出货控制程序
成品出货管理流程
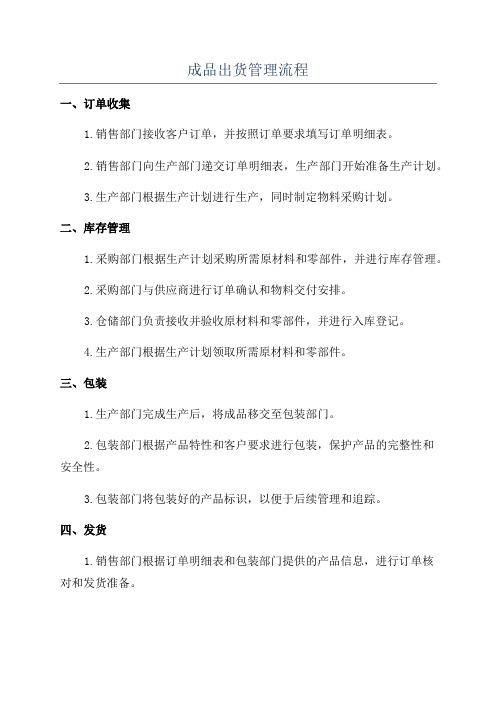
成品出货管理流程一、订单收集1.销售部门接收客户订单,并按照订单要求填写订单明细表。
2.销售部门向生产部门递交订单明细表,生产部门开始准备生产计划。
3.生产部门根据生产计划进行生产,同时制定物料采购计划。
二、库存管理1.采购部门根据生产计划采购所需原材料和零部件,并进行库存管理。
2.采购部门与供应商进行订单确认和物料交付安排。
3.仓储部门负责接收并验收原材料和零部件,并进行入库登记。
4.生产部门根据生产计划领取所需原材料和零部件。
三、包装1.生产部门完成生产后,将成品移交至包装部门。
2.包装部门根据产品特性和客户要求进行包装,保护产品的完整性和安全性。
3.包装部门将包装好的产品标识,以便于后续管理和追踪。
四、发货1.销售部门根据订单明细表和包装部门提供的产品信息,进行订单核对和发货准备。
2.仓储部门按照销售部门提供的发货清单,从库存中将产品调拨至出货区。
3.发货员核对发货清单和产品信息,进行出货操作,并记录出库信息。
4.发货员根据客户要求选择合适的运输方式,安排运输,并提供运输跟踪信息给销售部门和客户。
五、售后服务1.销售部门跟踪发货情况,与客户确认订单的收货情况。
2.客户收到货物后,进行验收,并及时反馈问题或反馈给销售部门。
3.销售部门协调相关部门解决客户问题,并提供售后服务,包括产品维修、退货等。
在整个成品出货管理流程中,需要各部门之间的紧密配合和信息沟通。
同时,需要建立完善的监控和追踪机制,确保订单能够按时发货,并对问题及时做出处理。
另外,企业还应不断优化流程,提高效率和准确性,提升客户满意度和市场竞争力。
出货检验控制程序(含表格)

出货检验控制程序(ISO9001-2015)1.0目的:确保交付给客户的产品符合客户品质要求。
2.0范围:凡本公司所销售之产品均属之。
3.0定义:无。
4.0权责:4.1品保部:产品出货前的检验工作。
4.2制造/仓储:出货产品的包装和搬运,交货工作。
4.3生管:制订出货计划和出货交付运输安排。
5.0作业内容:5.1生管课依据客户订单交期或排程做出生产出货计划表以E-MAIL或PAPER 档的形式通知到品保、仓储、制造等各相关单位。
5.2制程产品在入库前需经过OQC检验,仓储根据出货需求,把待出货之产品移置到“OQC待检区”。
5.3OQC依据《SIP》、承认样本及限度样品的要求对出货前的产品进行抽样检验,并把检验结果记录在《制程巡检/抽检品质记录表》及《出货检验报告单》中。
5.4抽检时OQC按每个栈板为一个批次或小件以不超过1000PCS为一个批次,按照《ISO2859抽样计划》正常单次抽样,AQL:MA为0.4,Mi为0.65。
出现客诉问题需重点检查,无客诉问题产品则以出货前的查核为主。
如有客户要求,则按客户要求标准进行。
5.5OQC检验判定合格:5.5.1OQC依据《检试验管理程序》的要求在《产品标识单》上盖“OQCPASS”章。
5.5.2制造依据《产品标示单》OQC的标识进行入库。
5.6OQC检验判定不合格:5.6.1OQC把不合格现象或不合格样品呈报上级主管后,确认为异常,则发出《品质异常联络单》给相关责任单位处理与改善,并要求相关责任单位在《品质异常联络单》背面会签。
具体依照《品质异常处理流程》执行。
不合格批,每一栈板朝外的最上层的左上角贴《不良品标示单》,注明相关不良现象等内容。
具体依照《检试验管理程序》执行。
5.6.2经OQC判定的不合格品依据《不合格管理程序》进行处理;相关单位评审是否采取纠正措施或预防措施,如需采取纠正措施或预防措施则依据《纠正与预防措施管理程序》执行。
如果不采取纠正措施,因出货紧急,在不影响功能的情况下,由生管或业务提出特采申请,具体依照《特采作业流程》执行。
成品出货控制程序
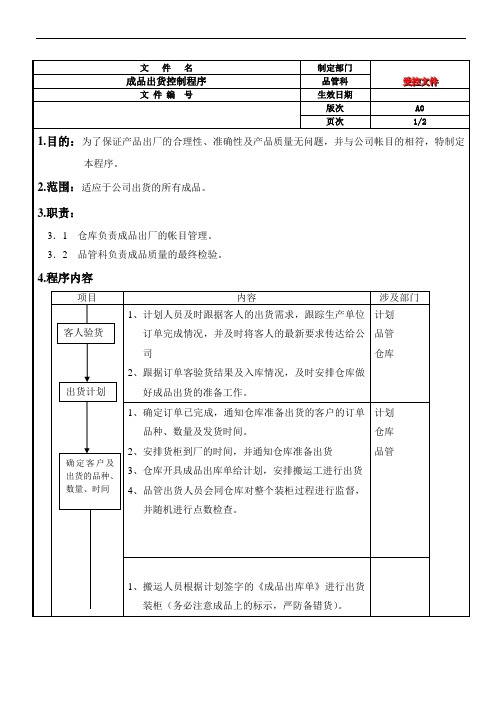
计划
船务
仓库
5、参考文件:
《质量手册》
6、引用表格:
6..1成品出仓单
6.2成品检验报告
2、安排货柜到厂的时间,并通知仓库准备出货
3、仓库开具成品出库单给计划,安排搬运工进行出货
4、品管出货人员会同仓库对整个装柜过程进行监督,并随机进行点数检查。
计划
仓库
品管
1、搬运人员根据计划签字的《成品出库单》进行出货装柜(务必注意成品上的标示,严防备错货)。
文件名
制定部门
受控文件
成品出货控制程序
品管科
仓库
品管
计划
搬运人员
装柜过程中,品管人员全程监督,不得出现野蛮装柜的现象;确认出货的货物是否与产品出货单的要求相一致;确认数量及货柜的编号是否与出货通知相一致;随机抽验出货产品的数量
品管
1.将核查完毕后的产品装车,按照不同的订单和客人业务的要求装车,仓管在在装车时再次清点数量、品种及附带品。
2.装车完毕后,计划人员签货柜的提货单,并把相关的通关资料对照相应的货柜交由司机或关务人员。
项目
内容
涉及部门客ຫໍສະໝຸດ 验货出货计划确定客户及出货的品种、数量、时间
1、计划人员及时跟据客人的出货需求,跟踪生产单位订单完成情况,并及时将客人的最新要求传达给公司
2、跟据订单客验货结果及入库情况,及时安排仓库做好成品出货的准备工作。
计划
品管
仓库
1、确定订单已完成,通知仓库准备出货的客户的订单品种、数量及发货时间。
文件名
制定部门
受控文件
成品出货控制程序
品管科
文件编号
生效日期
版次
出货检验控制程序V1

出货检验控制程序2.范围:适用于本厂生产之成品入库前或出货前的检验过程控制。
3.职责:3.1品质部:负责成品之检测标示与记录;OQC负责新产品在首次出货检验时召集相关群体人员进行CEPQ体验;3.2生产单位:负责成品送检及不合格之处理。
3.3成品仓管:负责库存成品出货前送检。
4.定义:无5过程识别图:6.程序内容:6.1出货前检验:6.11凡出货前产品均由成品仓管依《出货请检单》交OQC人员验货,或保存超过半年库存成品,由仓管申请交OQC复查。
6.1.2原则上以同一出货批次、同一订单号的同一产品数量为一批次进行抽查,以便于追溯。
6.1.30QC员依据抽样计划对送检成品进行抽样,按《0QC检验规范》及客户样板或工程签核样板对所抽样本进行检验,检验完成后,OQC员所检验结果详细记录于《0QC检验报告》,并呈主管以上人员或其代理人审核。
6.1.4当有客人来验货时,同业务和OQC人员准备相关资料及样板等,成品仓仓管配合进行。
6.2成品检验要求:6.2.1检验人员依据抽样计划对送检成品进行抽样。
6.2.2检验人员按照《0QC检验规范》或客人确认的样板及要求进行检验。
每批检验都需对CEPQ要求进行验证。
并反馈于报表。
6.2.3如果适用,检验人员需依据产品说明书之要求,对所检验的产品进行安装检验,安装检验所使用之配件和相关工具只限用被检产品的内配件箱工具。
6.2.4当有新产品在首次出货检验时,应由OQC组织相关群体人员进行该产品的CEPQ体验(主要体验群体应为非专业人员),并将体验过程记录于体验表内,同时对体验结果进行分析跟进.6.3检验结果标示处理6.3.1检验合格:OQC人员在《出货请检单》和产品标签上加盖α0QCPASSED”印章。
6.3.2检验不合格:a.OQC人员在《0QC检验记录表》上注明不合格及详细不合格原因,并在不合格成品上作出标示。
把《0QC检验记录表》交生产主管或生产经理确认,不合格成品按照不合格品控制程序进行处理。
出货管理控制流程

4.4.3:成品仓管员收到《送货单》后要对《送货单》要求的货物进行核实和确认,如是第三方送货(是指快递公司或货运公司)须将《送货单》的第二联用胶袋装好粘贴在货物的外箱上,并根据发货时间安排搬运。
4.3.4:一张《送货单》只能有一个送货单号,送货单号不能重复,如同一批货分几次送货的,每次送货为一个新的送货单号。
4.3.5:送货单号编号方式按年份+年度送货编号(由四位数字组成)如20110001。(此条自2011年1月份开始生效),不能出现重编号和不能跳号.
4.3.6:《送货单》内的产品名称规格项必须按客户下的订购合同的产品名称规格填写。如与本厂产品名称规格不同的可在第一联手写注明(注意不要印到其它联)。
4.4:送货前的准备
《送货单》的核对及货物的品种,数量,标识的核对。
4.4.1:仓库对当日的〈成品发货单〉上的产品要及时的跟进生产包装的进度做好相应的标识,品种,数量和其它的客户要求进行核对和抽查工作。对核对出不正确的货物填写<出货异常记录表>并要求生产部门进行返工处理。<出货异常记录表>每周一上午9点前经仓库主管审核后上交经理。
PC员
生产
品质
仓库
PC员
仓库
一:目的:
为确保提供客户的货物有效的控制。
二:适用范围:
适合于本厂的所有产品出货管理。
三:职责:
3.1:业务员负责核实客户的帐目收取状况,并通知PC员,及货物发货后的核查。
3.1:PC员(跟单员)负责编制《成品发货单》,《送货单》,及运输方式的确立。
生产订单至出货过程控制程序
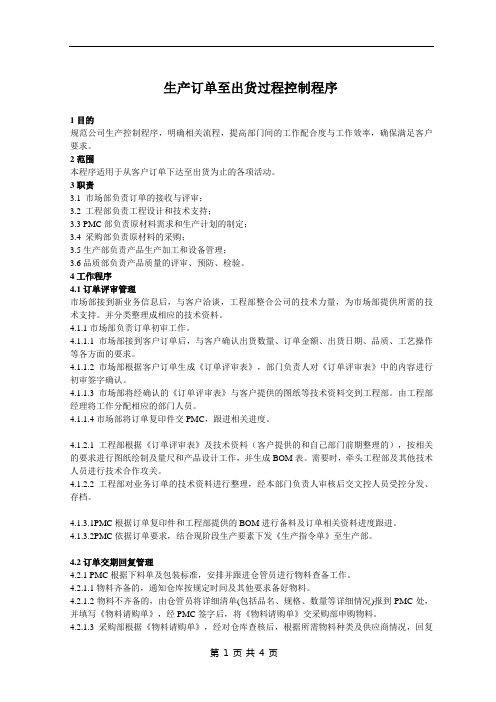
生产订单至出货过程控制程序1目的规范公司生产控制程序,明确相关流程,提高部门间的工作配合度与工作效率,确保满足客户要求。
2范围本程序适用于从客户订单下达至出货为止的各项活动。
3职责3.1 市场部负责订单的接收与评审;3.2 工程部负责工程设计和技术支持;3.3 PMC部负责原材料需求和生产计划的制定;3.4 采购部负责原材料的采购;3.5生产部负责产品生产加工和设备管理;3.6品质部负责产品质量的评审、预防、检验。
4工作程序4.1订单评审管理市场部接到新业务信息后,与客户洽谈,工程部整合公司的技术力量,为市场部提供所需的技术支持。
并分类整理成相应的技术资料。
4.1.1市场部负责订单初审工作。
4.1.1.1市场部接到客户订单后,与客户确认出货数量、订单金额、出货日期、品质、工艺操作等各方面的要求。
4.1.1.2市场部根据客户订单生成《订单评审表》,部门负责人对《订单评审表》中的内容进行初审签字确认。
4.1.1.3市场部将经确认的《订单评审表》与客户提供的图纸等技术资料交到工程部。
由工程部经理将工作分配相应的部门人员。
4.1.1.4市场部将订单复印件交PMC,跟进相关进度。
4.1.2.1工程部根据《订单评审表》及技术资料(客户提供的和自己部门前期整理的),按相关的要求进行图纸绘制及量尺和产品设计工作,并生成BOM表。
需要时,牵头工程部及其他技术人员进行技术合作攻关。
4.1.2.2工程部对业务订单的技术资料进行整理,经本部门负责人审核后交文控人员受控分发、存档。
4.1.3.1PMC根据订单复印件和工程部提供的BOM进行备料及订单相关资料进度跟进。
4.1.3.2PMC依据订单要求,结合现阶段生产要素下发《生产指令单》至生产部。
4.2订单交期回复管理4.2.1 PMC根据下料单及包装标准,安排并跟进仓管员进行物料查备工作。
4.2.1.1物料齐备的,通知仓库按规定时间及其他要求备好物料。
4.2.1.2物料不齐备的,由仓管员将详细清单(包括品名、规格、数量等详细情况)报到PMC处,并填写《物料请购单》,经PMC签字后,将《物料请购单》交采购部申购物料。
货物接收储存和出货控制程序

货物接收储存和出货控制程序货物接收、储存和出货,听起来好像是一个枯燥无味的工作,其实说起来,倒也有它的趣味和复杂之处。
说到这几项工作,大家脑袋里首先想到的是什么呢?是堆积如山的箱子、货车里密密麻麻的货物,还是忙得像陀螺一样的仓库管理员?货物接收和储存,乃至最后的出货,这一套流程,说白了就是大大小小的物流链条把所有的物品从一端送到另一端,保证你在需要的时候能拿到你想要的东西。
这中间的每一个环节,哪怕是最细小的一个疏漏,都会影响到整个过程的顺畅。
你说,这能不重要吗?接收货物,听起来就像是一件简单的事。
可实际上,它并不像我们想的那么轻松。
想象一下,一大堆货车一齐开到仓库门口,货物从车上卸下来,放在仓库门口一堆堆堆着。
天啊,这得多大一堆,才有那么多货物啊!而你作为负责接收的人,就得站在门口像个“门神”一样,检查每一件物品。
仔细看看有没有破损、漏水或者发霉的现象。
说实话,这个时候你得睁大眼睛,不能一丝不苟。
每一项货物都有自己的“身份证”,你得核对订单,看看数量对不对、规格对不对。
那可是严丝合缝的事,错一步,麻烦可就大了,事情不就“锅里掉铲子”了?接着说说储存这一环。
啊,这可不是简单地把货物随便一堆就完事了。
仓库不是超市,不是随便一放就行。
你得看货物是什么种类,有些货物得小心摆放,有些货物要远离水源和热源。
就拿易燃品来说,放在远离火源的地方是基本常识。
那些体积特别大的货物,估计需要你花上一些力气才能找到一个合适的地方。
你能想象一下,要是某个大箱子放错了地方,结果让整排货架都“倒塌”了,那可就真是“祸从天降”了!一切都得小心翼翼,没点心眼怎么行?别以为储存完了就完事了。
出货才是最考验你耐心和智慧的时刻!仓库一大堆货物堆得像小山一样,别说找某个特定的货物,连自己都可能会迷路。
你得事先知道每一件货物放在哪个位置,才能迅速定位、快速出货。
出货时,也不能马虎,不是随便抓起一堆就能发出去的,必须得一件件清点好,避免出现少发、漏发的情况。
出货控制程序

C
页次
1/2
出货控制程序
实施日期
2022-5-01
修改日期
2022-8-4
1.目的:确保出货作业顺利进行,按时按量交货。
2.范围:适用于公司出货作业控制。
3.权责
3.1搬运作业:物控。
3.2监督执行本作业程序:业务部、物管部、生产部、品管部。
4.定义:无
5.1内销出货
5.2.2成品仓库根据“出仓单”准备好产品,将出仓单交品管部QA;
5.2.3品管部QA根据“出仓单”进行出货抽检,完成后将“出仓单”签名后转回成品仓;如不合格,则需开出不合格处理单,交由品管主管确认处理办法,如品管主管无法确定,则需销售,开发进行评审;
5.2.4成品仓根据品管的签名确认是否出货;合格则可出货,不合格则需根据不合格处理单要求处理;
6.相关文件
6.1产品防护控制程序
6.2质量记录控制程序
7.质量记录
7.1出仓单
7.2装箱单
5.2.3货柜车到达公司后,由成品仓负责安排搬运人员及清点数量,外销部负责货物装放方式,装货完毕后,货柜封上承运公司的封条,并由承运公司开托运单。
5.3出货作业的搬运依《产品防护控制程序》执行。
5.4在出货时发货员要把产品的编码记录在发货记录上,以备之后查寻。
5.5相关质量记录以《质量记录控制程序》
5.1.4成品仓根据品管的签名确认是否出货;合格则可出货,不合格则需根据不合格处理单要求处理;
5.1.5货物上车后,由送货人员根据“出仓单”发货,详见《发货管理办法》。
5.2外销出货
5.2.1外销部接到客户交货通知后,应立即按客户要求开好“装箱单”交给客户,然后开“出仓单”,交成品仓仓管员作为出货依据。
- 1、下载文档前请自行甄别文档内容的完整性,平台不提供额外的编辑、内容补充、找答案等附加服务。
- 2、"仅部分预览"的文档,不可在线预览部分如存在完整性等问题,可反馈申请退款(可完整预览的文档不适用该条件!)。
- 3、如文档侵犯您的权益,请联系客服反馈,我们会尽快为您处理(人工客服工作时间:9:00-18:30)。
目的
为确保公司出货产品之质量与环保得以有效管控,满足客户之要求,特制定本办法。
适用范围
适用于制造部成品入库/出货检验、库存成品重新检验及供应商成品入库/出货检验等阶段。
权责
制造部
负责产品之加工、组装及自主检验等作业。
品保部
负责成品之尺寸与外观检验、功能测试及出货包装等检验作业; 负责出货产品之可靠性实验委托。
储运课
依品管单位之判定及标识,做适当之处置。
提出库存品重检。
理货及出货作业。
业务部
制订出货计划及安排出货相关作业。
生管课
特采申请之提出。
作业内容
作业流程图(见附件一)
成品检验
抽样计划
抽样计划若客户无特殊要求,则依MIL-STD-105EⅡ级单次抽样水平,若客户有要求,则依客要求订定。
详见《抽样检验作业办法》。
允收水平AQL: 重缺点:0.25 轻缺点:0.65。
如客户进料允收水平较本公司严格或客户对本公司出货检验允收水平有特别要求时,依客户允收水平。
产品性能(含功能及可靠性)采用计数值抽样,其允收水平一律为零缺点。
]
检验基准为成品检验规范、工程图面及规格书、工程样品等, 详见《抽样检验作业办法》。
详细作业内容参照《不合格品管制程序》之特采作业流程规定执行。
检测设备
使用之检验量具及仪器,品管应依校验单位之校验通知进行送校。
使用检验设备前,检验人员须确定校验日期是否过期或功能异常,如有异常立即通知校验单位并暂停使用。
检测设备之管理依《检测设备管制程序》规定执行。
统计技术
品管课资料统计人员依《统计技术管制程序》,将成品检验报告之结果进行统计分析,制作__月份( )质量异常统计表,提供相关单位作为质量改善依据。
出货检验
产品入库后,业务部根据相关要求开出出货计划表,由储运课执行理货动作。
储运课需确认出货品是否有超过库存期限,其库存期限之管理请参阅《产品防护管制程序》之规定。
若出货品超过库存期限,储运课需通知品管进行重新检验,检验方式参阅成品检验规范,若达判退标准则依《不合格品管制程序》执行之。
品管依照业务发出之出货计划表作为出货依据,针对已入库即将出货之所有产品,进行核对产品、外箱唛头标示、箱数、重量等是否正确,若有不正确情形,则要求相关责任单位进行重工,重工后品管则需重新确认。
若客户有额外之要求,储运课需依客户要求做适当之标示后,方准予出货。
不合格时统一由仓储单位修正,待品管复核确认合格后方可出货。
客户要求随货附带检验报告、实验报告或其它相关文件时,品管应确认相关报告或文件是否齐全、有效,绿色环保产品出货须出具ICP测试报告、产品成份表等相关证明文件,品管应检视其报告是否合格、是否在有效期限之内,具体情况可参考绿色环保物料管控表。
成品入库前实施入仓成品检验,即视同仓库为客户仓库,在入库前完成出货检验之成品检验部分,在出货交付
时完成包装要求的检验,但库存超过15天以上的产品,在出货时需重新进行全面的检验,并完成产品包装的全部检验。
供应商(委外加工)成品等入库检验
参照《进料检验作业办法》之相关规定实施,可靠性实验委托依《抽样检验作业办法》执行。
绿色环保产品出货检验作业相关规定详见《环保产品管制作业办法》与《环境管理物质检验规范》,不同客户的具体环境管理物质要求不同时,依《环境管理物质管制办法》执行。
记录之保存
检验记录由品管单位保存,保存期限参考《表单记录管制程序》。
参考文件
《检验与测试管制程序》《不合格品处理作业办法》《产品防护管制程序》《检测设备管制程序》《统计技术管制程序》《进料检验作业办法》《抽样检验作业办法》《环保产品管制作业办法》《环境管理物质管制办法》《环境管理物质检验规范》《表单记录管制程序》
相关表单
出/入库单
检验报告
过期重检单
质量异常处理/特采通知单。