具打开后,骨架尺寸则整体回弹)
唯一的辅助Z向RPS点 Z向值越接近零越好, 宁高勿低
3个主定位Z向RPS点 Z向值均为零
20
底盘RPS点的Z向平顺性 保证地盘平顺的三步骤: 1.排查前后左右4根纵梁单件→分总成,是否存在扭曲; 2.检查后地板总成的4个Z向RPS点是否在一个平面上; 3.用移动三坐标测量关键夹具,并优化夹具。
关键夹具,主要指: 3.1下部一主拼工位; 3.2下部一主拼工位紧后面的若干个补焊焊点较多的工位;(须说明,下图) 3.3下部二主拼工位; 3.4下部二主拼工位紧后面的若干个补焊焊点较多的工位。
培训材料1-白车身尺寸控制
2015.6.2
目录 白车身制造及装配流程简介 白车身尺寸控制手段 白车身各分总成的重要尺寸点,重点展开 功能尺寸知识 CP与CPK
汽车尺寸管理计划方案
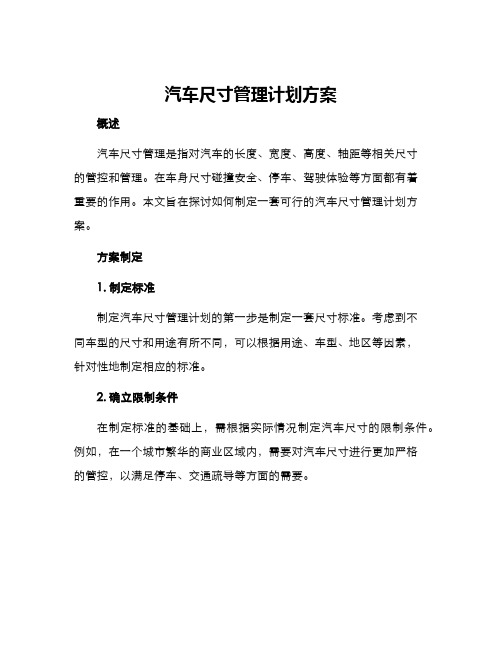
汽车尺寸管理计划方案概述汽车尺寸管理是指对汽车的长度、宽度、高度、轴距等相关尺寸的管控和管理。
在车身尺寸碰撞安全、停车、驾驶体验等方面都有着重要的作用。
本文旨在探讨如何制定一套可行的汽车尺寸管理计划方案。
方案制定1. 制定标准制定汽车尺寸管理计划的第一步是制定一套尺寸标准。
考虑到不同车型的尺寸和用途有所不同,可以根据用途、车型、地区等因素,针对性地制定相应的标准。
2. 确立限制条件在制定标准的基础上,需根据实际情况制定汽车尺寸的限制条件。
例如,在一个城市繁华的商业区域内,需要对汽车尺寸进行更加严格的管控,以满足停车、交通疏导等方面的需要。
3. 设定指标在确定了各个车型的获得准入的条件后,需要具体规定相关的指标。
例如,车长不能超过多少米、车宽不能超过多少米、车高不能超过多少米以及轴距等限制。
4. 建立审查机制制定汽车尺寸管理计划方案后,需要建立相应的审查机制。
在审查过程中,按照相关标准进行审核。
同时需要进行认真的反馈记录,以不断帮助完善汽车尺寸管理计划方案。
5. 宣传推广制定完毕汽车尺寸管理计划方案后,需要通过网络、媒体等渠道对计划方案进行宣传和推广,以便引导公众关注和反馈意见。
方案评估制定完毕汽车尺寸管理计划方案后,需要对方案进行评估。
其中包括方案实施过程中的利弊、实施效果等方面的评估。
1. 利弊分析对实施方案的利与弊进行分析,包括通过实施方案,是否能有效控制汽车尺寸,从而达到城市交通管理的目的;同时,需要分析方案对于汽车特定行业和用户的影响等。
2. 效果评估实施方案后,还需要根据实际效果,对方案进行评估。
这包括通过实施方案,是否能够达到预期的管理效果,是否可以减少交通管理中的事故事件等方面的考量。
总结通过对汽车尺寸的管控和管理,能够达到降低交通事故发生率、促进城市交通管理、提高道路停车场的利用率等好处。
本文提出的方案,可以有效地针对不同的城市或者用途制定相应的尺寸管理标准,从而更好地保障道路行车的安全。
- 1、下载文档前请自行甄别文档内容的完整性,平台不提供额外的编辑、内容补充、找答案等附加服务。
- 2、"仅部分预览"的文档,不可在线预览部分如存在完整性等问题,可反馈申请退款(可完整预览的文档不适用该条件!)。
- 3、如文档侵犯您的权益,请联系客服反馈,我们会尽快为您处理(人工客服工作时间:9:00-18:30)。
有效的车身尺寸控制方法作者:文章来源:发布时间:2010-07-13新浪微博QQ空间人人网开心网更多图1 车身尺寸变差鱼骨分析汽车车身尺寸控制是汽车生产的重要质量控制项目,也是一个系统工程,其控制能力综合反映了一个企业的产品开发和质量控制水平,因此是汽车制造企业的关注焦点。
江铃全顺工厂结合自身产品的特点,通过不断地总结和探索找到了一个适合自己的车身尺寸控制方法,即抓住根本,控制车身的变差源。
汽车制造四大工艺中冲压和焊接是基础,是整车质量的保证。
在冲压焊装的前期工艺规划中,零件模具和车身焊接夹具以及生产线的设计又是车身尺寸控制的关键环节。
设计工装模夹具时,不仅要考虑生产纲领,还必须要熟悉产品结构,了解钣金件变形特点,掌握冲压、涂装以及总装工艺的诸多要求,通晓零部件装配精度及公差分配。
只有做到这些,才能对模夹具进行全方位的设计,满足生产制造要求,达到车身尺寸质量要求。
下面结合全顺工厂的经验谈谈车身尺寸的控制方法。
变差的来源由于所有制造过程在人员、机器、材料、方法、环境以及测量方面都存在变动因素(如图1所示),所以车身尺寸的变差不可避免,在制造上也就有了公差的概念,公差的大小、过程能力的高低取决于控制变差能力的大小,这也具体反映了车身制造的质量水平。
经历过多次新产品开发流程,我们总结了6方面造成车身尺寸变差的权重:材料占45%,机器占30%,人员和方法占20%,环境和测量占5%。
冲压件在投产阶段对车身尺寸影响非常大,具体如表1所示。
表1 车身尺寸合格率与材料状态的对照控制变差源在车身开发阶段,有4个阶段会对车身尺寸产生较大影响,分别为产品设计、工艺开发、试生产及批量生产,各阶段产生的影响程度和侧重点不同。
要控制变差源,开发阶段控制占70%,过程控制占30%。
在开发阶段,产品设计和工艺开发尤为重要。
首先,要建立车身统一基准系统,用于统一从冲压件、零件检具、焊接总成、白车身装配,到总装装配的主定位基准原则,建立MCP(Master Control Point)清单,便于冲压、焊接、总装工艺在开发定位工装时协调一致,避免因工序定位选择不同而产生偏差。
其次,产品设计要避免冲压成形工艺过于复杂,减少冲压回弹和零件干涉现象,模夹具设计定位必须可靠,如夹具定位孔必须选择传递冲压的主定位孔,定位面必须选取冲压件的可靠面。
再次,工装设计时要便于员工取放料,易于操作和维护,以防生产过程中因人机工程问题造成的尺寸变差。
考虑到车身钣金件回弹,形状不规则,材质及冲压工艺的影响,车身夹具都采用过定位设计以校正零件变形,而且定位夹紧单元都设计成三维或二维方向可调以适应零件变化。
一般来说,车身夹具设计遵循的原则为:1. 对单个工件一般用二销二型面的“定位-夹紧”稳定原则。
实质上二销确定了X,Y 向,二型面则强化确定了Z向。
对特别大的工件,考虑到钣金弹性件可适当增加销与型面的“定位夹紧”,以增加局部区域的稳定性。
2. 定位尺寸一致性传递原则,即不同工序不同夹具的定位尺寸应一致。
3. 焊点可视原则。
4. 以大尺寸、复杂零部件为先导,其余零件随后装上夹具,即逐次“定位-夹紧”。
5. 定位销精度±0.05mm,定位面精度±0.2mm。
在试生产前,工装夹具的安装非常重要,只有合格的工装才能生产出合格的产品。
夹具安装到位后,需使用测量设备(如激光跟踪仪)对所有定位孔面进行全尺寸测量,建立完备的定位基准数据,便于生产期间的车身尺寸协调。
一般工装到位后的试生产需要维持6个月,以满足投产不同阶段的质量控制目标。
试生产阶段主要是解决实际零件和工装夹具的匹配协调性,同时解决操作过程中的实际困难,直到到达设计要求的节拍以及质量目标才可转入到批量生产。
图2 投产各阶段车身尺寸合格率及偏差大小和分布区域试生产阶段需要准备产品数模、模夹具数模、MCP主定位清单、零件设变清单、焊接工艺卡、产品检具、总装装车问题清单以及夹具调整记录表等相关文件,便于及时在现场排查机器和材料的状态。
进入批量生产阶段,主要是加强工艺和工装夹具的管理。
首先保证操作完全执行工艺文件,同时工装夹具的定位必须定期监控,及时维护模夹具定位的松动和磨损,保证定位系统完好。
最后要考虑环境和测量的影响,在恶劣环境下气温高低差会达到30°,定位会产生热胀冷缩现象而影响尺寸。
另外,测量系统必须做测量系统分析,同时还要保证测量定位基准与制造夹具的定位基准一致。
表2 车身尺寸不合格点的分类统计数据的收集和分析方法车身尺寸数据获取的方式很多,最常用的是通过三坐标测量系统,检具、PCF 和UCF 等工具都可以检测出实际车身及零部件相对于设计数模的符合性,再对比开发初期就制定好的各测量点公差带以及合格率的要求,从而判定车身尺寸的合格率。
基于三坐标测量系统的数据,我们每一台车身可以得到多则上千少则数百的整车测量点数据,但是逐个分析没有可能也不必要。
目前,我们的做法是:先统计不合格点的状态,然后在数据稳定的情况下对生产过程进行确认并整改。
我们现有的经验是关注不合格点的超差情况和分布,同时计算一些总装和顾客关注的需要控制的点的过程能力(CP),通过部分代表的点反映整个车身的质量状态。
1. 数据的分类整理及分析在实际工作中,初步数据整理一般把车身分为5大块:前门洞、前风窗框、后门洞、侧拉门洞以及车身前部(如表2所示)。
通过跟踪每一台车的不合格点,把其记录到表2中所列的不同区块,并记录偏离理论值的偏差,偏差小于1mm的标注绿色,大于1mm但小于2mm的标注为黄色,大于2mm的标注为红色,通过数据的不断积累,可得出各阶段不合格点数据和状态(如图2所示)。
通过表2、图2我们能了解到不合格点的变化趋势和集中的区域,方便关注重点,同时知道不合格点超差的范围,提高紧急度响应。
2. 数据CTQ分析CTQ即关键质量控制,是车身尺寸的能力指标,其分析方法是:选取车身上与装配相关的孔的测量点,(如在开发工装夹具时,我们非常关注:前风窗框、门洞尺寸、发动机装配孔、前后悬吊装配孔、前后灯具总成件装配孔位、顶盖装配尺寸、仪表板装配孔等),按照顾客关注的特性分别建立子系统单元,约20个左右,每个子系统包含若干个相关的车身尺寸数据点。
以仪表板装配子系统为例,把总装装配仪表板的10个安装孔的测量数据作为一个系统,分别计算这10个孔测量数据的过程能力(CP),然后按照一个科学的判定原则综合判定,得出仪表板子系统综合装配能力:绿色为过程能力强,红色表示过程能力不足需持续改进。
子系统判定原则为:在子系统所有点的CP>1.33的数据必须≥50%和CP>1的数据必须≥80%两种情况同时满足时呈现绿色;在CP<1的>50%时,该项目为红色;不在这两种情况中的则显示黄色。
图3 全顺工厂CTQ整改趋势图3是全顺工厂运用CTQ长期跟踪相关子系统的趋势,非常直观地反映了过程能力。
该分析系统的优点是,直观有效地分析出问题所在和过程能力整体趋势,与三坐标整体报告互补,三坐标尺寸报告反馈车身尺寸宏观状况和整车尺寸合格率,CTQ分析反映具体的装配效率和能力。
3. 检具PCF/UCF/Blue Buck分析以上是基于三坐标测量数据的分析,主要在欧系车型上采用,日系车型喜欢采用各类检具测量分析系统,有分总成协调检具(PCF),装配零件协调检具(UCF),甚至是标准车身检具(Blue Buck),而不喜欢研究三坐标的数据。
三坐标数据的分析和判断要求工程师对产品、夹具和工艺过程都非常了解,而检具测量系统只需对操作人员做简单的培训即可。
PCF的使用是将零件放在检具上面,通过塞尺来测量判断零部件是否合格。
UCF是将零件装配在检具上,通过测量和标准检具仿体的对比来判断每个装配件的对错。
在检具测量的基础上,目前新发展出来的综合检具测量系统十分有借鉴意义,其在车身上可以模拟总装的所有装配零件,且判断简单,只有通过或不通过。
如在车身上装配一个座椅,总装要装配四个螺栓,模拟检具就插三个插销,可以插入表示通过,否则不通过。
车身尺寸合格率=所有检具可通过的插销数量/所有检具的插销数量×100%这种方法能充分反映总装的装配需求,操作判断都很简单,是一种测量系统的发展趋势,比三坐标测量系统更为实用,惟一的缺点是只能针对单一车型,不能柔性测量。
车身尺寸变差整改数据收集和分析可以确定问题所在,并找出问题出现的根本原因。
通过工程师的简单确认,基本可以排除或纠正人员和方法两方面的影响,之后,再用检具检查冲压件。
用PCF 和UCF检查对应的分总成,分别记录数据,同时根据车身数据分析的结果,首先检查问题点焊接夹具定位面、定位销的位置精度,记录偏离值并判断是否与问题的趋势一致,如果一致先调整到理论位置。
其次将零件置于夹具之上,观察零件与定位面和定位销的对应状况,调整确保零件与定位面之间无干涉部位。
再次,检查零件在夹具上定位后是否有转动或移动现象,记录定位销与零件孔的对应尺寸,结合材料检测数据和车身的尺寸数据分析结果,形成对定位销和面的整改措施。
原则上,材料有问题先整改材料,然后整改机器(焊接夹具),但实际上只要材料状态保持稳定,很多车身尺寸问题都是通过夹具整改完成的,因为夹具整改相对来说更有效率也更经济。
车身尺寸在开发完成进入批量生产一段时期以后,材料和机器也相对稳定,这时只要定期检测材料和机器的状态,及时维护保持稳定就可以了,同时需要把精力转到对人员和工艺方法的执行管理方面。
在批量生产阶段,通过SPC控制图可以预防一些定位销、面松动和磨损的情况。
#p#结语车身尺寸控制是一个系统工程,全顺工厂结合自身产品的特点,通过不断地总结和探索找到了一个适合自己的车身尺寸控制方法。
当然,万变不离其宗,关键是要抓住根本,控制车身的变差源。
随着汽车产业的不断发展,市场竞争日益加剧,我们会不断探索,使我们的控制手段更加高效、经济,以在市场中立于不败之地。
您可以阅读与有效的车身尺寸控制方法相关的内容:•浅谈车门与白车身尺寸匹配控制方法•提高白车身尺寸控制精度的方法•基于三坐标测量的车身精度控制方法和技巧•基于功能分析的尺寸控制方法•白车身尺寸精度控制•车身尺寸检测与精度控制解决方案•工装基准与车身尺寸的关系•实现车身焊接质量的有效控制•机器人激光检测在白车身尺寸测试的运用•冲压件的回弹控制方法网友评论发表评论。