铜的湿法冶金
湿法冶金原理的化学方程式

湿法冶金原理的化学方程式
湿法冶金是一种利用化学反应来提取金属的方法,其原理涉及
多种化学方程式。
以提取铜为例,湿法冶金的原理包括浸出、沉淀、萃取和电解等步骤。
首先,浸出阶段涉及到化学方程式,通常是利用硫酸溶液浸出
含铜矿石,其化学反应方程式为:
CuFeS2 + 4H2SO4 + O2 → CuSO4 + FeSO4 + 2H2O + 2SO2。
在这个方程式中,CuFeS2代表含铜的黄铜矿,H2SO4代表硫酸,O2代表氧气,CuSO4代表硫酸铜,FeSO4代表硫酸铁,SO2代表二氧
化硫。
接下来是沉淀阶段,通过加入铁粉或者氢气还原硫酸铜溶液,
使其中的铜离子还原成固体的金属铜,化学反应方程式为:
CuSO4 + Fe → Cu + FeSO4。
然后是萃取阶段,通过有机溶剂来萃取金属离子,例如利用二
甲基苯酚(萘酚)来萃取铜离子,其化学反应方程式为:
2HNO3 + Cu → Cu(NO3)2 + H2O.
最后是电解阶段,将含铜离子的溶液进行电解,将铜离子还原成固体铜,化学反应方程式为:
Cu2+ + 2e→ Cu.
以上是湿法冶金提取铜的基本化学方程式,该原理在提取其他金属时也会有所不同,但都遵循类似的化学反应原理。
6——铜的湿法冶金
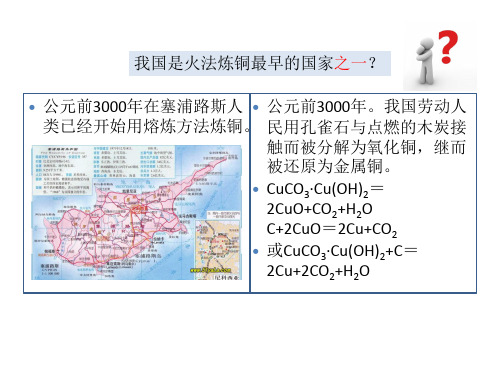
火法炼铜回顾
1、铜矿品位越来越低 2、大气环境污染
铜的湿法冶金
Hydrometallurgy of Copper
冶金与生态工程学院有色系 张娟
zhangjuan85@
湿法冶金发展史及现代湿法冶金 焙烧—浸出—电积法 浸取方式—以氧化铜矿为例 硫化铜矿湿法冶金 铜矿微生物浸取等其他方法
除铁方法:氧化水解法(MnO2);萃取法。 带机械搅拌的耐酸槽
(3) 电积 阴极:铜的始极片;阳极:铅锑合金板;电解液:净化液 槽总电反压应:为C1u.28+~+2H.52OV=,Cu电+1流/2O效2+率2H7+7~92% , 电 解 液 温 度 35 ~45°C , 阴 极 周 期 7d , 电 流 密 度 150~180A/m2 , 同 极 距 离 80~100mm。电解液中铜离子浓度越低,铁含量越高;温度 越高和阴极周期越长,则化学溶解量也越大,电流效率越低, 槽电压高和电流效率低,使电耗比铜电解精炼高10倍。
• 萃取时有机相的质子与水相的铜交换,使铜萃取到有 机相,质子进入水相补充浸取消耗的酸:
2RH+CuSO4 = CuR2+H2SO4 • 羟肟(wò)萃取剂:2-羟基二苯酮肟→ 2-羟基苯乙酮
肟→ 2-羟基苯甲醛肟。
有机相中负荷的铜在用阴电极积析残出,阳极析出氧 液反萃,得到富气电并解产液生,等电摩尔的硫酸。 解液酸度↓,萃取剂恢复酸 的形态,返回萃取。
1 铜湿法冶金发展历史
湿法炼铜概念:利用溶剂将铜矿、精矿或焙砂中的铜溶 解出来,再进一步分离、富集提取的方法。
世界冶金史界公认,湿法炼铜的工艺始于中国。汉代 《淮南万毕术》:白青(水胆矾Cu4SO4(OH)6 )得铁即 化为铜。
湿法炼铜的原理方程式

湿法炼铜的原理方程式湿法炼铜是一种重要的冶金工艺,广泛应用于铜的提取和精炼。
它利用了铜的化学性质和物理性质,通过一系列的化学反应和物理处理,将含铜矿石转化为高纯度的铜金属。
本文将详细介绍湿法炼铜的原理、方程式和工艺流程。
一、湿法炼铜的原理湿法炼铜是利用水溶液中的化学反应和物理处理将含铜矿石中的铜转化为可溶性的铜盐,再通过还原和沉淀等步骤将其转化为金属铜的过程。
这个过程可以分为以下几个步骤:1. 矿石破碎和浸出首先将含铜矿石破碎成小颗粒,然后将其浸入硫酸或氯化物等水溶液中。
水溶液中的酸或氯离子会与矿石中的铜离子结合形成可溶性的铜盐。
这个过程称为浸出。
2. 铜盐的萃取将浸出液中的铜盐与有机溶剂接触,利用有机溶剂对铜离子的选择性吸附,将铜盐从水溶液中萃取出来。
这个过程称为萃取。
3. 铜盐的还原将萃取出的铜盐加热至高温,使其分解为氧化物和铜金属。
这个过程称为还原。
4. 铜金属的沉淀将还原后的铜金属沉淀出来,通过过滤、干燥等步骤得到高纯度的铜金属。
这个过程称为沉淀。
以上几个步骤构成了湿法炼铜的基本原理。
二、湿法炼铜的方程式湿法炼铜的化学反应涉及到多种化学物质,其中比较常见的有硫酸、氯化物、铜盐、有机溶剂等。
下面列出了一些常见的反应方程式。
1. 矿石中的铜离子和硫酸的反应CuS + 2H2SO4 → CuSO4 + H2S↑ + SO2↑ + 2H2O2. 矿石中的铜离子和氯离子的反应CuS + 2HCl → CuCl2 + H2S↑3. 铜盐的还原反应2CuSO4 → 2CuO + 2SO2↑ + O2↑CuCl2 → Cu + Cl2↑4. 铜盐的萃取反应CuSO4 + 2HX → CuX2 + H2SO4其中,HX代表有机溶剂中的萃取剂,可以是酮、醇、酯等。
这些反应方程式描述了湿法炼铜过程中的化学反应和物理处理,为工艺流程的设计和优化提供了基础。
三、湿法炼铜的工艺流程湿法炼铜的工艺流程包括矿石破碎、浸出、萃取、还原和沉淀等步骤。
古代湿法冶金化学方程式

古代湿法冶金化学方程式古代湿法冶金是一种利用水和氧化剂来提取金属的方法。
这种方法起源于古代,被广泛应用于铜、铁、锡、银和金的制备过程中。
在湿法冶金中,金属矿石首先被粉碎成粉末,然后混合水和化学试剂,如硫酸、氢氧化钠和氯化铁等,生成溶液,通过加热和搅拌来促进反应,最终得到金属。
对于铜的湿法冶金过程,其化学方程式如下:CuFeS2(黄铜矿)+ 2O2 + H2O → CuSO4 + FeSO4 + 2H2SO4CuSO4 + Fe → Cu + FeSO4黄铜矿(CuFeS2)与氧气和水反应,生成硫酸、铁硫酸盐和铜硫酸盐。
接着,铁硫酸盐与铜硫酸盐反应,铜被还原成为纯铜,同时铁被氧化成为铁硫酸盐。
对于铁的湿法冶金过程,其化学方程式如下:Fe2O3(赤铁矿)+ 3H2SO4 → Fe2(SO4)3 + 3H2OFe2(SO4)3 + 3Zn → 3ZnSO4 + 2Fe赤铁矿(Fe2O3)与硫酸反应,生成硫酸亚铁和水。
接着,硫酸亚铁被还原成为纯铁,同时锌被氧化成为锌硫酸盐。
对于锡的湿法冶金过程,其化学方程式如下:SnO2(锡石)+ 4HC l → SnCl4 + 2H2OSnCl4 + 2H2O → SnO2 + 4HCl锡石(SnO2)与盐酸反应,生成氯化锡和水。
接着,氯化锡与水反应,生成锡石和盐酸。
对于银的湿法冶金过程,其化学方程式如下:Ag2S(硫化银)+ 2NaCN → Na2S + 2AgCN2AgCN + O2 + H2O → 2Ag + 2HCO3- + CN-硫化银(Ag2S)与氰化钠反应,生成硫化钠和氰化银。
接着,氰化银与氧气和水反应,生成纯银、碳酸氢根离子和氰根离子。
以上是古代湿法冶金的一些化学方程式,这些方程式的应用使得铜、铁、锡、银和金等金属的制备变得更加高效和可行。
这种方法的应用推动了全球经济的发展,同时也极大地促进了科学技术的进步。
虽然现代冶金方法已经发展到了更加高效和环保的程度,但是古代湿法冶金的发明和应用仍然是人类历史上重要的一步,对人类社会的发展产生了深远的影响。
现代铜湿法冶金概貌

现代铜湿法冶金概貌
萃取技术给铜的湿法冶金带来了革命性的变化,创建了现代湿法铜工业。
现代铜湿法工业包括浸取—萃取反萃—电积三部分,构成三个循环,如图所示。
浸取时酸与铜矿石反应使铜溶解进入溶液,萃取过程中铜离子和萃取剂的质子交换,进入有机相。
酸度重新提高的萃余液返回浸取。
有机相中负荷的铜用电积残液反萃,得到富电解液,电解液的酸度下降,而使萃取剂恢复酸的形态,返回萃取。
电积过程中,铜在阴极析出,阳极析出氧气并产生等摩尔的硫酸。
现代湿法提铜主要是从低品位矿,如氧化矿、剥离的表外矿、浮选尾矿、难选硫化矿甚至废弃的矿山中回收铜,而这些物料正是火法难以利用的原料。
因此,湿法与火法成为发展铜工业相辅相成的两种技术。
许多老矿山利用湿法处理过去开拓时剥离的表层岩石或者多年堆积的尾矿使产量显著提高。
有的新矿在设计时就将这两种方法结合起来,将边界品位之外的围岩、表层剥离物用湿法处理。
也有许多矿由于氧化程度高,开采后可进行湿法炼铜。
——郑州天一萃取。
湿法炼铜_精品文档
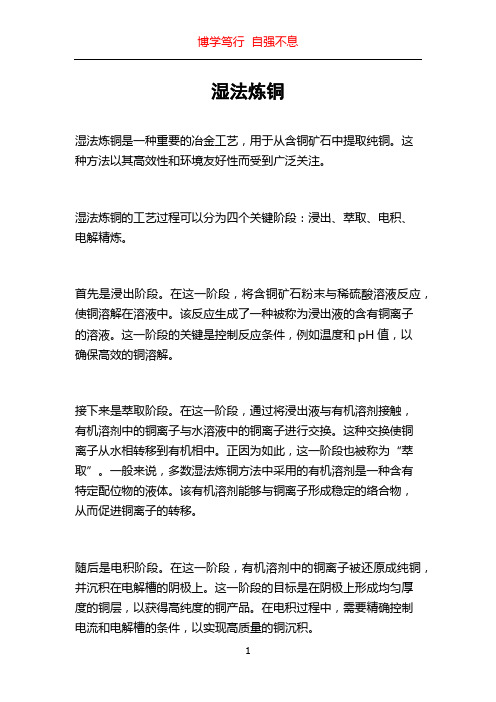
湿法炼铜湿法炼铜是一种重要的冶金工艺,用于从含铜矿石中提取纯铜。
这种方法以其高效性和环境友好性而受到广泛关注。
湿法炼铜的工艺过程可以分为四个关键阶段:浸出、萃取、电积、电解精炼。
首先是浸出阶段。
在这一阶段,将含铜矿石粉末与稀硫酸溶液反应,使铜溶解在溶液中。
该反应生成了一种被称为浸出液的含有铜离子的溶液。
这一阶段的关键是控制反应条件,例如温度和pH值,以确保高效的铜溶解。
接下来是萃取阶段。
在这一阶段,通过将浸出液与有机溶剂接触,有机溶剂中的铜离子与水溶液中的铜离子进行交换。
这种交换使铜离子从水相转移到有机相中。
正因为如此,这一阶段也被称为“萃取”。
一般来说,多数湿法炼铜方法中采用的有机溶剂是一种含有特定配位物的液体。
该有机溶剂能够与铜离子形成稳定的络合物,从而促进铜离子的转移。
随后是电积阶段。
在这一阶段,有机溶剂中的铜离子被还原成纯铜,并沉积在电解槽的阴极上。
这一阶段的目标是在阴极上形成均匀厚度的铜层,以获得高纯度的铜产品。
在电积过程中,需要精确控制电流和电解槽的条件,以实现高质量的铜沉积。
最后是电解精炼阶段。
在这一阶段,通过将电积得到的铜产品作为阳极,并将其浸入含有铜离子的电解液中,使阳极的铜溶解回溶液中。
这样,不纯度物质和其他杂质将被移动到电解液中并被分离,而高纯度的铜则在阴极上重新沉积。
这种电解过程可多次重复,以进一步提高铜的纯度。
湿法炼铜相对于其他炼铜方法有许多优势。
首先,湿法炼铜过程中不需要高温,相比干法炼铜过程更加节能。
其次,湿法炼铜是一种环保的方法,因为其涉及的溶液和有机溶剂可以通过再循环来减少废物的产生。
此外,湿法炼铜可以用于不同类型的矿石,包括低品位的矿石,这在一些地区具有重要意义。
最后,湿法炼铜还可以提供高品质的铜产品,可以在不同的应用领域广泛使用。
总结而言,湿法炼铜是一种高效、环保的冶金工艺,用于从含铜矿石中提取纯铜。
它包括浸出、萃取、电积和电解精炼四个关键阶段。
相比于其他炼铜方法,湿法炼铜具有许多优势,例如节能、环保和可适应不同的矿石类型。
湿法炼铜工艺流程
湿法炼铜工艺流程
湿法炼铜是一种常见的炼铜方法,下面将介绍湿法炼铜的工艺流程。
首先,湿法炼铜的原料是含铜矿石,如黄铜矿、黄铜硫矿等。
矿石经过破碎和磨矿处理,得到细粉末或浆料状的矿浆。
接下来,将矿浆经过搅拌和水洗净化处理。
这一步骤的目的是去除杂质和不含铜的矿石,将纯净的矿浆用于后续的处理。
然后,将纯净的矿浆经过浮选处理。
浮选是通过物理化学方法,将含有铜的矿石与其他杂质分离的过程。
通常会使用气体和药剂,使铜矿石悬浮在浮液中,然后利用气泡的粘附作用,将铜矿石从浮液中分离出来。
浮选后的铜矿石会进一步进行浓缩处理。
浓缩是通过过滤和沉淀等方法,将含有铜的矿石浓缩成铜精矿。
铜精矿是含有较高铜含量的固体物质,可以进一步进行提炼。
接下来,将铜精矿经过烧结处理。
烧结是将铜精矿加热至一定温度,以使其结合成一块块坚固的颗粒。
烧结后的颗粒可以更好地进行冶金处理。
然后,将烧结后的颗粒放入转炉中进行冶炼。
在冶炼过程中,通过加热和搅拌,使铜精矿中的铜和其他金属分离。
冶炼的结果是得到含有高纯度铜和其他金属的液体。
最后,通过电解或电解精炼的方法,将液体中的铜纯化。
电解是利用电流通过电解液,将铜离子还原为纯铜金属的过程。
电解精炼可以得到高纯度的铜。
综上所述,湿法炼铜的工艺流程包括破碎磨矿、水洗净化、浮选、浓缩、烧结、冶炼和电解等步骤。
这一工艺流程能够将含铜矿石中的杂质分离,得到纯净的铜金属。
湿法炼铜是一种常用且有效的炼铜方法。
湿法炼铜的做法和原理
湿法炼铜的做法和原理
湿法炼铜的做法和原理可以概括为以下几点:
一、湿法炼铜的主要原料
主要原料是含铜量丰富的矿石或粗铜,还需要添加返矿剂、熔剂等助熔剂。
二、湿法炼铜的主要设备
炉膛、电加热装置、粗铜供料机构、烟气处理系统等。
也需要有原料准备系统。
三、湿法炼铜的基本步骤
1. 配制含助熔剂的混合矿料。
2. 将混合料送入高温炉膛熔炼。
3. 熔炼分离粗铜质。
4. 精炼提高纯度。
5. 退火调质获得成品铜。
四、熔炼原理
1. 高温使硫化物分解,硫挥发,铜获得释放。
2. 返矿剂氧化铁类杂质,熔剂形成低熔点混合物。
3. 熔浴分离杂质与铜,铜集中沉淀。
五、精炼提纯机理
氧化反应将少量残留杂质氧化移除,获得高纯度铜。
六、环保与安全措施
收集处理烟气,确保操作安全,层层控制风险。
综上所述,这是湿法炼铜的主要工艺流程、装置以及背后的化学原理。
铜矿的湿法浸出与盐焙炉冶炼
湿法浸出是一种化学浸 出方法,用于提取铜矿
中的铜。
反应过程:首先将铜矿 粉碎,然后加入酸或碱 溶液,通过搅拌、加热 等手段促进反应进行。
原理:利用酸或碱溶 液与铜矿中的铜化合 物反应,将铜离子溶
解在溶液中。
浸出液中铜离子的浓 度可以通过控制反应 条件进行调整,以达
到最佳浸出效果。
硫酸:用于铜矿的氧化浸出,具有强酸性和氧化性 氯化物:用于铜矿的还原浸出,具有强还原性和络合能力 氨水:用于铜矿的氨浸出,具有碱性和络合能力 柠檬酸:用于铜矿的柠檬酸浸出,具有络合能力和抗沉淀能力
湿法浸出:成本 低,但设备投资 大,能耗高
盐焙炉冶炼:设 备投资小,能耗 低,但成本较高
综合考虑:根据 铜矿品位、规模 、地理位置等因 素选择合适的方 法
发展趋势:随着 环保要求的提高 ,湿法浸出逐渐 被盐焙炉冶炼取 代
湿法浸出: 废水产生量 大,需要处
理和回收
盐焙炉冶炼: 废气排放量 大,需要净 化和处理
浸出剂添加:向矿石中加入浸 出剂,如硫酸、硝酸等,使铜
离子进入溶液。
固液分离:将浸出后的固体残 渣与溶液分离,得到铜离子溶
液。
铜离子还原:将铜离子溶液中 的铜离子还原为铜单质,得到
铜粉。
铜粉干燥:将洗涤后的铜粉进 行干燥处理。
矿石准备:将铜矿石粉碎至一 定粒度,并混合均匀。
溶液净化:对铜离子溶液进行 净化处理,去除杂质离子。
搅拌速度:搅拌速度会影 响浸出剂与矿石的接触和 反应效果
压力:压力会影响浸出剂 的渗透和反应效果
焙烧:将预热后的物料放入 盐焙炉中,在特定温度下进 行焙烧,使铜矿石中的铜元 素被还原出来。
预热:将混合物料预热至一定 温度,使还原剂和熔剂充分反 应。
湿法炼铜原理
湿法炼铜原理
湿法炼铜是一种常用的冶炼方法,通过将铜矿石与水和化学溶剂混合,利用物理和化学反应来提取铜金属。
它的主要原理包括以下几个步骤:
1. 破碎和磨矿:将铜矿石破碎成较小的块状,并使用磨机将其磨成细粉。
这样有利于提高矿石表面积,使之更容易与水和化学溶剂发生反应。
2. 浸矿:将粉状的铜矿石与水混合,形成矿浆。
在浸矿过程中,水中的氧和硫酸等离子与铜矿石中的铜元素发生化学反应,生成铜离子。
3. 萃取:通过向矿浆中添加化学溶剂,如有机相(通常是含有萃取剂的有机溶剂),将铜离子从矿浆中萃取出来。
化学溶剂与含铜离子的矿浆中的其他杂质发生选择性溶解和反应,使铜离子从溶液中分离出来。
4. 脱水:在萃取过程中,溶剂中吸收了很多水分,这会降低其效率。
因此,需要对溶剂进行脱水处理,使其重新准备好萃取铜离子的工作。
5. 铜的电解:将从化学溶剂中萃取出的铜离子溶液传输到电解槽中,通过电解过程将铜离子还原成固态的铜金属,然后收集和提取这些铜金属。
总之,湿法炼铜通过浸矿、萃取、脱水和电解等步骤将铜矿石
中的铜元素提取并纯化成金属铜。
这种方法相对简单,运行成本较低,因此在铜冶炼中得到广泛应用。
- 1、下载文档前请自行甄别文档内容的完整性,平台不提供额外的编辑、内容补充、找答案等附加服务。
- 2、"仅部分预览"的文档,不可在线预览部分如存在完整性等问题,可反馈申请退款(可完整预览的文档不适用该条件!)。
- 3、如文档侵犯您的权益,请联系客服反馈,我们会尽快为您处理(人工客服工作时间:9:00-18:30)。
温度升高而升高,有利于反应加速进行,故可 提高生产率。
10
(2)萃取 用溶剂萃取法从铜浸出液富集铜的过程由
以下两步骤组成: 1)萃取
将铜浸出液—水相与不相溶的萃取剂—有 机相搅拌混合,水相中的铜离子转移到或被萃 取到有机相中,两相澄清分离后,留下负载有 机相,水相即为萃余液返回用于浸出矿石。
海绵铜。
0
国内外应用: 国外:美国亚利桑那州乌矿建成了世界上第一个
工业规模的浸出—萃取—电积(简称L—SX—EW) 工厂。1997年智利建成世界上最大的L—SX—EW法 炼铜工厂,其生产能力为22.5万吨/年,产品达到伦 敦金属交易所A级铜标准。合计:200万吨,占20%。
国内:海南(83年)建成了我国第一个L—SX— EW工厂。以后陆续在云南、中条山、西藏尼木、新 疆伽师、嫩江、江西等地建有一批湿法炼铜厂。目 前湿法炼铜厂的生产能力达20万吨/年。
①氧化铁硫杆菌; ②氧化硫杆菌。能在PH=1.5~3.5的酸性环境 中生存和繁殖。
30
细菌浸出的机理: 1)细菌的直接作用:
氧化铁硫杆菌 为取得维持生命的能源而将矿 石中的低价铁和硫氧化成高价,氧化过程中破坏了 矿石的晶格,使矿石中的硫化物变为硫酸盐而转入 溶液中。
CuFeS2 + 4O2 = CuSO4 + FeSO4 Cu2S + H2SO4 + 5/2O2 = 2CuSO4 + H2O
4
搅拌浸出 搅拌浸出是在装有搅
拌装置的浸出槽中进行, 用较浓的硫酸溶液(含 H2SO4 50 ~ 100g/L)浸出 细粒(-75μm占90%以上) 氧化矿或硫化矿的焙砂, 一般含铜品位较高。
搅拌浸出具有比槽浸 速度快、浸率高等优点, 但设备运转能耗高。
5
堆浸
堆浸常用于低铜表外矿、铜矿废石的浸出。
1、该法的优点
1)建厂投资和生产费用低,生产成本低于火 法,具有很强的市场竞争力;
2)以难选矿难处理的低品位含铜物料为原料, 独具技术优越性;
3)无废气、废水和废渣污染,符合清洁生产 要求;
4)拥有可靠的特效萃取剂市场供应。
27
硫化矿用稀酸浸出的速度较慢,但有细菌存 在时可显著加速浸出反应。
若浸出的对象是贫矿、废矿,所得浸出液含 铜很低,难以直接提取铜,必须经过富集,萃取技 术能有效地解决从贫铜液中富集铜的问题。
当温度较低时,化学反应速度小于气体的扩 散速度,过程总速度取决于表面反应的条件并服 从阿累尼乌斯指数定律。
当温度较高时,化学反应速度迅速增大并超过 气体扩散速度,过程总速度取决于气体的扩散速 度。
17
(4) 焙烧设备及经济指标
沸腾炉:一般为圆形(个别厂用长方形)。炉壳 用钢板焊成,内衬耐火砖。技术条件及经济指标列 于下表 11-1 。
1、工艺流程:
图 11.1 工艺流程
13
2、硫化铜精矿的焙烧
(1) 焙烧的目的 焙烧是首道工序,使炉料进行硫酸化焙烧,
其目的是使绝大部分的铜变为可溶于稀硫酸的 CuSO4和CuO•CuSO4,而铁全部变为不溶的氧化 物(Fe2O3),产出的SO2供制酸。
14
(2) 焙烧过程热力学
主要反应: MeS + 3/2O2= MeO+SO2 2SO2 + O2 = 2SO3 MeO + SO3= MeSO4
--------15 220 20~25 5
--80 20
15.0
9 825 --- 19 53
3、焙烧矿的浸出与净化
(1)浸出过程 焙砂中Cu主要以CuSO4、CuO•CuSO4、Cu2O、
CuO存在,而Fe以Fe2O3存在。当用稀硫酸作溶剂 时 , 除 CuO•Fe2O3 不 溶 外 , 其 余 都 溶 于 硫 酸 生 成 CuSO4。Fe2O3不溶于硫酸,但少量的FeSO4也溶于 其中。
常用的除铁法为氧化水解法,即在PH=1~1.5, T=60℃时,用MnO2将Fe2+氧化成Fe3+,然后使Fe3+ 水解成Fe(OH)3沉淀除去。即 2 FeSO4+MnO2+2H2SO4=Fe2(SO4)3+MnSO4+2H2O
Fe2(SO4)3+6H2O=2Fe(OH)3 ↓ +3H2SO4
21
焙砂
(%)
烟气中SO2浓度
(%)
炉料与焙砂中含硫量之差 (%)
给料率(干精矿) (吨/日)
炉料含铜
(%)
床能率(干料) (吨/日)
1.2 30 70 --10~14 19 17.4--18 3.82
1.3 30 70 6.7 11.5-22 10 17~19 4
--85 15 15.3 10~12 180~270 20 15- 25
680 525-560
炉料水分
(%)
1
0.1
20~22
30
10
直线速度
(米/秒)
O.23
O.42 O.13 -O.22 0.15
0.4
空气的体积速度 (米3/分) 27.5~28
14.2
100~170
325
420~ 500
风帽口风速
(米/秒)
12
22
---
---
---
空气过剩系数
(a)
产品:烟尘
(%)
阴极:Cu2+ + 2e = Cu 阳极:H2O - 2e = 1/2O2 + 2H+ 总反应:Cu2+ + H2O = Cu + 1/2O2 + 2H+
23
(2)电积实践及技经指标
电积时的 实 际槽 电 压为 1.8 ~2.5V, 电效 仅为 77~92%,电解液中Cu2+浓度越低,铁含量越高, 温度越高和阴极周期越长,促使化学溶解增高,电 效也就越低。槽电压和电效低的结果,使电耗为铜 电解精炼的十倍。
(3)浸出净化设备
浸出和净化都可在带机械搅拌的耐酸槽内进 行,浸出时可加絮凝剂加速沉淀,在Fe(OH)3成胶 状沉淀时,可吸附溶液中的As、Sb、Bi等杂质一同 除去。
22
4、电积过程
铜的电积也称不溶阳极电解,以纯铜作阴 极,以Pb-Ag(含Ag 1%))或Pb-Sb合金板作阳 极,上述经净化除铁后的净化液作电解液。电解 时,阴极过程与电解精炼一样,在始极片上析出 铜,在阳极的反应则不是金属溶解,而是水的分 解放出氧气。 (1)电积反应
影响浸出反应速度的因素是温度,溶剂浓度和 焙砂粒度,通常温度在80~90℃,H2SO4>15g/L, 焙砂粒度小于0.074mm,采取搅拌浸出。
20
(2)净化过程 浸出液的组成(g/L):50~110Cu、2~18H2SO4、
2~4Fe2+、1~4Fe3+,铁在电积时将反复氧化还原 而消耗电能,故必须净化除去。
Cu2CO3(OH)2+2H2SO4=2CuSO4+CO2+3H2O CuSiO3•2H2O+H2SO4=CuSO4+ SiO2+3H2O
2Cu2O+4H2SO4=4CuSO浸出:
又称微生物浸出,它是近30年发展起来的新技 术,是利用细菌的生物催化剂作用,加速矿石中有 价组分的浸出过程,成为处理低品位矿的一个重要 方法,每年从数量巨大的低品位尾矿及废矿石中生 产的铜超过50万吨。 浸铜菌种:
25
6、优缺点
各工序单元操作简单、成熟,建厂投资容易 。但工艺中废酸处理和渣中有价金属回收成了两道 难关。中和法处理废酸简单易行,但酸未得到利用 ,而且碱耗很大;浸出渣中1%左右的铜及贵金属也 无可行办法回收。正是这些难题,使兴旺了几年的 该湿法工艺,逐渐退出了炼铜领域。
26
三、硫酸浸出-萃取-电积法
11
2)反萃 以适量的废电解液与负载有机相进行搅拌
混合,负载有机相中的铜离子转入硫酸(废电 解)溶液中,即成为富铜电解液,反萃后的卸 载有机相(再生有机相)返回用于萃取。富铜 液送往电解车间沉积铜。
12
二、焙烧-浸出-电积法
(Roasting- Leaching- Electrowinning)。
8
就地浸出 就地浸出又称为地下浸出,可用于处理残留
矿石或未开采的氧化铜矿和贫铜矿。 加压浸出
对于在常压和普通温度下难于有效浸出的矿 物常采用加压浸出的方式。加压浸出即在密闭的 加压釜中,在高于大气压的压力下对矿进行浸出。
9
加压浸出的优点: 1)可以在较高温度下进行浸出; 2)在高温高压下,使一些在普通温度下不
1
2、湿法炼铜的优点
火法处理硫化铜矿虽具有生产率高,能耗低,电铜 质量好,有利于金、银回收等优点,但目前已面临 两个难题:一是资源问题;二是大气污染问题。
1)资源问题:硫化铜矿作为目前火法炼铜的主 要原料,开采品位越来越低,因此,低品位硫化矿、 复合矿、氧化矿和尾矿将成为今后炼铜的主要资源。 这类贫矿,火法是无法直接处理的。
浸出场地多选在不透水的山坡处,将开采出的废
矿石破碎到一定粒度筑堆;在矿堆表面喷洒浸出
剂,浸出剂渗过矿堆时铜被浸出,浸出液返流到
集液池以回收。
堆浸的特点是浸出设备投资少,运行费用低。
氧化矿的堆浸已进行了多年,技术有较大的改进。
近年来由于细菌浸矿技术的发展,硫化矿和混合
矿也可堆浸,甚至最难浸出的黄铜矿,也可引入
电积时电解液温度为35~45℃,阴极周期可取7 天 , Dk 为 150 ~ 180A/m2 , 所 得 电 铜 含 铜 为 99.5 ~ 99.95%。
24
5、废液及废渣的处理 (1)电解废液的处理: 电解废液最好全部返回浸出过 程但这种平衡很难达到,所以出现废液的处理问题。