硅酸乙酯——硅溶胶混合粘结剂及其精密铸造新工艺
硅溶胶精密铸造工艺.
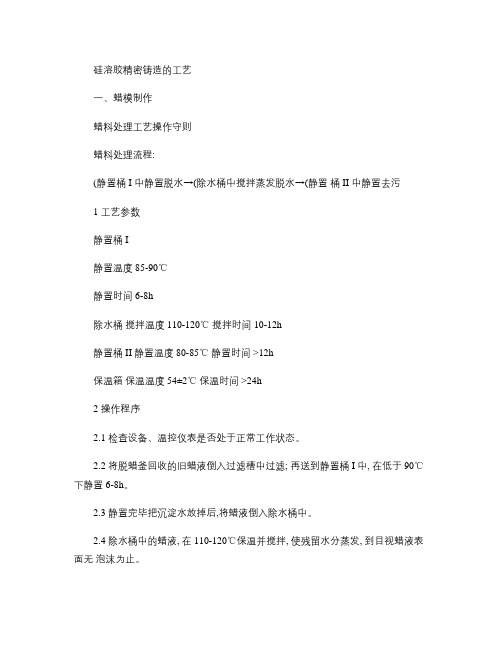
硅溶胶精密铸造的工艺一、蜡模制作蜡料处理工艺操作守则蜡料处理流程:(静置桶 I 中静置脱水→(除水桶中搅拌蒸发脱水→(静置桶 II 中静置去污1 工艺参数静置桶 I静置温度 85-90℃静置时间 6-8h除水桶搅拌温度 110-120℃搅拌时间 10-12h静置桶 II 静置温度 80-85℃静置时间 >12h保温箱保温温度 54±2℃保温时间 >24h2 操作程序2.1 检查设备、温控仪表是否处于正常工作状态。
2.2 将脱蜡釜回收的旧蜡液倒入过滤槽中过滤; 再送到静置桶 I 中, 在低于 90℃下静置 6-8h。
2.3 静置完毕把沉淀水放掉后,将蜡液倒入除水桶中。
2.4 除水桶中的蜡液, 在 110-120℃保温并搅拌, 使残留水分蒸发, 到目视蜡液表面无泡沫为止。
2.5 将除完水的蜡液, 经过<60目筛网过滤再放入<90℃的静置桶 II 中, 保温静置12h 以上。
2.6 各除水桶、静置桶应定期性的放掉其底部的残留水和脏杂物。
2.7 把静置桶 II 中处理好的回收蜡液送到模头压蜡机保温桶中, 用于主产模头(浇道。
2.8 根据旧腊料性能和腊料消耗情况,不定期的在静置桶 II 中适量加新蜡,一般在 3% -5%左右。
2.9 将合格的蜡液灌入保温箱内的蜡缸中, 为减少蜡缸内蜡液中的气体, 先保持一段高温时期 80℃/2h后降至 54℃。
在 54±2℃下保温 24h 后,方可用于压制蜡模。
3 注意事项3.1除水桶,静置桶均应及时排水、排污。
3.2经常检查各设备温控仪表的工作状况, 防止失控, 尤其应防止温度过高造成蜡料老化。
3.3每月检查一次蜡处理设备各导热油的液面位置, 油面应距设备顶面200㎜左右, 防止油溢出。
并注意检查设备有无渗油现象。
3.4经常检查环境状态,避免灰尘及外来物混入蜡料中。
压制蜡模工艺操作守则1 工艺要求室温 24±3℃蜡缸温度 54±2℃(大件应根据工艺要求设定射蜡嘴温度 57-64℃压射压力 4.2Mpa(42kgf/cm2保压时间 5-15s冷却水温度 <10℃2 操作规程2.1 检查压蜡机油压、保温温度、操作按钮等是否正常。
硅酸乙酯-水玻璃复合型壳在精密铸造中的应用
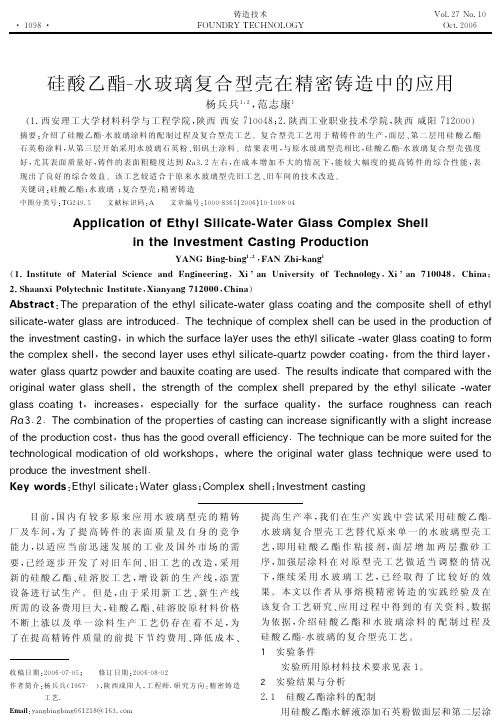
$ ! " # $ % & ’ $ ( + )? & ) / & / 0 1 " $" 2 0 + )) 0 + , 3 1 , 1 * / 0 ) < 4 / 0 ) &, / 3 3* " / 0 1 $ $ %0 + )* " . " 3 1 0 )3 + ) , ," 2) 0 + , ? ’ -/ ? ’ 3 1 , 1 * / 0 ) < 4 / 0 ) &, / 3 3/ & ) 1 $ 0 & " % # * ) % > ( + ) 0 ) * + $ 1 # )" 2 * " . , ) H3 + ) , , * / $F )# 3 ) % 1 $ 0 + )? & " % # * 0 1 " $" 2 V ? # 1 $4 + 1 * + 0 + )3 # & 2 / * ) , / ) & # 3 ) 3 0 + )) 0 + , 3 1 , 1 * / 0 ) < 4 / 0 ) & , / 3 3* " / 0 1 $ 0 " 2 " & . 0 + )1 $ E ) 3 0 . ) $ 0 * / 3 0 1 $ ’ ’ # # # 0 + )3 ) * " $ % , / ) & # 3 ) 3) 0 + , 3 1 , 1 * / 0 ) < # / & 0 A? " 4 % ) & * " / 0 1 $ 2 & " .0 + ) 0 + 1 & % , / ) & 0 + )* " . , ) H3 + ) , , ’ ’ V ’ ? 4 / 0 ) &, / 3 3V # / & 0 A? " 4 % ) & / $ %F / # H 1 0 )* " / 0 1 $ & )# 3 ) % > ( + ) & ) 3 # , 0 3 1 $ % 1 * / 0 ) 0 + / 0 * " . / & ) %4 1 0 + 0 + ) -/ ? # 0 + )3 0 & ) $ 0 +" 2 0 + )* " . , ) H3 + ) , ,? & ) / & ) %F + )) 0 + ,3 1 , 1 * / 0 )< 4 / 0 ) & " & 1 1 $ / ,4 / 0 ) &, / 3 33 + ) , , ? ? ’0 ’ # #) # , / 3 3* " / 0 1 $ 1 $ * & ) / 3 ) 3 3 ) * 1 / , , " &0 + )3 # & 2 / * )V # / , 1 0 0 + )3 # & 2 / * )& " # + $ ) 3 3* / $& ) / * + -0 ? ’2 ’ ! " 5> 7> ( + )* " . F 1 $ / 0 1 " $" 2 0 + )? & " ) & 0 1 ) 3" 2 * / 3 0 1 $ / $ 1 $ * & ) / 3 )3 1 $ 1 2 1 * / $ 0 , 1 0 +/3 , 1 + 0 1 $ * & ) / 3 ) ? -* ’4 # " 2 0 + )? & " % # * 0 1 " $* " 3 00 + # 3 + / 3 0 + )" " %" E ) & / , , ) 2 2 1 * 1 ) $ * > ( + ) 0 ) * + $ 1 # )* / $F ). " & )3 # 1 0 ) % 2 " & 0 + ) ’ V #4 + ) & )0 + )" & 1 1 $ / ,4 / 0 ) &, / 3 30 ) * + $ 1 # )4 ) & )# 3 ) %0 " 0 ) * + $ " , " 1 * / ,. " % 1 * / 0 1 " $" 2" , %4 " & 8 3 + " 3 V ? & " % # * ) 0 + ) 1 $ E ) 3 0 . ) $ 0 3 + ) , , > ? $ % % % ( ) , % #\ 0 + , 3 1 , 1 * / 0 )T / 0 ) &, / 3 3 Q " . , ) H3 + ) , , D $ E ) 3 0 . ) $ 0 * / 3 0 1 $ *+ ’ ? 国内有较多原来应用水玻璃型壳的精铸 !! 目 前 # 厂及车间# 为了提高铸件的表面质量及自身的竞争 能力# 以适应 当 前 迅 速 发 展 的 工 业 及 国 外 市 场 的 需 要# 已经逐步 开 发 了 对 旧 车 间’ 旧 工 艺 的 改 造# 采用 新的硅酸乙 酯’ 硅 溶 胶 工 艺# 增 设 新 的 生 产 线# 添置 由于采用新工艺’ 新生产线 设备进行试生产(但是# 所需的设备费用巨大# 硅酸乙酯’ 硅溶胶原材料价格 不断上涨以 及 单 一 涂 料 生 产 工 艺 仍 存 在 着 不 足# 为 了在提高精铸件质量的前提下节约费用’ 降低成本’ 提高生产率# 我们在生产实践中尝试采用硅酸乙酯 $ 水玻璃复合型壳工艺替代原来单一的水玻璃型壳工 艺# 即用 硅 酸 乙 酯 作 粘 接 剂# 面层增加两层撒砂工 序# 加强层涂 料 在 对 原 型 壳 工 艺 做 适 当 调 整 的 情 况 下# 继续 采 用 水 玻 璃 工 艺# 已经取得了比较好的效 果(本文以作者从事熔模精密铸造的实践经验 及 在 该复合工艺研究’ 应用过程中得到的有关资料’ 数据 为依据# 介绍 硅 酸 乙 酯 和 水 玻 璃 涂 料 的 配 制 过 程 及 硅酸乙酯 水玻璃的复合型壳工艺( $ =! 实验条件 实验所用原材料技术要求见表 &( 7! 实验结果与分析 !) &! 硅酸乙酯涂料的配制 用硅酸乙酯水解液添加石英粉做面层和第二层涂
硅溶胶精密铸造工艺
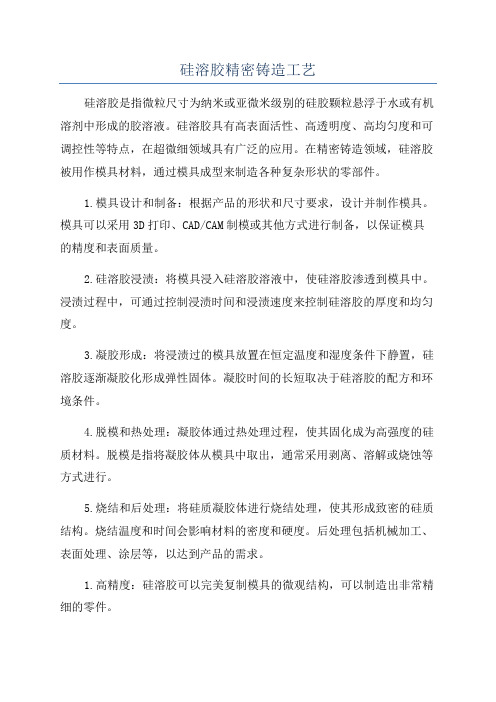
硅溶胶精密铸造工艺硅溶胶是指微粒尺寸为纳米或亚微米级别的硅胶颗粒悬浮于水或有机溶剂中形成的胶溶液。
硅溶胶具有高表面活性、高透明度、高均匀度和可调控性等特点,在超微细领域具有广泛的应用。
在精密铸造领域,硅溶胶被用作模具材料,通过模具成型来制造各种复杂形状的零部件。
1.模具设计和制备:根据产品的形状和尺寸要求,设计并制作模具。
模具可以采用3D打印、CAD/CAM制模或其他方式进行制备,以保证模具的精度和表面质量。
2.硅溶胶浸渍:将模具浸入硅溶胶溶液中,使硅溶胶渗透到模具中。
浸渍过程中,可通过控制浸渍时间和浸渍速度来控制硅溶胶的厚度和均匀度。
3.凝胶形成:将浸渍过的模具放置在恒定温度和湿度条件下静置,硅溶胶逐渐凝胶化形成弹性固体。
凝胶时间的长短取决于硅溶胶的配方和环境条件。
4.脱模和热处理:凝胶体通过热处理过程,使其固化成为高强度的硅质材料。
脱模是指将凝胶体从模具中取出,通常采用剥离、溶解或烧蚀等方式进行。
5.烧结和后处理:将硅质凝胶体进行烧结处理,使其形成致密的硅质结构。
烧结温度和时间会影响材料的密度和硬度。
后处理包括机械加工、表面处理、涂层等,以达到产品的需求。
1.高精度:硅溶胶可以完美复制模具的微观结构,可以制造出非常精细的零件。
2.高表面质量:硅溶胶的流动性好,可以填充模具的细小空隙,不会出现气孔和缺陷,从而得到高质量的表面。
3.复杂结构还原能力强:硅溶胶可以铸造出复杂的薄壁结构、镂空结构和内外复杂曲面结构,且能保持高精度。
4.可批量生产:硅溶胶工艺可以批量生产相同或不同的零件,提高生产效率。
5.环保且节能:硅溶胶精密铸造工艺无需模具,减少了材料浪费,省去了模具订制的时间和费用,减少了能源消耗。
尽管硅溶胶精密铸造工艺具有很多优点,但也存在一些限制,如硅溶胶成本较高,工艺流程复杂,对环境条件要求较高等。
但随着技术的不断发展和改进,这些限制将逐渐得到解决。
总之,硅溶胶精密铸造工艺以其优质的成品和高效的生产工艺,在各个领域得到了广泛应用。
硅溶胶精密铸造工艺.doc

硅溶胶精密铸造工艺焦作市恒辉精密制造有限公司企业标准特种合金熔模铸造工艺规程QQ/HH C4.1-20131适用范围1.1本规程适用于特种合金硅溶胶熔模铸造。
1.2其他合金硅溶胶熔模铸造可参照执行。
2特殊合金熔模铸造工艺流程图3控制要求3.1特殊合金熔模铸造生产过程的成型、组合、制壳、脱蜡、熔化和浇注、清洗、热处理和精修复,应制定各过程的通用工艺规程。
检验包括在检验规范中。
熔炼和浇注被确认为特殊过程。
3.2对于每个铸件,需要一个工艺规范。
3.3铸件的整个生产过程应严格按照工艺规程和工艺规程的要求进行。
根据工艺规程的要求,实施过程控制,并做好过程的原始记录。
焦作市恒辉精密制造有限公司企业标准特种合金熔模铸造工艺代码蜡模生产QQ/HH C4.2-1.2其他合金硅溶胶熔模铸造可参照执行。
2特殊合金熔模铸造工艺流程图3控制要求3.1特殊合金熔模铸造生产过程的成型、组合、制壳、脱蜡、熔化和浇注、清洗、热处理和精修复,应制定各过程的通用工艺规程。
检验包括在检验规范中。
熔炼和浇注被确认为特殊过程。
3.2对于每个铸件,需要一个工艺规范。
3.3铸件的整个生产过程应严格按照工艺规程和工艺规程的要求进行。
根据工艺规程的要求,实施过程控制,并做好过程的原始记录。
焦作市恒辉精密制造有限公司,企业标准特殊合金熔模铸造工艺代码蜡模制作QQ/Hhhc4.2:(在蒸馏桶内)蒸馏脱水→(在移除桶内)搅拌蒸发脱水→(在蒸馏桶内)蒸馏去污1.2工艺参数a .蒸馏桶蒸馏温度85-90°c .蒸馏时间6-8小时c .移除桶搅拌温度110-120°c .搅拌时间10-12小时e .蒸馏桶蒸馏温度80-85°c .蒸馏时间> 12小时g 1.3.2将脱蜡釜回收的旧蜡液倒入过滤罐中过滤;然后送入静置桶中,将脱蜡釜回收的旧蜡液倒入过滤罐中过滤至85-1 . 3 . 2;然后送至立筒中细化晶粒,消除魏氏组织,铸造应力低于85%。
硅溶胶精密铸造工艺流程
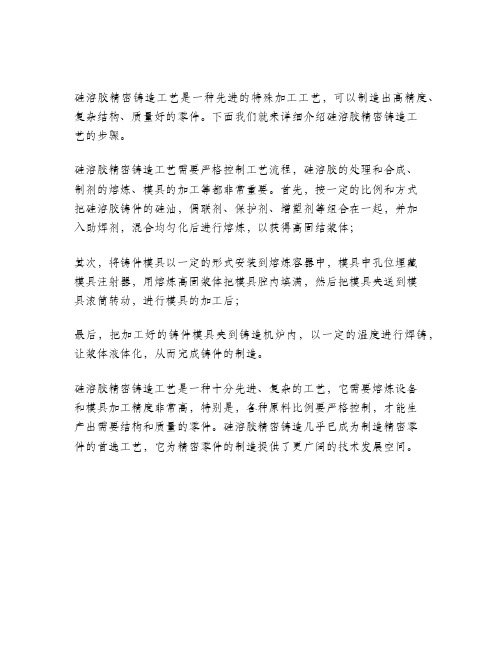
硅溶胶精密铸造工艺是一种先进的特殊加工工艺,可以制造出高精度、复杂结构、质量好的零件。
下面我们就来详细介绍硅溶胶精密铸造工
艺的步骤。
硅溶胶精密铸造工艺需要严格控制工艺流程,硅溶胶的处理和合成、
制剂的熔炼、模具的加工等都非常重要。
首先,按一定的比例和方式
把硅溶胶铸件的硅油,偶联剂、保护剂、增塑剂等组合在一起,并加
入助焊剂,混合均匀化后进行熔炼,以获得高固结浆体;
其次,将铸件模具以一定的形式安装到熔炼容器中,模具中孔位埋藏
模具注射器,用熔炼高固浆体把模具腔内填满,然后把模具夹送到模
具滚筒转动,进行模具的加工后;
最后,把加工好的铸件模具夹到铸造机炉内,以一定的温度进行焊铸,让浆体液体化,从而完成铸件的制造。
硅溶胶精密铸造工艺是一种十分先进、复杂的工艺,它需要熔炼设备
和模具加工精度非常高,特别是,各种原料比例要严格控制,才能生
产出需要结构和质量的零件。
硅溶胶精密铸造几乎已成为制造精密零
件的首选工艺,它为精密零件的制造提供了更广阔的技术发展空间。
硅溶胶在精密铸造中的运用
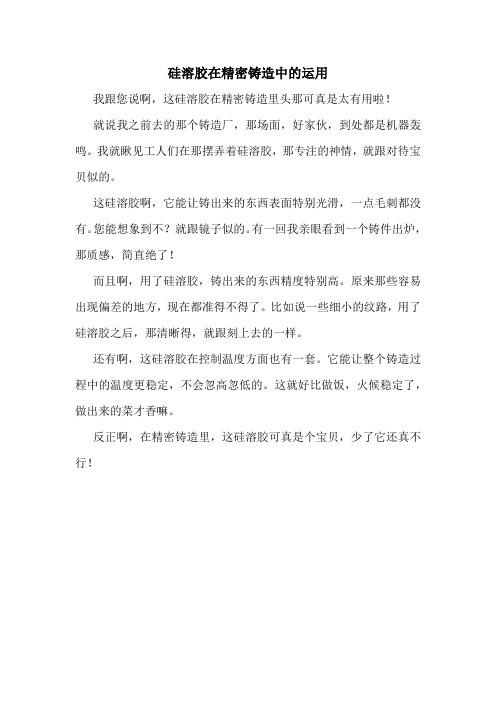
硅溶胶在精密铸造中的运用
我跟您说啊,这硅溶胶在精密铸造里头那可真是太有用啦!
就说我之前去的那个铸造厂,那场面,好家伙,到处都是机器轰鸣。
我就瞅见工人们在那摆弄着硅溶胶,那专注的神情,就跟对待宝贝似的。
这硅溶胶啊,它能让铸出来的东西表面特别光滑,一点毛刺都没有。
您能想象到不?就跟镜子似的。
有一回我亲眼看到一个铸件出炉,那质感,简直绝了!
而且啊,用了硅溶胶,铸出来的东西精度特别高。
原来那些容易出现偏差的地方,现在都准得不得了。
比如说一些细小的纹路,用了硅溶胶之后,那清晰得,就跟刻上去的一样。
还有啊,这硅溶胶在控制温度方面也有一套。
它能让整个铸造过程中的温度更稳定,不会忽高忽低的。
这就好比做饭,火候稳定了,做出来的菜才香嘛。
反正啊,在精密铸造里,这硅溶胶可真是个宝贝,少了它还真不行!。
硅溶胶工艺铸铝件
硅溶胶工艺铸铝件硅溶胶工艺是一种常用于铸造铝件的高精度成形工艺。
通过该工艺可以制造出形状复杂、尺寸精确的铝件,适用于各种领域的应用,如汽车零部件、航空航天零部件、机械零件等。
在硅溶胶工艺中,首先需要制作模具,然后将铝液注入模具中进行成形,最后经过热处理和表面处理等工艺步骤,得到最终的铝件产品。
硅溶胶工艺铸造铝件的步骤主要包括以下几个方面:1. 模具制作:首先根据需要铸造的铝件形状和尺寸,制作相应的模具。
通常情况下,硅溶胶工艺使用的是耐高温的硅溶胶模具,可以承受铝液的高温。
2. 涂覆硅溶胶:将模具表面涂覆一层硅溶胶,使其形成一层均匀的薄膜。
这一步是为了保护模具,避免铝液直接接触模具表面。
3. 硅溶胶干燥:将涂覆硅溶胶的模具进行干燥,将水分蒸发掉,使硅溶胶形成坚固的陶瓷状结构。
4. 脱模:将硅溶胶模具放入烘炉中升温,使硅溶胶完全烧结,然后从模具中取出,并在模具中形成了与铝件相同的型腔。
5. 浇注铝液:将预热的铝液倒入硅溶胶模具中,充满整个型腔,以确保铝液可以完全填充模具。
6. 固化:让铝液在模具中冷却凝固,直至成型。
这一步需要控制好冷却速度和温度,以确保铝件的尺寸精度和表面质量。
7. 脱模清理:待铝件冷却凝固后,将其从硅溶胶模具中取出,并清理表面的残留物。
8. 热处理:经过硅溶胶工艺制造的铝件通常需要进行热处理,以提高其力学性能和耐腐蚀性能。
9. 表面处理:最后对铝件进行表面处理,如喷涂、阳极氧化等工艺,以提高其表面硬度和耐磨性。
总的来说,硅溶胶工艺铸造铝件具有成形精度高、表面光洁度好、尺寸一致性高等优点,适用于制造需要高精度铝件的领域。
虽然硅溶胶工艺的成本相对较高,但是其成形效果和制造效率却是得到广泛认可的,因此在汽车、航空航天、机械等领域得到了广泛应用。
硅酸乙酯粘结剂使用方法
硅酸乙酯粘结剂使用方法全文共四篇示例,供您参考第一篇示例:硅酸乙酯粘结剂,又称乙硅酸酯,是一种常用于建筑及装饰行业的粘结材料。
它具有优异的粘结性能和耐候性,广泛应用于建筑幕墙、瓷砖、地板、玻璃等领域。
为了更好地利用硅酸乙酯粘结剂,以下将介绍其使用方法。
选择合适的基材。
硅酸乙酯粘结剂适用于混凝土、石膏板、水泥基板、石材等多种建筑材料的粘接,但不同的基材需要选择不同的粘结剂产品,以保证粘结效果。
准备表面。
在进行粘结之前,需确保基材表面清洁、干燥、坚固。
清除表面的灰尘、油污和其他杂物,以确保粘结剂能够充分附着于基材表面,提高粘结强度。
然后,进行混合。
按照硅酸乙酯粘结剂的使用说明,将粘结剂与稀释剂按一定比例混合均匀。
在搅拌的过程中,一定要注意保持搅拌器具和容器的清洁,以免杂质进入粘结剂中影响粘结效果。
接着,施工操作。
在进行粘结剂的施工时,需要严格按照操作说明进行,确保施工平整、均匀。
特别要注意的是在施工的过程中,要保持室温和基材温度的适宜,避免在极端温度下施工。
养护处理。
在粘结剂施工完成后,需要进行一定的养护处理,以确保粘结剂充分发挥其粘结作用。
通常情况下,硅酸乙酯粘结剂会有一个固定的养护时间,在这段时间内需要避免外力冲击,保持基材表面的干燥。
硅酸乙酯粘结剂作为一种重要的建筑装饰材料,在使用时需要注意以上几个关键步骤。
通过合理的选择基材、表面处理、混合、施工操作以及养护处理,可以确保硅酸乙酯粘结剂发挥最佳的粘结性能,提高建筑装饰材料的质量和使用寿命。
第二篇示例:硅酸乙酯粘结剂是一种常用的建筑材料,广泛应用于建筑、装修和家具行业。
它具有粘结力强、耐水、耐候等特点,能够有效粘结各种材料,如混凝土、砖瓦、陶瓷、金属等。
以下将介绍硅酸乙酯粘结剂的使用方法。
一、准备工作1.确保工作场所通风良好,保持空气流通,避免吸入有害气体。
2.穿戴好劳动保护用具,如手套、口罩和护目镜,避免粘结剂直接接触皮肤和呼吸道。
3.检查硅酸乙酯粘结剂包装,确保密封完好,防止变质。
硅溶胶在熔模精密铸造中的应用
粘结 ,且在室温配制涂料时又不会引起料浆胶凝 。常
使用粒径为 0. 075 mm 左右的氧化铝 、氧化锆 、莫来
石 、铝矿石及石英玻璃粉 ,为了改善涂料的浸涂性 ,往
往还要加入悬浮剂 、矿化剂 、渗透剂 、流平剂等辅助材
料 。稀释剂常用去离子水或酒精 。粉料的加入必须是 边加入边搅拌 ,防止局部粉料过多吸水导致硅溶胶胶 凝 。选定配方后 ,涂料的性能由其粘度和密度来决定 。 表 2 列出铸造镍基高温合金定向凝固铸件用壳型涂料 的典型配方及其性能 。
随着涂料浸渍使用 ,其性能必然发生变化 。水分 蒸发减少 ,粘度提高 ,故需按计算量补加少许硅溶胶和 去离子水 ,以保证原涂料 SiO2 含量及粘度 。冬季使用 硅溶胶粘结剂时 ,如果室内温度过低 ,配制涂料时粘度 会偏高 ,易产生气泡而影响型壳品质 。
表 2 定向凝固壳型涂料的典型配方及性能[3 ] Tab. 2 Typical component and properties of shell casting for di2
我国从 60 年代起开始生产和使用硅溶胶 ,近年来 用于熔模铸造的国产硅溶胶 ,品质日趋稳定并逐步向 国际商业品类靠拢 。北京航空材料学院从60年代末
收稿日期 :2001206220 ; 修订日期 :2001207218 作者简介 :肖 克 (19622 ) ,北京人 ,工程师 ,工学学士 1
作为熔模铸造壳型粘结剂的硅溶胶的性能指标包 括 SiO2 含量 、密度 、稳定剂的含量 、p H 值 、SiO2 粒径 。 表 1 列出熔模铸造行业常用的硅溶胶及其性能 。
表 1 熔模铸造行业常用的硅溶胶[1 、3 ] Tab. 1 Silica sol using for investment cast vocation
熔模铸造中硅溶胶-硅酸乙酯涂粒配制工艺
( )采 用 精 馏 乙 醇或 工 业 乙醇 。 4
熔模铸造 中的硅酸乙酯S 0含量分 别为3 %、 i 2
参磊 加 势 粤 铸 workl FI950. Or 2 工热工 ww ̄. et孳 n 羔 n 9 馋 m a/ C
研 究 s 应 用
ee r h& A pl ain sa c p i to c
≤ 08 .
≤ O. 5
其 他 粒 度 范 围 OO 1 . 5 .5 ~00 4 (8 ~3 0 20 2) 04 0 . 4 .5 ~02 、 2 OO 1 .4 .5 ~00 5 (6、 4 0
.
≤O5 .
07 1~ 0 0 3 .5
≤05 .
0 4 0~ 0 2 4、 .5 .2
颗粒 比表面不受严格检测 ,二氧化硅的浓度低 ,酸 性或 中性条件下稳定性差 ,使用周期短 ,以及或多 或少带点颜色 ,品种少等 。而硅溶胶型壳高温强度
好 ,高 温 抗 变 形 能 力 强 ,热 震 稳 定 性好 ,型 壳 表 面
一
、
概述
熔模铸造是生产精密铸件的一种先进 工艺 ,硅 溶胶是影响型壳 质量的重要因素 ,如何提 高精密铸
践 , 分析 了成 分 、制备 工 艺、 设备 等注 意 事项 。
硅 溶 胶 ,6 %SO 的硅 溶 胶 也 已试 制 成 功 。 0 I 与 国际 知 名 硅 溶 胶 品牌 相 比 , 目前 国产 硅溶 胶 的主 要 缺 点 为 杂 质含 量 高 ,颗 粒 大 小 无严 格 控 制 ,
表2 三种耐火材料 的成分( 质量分数 ,%) 和粒度范 围
成 分
粉
S O2 i 2 4~ 2 8
铝矾土
- 1、下载文档前请自行甄别文档内容的完整性,平台不提供额外的编辑、内容补充、找答案等附加服务。
- 2、"仅部分预览"的文档,不可在线预览部分如存在完整性等问题,可反馈申请退款(可完整预览的文档不适用该条件!)。
- 3、如文档侵犯您的权益,请联系客服反馈,我们会尽快为您处理(人工客服工作时间:9:00-18:30)。
硅酸乙酯——硅溶胶混合粘结剂及其精密铸造新工艺
作者:罗守信, 盛玉海, 刘佑年
作者单位:武汉机械工艺研究所有限责任公司
1.期刊论文杨兵兵.范志康.YANG Bing-bing.FAN Zhi-kang硅酸乙酯-水玻璃复合型壳在精密铸造中的应用-铸造
技术2006,27(10)
介绍了硅酸乙酯-水玻璃涂料的配制过程及复合型壳工艺.复合型壳工艺用于精铸件的生产,面层、第二层用硅酸乙酯石英粉涂料,从第三层开始采用水玻璃石英粉、铝矾土涂料.结果表明,与原水玻璃型壳相比,硅酸乙酯-水玻璃复合型壳强度好,尤其表面质量好,铸件的表面粗糙度达到Ra3.2左右,在成本增加不大的情况下,能较大幅度的提高铸件的综合性能,表现出了良好的综合效益.该工艺较适合于原来水玻璃型壳旧工艺、旧车间的技术改造.
2.期刊论文温虹.严青松.郭志军硅溶胶-硅酸乙酯交替复合制壳工艺在不锈钢精铸生产中的应用-铸造
2003,52(5)
介绍了硅溶胶-硅酸乙酯涂料的配制过程及硅溶胶-硅酸乙酯的交替复合制壳工艺,采用硅溶胶-硅酸乙酯复合型壳对新材料CF-8M不锈钢精密铸件进行了生产应用.结果表明,采用硅溶胶-硅酸乙酯交替复合制壳工艺,型壳质量有很大提高,生产的不锈钢精铸件表面质量和尺寸精度都得到很大提高.
3.期刊论文常连华.孙广平.朱春.CHANG Lian-hua.SUN Guang-ping.Zhu Chun硅溶胶—硅酸乙酯复合涂料在精铸
叶片生产中的应用-汽轮机技术2001,43(2)
介绍硅溶胶涂料的配制过程及复合制壳工艺,对使用结果作了简要分析。
4.期刊论文罗守信.盛玉海.刘佑年.Luo Shouxin.Sheng Yuhai.Liu Younian混合粘结剂-水玻璃复合型壳精密铸
造新工艺-特种铸造及有色合金2005,25(10)
混合粘结剂采用硅酸乙酯水解液、硅溶胶以及活性剂酒精混合而成.混合粘结剂用于型壳的1~3层,而加固层采用水玻璃粘结剂.采用混合粘结剂制壳的优点是,不用氨气化学硬化,而型壳干燥比硅溶胶快,层间干燥时间通常不超过1 h.混合粘结剂的的应用,缩短了制壳生产周期,提高了精铸件的质量,改善了劳动条件,减少了环境污染,大幅度降低了生产成本.
5.会议论文杨维敏.龙兵硅酸乙酯40在制壳中的试验与应用1994
6.期刊论文杨觉明.包小平.李建平.YANG Jue-ming.BAO Xiao-ping.LI Jian-ping高铍含量铍青铜熔模精密铸造
技术的研究-铸造2001,50(1)
对高铍含量的ZCuBe2.5合金的大气熔炼工艺、熔模精铸工艺及热处理工艺进行了研究。
结果表明:采用氧化铜脱氧剂和降低浇注温度,可以在大气熔炼条件下熔铸出冶金质量优良的ZCuBe2.5合金。
采用790℃固溶+420℃时效的热处理工艺,可使ZCuBe2.5合金的力学性能达到
:σb>900MPa,δ≈3%~3.5%,HRC=25~30。
采用硅酸乙酯-硅铝系耐火材料型壳以及合适的制壳工艺,可以铸造出形状复杂、尺寸精度和表面粗糙度要求高的高强度铍青铜熔模精铸件。
7.会议论文吴仁智ZF-801型增强快干硅溶胶2005
从二十世纪九十年代起,精密铸造业在环保法的要求下,精铸厂相继用硅溶胶制壳工艺取代了硅酸乙酯制壳工艺。
硅溶胶制壳工艺的优点是解决了环保要求,成本低廉。
但在高速发展的形势下,它制壳工艺周期长的缺点就越来越突出了,同时它的残留强度高
,清壳困难易损伤铸件,造成后期返修率增加是很不合算的。
在现有的厂房设施基本不变的前提下,要想提高生产能力缩短生产周期,扩大市场销量,提高碎溶胶制壳工艺的速率是很关键的步骤。
因为仅制壳工艺周期时间长达5-7大,它成为精铸整个工艺的时间瓶颈,所以对硅溶胶制壳工艺的改进是当务之急。
本文介绍精铸行业的快干硅溶胶制壳工艺。
制壳工艺时间从原来5-7天缩短到1-2天,从而缩短了整个生产周期,降低成本,提高了企业经济效益及对市场的竞争力。
8.学位论文王兴牙科铸钛包埋料成分及热膨胀性研究2004
牙科精密铸造是口腔修复体的主要成型方法,而钛在冷却过程中收缩量大,由于型壳是对牙齿形状的精确复制,为了得到尺寸精度良好的铸件,需要以包埋料的热膨胀补偿液态金属的凝固收缩.该课题的主要研究目的就是研制一种线热膨胀率1.0﹪左右,并可以简单方便的调整其热膨胀性的包埋料,拟以氧化镁和氧化铝为骨料,利用氧化镁和氧化铝反应生成尖晶石时发生体积膨胀来补偿熔融钛的凝固收缩.通过粘结剂的对比实验发现,以硅酸乙酯水解液和磷酸二氢铵为粘结剂时,包埋料的固化时间和固化强度均比较合适,确定硅酸乙酯水解液和磷酸二氢铵为本实验用粘结剂,并加入微量缓凝剂以调节以磷酸二氢铵为粘结剂的固化时间.通过正交实验确定了以硅酸乙酯水解液为粘接剂的包埋料的最佳配比,其热膨胀率可达到0.79﹪,骨料细化后热膨胀率可达到
0.91﹪,与预期值还有少许差距.X衍射分析和综合热分析证实有尖晶石生成.通过正交实验确定了以磷酸二氢铵为粘结剂的包埋料的最佳配比,热膨胀率为
1.26﹪,可以达到预期值.X衍射分析和综合热分析证实有尖晶石生成.对比研究表明从固化时间,固化强度,与熔融钛的反应性和使用方便性几方面考虑,采用磷酸二氢铵为粘结剂为宜.研究了粉液比、焙烧温度、焙烧时间对以磷酸二氢铵为粘结剂包埋料热膨胀性的影响,给出了不同粉液比和不同焙烧时间对包埋料的热膨胀率影响的变化范围图,以方便使用者调整包埋料的热膨胀率.
9.期刊论文崔春兰.柳贤福.张华.罗永滨.王宏.CUI Chun-lan.LIU Xian-fu.ZHANG Hua.LUO Yong-bin.WANG Hong
快干硅溶胶的生产应用-汽轮机技术2005,47(1)
介绍了新型快干硅溶胶,可使型壳层间干燥时间缩短到1h~2h,并且具有很高湿强度时,高温强度和残留强度与硅酸乙酯相当.而且在型壳性能、制壳速度上已全面接近国际优质快干硅溶胶水平.
10.会议论文王洪基.柳贤福整流支柱精铸工艺及真空热处理工艺的研究2003
本文介绍了整流支柱精铸工艺的全过程,包括模料的选用,硅溶胶--硅酸乙酯复合制壳工艺、真空浇铸及真空热处理等,并且对结论进行了分析和说明。
本文链接:/Conference_7068922.aspx
下载时间:2010年7月13日。