乙苯工艺流程说明复习课程
乙苯制苯乙烯讲解学习

乙苯制苯乙烯南京工业大学化学化工学院《化工过程与工艺设计》设计题目乙苯脱氢制苯乙烯装置工艺设计学生姓名吴美妍班级、学号化工100704指导教师姓名林陵设计时间 2013年 6 月27日-2013 年7月12日课程设计成绩:指导教师签字目录第一部分设计说明书第一部分设计说明书 (5)前言 (5)第一章概述 (6)1.1生产方法 (6)1.2工艺流程 (6)1.3乙苯脱氢生产方法 (7)第二章原料与产品性质 (8)2.1原料 (8)2.2产品 (9)第三章主要设备选型 (10)第四章安全措施与劳动保护 (11)4.1安全标准 (11)4.2安全管理规定和劳动保护 (11)第五章三废排放与治理方案 (13)5.1.1化工“三废”的处理 (13)5.1.2废气 (13)5.1.3废渣 (13)5.1.4废液 (14)5.1.5副产品处理一览表 (14)5.1.6 废物处理一览表 (14)第六章原料、中间产品和产品分析方法及频率 (15)第七章生产班制定员 (16)第二部分设计计算书 (16)第一章物料衡算 (16)1.1计算依据 (16)1.2 物料衡算 (17)第二章乙苯塔的热量衡算及塔板数计算 (19)第三章乙苯塔的设计 (23)3.1填料的选择 (23)3.2乙苯塔塔径和填料层高度的计算 (24)3.3塔顶冷凝器和塔釜再沸器 (26)3.3.1塔顶冷凝器 (26)3.3.2塔釜再沸器 (30)3.4管径计算 (34)3.5塔高 (34)3.6附件选择 (35)3.6.1 液体分布器 (35)3.6.2填料压紧装置 (35)3.6.3填料支撑装置 (36)3.6.4液体再分布器装置 (36)3.6.5除沫装置 (36)3.7乙苯塔进料泵 (36)第四章反应器计算(列管式) (37)致谢 (38)参考文献 (39)附录4 PFD图附录5 PID图附录5 平面布置图附录6 立面布置图(可选)第一部分设计说明书前言苯乙烯是一种重要的石油化工基本原料,是除聚乙烯(PE)、聚氯乙烯(PVC)、环氧乙烷(EO)以外的第四大乙烯衍生产品。
工艺流程

PEB回收塔从不可回收的双环化合物如二苯甲烷和二苯乙烷中,分离可回收利用的组分,主要是二乙苯、丁苯和三乙苯。PEB回收塔的操作要求是控制PEB在塔釜残油中含量最少,同时限制馏出物中双环化合物的量。
PEB回收塔在真空下操作。此塔的再沸器使用高压蒸汽,塔顶冷凝器TT-1114产生低低压蒸汽。PEB塔再沸器是用泵循环、抑制汽化的设计,目的是为了获得好的操作弹性和稳定的沸腾状态。从PEB塔回流罐MS-1112来的塔顶凝液用PEB回流泵PP-1112A/S既作为回流送至塔顶,又作为精制循环PEB送至转烷基化反应器。塔釜的出料作为吸收塔的贫油,被PEB塔釜泵PP-1113A/S送至苯乙烯单元的尾气吸收系统。在残油进储罐之前,其可以被PEB残油冷却器TP-1120冷却。一小股泵出口的塔釜物料经TP-1120冷却再经过PEB残油过滤器GF-1138A/S,用作PP-1113A/S的净化冲洗。PEB回收塔的尾气经PEB塔尾气冷凝器的冷却水进一步冷凝,同时PEB塔真空泵PV-1129提供了塔的真空。
转烷基化反应器的进料是苯和PEB的混合物,操作的比例是苯比PEB质量比2.0。循环PEB与苯混合并在转烷基化反应器TT-1102进料加热器中被高压蒸汽加热。当催化剂是新的时,转烷基化反应进料温度期望大约在190oC。渐渐地随着转烷基化反应催化剂活性下降,入口温度会提高到220oC,这是最高的循环温度。
在精馏单元,未反应的苯,PEB和重组分从烷基化和转烷基化反应器出料中分离出来以生产EB产品。EB单元内的精馏单元共有5个塔,其中4个可以由其塔顶馏出物冷凝(放热)而产生可用的蒸汽。
苯回收塔(AS-1101)从烷基化和转烷基化反应器出料中回收苯。经过苯回收塔精馏后的液苯将给烷基化和转烷基化反应器系统进料。苯回收塔的塔釜液给EB回收塔进料。在EB回收塔的塔顶可得到精馏后的高纯度乙苯。EB回收塔的塔釜液给PEB回收塔进料,PEB回收塔可以从重组分中分离出PEB和其他更高级的烷基苯。纯净的PEB馏出物给转烷基化反应器系统进料,PEB回收塔的塔釜液将作为苯乙烯单元的贫油吸收剂,最终作为燃料油焚烧。为了移除在反应器中产生的和进料带来的水和少量的烃(碳氢化合物)组分,还提供了一个轻组分塔。轻组分浓缩后和苯乙烯单元排放气一起通入苯乙烯单元的尾气吸收系统最终进入氢气压缩机或作为苯乙烯单元的蒸汽加热炉燃料。
(整理)乙苯单元操作法.

25万吨/年苯乙烯装置操作法常州新日化学有限公司目录1 岗位任务和管理范围 (1)1.1 岗位任务 (1)1.2 管理范围 (1)2 产品和原材料规格 (3)2.1 苯...................................................................................... (3)2.2 乙烯2.3 催化剂2.4 白土3 工艺流程说明3.1烃化反应和后烃化反应系统3.1.1 烃化反应3.1.2 后烃化反应3.1.3 蒸汽发生3.2 烃化液精馏系统4 开车前的准备工作5 投料开车6 正常操作6.1 正常控制的指标6.2 主要操作参数的控制7 停车操作 (20)7.1 正常停车7.2 紧急停车8 异常现象分析 (23)9 安全生产规定以上是氧化岗位操作法的目录格式。
在操作法的最后还附有工艺流程简图和安全生产规定。
1 岗位任务及管理范围1.1 岗位任务乙苯单元岗位的任务是将界区外来的乙烯和来自苯回收塔塔顶采出泵P-1202A/B的苯按一定比率通入二个串联操作的反应器(前烃化反应器R-1101和后烃化反应器R-1102),在加热至200℃及分子筛催化剂EBZ-500及作用下进行烃化反应生成粗乙苯,另外原料苯首先在保护反应器R-1104中脱除苯中催化剂毒物,对前烃化反应器R-1101和后烃化反应器R-1102中的催化剂起到保护作用。
而乙苯精馏单元回收的多乙苯和苯按比率加入反烃化反应器R-1103中,在加热至190℃及分子筛催化剂EBZ-100作用下发生反烃化反应生成粗乙苯。
反应生成的烃化混合液和反烃化混合液送至苯回收塔T-1201进行苯回收及粗乙苯分离,粗乙苯在乙苯回收塔T-1203进行精制得高纯度中间产品乙苯,乙苯回收塔T-1203塔釜液去多乙苯回收塔T-1204进行多乙苯回收去后烃化反应器R-1103反应得反烃化液。
本岗位还负责烃化/后烃化催化剂离线再生任务。
乙苯装置工艺流程及生产原理
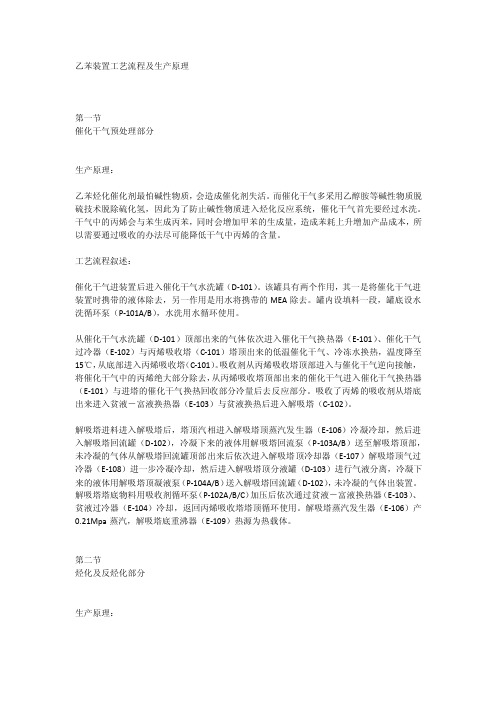
乙苯装置工艺流程及生产原理第一节催化干气预处理部分生产原理:乙苯烃化催化剂最怕碱性物质,会造成催化剂失活。
而催化干气多采用乙醇胺等碱性物质脱硫技术脱除硫化氢,因此为了防止碱性物质进入烃化反应系统,催化干气首先要经过水洗。
干气中的丙烯会与苯生成丙苯,同时会增加甲苯的生成量,造成苯耗上升增加产品成本,所以需要通过吸收的办法尽可能降低干气中丙烯的含量。
工艺流程叙述:催化干气进装置后进入催化干气水洗罐(D-101)。
该罐具有两个作用,其一是将催化干气进装置时携带的液体除去,另一作用是用水将携带的MEA除去。
罐内设填料一段,罐底设水洗循环泵(P-101A/B),水洗用水循环使用。
从催化干气水洗罐(D-101)顶部出来的气体依次进入催化干气换热器(E-101)、催化干气过冷器(E-102)与丙烯吸收塔(C-101)塔顶出来的低温催化干气、冷冻水换热,温度降至15℃,从底部进入丙烯吸收塔(C-101)。
吸收剂从丙烯吸收塔顶部进入与催化干气逆向接触,将催化干气中的丙烯绝大部分除去,从丙烯吸收塔顶部出来的催化干气进入催化干气换热器(E-101)与进塔的催化干气换热回收部分冷量后去反应部分。
吸收了丙烯的吸收剂从塔底出来进入贫液-富液换热器(E-103)与贫液换热后进入解吸塔(C-102)。
解吸塔进料进入解吸塔后,塔顶汽相进入解吸塔顶蒸汽发生器(E-106)冷凝冷却,然后进入解吸塔回流罐(D-102),冷凝下来的液体用解吸塔回流泵(P-103A/B)送至解吸塔顶部,未冷凝的气体从解吸塔回流罐顶部出来后依次进入解吸塔顶冷却器(E-107)解吸塔顶气过冷器(E-108)进一步冷凝冷却,然后进入解吸塔顶分液罐(D-103)进行气液分离,冷凝下来的液体用解吸塔顶凝液泵(P-104A/B)送入解吸塔回流罐(D-102),未冷凝的气体出装置。
解吸塔塔底物料用吸收剂循环泵(P-102A/B/C)加压后依次通过贫液-富液换热器(E-103)、贫液过冷器(E-104)冷却,返回丙烯吸收塔塔顶循环使用。
干气制乙苯流程说明

工艺流程说明一干气制乙苯包括脱丙烯、烃化及反烃化反应、吸收及苯回收、乙苯分离等四个工艺过程。
1 脱丙烯:来自界区外的催化干气进入催化干气水洗罐(D-101),通过水洗除去催化干气中可能夹带的脱硫剂乙醇胺,以免造成烃化催化剂中毒失活。
由催化干气水洗罐出来的催化干气经过催化干气换热器(E-101)与丙烯吸收塔(C-101)顶的脱丙烯催化干气换热,再经催化干气过冷器(E-102)冷却到15℃后进入丙烯吸收塔底部。
经过吸收剂吸收丙烯后的脱丙烯催化干气经过催化干气换热器冷却到35℃左右后去烃化反应器(R-101A/B)。
丙烯吸收塔的吸收剂为反烃化料,其主要成分为二乙苯。
丙烯吸收塔底的富吸收剂经过贫液-富液换热器(E-103)后进入解吸塔(C-102)中部第16板,解吸塔底用热载体加热到257℃。
解吸塔釜液由吸收剂循环泵(P-102A/B/C)输送经贫液-富液换热器冷却到40℃,再经贫液过冷器(E-104)过冷到15℃后进入丙烯吸收塔顶部。
解吸塔顶气体经过解吸塔顶蒸汽发生器(E-106)在165℃下部分冷凝进入解吸塔回流罐(D-102),冷凝液由解吸塔回流泵(P-103A/B)输送回流到解吸塔顶部。
由解吸塔回流罐排出的气体经过解吸塔顶气冷却器(E-107)和解吸塔顶气过冷器(E-108)冷却到10℃后进入解吸塔顶气分液罐(D-103),冷凝下的液体由解吸塔顶凝液泵(P-104A/B)送回解吸塔回流罐,不凝的富丙烯催化干气去界区外催化装置或排空管网。
2 烃化及反烃化反应:来自循环苯塔(C-104)11板侧线的循环苯由循环苯塔侧线抽出泵(P-111A/B)输送到循环苯罐(D-105),然后由循环苯泵(P-106A/B)输送一部分进入反烃化反应进料罐(D-106),大部分经过新鲜苯-循环苯换热器(E-115)、反应产物-循环苯换热器(一)(E-111)、反应产物-循环苯换热器(二)(E-110)换热到250℃后进入循环苯加热炉(F-102),循环苯加热炉出来的循环苯达到348℃,进入烃化反应器(R-101A/B)顶部。
乙苯生产工艺流程

乙苯生产工艺流程
《乙苯生产工艺流程》
乙苯是一种重要的有机化合物,广泛用于橡胶、塑料、化妆品等行业。
其生产工艺流程主要分为苯和乙烯的加氢反应,以下是乙苯的生产工艺流程:
1. 原料准备:首先准备苯和乙烯作为生产乙苯的原料,这两种原料通常通过石油提炼或裂解石油得到。
2. 加氢反应:将苯和乙烯送入加氢反应器中,在催化剂的作用下进行加氢反应,生成乙苯。
这个反应需要在一定的温度和压力下进行,控制好反应条件可以提高乙苯的产率。
3. 分离精馏:由于反应生成的产物中可能还含有杂质或未反应的原料,需要进行分离精馏处理。
通过恰当的精馏方法,将乙苯从未反应的原料和其它杂质中分离出来,得到纯净的乙苯产物。
4. 产品脱水:乙苯作为有机溶剂广泛用于化工生产,但其水含量严重影响着产品的质量。
因此,通常需要对乙苯进行脱水处理,降低产品中的水含量。
5. 储存包装:最后将经过处理的乙苯产品进行储存和包装,以便运输到使用场所。
这就是乙苯的生产工艺流程,通过严格控制生产过程和加工工
艺可以得到高纯度的乙苯产品,为相关行业的生产提供了稳定的原料支持。
气相法生产乙苯基本工艺流程
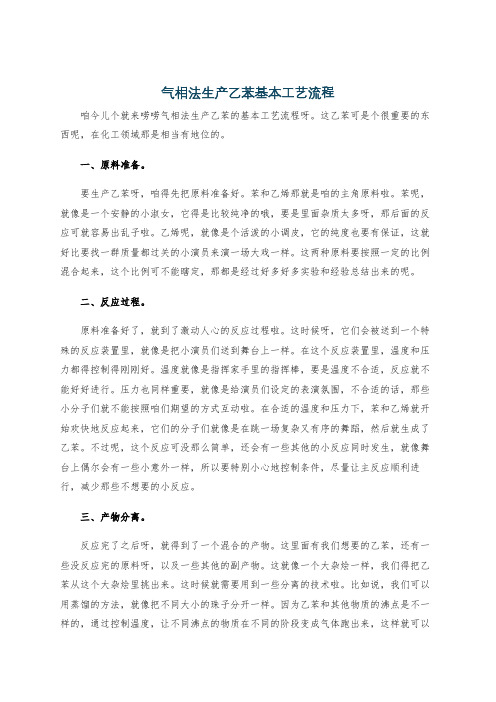
气相法生产乙苯基本工艺流程咱今儿个就来唠唠气相法生产乙苯的基本工艺流程呀。
这乙苯可是个很重要的东西呢,在化工领域那是相当有地位的。
一、原料准备。
要生产乙苯呀,咱得先把原料准备好。
苯和乙烯那就是咱的主角原料啦。
苯呢,就像是一个安静的小淑女,它得是比较纯净的哦,要是里面杂质太多呀,那后面的反应可就容易出乱子啦。
乙烯呢,就像是个活泼的小调皮,它的纯度也要有保证,这就好比要找一群质量都过关的小演员来演一场大戏一样。
这两种原料要按照一定的比例混合起来,这个比例可不能瞎定,那都是经过好多好多实验和经验总结出来的呢。
二、反应过程。
原料准备好了,就到了激动人心的反应过程啦。
这时候呀,它们会被送到一个特殊的反应装置里,就像是把小演员们送到舞台上一样。
在这个反应装置里,温度和压力都得控制得刚刚好。
温度就像是指挥家手里的指挥棒,要是温度不合适,反应就不能好好进行。
压力也同样重要,就像是给演员们设定的表演氛围,不合适的话,那些小分子们就不能按照咱们期望的方式互动啦。
在合适的温度和压力下,苯和乙烯就开始欢快地反应起来,它们的分子们就像是在跳一场复杂又有序的舞蹈,然后就生成了乙苯。
不过呢,这个反应可没那么简单,还会有一些其他的小反应同时发生,就像舞台上偶尔会有一些小意外一样,所以要特别小心地控制条件,尽量让主反应顺利进行,减少那些不想要的小反应。
三、产物分离。
反应完了之后呀,就得到了一个混合的产物。
这里面有我们想要的乙苯,还有一些没反应完的原料呀,以及一些其他的副产物。
这就像一个大杂烩一样,我们得把乙苯从这个大杂烩里挑出来。
这时候就需要用到一些分离的技术啦。
比如说,我们可以用蒸馏的方法,就像把不同大小的珠子分开一样。
因为乙苯和其他物质的沸点是不一样的,通过控制温度,让不同沸点的物质在不同的阶段变成气体跑出来,这样就可以把乙苯和其他东西分开啦。
这一步可得细心呢,要是分不干净,乙苯的纯度就不达标,那就不好用啦。
四、产品精制。
把乙苯从大杂烩里分离出来还不够哦,它可能还不是特别纯净呢。
苯烷基化生产乙苯教学课件
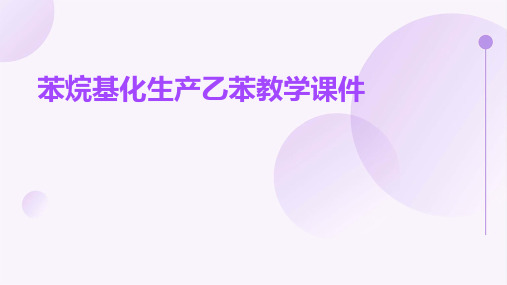
生产现场应配备相应的安全设施,如 紧急停车系统、安全阀、压力表、温 度计等,并确保其正常运行。
严格控制工艺参数,如温度、压力、 流量等,避免因超温、超压、超流量 等导致安全事故。
环保要求与处理措施
苯烷基化生产乙苯过程中产生 的废气、废水和固废应严格按 照国家和地方环保法规进行处
物质的浓度,促进反应的进行。但过高的压力可能导致设备成本增加和
安全性问题。
03
催化剂
催化剂是影响苯烷基化生产乙苯的重要因素之一。不同类型的催化剂对
反应速率和乙苯的产率有不同的影响。选择合适的催化剂可以提高乙苯
的产率和纯度,降低副产物的生成。
03
苯烷基化生产乙苯的工艺流程
原料准备与预处理
原料选择
选择纯度较高的苯作为原料,确 保生产出的乙苯质量稳定。
定期检查
定期对设备进行检查,发现并 解决潜在问题。
清洗与清理
定期清洗设备,去除积聚的杂 质和副产物。
更换磨损件
及时更换磨损的设备和零件, 确保设备的正常运行。
记录与报告
对设备的维护和保养情况进行 记录和报告,为设备的长期运
行提供保障。
05
苯烷基化生产乙苯的安全与环保
安全注意事项
操作人员需经过专业培训,熟悉苯烷 基化生产乙苯的工艺流程和安全操作 规程。
技术进步推动市场拓展
02
苯烷基化生产乙苯技术的不断进步,将进一步拓展市场应用领
域和规模。
国际市场竞争加剧
03
随着全球经济一体化的深入发展,国际市场竞争将更加激烈,
对苯烷基化生产乙苯技术的要求也将越来越高。
政策法规影响
- 1、下载文档前请自行甄别文档内容的完整性,平台不提供额外的编辑、内容补充、找答案等附加服务。
- 2、"仅部分预览"的文档,不可在线预览部分如存在完整性等问题,可反馈申请退款(可完整预览的文档不适用该条件!)。
- 3、如文档侵犯您的权益,请联系客服反馈,我们会尽快为您处理(人工客服工作时间:9:00-18:30)。
乙苯工艺流程说明2.2 工艺说明2.2.1工艺特点技术路线为当今应用广泛、技术成熟可靠、经济合理且无腐蚀无污染的分子筛液相法苯烷基化制乙苯生产技术,所用的分子筛催化剂是AEB 型分子筛催化剂,其主要工艺特点是:1) 新一代的AEB 型烷基化催化剂(AEB-6)和烷基转移催化剂(AEB-1)活性高、乙苯选择性好,具有优良的稳定性,催化剂再生周期长(5年),预期寿命10年。
2) 反应条件缓和,反应压力约3.5-4.2MPaG ,烷基化反应温度190~240℃,烷基转移反应温度175~235℃;副反应少,产品纯度高,二甲苯含量低,乙苯选择性和收率高,工艺物耗低。
3) 使用多点注乙烯加部分反应物循环的工艺流程,可以采用较低的苯/乙烯比,使乙烯能完全溶解在反应物料中,维持液相反应条件,并控制床层温升在合理范围,确保装置平稳运行。
4) 由于反应条件缓和而且催化剂和反应物料均无腐蚀性,使主要设备可采用碳钢。
5) 催化剂采用器外再生,节省了器内再生设备和时间。
6) 采用合理的换热流程,充分回收利用低温能量,能耗低。
2.2.2反应基理2.2.2.1 烷基化反应在一定温度、压力下,乙烯与苯在酸性催化剂上进行烷基化反应生成乙苯,化学方程式如下:56526242H C H C H C H C −→−+同时,生成的乙苯还可以进一步与乙烯反应生成少量二乙苯和更少量的三乙苯,而四乙苯以上的多乙苯很少,方程如下所示:46252565242)(H C H C H C H C H C −→−+363524625242)()(H C H C H C H C H C −→−+264523635242)()(H C H C H C H C H C −→−+H C H C H C H C H C 65522645242)()(−→−+6652655242)()(C H C H C H C H C −→−+理论上讲,从二乙苯一直到六乙苯都可以生成,但是由于苯环上乙基不断地增加,生成四乙苯、五乙苯、六乙苯的难度加大。
这一方面是因为苯环上乙基之间位阻增大,另一方面是因为多乙苯的分子结构越大越妨碍其在催化剂颗粒内的扩散,那么发生进一步反应的机会就越少。
所以,实际上生成的四乙苯很少,而五乙苯、六乙苯几乎没有。
由于目的产物是乙苯,因此在反应系统中应尽量控制多乙苯的生成,特别是四乙苯以上物质的生成。
除以上的反应外,主要的副反应有乙烯与两个苯环发生耦合反应生成二苯基乙烷,乙烯、苯或芳烃自聚生成多环化合物等重质物。
显然,这些物质的生成将降低乙苯产品的收率,增加物耗,因此要最大可能地减少这些副反应的发生。
上述反应是强放热反应,其中乙烯和苯的反应热约为1072.6kJ/ kg 乙苯。
反应热将使物料及催化剂床层的温度升高,为使烷基化反应在最佳条件下进行,需采取措施,不断取走多余的热量,控制反应温度和床层温升在合适的范围内。
在反应条件下,乙烯是以气相存在的。
由于气相乙烯极易在催化剂上发生聚合反应而生成大分子烯烃或高聚物,一方面增加了物耗,另一方面导致催化剂失活,缩短催化剂寿命。
因此,必须使乙烯完全溶解在反应进料中,保证烷基化反应在液相中进行。
虽然可以采用大量苯循环来解决上述问题,但导致分馏系统投资和能耗的增加。
因此,为了保证乙烯溶解、控制床层温升,同时满足苯烯比 3.0的工艺条件,采用过量苯和部分反应产物循环与多点乙烯进料相结合的方法,既降低了苯烯比、减少了能耗,还可保证物耗没有增加。
2.2.2.2 影响烷基化反应的主要因素影响烷基化反应的主要因素包括反应温度、苯烯比、乙烯空速和原料杂质。
反应压力对催化剂活性、选择性的影响不大。
反应压力高,有利于乙烯的溶解,但也不宜太高,否则会增加投资和能耗。
因此,应根据维持反应系统完全处于液相状态的要求,确定合适的反应压力。
反应温度是影响反应的重要因素。
试验表明,在较低温度下,乙苯选择性高,但是催化剂的活性较低;随着反应温度升高,催化剂的活性增加,但乙苯选择性下降,当反应温度升到240、250℃时,乙苯选择性反而增加。
这是因为在上述条件下,催化剂的烷基转移性能得以发挥,生成的多乙苯又与过量苯转化成为乙苯,提高了乙苯的选择性。
值得注意的是,反应温度过高,将使重质物增多,乙苯收率下降。
根据以上分析,烷基化反应的温升应控制在适当范围内(小于40℃),以保证最有效地发挥催化剂的活性和稳定性。
烷基化反应的正常操作温度是200~245℃。
苯烯比是指反应原料苯与乙烯的摩尔比。
试验表明,苯烯比越大,乙苯选择性越高,多乙苯选择性越低;反之,则乙苯选择性下降,多乙苯选择性增加,增加的多乙苯虽然可通过烷基转移反应转化为乙苯,但处理量增大。
另外,苯烯比过低,将使生成的重质物增多。
因此,苯烯比的大小将直接影响装置的能耗和反应结果。
设计的烷基化反应的苯烯比是3.0。
乙烯空速低,有利于提高乙苯的选择性。
但催化剂装量大,生产成本高。
应根据催化剂的性能,确定适宜的乙烯空速。
原料杂质对烷基化反应的影响主要表现在对催化剂寿命的影响。
原料乙烯和苯中的碱性氮化物将占据催化剂的酸性中心,造成催化剂失活,极大地减少催化剂的寿命。
通常采用白土对原料苯进行预处理。
另外,反应物中少量的溶解水对维持催化剂活性稳定性是有益的,但如果长期使催化剂处于高水含量的反应物中,对催化剂的寿命极为不利。
最佳的反应物中水含量是100~200ppm 。
因此,必须严格控制原料中的杂质含量。
2.2.2.3 烷基转移反应烷基化反应中产生的少量多乙苯(主要是二乙苯、三乙苯)可在一定的温度、压力条件和酸性催化剂的作用下,通过与苯发生烷基转移反应,转化成为乙苯,从而提高乙苯收率。
其主要方程式如下:565246252662)(H C H C H C H C H C −→←+4625256523635266)()(H C H C H C H C H C H C H C +−→←+理论上讲,所有的多乙苯都可以进行烷基转移反应,但实际上受分子筛孔道及扩散的限制,四乙苯以上的多乙苯几乎不发生烷基转移反应。
烷基转移反应是可逆的二级反应,接近热力学平衡。
由于烷基转移反应的热效应很小,因此反应器催化剂床层中几乎没有温升。
同烷基化反应一样,烷基转移反应也是发生在分子筛催化剂的酸性活性中心上。
除了生成乙苯外,还可生成重质化合物,从而导致物耗增加,乙苯收率下降,因此应最大可能地减少副反应的发生。
工艺要求烷基转移反应在液相条件下进行。
2.2.2.4 影响烷基转移反应的主要因素影响烷基转移反应的主要因素包括反应温度、苯与多乙苯分子比、空速和原料杂质。
反应压力是根据保证在全液相反应条件下操作来确定的,它对烷基转移反应的结果没有影响。
反应温度是控制催化剂活性的主要工艺参数之一。
温度越高,催化剂活性越高。
当催化剂逐渐失活时,即烷基转移反应器多乙苯单程转化率下降,可通过逐步提高温度使其活性恢复。
设计反应温度的范围是175~235℃。
需注意的是:升温可以提高烷基转移反应的速率,但如果升温速度太快,将导致催化剂失活速度加快,使用周期缩短,因此必须严格控制反应温度和升温速度。
通常是根据反应系统中多乙苯产量平衡来确定适宜的反应温度。
进料中苯量增加可以获得较高的多乙苯转化率和乙苯选择性。
但过多的苯在系统中循环将增加苯塔的负荷,增加能量消耗。
设计的烷基转移反应苯与多乙苯分子比为8。
由于烷基转移反应是热力学平衡控制,降低空速,增加反应的停留时间有利于提高多乙苯的转化率。
但空速也不宜过低,否则催化剂装量过多,增加了成本。
烷基转移反应时,进料中水含量与反应温度的控制关系密切。
如果水含量过高,需要增加反应温度。
通常苯中水含量无需控制,但需时常监测,并据此调整反应温度。
一般反应进料中的水含量为50~150ppmwt。
2.2.3 工艺流程说明乙苯单元工艺流程主要包括烷基化反应、烷基转移反应、苯原料精制、乙苯精馏等部分。
乙苯单元的工艺原则流程图见附图POSM-10-N-8001~ POSM-10-N-8007。
2.2.3.1 烷基化工艺流程1) 正常操作工况下的烷基化工艺流程烷基化反应系统的作用是将苯和乙烯转化为乙苯和多乙苯。
本装置设计的烷基化反应的苯烯比为 3.0。
为了更好地控制烷基化反应器的温升,保证乙烯的溶解,减少催化剂的积炭,延长催化剂的使用寿命;以及为了提高烷基化反应的乙苯选择性,烷基化工艺设计采用三反七段加循环的流程。
通过调整各段乙烯进料与循环物料的流量,保证乙烯的溶解和各段催化剂床层的温升在适当范围。
设计烷基化反应器为绝热反应器,共三台,第一台反应器中有一段催化剂床层,第二台反应器中有二段催化剂床层。
第三台反应器中有四段催化剂床层。
要求反应器在足够的压力下操作,以维持反应在全液相状态下进行。
乙烯按一定的比例分成7份,分别进入7段催化剂床层中,原料苯从第一烷基化反应器依次通过第二、第三烷基化反应器,物流的流向均为自下而上。
在第二烷基化反应器的出口使部分物流返回到第一烷基化反应器的入口,可增大反应原料对乙烯的溶解,设计第一烷基化反应器与第二、第三烷基化反应器各段乙烯进料之比是1.3186:1.3186:1,三台反应器的温升均小于40℃。
在本工艺设计中,由于苯烯比仅为 3.0,烷基化反应系统放出的热量大于需要提供的热量。
因此在每台反应器之间设置取热装置,以保证满足适宜的反应条件。
第一烷基化反应器的出料用于发生0.45MPaG的蒸汽,第二烷基化反应器的出料先预热烷基化反应原料苯,多余的热量再发生0.45MPaG的蒸汽,第三烷基化反应器中段出料先加热烷基转移反应的进料,再发生0.45MPaG的蒸汽,第三烷基化反应器的出料直接送入乙苯精馏工段。
因烷基转移反应温度需要随着催化剂活性的降低而逐渐提升,当反应温度达到235℃时,需将第三烷基化反应器的出口温度提高至245℃,以满足加热烷基转移进料的要求。
烷基化反应原料苯来自乙苯精馏工段。
正常工况下,烷基化反应原料苯与第二烷基化反应器的出料换热后就能达到第一烷基化反应器入口温度;开工时,则用开停工加热器预热苯进料。
来自界外的乙烯被分别送入第一、第二和第三烷基化反应器各段,与苯进行烷基化反应。
在第一烷基化反应器、第二烷基化反应器下段和第三烷基化反应器的1、3段,乙烯与苯在反应器外的静态混合器中混合,而第二烷基化反应器上段和第三烷基化反应器的2、4段,乙烯与苯在反应器内混合。
2) 切换工况下的烷基化工艺流程由于第一烷基化反应器的催化剂受原料杂质的影响最直接,更易失活,为保证装置满足5年的运转周期,设计了第一烷基化反应器可切出更换催化剂的流程(切换流程)。
即:将第一烷基化反应器与其余二台反应器隔离,单独更换催化剂。
换剂期间,另二台烷基化反应器仍可继续操作。
此时,乙烯与苯分别在第二和第三烷基化反应器中的六段催化剂床层上发生烷基化反应,在苯进料量不变的条件下,通过调整各段乙烯进料与循环物料的流量,乙苯装置操作负荷仍可达到100%。