PCB板焊盘与通孔的设计规范标准
pcb焊盘设计规范
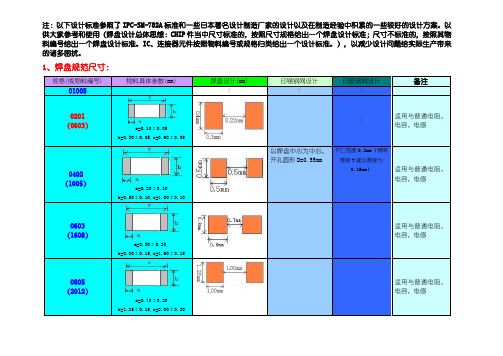
注:以下设计标准参照了IPC-SM-782A标准和一些日本著名设计制造厂家的设计以及在制造经验中积累的一些较好的设计方案。
以供大家参考和使用(焊盘设计总体思想:CHIP件当中尺寸标准的,按照尺寸规格给出一个焊盘设计标准;尺寸不标准的,按照其物料编号给出一个焊盘设计标准。
IC、连接器元件按照物料编号或规格归类给出一个设计标准。
),以减少设计问题给实际生产带来的诸多困扰。
1、焊盘规范尺寸:规格(或物料编号) 物料具体参数(mm) 焊盘设计(mm) 印锡钢网设计印胶钢网设计备注01005 / / / /0201(0603)a=0.10±0.05b=0.30±0.05,c=0.60±0.05 /适用与普通电阻、电容、电感0402(1005)a=0.20±0.10b=0.50±0.10,c=1.00±0.10 以焊盘中心为中心,开孔圆形D=0.55mm开口宽度0.2mm(钢网厚度T建议厚度为0.15mm)适用与普通电阻、电容、电感0603(1608)a=0.30±0.20,b=0.80±0.15,c=1.60±0.15 适用与普通电阻、电容、电感0805(2012)a=0.40±0.20b=1.25±0.15,c=2.00±0.20 适用与普通电阻、电容、电感1206(3216)a=0.50±0.20b=1.60±0.15,c=3.20±0.20 适用与普通电阻、电容、电感1210(3225)a=0.50±0.20b=2.50±0.20,c=3.20±0.20 适用与普通电阻、电容、电感1812(4532)a=0.50±0.20b=3.20±0.20,c=4.50±0.20 适用与普通电阻、电容、电感2010(5025)a=0.60±0.20b=2.50±0.20,c=5.00±0.20 适用与普通电阻、电容、电感2512(6432)a=0.60±0.20b=3.20±0.20,c=6.40±0.20 适用与普通电阻、电容、电感1:1开口,不避锡珠5700-250AA2-0300排阻0404(1010)a=0.25±0.10,b=1.00±0.10c=1.00±0.10,d=0.35±0.10p=0.65±0.05排阻0804(2010)a=0.25±0.10,b=2.00±0.10c=1.00±0.10,d=0.30±0.15p=0.50±0.05排阻1206(3216)a=0.30±0.15,b=3.2±0.15c=1.60±0.15,d=0.50±0.15p=0.80±0.10排阻 1606 (4016)a=0.25±0.10,b=4.00±0.20 c=1.60±0.15,d=0.30±0.10p=0.50±0.05472X-R05240-10a=0.38±0.05,b=2.50±0.10 c=1.00±0.10,d=0.20±0.05 d1=0.40±0.05,p=0.50钽质电容适用于钽质电容1206 (3216) a=0.80±0.30,b=1.60±0.20 c=3.20±0.20,d=1.20±0.10 A=1.50,B=1.20,G=1.401411 (3528) a=0.80±0.30,b=2.80±0.20 c=3.50±0.20,d=2.20±0.10 A=1.50,B=2.20,G=1.702312 (6032) a=1.30±0.30,b=3.20±0.30 c=6.00±0.30,d=2.20±0.10 A=2.00,B=2.20,G=3.202917 (7243)a=1.30±0.30,b=4.30±0.30 c=7.20±0.30,d=2.40±0.10A=2.00,B=2.40,G=4.50铝质电解电容适用于铝质电解电容(Ø4×5.4)d=4.0±0.5h=5.4±0.3a=1.8±0.2,b=4.3±0.2c=4.3±0.2,e=0.5~0.8p=1.0A=2.40,B=1.00P=1.20,R=0.50(Ø5×5.4)d=5.0±0.5h=5.4±0.3a=2.2±0.2,b=5.3±0.2c=5.3±0.2,e=0.5~0.8p=1.3A=2.80,B=1.00P=1.50,R=0.50(Ø6.3×5.4)d=6.3±0.5h=5.4±0.3a=2.6±0.2,b=6.6±0.2c=6.6±0.2,e=0.5~0.8p=2.2A=3.20,B=1.00P=2.40,R=0.50(Ø6.3×7.7)d=6.3±0.5h=7.7±0.3a=2.6±0.2,b=6.6±0.2c=6.6±0.2,e=0.5~0.8p=2.2A=3.20,B=1.00P=2.40,R=0.50(Ø8.0×6.5)d=6.3±0.5h=7.7±0.3a=3.0±0.2,b=8.3±0.2c=8.3±0.2,e=0.5~0.8p=2.2A=3.20,B=1.00P=2.40,R=0.50(Ø8×10.5)d=8.0±0.5h=10.5±0.3a=3.0±0.2,b=8.3±0.2c=8.3±0.2,e=0.8~1.1p=3.1A=3.60,B=1.30P=3.30,R=0.65(Ø10×10.5)d=10.0±0.5h=10.5±0.3a=3.5±0.2,b=10.3±0.2c=10.3±0.2,e=0.8~1.1p=4.6A=4.20,B=1.30P=4.80,R=0.65二极管(SMA) 4500-234031-T0 4500-205100-T0a=1.20±0.30b=2.60±0.30,c=4.30±0.30d=1.45±0.20,e=5.2±0.30二极管(SOD-323)4500-141482-T0a=0.30±0.10b=1.30±0.10,c=1.70±0.10d=0.30±0.05,e=2.50±0.20二极管(3515)a=0.30b=1.50±0.1,c=3.50±0.20二极管(5025)a=0.55b=2.50±0.10, c=5.00±0.20 三极管(SOT-523)a=0.40±0.10,b=0.80±0.05c=1.60±0.10,d=0.25±0.05p=1.00三极管(SOT-23)a=0.55±0.15,b=1.30±0.10c=2.90±0.10,d=0.40±0.10p=1.90±0.10SOT-25a=0.60±0.20,b=2.90±0.20c=1.60±0.20,d=0.45±0.10p=1.90±0.10SOT-26a=0.60±0.20,b=2.90±0.20c=1.60±0.20,d=0.45±0.10p=0.95±0.05SOT-223a1=1.75±0.25,a2=1.5±0.25b=6.50±0.20,c=3.50±0.20d1=0.70±0.1,d2=3.00±0.1p=2.30±0.05SOT-89a1=1.0±0.20,a2=0.6±0.20b=2.50±0.20,c=4.50±0.20d1=0.4±0.10,d2=0.5±0.10d3=1.65±0.20,p=1.5±0.05TO-252a1=1.1±0.2,a2=0.9±0.1b=6.6±0.20,c=6.1±0.20d1=5.0±0.2,d2=Max1.0e=9.70±0.70,p=2.30±0.10TO-263-2a1=1.30±0.1,a2=2.55±0.25b=9.97±0.32,c=9.15±0.50d1=1.3±0.10,d2=0.75±0.24e=15.25±0.50,p=2.54±0.10TO-263-3a1=1.30±0.1,a2=2.55±0.25b=9.97±0.32,c=9.15±0.50d1=1.3±0.10,d2=0.75±0.24e=15.25±0.50,p=2.54±0.10 TO-263-5a1=1.66±0.1,a2=2.54±0.20b=10.03±0.15,c=8.40±0.20d=0.81±0.10,e=15.34±0.2p=1.70±0.10SOP(引脚(Pitch>0.65mm)A=a+1.0,B=d+0.1G=e-2*(0.4+a)P=pSOP(Pitch≦0.65mm)A=a+0.7,B=dG=e-2*(0.4+a)P=pSOJ(Pitch≧0.8mm)A=1.8mm,B=d2+0.10mmG=g-1.0mm,P=pQFP(Pitch≧0.65mm)A=a+1.0,B=d+0.05P=pG1=e1-2*(0.4+a)G2=e2-2*(0.4+a)QFP(Pitch=0.5mm)A=a+0.9,B=0.25mmP=pG1=e1-2*(0.4+a)G2=e2-2*(0.4+a)QFP(Pitch=0.4mm)A=a+0.8,B=0.19mmP=pG1=e1-2*(0.4+a)G2=e2-2*(0.4+a) 引脚长由原来的a+0.70mm更改为a+0.80mm,有利于修理和印刷拉尖的处理。
pcb焊孔间距标准

pcb焊孔间距标准
PCB焊孔间距标准是指导PCB设计的重要规范之一,其要点包括:
1.导线的间距。
根据PCB生产厂家的生产能力,走线与走线之间的间距不
得低于4MIL。
在有条件的情况下,最小线距最好是越大越好。
常规的10MIL比较常见。
2.焊盘孔径与焊盘宽度。
焊盘孔径如果以机械钻孔方式,最小不得低于
0.2mm。
而孔径公差根据板材不同略微有所区别,一般能管控在0.05mm
以内。
焊盘宽度最小不得低0.2mm。
3.焊盘与焊盘的间距。
根据PCB生产厂家的加工能力,焊盘与焊盘的间距
不得小于0.2MM。
4.铜皮与板边之间的间距。
带电铜皮与PCB板边的间距最好不小于0.3mm,
如果是大面积铺铜,通常也是与板边需要有内缩距离,一般设为20mil。
5.孔间距问题。
钻孔按功能可分为零件孔、工具孔、通孔、盲孔、埋孔等。
在钻完第一个孔过后,在钻第二个孔时一边方向的材质会过薄,造成钻咀受力不均及钻咀散热不一,导致断钻咀,从而造成PCB孔崩不美观或漏钻孔不导通。
PCB板焊盘与通孔的设计规范标准

PCB设计工艺规范1概述与范围本规范规定了印制板设计应遵循的基本工艺规范,适合于公司的印制电路板设计。
2 .性能等级(Class)在有关的IPC标准中建立了三个通用的产品等级(class),以反映PCB在复杂程度、功能性能和测试/检验方面的要求。
设计要求决定等级。
在设计时应根据产品等级要求进行设计和选择材料。
第一等级通用电子产品包括消费产品、某些计算机和计算机外围设备、以及适合于那些可靠性要求不高,外观不重要的电子产品。
第二等级专用服务电子产品包括那些要求高性能和长寿命的通信设备、复杂的商业机器、仪器和军用设备,并且对这些设备希望不间断服务,但允许偶尔的故障。
第三等级高可靠性电子产品包括那些关键的商业与军事产品设备。
设备要求高可靠性,因故障停机是不允许的。
2.1组装形式PCB的工艺设计首先应该确定的就是组装形式,即SMD与THC在PCB正反两面上的布局,不同的组装形式对应不同的工艺流程。
设计者设计印制板应考虑是否能最大限度的减少流程问题,这样不但可以降低生产成本,而且能提高产品质量。
因此,必须慎重考虑。
针对公司实际情况,应该优选表1所列形式之一。
表1 PCB组装形式3. PCB材料3. 1 PCB基材:PCB基材的选用主要根据其性能要求选用,推荐选用FR— 4环氧树脂玻璃纤维基板。
选择时应考虑材料的玻璃转化温度、热膨胀系数(CTE、热传导性、介电常数、表面电阻率、吸湿性等因素。
3. 2印制板厚度范围为0.5m叶6.4mm常用0.5mm,0.8mm,1mm,1.6mm,2.4mm,3.2m ft种。
3. 3铜箔厚度:厚度种类有18u,35u,50u,70u。
通常用18u、35u。
3. 4 最大面积:X*Y=460mm350mm 最小面积:X*Y=50mm50mm3. 5在印刷板的上下两表面印刷上所需要的标志图案和文字代号等,例如元件标号和标称值、元件外廓形状和厂家标志、生产日期等等。
丝印字符要有 1.5~2.0mm的高度。
PCB板焊盘及通孔的设计规范分析
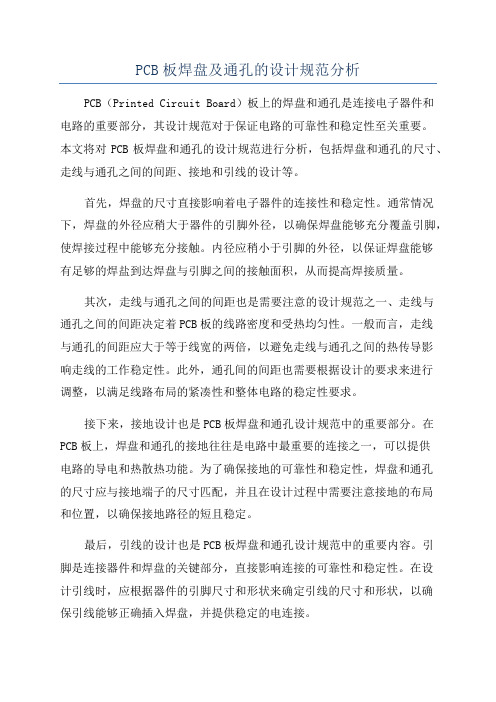
PCB板焊盘及通孔的设计规范分析PCB(Printed Circuit Board)板上的焊盘和通孔是连接电子器件和电路的重要部分,其设计规范对于保证电路的可靠性和稳定性至关重要。
本文将对PCB板焊盘和通孔的设计规范进行分析,包括焊盘和通孔的尺寸、走线与通孔之间的间距、接地和引线的设计等。
首先,焊盘的尺寸直接影响着电子器件的连接性和稳定性。
通常情况下,焊盘的外径应稍大于器件的引脚外径,以确保焊盘能够充分覆盖引脚,使焊接过程中能够充分接触。
内径应稍小于引脚的外径,以保证焊盘能够有足够的焊盐到达焊盘与引脚之间的接触面积,从而提高焊接质量。
其次,走线与通孔之间的间距也是需要注意的设计规范之一、走线与通孔之间的间距决定着PCB板的线路密度和受热均匀性。
一般而言,走线与通孔的间距应大于等于线宽的两倍,以避免走线与通孔之间的热传导影响走线的工作稳定性。
此外,通孔间的间距也需要根据设计的要求来进行调整,以满足线路布局的紧凑性和整体电路的稳定性要求。
接下来,接地设计也是PCB板焊盘和通孔设计规范中的重要部分。
在PCB板上,焊盘和通孔的接地往往是电路中最重要的连接之一,可以提供电路的导电和热散热功能。
为了确保接地的可靠性和稳定性,焊盘和通孔的尺寸应与接地端子的尺寸匹配,并且在设计过程中需要注意接地的布局和位置,以确保接地路径的短且稳定。
最后,引线的设计也是PCB板焊盘和通孔设计规范中的重要内容。
引脚是连接器件和焊盘的关键部分,直接影响连接的可靠性和稳定性。
在设计引线时,应根据器件的引脚尺寸和形状来确定引线的尺寸和形状,以确保引线能够正确插入焊盘,并提供稳定的电连接。
综上所述,PCB板焊盘和通孔的设计规范对于保证电路的可靠性和稳定性至关重要。
设计时需注意焊盘和通孔的尺寸、走线与通孔之间的间距、接地和引线的设计等方面,以确保电路的正常工作。
同时,还需要根据具体的设计要求和器件特性进行调整和优化,以提高电路的可靠性和稳定性。
PCB焊盘与孔设计规范

PCB 焊盘与孔设计工艺规范1. 目的规范产品的PCB焊盘设计工艺,规定PCB焊盘设计工艺的相关参数,使得PCB 的设计满足可生产性、可测试性、安规、EMC、EMI 等的技术规范要求,在产品设计过程中构建产品的工艺、技术、质量、成本优势。
2. 适用范围本规范适用于空调类电子产品的PCB 工艺设计,运用于但不限于PCB 的设计、PCB 批产工艺审查、单板工艺审查等活动。
本规范之前的相关标准、规范的内容如与本规范的规定相抵触的,以本规范为准3.引用/参考标准或资料TS—S0902010001 <<信息技术设备PCB 安规设计规范>>TS—SOE0199001 <<电子设备的强迫风冷热设计规范>>TS—SOE0199002 <<电子设备的自然冷却热设计规范>>IEC60194 <<印制板设计、制造与组装术语与定义>> (Printed Circuit Board designmanufacture and assembly-terms and definitions)IPC—A—600F <<印制板的验收条件>> (Acceptably of printed board)IEC609504.规范内容4.1焊盘的定义通孔焊盘的外层形状通常为圆形、方形或椭圆形。
具体尺寸定义详述如下,名词定义如图所示。
1)孔径尺寸:若实物管脚为圆形:孔径尺寸(直径)=实际管脚直径+0.20∽0.30mm(8.0∽12.0MIL)左右;若实物管脚为方形或矩形:孔径尺寸(直径)=实际管脚对角线的尺寸+0.10∽0.20mm(4.0∽8.0MIL)左右。
2)焊盘尺寸:常规焊盘尺寸=孔径尺寸(直径)+0.50mm(20.0 MIL)左右。
4.2 焊盘相关规范4.2.1所有焊盘单边最小不小于0.25mm,整个焊盘直径最大不大于元件孔径的3倍。
PCB焊盘与孔径设计一般规范

PCB焊盘与孔径设计一般规范PCB焊盘与孔径设计是PCB设计中非常重要的一环,它直接影响到焊接质量和可靠性。
下面是PCB焊盘与孔径设计的一般规范,供参考:1.焊盘设计:-焊盘形状:常见的焊盘形状有圆形、方形和矩形等,一般情况下,圆形焊盘比较容易打磨,方形和矩形焊盘则更容易定位。
-焊盘大小:焊盘的尺寸应根据焊接工艺和元件封装尺寸进行合理设计,通常要留出一定的空余空间,以便焊接时不会出现短路现象。
-焊盘间距:焊盘之间的间距应根据PCB板的层数和制板工艺进行设计,一般情况下,在同一面板上焊盘间距应大于焊锡的间隙。
-焊盘位置:焊盘的位置应根据被连接元件的布局进行合理设计,避免受限制、干扰和误操作等问题。
- 焊盘标记:焊盘应标明焊盘编号和对应的元件设计ator,以方便组装时的对应和定位。
-焊盘连接:焊盘与元件之间的连接方式可以采用电镀(HAL、ENIG等)或者热转印等方法,根据实际需求选择合适的连接方式。
2.孔径设计:- 孔径规格:孔径的大小取决于被连接元件的引脚,通常按照元件的要求进行设计。
常见的孔径规格有0.25mm、0.3mm、0.35mm等。
-孔径形状:常见的孔径形状有圆形、椭圆形和矩形等,一般情况下,圆孔比较容易进行穿孔操作,矩形孔适用于非标准元件的布局。
-孔径间距:孔径之间的间距应根据PCB板的层数和制板工艺进行设计,一般情况下,孔径间距应大于孔径的直径。
-孔径位置:孔径的位置应根据被连接元件的布局进行合理设计,避免受限制、干扰和误操作等问题。
- 孔径划线:孔径应标明孔径编号和对应的元件设计ator,以方便组装时的对应和定位。
-孔径填充:如果没有被连接元件需要通过孔径连接的话,可以考虑在孔径上进行焊盘填充,以增加板的机械强度。
总的来说,焊盘与孔径的设计需要考虑到焊接工艺、元件布局、层数和制板工艺等因素,合理设计可以提高焊接质量和可靠性。
每个项目都有其特定的需求,因此在实际设计前最好与组装、制板等相关人员进行沟通与确认。
PCB板焊盘及通孔的设计规范
PCB板焊盘及通孔的设计规范PCB板(Printed Circuit Board)的焊盘和通孔是PCB设计中非常重要的部分。
焊盘和通孔的设计规范直接影响着PCB板的可靠性和性能。
下面将详细介绍焊盘和通孔的设计规范。
-焊盘尺寸:焊盘的尺寸要足够大,以便实现良好的焊接和质量控制。
一般来说,焊盘的直径应大于焊点直径的1.5到2倍。
-焊盘间距:相邻焊盘之间的间距应足够大,以确保焊接的可靠性和防止短路。
一般来说,焊盘之间的间距应大于焊盘直径的1倍。
-焊盘形状:常见的焊盘形状有圆形、方形和椭圆形等。
在选择焊盘形状时,应考虑到焊接工艺和组装工艺的要求。
-焊盘排列方式:焊盘的排列方式通常有线性排列和阵列排列两种。
线性排列适用于较简单的电路板,而阵列排列适用于多通道或高密度的电路板。
- 焊盘材料:常见的焊盘材料有HASL(Hot Air Solder Leveling)、金属化和电镀等。
选择合适的焊盘材料可以增强焊接的可靠性和稳定性。
-通孔类型:通孔通常分为过孔和盲孔两种类型。
过孔是从一侧通过整个电路板,而盲孔只在一侧存在。
选择合适的通孔类型取决于PCB板的设计要求和组装工艺。
-通孔尺寸:通孔的尺寸应根据焊接或组装的需求来确定。
一般来说,通孔的直径应大于插入物件的直径。
-通孔间距:相邻通孔之间的间距应足够大,以避免电气和机械冲突。
一般来说,通孔之间的间距应大于通孔直径的3倍。
-通孔位置:通孔的位置应根据电路板的布局和连接要求来确定。
通孔的位置应尽量靠近连接元件,以减少走线长度和电阻。
-通孔涂覆:通常情况下,通孔需要涂覆防腐层以保护其表面和内部金属不受氧化,常用的涂覆材料有锡、镍和金等。
综上所述,焊盘和通孔的设计规范是PCB设计中非常重要的环节。
合理的设计可以提高PCB板的可靠性、性能和生产效率。
PCB设计工艺要求
目的:明确设计PCB过程中的工艺各项要求,做到标准化设计。
以提高开发效率及方便生产。
适用范围:适用于本公司的电话机产品设计。
职责:各开发工程师及PCB Layout工程师按规定执行。
1、单面板要求:1:线径、线距不小于0.3mm,建议为0.35mm以上。
(半玻纤板及玻纤板不小于0.18mm)。
2:焊盘和焊盘之间的间距不小于0.5mm。
3:走线至板边距离板不小于0.8mm。
4:过孔至板边距离不小于1.6mm。
5:元件焊盘孔径不小于0.7mm。
6:丝印文字线宽不小于0.18mm,SMT不小于0.13mm。
7:板的碳桥宽度不小于2.0mm。
碳桥与碳桥之间的距离不小于1mm。
碳桥越短越好,最长不能超过15mm。
(除非特殊限制,但需项目工程师以上人员同意才能使用)8:板边宽的部分离焊盘必须大于3mm以上,SMT板大于5mm。
9:固定螺丝的孔位直径5mm以内不能有元件实体;与非地线的铜皮直径距离为5mm。
2、双面板要求:1:线径、线距(金板)不小于0.15mm。
(锡板不小于0.18mm)2:线边距板边不小于0.8mm。
3:孔边距板边不小于1.6mm。
4:孔径不小于0.35mm。
5:丝印文字线宽不小于0.18mm,SMT不小于0.13mm。
6:板边宽的部分离焊盘必须大于3mm以上,SMT板大于5mm。
7:焊盘和焊盘之间的间距不小于0.5mm8:固定螺丝的孔位直径5mm以内不能有元件实体;与非地线的铜皮直径距离为5mm。
9:双面板PCB螺丝孔位不能灌铜(锡浆板除外)。
3、PCB设计布局及走线等基本要求:1、所有元件放置要有规律,同一工作部分电路尽量靠在一起,避免走长线;电阻要平插元件尽量排成行,如无特殊要求尽量减少直立元件插件。
2、外线进线部分(包括压敏电阻)必须靠在一起,因开关电路以前的电路属于高压部分,此走线不要太长越短越好,铜皮走线线径不能小于0.45mm;,不要靠近其它信号线和CPU的IO口,避免对它的干扰。
(完整版)PCB焊盘与孔径设计一般规范(仅参考)
PCB 焊盘与孔设计工艺规范1. 目的规范产品的PCB焊盘设计工艺,规定PCB焊盘设计工艺的相关参数,使得PCB 的设计满足可生产性、可测试性、安规、EMC 、EMI 等的技术规范要求,在产品设计过程中构建产品的工艺、技术、质量、成本优势。
2. 适用范围本规范适用于空调类电子产品的PCB 工艺设计,运用于但不限于PCB 的设计、PCB 批产工艺审查、单板工艺审查等活动。
本规范之前的相关标准、规范的内容如与本规范的规定相抵触的,以本规范为准3. 引用/参考标准或资料TS—S0902010001 << 信息技术设备PCB 安规设计规范>>TS—SOE0199001 << 电子设备的强迫风冷热设计规范>>TS—SOE0199002 << 电子设备的自然冷却热设计规范>>IEC60194 << 印制板设计、制造与组装术语与定义>> ( Printed Circuit Board design manufacture and assembly-terms and definitions )IPC—A—600F << 印制板的验收条件>> ( Acceptably of printed board ) IEC609504. 规范内容4.1 焊盘的定义通孔焊盘的外层形状通常为圆形、方形或椭圆形。
具体尺寸定义详述如下,名词定义如图所示。
1) 孔径尺寸:若实物管脚为圆形:孔径尺寸(直径) =实际管脚直径+0.20 ∽0.30mm(8.0∽12.0MIL )左右;若实物管脚为方形或矩形: 孔径尺寸(直径) =实际管脚对角线的尺寸+0.10 ∽0.20mm( 4.0 ∽8.0MIL )左右。
2) 焊盘尺寸:常规焊盘尺寸=孔径尺寸(直径) +0.50mm(20.0 MIL) 左右。
4.2 焊盘相关规范4.2.1 所有焊盘单边最小不小于0.25mm,整个焊盘直径最大不大于元件孔径的 3 倍。
(完整版)PCB焊盘与孔径设计一般规范(仅参考)
PCB 焊盘与孔设计工艺规范1. 目的规范产品的PCB焊盘设计工艺,规定PCB焊盘设计工艺的相关参数,使得PCB 的设计满足可生产性、可测试性、安规、EMC、EMI 等的技术规范要求,在产品设计过程中构建产品的工艺、技术、质量、成本优势。
2. 适用范围本规范适用于空调类电子产品的PCB 工艺设计,运用于但不限于PCB 的设计、PCB 批产工艺审查、单板工艺审查等活动。
本规范之前的相关标准、规范的内容如与本规范的规定相抵触的,以本规范为准3.引用/参考标准或资料TS—S0902010001 <<信息技术设备PCB 安规设计规范>>TS—SOE0199001 <<电子设备的强迫风冷热设计规范>>TS—SOE0199002 <<电子设备的自然冷却热设计规范>>IEC60194 <<印制板设计、制造与组装术语与定义>> (Printed Circuit Board designmanufacture and assembly-terms and definitions)IPC—A—600F <<印制板的验收条件>> (Acceptably of printed board)IEC609504.规范内容4.1焊盘的定义通孔焊盘的外层形状通常为圆形、方形或椭圆形。
具体尺寸定义详述如下,名词定义如图所示。
1)孔径尺寸:若实物管脚为圆形:孔径尺寸(直径)=实际管脚直径+0.20∽0.30mm(8.0∽12.0MIL)左右;若实物管脚为方形或矩形:孔径尺寸(直径)=实际管脚对角线的尺寸+0.10∽0.20mm(4.0∽8.0MIL)左右。
2)焊盘尺寸:常规焊盘尺寸=孔径尺寸(直径)+0.50mm(20.0 MIL)左右。
4.2 焊盘相关规范4.2.1所有焊盘单边最小不小于0.25mm,整个焊盘直径最大不大于元件孔径的3倍。
- 1、下载文档前请自行甄别文档内容的完整性,平台不提供额外的编辑、内容补充、找答案等附加服务。
- 2、"仅部分预览"的文档,不可在线预览部分如存在完整性等问题,可反馈申请退款(可完整预览的文档不适用该条件!)。
- 3、如文档侵犯您的权益,请联系客服反馈,我们会尽快为您处理(人工客服工作时间:9:00-18:30)。
PCB设计工艺规范1概述与范围本规范规定了印制板设计应遵循的基本工艺规范,适合于公司的印制电路板设计。
2 .性能等级(Class)在有关的IPC标准中建立了三个通用的产品等级(class),以反映PCB在复杂程度、功能性能和测试/检验方面的要求。
设计要求决定等级。
在设计时应根据产品等级要求进行设计和选择材料。
第一等级通用电子产品包括消费产品、某些计算机和计算机外围设备、以及适合于那些可靠性要求不高,外观不重要的电子产品。
第二等级专用服务电子产品包括那些要求高性能和长寿命的通信设备、复杂的商业机器、仪器和军用设备,并且对这些设备希望不间断服务,但允许偶尔的故障。
第三等级高可靠性电子产品包括那些关键的商业与军事产品设备。
设备要求高可靠性,因故障停机是不允许的。
2.1组装形式PCB的工艺设计首先应该确定的就是组装形式,即SMD与THC在PCB正反两面上的布局,不同的组装形式对应不同的工艺流程。
设计者设计印制板应考虑是否能最大限度的减少流程问题,这样不但可以降低生产成本,而且能提高产品质量。
因此,必须慎重考虑。
针对公司实际情况,应该优选表1所列形式之一。
表1 PCB组装形式3. PCB材料3. 1 PCB基材:PCB基材的选用主要根据其性能要求选用,推荐选用FR— 4环氧树脂玻璃纤维基板。
选择时应考虑材料的玻璃转化温度、热膨胀系数(CTE、热传导性、介电常数、表面电阻率、吸湿性等因素。
3. 2印制板厚度范围为0.5m叶6.4mm常用0.5mm,0.8mm,1mm,1.6mm,2.4mm,3.2m ft种。
3. 3铜箔厚度:厚度种类有18u,35u,50u,70u。
通常用18u、35u。
3. 4 最大面积:X*Y=460mm350mm 最小面积:X*Y=50mm50mm3. 5在印刷板的上下两表面印刷上所需要的标志图案和文字代号等,例如元件标号和标称值、元件外廓形状和厂家标志、生产日期等等。
丝印字符要有 1.5~2.0mm的高度。
字符不得被元件挡住或侵入了焊盘区域。
丝印字符笔划的宽度一般设置为10Mil。
3. 6常用印制板设计数据:普通电路板:板厚为1.6mm对四层板,内层板厚用0.71mm,内层铜箔厚度为35u。
对六层板,内层厚度用0.36mm,内层铜箔厚度用35u。
外层铜箔厚度选用18u,特殊的板子可用35u,70u(如电源板)。
后板:板厚用3.2mm, 铜箔厚度用18u或35u.对于四层板,内层板厚用2.4mm,内层铜箔用35u。
3. 7 PCB允许变形弯曲量应小于0.5 %,即在长为100mr的PC范围内最大变形量不超过0.5mm3. 8设计中钻孔孔径种类不要用的太多。
应适当选用几种规格孔径4.布线密度设计4. 1在组装密度许可的情况下,尽量选用低密度布线设计,以提高可制造性。
推荐采用以下三种密度布线:4. 11一级密度布线,适用于组装密度低的印制板。
特征:组装通孔和测试焊盘设立在2.54mm的网络上,最小布线宽度和线间隔为0.25mm ,通孔之间可有两条布线。
4Q.1OT 啊4. 12二级密度布线,适用于表面贴装器件多的印制板。
特征:组装通孔和测试焊盘设立在1.27mm的网络上。
最小布线宽度和线间隔为0.2mm 在表面贴装器件引线焊盘1.27mm的中心距之间可有一条0.2mm的布线4. 13三级密度布线,适用于表面贴装器件多, 组装通孔和测试焊盘设立在1.27mm 勺网络上。
在表面贴装器件引线焊盘1.27mm 的中心距之间可有一条0.2mm 的布线。
2.54mm 中心距插装通孔之间可有三条0.15mm 勺布线。
最小布线宽度、焊盘与焊盘,焊盘与线,线与线的最小间隔大于等于 0.15mm 导通过孔最小孔径为0.2mm 可不放在网格上。
测试通孔直径最小为0.3mm ,焊 盘直径0.8mm 必须放在网格上。
4. 2线路,焊盘在布线区内,布线区不允许紧靠板边缘,须留出至少1mr 的距离。
3在印制板设计时,应注意板厚、孔径比应小于 6。
5. 焊盘与线路设计5. 1焊盘:5. 11焊盘选择和修正:EDA 软件在封装库中给出了一系列不同大小和形状的焊盘。
选择元件的焊盘类型要综合考虑该元件的形状、大小、布置形式、振动和受 热情况、受力方向等因素。
一般情况下,可选择库中的优选焊盘。
对有特殊要求 的情况,应做适当修正。
5. 12对使用波峰焊接和再流焊接的表面贴装元器件的焊盘应采用不同的焊盘标 准。
5. 13对发热且受力较大、电流较大的焊盘,可设计成“泪滴状”。
5. 14对插件元器件,各元件通孔的大小要按元件引脚粗细分别编辑确定,原则是孔的尺寸比引脚直径大0. 2- 0 . 4毫米。
5. 15在大面积的接地(电)中,如果元器件的腿与其连接,做成十字花焊盘, 俗称热焊盘(Thermal ),这样,可使在焊接时因截面过分散热而产生虚焊点的 可能性大大减少。
多层板的过孔在内层接电(地)处的处理相同。
5. 2印制导线与焊盘5. 21减小印制导线连通焊盘处的宽度,除非受电荷容量、印制板加工极限等因 素的限制,最大宽度应为0.4mm或焊盘宽度的一半(以较小焊盘为准)。
高密度的印制板。
特征:4.5. 22应避免呈一定角度与焊盘相连。
只要可能,印制导线应从焊盘的长边的中h □. & mm15 — 口; ----- 1 ---- T |0!0| || —4 ■n L □; 口! 口 [口! 1 冋 1□j 口丨口 1 口 ------- L1 己 5. 3焊盘与阻焊膜 5. 31印制板上相应于各焊盘的阻焊膜的开口尺寸,其宽度和长度分别应比焊 盘尺寸大0.10~0.25mm 防止阻焊剂污染焊盘,如果阻焊膜的分辨率达不到应用 于细间距焊盘的要求时,贝呼田间距焊盘图形范围内不应有阻焊膜。
5. 32建议阻焊窗口与实际焊盘要有 3miI 间隔心处与之相连。
5. 23焊盘与较大面积的导电区,如地、 细的导电线路进行热隔离。
电源等平面相连时,应通过一长度较短 热隔离带错误 正确5. 24当布线层有大面积铜箔时,应设计成网格状5. 33阻焊膜的厚度不得大于焊盘的厚度。
5. 34如果两个焊盘之间间距很小,因为绝缘需要中间必须有阻焊绿油。
绿油桥应大于7MiI间距。
5. 4导通孔布局5. 41避免在表面安装焊盘上设置导通孔,距焊盘边缘0.5mm以内也要尽量避免设置导通孔,如无法避免,则必须用阻焊剂将焊料流失通道阻断,或将孔堵塞、掩盖起来。
6. 布局6. 1印制板元件面应该有印制板的编号和版本号。
6. 2元件布置的有效范围:PCB板X,丫方向均要留出传送边,每边》4mm此区域里不得有孔、焊盘和走线。
遇有高密度板无法留出传送边的,可设计工艺边,以V形槽或长槽孔与原板相连,焊接后去除。
6. 3光学基准点的使用6. 3. 1光学基准点标记为装配工艺中的基准点。
允许装配使用的每个设备精确地定位电路图案。
有两种类型的基准点标记,它们是:全局基准点(Global Fiducials),局部基准点(Local Fiducials)6. 3. 2全局基准点(Global Fiducials)标记用于在单块板上定位所有电路特征的位置。
当一个图形电路以拼板(panel)的形式处理时,全局基准点叫做拼板基准点。
(见图6.1图6.2 )6. 3. 3局部基准点(Local Fiducials) 用于定位单个元件的基准点标记。
(见图 6.1 )图4—1局部/全局基准点图6 —2拼板/全局基准点6. 4. 4要求每一块印制板至少设两个全局基准点,一般要求设三个点。
这些点在电路板或拼板上应该位于对角线的相对位置,并尽可能地距离分开。
6.4.5对于引脚间距小于0.65mm(25mil)的器件,要求对角设两个局部基准点' 如果空间有限,可设一个位于器件外形图案中点的基准点作为中心参考点。
6. 4. 6常用的基准点符号形状有四种:■• ▲ +,推荐使用•(实心圆)6. 4. 7圆形基准点直径是推荐使用1.25mm(50mil )。
在同一块板上应保持所有的基准点为同一尺寸。
6. 4. 8基准点可以是由防氧化涂层保护的裸铜或镀焊锡涂层(热风整平) 。
在PCB Layout时应标出。
同时应考虑材料颜色与环境的反差,通常留出比标识符大1.5mm的无阻焊区(clearanee )。
(见图4 —3)图6 —3基准点空旷度要求6. 4. 9边缘距离:基准点要距离印制板边缘至少 5.0mm[0.200"],并满足最小的基准点空旷度要求。
6. 5印制板设计前应根据组装密度、元器件情况考虑采用何种工艺流程进行焊接(如双面再流捍、双面混装焊等)。
根据工艺流程来决定主要元器件的位置6. 6板上元件需均匀排放,避免轻重不均。
布局时应考虑热平衡,避免热容量大的元器件集中在某个区域。
片状元件衽印制板豁口附近的配置方向6. 7元器件在PCB上的排向,原则上应随元器件的类型改变而变化,即同类元器件尽可能按相同的方向排列,以便元器件的贴装、焊接和检测。
所有的有极性的表面贴装元件在可能的时候都要以相同的方向放置。
(见图4 —4)图6-4表面贴装元器件的排列6. 8元件间隔在PCB布局时要考虑到器件间距不得太小,以考虑维修时元器件方便拆卸。
6. 9在高密度组装板中,为了焊后检验(人工或自动),元器件应留出视觉空间特别是在QFP PLCC器件周围不要有较高的器件。
(如图4—5)OIF WE图6 —5视线考虑6.10采用波峰焊接时的元器件布局6. 10. 1适合于插装元器件、片式阻容元件、SOT引线中心距大于或等于1 mm 的SOP的焊接,不能用于QFP PLCC BGA引线中心距小于1mn!勺SOP的焊接。
6. 10. 1当采用波峰焊时,尽量保证元器件的两端焊点同时接触焊料波峰。
片状元件,尽量保证元件的长轴要垂直于板沿着波峰焊接机传送的方向且相互平行。
SOIC必须保证长轴平行于传送方向;QFR PLCC应斜45°布放。
6. 10. 2当尺寸相差较大的片状元器件相邻排列,且间距很小时,较小的元器件在波峰时应排列在前面,先进入焊料波,否则尺寸较大的元器件遮蔽其后尺寸较小的元器件,造成漏焊。
这种遮蔽效应对于大小相等,交错排列的元器件也是适用的。
图6-6波峰焊接应用中的元件方向7 .拼板设计7. 1对于面积较小的PC板,为了充分利用基板,提高生产效率方便加工,可以将多块同种小型印制板拼成一张较大的板面。
同种产品的几种小块印制板也可拼在一起。
这时要注意各小印制板的参数和层数应相同。
7. 2拼板的尺寸范围控制在350mmX300以内,外形应为长方形。
7. 3对于异形板(外形非矩形)为了便于加工和节省成本,应合理地拼合图形, 尽量减少板面积。
7. 3拼板的连接和分离方式,主要采用邮票孔或者双面对刻的V型槽。