PCBA(SMT)外观检验判定标准1
PCBA(SMT)外观检验判定标准1

少锡(SOP、QFP)
元件焊锡量未达到正常要求
判定标准:
1.最小末端焊点宽度C小于引脚宽度W的50%
2.最小侧面焊点长度D小于引脚长度50%
3.最小跟部焊接高度F小于焊接厚度G加连接处的引脚厚度T的50%
以上任一情況拒收
少锡(QFN类元件)
元件焊锡量未达到正常要求
判定标准:
1.城堡类QFN最小焊点高度F未达到焊锡高度H的50%
PCB掉铜箔
PCB铜箔有掉落现象
判定标准:
所有功能位掉铜箔不良均判拒收
SIM卡座坏
SIM卡座有金手指翘起、脫落、或弹片变形脫落等现象
判定标准:
有金手指翘起、脫落、或弹片变形脫落等任一情況的拒收
元件烫伤
影响外形、装配和功能变形、缺口、刮削、刻痕或熔毀现象
判定标准:
裂痕或其它变形影响了机械性质的完整均判拒收
2.电池座/USB/卡座/天线弹片偏移超出焊接端或焊盘的25%或存在角度偏差
以上有任一情況均判拒收
少件
BOM要求進行元件贴装的位置无元件
判定标准:
所有少件均判拒收
少锡(片式元件)
元件焊锡量未达到正常要求
判定标准:
1.片式元件末端焊点宽度C未达到元件可焊端宽度W的50%,或焊盘宽度的50%
2.最小焊接高度F未达到焊锡厚度G加可焊端高度H25%.
2.元件末端偏移
以上有任一情況均判拒收
浮高
元器件与PCB存在间隙或高度超过0.3mm。
判定标准:
目视或用塞规量测超过0.2 mm的拒收
偏位(IC/卡座/USB/电池座)
元件贴装位置未和焊盘或丝印重合,有偏移
判定标准:
1.圆柱体、扁平、L形和翼型引脚的SOP、QFP、QFN侧面偏移大于引脚焊接宽度的25%
PCBA外观检查标准范文

PCBA外观检查标准范文一﹑适用范围﹕本规范适用于所有PCBA的外观检查.二﹑检验条件与工具:1﹑检验须在距60W灯光下1m处进行,SMT元件须在3-5倍的放大镜下检查.2﹑检验时必须注意静电防护﹐如戴防静电手套或防静电手环等。
3﹑置于眼前30CM处,旋转45º,停滞3秒仍无法确认的轻微缺陷,不被视为不良点。
三﹑名词解释﹕1﹑严重缺点(以CR表示)﹕凡足以对人体或机器产生伤害﹐或危及生命财产安全的缺点﹐谓之严重缺点﹐任何一个严重缺点均将导致整批的批退。
2﹑主要缺点(以MA表示)﹕可能造成产品损坏﹑功能NG,或影响材料﹑产品使用寿命,或使用者需要额外加工的﹐定义为主缺。
严重的外观不良, 标签错误,漏执行ECN,混板等引起客户强烈反感的缺陷也定义为主缺。
3﹑次要缺点(以MI表示)﹕不影响产品功能﹑使用寿命的缺点﹐泛指一般外观或机构组装上的轻微不良或差异, 定义为次要缺点.四﹑参考文件﹕IPC-A-610C五﹑内容﹕1﹑SMT产品检验标准﹕SMT常见之不良现象有:1.1 短路﹕指两独立相邻焊点之间﹐在焊锡之后形成接合之现象﹐其发生之原因为焊点距离过近﹑零件排列设计不当﹑焊锡方向不正确﹑焊锡速度过快﹑助焊剂涂布不足及零件焊锡性不良﹑锡膏涂布不佳﹑锡膏量过多等。
(MA)1.2 空焊﹕锡堑上未沾锡﹐未将零件及基板焊接在一起﹐此情形发生之原因有焊堑不洁﹑脚高翘﹑零件焊锡性差,零件位侈,点胶作业不当﹐以致溢胶于焊堑上等﹐均会造成空焊。
空焊的零件PAD多呈光亮圆滑形.(MA)1.3 假焊﹕零件脚与焊堑间沾有锡﹐但实际上没有被锡完全接住。
多半原因为焊点中含有松香或是造成。
(MA)1.4 冷焊﹕亦称未溶锡﹔因流焊温度不足或流焊时间过短而造成﹐如此一缺点可藉二次流焊改善,冷焊点的锡膏表层暗黑,,大多呈有粉末状。
(MA)1.5 零件脱落﹕锡焊作业之后﹐零件不在应有的位置上﹐其发生之原因有胶材选择或点胶作业不当﹐胶材熟化作业不完全﹐锡波过高且锡焊速度过慢等。
PCBASMT外观检验判定标准

PCBASMT外观检验判定标准外观检验在PCBASMT(Printed Circuit Board Assembly and Surface Mount Technology)制造过程中起着至关重要的作用。
外观检验是为了确保PCBASMT产品的质量和性能符合预期,同时也是保证产品外观美观无瑕疵的重要环节。
本文将介绍PCBASMT外观检验的判定标准,帮助读者更好地了解和应用这一标准。
一、PCBASMT外观检验的重要性PCBASMT外观检验是在PCBASMT生产流程中进行的一项质量控制措施。
通过外观检验,可以确保组装过程中没有缺陷和损伤,保证产品的功能和性能正常。
外观检验还可以及时发现和纠正潜在的质量问题,避免不必要的成本和资源浪费。
二、PCBASMT外观检验的判定标准1. 表面质量PCBASMT产品的表面应当平整光滑,无明显的凹凸、磨损或划痕。
表面应呈现出一致的光泽度和颜色,不应有明显的色差或变色现象。
2. 焊接质量焊接是PCBASMT中的重要步骤,焊接质量直接关系到产品的可靠性和性能。
焊接点应当均匀、牢固,焊接接触面应无气泡、空洞或裂纹。
焊点应与电路板表面保持平齐,不应有高于或低于表面的情况。
3. 印刷质量PCBASMT中的印刷是将导电材料印在电路板上的过程。
印刷质量的好坏直接影响到电路板的导电性和可靠性。
印刷应当均匀、覆盖面积大,无虚焊、少焊或多焊的现象。
印刷位置应准确无误,不应有偏移或模糊的情况。
4. 零件安装质量PCBASMT中的零件安装是将元器件精确地安装在电路板上的过程。
零件应当安装在规定的位置上,位置准确无误。
零件安装应牢固可靠,无松动或倾斜。
引脚或焊点应与电路板保持良好的接触。
5. 清洁度PCBASMT中的清洁度是保证产品外观整洁、无污染的关键环节。
电路板上不应有灰尘、污渍或异物。
焊接接头和元器件之间不应有焊锡飞溅、焊锡球或焊锡桥等异常情况。
三、PCBASMT外观检验的方法1. 目视检查目视检查是最直接、简单的外观检验方法之一。
PCBA外观检 标准(贴片元件面)-品质看板

缺陷类别 严重 主要 缺陷 缺陷
V
2
错件
所贴片零件没有按BOM表与 工艺要求执行贴片
V
12
损件
元件破损、裂缝明显,但不影 响性能
V
应贴0603元
错贴0805元
3 反向 元件放置方向错误
4 侧立 元件侧面与焊盘接触。
5 立碑 元件端子与焊盘单面接触
6 反白 元件字面向下
7
Y轴偏移
超出焊盘或元件宽度的 1/3,其中较小者
验 标 准(SMT 元 件 面)
术语 定 义: 缺 陷: 指组 件在 其最 终使 用环 境下 影响 了外 形、 装配 和功 能的 现象 。
致命 缺 陷: 指缺 陷足 以造 成人 体或 机器 产生 伤害 或危 及生 命财 产安 全的 缺 陷; 主要 缺 陷: 指缺 陷对 制品 的实 质功 能上 已失 去实 用性 或造 成可 靠度 降 低, 产品 损坏 、功 能不 良;
8
X轴偏移
超出焊盘或元件宽度的 1/4,其中较小者。
元件表面划伤、破损轻微,未
V
13 损件 暴露出内部基材,且不影响性
能
V
14 空焊 引脚与焊盘之间无焊料填充
V
V
15
短路
线路与线路或元件引脚之间不 应导通而导通
V
V
16
虚焊
焊点外观良好,焊锡量适合, 但没有与引脚焊接在一起
V
V
17 假焊 焊接外观良好,但实际未接触
24 锡渣 直径超过0.5mm
25
多锡
焊料润湿过多,元件脚轮廓不 可辨认;焊料接触元件本体
26
溢红胶
红胶溢出,沾染焊盘,影响焊 锡性
27
溢红胶
PCBA插件SMT品质缺陷判定标准
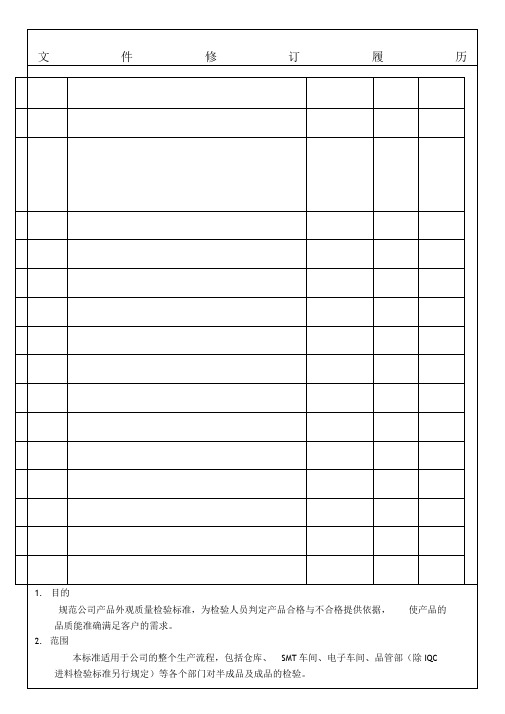
3.说明3.1本标准中的合格是指产品没有出现不良判定的任意一项内容。
3.2本标准中的不合格是指产品出现不良判定的任意一项内容。
缺陷判定分“严重缺陷”、“主要缺陷”、“次要缺陷”三种4.作业要求4.1 4.24.34.4 检验条件:室内照明要求良好,必要时用带灯的5倍以上放大镜检验。
各检验工位作业人员需按本工位的作业规范进行作业,按本标准中附页描述的各类标准及不良状况做出合格与不合格的判断。
不合格品用不良标签标识位置,并做好各检查记录后贴上相应标识,按照《不良品处理规范》处理。
注意事项4.4.1 4.4.2 本标准若与工艺文件内容有重复或抵触时,以工艺文件要求为准,本标准未涉及的内容,以工艺文件作为补充。
本标准部份图片及内容自IP C-A-610D摘录,如客户有特殊要求时依客户要求作业, 必要时由客户提供书面资料作参考。
示意图仅作参考,以文字描述为主要判定依据。
目检作业过程中需戴好静电手环。
4.4.34.4.44.5品质缺陷判定标准如下:SMT元件放置状态标准元件类别图片说明及标准描述元件贴装在焊盘的正中间,没有发生侧面与末端的偏移;红胶元件高度为钢网高度(0.15-0.2mm ),锡膏元件平贴板面;BGA边缘与PCB上的丝印标识在四个方向上的距离相等。
所有元件按工艺要求该贴片的位置都贴上正确的元件,极性元件方向正确;板面干净。
所有元件所有元件缺件:应贴片的位置未贴上元件。
错件:所贴元件与+工艺要求不相符。
反向:元件放置方向错误。
缺陷描述侧立:元件侧面与焊盘接触。
立碑:元件端子与焊盘单面接触。
反白:元件字面向下。
应贴错贴成0603 元0805 元I图片说明SMT元件放置状态缺陷元件类缺陷类别别严重缺陷主要缺陷次要缺陷元件引脚与焊盘接触面可见明显焊料润湿,焊点光亮、平滑;片状、圆柱、矩形 元件焊料润湿高度至少为0.5mm,超过2mm 高度的元件,焊料润湿高度至少为元件高 度的1/4 ;翼形引脚元件焊料润湿厚度至少为元件脚厚度或直径的 1/2,润湿高度至少为元件脚下弯至上弯处的1/3 。
PCBA外观检验规范
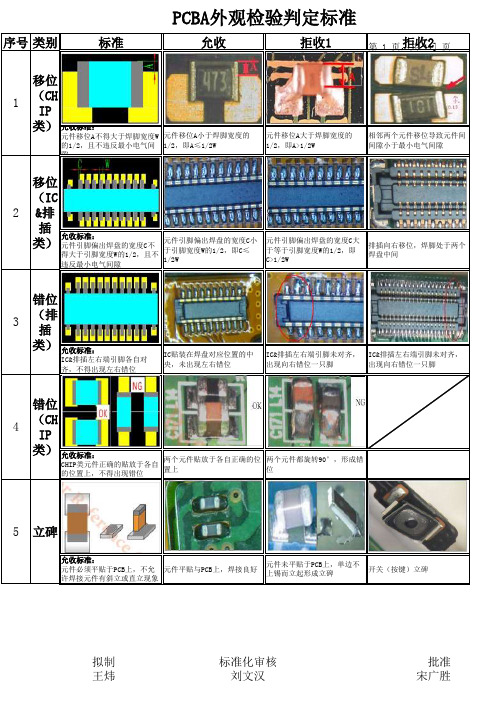
两个元件都旋转90°,形成错 位
5 立碑
允收标准: 元件必须平贴于PCB上,不允 元件平贴与PCB上,焊接良好 许焊接元件有斜立或直立现象
元件未平贴于PCB上,单边不 上锡而立起形成立碑
开关(按键)立碑
拟制 王炜
标准化审核 刘文汉
批准 宋广胜
序号 类别
标准
PCBA外观检验判定标准
允收
拒收1
第 2 页,拒共收121] 页
类) 允收标准:
IC&排插左右端引脚各自对 齐,不得出现左右错位
IC贴装在焊盘对应位置的中 IC&排插左右端引脚未对齐, IC&排插左右端引脚未对齐,
央,未出现左右错位
出现向右错位一只脚
出现向右错位一只脚
错位
4
(CH IP
类) 允收标准:
CHIP类元件正确的贴放于各自 的位置上,不得出现错位
两个元件贴放于各自正确的位 置上
1.垂直锡尖小于0.5mm 2.水平锡尖未超过最小电气间 隙
水平锡尖超过最小电气间隙
撞件 21 /破
件
允收标准: 所有元件本体不得有裂痕、破 元件本体无裂痕,焊接无异常 元件本体破损 损以及被撞击
元件被撞击后与焊点脱离
孔上
22 型
MIC
允收标准: 1.MIC与PCB的间隙A不得大于 0.1mm
MIC平贴与PCB上,零件与PCB 间隙<0.1mm
1.线路不同的引脚之间不得有
连2.锡空、脚碰与脚接拟等地制现脚象之间不得连锡 同形一成元短件路的焊脚焊标点准良好化,未审核同连一,元形件成的短两路个焊脚焊点相
3.空脚或接王地炜脚与引脚线路不
得连锡
刘文汉
相短邻路两个元件焊接批相连准,形成 宋广胜
PCBA外观检验标准01
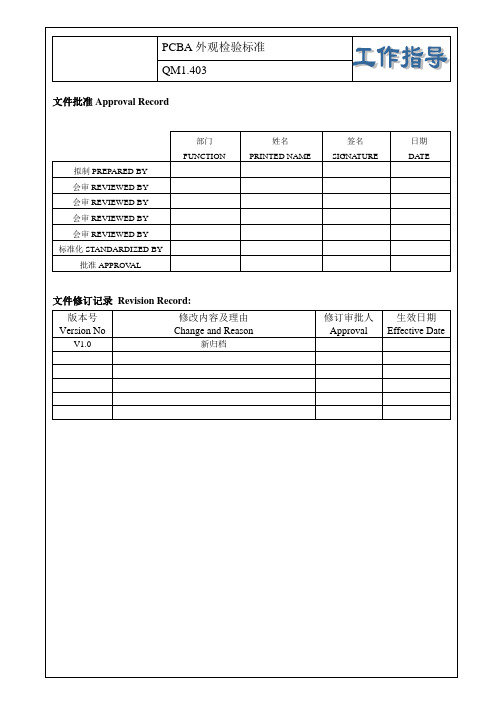
3、 定义 Definition: 3.1 标准 【允收标准】 (Accept Criterion):允收标准为包括理想状况、允收状况、拒收状况等
三种状况。 【理想状况】 (Target Condition):此组装情形接近理想与完美之组装结果。能有良好
组装可靠度,判定为理想状况。 【允收状况】 (Accept Condition):此组装情形未符合接近理想状况,但能维持组装可
带。 3.引线脚的轮廓清楚可见
允收状况(Accept Condition) 1.引线脚与板子焊垫间的焊锡连接很
好且呈一凹面焊锡带。 2.引线脚的侧端与焊垫间呈现稍凸的
焊锡带。 3.引线脚的轮廓可见。
拒收状况(Reject Condition)
1.焊锡带延伸过引线脚的顶部(MI)。 2.引线脚的轮廓模糊不清(MI)。 3. 以上缺陷任何一个都不能接收。
的接脚,已超过接脚本身宽度的 1/2W(MI)。(X>1/2W ) 2.偏移接脚之边缘与焊垫外缘之垂直 距离<5mil(0.13mm)以下(MI)。
(S<5mil)
3. 以上缺陷大于或等于一个就拒收。
7.9 鸥翼(Gull-Wing)脚面焊点最小量
理想状况(Target Condition) 1.引线脚的侧面,脚跟吃锡良好 2.引线脚与板子焊垫间呈现凹面焊锡
X≦1/2W
芯片状零件恰能座落在焊垫的中央且 未发生偏出,所有各金属封头都能完全
与焊垫接触。
注:此标准适用于三面或五面之芯片状
Hale Waihona Puke 零件WY1 ≧1/4W
允收状况(Accept Condition) 1. 零件纵向偏移,但焊垫尚保有其零
W
PCBA(SMT)外观检验判定标准
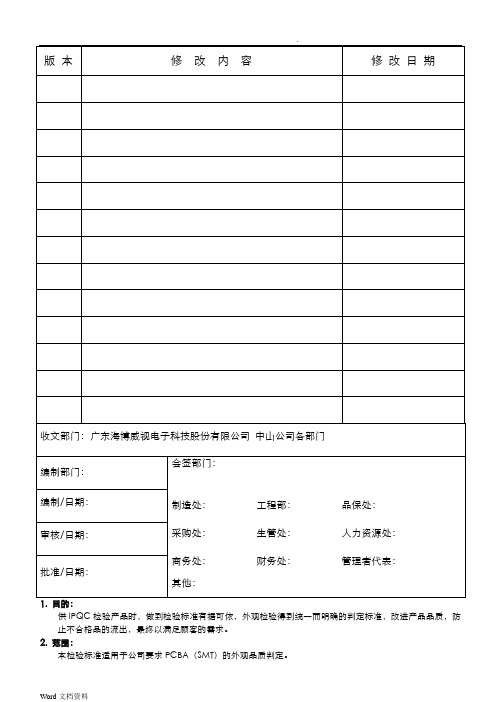
供IPQC检验产品时,做到检验标准有据可依,外观检验得到统一而明确的判定标准,改进产品品质,防止不合格品的流出,最终以满足顾客的需求。
2. 范围:本检验标准适用于公司要求PCBA(SMT)的外观品质判定。
3. 职责权限:3.1工程处(此标准做为工程制作工装、文件等需依此标准为基础).3.2制造处负责此标准的执行.3.3品保处(IPQC、QC、领班负责此标准的执行与监督,QE负责更新维护).4.相关参考文件:4.1. IPC-A-610D 电子组件可接受性标准。
4.2 BOM4.3 ECN4.3 工程图纸5.作业内容:5.1缺陷现象定义:菲林尺:为透明的PVC测试工具,用于识别点及线的大小缺陷判定。
塞规:为金属片状测试工具,用于缝隙大小的测试,也称厚溥规。
游标卡尺:用于物体尺寸的测量。
LCR(LCZ):用于测试电阻、电容、电感的阻值、容值、感值的测试仪器。
万用表:用于测量元器件的电压、电流及导通状态的仪器。
放大镜(显微镜):用于对所观察物体进行放大倍数,便于人眼识别的检验仪器。
推力计:用于对测试元器件所能存受的力度的仪器。
5.6检验要求:1.检验的环境及方法:a)距离:人眼与被测物表面的距离为300±50mm。
b)时间:每片检查时间不超过12s。
c)位置:检视面与桌面成45°;上下左右转动15°。
d)照明:40W冷白荧光灯,光源距被测物表面500~550mm (照度达500~800Lux)。
2.检验前准备:a)检验前需先确认所使用工作平台清洁及配戴清洁手套;b)ESD防护:凡接触PCBA必需配戴良好的静电防护措施(配戴防静电手环并接上静电接地线)。
3.PCBA持握的方法:正确的拿板作业姿势,在/ESD护防的条件下,并戴干净的手套握持PCBA(如下图),看板时板平面与眼睛存45°角,距离20~30CM,并注意转换方向,看到焊接的每一个面。
4.抽检方法要求:例如:如送检样本量:600PCS,按GB/T2828.1-2003一般检验水平II要求,抽检数量:80PCS,为保证抽检的均匀性,要求如下:4.1求抽检方法按照每栏上、中、下方式进行抽检。
- 1、下载文档前请自行甄别文档内容的完整性,平台不提供额外的编辑、内容补充、找答案等附加服务。
- 2、"仅部分预览"的文档,不可在线预览部分如存在完整性等问题,可反馈申请退款(可完整预览的文档不适用该条件!)。
- 3、如文档侵犯您的权益,请联系客服反馈,我们会尽快为您处理(人工客服工作时间:9:00-18:30)。
1. 目的:供IPQC检验产品时,做到检验标准有据可依,外观检验得到统一而明确的判定标准,改进产品品质,防止不合格品的流出,最终以满足顾客的需求。
2. 范围:本检验标准适用于公司要求PCBA(SMT)的外观品质判定。
3. 职责权限:3.1工程处(此标准做为工程制作工装、文件等需依此标准为基础). 3.2制造处负责此标准的执行.3.3品保处(IPQC、QC、领班负责此标准的执行与监督,QE负责更新维护).4.相关参考文件:4.1. IPC-A-610D 电子组件可接受性标准。
4.2 BOM4.3 ECN4.3 工程图纸5.作业内容:5.1缺陷现象定义:5.2缺陷级别定义:5.4名词定义:5.5关于工具的定义:菲林尺:为透明的PVC测试工具,用于识别点及线的大小缺陷判定。
塞规:为金属片状测试工具,用于缝隙大小的测试,也称厚溥规。
游标卡尺:用于物体尺寸的测量。
LCR(LCZ):用于测试电阻、电容、电感的阻值、容值、感值的测试仪器。
万用表:用于测量元器件的电压、电流及导通状态的仪器。
放大镜(显微镜):用于对所观察物体进行放大倍数,便于人眼识别的检验仪器。
推力计:用于对测试元器件所能存受的力度的仪器。
5.6检验要求:1.检验的环境及方法:a)距离:人眼与被测物表面的距离为300±50mm。
b)时间:每片检查时间不超过12s。
c)位置:检视面与桌面成45°;上下左右转动15°。
d)照明:40W冷白荧光灯,光源距被测物表面500~550mm (照度达500~800Lux)。
2.检验前准备:a)检验前需先确认所使用工作平台清洁及配戴清洁手套;b)ESD防护:凡接触PCBA必需配戴良好的静电防护措施(配戴防静电手环并接上静电接地线)。
3.PCBA持握的方法:正确的拿板作业姿势,在/ESD护防的条件下,并戴干净的手套握持PCBA(如下图),看板时板平面与眼睛存45°角,距离20~30CM,并注意转换方向,看到焊接的每一个面。
4.抽检方法要求:例如:如送检样本量:600PCS,按GB/T2828.1-2003一般检验水平II要求,抽检数量:80PCS,为保证抽检的均匀性,要求如下:4.1求抽检方法按照每栏上、中、下方式进行抽检。
4.2栏抽检数量尽可能保证一致性。
4.3周转车图示见下图:5.7相关不良检验图片及标准说明参见下图:示图不良定义目检技巧及判定标准短路非连接导通电路有焊锡相连状态短路多发生在细间距的元件相引脚及相邻元件上。
焊锡堆积,目检时上下左右四个方向倾斜45度PCBA容易发现。
判定标准:所有非连接导通电路的短路均判拒收侧立元件焊接端未有侧立多发生在效贴装,呈侧面贴装状态chip类电阻上,元件高度会高于旁边同类元件,且正常贴装上表面为黑色,侧立不良的上表面多为白色。
判定标准:所有侧立均判拒收立碑因回焊拉力导致元件未有效焊接,呈墓碑状立碑多发生在chip 电阻电容上,元件高度会明显高于旁边同类元件判定标准:所有侧立均判拒收多件BOM不要求贴料的位置有元件,或同一位置有一个以上物料多件的检查可关注PCB非焊盘区域,主要是板中间区域和相邻焊接元件的间隙处判定标准:所有多件均判拒收假焊(功能元件)元件焊接端未与PCB焊盘有效焊接,存在间隙或呈不固定状态多发生在细间距的元件引脚、卡座固定脚及chip元件上。
多因材料本身变形或焊锡润湿不足所致。
目检时上下左右四个方向倾斜45度PCBA确认。
判定标准:所有需连接导通电路、起固定作用的元件假焊均判拒收.假焊(屏蔽框)屏蔽框底部焊接判定标准:端未与PCB焊盘有效焊接,存在间隙並呈不固定状态单条边假焊,但假焊长度不超过相应边长的25%,其它三条边焊接OK可接收冷焊元件脚金属部分与焊点焊接牢固,锡膏未完全溶化,如左图所示判定标准:所有冷焊均拒收爬锡元件脚或Pin针与PAD间的焊锡爬锡高度已超过零件本体高度或Pin脚高度的2/3,焊锡已将元件脚覆盖,吃锡过多状况。
判定标准:拒收反向(极性元件、屏蔽框、SIM卡座)元件贴装极性点未和PCB极性标识点/丝印图标识点对应点对点、缺口对缺口匹配原则,PCB 无点则参考样板或丝印图。
判定标准:所有反向均判拒收上锡非上锡区域(按上锡绝大多数发键、金手指)有上锡生在按键等面积较大的镀金区,呈点状或片状分布判定标准:按键、金手指、天线区不可上锡,其它区域可允许直径0.5mm的锡点,点数小于2个且無凸点。
损件已焊接完成元件受到外力撞击导致损件或元件破裂损件会有元件本体残留在焊盘上,多发生在板边缘区域、测试夹具测试接触区、LED灯区,视PCB的結构而定判定标准:所有损件均判拒收偏位(片式元件)元件贴装位置未和焊盘重合,有偏移判定标准:1.片式元件、晶体管类元件侧面偏移A大于元件焊接端或焊盘宽度W的50%2.元件末端偏移以上有任一情況均判拒收浮高元器件与PCB存在间隙或高度超过0.3mm。
判定标准:目视或用塞规量测超过0.2 mm的拒收偏位(IC/卡座/USB/电池座)元件贴装位置未判定标准:和焊盘或丝印重合,有偏移1.圆柱体、扁平、L 形和翼型引脚的SOP 、QFP 、QFN 侧面偏移大于引脚焊接宽度的25%2.电池座/USB/卡座/天线弹片偏移超出焊接端或焊盘的25%或存在角度偏差以上有任一情況均判拒收少件BOM 要求進行元件贴装的位置无元件判定标准:所有少件均判拒收少锡(片式元件)元件焊锡量未达到正常要求判定标准: 1.片式元件末端焊点宽度C 未达到元件可焊端宽度W 的50%,或焊盘宽度的50% 2.最小焊接高度F 未达到焊锡厚度G 加可焊端高度H25%.以上任一情況拒收少锡(SOP 、QFP)元件焊锡量未达到正常要求判定标准: 1.最小末端焊点宽度C 小于引脚宽度W 的50% 2.最小侧面焊点长度D 小于引脚长度50% 3.最小跟部焊接高度F 小于焊接厚度G 加连接处的引脚厚度T 的50%以上任一情況拒收少锡(QFN 类元件)元件焊锡量未达判定标准:到正常要求 1.城堡类QFN最小焊点高度F未达到焊锡高度H的50%2.最小末端焊点宽度C未达到城堡宽度W的75%以上任一情況拒收多锡元件焊锡量超出正常要求判定标准:最大高度焊点超出焊盘或延伸至可焊端金属镀层顶部至元件体以上情況拒收划伤PCBA表面存在刮痕判定标准:PCB或按键等划伤及铜箔裸露现象(PCB板同一面划伤长度不可超过宽0.2mm*长10mm*2条,按键、金手指划伤不可超过宽0.2mm*长3mm/2条,PCB板同一面有感划伤长度不可超过宽0.2mm*长5mm且不能裸露铜箔,按键与金手指不允许有有感划伤。
PCB脏污有不同颜色污染的混入顏色差异明显容易检出,多发生在维修板中判定标准:脏污呈片状分布,面积大于1mm2均判拒收混板不同机种/硬件、判定标准:不同软件、不同工令版本的板混在一起混板全部不可接收,且必須严格区分,通知产线全检零件破损元件本体出现破损现象判定标准:在不影响功能的情况下封装层破损程度依左图标准执行,否则判拒收PCB掉铜箔PCB铜箔有掉落现象判定标准:所有功能位掉铜箔不良均判拒收SIM卡座坏SIM卡座有金手指翘起、脫落、或弹片变形脫落等现象判定标准:有金手指翘起、脫落、或弹片变形脫落等任一情況的拒收元件烫伤影响外形、装配和判定标准:功能变形、缺口、刮削、刻痕或熔毀现象裂痕或其它变形影响了机械性质的完整均判拒收断路PCB线路断开现象。
判定标准:所有PCB断路均拒收错位元器件或元器件脚的位置移到其它PAD或脚的位置上。
判定标准:拒收反白(翻件)元器件有区别的相对称的两个面互换位置(如:有丝印标识的面与无丝印标识的面上下颠倒面),片状电阻常见。
判定标准:所有翻件均拒收锡珠元器件脚之间或PAD以外的地方的小锡点.判定标准:一块板同一面不能超过2个0.13 mm的锡珠拒收锡裂焊锡有裂痕(裂判定标准:拒收开)现象。
孔塞PCB插件孔或导通孔等被焊锡或其它阻塞。
判定标准:拒收针孔(凹点)PCB、PAD、焊点等有针孔凹点(一块板不允许有3个直径为0.2mm的针孔)。
判定标准:一块板有3个直径为0.2mm的针孔不良现象判拒收PCBA变形元器件或PCB本体或边角不变形高度其对角线的0.75%判定标准:在此范围可接受,超出判拒收起泡(分层)PCB或元器件与铜铂分层,且有间隙.判定标准:PCB板有线路的部分不允许有起泡现象,在不影响功能的情况下其它无线路的区域起泡的面积超过4 mm2,判拒收焊点气泡焊点内呈气泡现象判定标准:焊点内气泡不允许超过焊点直径的1/3,否则判拒收.焊点偏移焊锡与PAD未垂直焊接.判定标准:焊锡偏移超出PAD面积的1/3,判拒收O N锡尖元器件焊点不平滑,且存拉尖状况,锡尖等于或大于0.5mm为拒收判定标准:锡尖等于或大于0.5mm 的,判拒收毛边(披峰)PCB 板边或毛刺超出要求范围或长度(0.2mm)。
判定标准: 超过0.2mm 的,判拒收错件元器件规格、型号、参数、形体等要求与(BOM 、样品 客户资料等)不符。
判定标准: 所有错件均判拒收过孔检查PCB 板时重点检查下孔存是否存在不良现象 (检查方法:测量、实配、对比)判定标准: 出现难插或插不进判拒收5.8以上标准为正常情况下的检验依据,如客户特殊要求,则依客户要求执行。
5.9以上标准当外观出现瑕疵但属于可接收范围,必须保证产品功能OK ,否则判拒收。
物别说明:1、 如有特殊要求则按照物殊要求执行。
2、 检验员在日常工作中发现以上未包含的问题时,请及时提出。
ON。