氧化铝焙烧工艺设备流程图
拜耳法氧化铝生产工艺流程框图

拜耳法氧化铝生产工艺流程框图成品氧化铝图一焙烧2O 3图二 碱法生产氧化铝基本过程开曼铝业氧化铝厂工艺流程简图氧化铝厂主要生产车间一车间:原料准备包括:地磅房、破碎站、原矿堆场、均化库、石灰仓、石灰消化及原料磨等工段a.石灰消化:3台ф1200x10500m化灰机,2用1备b.石灰仓:3台ф14x18mc.拜尔原料磨(棒球两段磨加水力漩流器):4组,每组配一级棒磨ф3.2x4.5m及二级球磨ф3.6x8.5m,产能100t/h,用3备1。
二车间:高压溶出包括:常压脱硅、高压泵房、管道化预热、溶出及稀释a.常压脱硅:3台带加热管束搅拌的ф10x16m预脱硅加热槽及11台机械搅拌的ф10x16m脱硅槽,1台ф6x6m赤泥洗液槽。
其中预脱硅加热槽2用1备,脱硅槽10用1备。
b.高压泵房:3台高压引进的高压隔膜泵,泵压力6~6.8MPa,流量400-500m31备。
c.溶出装置:26级套管预热,4级压煮器预热,新蒸汽间接加热,保温压煮器停留30分钟,10级闪蒸降温。
每组配套预热管预热器长度2880m,19台ф2.8x16.8m压煮器,12台ф3.0-5.0x9.7m闪蒸器。
2台ф12.5x13.5m溶出后槽,稀释料浆停留4.2小时,产能400-500kt/a.三车间:赤泥沉降包括:赤泥分离及洗涤、絮凝剂制备、控制过滤、赤泥贮槽及赤泥泵站、赤泥堆场、热水站a.赤泥分离及洗涤:2组。
采用高效深锥沉降槽技术及设备。
每组配6台ф14x16-18m高效沉降槽,其中分离槽1台,洗涤槽4台,备用槽1台。
b.控制过滤:7台226m2立式叶滤机,其中用6台备1台。
c.赤泥泵站:3台引进的高压隔膜泵,2用1备。
d.絮凝剂制备、热水站。
四车间:分解分级包括:精液热交换、分解分级、中间降温、种子过滤a.精液热交换(板式换热器):4组。
每组为两级换热,第一级精液与母液换热,配3台450m3 换热器,第二级精液与水换热,配1台230 m3 换热器。
氧化铝生产流程图

一.工艺简介氧化铝的生产工艺,是用碱来处理铝矿石,使矿石中的氧化铝转变成铝酸钠溶液。
矿石中的铁、钛等杂质和绝大部分的硅则成为不溶解的化合物,将不溶解的残渣与溶液分离,经洗涤后弃去或综合利用,以回收其中的有用组分。
纯净的铝酸钠溶液分解析出氢氧化铝,经与母液分离、洗涤后进行焙烧,得到氧化铝产品。
分解母液可循环使用,处理另外一批矿石。
-整个生产工艺分为8个工段:原料磨、溶出、赤泥沉降、控制过滤、分解分级、蒸发、成品过滤、焙烧。
下面从这八个工段分别介绍。
-二.原料磨在原料磨工段,铝土矿、石灰及循环母液按比例加入棒磨和球磨机中磨制原矿浆,原矿浆由水力旋流器进行分级,分级机溢流为合格的原矿浆,送入原矿浆槽,再用矿浆泵送往溶出车间的常压脱硅工段。
--三.溶出从原料车间送来的原矿浆进入常压脱硅工段的加热槽中,采用蒸汽加热,将矿浆温度控制在100℃~110℃,然后送入脱硅槽中进行连续脱硅。
在脱硅槽的末槽用母液调整经脱硅后的原矿浆RP和温度。
合格原矿浆送至高压泵房的隔膜泵,脱硅机理底部设有返砂管、返砂泵,每班定期将粗砂返回原料磨工段。
-用隔膜泵将原矿浆送往溶出工段的套管预热器,由六级套管加热器将原矿浆温度预热至174~180℃,而后采用高压新蒸汽间接加热,原矿浆加热至260℃,保温停留60分钟。
溶出后料浆经十级闪蒸,温度从260℃降至125℃,然后送入稀释槽。
从赤泥洗涤送来的赤泥洗液同时加入稀释槽中,稀释料浆用泵送往溶出后槽,停留守4小时以上,以脱除溶液中的硅、铁、锌等杂质。
--四.赤泥沉降从溶出后槽送来的稀释料浆与从絮凝剂制备工段来的絮凝剂一同进入分离沉降槽中,分离沉降槽底流含固量约38%~42%,用泵送往洗涤沉降槽,采用四次反向洗涤,洗水从末槽加入,末次洗涤底流固体含量约46%~54%,拟用高压隔膜泵送往赤泥堆场堆存。
--五.控制过滤分离沉降槽溢流送控制过滤工段的粗液槽,控制过滤采用立式叶滤机,同时将少量石灰乳加进粗液槽中作为助滤剂,叶滤得到的精液送分解车间的精液板式热交换工段,叶滤渣进滤渣槽中,用泵送回一洗沉降槽。
氧化铝悬浮焙烧炉新工艺流程

氧化铝悬浮焙烧炉新工艺流程
氧化铝悬浮焙烧炉新工艺流程如下:
(一)原料准备:使用铝矾土作为原料,经过破碎、磨细等工序后,得到粉末状的氢氧化铝原料。
(二)气态悬浮:将氢氧化铝原料通过给料装置加入到气态悬浮焙烧炉中。
气态悬浮焙烧炉内设置有多层炉壁,通过控制炉壁温度,使得氢氧化铝原料在炉内悬浮。
同时,在炉内通入适量的气体,如氮气或空气,以保持炉内的气氛。
(三)焙烧反应:在气态悬浮焙烧炉中,氢氧化铝原料与气体中的氧气发生氧化反应,生成氧化铝。
这个过程需要在高温下进行,通常在1000-1200℃下进行。
(四)产物收集:氧化铝颗粒从炉中排出,通过输送装置输送到收集装置中。
收集到的氧化铝颗粒可以进行进一步的处理,如分级、洗涤、干燥等。
(五)尾气处理:焙烧过程中产生的尾气中含有未完全反应的气体和杂质,需要进行处理,以防止对环境造成污染。
尾气处理通常包括除尘、除杂、废气排放等步骤。
(六)工艺控制:整个工艺流程需要控制各个参数,如温度、气氛、原料质量等,以保证焙烧过程的顺利进行和获得高质量的氧化铝产品。
以上是氧化铝悬浮焙烧炉新工艺流程的基本步骤,具体操作还需要根据不同设备和工艺条件进行调整和优化。
氧化铝厂焙烧炉工艺流程

氧化铝厂焙烧炉工艺流程下载温馨提示:该文档是我店铺精心编制而成,希望大家下载以后,能够帮助大家解决实际的问题。
文档下载后可定制随意修改,请根据实际需要进行相应的调整和使用,谢谢!并且,本店铺为大家提供各种各样类型的实用资料,如教育随笔、日记赏析、句子摘抄、古诗大全、经典美文、话题作文、工作总结、词语解析、文案摘录、其他资料等等,如想了解不同资料格式和写法,敬请关注!Download tips: This document is carefully compiled by theeditor. I hope that after you download them,they can help yousolve practical problems. The document can be customized andmodified after downloading,please adjust and use it according toactual needs, thank you!In addition, our shop provides you with various types ofpractical materials,such as educational essays, diaryappreciation,sentence excerpts,ancient poems,classic articles,topic composition,work summary,word parsing,copy excerpts,other materials and so on,want to know different data formats andwriting methods,please pay attention!氧化铝厂焙烧炉工艺流程。
1. 原料装料。
将干燥后的铝土矿粉料、焦炭粉料、熟石灰粉料按配比加入炉内。
氧化铝厂 焙烧炉工艺流程

氧化铝厂焙烧炉工艺流程A calcination furnace, also known as a roasting furnace, is an essential part of the aluminum oxide production process. 钙钛矿石产生的氧化铝需要在高温下经过焙烧才能得到纯净的氧化铝产品。
Calcination is the process of heating the aluminum oxide at high temperatures to drive off water and carbon dioxide, leaving behind pure aluminum oxide. 焙烧炉的工艺流程需要精确控制温度和气氛以确保产品的质量。
The process involves careful control of temperature and atmosphere to ensure the quality of the product.The first step in the process is the preheating stage, where the raw aluminum oxide is loaded into the furnace and heated to a certain temperature. 炉子在这个阶段会使用燃料加热,以达到合适的温度。
During this stage, any impurities in the aluminum oxide will start to break down and evaporate, leaving behind a purer product. 在预热阶段,需要适当的控制加热速度和温度以及气氛,以确保原料完全适应高温环境。
The heating rate, temperature, and atmosphere need to be carefully controlled during the preheating stage to ensure that the raw material can withstand the high temperatures.Once the preheating stage is complete, the temperature is increased further to begin the calcination process. 这个阶段需要持续一段时间,使得原料中的水分和二氧化碳得以完全挥发。
氧化铝冶炼工艺流程简介
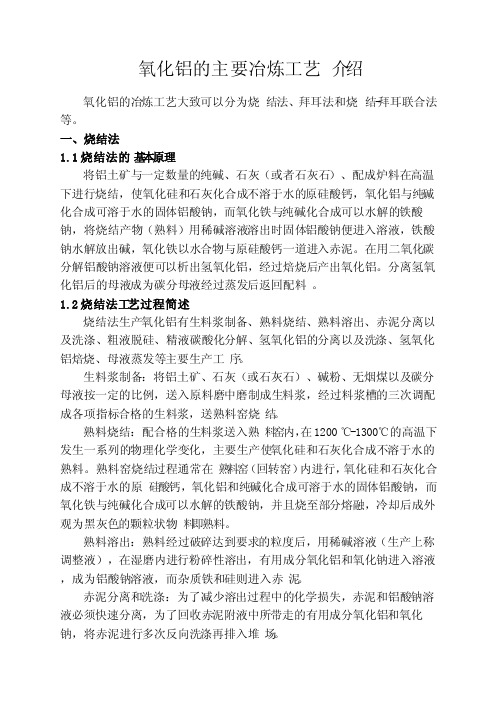
氧化铝的主要冶炼工艺介绍氧化铝的冶炼工艺大致可以分为烧结法、拜耳法和烧结-拜耳联合法等。
一、烧结法1.1烧结法的基本原理将铝土矿与一定数量的纯碱、石灰(或者石灰石)、配成炉料在高温下进行烧结,使氧化硅和石灰化合成不溶于水的原硅酸钙,氧化铝与纯碱化合成可溶于水的固体铝酸钠,而氧化铁与纯碱化合成可以水解的铁酸钠,将烧结产物(熟料)用稀碱溶液溶出时固体铝酸钠便进入溶液,铁酸钠水解放出碱,氧化铁以水合物与原硅酸钙一道进入赤泥。
在用二氧化碳分解铝酸钠溶液便可以析出氢氧化铝,经过焙烧后产出氧化铝。
分离氢氧化铝后的母液成为碳分母液经过蒸发后返回配料。
1.2烧结法工艺过程简述烧结法生产氧化铝有生料浆制备、熟料烧结、熟料溶出、赤泥分离以及洗涤、粗液脱硅、精液碳酸化分解、氢氧化铝的分离以及洗涤、氢氧化铝焙烧、母液蒸发等主要生产工序。
生料浆制备:将铝土矿、石灰(或石灰石)、碱粉、无烟煤以及碳分母液按一定的比例,送入原料磨中磨制成生料浆,经过料浆槽的三次调配成各项指标合格的生料浆,送熟料窑烧结。
熟料烧结:配合格的生料浆送入熟料窑内,在1200℃-1300℃的高温下发生一系列的物理化学变化,主要生产使氧化硅和石灰化合成不溶于水的熟料。
熟料窑烧结过程通常在熟料窑(回转窑)内进行,氧化硅和石灰化合成不溶于水的原硅酸钙,氧化铝和纯碱化合成可溶于水的固体铝酸钠,而氧化铁与纯碱化合成可以水解的铁酸钠,并且烧至部分熔融,冷却后成外观为黑灰色的颗粒状物料即熟料。
熟料溶出:熟料经过破碎达到要求的粒度后,用稀碱溶液(生产上称调整液),在湿磨内进行粉碎性溶出,有用成分氧化铝和氧化钠进入溶液,成为铝酸钠溶液,而杂质铁和硅则进入赤泥。
赤泥分离和洗涤:为了减少溶出过程中的化学损失,赤泥和铝酸钠溶液必须快速分离,为了回收赤泥附液中所带走的有用成分氧化铝和氧化钠,将赤泥进行多次反向洗涤再排入堆场。
氧化铝生产工艺总结
氧化铝生产工艺原料车间工艺图由矿石进场开始原料车间总结:1、母液就是碱液2、球磨机之前实际生产工艺中不加石灰石,只有母液和矿石。
溶出车间(管道化)工艺图原料合格料浆↓溶出矿浆槽合格水送电厂不合格水送热水站水凝水去热水站←新蒸汽↓乏汽保温罐↓料浆自蒸发器(闪蒸器)↓乏汽一次洗液稀释罐↓稀释后槽↓稀释泵(用2备1)冷凝水槽赤泥分离沉降沉降热水站沉降车间工艺图溶出稀释浆液分离沉降槽 一洗沉降槽 二洗沉降槽三洗沉降槽四洗沉降槽五洗沉降槽 外排饲料槽 溢流 溢流泵 粗液槽 粗液泵 立式叶滤机精液槽精液泵送去板式换热器石灰乳槽石灰乳 絮凝剂溶解槽絮凝剂泵洗水泵热水槽新蒸汽 溶出冷凝水、蒸发不合格水、消防水、赤泥回水等溶出稀释灌一次洗液纯品絮凝剂 各槽加入点 制备水槽排赤泥堆场焙烧车间(氧化铝最后一道工序)2.1、氢氧化铝经过焙烧炉的干燥段、焙烧段、和冷却段使之烘干、脱水和晶型转变后而成为氧化铝,其变化过程可分为如下几个阶段:2.1.1 附着水的脱除100℃AL(OH)3•H2O ————→AL(OH)3+H2O ↑2 .1.2结晶水的脱除250-300℃AL(OH)3•H2O——————→AL2O3•H2O+2H2O ↑500-560℃AL2O3•H2O——————→γ-AL2O3+H2O ↑2 .1.3晶型的转变γ-AL2O3在950℃开始晶型转变,逐渐由γ-AL2O3转变为α-AL2O3 。
2.2、焙烧炉工艺流程图:(见附页)2.3、工艺流程及原理平盘过滤机过滤的产品氢氧化铝落在皮带上,由皮带提升,进入缓冲小料仓L01中,再由计量皮带秤F01称量后入给料螺旋A01,由给料螺旋A01塞入文丘里干燥器A02,带一定附水的AH在文丘里干燥器中由来自焙烧炉P02的高温烟气干燥,并由高温烟气提升至预热旋风筒PO1中。
在PO1中进行气固分离后的烟气入电收尘器P11,分离开的并经过预热脱水的物料由PO1的下料管进入第二级预热旋风筒PO2,在PO2中进行预焙烧。
氧化铝焙烧工序简介
焙烧工序简介一、焙烧工序概述把从种分车间送过来的氢氧化铝料浆经洗涤过滤后送入焙烧炉的干燥与预热段,被预热的物料进入焙烧炉完成焙烧作业;焙烧物料经冷却系统冷却,得到合格的氧化铝送入氧化铝大仓。
二、焙烧主要设备及性能平盘过滤系统主要设备有平盘过滤机、真空泵、料浆泵、滤液槽等,过滤机为65㎡平盘过滤机,生产能力1.5t/m3.h.台。
焙烧系统主要设备有气态悬浮焙烧炉、ID风机、双室流态化冷却器、罗茨鼓风机、静电收尘器、干燥热发生器等。
焙烧采用气态悬浮焙烧炉,生产能力1400t/d.台;焙烧燃料为煤气,由厂区煤气站3台灰熔聚流化床粉煤气化炉提供,煤气值为1400kcal/Nm3。
三、焙烧工艺流程焙烧工序主要分为平盘和焙烧炉两大岗位。
平盘系统主要是处理由种分车间送过来固含在750~900g/L的氢氧化铝料浆,送入料浆槽,由料浆泵打上平盘,经布料均匀分布在平盘表面,在平盘转动一周的过程中完成两次洗涤、三次液固分离,液体在分配盘和真空的作用下分别进入母液槽、强液槽、弱液槽,产出的弱液经弱液泵打上平盘作一次洗液,强液送至化灰机进行化灰,母液送到六车间母液槽;洗涤合格后的氢氧化铝(附碱≤0.1%;附水≤8%),通过螺旋卸料,经皮带输送机进入氢氧化铝大仓。
焙烧系统主要处理平盘送过来的合格氢氧化铝,由皮带称称重后,经螺旋输送机送到文丘里干燥器中与旋风预热器PO2出来的大约350~400℃烟气相混合传热,脱去大部分附着水后进入PO1旋风预热器进行预热、分离。
PO1分离出的氢氧化铝和来自热分离旋风筒(PO3)的热气体(1000~1200℃)充分混合进行载流预热并带入PO2,氢氧化铝物料被加热至320~360℃,脱除大部分结晶水。
CO1旋风分离出来的风(600~800℃)从焙烧炉PO4底部的中心管进入,从旋风预热器PO2出来的氢氧化铝沿着锥部的切线方向进入焙烧炉,以便使物料、燃料与燃烧空气充分混合,在VO8、V19两个燃烧器的作用下,温度约为1050~1200℃,物料通过时间约为1.4S,高温下脱除剩余的结晶水,完成晶型转变。
山西铝业氧化铝焙烧流程
山西铝业氧化铝焙烧流程
山西铝业是中国最大的氧化铝生产企业之一,拥有先进的焙烧工艺流程。
焙烧是氧化铝生产的核心环节之一,其目的是将铝矾土中的结晶水和有机物质等挥发出去,使铝矾土转变为氧化铝。
一、铝矾土的预处理
山西铝业在氧化铝焙烧前,首先对铝矾土进行预处理。
铝矾土经过破碎、磨矿等工艺,得到粉碎后的铝矾土粉末。
然后,将铝矾土粉末与适量的水混合,形成矿浆。
二、矿浆的过滤
将铝矾土矿浆通过过滤设备进行过滤,去除其中的杂质和固液分离。
过滤后得到的固体物质称为滤渣,其中含有一定量的铝氧化物。
三、滤渣的焙烧
滤渣经过干燥处理后,进入焙烧炉进行焙烧。
焙烧炉内部温度高达1000℃以上,通过高温将滤渣中的结晶水和有机物质等挥发出去,使滤渣中的铝氧化物得到进一步提纯。
四、焙烧废气的处理
焙烧过程中产生的废气含有大量的有害气体和颗粒物,需要进行处理。
山西铝业采用先进的废气处理设备,如脱硫除尘装置和脱硝装置,将废气中的有害物质去除,以保护环境和员工的健康。
五、氧化铝的回收
焙烧后的滤渣经过冷却处理后,进一步加工提纯,得到高纯度的氧化铝。
氧化铝是一种重要的工业原料,广泛用于电子、建筑、化工等领域。
山西铝业通过优化焙烧工艺,不断提高氧化铝的产量和质量。
该企业还注重环保,积极推行废气处理和资源回收利用,以减少对环境的影响。
总结:
山西铝业的氧化铝焙烧流程包括铝矾土的预处理、矿浆的过滤、滤渣的焙烧、焙烧废气的处理和氧化铝的回收等环节。
通过先进的工艺和设备,山西铝业实现了氧化铝的高效生产和环保处理,为中国的氧化铝行业做出了重要贡献。
氧化铝粉焙烧工艺及设备
焙
烧
烧
区
区
域
域
工
设
艺
备
焙烧区域的任务
1、把分解车间送来的料浆 经过平盘过滤,得到合格 的氢氧化铝; 2、把平盘过滤的氢氧化铝 经过高温焙烧,制成合格 的氧化铝送到氧化铝大仓; 3、把大仓内的氧化铝根据 需要,包装成吨袋送至堆 栈发运。
焙烧区域的工序
本区域包括三个工序, 分别为成品过滤(包 括焙烧循环水)、氢 氧化铝焙烧(包括天 然气调压站)、氧化 铝仓及堆栈(包括氧 化铝输送系统)。
艺
•生产上水:
指
•平时水温 •夏季水温
≤32℃ ≤37℃
标
•电力供应:
标
•正常电压波动范围 ±5%
准
来料指标标准:
平盘
焙烧炉
• 洗水温度
85-90℃
• 洗水用量 化铝
0.57t/t-氢氧
• ቤተ መጻሕፍቲ ባይዱ浆固含
600-800g/l
• 调整后反吹风压力 0.050.1Mpa
• 真空度0.06Mpa
入炉氢氧化铝滤饼:附水 含量≤8% • 附碱含量≤0.12%
除尘,收集的粉尘被送回焙烧系统第二级冷
却旋风筒(Cc102,Cc202),净化后的烟气(含 尘量低于50mg/m3)排入大气中。 燃烧器系统包括:启动燃烧器
T12(SHG101,SHG201),主燃烧器 V19(CB101,CB201),辅助燃烧器V08(PB101,201), 文丘里干燥热发生器T11(VHG101,201)。
(Pc103,Pc203)进行气料分离;在一级旋风预 热器(Pc101,Pc201)分离后的烟气进入静电除尘 器。
经热分离器(Pc103,Pc203)分离后的氧化铝与二级 冷却旋风筒(Cc102,Cc202)来的预热空气混合并进 入一级冷却旋风筒(Cc101,Cc201)进行分离;经一 级冷却旋风筒(Cc101,Cc201)分离后的氧化铝与三 级冷却旋风筒(Cc103,Cc203)来的预热空气混合并 进入二级冷却旋风筒(Cc102,Cc202)进行分离;依 此类推,最终氧化铝经四级冷却旋风筒