专用钻床液压系统设计11316149(DOC)
专用卧式钻床液压设计Word版

摘要随着现代机械制造工业的快速发展,制造装备的改进显得尤为重要,尤其是金属切削设备的改造是提高生产力一项重要因素。
专用卧式铣床液压系统的设计,除了满足主机在动作和性能方面规定的要求外,还必须符合体积小、重量轻、成本低、效率高、结构简单、工作可靠、使用和维修方便等一些公认的普遍设计原则。
铣床液压系统的设计主要是根据已知的条件,来确定液压工作方案、液压流量、压力和液压泵及其它元件的设计。
通过对专用铣床进行改造实现液压夹紧和液压进给,使其在生产过程中据有降低成本、工作可靠平稳,易于实现过载保护等优点。
关键词:液压系统,液压夹紧,液压进给目录摘要 (1)1、明确液压系统的设计要求 (3)2、负载与运动分析 (4)3、负载图和速度图的绘制 (6)4、确定液压系统主要参数 (7)4.1确定液压缸工作压力 (7)4.2计算液压缸主要结构参数 (7)4.3绘制液压缸工况图 (9)5、液压系统方案设计 (10)5.1确定调速方式及供油形式 (10)5.2快速运动回路和速度换接方式的选择 (10)5.3换向回路的选择 (11)5.4调压和卸荷回路的选择 (11)5.5组成液压系统原理图 (12)5.6系统图的原理 (13)6、液压元件的选择 (16)6.1确定液压泵的规格和电动机功率 (16)6.2确定其它元件及辅件 (17)6.3主要零件强度校核 (19)7、液压系统性能验算 (21)7.1验算系统压力损失并确定压力阀的调整值 (21)7.2油液温升验算 (22)设计小结 (24)参考文献 (26)1 明确液压系统的设计要求设计一台专用卧式钻床的液压系统,要求液压系统完成“快进—工进—快退—停止”的工作循环。
已知:最大轴向钻削力为14000N,动力滑台自重为15000N,工作台快进行程为100mm,工进行程为50mm,快进、快退速度为5.5m/min,工进速度为51—990mm/min,加、减速时间为0.1s,动力滑台为平导轨,静摩擦系数为0.2,动摩擦系数为0.1。
专用钻床液压系统设计

专用钻床液压系统设计钻床液压系统设计是钻床工作中非常关键的一部分,其性能直接影响到钻床的工作效率和质量。
为了设计出高性能的液压系统,需要充分考虑钻床的工作要求以及使用环境的特点。
首先,对于钻床液压系统的设计而言,需要明确钻床的工作要求。
钻床通常用于钻孔、扩孔和攻丝等工序,因此需要具备稳定的工作压力和流量。
在设计液压系统时,需要根据钻床的工作要求来选择合适的液压元件,如液压泵、液压缸和液压阀等。
同时,应根据钻床的工作负荷来确定液压泵的流量和工作压力的范围,以确保系统能够满足钻床的工作需要。
其次,钻床液压系统的设计还需要考虑使用环境的特点。
由于钻床通常在工厂环境中使用,因此系统需要具备良好的耐用性和抗污染能力。
液压元件应选择质量可靠的产品,以提高系统的稳定性和可靠性。
此外,液压系统还需要安装滤清器和冷却装置等附件,以确保液压油的清洁程度和温度的适宜性。
这样可以避免液压系统由于污染和过热等原因出现故障,提高系统的可靠性和使用寿命。
另外,在钻床液压系统设计中,还需要合理选择液压元件的布置方式和管路设计。
液压元件的布置方式应简洁紧凑,以减小系统的体积和重量。
同时,液压元件之间的管路设计需要简单明了,以减小流阻和压力损失,提高系统的效率。
此外,对于较大的钻床液压系统,还应考虑采用并联布置方式,以提高系统的可靠性和冗余度。
最后,钻床液压系统的设计中,还需要充分考虑系统的安全性和人机工程学要求。
液压系统应配备相应的安全阀和压力控制装置,以确保系统在超压和故障状态下能够自动停机或报警。
此外,液压系统的工作控制方式应符合人体工程学要求,方便操作人员的操作和维护。
综上所述,钻床液压系统设计需要充分考虑钻床的工作要求和使用环境的特点,选择合适的液压元件,合理布置元件和管路,确保系统的可靠性、稳定性和效率。
同时,还需要满足系统的安全性和人机工程学要求,提高系统的可操作性和可维护性。
只有在各方面因素充分考虑下的设计,才能够设计出高性能的钻床液压系统。
四轴卧式钻孔专用机床液压系统设计

四轴卧式钻孔专用机床液压系统设计
钻孔机床液压系统主要是由油箱、泵、电机、电磁阀、缸体、阀门等组成。
液压系统的主要功能是提供稳定的油压,驱动机床的各个部件实现钻孔加工操作。
液压系统的设计需要考虑以下几个方面:
1. 液压油箱的容量和形状设计:油箱应具有足够的容量和形状,以确保液压油的供应充足并且能够有效地冷却液压油。
2. 泵和电机的选型:根据机床的需求,选择合适的泵和电机,以提供足够的流量和压力。
同时,考虑电机的功率和转速,以确保其能够满足机床的运行要求。
3. 阀门的设计:选择合适的液压阀门,以实现机床的各项功能。
同时,在液压系统中设置压力维持阀,以确保系统的稳定性和安全性。
4. 缸体的设计:根据机床的不同需求,选择不同类型和规格的缸体,以实现机床的各个部件运动控制。
5. 液压系统的控制:根据机床的需要,选择合适的控制方式,如手动控制、自动控制等。
总的来说,设计液压系统需要考虑机床的需求和工作条件,以确保液压系统的稳定性、可靠性和安全性。
任务书-专用钻床液压系统设计

机电建筑工程_部_机械设计及自动化教研室
___机械设计制造及自动化___专业
题目专用钻床液压进给系统及泵站设计
任务起止日期:2013年1月14日至2013年5月5日
学生姓名学号______________
指导教师
教研室主任201年月日审查
系主任____________ 201年月日批准
5相关的机械和液压设计手册及书籍
备
注
注:1、学生进行毕业论文(设计)前,指导教师应填好此任务书,经教研室、部(系)主任签字后,正式给学生下达任务。
2、若是课题组共同完成一项大任务应在备注栏内填写同组设计者名单。
2.文献综述、开题报告:要认真阅读指导教师指定的和自选的与研究课题有关的有代表性的参考文献资料15篇以上,写出3千字左右的文献综述、开题报告。
3.外文阅读与翻译:与研究课题有关的外文参考资料阅读量不少于10万印刷符,外文翻译不少于1.5万印刷字符(3.5千汉字以上)。
4.毕业设计说明书正文字数不少于1.5万字篇幅的内容(含图表)。目的 Nhomakorabea和
要
求
设计一台钻盲孔组合机床的液压进给系统,机床的工作循环为“快进—工进—死挡铁停留—快退—原位停止”,工件的夹紧由液压缸完成,夹紧力为5000N,夹紧行程为50mm,夹紧时间Δt2=1s,切削负载为15000N,工件及夹具重量G2=800N,快进、快退速度V1=5000mm/min,进给速度V2=60~1000mm/min,最大有效行程为300mm,工进行程为50mm,启动换向时间Δt2=0.2s,采用平导轨,静摩擦系数f=0.2,动摩擦系数f=0.1。
通过毕业设计,掌握液压系统设计的一般方法和步骤,提高综合运用基础理论和专业知识分析问题和解决问题的能力及编写技术文件的能力,为毕业生走上社会尽快地适应工作打下基础。
(完整版)液压系统设计-设计一台专用钻床液压系统.

液压系统课程设计课程题目_________________________________ 班级____________________________________ 学号____________________________________姓名____________________________________目录一、液压传动课程设计的目的和要求 ............................ 3..二、液压传动课程作业的题目和任务 ............................ 3..三、技术要求 ............................................... 5...四、工况分析 ............................................... 6...五、确定参数,绘图工况 ..................................... 7...六、拟定液压系统原理图 ..................................... 9...七、组成液压元件、附件设计1..1八、液压系统的技术损失1.3.九、设计体会1..3.十、参考文献1..3.一、液压传动课程设计的目的和要求一、目的液压传动课程作业是本课的一个综合实践教学环节,通过该教学环节,要求达到以下三个目的:1、巩固和深化已学的理论知识,掌握液压系统设计的一般方法和步骤;2、能正确合理的确定执行元件,选用标准液压元件;能熟练的运用液压基本回路组合成满足基本性能要求的、高效率的液压系统;3、熟练并运用有关的国家标准、部件标准、设计手册和产品样本等技术资料。
_____ i ll,[、-二、要求1、设计是必须从实际出发,综合考虑使用性、经济性、安全性及操作方便和结构简单。
多设想几种方案进行分析对此后确定最理想的一个;2、独立完成作业。
专用钻床的液压系统设计

专用钻床的液压系统设计引言:钻床作为一种常用的金属加工设备,液压系统作为其重要组成部分之一,发挥着重要的作用。
本文将介绍专用钻床的液压系统设计,包括液压系统结构、液压元件的选择与布置、液压系统的工作原理与工作过程等内容。
通过合理设计液压系统,可以有效提高钻床的加工精度和工作效率。
一、液压系统结构1.液压源:液压源一般采用液压泵来提供压力油源,可以选择柱塞泵、齿轮泵等。
液压泵应具有足够的流量和压力,以满足钻床工作时的需要。
2.液压元件:液压元件包括液压缸、液压阀、压力阀、流量阀等。
液压缸一般用于提供钻削力,可以选择单作用液压缸或双作用液压缸。
液压阀用于控制液压系统的工作,可以选择控制阀、方向阀等。
压力阀和流量阀用于调节液压系统的压力和流量。
3.控制元件:控制元件一般包括电磁阀、压力开关、流量开关等。
电磁阀用于控制液压阀的开关,实现液压系统的工作。
4.执行元件:执行元件主要是指钻头,它通过液压缸的工作实现对工件的加工。
二、液压元件的选择与布置在设计液压系统时,应根据实际需要选用合适的液压元件,并合理布置在钻床设计中。
1.液压泵的选择:液压泵应具有足够的流量和压力,以满足钻床的工作需要。
选择液压泵时要考虑钻床的功率和工作压力,以及泵的性能指标。
2.液压缸的选择:液压缸可以选择单作用液压缸或双作用液压缸。
单作用液压缸只有一个工作腔,只能实现单向的力作用;双作用液压缸有两个工作腔,可以实现双向力的作用。
选择液压缸时要考虑钻床的加工力和工作空间等因素。
3.液压阀的选择与布置:液压阀的选择需要根据液压系统的控制要求来确定。
液压阀可以选择控制阀、方向阀等,布置时要考虑液压阀与液压缸和液压源的连接。
4.压力阀和流量阀的选择:压力阀和流量阀用于调节液压系统的压力和流量,应根据液压系统的工作压力和流量来选择。
三、液压系统的工作原理与工作过程液压系统的工作原理是靠液体传递压力来实现的。
液压系统的工作过程主要分为压力产生、压力传递和执行控制三个过程。
液压钻机的液压系统设计_毕业设计精品

液压钻机的液压系统设计_毕业设计精品液压钻机是一种利用液压能量进行工作的设备,液压系统设计对于液压钻机的性能和工作效率具有重要影响。
液压钻机的液压系统设计需要考虑以下几个方面:液压系统的工作原理、系统的组成部分、控制方式、液压元件的选型和系统参数的计算与估算等。
首先,液压钻机液压系统的工作原理是通过液压泵将液压油压力传递给液压马达或液压缸,从而产生的力和运动。
液压泵通过驱动机械将机械能转化为液压能,并提供所需的流体压力。
液压马达或液压缸则通过液压油的流动将液压能转化为机械能,从而实现工作。
液压钻机液压系统的组成部分一般包括液压泵、液压马达或液压缸、液压控制阀、油箱、管路和配件等。
液压泵用于提供流体压力,液压马达或液压缸用于转化液压能为机械能,液压控制阀用于控制流体进出液压马达或液压缸,油箱用于储存液压油,管路和配件用于连接和配合各个部分。
液压钻机液压系统的控制方式可以分为手动控制和自动控制两种。
手动控制方式需要操作人员手动控制液压控制阀的开关,从而实现液压机件的启动、停止和控制。
自动控制方式则通过电气控制系统或其他控制装置,根据设定的程序或信号控制液压系统的工作状态和运动。
液压钻机液压系统中的液压元件选型需要根据工作条件和要求,选择合适的液压泵、控制阀、油缸和油管等。
根据所需的流量和压力,选择适当类型和规格的液压泵;根据工作负荷和速度,选择合适的液压马达或液压缸;根据工作方式和控制要求,选择合适的液压控制阀;根据工作环境和特殊要求,选择适当的油管和配件。
液压钻机液压系统参数的计算与估算是设计过程中的重要环节。
通过对钻机工作负荷、速度、压力等因素的分析和估算,计算出液压系统的流量、压力、功率以及油箱容积等参数。
同时,还需要考虑液压系统的稳定性和可靠性,通过合理的设计和计算,确保系统能够满足实际工作需求。
综上所述,液压钻机的液压系统设计是一个涉及多个方面的复杂任务,需要综合考虑液压系统的工作原理、组成部分、控制方式、液压元件的选型和系统参数的计算估算等因素。
专用钻床液压系统设计说明书
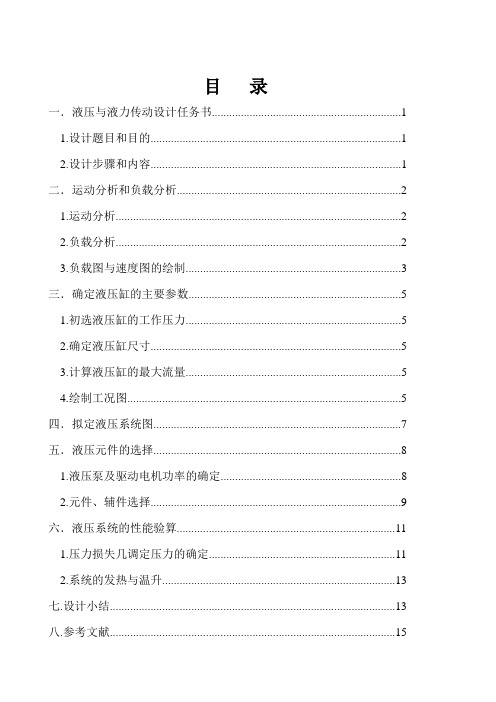
目录一.液压与液力传动设计任务书 (1)1.设计题目和目的 (1)2.设计步骤和内容 (1)二.运动分析和负载分析 (2)1.运动分析 (2)2.负载分析 (2)3.负载图与速度图的绘制 (3)三.确定液压缸的主要参数 (5)1.初选液压缸的工作压力 (5)2.确定液压缸尺寸 (5)3.计算液压缸的最大流量 (5)4.绘制工况图 (5)四.拟定液压系统图 (7)五.液压元件的选择 (8)1.液压泵及驱动电机功率的确定 (8)2.元件、辅件选择 (9)六.液压系统的性能验算 (11)1.压力损失几调定压力的确定 (11)2.系统的发热与温升 (13)七.设计小结 (13)八.参考文献 (15)一.液压与液力传动设计任务书1.设计题目和目的题目:试设计一专用钻床的液压系统,要求完成”快进-工作-快退-停止(卸荷)”的工作循环.已知:切削阻力为13412N,运动部件自重为5390N,快进行程为300mm,工进行程为100mm,快进,快退运动速度为4.5m/min,工进速度为60-1000mm/min,加速和减速时间为△t=0.2sec,机床采用平导轨,摩擦系数为Fs=0.2,Fd=0.1目的:液压系统的设计是整机设计的重要组成部分,主要任务是综合运用前面各章的基础知识,学习液压系统的设计步骤、内容和方法。
通过学习,能根据工作要求确定液压系统的主要参数、系统原理图,能进行必要的设计计算,合理地选择和确定液压元件,对所设计的液压系统性能进行校验算,为进一步进行液压系统结构设计打下基础。
2.设计步骤和内容液压系统的设计步骤和内容大致如下:(1)明确设计要求,进行工况分析,绘制负载和速度循环图;(2)确定液压系统的主要性能参数;(3)进行方案设计、拟订液压系统原理图;(4)计算和选择液压元件;(5)验算液压系统的性能;(6)液压缸设计;(7)绘制工作图,编写技术文件,并提出电气控制系统的设计任务书。
以上步骤中各项工作内容有时是互相穿插、交叉进行的。
- 1、下载文档前请自行甄别文档内容的完整性,平台不提供额外的编辑、内容补充、找答案等附加服务。
- 2、"仅部分预览"的文档,不可在线预览部分如存在完整性等问题,可反馈申请退款(可完整预览的文档不适用该条件!)。
- 3、如文档侵犯您的权益,请联系客服反馈,我们会尽快为您处理(人工客服工作时间:9:00-18:30)。
湖北文理学院理工学院《液压与气压传动课程设计》说明书课题名称:专用钻床的液压传动学生姓名:殷红进学号:专业:机械设计制造及其自动化班级:机械1111 成绩:指导教师签字:2014年5月30日目录No table of contents entries found.设计内容计算说明结论题目及要求动作要求分析一,设计题目及要求:试设计一专用钻床的液压系统,要求完成”快进-工作-快退-停止(卸荷)”的工作循环.已知:切削阻力为15000N,运动部件自重为5000N,快进行程为220mm,工进行程为80mm,快进,快退运动速度为5m/min,工进速度为60-1000mm/min,加速和减速时间为△t=,机床采用平导轨,摩擦系数为Fs=,Fd=二,工况分析动作要求分析根据主机动作要求画出动作循环图如图1-1图1-1 动作循环图设计内容计算说明结论工作负载摩擦负载惯性负载负载分析(1)工作负载:工作负载与设备的工作情况有关,在机床上,与运动件的方向同轴的切削力的分量是工作负载。
F L=15000N(2)摩擦负载:摩擦阻力是指运动部件与支撑面间的摩擦力,它与支承面的形状,放置情况,润滑条件以及运动状态有关。
静摩擦负载 F fs=fsG = *5000)=1000N动摩擦负载 F fd=fdG = *5000)=500N(3)惯性负载:惯性负载是运动部件的速度变化是,由其惯性而产生的负载,可用牛顿第二定律计算。
加速F a1=m*a1=(5000/10)*=减速 F a2 = m*a2=(5000/10)*=185NF L=15000NF fs=1000NF fd=500NFa1=F a2=185N设计内容计算说明结论制动 F a3 = m*a3 =(5000/10)*=反向加速 F a4 = Fa1 =反向制动 F a5 = Fa4 =185N如果忽略切削力引起的颠覆力矩对导轨摩擦里的影响,并设液压缸的机械效率ηm=,则液压缸在各工作阶段的总机械负载可以算出,见表工况计算公式总负载F/N缸推力F/N启动F fs1000加速F fd + F a1快进F fd500减速F fd - F a2315工进F L + F fd15500制动F L+F fd–F a318350 反向加速F fd - F a4快退F fd 500制动F fd+ F a5685 Fa3=F a4=F a5=185N负载图和速度图的绘制负载图和速度图的绘制根据负载计算结果和已知的各个阶段的速度,由于行程是400mm,设定快进时的行程L1=300mm,工进时的行程L2=100mm。
可绘出负载图(F-l)和速度图(v-l),见图1-2a、b。
横坐标以上为液压缸活塞前进时的曲线,以下为液压缸退回时的曲线。
1-2a,b液压缸主要参数确定初选液压缸的工作压力液压缸尺寸、液压缸主要参数确定(1)、初选液压缸的工作压力按负载大小根据表2选择液压缸工作压力表2 按负载选择执行元件工作压力根据最大负载F=19412N, 初选液压缸的工作压力为3MPa(2)、计算液压缸尺寸按最大负载Fmax计算缸筒面积A得3MPa246max1071.5410394.16412A mpF-⨯=⨯==计算缸筒内径D得按计算结果根据表3选择缸筒内径标准值。
表 3 液压缸内径和活塞杆直径标准系列(GB/T2348—1993) mm按标准取D = 90mm(壁厚5mm,单重m)根据快进和快退速度相等要求,拟定液压系统在快进时采用差动连接。
设活塞杆直径为d,于是有D2/(D2-d2) = d=按标准取 d = 45mm则液压缸的有效作用面积为:无杆腔的面积 A1=1/4 *π*D2 = 1/4*π*92=有杆腔的面积 A2=1/4 *π*(D2-d2) = 1/4*π* =(3 )活塞杆稳定性校核D=83mmA1=A2=mmmA83083.014159.31071.5444D4==⨯⨯==-π)dD(q4dq4222-π=π活塞杆稳定性校核流量计算压力计算功率计算活塞杆的总行程为400 mm , 而活塞杆的直径为45mm , l/d =400/45=<10∴不用稳定性校核(4)、计算液压缸流量、压力和功率1)流量计算2)压力计算3)功率计算4、绘制工况图不用稳定性校核MPaFMPaFMPaaAF13.0Pa1013.01069.4712.634Ap58.2Pa1058.21059.6394.16412Ap4.0P1040.010)69.4759.63(12.634Ap6426416421=⨯=⨯===⨯=⨯===⨯=⨯-=-=-----快退快退工进工进快进快进WWW4.4660104.211013.0qpP3.13360101.31058.2qpP7.476010155.7104.0qpP363636=⨯⨯⨯===⨯⨯⨯===⨯⨯⨯==---快退快退快退工进工进工进快进快进快进min/4.21/m105.3605.41059.47vAqmin/1.3/m103.5605.01059.63vAqmin/155.7/m1019.1605.410)69.4759.63(v)A(q3443235421344121LsLsLsA=⨯=⨯⨯===⨯=⨯⨯===⨯=⨯⨯-=-=------快退工进快进工况图工作循环中液压缸各阶段压力、流量和功率如表4所示。
由表绘制液压缸的工况图如图3所示。
图 3 液压缸的工况图t(s) p(MPa)q(L/min)t(s) P(W)t(s)快进工进快退设计内容计算说明结论选用执行元件确定供油方式调速方式选择三,液压系统设计、液压系统图的拟定1、选用执行元件由系统动作循环图,选定单活塞杆液压缸做为执行元件。
根据快进和快退速度相等的要求,拟定在快进时采用差动连接,因此应使无杆腔有效面积为有杆腔有效面积的两倍。
2、确定供油方式由工况图分析可知,液压缸在快进、快退时所需流量较大,但持续时间较短;而在工进时所需流量较小,但持续时间较长。
因此从提高系统效率,节省能源的角度考虑,系统供油方式不宜采用单个定量泵,而宜采用双泵或变量泵。
因此参考同类组合机床,选用双作用叶片泵双泵供油方式。
3、调速方式选择由工况图可知,快进和快退时有速度要求,因此在有杆腔油口处统一采用调速阀调速。
工进时速度低,考虑到系统负载变化小,所以采用调采用差动连接双作用叶片泵双泵供油调速阀进油节流调速速度换接选择换向方式选择速阀进油节流调速回路。
4、速度换接选择快进和工进之间速度需要换接,为便于对换接的位置进行适当的调整,因此采用二位二通行程阀来实现速度的换接。
另外采用液控顺序阀与单向阀来切断差动回路。
因此速度换接回路为行程与压力联合控制形式。
5、换向方式选择采用三位五通电磁阀进行换向,以满足系统对换向的各种要求。
选用三位阀的中位机能为M型,以实现可以随时在中途停止运动的要求。
为提高换向的位置要求,拟采用止挡块和压力继电器的行程终点返回控制。
6、其它选择为便于观察调整压力,在液压泵的出口处和液压缸的两接口处均设置测压点,并配置多点压力表开关,以便利用一个压力表即能观测各点压力。
完成以上各项选择后,作出拟定的液压系统原理图和各电磁铁的动作顺序表如图4所示。
回路。
行程与压力联合控制形式挡块和压力继电器的行程终点返回控制快进工进、液压系统的工作原理1、快进按下起动按钮,电磁铁1YA通电,电磁换向阀8的阀芯右移,换向阀工作在左位,实现快进,油路为:进油路:泵2→换向阀8左位→行程阀13下位→液压缸左腔;回油路:液压缸右腔→调速阀14 →换向阀8左位→单向阀9→行程阀13下位→液压缸左腔,形成差动连接。
2、工进当滑台快速运动到给定位置时,滑台上的撞块压下行程阀13阀芯,切断通道,使压力油经调速阀10进入液压缸左腔。
由于油液流经调速阀,系统压力上升,打开液控顺序阀7,此时单向阀9关闭,切断液压缸差动回路,实现工进,油路为:进油路:泵2→换向阀8左位→调速阀10→液压缸左腔;回油路:液压缸右腔→调速阀14 →换向阀8左位→顺序阀7→背压阀6 →油箱。
快退液压泵压力3、快退当滑台工进完毕之后,停留在止挡块处,系统压力升高,直到压力继电器12的调整值时,压力继电器动作,2YA通电,电磁换向阀8工作在右位,滑台快退返回。
快退油路为:进油路:泵2 →调速阀14 →换向阀8右位→液压缸右腔;回油路:液压缸左腔→单向阀11→换向阀8右位→油箱。
、液压元件的选择1、确定液压泵的型号及电动机功率1)计算液压泵压力估算压力损失经验数据:一般节流调速和管路简单的系统取∑△pl=~,有调速阀和管路较复杂的系统取∑△pl=~。
液压缸在整个工作循环中最大工作压力为,由于系统有调速阀,但管路简单,所以取压力损失∑△pl=,计算液压泵的工作压力为pp=p+∑△pl=+=选用电动机标准件油管油箱4)选用电动机拟选Y系列三相异步电动机,满载转速960r/min,按此计算液压泵实际输出流qp=(10+16)×10﹣3 ×960 ×=min计算所需电动机功率为由[3]第4卷P569选用Y132S-6电动机。
电动机额定功率为3KW,满载转速为960r/min。
2、选择阀类元件及辅助元件1)标准件根据系统的工作压力和通过各个阀类元件和辅助元件的流量,由产品目录确定这些元件的型号及规格如表5 所示。
2)非标件a)油管油管尺寸根据实际流量类比确定,采用内径为16mm,外径为20mm的紫铜管。
b)油箱油箱容积计算如下V=(5~7)qp=(5~7)×=~Y132S-6电动机内径为16mm,外径为20mmV=150WqpPpppp3361016.18.0601022.211063.2⨯=⨯⨯⨯⨯==-η压力损失验算取V=150L。
表5 液压元件型号及规格序号名称通过流量qmax(L/min) 型号及规格1 滤油器XU-C32×100B2 双联叶片泵YB1—10/163 溢流阀Y-10B4 单向阀I-25B5 顺序阀X-B25B6 溢流阀Y-10B7 顺序阀XB-25B8 三位五通电磁换向阀35D-25BM9 单向阀I-25B10 调速阀Q-25B11 单向阀I-25B12 压力继电器DP-25B13 二位二通行程阀22D-25B14 调速阀Q-25B15 压力表开关K-3B16 压力表Y-100T17 电动机Y132S-6四,验算性能完成设计、液压系统的性能验算1、压力损失验算按液压泵的实际输出流量估算压力损失。
1)油液在油管中的流速进油管流速v'回油管流速v"Ls/m52.510166041022.21Aqv'623p=⨯⨯⨯⨯==--s/m81.252.554.7806.40'vAAv"12=⨯==沿程压力损失△Pf回油沿程压力损失2)沿程压力损失△Pf设系统采用L-HM32液压油,室温为20℃时粘度为ν=×10﹣4 m2/sa)进油沿程压力损失△Pf1层流状态:λ1=75/Re1=75/552= 取油液的密度为ρ=890kg/m3,进、回油管长度均为2m,得进油沿程压力损失为b)回油沿程压力损失层流状态:λ2=75/Re2=75/281=c)总沿程压力损失2300552100.1101052.5'Re431<=⨯⨯⨯==--νdv层流状态:λ1=75/Re1=75/552=M Pa38.0Pa108.3252.58901010214.02'vdlp52321f1=⨯=⨯⨯⨯⨯=ρλ=∆-2300281100.1101081.2d"vRe432<=⨯⨯⨯=ν=--M Pa19.0Pa109.1281.28901010227.02"vdlp52322f2=⨯=⨯⨯⨯⨯=ρλ=∆-总沿程压力损失局部压力损失△Pr总压力损失∑△p调定压力的确定3)局部压力损失△Pr局部压力损失包括液压阀的压力损失及管道和管接头的压力损失。