散热风扇叶模具设计实例讲解
solidworks案例教程《风扇叶片建模》
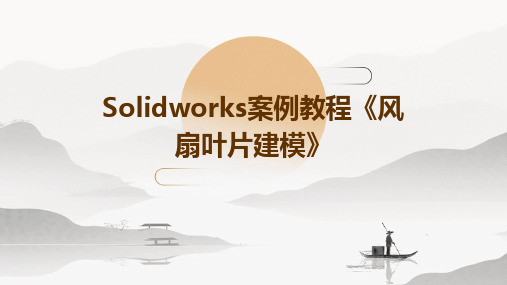
目录
• 引言 • Solidworks基础操作 • 风扇叶片设计理念 • 风扇叶片建模过程 • 风扇叶片后处理与优化 • 课程总结与展望
01
引言
课程背景
风扇叶片作为机械设备中的重要组成部分,其设计质量和加工精度直接影响设备 的性能和安全性。
随着计算机技术的发展,CAD(计算机辅助设计)软件在机械设计领域得到了广泛 应用,其中SolidWorks是一款功能强大、易学易用的CAD软件,广泛应用于各种机 械设计领域。
06
课程总结与展望
本课程学习重点回顾
风扇叶片设计原理
Solidworks基本操作
理解风扇叶片的工作原理和设计要求,以 便更好地进行建模。
掌握Solidworks的基本操作,如草图绘制 、特征创建、装配体设计等。
参数化设计
优化设计
学习如何使用Solidworks的参数化设计功 能,提高设计效率和准确性。
倒角
在实体的边角上添 加倒角,使实体更 加坚固。
实例操作:简单零件建模
打开Solidworks软件, 新建一个零件文件。
执行拉伸命令,将矩 形拉伸成一个长方体。
在草图绘制模式下, 绘制一个矩形,作为 拉伸特征的基础。
实例操作:简单零件建模
在长方体的顶部绘制一个圆形 草图,作为旋转特征的基础。
执行旋转命令,将圆形草图旋 转成一个圆柱体。
提供常用命令的快速访 问按钮,方便用户操作。
显示当前零件的结构和 特征,方便用户进行编
辑和修改。
绘图区域
用于显示和编辑零件的 三维模型。
基础命令介绍
拉伸
将草图沿着一个方 向拉伸,形成三维 实体。
电风扇叶片塑料模具设计说明

第1章注射模可行性分析1.1注射模设计的特点塑料注射模塑能一次性地成型形状复杂、尺寸精确或嵌件的塑料制品。
在注射模设计时。
必须充分注意以下三个特点:(1)塑料熔体大多属于假塑料液体,能剪切变稀。
它的流动性依赖于物料品种、剪切速率、温度和压力。
因此须按其流变特性来设计浇注系统,并校验型腔压力及锁模力。
(2)视注射模为承受很高型腔压力的耐压容器。
应在正确估算模具型腔压力的基础上,进行模具的结构设计。
为保证模具的闭合、成型、开模、脱模和侧抽芯的可靠进行,模具零件和塑件的刚度与强度等力学问题必须充分考虑。
1.2注射模组成凡是注射模,均可分为动模和定模两大部件。
注射充模时动模和定模闭合,构成型腔和浇注系统;开模时定模和动模分离,取出制件。
定模安装在注射机的固定板上,动模则安装在注射机的移动模板上。
根据模具上各个零件的不同功能,可由一下个系统或机构组成。
(1)成型零件指构成型腔,直接与熔体相接触并成型塑料制件的零件。
通常有凸模、型芯、成型杆、凹模、成型环、镶件等零件。
在动模和动模闭合后,成型零件确定了塑件的内部和外部轮廓尺寸。
(2)浇注系统将塑料熔体由注射机喷嘴引向型腔的流道称为浇注系统,由主流道、分流道、浇口和冷料井组成。
(3)导向与定位机构为确保动模与定模闭合时,能准确导向和定位对中,通常分别在动模和定模上设置导柱和导套。
深腔注射模还须在主分型面上设置锥面定位,有时为保证脱模机构的准确运动和复位,也设置导向零件。
(4)脱模机构是指模具开模过程的后期,将塑件从模具中脱出的机构。
(5)侧向分型抽芯机构带有侧凹或侧孔的塑件,在被脱出模具之间,必须先进行侧向分型或拔出侧向凸模或抽出侧型芯。
1.3塑料风叶设计与分析风叶是利用一定空间曲面的叶片,通过主体的高速旋转产生风能。
以前,大都是采用金属片材,经过模压制成风叶片。
然后与风叶主体固定安装成风叶。
由于模压叶片和装配等方面的原因,往往风叶的静、动平衡难以达到设计要求。
电风扇叶注塑模设计

4 电风扇叶注塑模设计4.1 注塑模设计的基本流程传统方法的注塑模设计是在二维环境下进行,从图4.1中可以看出,传统的模具制造工艺路线只是典型的串行流程,任何其中一部分没有完成都会影响下面的工作,相互之间的制约性太大,这样的结果就是生产周期的延长,人工进行的工作量非常大,而且做工粗糙、精度不高,在CAD/CAM技术高速发展的今天,传统方法终将被取而代之。
基于UG 的注塑模具的设计是在三维环境下进行的,这用方法的采用不仅提高了生成型芯和型腔零件的速度和准确度还可以进行造型设计,还能完成模具的总装配,大大缩短了模具设计周期并及时发现模具设计中的错误,有效地避免工人重复劳动[16]。
图4.1传统方式的注塑模具设计过程图4.2 基于UG的注塑模设计工程4.2 注塑模具的基本结构设计4.2.1 扇叶材料的分析风扇为人们日常生活常用品,需大批量生产,又与人们紧密接触,所以扇叶的材料必须无毒无害,同时考虑没有很高的强度要求,收缩率方面也无特殊要求,故选择ABS材料进行注塑生产。
ABS具有良好的成型加工型,制品表面光洁度高,且具有良好的涂装性和染色性,可电镀成多种光泽[17]。
塑料ABS具有以下性能:(1)冲击强度极好,耐磨性优良,尺寸的稳定性好。
(2)从热学性能上来看热变形温度为85℃左右,制品经退火处理以后还可提高10℃左右。
在-40℃时仍能表现出一定的韧性,可在-40℃到85℃的温度范围内长期使用。
(3)ABS的电绝缘性较好,并且几乎不受温度、湿度和频率的影响。
(4)ABS流动性好,易溢料,具有优良的化学稳定性、不吸水,是易成型加工的材料可用于注塑。
4.2.2 分型面的选择分型面是指上、下两模芯互相接触的表面,而分型面的设计在电风扇叶的注塑模设计中是非常重要的。
分型面一般是在确定浇注位置或被称为进料口的位置后再选择。
但在分析各种分型面方案的优缺点之后,也有可能需要重新调整浇注位置。
分型面选择原则有两个,首先要考虑到是塑件在开模时尽可能留在动模部分,同时由于塑件有曲面扇叶,所以也要尽可能留在动模部分。
风扇叶片模具设计论文
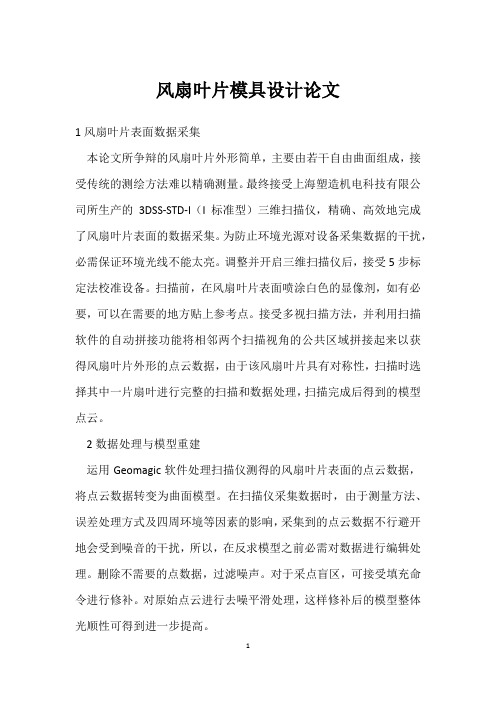
风扇叶片模具设计论文1风扇叶片表面数据采集本论文所争辩的风扇叶片外形简单,主要由若干自由曲面组成,接受传统的测绘方法难以精确测量。
最终接受上海塑造机电科技有限公司所生产的3DSS-STD-I(I标准型)三维扫描仪,精确、高效地完成了风扇叶片表面的数据采集。
为防止环境光源对设备采集数据的干扰,必需保证环境光线不能太亮。
调整并开启三维扫描仪后,接受5步标定法校准设备。
扫描前,在风扇叶片表面喷涂白色的显像剂,如有必要,可以在需要的地方贴上参考点。
接受多视扫描方法,并利用扫描软件的自动拼接功能将相邻两个扫描视角的公共区域拼接起来以获得风扇叶片外形的点云数据,由于该风扇叶片具有对称性,扫描时选择其中一片扇叶进行完整的扫描和数据处理,扫描完成后得到的模型点云。
2数据处理与模型重建运用Geomagic软件处理扫描仪测得的风扇叶片表面的点云数据,将点云数据转变为曲面模型。
在扫描仪采集数据时,由于测量方法、误差处理方式及四周环境等因素的影响,采集到的点云数据不行避开地会受到噪音的干扰,所以,在反求模型之前必需对数据进行编辑处理。
删除不需要的点数据,过滤噪声。
对于采点盲区,可接受填充命令进行修补。
对原始点云进行去噪平滑处理,这样修补后的模型整体光顺性可得到进一步提高。
3风扇叶片注塑模具设计在逆向工程的基础上,在UG注塑模具设计(MoldWizard)模块中,对该风扇叶片进行了注塑模设计。
模具设计的基本流程如下:导入制件三维实体模型;对设计项目进行初始化,加载实体模型,确定材料及收缩率;分析实体模型出模斜度及分型状况;确定模具的分型面、型腔布局、推杆、浇口和冷却系统等;修补开方面,定义分型面;生成型芯、型腔等工作部件;加入标准模架、推杆、滑块等部件;设计浇注系统、冷却系统;完善设计图纸等。
依据该塑件外观质量及尺寸精度要求,选用模具为一模一腔单分型面模具。
结合分型面的选择原则,选取单分型面垂直分型。
避开了顶杆端部与叶片的接触,保证产品外观的完整性。
模具毕业设计55风扇叶片注射模具设计

模具毕业设计55风扇叶片注射模具设计一、设计背景和目的风扇作为现代生活中必不可少的电器之一,其叶片的设计和制造对于风扇的性能和使用效果具有重要影响。
因此,设计一款优质、高效的55风扇叶片注射模具对于提高风扇叶片的生产效率和质量具有重要意义。
本设计旨在设计一款能够满足产品需求的注射模具,通过优化模具设计和材料选择,提高模具的使用寿命和生产效率,并保证产品的质量。
二、设计步骤和流程1.研究分析:首先对现有55风扇叶片的设计进行详细研究,并分析其结构和生产工艺。
2.模具结构设计:根据风扇叶片的形状和尺寸,设计模具的整体结构,包括模具的上模、下模和侧模的形状和尺寸等。
3.模具材料选择:根据模具的使用寿命要求和生产效率要求,选择合适的模具材料,如优质钢材或耐磨合金材料等。
4.模具加工工艺:确定模具的加工工艺和加工设备,包括模具的精度要求、加工配件的尺寸要求等。
5.模具生产和试模:根据设计要求制造模具,并进行试模,测试模具的性能和生产效果。
6.模具调试和优化:根据试模结果进行模具的调试和优化,改进模具的结构和工艺参数,提高模具的生产效率和质量。
7.模具维护和保养:制定模具的维护保养计划,定期对模具进行保养和维修,延长其使用寿命。
三、设计要求和技术方案1.叶片形状设计:根据55风扇叶片的要求,设计叶片的外形和内部结构,保证叶片的强度和风力输出效果。
2.注射模具结构设计:根据叶片形状设计模具的上模、下模和侧模等,确保注射过程中的材料流动和成型效果。
3.模具材料选择:选择优质的钢材或耐磨合金材料,提高模具的硬度和使用寿命。
4.模具加工工艺:根据设计要求确定模具的加工工艺和加工设备,保证模具的精度和质量。
5.模具试模和调试:进行模具试模和调试,测试模具的生产效率和成型质量,进行必要的参数调整和优化。
6.模具维护和保养:制定模具的维护保养计划,包括定期润滑、清洁和维修等,延长模具的使用寿命。
四、设计成果和预期效果根据以上设计流程和技术方案,预计可以设计出一款满足生产需求的55风扇叶片注射模具,具备以下特点和效果:1.提高生产效率:优化模具设计和加工工艺,提高模具的开模速度和成型效率,提高生产效率。
风扇叶片建模实例PPT
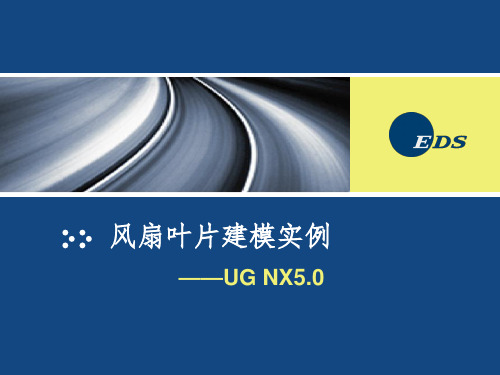
8
风扇叶片建模步骤
12、对圆柱顶端倒圆角,半径12. 13、在圆柱底面创建“孔”,直径20,深度28.
9
风扇叶片建模实例
——UG 0
风扇叶片模型
2
风扇叶片建模步骤
1、拉伸一圆柱体,直径30,高40. 2、用“偏置曲面”命令,偏置圆柱面,距离80.
3
风扇叶片建模步骤
3、在YZ面上绘制下列草图.
4
风扇叶片建模步骤
3、用“投影”命令,将2条曲线分别投影到小圆柱和大圆柱上,投 影方向为X轴。 4、隐藏大圆柱。
5
风扇叶片建模步骤
5、用“编辑/曲线长度”命令,调整2条投影曲线的长度,短曲线2端都 缩短-6,长曲线2端都缩短-40. 6、用“通过曲线组”命令,创建曲面.
6
风扇叶片建模步骤
7、用“加厚”,将曲面向2侧加厚,厚度为1. 8、用“边倒圆”,对叶片尖角倒圆角,左边R=40,右边R=22.
7
风扇叶片建模步骤
电风扇叶片塑料模具设计说明

第1章注射模可行性分析1.1注射模设计的特点塑料注射模塑能一次性地成型形状复杂、尺寸精确或嵌件的塑料制品。
在注射模设计时。
必须充分注意以下三个特点:(1)塑料熔体大多属于假塑料液体,能剪切变稀。
它的流动性依赖于物料品种、剪切速率、温度和压力。
因此须按其流变特性来设计浇注系统,并校验型腔压力及锁模力。
(2)视注射模为承受很高型腔压力的耐压容器。
应在正确估算模具型腔压力的基础上,进行模具的结构设计。
为保证模具的闭合、成型、开模、脱模和侧抽芯的可靠进行,模具零件和塑件的刚度与强度等力学问题必须充分考虑。
1.2注射模组成凡是注射模,均可分为动模和定模两大部件。
注射充模时动模和定模闭合,构成型腔和浇注系统;开模时定模和动模分离,取出制件。
定模安装在注射机的固定板上,动模则安装在注射机的移动模板上。
根据模具上各个零件的不同功能,可由一下个系统或机构组成。
(1)成型零件指构成型腔,直接与熔体相接触并成型塑料制件的零件。
通常有凸模、型芯、成型杆、凹模、成型环、镶件等零件。
在动模和动模闭合后,成型零件确定了塑件的内部和外部轮廓尺寸。
(2)浇注系统将塑料熔体由注射机喷嘴引向型腔的流道称为浇注系统,由主流道、分流道、浇口和冷料井组成。
(3)导向与定位机构为确保动模与定模闭合时,能准确导向和定位对中,通常分别在动模和定模上设置导柱和导套。
深腔注射模还须在主分型面上设置锥面定位,有时为保证脱模机构的准确运动和复位,也设置导向零件。
(4)脱模机构是指模具开模过程的后期,将塑件从模具中脱出的机构。
(5)侧向分型抽芯机构带有侧凹或侧孔的塑件,在被脱出模具之间,必须先进行侧向分型或拔出侧向凸模或抽出侧型芯。
1.3塑料风叶设计与分析风叶是利用一定空间曲面的叶片,通过主体的高速旋转产生风能。
以前,大都是采用金属片材,经过模压制成风叶片。
然后与风叶主体固定安装成风叶。
由于模压叶片和装配等方面的原因,往往风叶的静、动平衡难以达到设计要求。
olidworks案例教程《风扇叶片建模
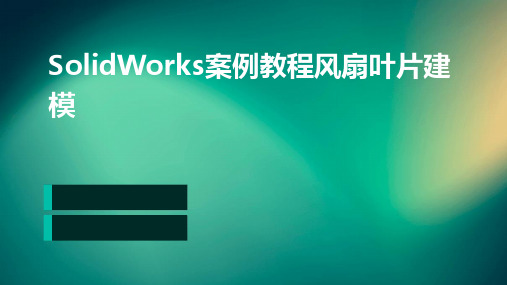
建模前的准备工作
01
了解风扇叶片的设计要 求和参数,如叶片数量、 长度、宽度、厚度等。
02
准备相关参考图纸和数 据,如风扇叶片的实物 或图片、相关尺寸参数 等。
03
安装并打开SolidWorks 软件,创建一个新的零 件文件。
04
设置工作单位和材料属 性,如选择适当的单位 (如毫米)和材料(如 铝合金)。
渲染与可视化
讲解了如何使用SolidWorks的渲染工具来提高模 型的可视化效果,以便更好地展示设计意图。
实际应用与项目拓展
实际应用案例
分享了SolidWorks在风扇叶片设计领 域的实际应用案例,包括复杂的Βιβλιοθήκη 扇 叶片设计和优化。项目拓展
提供了项目拓展的建议,如如何将 SolidWorks与其他CAD软件进行集成, 以及如何利用SolidWorks进行风扇性 能模拟和分析。
高级特征应用
如扫描、放样、阵列等,如何利用这些功能创建复杂的叶片形状。
参数与配置管理
如何利用参数和配置管理器来控制风扇叶片的尺寸和形状。
SolidWorks的高级功能与技巧
高级草图功能
介绍了如何使用高级草图工具,如几何关系、尺 寸和约束等,来提高建模效率。
装配体设计
探讨了如何在装配体中管理和组织零部件,以及 如何进行高效的装配设计。
工具栏
提供常用命令的快速访问按钮 。
特征树
显示当前文档的三维模型历史 记录,包括草图、特征等。
绘图区域
用于显示和编辑模型的地方。
草图绘制
01
02
03
创建草图
在绘图区域创建二维图形。
编辑草图
对已创建的草图进行修改 和调整。
- 1、下载文档前请自行甄别文档内容的完整性,平台不提供额外的编辑、内容补充、找答案等附加服务。
- 2、"仅部分预览"的文档,不可在线预览部分如存在完整性等问题,可反馈申请退款(可完整预览的文档不适用该条件!)。
- 3、如文档侵犯您的权益,请联系客服反馈,我们会尽快为您处理(人工客服工作时间:9:00-18:30)。
2 初始化项目
• 初始化项目过程是MoldWizard克隆模具装配体结 构的复制过程。在NX6.0中,产品的初始化项目过 程包括加载产品和初始化项目。
2.1 加载产品
• 在产品模型进行初始化项目时,NX6.0与旧版本有所区别的是,必须在打 开的模型文件中显示实体模型。因此,产品的加载是初始化项目过程中不 可缺少的重要步骤。其操作步骤如下:
散热风扇叶注塑模设计实例讲解
深圳美风机电技术有限公司 王宝林
• 本文将以塑胶制品—风扇叶为例,将塑料注塑模具的 整个设计流程作详细的介绍,其中包括有产品设计任 务、项目初始化、分模设计、模架加载、浇注系统设 计、顶出系统设计和冷却系统设计。
• 通过本文的风扇叶注塑模设计实例,能使读者对前面 所学内容有更充分的理解和掌握。下面将风扇叶注塑 模设计的整个设计流程介绍如下。
4.1 加载模架
• 通常,模架的选用是根据具有国家标准的龙记模 架系列来确定的。鉴于本文产品模型较大,所以 选用的是龙记大水口模架。操作步骤如下:
4.2 调整模腔
• 由于“模架管理”对话框无模架的平移变换功能, 所以只能调整模腔。调整模腔过程包括模具坐标 系的重定义和工件的参数编辑。操作步骤如下:
• 由于本文风扇叶模具为单模腔设计,也就不再进行模腔布局设计了。 • 1. 设置模具坐标系 • 2. 创建自动工件
3.2 MPV模型验证
• MPV模型验证是MW自动分模设计必须经过的一个过 程。否则,后续的分模设计将无法进行,操作步 骤如下:
3.3 主分型面设计
• 风扇叶的主分型面最好作成碰穿形式,可进行模具精确定位,并有助于减 少开模动作部件之间的摩擦。
• 1. 加载定位环 • 2. 加载浇口衬套
5.2 创建浇口
• 单腔模的浇口多数情况下采用单点浇口或潜浇口, 本例模具采用单点浇口形式。其操作步骤如下:
5.3 创建流道与浇口空腔
• 使用“注塑模向导”工具条上的“腔体”工具在 模具定模部分中创建出浇注系统组件的空腔。
6 创建顶出系统
• 本例产品无内、外侧凹或侧孔特征,所以顶出系 统的创建仅仅是加载并修剪顶杆。
• (1)启动UG NX6.0,进入基本环境界面中。 • (2)在“标准”工具条上执行“开始>所有应用模块>建模”命令,载
入建模模块,接着调入“特征”工具条、“曲面”工具条、“曲线”工具 条等。 • (3)在“标准”工具条上执行“开始>所有应用模块>注塑模向导”命 令,载入MoldWizard模块。 • (4)单击“标准”工具条上的“打开”按钮,弹出“打开”对话框。进 入随书光盘中打开Example\ch11\fox.prt产品模型文件,如图11-2所示。
• 1. 抽取型芯、型腔区域面 • 2. 自动修补破孔
3.5 创建型腔和型芯
• 虽然前面创建了主分型面,但它并不是MW默认的分型面,因此还 要进行MW分型面的创建,然后才能自动分割出型腔和型芯。
• 1. 创建MW默认的分型面 由于产品并无复杂的侧凹、侧孔、倒扣等复杂特 征,因此,模架结构可采用简单的二板模,即不 要支承板、卸料板。
2.2 初始化项目
• 产品模型加载后,即可执行初始化项目进程操作,在此进程中可进行项目 路径的更改、项目的重命名、产品材料的选择以及项目单位的设置等操作。 操作步骤如下:
• (1)在“注塑模向导”工具条上单击“初始化项目”按钮,弹出“初始 化项目”对话框。
• (2)在对话框的“材料”下拉列表中选择“ABS+PC”,保留对话框中其 他默认设置,单击“确定”按钮进入初始化项目进程,如图11-3所示。
• (3)经过一段时间的初始化项目过程后,完成了模具总装配体的克隆装 配,在装配导航器中可看见模具总装配体结构,如图11-4所示。
3 分模设计
• 产品的分模设计过程包括模具设计准备过程、MPV 模型验证、主分型面设计、抽取区域和自动补孔、 创建型芯与型腔5个设计过程。
3.1 模具设计准备过程
• 模具设计准备过程是完成模具设计的前期阶段,同时也是极为重要的设计阶段。 模具设计准备过程包括模具坐标系的设置、创建自动工件和模腔布局。
• 1. 创建条带曲面 • 2. 创建拉伸曲面 • 3. 拉伸曲面拔模处理 • 4. 创建延伸曲面 • 5. 创建另外两片风扇叶的碰穿面 • 6. 完成主分型面的创建 • 7. 完成MPV模型验证
3.4 抽取区域面及自动补孔
• 产品的MPV模型验证完成后,接着就可以抽取型芯、型腔区 域面和自动修补模型的破孔了。
1 设计任务
• 本文注塑模具设计实例产品为风扇叶,如图11-1所示。 • 产品规格:350mm×335mm×51mm。 • 产品壁厚:最大3mm,最小2mm。 • 产品设计、生产任务: • 材料为ABS+PC; • 产品收缩率为0.0045; • 单腔模布局; • 产量15000个/年; • 产品外部表面光滑,无明显制件缺陷,如翘曲、缩痕、凹坑等;
7 创建冷却系统
• 本例注塑模具的冷却系统分别创建在模具的定模 部分和动模部分。
7.1 创建定模部分冷却管道
• 定模部分冷却管道主要由型腔冷却管道和定模板 冷却管道构成。
• 1. 型腔冷却管道设计 • 2. 定模板冷却管道设计
6.1 加载顶杆
• 为使制件能平稳地推出,顶杆的分布应尽量均匀。 加载顶杆的操作步骤如下:
6.2 修剪顶杆
• 顶杆标准件加载以后,需要将其修剪成型芯部件 上的一部分形状,使产品内部保持原有形状。操 作步骤如下:
6.3 创建顶杆的空腔
• 使用“注塑模向导”工具条上的“腔体”工具, 选择型芯、动模板和推件固定板作为目标体,选 择所有的顶杆作为工具体,创建出顶杆的空腔。
4.3 创建空腔
• 模架加载后,为了便于后续的设计,需先创建出 模腔在动、定模板上的空腔。操作步骤如下:
5 创建浇注系统
• 风扇叶模具的浇注系统组件包括主流道、分流道 和浇口。但由于模具采用的是单点浇口进料,因 此不设分流道。
5.1 创建主流道
• 模具的主流道主要为标准件浇口衬套,同时加载 用于定位注射机机嘴的定位环标准件。