汽车轻量化研究报告
汽车轻量化发展趋势报告(1)

汽车轻量化发展趋势报告①汽车轻量化不是什么新鲜的名词,但却是在近两年被提及的越来越频繁,从试点过渡到普遍的应用技术,汽车轻量化的优势不言而喻,然而每个企业对于轻量化的方向不同,所以也引发了很多争议。
什么是汽车轻量化汽车轻量化就是为汽车瘦身,在确保稳定提升性能的基础上,节能化设计各总成零部件,持续优化车型。
实验证明,若汽车整车重量降低10%,燃油效率可提高6%—8%;汽车重量降低1%,油耗可降低0.7%;汽车整备质量每减少100千克,百公里油耗可降低0.3—0.6升。
目前轻量化被最广泛应用的是铝合金的技术。
1990年9月开始销售的日本本田NSX车采用了全铝承载式车身,比用冷轧钢板制造的同样车身轻200kg,引起全世界的瞩目。
本田NSX车采用了全铝承载式车身近年来奥迪、捷豹、新揽胜都使用了全铝式的车身结构,铝合金已经成为了一种比较理想的轻量化材料,铝合金还可以按照添加合金的不同和比例的不同以及制造工艺的区别,应用在车身、车架、制动盘、发动机气缸体、气缸盖、活塞、进气歧管、摇臂、发动机悬置支架、空压机连杆、传动器壳体、离合器壳体、车轮、制动器零件、把手及罩盖壳体类等地方。
近年来,铝合金用于车身材料的加工方式的成本有所降低。
以前都要将厚的铝合金板冲压成薄板再进行加工,目前通用引入了和钢板冲压类似的热冲压成形技术。
奥迪ASF全铝车身结构这对工艺的要求是十分严格的,因为冲压时摩擦因数的增大,不仅会增加压边区材料进入成形区的难度,并且在成形区内,由于摩擦力的作用,截面各处材料流动不均,容易在应力集中地方产生急剧减薄而发生破裂。
协调好压边力与冲压力的关系,加上良好的润滑,是实现铝合金热冲压再次降低材料成本的关键。
当然铝合金作为大范围量产的轻量化材料固然理想,也有自身的缺点,比如工艺复杂且后续维修费用高。
对于本文,我们不对铝合金的材料做重点阐述,我们将主要讲解轻量化的其他发展方向。
碳纤维的春天当然,还有更多的轻量化材料和科技应用在现在的汽车当中,在文章开篇中提到的第六代宝马7系所使用的i3与i8轻量化科技,其中就包括了碳纤维车身。
SUV白车身有限元分析与轻量化研究的开题报告
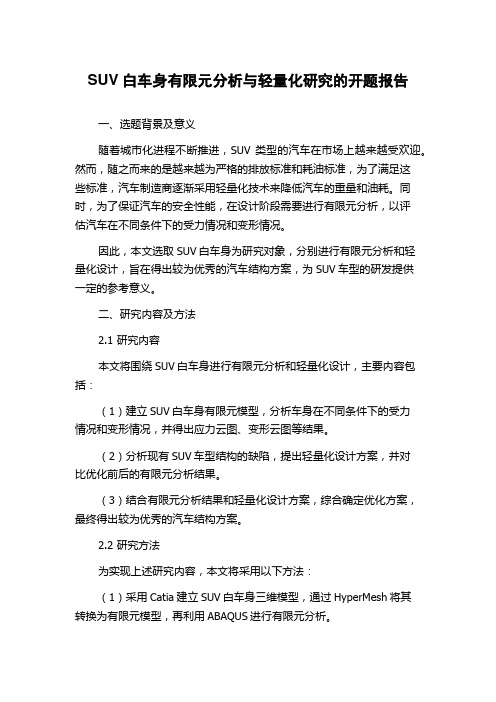
SUV白车身有限元分析与轻量化研究的开题报告一、选题背景及意义随着城市化进程不断推进,SUV类型的汽车在市场上越来越受欢迎。
然而,随之而来的是越来越为严格的排放标准和耗油标准,为了满足这些标准,汽车制造商逐渐采用轻量化技术来降低汽车的重量和油耗。
同时,为了保证汽车的安全性能,在设计阶段需要进行有限元分析,以评估汽车在不同条件下的受力情况和变形情况。
因此,本文选取SUV白车身为研究对象,分别进行有限元分析和轻量化设计,旨在得出较为优秀的汽车结构方案,为SUV车型的研发提供一定的参考意义。
二、研究内容及方法2.1 研究内容本文将围绕SUV白车身进行有限元分析和轻量化设计,主要内容包括:(1)建立SUV白车身有限元模型,分析车身在不同条件下的受力情况和变形情况,并得出应力云图、变形云图等结果。
(2)分析现有SUV车型结构的缺陷,提出轻量化设计方案,并对比优化前后的有限元分析结果。
(3)结合有限元分析结果和轻量化设计方案,综合确定优化方案,最终得出较为优秀的汽车结构方案。
2.2 研究方法为实现上述研究内容,本文将采用以下方法:(1)采用Catia建立SUV白车身三维模型,通过HyperMesh将其转换为有限元模型,再利用ABAQUS进行有限元分析。
(2)根据有限元分析结果确定优化方案,并利用HyperMesh对车身进行重构,再次进行有限元分析,对比优化前后的结果。
(3)分析不同方案的优缺点,结合实际情况,最终确定较为优秀的汽车结构方案。
三、预期成果及研究进展本文的预期成果包括:(1)建立SUV白车身的有限元模型,分析车身在不同条件下的受力情况和变形情况。
(2)提出轻量化设计方案,并利用有限元分析对比优化前后的结果,为SUV车型的研发提供一定的参考意义。
目前,已经完成了车身模型的建立和网格化,正在进行有限元分析和轻量化设计的工作。
预计在下学期完成全部研究工作,提交毕业设计。
汽车轻量化专题报告

目录一、会议简介 (1)(一)轻量化车身会议 (1)(二)中国汽车轻量化技术国际研讨会 (1)二、汽车轻量化概念 (1)(一)汽车轻量化的重要性 (1)(二)汽车轻量化的相关政策 (4)三、汽车轻量化的原则 (5)(一)保证足够的刚度 (5)(二)保证足够的强度 (6)(三)保持良好的疲劳耐久性能 (6)四、汽车轻量化的关键技术领域 (6)(一)轻量化设计技术 (6)(二)轻量化材料技术 (7)1.高强度钢 (7)2.铝合金 (9)3.非金属材料 (12)(三)轻量化制造技术 (13)(四)轻量化的发展趋势 (14)(五)轻量化的评价指标 (14)五、典型案例 (15)(一)东风风神E30纯电动汽车 (15)(二)诺贝丽斯全铝车身 (15)(三)长城华冠前途K5纯电动跑车的轻量化应用.. 16一、会议简介会议包括两项,中国轻量化车身会议和中国汽车轻量化技术国际研讨会。
(一)轻量化车身会议在轻量化车身会议中,有东风风神E30、吉利博瑞、广汽传祺GA6、奇瑞M16、上汽名爵锐腾、江淮瑞风A60、长安悦翔V7七款自主品牌车型参会,每家企业选派2-3名工程师,分别从设计、材料、工艺的角度介绍其车型的轻量化设计思想和设计理念。
(二)中国汽车轻量化技术国际研讨会会议采用讲座形式,主要是汽车轻量化相关的技术讲解。
涉及到汽车用高强度钢、汽车非金属材料、汽车非金属材料、汽车连接技术、汽车有色金属。
二、汽车轻量化概念汽车的轻量化,就是在保证汽车的强度和安全性能的前提下,尽可能地降低汽车的整备质量,从而提高汽车的动力性,减少燃料消耗,降低排气污染。
由于环保和节能的需要,汽车的轻量化已经成为世界汽车发展的潮流。
(一)汽车轻量化的重要性1.汽车轻量化是实现汽车产品节能减排的有效措施面对日益严峻的油耗法规,世界各国汽车企业都在采取积极的措施以推动汽车产品的节能减排,对燃油汽车来说,轻量化是一种有效的手段;对新能源汽车来说,轻量化可以有效增加新能源汽车续驶里程。
2023年汽车轻量化行业市场调查报告
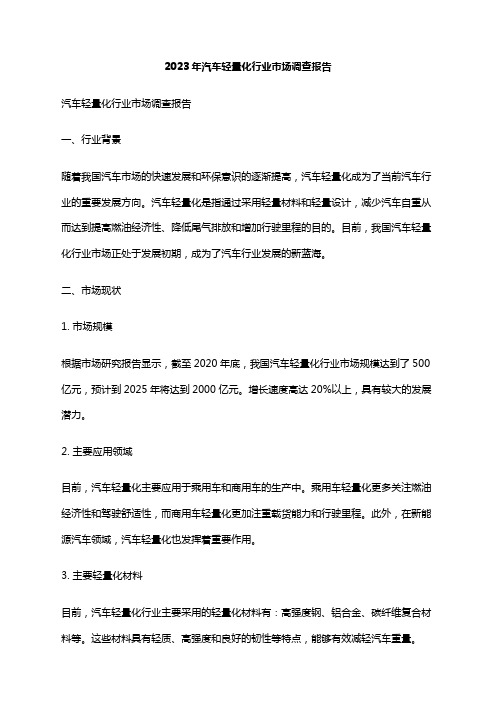
2023年汽车轻量化行业市场调查报告汽车轻量化行业市场调查报告一、行业背景随着我国汽车市场的快速发展和环保意识的逐渐提高,汽车轻量化成为了当前汽车行业的重要发展方向。
汽车轻量化是指通过采用轻量材料和轻量设计,减少汽车自重从而达到提高燃油经济性、降低尾气排放和增加行驶里程的目的。
目前,我国汽车轻量化行业市场正处于发展初期,成为了汽车行业发展的新蓝海。
二、市场现状1. 市场规模根据市场研究报告显示,截至2020年底,我国汽车轻量化行业市场规模达到了500亿元,预计到2025年将达到2000亿元。
增长速度高达20%以上,具有较大的发展潜力。
2. 主要应用领域目前,汽车轻量化主要应用于乘用车和商用车的生产中。
乘用车轻量化更多关注燃油经济性和驾驶舒适性,而商用车轻量化更加注重载货能力和行驶里程。
此外,在新能源汽车领域,汽车轻量化也发挥着重要作用。
3. 主要轻量化材料目前,汽车轻量化行业主要采用的轻量化材料有:高强度钢、铝合金、碳纤维复合材料等。
这些材料具有轻质、高强度和良好的韧性等特点,能够有效减轻汽车重量。
三、市场竞争1. 主要企业目前,我国汽车轻量化行业市场竞争激烈,主要企业包括上汽集团、吉利汽车、比亚迪、长城汽车等。
这些企业在轻量化技术研发、生产制造和市场推广等方面具有较强的实力。
2. 技术创新轻量化技术是企业在市场竞争中重要的竞争力。
目前,我国汽车轻量化行业企业广泛应用数值模拟、材料工程等先进技术,推动轻量化材料和设计工艺的创新。
此外,与国外企业合作、引进技术也是企业加强竞争的一种方式。
四、发展前景1. 政策支持我国政府近年来加大了对汽车轻量化行业的支持力度,推出了一系列鼓励政策,包括减免税收、资金支持和研发补贴等,以促进汽车轻量化的发展。
2. 环保压力随着环保压力的逐渐增大,汽车行业对汽车轻量化的需求将进一步增加。
汽车轻量化不仅可以减少尾气排放,降低环境污染,还能提高燃油经济性,降低能源消耗。
3. 新能源汽车需求随着新能源汽车的快速发展,汽车轻量化行业市场也将迎来新的机遇。
汽车轻量化材料力学性能实验报告

汽车轻量化材料力学性能实验报告一、实验背景随着环保和节能要求的不断提高,汽车轻量化已成为汽车工业发展的重要趋势。
轻量化材料的应用可以显著降低汽车的重量,从而提高燃油经济性、减少尾气排放,并提升车辆的性能。
在众多轻量化材料中,铝合金、高强度钢、镁合金和复合材料等因其优异的力学性能而受到广泛关注。
为了深入了解这些材料的力学性能,为汽车设计和制造提供可靠的数据支持,特进行本次实验。
二、实验目的本次实验的主要目的是对几种常见的汽车轻量化材料(铝合金、高强度钢、镁合金和复合材料)进行力学性能测试,包括拉伸试验、压缩试验和弯曲试验,获取材料的强度、刚度、韧性等力学性能参数,并对实验结果进行分析和比较,为汽车轻量化设计和选材提供依据。
三、实验材料与设备(一)实验材料1、铝合金:选用 6061-T6 铝合金板材,厚度为 3mm。
2、高强度钢:选用 Q345 高强度钢板材,厚度为 2mm。
3、镁合金:选用 AZ31B 镁合金板材,厚度为 25mm。
4、复合材料:选用碳纤维增强环氧树脂复合材料板材,厚度为2mm。
(二)实验设备1、万能材料试验机:型号为 WDW-100,最大试验力为 100kN,精度为 1%。
2、引伸计:精度为 05%,用于测量材料的变形。
3、游标卡尺:精度为 002mm,用于测量试样的尺寸。
四、实验过程(一)拉伸试验1、试样制备根据国家标准 GB/T 2281-2010《金属材料拉伸试验第 1 部分:室温试验方法》,分别从铝合金、高强度钢、镁合金和复合材料板材上加工拉伸试样。
试样的形状为矩形截面试样,标距长度为 50mm,原始横截面积通过测量试样的宽度和厚度计算得出。
2、试验步骤(1)将拉伸试样安装在万能材料试验机的夹头上,确保试样的轴线与试验机的加载轴线重合。
(2)设置试验机的加载速度为 2mm/min,启动试验机进行加载,直至试样断裂。
(3)在试验过程中,通过引伸计实时测量试样的变形,并记录试验力位移曲线。
《汽车材料及轻量化趋势》报告总结

《汽车材料及轻量化趋势》报告总结汽车材料及轻量化趋势报告总结随着环境保护和能源消耗的日益严重,汽车行业对节能减排和轻量化技术的需求越来越高。
本报告对当前汽车材料及轻量化趋势进行了研究和总结,以下为报告总结的主要内容。
首先,报告对目前汽车材料的使用情况进行了分析。
目前,汽车主要采用的材料包括钢铁、铝合金、塑料和复合材料等。
钢铁是汽车材料中使用最广泛的材料,其优点是强度高、价格低廉,但密度较大,不利于车辆的轻量化。
铝合金具有重量轻、强度高的特点,但价格相对较高。
塑料和复合材料具有重量轻、强度高、耐腐蚀等优点,但在成本和可回收性方面仍存在一定的挑战。
其次,报告对轻量化技术的发展趋势进行了探讨。
随着材料科学和工程技术的不断进步,新型材料的研发和应用也得到了广泛关注。
其中,碳纤维复合材料、镁合金和高强度钢等被认为是未来汽车轻量化的重要方向。
碳纤维复合材料具有高强度、高刚度和低密度的特点,可以显著减轻车辆重量,但制造成本较高。
镁合金具有重量轻、强度高和良好的可塑性,但存在易燃、易腐蚀和价格高等问题。
高强度钢通过优化合金设计和热处理工艺,可以在保证强度的前提下减轻材料的重量,但成本较高。
最后,报告对轻量化技术的市场前景进行了展望。
随着政府对环境保护和能源消耗的要求越来越严格,汽车行业对轻量化技术的需求将持续增加。
轻量化技术除了能够减少燃料消耗和排放,还能提高汽车的性能和安全性。
因此,未来几年内,轻量化技术有望在汽车行业取得广泛应用。
特别是碳纤维复合材料和高强度钢等新型材料的研发和应用将成为汽车轻量化的重要方向。
综上所述,汽车材料及轻量化趋势报告指出当前汽车材料的使用情况,并对轻量化技术的发展趋势进行了分析和总结。
报告认为,未来汽车行业对轻量化技术的需求将持续增加,并展望了轻量化技术的市场前景。
希望该报告可以为相关企业和研究机构提供有价值的参考和指导,推动汽车轻量化技术的研发和应用。
汽车轻量化材料项目可行性研究报告
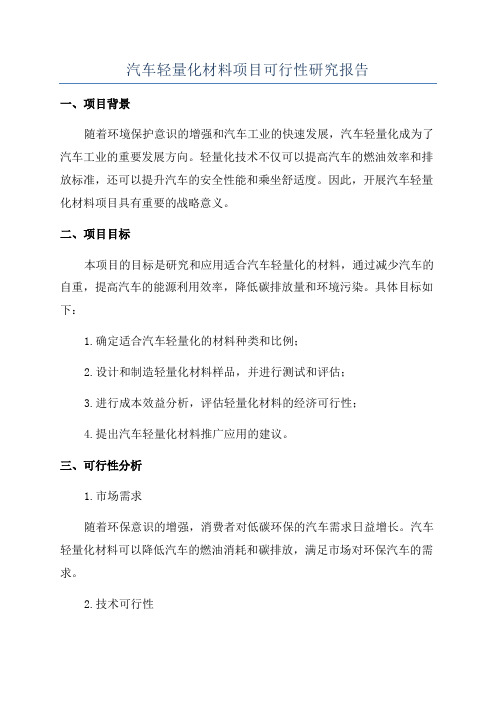
汽车轻量化材料项目可行性研究报告一、项目背景随着环境保护意识的增强和汽车工业的快速发展,汽车轻量化成为了汽车工业的重要发展方向。
轻量化技术不仅可以提高汽车的燃油效率和排放标准,还可以提升汽车的安全性能和乘坐舒适度。
因此,开展汽车轻量化材料项目具有重要的战略意义。
二、项目目标本项目的目标是研究和应用适合汽车轻量化的材料,通过减少汽车的自重,提高汽车的能源利用效率,降低碳排放量和环境污染。
具体目标如下:1.确定适合汽车轻量化的材料种类和比例;2.设计和制造轻量化材料样品,并进行测试和评估;3.进行成本效益分析,评估轻量化材料的经济可行性;4.提出汽车轻量化材料推广应用的建议。
三、可行性分析1.市场需求随着环保意识的增强,消费者对低碳环保的汽车需求日益增长。
汽车轻量化材料可以降低汽车的燃油消耗和碳排放,满足市场对环保汽车的需求。
2.技术可行性目前,轻量化材料的研究和应用已经取得了一定的进展。
材料科学和工程技术不断发展,为汽车轻量化提供了可行的技术方案。
3.经济可行性4.管理可行性轻量化材料的研究和应用需要进行科学而有效的管理。
项目管理团队应具备专业的知识和丰富的经验,确保项目的顺利进行和资源的合理配置。
四、项目实施方案1.确定研究内容确定适合汽车轻量化的材料种类和比例,并进行材料的性能测试和评估;2.设计和制造样品根据研究结果,设计和制造轻量化材料样品,进行性能测试和评估;3.成本效益分析对轻量化材料的研发和生产成本进行分析,评估其经济可行性;4.推广应用建议根据研究结果和成本效益分析,提出汽车轻量化材料的推广应用建议,包括技术支持、政策支持等方面。
五、预期成果1.确定适合汽车轻量化的材料种类和比例;2.设计和制造轻量化材料样品,并进行性能测试和评估;3.进行成本效益分析,评估轻量化材料的经济可行性;4.提出汽车轻量化材料推广应用的建议。
六、项目风险与对策1.技术风险:轻量化材料的研究和应用是一个较为复杂的工程,可能会出现技术难题。
汽车车门轻量化研究报告
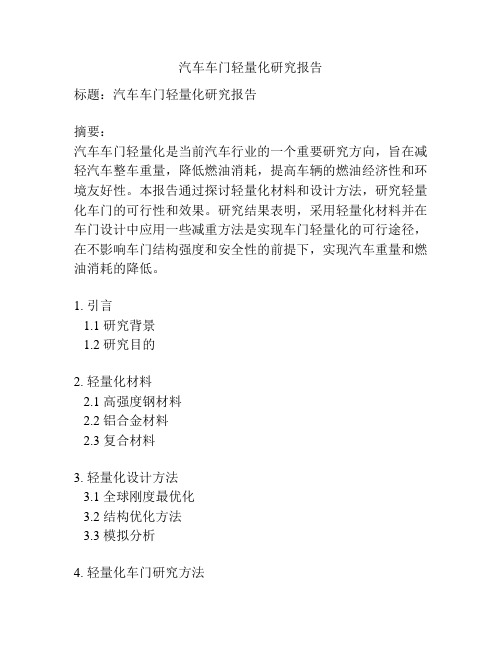
汽车车门轻量化研究报告
标题:汽车车门轻量化研究报告
摘要:
汽车车门轻量化是当前汽车行业的一个重要研究方向,旨在减轻汽车整车重量,降低燃油消耗,提高车辆的燃油经济性和环境友好性。
本报告通过探讨轻量化材料和设计方法,研究轻量化车门的可行性和效果。
研究结果表明,采用轻量化材料并在车门设计中应用一些减重方法是实现车门轻量化的可行途径,在不影响车门结构强度和安全性的前提下,实现汽车重量和燃油消耗的降低。
1. 引言
1.1 研究背景
1.2 研究目的
2. 轻量化材料
2.1 高强度钢材料
2.2 铝合金材料
2.3 复合材料
3. 轻量化设计方法
3.1 全球刚度最优化
3.2 结构优化方法
3.3 模拟分析
4. 轻量化车门研究方法
4.1 车门重量测量
4.2 车门结构强度测试
4.3 材料性能测试
5. 轻量化车门研究结果与讨论
5.1 材料比较分析
5.2 车门重量变化结果
5.3 结构强度与安全性分析
5.4 燃油消耗与经济性分析
6. 结论
6.1 轻量化车门的可行性
6.2 车门轻量化的效果
6.3 进一步研究建议
该报告针对汽车车门轻量化进行了深入研究,提供了轻量化材料和设计方法的详细介绍,并通过实验测试和数据分析来评估轻量化车门的效果。
该报告为汽车制造商和研发人员提供了有关轻量化车门的重要信息,并为进一步研究和开发提供了建议。
- 1、下载文档前请自行甄别文档内容的完整性,平台不提供额外的编辑、内容补充、找答案等附加服务。
- 2、"仅部分预览"的文档,不可在线预览部分如存在完整性等问题,可反馈申请退款(可完整预览的文档不适用该条件!)。
- 3、如文档侵犯您的权益,请联系客服反馈,我们会尽快为您处理(人工客服工作时间:9:00-18:30)。
在保证汽车的强度和安全性能的前提下,尽可能地 降低汽车的整备质量,从而提高汽车的动力性,减少燃 料消耗,降低排气污染。
意义
据研究,若汽车整车质量降低10%,燃油效率可提 高6%~8%;若滚动阻力减少10%,燃油效率可提高 3%;若车桥、变速器等机构的传动效率提高10%,燃 油效率可提高7%。从绝对量来说,汽车质量每降低 100kg,每百公里可节约0.6L燃油。
主流轻量化材料
既能保证车体结构的性能,又能大幅度降低车体重量的材料,目前行业内普遍使用的 是碳纤维、铝合金、镁合金、工程塑料等密度较小的材料。这些材料在车体结构中的使用, 轻量化效果非常明显。以铝合金车身的福特F150为例,车身实现了40%以上的减重,整备 质量降低了300kg。车身采用碳纤维和铝合金粘连工艺而成的宝马i3,轻量化效果更为明显, 作为纯电动车型整备质量却只有1195kg,相比同尺寸的常规车型来说,都要轻了150Kg左 右。
铝合金在轻量化中的应用
铸造铝合金
汽车工业是铝铸件的主要市场,例如日本,铝铸件的76%、铝压铸件的77%为汽车铸 件。铝合金铸件主要应用于发动机气缸体、气缸盖、活塞、进气歧管、摇臂、发动机 悬置支架、空压机连杆、传动器壳体、离合器壳体、车轮、制动器零件、把手及罩盖 壳体类零件等。 铝铸件中不可避免地存在缺陷,压铸件还不能热处理,因此在用铝合金来生产要求较 高强度铸件时受到限制。为此在铸件生产工艺上作了改进,铸造锻造法和半固态成型 法将是未来较多用的工艺。
主要途径
一、通过结构的合理、精准化设计,对车体的主要承力部件进行加强、非主要承力部件
进行合理的弱化,在性能满足的前提下尽量减小传力通道截面大小,合理、精细化的选 用材料板厚等来实现结构轻量化设计。 二、使用新材料替代普通钢材来实现轻量化设计,比如用铝合金、GFRP(玻璃纤维增强 塑料)和CFRP(碳纤维)等密度更小的新材料来代替钢材来实现轻量化设计,比如用强度 更高、板厚更薄的热成型材料(热成型材料本质上还是钢材)代替普通高强度钢来减少 加强结构零件的数量实现轻量化设计。
汽车轻量化 2016
•
近年来,能源与环境的危机加速了各国政府对汽车行业的产品能耗和排 放的严格控制。到2020年,除美国之外的全球主要的汽车生产与消费国家 和地区对乘用车燃油油耗的要求都将严格限制在5L/100km以下的水平,而 且碳排放也更为严格(国内在2020将采用国Ⅵ的排放标准)。
定义
铝合金在轻量化中的应用
2
变形铝合金
变形铝合金指铝合金板带材、挤压型材和锻造材,在汽车上主要用于车身面板、车身骨架、 发动机散热器、空调冷凝器、蒸发器、车轮、装饰件和悬架系统零件等。 由于轻量化效果明显,铝合金在车身上的应用正在扩大。如1990年9月开始销售的日本本田 NSX车采用了全铝承载式车身,比用冷轧钢板制造的同样车身轻200kg,引起全世界的瞩目。 NSX全车用铝材达到31.3%,如在全铝车身上,外板使用6000系列合金,内板使用5052-0合 金,骨架大部使用5182-0合金;由于侧门框对强度和刚度要求很高,使用以6N01合金为基础、 适当调整了Mg和Si含量的合金。在欧美也有用2036和2008合金作车身内外板的。 铝散热器发源于欧洲而后遍及全世界。在欧洲,到20世纪80年代后期铝散热器已占领市场的 90%。随?车用空调、油冷却器等的大量使用,铝热交换器的市场迅速扩大。从材料的角度看, 铝在热交换器上的广泛应用在很大程度上归功于包覆料覆层铝板和铝带的成功开发。
汽车轻量化的发展现状2016
2016年的夏天,汽车轻量化研究与推广着
实火了一把。除了第20届德累斯顿国际轻 量化论坛在德国举办,家门口的上海国际 新能源及智能化技术展览会也专门设置了 “汽车轻量化发展趋势”主题环节。 在我国,随着2020年当年产乘用车平均燃 料消耗降至5.0升/百公里的目标越来越近, 很多汽车制造商都在寻找提升燃油效率的 方法。
铝合金在轻量化中的应用
3
铝基复合材料
铝基复合材料密度低、比强度和比模量高、抗热疲劳性能好,但在汽车上的应用受到价格及 生产质量控制等方面的制约,还没有形成很大的规模。目前,铝基复合材料在连杆、活塞、 气缸体内孔、制动盘、制动钳和传动轴管等零件上的试验或使用显示出了卓越的性能,如本 田公司开发成功的由不?钢丝增强的铝基复合材料连杆比钢制连杆降重30%,对1.2L的汽油发 动机可提高燃料经济性5%;采用激冷铝合金粉末与SiC粉末(重量百分数2%)混合并挤压成棒材, 用此棒材经锻造成型的活塞因强度高可降重20%,发动机功率大幅度提高;用铝基复合材料强 化活塞头部而取消第一道环槽的奥氏体铸铁镶块可降重20%;铝基复合材料制动盘比铸铁制动 盘降重50%。
应用
在整车中,质量最大的组件为动力系统、底盘系统以及车身,这3大系统的总质量达到整车质 量的83%,其中车身质量占比为28%。
据预测,汽车材料铝化率达到60%在经济上是可取的。近年来,发达国家汽车用铝大幅提高,全球 汽车平均用铝量1978年仅50kg/辆,2008年上升到107kg/辆,增长了1.14倍;估计10年后可以提高 到300kg/辆,在发达国家更是可以提高到320kg/辆。近年来奥迪、捷豹路虎、福特等都使用了全铝 式的车身结构,铝合金已经成为了一种比较理想的轻量化材料。另外,铝合金还可以按照添加合金 的不同和比例的不同以及制造工艺的区别,应用在车身、车架、制动盘、发动机气缸体、气缸盖、 活塞、进气歧管、摇臂、发动机悬置支架、空压机连杆、传动器壳体、离合器壳体、车轮、制动 器零件、把手及罩盖壳体类等地方。
铝合金在汽车中各系统的使用比例可以见下图,主要使用是在车身和底盘系统部件中
车用轻量化新材料使用成本
目前国内每吨车用冷轧汽车板材的成本在5000~9000之间,而每吨铝合金的材料成本 高达4.5万左右,碳纤维的材料成本则更高,每吨约在80万左右,又因为其较高的成型废品 率问题,让很多中低端车型在碳纤维的使用上更是望而却步。所以目前采用铝合金、碳纤 维等新材料作为车身主结构的车型售价基本都在40万以上,铸铝件则较早就在发动机壳体、 悬架摆臂、副车架等底盘和动力系统部件上使用,因所占车型开发成本比例较小,搭载车 型级别不一。