高精度珩磨头磨头体的参数优化
铰珩磨头的拆卸工具优化

1 序言连杆大孔的光整加工采用的是铰珩工艺,与珩磨技术中珩磨头与主轴采用浮动联接不同的是,铰珩磨头与机床主轴采用刚性联接。
铰珩除了具有精度高、表面质量好的优点,还能一定程度上修正被加工孔的位置度,因此铰珩主轴跳动等精度要求也比珩磨主轴要求更高。
2 背景介绍连杆的AF90是对连杆大孔珩磨的工序(见图1),加工精度φ(50.606±0.006)mm。
连杆大孔在发动机装配过程中与曲轴连杆颈配合,将活塞的爆炸做功通过连杆传递到曲轴。
连杆与曲轴的配合精度直接影响发动机运行过程的平稳性和噪声强弱,因此连杆大孔采用珩磨工艺。
珩磨是利用珩磨头(见图2)上圆周分布的砂条(油石)对内孔表面进行光整加工的一种工艺。
其工作过程是心轴在弹簧力的作用下向上顶起,膨胀块径向收缩。
当珩磨头进入到连杆大孔中,机床主轴内的推杆推动心轴克服弹簧力向下运动。
通过心轴和膨胀块的锥面配合,将心轴的向下运动转换为膨胀块的径向扩张。
固定在膨胀块外缘的砂条贴在工件内孔表面。
珩磨机主轴开始旋转和轴向往复运动,实现对孔壁表面的磨削加工。
由于珩磨需要实现砂条的径向膨胀运动,在珩磨头内部设计了带锥度的心轴,因此铰珩磨头没有办法采用类似普通铣床7∶24锥柄尾部内螺纹、拉杆的联接结构。
原有的珩磨头更换拆装方式:对刀杆起锁紧作用的圆螺母外套一个专用扳手,用锤子敲击扳手,利用主轴的惯性和敲击的冲击力拆卸珩磨头。
a)珩磨机主轴与珩磨头联接方式b)珩磨头图1珩磨机主轴与珩磨头联接方式及珩磨头图2珩磨头1—防尘圈2—锥柄3—心轴4—膨胀块5—砂条6、8—弹簧7—轴9—端盖该方式存在以下问题。
1)锤子敲击过程对机床主轴的轴承有一定冲击。
AF90珩磨机是精密加工设备,长期靠敲击主轴拆卸珩磨头会造成主轴跳动增加,珩磨后孔壁产生振纹。
造成设备损坏,增加维修成本和停机损失。
2)通过锤子敲击的方式,需要有较大的手臂摆动量,才能积累起足够的动能。
机床内部结构较小,手臂水平方向挥动容易撞到机床内部支架,造成人员受伤等问题。
珩磨加工参数设定参考资料

珩磨加工参数设定参考资料一、珩磨机相关技术规格:1.2MK228A/12.2MK225/13.加工参数1) P1:对刀点。
单位:mm2)P2:工进量。
单位:㎜。
顶杆的移动量。
最小设定值0.001㎜。
3)P3:工进速度。
单位:㎜/min(毫米/每分钟)。
此值可在0~2㎜/ min之间连续设定。
4)P4:刀具磨损补偿量。
单位:㎜。
根据刀具的磨损值设定此参数,并于P6和P7配合使用。
5)P6:补偿次数。
单位:次。
根据加工多少件补偿一次设定此值。
设定为0,表示不补偿;设定为1.则每加工一件补偿一次;设定为2,表示第一件不补偿,第二件补偿;以此类推。
6)P7:有无补偿。
若设定为0,表示没有补偿;若设定其他值,则表示有补偿。
7)精珩时间:单位:S(秒)。
精珩时间最长可设定为99秒。
二、珩磨前的准备工作:1.工装调整:1)选择适用的珩磨杆、瓦,将其装在主轴上面。
2)将定位盘装在工装上面。
3)根据产品的顶深调整珩磨深度。
2.产品分类要求:(采用分组珩磨的方法)1)磨后成品尺寸要求¢D 0/+0.03的内孔分组要求:珩磨前把镀后内孔尺寸进行分组,0.01㎜为一组,即¢D-0.01~0、0~+0.01、+0.01~+0.02三组,尺寸在-0.01~-0.02㎜的检出,单独设定珩磨参数加工。
尺寸大于+0.02㎜的退电镀返镀。
2)磨后成品尺寸要求¢D 0/+0.025的内孔分组要求:珩磨前把镀后内孔进行分组,即¢D-0.01~0、0~+0.015两组,尺寸在-0.01~-0.02㎜的检出,单独设定珩磨参数加工。
尺寸大于+0.015㎜的退电镀返镀。
3)将内孔返镀产品与内孔第一次电镀产品区分,上述分组要求是针对内孔第一次电镀的产品。
为避免内孔珩磨不光,返镀(内孔粗糙)的产品直径尺寸应控制在¢D -0.03/0,这类产品检出后单独设定珩磨参数加工。
三、加工参数的设定:(以缸径¢40为例)1.对刀点的设定:(分组对刀)1)珩磨杆、瓦装好后,将工作台落下,将缸体内孔套在珩磨瓦上,点动膨胀键。
提高珩磨精度作业指导书

徐州光环公司珩磨缸筒精度作业指导书
1、油磨石的选择:
选择合理的油磨石粗珩用80#~180#;半精珩用180#~280#;精珩用W40以上;抛光用GXK56.P600-800粒度棕刚玉砂布。
油石的硬度对珩磨工件的表面粗糙度有很大影响。
珩磨油石太软,精珩时磨粒易脱落,抛光作用差,不易获得较好的表面质量。
珩磨油石太硬,已磨耗的磨粒不易脱落,油石自锐性不良,油石表面易堵塞,磨削性能低甚至消失,工件表面质量低劣,容易引起工件表面烧伤。
考虑油石的自锐性,珩磨硬金属要选较软的油石;珩磨软金属则要选择较硬的油石;工件材质太软,则应选硬的或粒度细的或注蜡的油石。
2、工件转速与珩磨头连杆速度选择:
连杆往复运动速度10m/min不变。
粗珩工件的旋转速度100 r/min,;精珩时应提高到150~200 r/min 。
3、余量参考:
粗珩0.06~0.15mm;精珩0.04~0.08mm;抛光0.01~0.03mm。
抛光工序: 抛光须采用GXK56P600-800粒度的棕刚玉砂布,在精珩工件转速不变连杆往复运动速度不变的参数下进行5-8分钟。
4、粗糙度要求:
Ø50—500缸径的内孔粗糙度,经过粗珩、精珩、抛光以后要达到Ra 0.2级以上。
5、操作者应根据珩磨条的磨损情况及时更换新的珩磨条,以此保证磨削量的均匀,达到缸筒在磨削过程中,前部、中部、后部的磨削尺寸一致。
6、加大切削液的工作压力,并过滤处理。
定期更换磨削液。
技术部
2012.09.30。
双进给珩磨头灵敏度元分析及结构优化

l 48
Ma c h i n e r y D e s i g n &
Ma n u a c t u r e
第1 1 期 2 0 1 3年 l 1 月
双进给珩磨 头灵敏度元分析及 结构优化
侯 杰 文
( 兰州理工大学 机 电工程学院, 甘肃 兰州 7 3 0 0 5 0 )
结构参数对加工质量影响的规律 。 关键词 : 双进给珩磨头 ; 灵敏度分析 ; 结构优化 中图分类号 : T H1 6 ; T G 5 8 0 . 6 7 文献标识码 : A 文章编号 : 1 0 0 1 — 3 9 9 7 ( 2 0 1 3 ) 1 1 - 0 1 4 8 - 0 3
Du a l — — F e e d Ho n i n g He a d Se n s i t i v i t y E l e me n t An a l y s i s a n d St r u c t u r e Op t i mi z a t i o n
HOU J i e — . w e n ( C o l l e g e o f Me c h a n i c a l a n d E l e c t i r c a l E n g i n e e i r n g , L a n z h o u U n i v e r s i t y o f T e c h n o l o g y , G a n s u L a n z h o u 7 3 0 0 5 0 , C h i n a )
h o n i n gpr o c e s s t o i m p r o v e t h e ma c h i n i n gp r e c i s i o n .An d u s i n g n o n - c o n t ct a pn eu ma t i c me a s u r i n g. e s h o n i n g h e d a r e di z e
瓷砖抛光磨头磨削参数优化
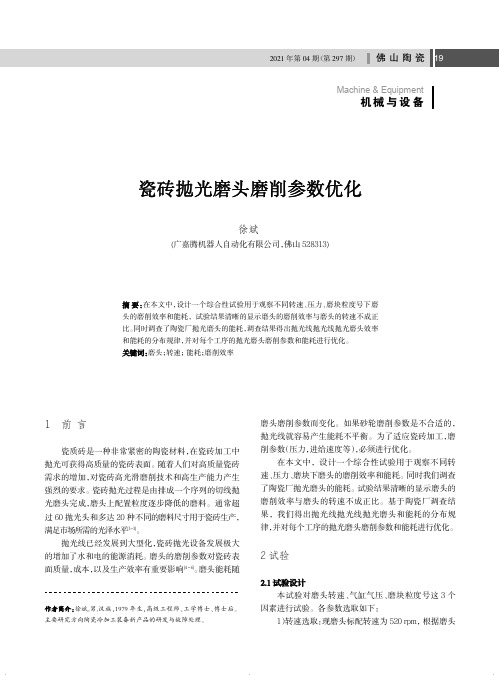
,1979年生,高级工程师、工学博士、博士后。
主要研究方向陶瓷冷加工装备新产品的研发与故障处理。
1前言瓷质砖是一种非常紧密的陶瓷材料,在瓷砖加工中抛光可获得高质量的瓷砖表面。
随着人们对高质量瓷砖需求的增加,对瓷砖高光滑磨削技术和高生产能力产生强烈的要求。
瓷砖抛光过程是由排成一个序列的切线抛光磨头完成,磨头上配置粒度逐步降低的磨料。
通常超过60抛光头和多达20种不同的磨料尺寸用于瓷砖生产,满足市场所需的光泽水平[1~3]。
抛光线已经发展到大型化,瓷砖抛光设备发展极大的增加了水和电的能源消耗。
磨头的磨削参数对瓷砖表面质量,成本,以及生产效率有重要影响[4~6]。
磨头能耗随磨头磨削参数而变化。
如果砂轮磨削参数是不合适的,抛光线就容易产生能耗不平衡。
为了适应瓷砖加工,磨削参数(压力,进给速度等),必须进行优化。
在本文中,设计一个综合性试验用于观察不同转速、压力、磨块下磨头的磨削效率和能耗。
同时我们调查了陶瓷厂抛光磨头的能耗。
试验结果清晰的显示磨头的磨削效率与磨头的转速不成正比。
基于陶瓷厂调查结果,我们得出抛光线抛光线抛光磨头和能耗的分布规律,并对每个工序的抛光磨头磨削参数和能耗进行优化。
2试验本试验对磨头转速、气缸气压、磨块粒度号这3个因素进行试验。
各参数选取如下:1)转速选取:现磨头标配转速为520rpm,根据磨头设计一个综合性试验用于观察不同转速、压力、磨块粒度号下磨头的磨削效率和能耗,试验结果清晰的显示磨头的磨削效率与磨头的转速不成正比。
同时调查了陶瓷厂抛光磨头的能耗,调查结果得出抛光线抛光线抛光磨头效率和能耗的分布规律,并对每个工序的抛光磨头磨削参数和能耗进行优化。
转速;能耗;磨削效率徐斌(广嘉腾机器人自动化有限公司,佛山528313)机械与设备Machine &Equipment表3配置240#碳化硅磨块磨头的磨削效率和能耗磨头转速(rpm)瓷砖磨削量(Kg)磨头最大电流(A)0.2MPa 0.3MPa 0.4MPa 0.2MPa 0.3MPa 0.4MPa 4700.600.600.702325275200.800.700.802427305400.650.700.952530385600.750.750.852*********.75 1.000.952738386100.850.950.90283336表2配置46#金刚石磨块磨头的磨削效率和能耗磨头转速(rpm)瓷砖磨削量(kg)磨头最大电流(A)0.2MPa 0.3MPa 0.4MPa 0.2MPa 0.3MPa 0.4MPa 470 4.53 5.6 6.4171922520 4.67 5.68.81619225407.877.478.93182122560 6.007.338.131******** 4.93 4.93 5.601824226104.535.47 5.73182323小皮带轮轴心尺寸和传动比,试验转速取值540rpm,560rpm,590rpm,610rpm。
珩磨的加工原理、珩磨加工的特点以及珩磨主要参数的选择

珩磨的加工原理、珩磨加工的特点以及珩磨主要参数的选择(一)珩磨的加工原理珩磨加工的工具主要采用珩磨头。
珩磨加工时有三种运动,即油石的径向进给、珩磨头的旋转和上、下往复运动。
珩磨头的旋转和上下运动是主运动,完成微量磨削和抛光加工;珩磨头的旋转和上下往复运动,使油石的磨粒走过的轨迹交叉成网状,因而容易获得较小的表面粗糙度;珩磨加工是以工件孔导向;珩磨头与珩磨机应浮动连接。
(二)珩磨加工的特点(1)加工精度高精度可达IT6、圆度、圆柱度可达0.003~0.005mm,但不能纠正上道工序的位置公差。
(2)表面质量好表面粗糙度可达Ra0.2~0.04,甚至0.02;且不烧伤表面。
(3)效率高。
(4)应用范围广可加工Ф5~Ф500mm的工件,长径比L/D可达10,可加工铸铁、钢(淬硬、未淬硬)。
但不适合加工断续表面及韧性高的金属材料。
(三)珩磨主要参数的选择1.油石的选择(1)材料的选择钢件选刚玉,铸铁选碳化硅。
(2)粒度的选择根据表面粗糙度要求不同选取。
表面粗糙度要求为Ra0.4~0.2时,选粒度为120#~W40;表面粗糙度要求为Ra0.2~0.04时,选粒度为W40~W20;表面粗糙度要求为Ra0.02~0.01,选粒度为W20~W14。
(3)硬度的选择一般选R3~ZY1。
2.切削用量的选择粗珩:θ=40°~60°,精珩θ=20°~40°;圆周速度:未淬硬36~49m/min,淬硬23~36m/min,铸铁61~70 m/min;油石压力:粗加工铸铁0.5~1N/mm2,粗加工钢0.8~2N/mm2,精加工铸铁0.2~0.5N/mm2,精加工钢0.4~0.8N/mm2,超精加工0.05~0.1N/mm2。
3.加工余量的选择一般0.1mm以下。
4.切削液的选择一般选60%~90%的煤油加40%~10%的硫化油或动物油。
加工青铜时,用水或干珩。
参考资料:/supply/index.html。
珩齿加工机床珩磨头部分的设计

摘要随着科学技术的发展,即使原来属于先进的机床也会变得陈旧、落后,满足不了产品种类日益增加和质量不断提高的需要,因此有必要以现有的机床为基础,对机床的使用工艺和装备进行革新,对机床的现有结构进行改装。
这样既可以使现有机床的加工能力得以提高,同时又能节约新机床设计研发时间,可以得到许多意想不到得效果。
本次毕业设计的题目是珩齿加工机床的珩磨头部分设计,这是在普通车床上面进行改进设计的。
本改装采用的是双面变压珩磨法,珩磨轮与工件的啮合关系、运动情况和剃齿大体上相同;其特点是工件带动珩磨轮正反转动,珩磨轮沿轴线作往复直线运动。
但径向运动不像剃齿那样在每次往复行程后都有一次进给,而是按珩齿所需要的初压力调整好珩磨轮与工件的中心距,开车后一次进给到预定的位置。
珩齿开始时齿面的压力较大,随后逐渐减小,直至接近消失时珩齿结束。
应当指出,虽然珩齿的运动和剃齿大体相同,珩轮的结构和剃齿刀比较相似,但是珩齿过程的本质和剃齿是不相同的,其特点如下:(1) 珩轮的齿面上均匀密布着磨粒,各磨粒间以粘结剂相隔.珩磨速度远比磨削时低.因此,珩齿切削过程的本质是低速磨削﹑研磨和抛光的的综合过程。
(2) 珩轮的磨粒可以看成是十分接近的连续的切削刃,珩齿的过程可以接近于连续挤压的过程.因此,珩磨后齿面上的切削纹路很细,光洁度比剃齿高,不会产生冷硬现象。
(3) 珩轮弹性大,不能强行切下误差部分的金属,因此,珩齿修正误差的能力没有剃齿强.而另一方面,珩轮本身的误差,也就不会全部反映到齿轮上,因此珩轮的精度要求不高,而对珩前的齿轮则要求较高的精度.珩齿主要用于改善表面质量。
(4) 珩齿时,齿面间除了沿齿向产生滑动切削外,沿渐开线方向的滑动使磨粒也能切削,于是就构成了齿面刀痕的复杂纹路,使齿面的光洁度提高。
本改装是在普通车床上进行的,主要用于除去齿轮热处理后的氧化皮及毛刺,可使光洁度从▽6提高到▽8~10,齿轮传动噪声也略有降低,生产率很高.但对齿形和齿向误差的纠正很不稳定,有时甚至会使齿形误差有所增大。
珩磨工艺参数的优化设计

程 次数 为
整理 得 出
X・ s ≥竹 一 L ・ c o t O — b
≥( 竹 n — ・ c o t O - b) / s
f T l = ( 竹 n — L ‘ c o t O - b) / ( s )
( 1 2 )
( 1 3 )
迹 与它 当前 位 置对 应并 与 之左 侧 邻 近 的前 次往 复 行程 轨 迹 相交 , 保 证 了珩 磨 轨迹 的完整 性 。如 图 1 中, 油石 C 的 珩磨 轨迹 与 e的珩磨 轨迹 相 交 。
・ c o t O >(  ̄ k - 1 ) 竹 n — s — b ( k = O , 1 , 2 , …… , n 一 1 )
( 1 4)
给 定 工 件
尺寸和工具参
数 ,因 此 图 3 中 的一 些 变 量
珩 磨 中 不 宜设 计 使 用 的运 动8参 数 表 4 4 6
珩磨 主轴转速/ r ・ m i n
∞
即一 个零 件 表 面完整 加工 的最 短 加工 时 间 t 为
醯 m・ g 8 g 8 油石 往复速度/ a r i n
及往 复速度 均可 以合理 调整 ,避免 加工 轨迹 的重 5 结
复循环 , 保证 被加 工表 面珩 磨轨 迹均 匀 完整 , 以 最 短 时 间 完 成 工 件 的 加 工 ,从 而 设 计 出 合 理 的 珩 磨 加 工
框 图 如 图 3所 示 。 4 分 析 结果
语
建立珩磨加工工艺参数的优化设计依据, 便可以设计 出相应的参数选择程序 。在实际生产中, 可根据具体加工 数。对珩磨加工工艺参数进行设计 , 是实际珩磨生产中必 不 可少 的过 程 , 它从 工艺上 保证 了工件 的加 工表 面质量 。
- 1、下载文档前请自行甄别文档内容的完整性,平台不提供额外的编辑、内容补充、找答案等附加服务。
- 2、"仅部分预览"的文档,不可在线预览部分如存在完整性等问题,可反馈申请退款(可完整预览的文档不适用该条件!)。
- 3、如文档侵犯您的权益,请联系客服反馈,我们会尽快为您处理(人工客服工作时间:9:00-18:30)。
D. 10.5 -0.006 5 23.795 Ⅳ. 1.6 O.007 2 62.136 形t -2.8 -0.003 8 -2.29
437E+08
130E+09
216E+09
302F+09
388E+09
▲罔1
廖央体的f苴,J分析
2正交试验设计
2.1
试验参数选取 在应力分析计算时,选取磨头体最大应力、最大位
表2试验参数 参数
l 2 3 DI/mm 42 40 38 HI/nun 16 ll 6 W,/nun 16.5 11 6
常数
-33.8 0.363 6 461.64
应力系数 位移系数
质量系数
3磨头体的轻■化
3.1设计变量 设计的变量为最顶端支撑件的直径(D。)、油石座 顶部厚度(日。)、磨头体底座长度(矽。)。 3.2 目标函数建立 对于珩磨头磨头体的轻量化设计,其目标函数就 是在保证其应力、应变和最大位移都符合刚度要求的 前提下,质量最轻。所以目标函数为:
珩磨作为一种高效加工方法。不仅能去除较大的 加工余量,也是一种提高工件尺寸、几何形状精度和降 低表面粗糙度值的有效加工方法N-2]。珩磨加工过程 中,珩磨头在缸套内作上下往复运动.在高速换向的情 况下,其往复速度≥30 n,-Wmin、加速度≥2.59,磨头质 量及惯性对珩磨机性能有一定影响.进而影响到珩磨 质量。因此,磨头体设计时应考虑在保证自身刚度的 前提下,尽量减小质量。即实现磨头体轻量化设计[3]。 近年来,实现轻量化主要有采用轻型材料[4]和结 构优化[5]两种途径。清华大学吕毅宁、吕振华等对薄壁 结构用轻型材料替代方法实现轻量化,减重效果明显: 郭永辉、王源绍等人致力于结构优化方面的研究来实 现轻量化目标。现阶段轻量化方法主要应用在机床、 汽车、铁路运输机械等领域,机械零件的结构优化逐年 推广,且势头迅猛。 目前,珩磨头结构优化㈨中尺寸优化的理论和应
16 ll 6 ll 6 11 6 1l 6
16.5 11 40l 418 373 480 387 398 366 490
』J
4 5 6 7 8 9
雾|髂
l_
l删
z
2.3构造回归函数方程 由表3看出.9组试验结果中最大应力为490 MPa.最大位移为0.204 mm。未超过材料屈服强度785
…嘉毳篙:嬲鬻麓裟淼盎:
上海交通大学.2009.
[5]赵东辉,金长虹,乔伟杰.制动盘平衡机去重模块虚拟样机 的设计与研究[J].机床与液压,2009,37(7):239—243.
[6]张青雷,沈海鸥,王少波,等.高速动平衡机摆架振动特性
参考文献
[1]胡会杰.全自动轮胎动平衡试验机的研制[D].东营:中国
-.-J-__.
同
C=
精度珩磨头磨头体的参数优化
口廖秋岩1,2 口张龙波1,2 口樊思敏1,2
兰州730050
1.兰州理工大学数字制造技术与应用省部共建教育部重点实验室
2.兰州理工大学机电工程学院兰州730050
摘
要:运用SolidWorks软件对珩磨头磨头体进行参数化建模,通过正交试验模拟实际工况,利用ANSYS分析得出
D,/nun
42 40 40 38 38 40 40 38 38
H,/nun
Ⅳ./nun
最大应力,
MPh
最大位移/
mm 0.145 0.184 0.181 0.161 0.202 O.160 0.173 0.173 0.204
总质量,
g 2 318.57 l 814.70 1 991.24 l 971.75 l 767.12 l 983.20 l 870.33 1 935.6l 1 822.75
+国家重大科技专项(编号:2010ZX04001—181) 甘肃省自然科学基金资助项目(编号:1112RJZA025)
收稿日期:2014年8月
用已趋于成熟,形状优化的理论已经基本建立,并趋向 于着重解决实际应用方面的问题。结构拓扑优化由于 理论和计算上的复杂性而成为结构优化中最富有挑战 性的研究领域。本文根据珩磨头磨头体的结构特点,通 过构建结构主要参数与其应力、位移之间的线性回归 方程.得出最优修改方案,最终达到轻量化的目的。
石油大学.2011.
分析与改进[J].工程设计学报,2012,119(2):91—95. [7]石清鑫,袁奇,胡永康250t高速动平衡机摆架的动刚度分
析[J].机械工程学报,201l,47(1):76—79.
[2]周瑾,王玉龙,郭勤涛.基于动平衡机有限元模型的无试重
动平衡方法[J].江苏大学学报,2013,34(1):72—75.
3.3.3几何约束 根据磨头体的基本尺寸确定参数的最大、最小变 形,从而得出参数的几何约束:
y(3)=40-Dl Y(4)--/9I-38 y(5)=16-HI y(6);日l一6 (4) (5) (6) (7) (8) (9)
y(7)=16.5一Wl l,(8)=形广6
3.4数学模型的建立 根据上述构造的目标函数和约束函数,得出珩磨 头磨头体轻量化的数学模型为: 设计变量:X={D。,日l,形。l 约束方程:y(i)≤O(i=1,2,…,8) 目标函数:
minF(X)=23.795Dl+62.1 36日l一2.29w1+461.64
3.5
参考文献
[1]熊元一,郭建忠,侯军丽.珩磨工艺原理简介[J].机械工人
(冷加工),2004(5):29—30.
[2]苏达智.珩磨工艺技术[Z].银川:宁夏机械工程学会,2006. [3]贾维新,郝志勇,徐红梅.基于结构优化方法的单缸机机体 轻量化设计[J].浙江大学学报(工学版),2008(2):224—
785
优化前
优化后 改变量 改变比例
MPa,取安全系数为2,则[盯J=393 MPa。可得出强
度的约束函数,即盯一一[盯]≤0。 则应力约束函数为:
y(1)=10.5Dl+1.6日广2.8形l一33.8 (2)
由表5可以看出,优化后的应力有所减小,满足安 全系数为2的强度要求;最大位移有所增加,但未超出 极限变形值,符合实际的工况要求。优化后质量减少了 14.55%.得到满足刚度条件下的最优磨头体质量。
8
[5]冯帧.拓扑优化在产品设计中的应用探索[J].机械设计与
制造,2007(3):138一139.
[6]侯运丰,张志万.珩磨顶杆的有限元分析及结构优化[Jj.
机械设计与制造,2012(8):23—25.
盛
机械制造53卷第605期
2015/1回
万方数据
minF(X)=23.795D1+62.136H广2.29形1+461.64
(1)
优化后的最大应力、位移值。将数值代入强度、刚度约 束函数中。看其是否满足磨头体自身刚度要求。对比结 果见表5。
表5优化前后各性能结果 名称 最大应力,MPa
388 370 一18 --4.64%
移以及自身质量为正交试验的指标。对整体结果影响 的因素有很多,根据对磨头体的应力分析,选取应力、 位移变化不大之处为主要试验参数。通过图1可确定 最终的修改参数有:最顶端支撑件的直径(D。)、油石座 顶部厚度(日。)、磨头体底座长度(W。)。暂不考虑其它因 素的影响。 为方便检测各参数对试验结果的影响。选取原方 案的设计尺寸为基本尺寸。各个参数尺寸在基本尺寸 上下浮动,变化的大小基本一致,见表2。
裹3正交试验计算结果 试验号
l 2 3
l材料名称
40Cr
弹性模量 Ef(沿a
21l
泊松比p p|(kg・m。、
0.277 7 870
密度
屈服强度
,MPa 785
抗拉强度
,MPa 980
根据磨头体的结构形式和受力特点.利用ANSYS 软件选取自由划分网格[91,结构单元类型定义为8节 点的Solidl85。网格划分在油石座与磨头体接触之处 进行细化。在珩磨工作中,最上端不受力的作用,可在 磨头体上端两个孑L添加全约束.在磨头体安装油石座 孔端受圆周切削力。上下两端面受轴向切削力.取油 石座对磨头体的工作压力为2 MPa.对磨头体进行静 应力分析,如图l所示。
1
1.1
参数化建模及有限元分析
建立参数化模型 磨头体结构模型的参数化有利于不同尺寸有限元
模型的快速建立,节省了优化分析的时间。基于CAD 软件SolidWorks…的底层开发接口.并利用VC++语 言,对珩磨头磨头体模型进行尺寸重构。有限元分析 时,利用SolidWorks和ANSYS Workbench[81软件间的 无缝连接进行转换,对磨头体进行应力分析。 磨头体尺寸的参数化.需事先预定义模型各尺寸
应力分布云图。根据所得的试验样本,运用数值分析方法得出最大应力、位移与结构主要参数间的线性关系。依据最优准
则法计算优化的数学模型,获得最终的轻量化方案,为双进给珩磨头的轻量化提供了理论依据。
关键词:高精度珩磨头磨头体参数优化 中图分类号:THl23;TG74+.7 文献标识码:A
文章编号:1000—4998(2015)01—0030—03
259E加9
.345E+09
l:
67 11 25
.867E+08
l 73E+09
MPa。位移变形也在范围之内。因此改变因素参数对磨 头体整体的刚度影响较小。从而证明修改参数准确,符 合轻量化要求。 根据表3所得到的试验结果.应用数值分析最小 二乘法原理,构造正交矩阵,代人试验数据仿真计算, 得机身最大应力、最大位移和磨头体重量与结构主参 数的回归系数。见表4。
3.3约束函数 磨头体的优化设计必须在减轻自身重量的同时, 满足自身的应力和位移限制需求。
3.3.1
强度状态变量及约束函数
最大位移/nan
0.145 0.16 0.015 lo.34%
总质量,g