电解铝预焙阳极炭块焙烧质量分析
浅谈影响预焙阳极质量的因素
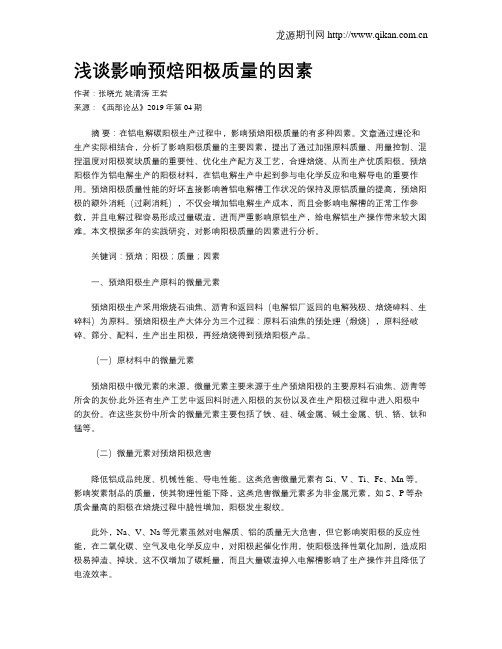
浅谈影响预焙阳极质量的因素作者:张晓光姚清涛王岩来源:《西部论丛》2019年第04期摘要:在铝电解碳阳极生产过程中,影响预焙阳极质量的有多种因素。
文章通过理论和生产实际相结合,分析了影响阳极质量的主要因素,提出了通过加强原料质量、用量控制、混捏温度对阳极炭块质量的重要性、优化生产配方及工艺,合理焙烧、从而生产优质阳极。
预焙阳极作为铝电解生产的阳极材料,在铝电解生产中起到参与电化学反应和电解导电的重要作用。
预焙阳极质量性能的好坏直接影响着铝电解槽工作状况的保持及原铝质量的提高,预焙阳极的额外消耗(过剩消耗),不仅会增加铝电解生产成本,而且会影响电解槽的正常工作参数,并且电解过程容易形成过量碳渣,进而严重影响原铝生产,给电解铝生产操作带来较大困难。
本文根据多年的实践研究,对影响阳极质量的因素进行分析。
关键词:预焙;阳极;质量;因素一、预焙阳极生产原料的微量元素预焙阳极生产采用煅烧石油焦、沥青和返回料(电解铝厂返回的电解残极、焙烧碎料、生碎料)为原料。
预焙阳极生产大体分为三个过程:原料石油焦的预处理(煅烧),原料经破碎、筛分、配料,生产出生阳极,再经焙烧得到预焙阳极产品。
(一)原材料中的微量元素预焙阳极中微元素的来源。
微量元素主要来源于生产预焙阳极的主要原料石油焦、沥青等所含的灰份.此外还有生产工艺中返回料时进入阳极的灰份以及在生产阳极过程中进入阳极中的灰份。
在这些灰份中所含的微量元素主要包括了铁、硅、碱金属、碱土金属、钒、铬、钛和锰等。
(二)微量元素对预焙阳极危害降低铝成品纯度、机械性能、导电性能。
这类危害微量元素有Si、V 、Ti、Fe、Mn等。
影响炭素制品的质量,使其物理性能下降,这类危害微量元素多为非金属元素,如S、P等杂质含量高的阳极在焙烧过程中脆性增加,阳极发生裂纹。
此外,Na、V、Na等元素虽然对电解质、铝的质量无大危害,但它影响炭阳极的反应性能,在二氧化碳、空气及电化学反应中,对阳极起催化作用,使阳极选择性氧化加剧,造成阳极易掉渣、掉块。
电解铝预焙阳极炭块焙烧质量分析(5篇模版)

电解铝预焙阳极炭块焙烧质量分析(5篇模版)第一篇:电解铝预焙阳极炭块焙烧质量分析电解铝预焙阳极炭块焙烧质量分析一、前言我公司焙烧有54炉室和18炉室两个生产系统,焙烧炉是敞开式、w型环式炉,分别采用煤气和重油做燃料进行加热升温。
54室焙烧炉结构为8火道7料箱,料箱尺寸为:3440×730×4170mm,每炉平装生块84块,有三个火焰系统每个火焰系统为18个炉室。
18室焙烧炉结构为9火道8料箱,料箱尺寸为:5330×703×5240mm,每炉立装生块192块,一个火焰系统。
两系统年生产能力达到8万吨。
二、制定合理的升温曲线焙烧是炭素制品生产中的一个重要工序,生坯炭块的焙烧是生坯炭块在专门设计的加热炉内周围用填充料隔绝空气,按一定升温速度将生坯加热到1000℃---1050℃左右的生产工序。
在焙烧过程中生坯炭块主要是进行粘结剂的分解和聚合反应。
焙烧的升温速度、温度梯度及最高温度对阳极质量都有很大影响。
生坯炭块在焙烧过程中主要是粘结剂的焦化过程,即是沥青进行分解、环化、芳构化和缩聚等反应的综合过程。
具体生坯炭块在焙烧炉内焦化过程与温度加热变化如下表。
我公司根据生坯炭块在焙烧炉内焦化的过程及54室焙烧炉室、18室焙烧炉室的结构和煤气、重油的热值计算,分别对54室焙烧炉室和18室焙烧炉室采用了252小时和168小时的加热炭块升温曲线的生产过程。
移炉周期分别采用36小时和28小时。
低温预热阶段200℃左右制品粘结剂开始软化中温阶段200℃--300℃制品内吸附的水和化合水以及低分子烷烃被排出。
400℃以上变化最为突出500℃--650℃ 碳环聚合形成半焦高温烧结阶段700℃以上半焦结构分解,逐渐形成焦炭,构成乱层堆积结构基本单位的六角网状平面。
900℃以上这种二维排列的碳原子网格进一步脱氢和收缩,以后就变成了沥青焦。
燃料生产大规格炭块和炭块平装的生产要求,及用重油作为燃料生产大规格炭块和炭块立装的生产要求,该曲线容易操作又安全,尤其在排出挥发份阶段,排出的挥发份不但能充分燃烧,焦化反映比较彻底,而且对低温炉室起到一个很好的预热作用,使系热得到合理利用,烟气进入烟斗后温度平均为200 ℃,到净化系统温度在60℃--130℃,达到技术要求,有利于净化系统对烟气的净化与排放。
用反应性指标评定阳极的质量-文档

用反应性指标评定阳极的质量1问题的提出在预焙槽铝电解生产中,预焙阳极浸入高温和具有很强腐蚀反应而不断连续的消耗。
再加上工艺残极,阳极单耗往往较理论值高出50%- 75%即500〜580kg/t-AL。
为了摆脱阳极消耗带来性的冰晶石熔盐中。
炭阳极不仅起导电作用,同时也参与电化学的一系列问题,国外已研发了多种不消耗的阳极,但在现阶段,还未在工业电解槽上大规模使用,因而,提高炭阳极的质量,仍然是降低吨铝的成本,改善电解操作过程,提高原铝液的质量,提高电流效率的方法之一。
从理论上讲,生产每吨铝所消耗的炭阳极最低消耗量是333kg/t-AL 。
按照每安培时电量的和算的实际的炭耗量对理论耗量的比值,称为炭耗指数。
对自焙阳极而言为1.83%〜2.00%之间,预焙阳极而言为1.73〜7.93 之间,阳极消耗的机理和原因是多方面的,主要是氧化铝电解还原作用从阳极的底部释放的氧和阳极材料之间的电化学反应,阳极的空气氧化和布达反应引起的;同时由于阳极的粘结剂沥青的焦碳在电解槽中使用时的选择氧化造成,最终造成阳极的骨料颗粒的氧化脱落造成阳极的过量消耗等。
2预焙阳极在电解槽中的消耗分析在冰晶石一氧化铝熔盐电解池中,预焙阳极用于电解槽有两方面的作用: 第一,它作为电极使用,把电流导入炉膛。
第二,参与氧化铝电解的电化学反应过程,电解时离析出氧,氧与炭阳极直接发生化学反应,并以C02和CO的形式从电解槽中排除,其总的反应式如下。
AL2O3+3/(1+N)C=2AL+3N/(1+N)CO2+3(1-N)/(1+N)CO式中N为CO2%体积百分比);1-N为CO%体积百分比)。
对电解槽气体的研究证明,铝电解的一次气体是CO2 CO是由一次气体C02与熔在电解液中的C反应生成。
通过上式计算,所以每吨铝消耗的阳极的质量为333kg/t-AL 。
实际上在电解的生产中净消耗的阳极一般为420-450kg/t-AL ,含残极,即俗称毛耗”一般为500-580kg/t-AL 。
电解铝预焙阳极质量对电解铝生产的影响及分析

电解铝预焙阳极质量对电解铝生产的影响及分析摘要:在电解铝的生产中,电解铝预焙阳极质量起到了重要的影响,好的阳极质量有助于电解铝的生产,增强电解效果,相反质量不达标则会带来阳极脱落、松散等问题。
因此,要加强对阳极质量的重视,做好质量监控工作,避免带来生产安全问题。
本文从阳极质量对电解铝生产的影响出发,探讨了如何更好地提升阳极的质量,带动电解铝的高质量生产,助力电解铝行业的发展。
关键词:电解铝;预焙阳极;影响在电解铝生产中,预焙阳极在铝电解槽中是极其重要的部分。
阳极的质量直接影响到了日常的电解铝生产,对铝液质量以及其它各项技术指标有着重要的影响。
因此,要高度重视阳极质量的控制工作,贯穿到电解铝生产的整个过程中去。
基于生产成本的考虑,要注重生产的经济性,要持续创新预焙阳极的生产,促进阳极质量的提升,从而整体提升电解铝的生产效益。
一、阳极质量的重要影响预焙阳极在电解铝的生产中,有着重要的影响,工作人员在生产过程中,要及时地更换阳极炭块,防止出现阳极质量问题。
阳极质量出现问题,容易带来电解质出现裂纹、阳极氧化等问题,不利于电解铝的安全稳定生产,具体来说,有以下几个方面。
(一)对原铝质量的影响在阳极质量不过关的情况下,原铝的消耗量会大大得以增加,在更换阳极的时期,就可能带来原铝脱极、化爪等问题,严重的情况,还会带来铝液铁质量增加的问题,直接影响到原铝的使用需求。
(二)对电解槽温度影响预焙阳极也会影响到电解槽的温度,如果电阻率缺乏可靠性和稳定性,在阳极电流不断增加的情况下,阳极电压容易发生改变,偏离正常值,进一步抬升电解槽的电压。
从而产生更多的热量,热量的激增容易带来电解质的其他参数的改变,出现阳极掉块和脱落等问题。
在出现这些情况的时候,就要及时地清理电解槽,增加电解槽内部的沉淀物。
然而,沉淀物的不断增加又导致了炉底返热的问题,大大增加了电解质的温度,如此一来,就形成了一个恶性循环。
此外,阳极炭渣过多,也会持续增加炭渣层的厚度,在角部形成大量的残留物,容易带来阳极附近电流出现短路等问题,影响生产的开展。
阳极组装工序对预焙阳极质量影响及控制措施探讨
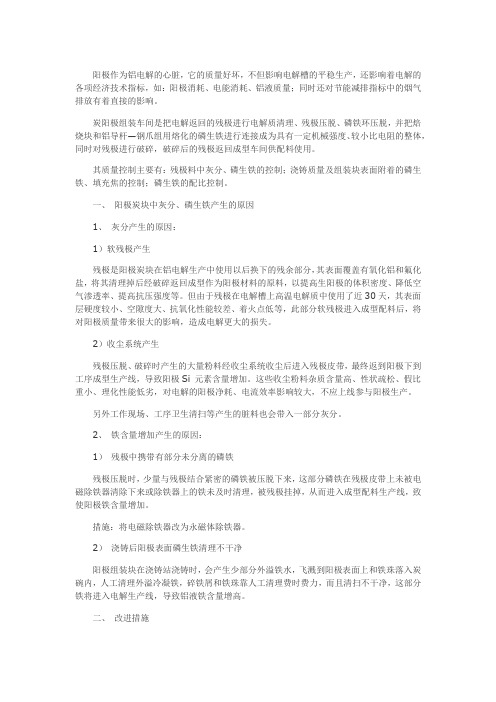
阳极作为铝电解的心脏,它的质量好坏,不但影响电解槽的平稳生产,还影响着电解的各项经济技术指标,如:阳极消耗、电能消耗、铝液质量;同时还对节能减排指标中的烟气排放有着直接的影响。
炭阳极组装车间是把电解返回的残极进行电解质清理、残极压脱、磷铁环压脱,并把焙烧块和铝导杆—钢爪组用熔化的磷生铁进行连接成为具有一定机械强度、较小比电阻的整体,同时对残极进行破碎,破碎后的残极返回成型车间供配料使用。
其质量控制主要有:残极料中灰分、磷生铁的控制;浇铸质量及组装块表面附着的磷生铁、填充焦的控制;磷生铁的配比控制。
一、阳极炭块中灰分、磷生铁产生的原因1、灰分产生的原因:1)软残极产生残极是阳极炭块在铝电解生产中使用以后换下的残余部分,其表面覆盖有氧化铝和氟化盐,将其清理掉后经破碎返回成型作为阳极材料的原料,以提高生阳极的体积密度、降低空气渗透率、提高抗压强度等。
但由于残极在电解槽上高温电解质中使用了近30天,其表面层硬度较小、空隙度大、抗氧化性能较差、着火点低等,此部分软残极进入成型配料后,将对阳极质量带来很大的影响,造成电解更大的损失。
2)收尘系统产生残极压脱、破碎时产生的大量粉料经收尘系统收尘后进入残极皮带,最终返到阳极下到工序成型生产线,导致阳极Si 元素含量增加。
这些收尘粉料杂质含量高、性状疏松、假比重小、理化性能低劣,对电解的阳极净耗、电流效率影响较大,不应上线参与阳极生产。
另外工作现场、工序卫生清扫等产生的脏料也会带入一部分灰分。
2、铁含量增加产生的原因:1)残极中携带有部分未分离的磷铁残极压脱时,少量与残极结合紧密的磷铁被压脱下来,这部分磷铁在残极皮带上未被电磁除铁器清除下来或除铁器上的铁未及时清理,被残极挂掉,从而进入成型配料生产线,致使阳极铁含量增加。
措施:将电磁除铁器改为永磁体除铁器。
2)浇铸后阳极表面磷生铁清理不干净阳极组装块在浇铸站浇铸时,会产生少部分外溢铁水,飞溅到阳极表面上和铁珠落入炭碗内,人工清理外溢冷凝铁,碎铁屑和铁珠靠人工清理费时费力,而且清扫不干净,这部分铁将进入电解生产线,导致铝液铁含量增高。
电解铝预焙阳极质量差危害及应对措施研究

电解铝预焙阳极质量差危害及应对措施研究摘要:在实际电解铝的生产过程中,预焙阳极质量对整个操作过程起着至关重要的作用。
通过大量的实践经验,我们发现出现阳极脱落以及阳极裂纹、断层以及阳极松散现象的主要原因是由于预焙阳极的质量差。
因而这对实际开展质量监管的人员提出更高的要求。
本文主要从预焙阳极的作用以及提升预焙阳极质量措施两方面进行论述,旨在为相关的工作人员以及研究人员提供切实可行的建议,促进电解铝行业的良性和可持续发展。
关键词:电解铝预焙阳极;质量差危害;应对措施众所周知,近些年我国的经济得到迅猛发展,但是由于经济的粗放式发展,导致一些行业在生产过程中依旧存在浪费的状况。
在本文电解铝过程中,假如不能很好地控制预焙阳极的质量,不仅会出现生产浪费的状况,更会影响整个电解过程的高效进行,还会对铝液的质量造成极大的危害。
究其原因是因为铝电解槽是进行电解的主要场所,而预焙阳极是主要参与电解反应的主体之一。
一、电解铝预焙阳极质量差的危害(1)增大铝资源的消耗量在实际的电解铝过程中,假如预焙阳极质量不达标,会增大原铝溶液的使用速度。
究其原因是因为预焙阳极质量不达标,会影响整体的电解效率,即在阳极的部分会出现化爪,甚至是脱级的现象,从而进一步增强铝液中铁的含量,进而导致整体的电解不充分,因而存在大量铝原液浪费的现象。
(2)提升电解质温度,降低电流工作效率通过具体的实践,我们发现假如在电解质中含有0.04%炭渣,则对应的电解质的导电性会降低1%,当有1%时,则对应的电解质的导电性会降低11%。
假如在电解质中的碳渣含量逐渐增加,则电解质的阻值也会相应增大,从而影响整个电解过程中的高效进行。
预焙阳极的质量差,会在电解反应的过程中,出现掉渣的现象,假如掉渣现象严重,则会进一步造成电解溶液的阻值过大,从而影响整体的电解质量的提升。
与此同时,因为残渣的出现,会造成整个电解液阻值增大,进而依据“电可制热的原理”,从而会让整个电解液的温度上升,再次提升整个电解液的阻值,进而形成恶性循环,阻碍电解效率的提升。
预焙阳极 电解铝
预焙阳极电解铝预焙阳极电解铝是一种常见的铝生产工艺,它在铝电解过程中起到了重要的作用。
预焙阳极电解铝的制备过程相对简单,但其在铝生产中的应用却十分广泛。
让我们来了解一下预焙阳极电解铝的基本原理。
预焙阳极电解铝是指在铝电解槽中,通过预先烧结的阳极来进行铝电解的过程。
在这个过程中,阳极的主要作用是提供氧化反应所需的氧气,并参与到铝的电解过程中。
通过预焙阳极电解铝,可以实现铝的高效生产,提高生产效率和质量。
预焙阳极电解铝的制备过程包括以下几个步骤。
首先,选取合适的原料进行配制。
一般来说,预焙阳极电解铝的原料主要包括铝土矿、焦炭和煤焦矸石等。
这些原料需要经过破碎、混合和筛分等工艺进行预处理,以保证原料的质量和配比的准确性。
接下来,将经过预处理的原料送入焙烧炉进行焙烧。
焙烧的目的是使原料中的有机物和水分等挥发出来,同时进行物理和化学变化,使原料在高温下形成焙烧块。
焙烧的温度和时间需要根据原料的性质和要求进行控制,以保证焙烧块的质量和活度。
焙烧后的阳极块需要进行破碎和筛分,以获得符合要求的颗粒度。
然后,将颗粒状的阳极块送入铝电解槽中,作为阳极进行铝电解。
在电解过程中,阳极的氧化反应释放出氧气,并与铝离子结合生成铝金属。
同时,阳极也会随着电解过程的进行逐渐耗损,产生阳极泥。
为了保证电解的稳定进行,需要定期更换阳极。
通常情况下,预焙阳极电解铝的阳极寿命可以达到几个月甚至更长。
一旦阳极耗损到一定程度,就需要停机更换阳极,以保证铝的正常生产。
预焙阳极电解铝的应用范围非常广泛。
这种工艺可以用于生产各种铝及铝合金产品,如铝板、铝卷、铝材等。
预焙阳极电解铝具有生产效率高、能耗低、产品质量好等优点,因此被广泛应用于铝工业。
预焙阳极电解铝是一种重要的铝生产工艺,通过预先烧结的阳极来进行铝电解,可以实现铝的高效生产。
预焙阳极电解铝的制备过程相对简单,但其在铝生产中的应用却十分广泛。
预焙阳极电解铝不仅提高了铝的生产效率和质量,也为铝工业的发展做出了重要贡献。
电解铝预焙阳极质量对电解铝生产的影响及分析
电解铝预焙阳极质量对电解铝生产的影响及分析摘要:预焙阳极质量的优劣直接会影响到电解铝的生产情况和电解效果,如果预焙阳极质量不达标,还会产生阳极裂纹、松散、断层、高灰份以及阳极脱落等问题。
只有全面做好电解铝预焙阳极质量的监控工作,才能有效预防意外情况的发生。
本文主要分析预焙阳极质量对铝电解生产产生的影响,并对其相应的应对措施进行了探讨,以期提高电解铝预焙阳极质量,进而促进我国电解铝生产行业的可持续发展。
关键词:电解铝预焙阳极质量;电解铝生产;影响在生产铝电解的过程中,预焙阳极占据着铝电解槽的核心位置。
同时,预焙阳极质量控制工作始终贯穿于整个生产及使用的过程中。
因此,预焙阳极质量的好坏不仅会影响到正常的电解生产活动,而且也会对电解各项重要经济技术指标以及铝液质量等产生负面影响。
由于我国当前的经济状况及各种资源比较紧张,科学合理地优化预焙阳极的生产工艺,提高预焙阳极的质量,具有重要的经济和现实意义。
一、电解铝预焙阳极质量对电解铝生产的主要影响在生产电解铝的过程中,相关工作人员需要定期更新阳极炭块。
一旦预焙阳极的质量出现问题较多,电解质中便会出现掉渣、掉块、裂纹以及阳极氧化等缺陷,进而给电解铝的生产带来不利的影响,主要影响包括以下几个方面。
1.影响原铝的质量在阳极质量存在不达标的情况下,阳极消耗的速度就会变快。
因此,在换极周期内,阳极便可能会出现脱极、化爪,甚至直接增加铝液中铁含量的问题,最终影响到铝资源的使用需求。
2.影响电解槽的温度如果预焙阳极的电阻率缺少了相应的稳定性,一旦出现持续增加阳极电流的情况,便会改变阳极电压的正常值,进而升高电解槽的电压。
电压升高后自然会产生热量,产生的热量会导致电解质中的其他参数发生变化,比如,阳极出现掉块、裂纹或者是脱落的现象。
一旦发生上述问题,便需要不断地对电解槽进行清理,进而使槽底的沉淀物不断增加。
这样一来,便会形成恶性循环,沉淀物的不断积累又会使炉底出现返热的现象,进一步升高电解质的温度。
铝电解槽应用优质阳极炭块的技术经济分析与评价
铝电解槽应用优质阳极炭块的技术经济分析与评价摘要∶该文主要从铝电解式生产中的阳极损耗、电耗、阳级破坏性故障降低,以及强化输出电压活力等方面和阳级特性的有关问题亲入手,统计并剖析了铝电解槽用优良阳极和普通阳极以及品质较差的阳极之间的区别,并阐述了判别方式,作者认为若使用优良的阳极,吨铝生产成本可降低约三百多元人民币。
关键词:铝电解槽;优质阳极炭块;技术分析一、引言有些铝厂在购进阳极时,谁便宜买了谁的,使中国对高品质阳极的制造遇到了困难。
在铝电解槽产品中,采用质量高品质产品的价格相对较高,还是采用品质一般或质量稍差但产品价格相对低廉的阳极炭块较好呢?两者在铝电解槽应用过程中究竟有多大区别,本文将力图从科技与经济效益上解析和评价这一问题[1]。
二、铝电解槽应用优质阳极炭块的问题近年来,中国国内的阳极炭块交易市场逐渐转向了买方市场,由于产品供应过剩,产品价格一路下降。
在太阳阳极生产原料石油焦和煤沥青料涨价达到40%的情形下,阳级炭块产品为3560-1950元上下。
于是某些炭素厂大打价钱战,用不计成本的低廉产品求得占有行业市场一席之地。
产品价格低,无利润空间,只好用低价质量差的原料和“带病”的设备、落后的工艺以求减少亏损。
只要严密地根据ISO国际标准的十多项技术指标(包含物化特性,应用特性和微量元件)检查是能够辨别优良阳级的。
但由于当前中国国内太阳能炭块产品质量规范,仍是最常见的“硬度”、“阻值率”、“灰分”、“真密度系数”和“体积密度系数”等几个主要技术指标,而大多数厂家对阳级炭块的热学技术应用性能指标以及各种微量元件都还没有测定,所以对太阳能极炭块的质量优良与否,主要是靠在电解槽上的实际使用效果来辨别。
但这种区别时效性较慢,加之很多铝厂都无法保证同一个电解槽上只有同一家厂家出产的炭块,而不同厂家出产的炭块又要分槽利用,所以鱼目混珠,优劣难分。
三、铝电解槽阳极节电计算阳极炭块阻力率通常在52~68μ。
根据焙烧高温、原料品质、阳极制作工艺技术条件等影响阳极电阻率。
预焙铝电解槽焙烧质量及焙烧启动新工艺探讨
不对 内衬产生很大的气体压力。再者 ,为实现大幅度
延 长槽 龄 的 目的而 消 耗部 分 焙烧 所 用 的必 要 电能是 完 全值 得 的 。
22 焙 烧温 度的 选择 .
焙 烧 温 度 与 焙 烧 速 度 应 相 辅 相 成 。 理 想 的 情 况 是 ,焙 烧 最终 温度 应 接 近 电解 质熔 体 的温度 ,以减 少 内衬 产 生 的热 冲击 。但 是 ,在 保证 焙 烧 时 间充 分 、温 度 梯度 分 布均 匀 的情 况 下 ,电解槽 焙 烧最 终 温 度 可略 低 于 电解 质温 度 。根 据 文献 … ,焦粒 焙烧 过程 中阴极
解过 程 中产 生 的挥 发 分 能够 缓 慢地 从 内衬 中排 除 ,而
行 传 热 ,加热 速 度快 ,温 度分 布 均 匀 。 同时 ,阳极 上 覆 盖 的是 氧化 铝 保 温料 而 不是 冰 晶 石 ,从 而减 少 了换 极 时 带 出大量 氟 盐 。而 且 在启 动 时 液体 电解 质 容 易从 阳极 缝 之 间顺 畅地 流到 槽 膛 内各 部 位 ,上 抬 阳极 时 不
42 启 动 时槽 电压 .
约 占最终 正 常生 产时铝 量 的 5%l 0 2 】 。
启 动 时槽 电压不 宜 过低 ,是 为 了补 充 阳极 的散热 量 。当 电解质 注 入 到 电解 槽 中之 后 ,将 槽 电压 提 高 到 2 V发 生 效 应 ,但 持 续 时 间应 控 制 在 4 rn 0 0 i,因 为 时 a 间过 长产 生 的剧 烈 高温 和振 动 会 导致 阳极 碎裂 或 内衬
槽况 稳定 。
焦 粒 粒 度 选 择 1~ m 3 m,其 中添加 较 小 的人 造 石
墨颗粒 ,能降低焦粒 配料 的电阻… 。某 铝业公 司采用 胶 木板 做 成 的筛 网代 替 铝合 金 铺设 框 架 ,铺 设 时 筛 网
- 1、下载文档前请自行甄别文档内容的完整性,平台不提供额外的编辑、内容补充、找答案等附加服务。
- 2、"仅部分预览"的文档,不可在线预览部分如存在完整性等问题,可反馈申请退款(可完整预览的文档不适用该条件!)。
- 3、如文档侵犯您的权益,请联系客服反馈,我们会尽快为您处理(人工客服工作时间:9:00-18:30)。
电解铝预焙阳极炭块焙烧质量分析
一、前言
我公司焙烧有54炉室和18炉室两个生产系统,焙烧炉是敞开式、w型环式炉,分别采用煤气和重油做燃料进行加热升温。
54室焙烧炉结构为8火道7料箱,料箱尺寸为:3440×730×4170mm,每炉平装生块84块,有三个火焰系统每个火焰系统为18个炉室。
18室焙烧炉结构为9火道8料箱,料箱尺寸为:5330×703×5240mm,每炉立装生块192块,一个火焰系统。
两系统年生产能力达到8万吨。
二、制定合理的升温曲线
焙烧是炭素制品生产中的一个重要工序,生坯炭块的焙烧是生坯炭块在专门设计的加热炉内周围用填充料隔绝空气,按一定升温速度将生坯加热到1000℃---1050℃左右的生产工序。
在焙烧过程中生坯炭块主要是进行粘结剂的分解和聚合反应。
焙烧的升温速度、温度梯度及最高温度对阳极质量都有很大影响。
生坯炭块在焙烧过程中主要是粘结剂的焦化过程,即是沥青进行分解、环化、芳构化和缩聚等反应的综合过程。
具体生坯炭块在焙烧炉内焦化过程与温度加热变化如下表。
我公司根据生坯炭块在焙烧炉内焦化的过程及54室焙烧炉室、18室焙烧炉室的结构和煤气、重油的热值计算,分别对54室焙烧炉室和18室焙烧炉室采用了252小时和168小时的加热炭块升温曲线的生产过程。
移炉周期分别采用36小时和28小时。
低温预热阶段
200℃左右
制品粘结剂开始软化
中温阶段
200℃--300℃
制品内吸附的水和化合水以及低分子烷烃被排出。
400℃
以上变化最为突出 500℃--650℃
碳环聚合形成半焦
高温烧结阶段
700℃以上
半焦结构分解,逐渐形成焦炭,构成乱层堆积结构基本单位的六角网状平面。
900℃以上
这种二维排列的碳原子网格进一步脱氢和收缩,以后就变成了沥青焦。
燃料生产大规格炭块和炭块平装的生产要求,及用重油作为燃料生产大规格炭块和炭块立装的生产要求,该曲线容易操作又安全,尤其在排出挥发份阶段,排出的挥发份不但能充分燃烧,焦化反映比较彻底,而且对低温炉室起到一个很好的预热作用,使系热得到合理利用,烟气进入烟斗后温度平均为200 ℃,到净化系统温度在60℃--130℃,达到技术要求,有利于净化系统对烟气的净化与排放。
从产品质量取样结果分析看,理化指标和外观质量都比较好,故我公司54室焙烧炉室采用252小时加热升温曲线,18室焙烧炉室采用168小时加热升温曲线是合理的。
三、炭块变形破损原因分析及解决
生炭块经过焙烧后出下列几种废品
1.立装炭块炭碗塌陷变形 18室焙烧炉室立装炭块经焙烧后炭碗塌陷变形,导致阳极导杆不能安装。
其原因:
1.1立装炭块在炉室内填充料不能将炭碗填实, 炭碗内有空隙。
在焙烧炭块过程中制品处在软化阶段时,由于炭碗内有空隙炭碗处制品塌陷引起变形,造成废品。
1.2生炭块粘结剂用量偏高。
1.3振动成型压力较低。
我公司现使用纸板将装满填充料的炭碗先固定后再装炉。
具体是先将填充料填满炭碗,再用根据炭碗结构尺寸制作的纸板将炭碗内的填充料固定,使立装起的炭块炭碗内被填充料填实,在焙烧过程中炭块炭碗内没有空隙就避免了炭块炭碗的变形。
2.炭块表面出现裂纹
2.1横裂:横裂是沿制品方向产生的裂纹,主要是生炭块质量偏低所引起,其原
因:
2.1.1原料煅烧温度过低,炭质原料得不到充分收缩,挥发分不能完全排除,原料理化性能达不到稳定。
在焙烧进程中骨料颗粒产生大的二次收缩,则可能在炭块表面出现不规则的裂纹(网状)。
2.1.2振动成型进糊料温度低,振动时间不够。
2.1.3前后糊料的差别较大且结合不好,振动成型时造成生炭块内部结构有缺陷,虽然
炭块表面未出现问题,但在焙烧时容易出现横裂。
2.1.4粘结剂用量偏少。
2.1.5升温过快。
火道上,下温差大,相邻两条火道温差大,也能造成制品横裂。
2.2纵裂
2.2.1生块装炉时,靠火道墙太近,导致炭块局部升温过快,生块局部表面的挥发份分解速度过快,使生炭块产生不均匀膨胀和收缩,造成炭块纵裂。
2.2.2升温曲线的制定不合理,挥发份大量排出阶段升温速度过快,造成产品内部与表面温差过大,炭块表面已烧结而内部还在继续排出挥发份而引起炭块表层产生裂纹。
2.2.3冷却阶段降温速度过快,炭块表层现内部收缩不一致也会产生裂纹。
上述几种情况外生炭块在振动成型时,配料不合理,粘结剂用量偏少,生炭块内部结构有缺陷,则在焙烧中产生纵裂的可能性大大增加。
粘结剂用量偏多时, 振动成型压力较低,生坯在焙烧过程中的体积收缩以及生坯内粘结剂的迁移从而也使焙烧废品产生.
2.3变形
2.3.1加热速度缓慢,促成了制品沿直径方向过大的膨胀,制品沿长度方向下沉导致变形.
2.3.2振动成型时出现变形块(高低块)
2.3.3焙烧天车工装炉操作不当,层间料不平,炭块底部局部缺料,焙烧后造成炭块变形。
2.3.4填充料含有水分,大小粒度不一,填充不实炭块四周有局部空区,焙烧时造成炭块变形。
2.3.5炉室状况不佳,料箱破损严重,也能造成炭块变形。
2.4氧化
2.4.1装炉时填充料没有填实或焙烧中发生局部填充料下陷,致使炭块局部暴露,造成氧化。
2.4.2装炉时炭块靠火道墙,焙烧后造成氧化。
2.4.3出炉时温度高(出红块)造成表面氧化。
2.4.4出炉时时间未到就吸出料箱内填充料,也会造成炭块表面氧化。
2.4.5火道墙有裂纹,燃料(煤气)进入料箱接触炭块将炭块烧损。
2.5 缺陷
2.5.1振动成型后炭块表面搭配不合理,在焙烧过程中能造成缺陷块。
2.5.2机械损伤,由于操作者操作不当,下夹具时没有对正,在装出炉时,库房摆块时,夹具将炭块切掉一块。
生炭块在焙烧过程中,由于生产技术水平的差异,操作者的责任心的高低,炉室火道的破损、变形、负压的影响,焙烧实际生温曲线偏离设计曲线,保温时间和冷却时间不够,各火道间有温差、火道内上、下有温差,对阳极炭块的质量也都有较大的影响。
四、提高焙烧炭块的质量途径
1.要在原料进口把住石油焦的质量并提高煅后焦的质量。
2.成型要有优质的生炭块来保证焙烧工序的正常运行与生产。
3.焙烧根据炉室结构和加热燃料的热值制定出合理的焙烧升温曲线和冷却曲线。
4.在焙烧的各升温阶段过程中,必须严格执行升温曲线的技术标准。
5.进行岗位技能培训,提高工人的技术水平和操作水平。
避免由于操作引起外观的损坏及变形块。
五、结语
实践证明,焙烧出合格的炭块首先要在原料上把质量关。
煅烧严格执行工艺,确保煅烧的温度,煅烧过程中充分排除原料中的水分和挥发分,改善原料的导电性能,提高原料的密度、机械强度、抗氧化性能。
成型中控制干料干混温度,控制湖料混涅温度,混涅时间,控制粘结剂用量,控制成型压力、温度、振动时间。
焙烧制定好升温曲线,严格升温速度进行加热,精心装出炉作业。
生产出合格的阳极炭块。