板式吊耳的设计及应用
浅谈船舶吊装吊耳设计
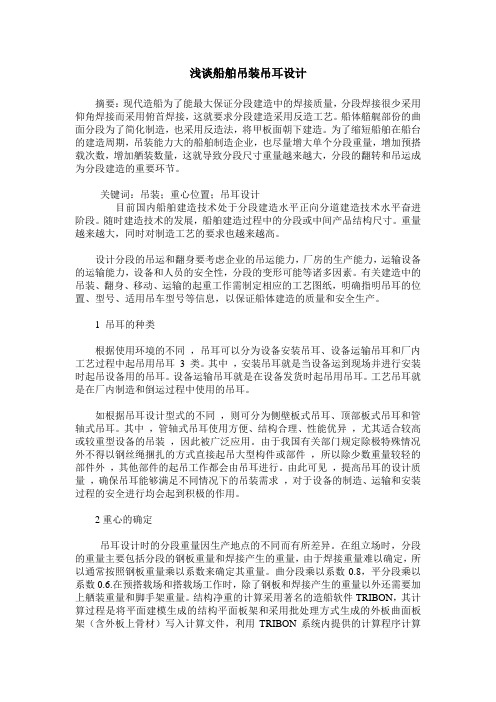
浅谈船舶吊装吊耳设计摘要:现代造船为了能最大保证分段建造中的焊接质量,分段焊接很少采用仰角焊接而采用俯首焊接,这就要求分段建造采用反造工艺。
船体艏艉部份的曲面分段为了简化制造,也采用反造法,将甲板面朝下建造。
为了缩短船舶在船台的建造周期,吊装能力大的船舶制造企业,也尽量增大单个分段重量,增加预搭载次数,增加舾装数量,这就导致分段尺寸重量越来越大,分段的翻转和吊运成为分段建造的重要环节。
关键词:吊装;重心位置;吊耳设计目前国内船舶建造技术处于分段建造水平正向分道建造技术水平奋进阶段。
随时建造技术的发展,船舶建造过程中的分段或中间产品结构尺寸。
重量越来越大,同时对制造工艺的要求也越来越高。
设计分段的吊运和翻身要考虑企业的吊运能力,厂房的生产能力,运输设备的运输能力,设备和人员的安全性,分段的变形可能等诸多因素。
有关建造中的吊装、翻身、移动、运输的起重工作需制定相应的工艺图纸,明确指明吊耳的位置、型号、适用吊车型号等信息,以保证船体建造的质量和安全生产。
1 吊耳的种类根据使用环境的不同,吊耳可以分为设备安装吊耳、设备运输吊耳和厂内工艺过程中起吊用吊耳 3 类。
其中,安装吊耳就是当设备运到现场并进行安装时起吊设备用的吊耳。
设备运输吊耳就是在设备发货时起吊用吊耳。
工艺吊耳就是在厂内制造和倒运过程中使用的吊耳。
如根据吊耳设计型式的不同,则可分为侧壁板式吊耳、顶部板式吊耳和管轴式吊耳。
其中,管轴式吊耳使用方便、结构合理、性能优异,尤其适合较高或较重型设备的吊装,因此被广泛应用。
由于我国有关部门规定除极特殊情况外不得以钢丝绳捆扎的方式直接起吊大型构件或部件,所以除少数重量较轻的部件外,其他部件的起吊工作都会由吊耳进行。
由此可见,提高吊耳的设计质量,确保吊耳能够满足不同情况下的吊装需求,对于设备的制造、运输和安装过程的安全进行均会起到积极的作用。
2重心的确定吊耳设计时的分段重量因生产地点的不同而有所差异。
在组立场时,分段的重量主要包括分段的钢板重量和焊接产生的重量,由于焊接重量难以确定,所以通常按照钢板重量乘以系数来确定其重量。
附塔管线吊装板式吊耳的设计与校核
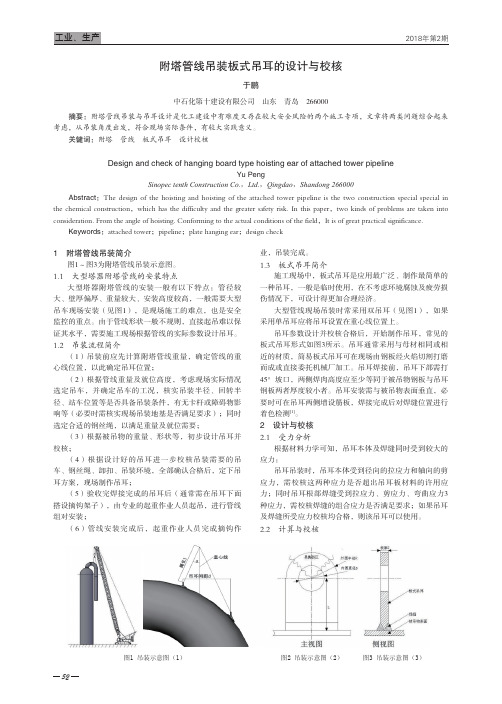
521 附塔管线吊装简介图1~图3为附塔管线吊装示意图。
1.1 大型塔器附塔管线的安装特点大型塔器附塔管线的安装一般有以下特点:管径较大、壁厚偏厚、重量较大、安装高度较高,一般需要大型吊车现场安装(见图1),是现场施工的难点,也是安全监控的重点。
由于管线形状一般不规则,直接起吊难以保证其水平,需要施工现场根据管线的实际参数设计吊耳。
1.2 吊装流程简介(1)吊装前应先计算附塔管线重量,确定管线的重心线位置,以此确定吊耳位置;(2)根据管线重量及就位高度,考虑现场实际情况选定吊车,并确定吊车的工况,核实吊装半径、回转半径、站车位置等是否具备吊装条件,有无卡杆或障碍物影响等(必要时需核实现场吊装地基是否满足要求);同时选定合适的钢丝绳,以满足重量及就位需要;(3)根据被吊物的重量、形状等,初步设计吊耳并校核;(4)根据设计好的吊耳进一步校核吊装需要的吊车、钢丝绳、卸扣、吊装环境,全部确认合格后,定下吊耳方案,现场制作吊耳;(5)验收完焊接完成的吊耳后(通常需在吊耳下面搭设摘钩架子),由专业的起重作业人员起吊,进行管线组对安装;(6)管线安装完成后,起重作业人员完成摘钩作业,吊装完成。
1.3 板式吊耳简介施工现场中,板式吊耳是应用最广泛、制作最简单的一种吊耳,一般是临时使用,在不考虑环境腐蚀及疲劳损伤情况下,可设计得更加合理经济。
大型管线现场吊装时常采用双吊耳(见图1),如果采用单吊耳应将吊耳设置在重心线位置上。
吊耳参数设计并校核合格后,开始制作吊耳,常见的板式吊耳形式如图3所示。
吊耳通常采用与母材相同或相近的材质,简易板式吊耳可在现场由钢板经火焰切割打磨而成或直接委托机械厂加工。
吊耳焊接前,吊耳下部需打45°坡口,两侧焊肉高度应至少等同于被吊物钢板与吊耳钢板两者厚度较小者。
吊耳安装需与被吊物表面垂直,必要时可在吊耳两侧增设筋板,焊接完成后对焊缝位置进行着色检测[1]。
2 设计与校核2.1 受力分析根据材料力学可知,吊耳本体及焊缝同时受到较大的应力:吊耳吊装时,吊耳本体受到径向的拉应力和轴向的剪应力,需校核这两种应力是否超出吊耳板材料的许用应力;同时吊耳根部焊缝受到拉应力、剪应力、弯曲应力3种应力,需校核焊缝的组合应力是否满足要求;如果吊耳及焊缝所受应力校核均合格,则该吊耳可以使用。
板式吊耳设计及应用

板孔式吊耳设计及应用李景乐(中国石油天然气第一建设公司, 河南·洛阳 471023)摘 要:本文结合应用实例,对吊装常用板孔式吊耳的设计与校核进行了归纳和总结,弥补了相关规范涵盖范围的不足,为类似板孔式吊耳的设计及应用提供了良好的借鉴。
关键词:板孔式 吊耳 设计 应用 前 言在吊装工程中经常使用板孔式吊耳,而相应的规范或参考资料没有大于20t 的板孔式吊耳的相关设计参数。
通常板孔式吊耳的失效形式以吊耳板与设备本体的焊接强度不够及板孔撕裂为多,易造成不安全因素。
所以吊耳板孔的强度和焊缝强度是板孔式吊耳设计的最重要环节。
本文仅介绍单板孔吊耳的设计计算,双板孔吊耳的设计计算参照执行。
1 吊耳板孔的强度计算 1.1 拉曼公式图1 板孔式吊耳 图2孔壁承压应力分布 图3板孔失效形式图1为板孔式吊耳的基本形式,即单板孔吊耳。
图2为板孔式吊耳在受外力作用下孔壁承压应力分布情况。
图3为板孔式吊耳板孔强度不够吊耳板被撕裂的主要失效形式示意图。
也就是说板孔失效是吊轴与板孔接触所形成的接触压应力过大,不是造成接触处压溃,而是吊耳在外力的作用下对吊耳板进行的剪切作用引起的。
所以吊装工程中常用拉曼公式来对吊耳板孔进行抗剪强度校验。
拉曼公式板孔校核表达式为:[]22v 22k P R r f d R rσδ+=⋅≤- (1)式中:k —动载系数,k=1.1;σ—板孔壁承压应力,MPa ;P —吊耳板所受外力,N ; δ—板孔壁厚度,mm ; d —板孔孔径,mm ;R —吊耳板外缘有效半径,mm ; r —板孔半径,mm ;[]v f —吊耳板材料抗剪强度设计值,N/mm 2;1.2 吊耳参数确定从(1)式可以看出,当P 、d 卸扣、δ一定时,取2222R r R r+-适宜的值可最节省材料,显然22221R r R r+>-,令22221.1R r R r+=-,则4.583R r=。
从理论而言, 4.583R r =较为科学,但使用单板孔吊耳,还应考虑卸扣和绳扣连接时必须预留的间隙,显然R 值不宜太大。
大型吊装中设备吊耳设计与验收_潘文江
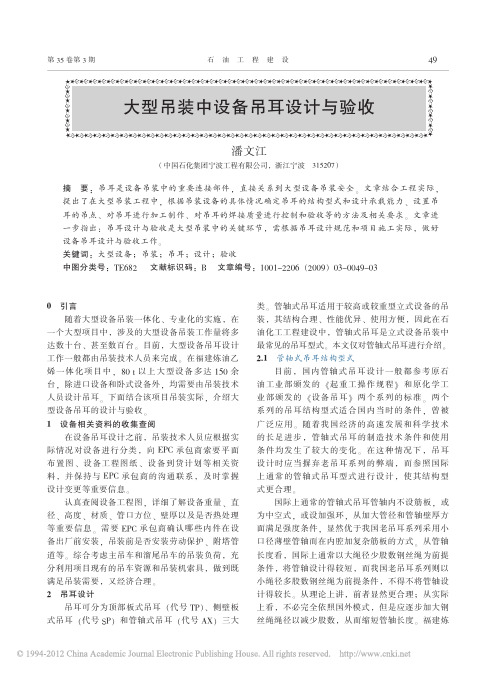
第35卷第3期潘文江(中国石化集团宁波工程有限公司,浙江宁波315207)摘要:吊耳是设备吊装中的重要连接部件,直接关系到大型设备吊装安全。
文章结合工程实际,提出了在大型吊装工程中,根据吊装设备的具体情况确定吊耳的结构型式和设计承载能力、设置吊耳的吊点、对吊耳进行加工制作、对吊耳的焊接质量进行控制和验收等的方法及相关要求。
文章进一步指出:吊耳设计与验收是大型吊装中的关键环节,需根据吊耳设计规范和项目施工实际,做好设备吊耳设计与验收工作。
关键词:大型设备;吊装;吊耳;设计;验收中图分类号:TE682文献标识码:B文章编号:1001-2206(2009)03-0049-03大型吊装中设备吊耳设计与验收!!!!!!!!!!!!!!!!!!!!!!!!!!!!!!!!!!!!!!!!"!!!!!"!!!!!!!!!!!!!!!!!!!!!!!!!!!!!!!!!!!!!!!!"!!!!!"0引言随着大型设备吊装一体化、专业化的实施,在一个大型项目中,涉及的大型设备吊装工作量将多达数十台、甚至数百台。
目前,大型设备吊耳设计工作一般都由吊装技术人员来完成。
在福建炼油乙烯一体化项目中,80t 以上大型设备多达150余台,除进口设备和卧式设备外,均需要由吊装技术人员设计吊耳。
下面结合该项目吊装实际,介绍大型设备吊耳的设计与验收。
1设备相关资料的收集查阅在设备吊耳设计之前,吊装技术人员应根据实际情况对设备进行分类,向EPC 承包商索要平面布置图、设备工程图纸、设备到货计划等相关资料,并保持与EPC 承包商的沟通联系,及时掌握设计变更等重要信息。
认真查阅设备工程图,详细了解设备重量、直径、高度、材质、管口方位、壁厚以及是否热处理等重要信息。
需要EPC 承包商确认哪些内件在设备出厂前安装,吊装前是否安装劳动保护、附塔管道等。
综合考虑主吊车和溜尾吊车的吊装负荷,充分利用项目现有的吊车资源和吊装机索具,做到既满足吊装需要,又经济合理。
吊耳布置及焊缝计算

吊耳布置及焊缝计算主纵梁、横隔板(分段)、横隔板(整体)均采用两点吊,吊点均设置在钢梁翼缘顶面、主腹板与肋板交点位置,吊耳耳板与主腹板线行重合。
吊耳与顶板翼缘采用双面1.5cm角焊缝连接,耳板正对钢梁腹板,底部三角筋板正对钢梁肋板。
吊耳包含两种尺寸,其中大尺寸吊耳适用于主纵梁、横隔板(整体)所有节段,配合40t卡环使用;小尺寸适用于横隔板(分段)所有节段,配合20t卡环适用。
起吊时钢丝绳与水平夹角须大于60°。
吊耳布置、具体尺寸及计算如下所示:一、吊耳布置图1、主纵梁吊耳布置图图2、横隔板(整体)吊耳布置图图3、横隔板(分段)吊耳布置图二、吊耳尺寸图4、大尺寸吊耳细部图图5、小尺寸吊耳细部图三、大尺寸吊耳受力计算大尺寸吊耳适用于主纵梁及横隔板(整体),最大杆件重量为25t,采用两点吊,钢丝绳与水平面夹角为60°。
吊耳最大荷载: N=25×0.7×1.1×tan60°×104=333×103N。
耳板孔净截面处抗拉强度:σ=N2tb1≤fb1=min (2t+16,b−d0 3 )t=30mm,d0=75mm,b=80mm,b1=55mmσ=N2tb1=333×1032×30×55=100.9MPa≤f=215MPa耳板端部截面抗拉(劈开)强度:σ=N2t(a−2d03)=333×1032×30×(80−2×753)=185MPa≤f =215MPa耳板抗剪强度:Z=√(a+d0/2)2−(d0/2)2=√(80+75/2)2−(75/2)2=111.4mmτ=N2tZ=333×1032×30×111.4=49.8MPa≤f v=125MPa焊缝验算:N y=25×0.7×1.1×104=192.5×103NN x =N 2=333×1032=166.5×103N√(σf βf )2+τf 2=√(N y ∑l w ℎe )2+(N x∑l w ℎe)2=√(192.5×1032×240×10.5)2+(166.5×1032×240×10.5)2=50.5MPa ≤f f w=160MPaβf ——正面角焊缝强度增大系数,动载时取1.0;ℎe ——焊缝有效高度,ℎe =0.7ℎf =0.7×15=10.5mm ;l w ——角焊缝有效长度,l w =270−2ℎf =240mm ; f f w ——角焊缝承载力设计值,采用自动焊、半自动焊和E43XX 型焊条的手工焊接Q235钢构件时取160MPa四、小尺寸吊耳受力计算小尺寸吊耳适用于横隔板(分段),最大杆件重量为15t ,采用两点吊,钢丝绳与水平面夹角为60°。
吊耳的设计说明书1

1.1.零件的工艺分析
由零件图可知,其材料为:35号钢,优质碳素结构钢有良好的塑性和适当的强度,工艺性能较好,焊接性能尚可,大多在正火状态和调质状态下用。
由后钢板弹簧吊耳零件图知可将其分为两组加工表面。
它们相互间有一定的位置要求。
现分析如下:
(1)以∅30mm两外圆端面为主要加工表面的加工面。
这一组加工表面包括:∅30mm两外圆端面的铣削,加工∅37mm的孔,其中∅30mm两外圆端面表面粗糙度要求为Ra6.3,∅37mm的孔表面粗糙度要求为Ra1.6
(2)以∅30mm孔为主要加工表面的加工面。
这一组加工表面包括:2个以∅30mm的孔,2个∅10.5mm的孔、2个∅30mm孔的内外两侧面的铣削,宽度为4mm 的开口槽的铣削、表面粗糙度要求为Ra50,2个∅30mm在同一中心线上数值为∅0.01的同轴度要求。
其中2个∅30mm的孔表面粗糙度要求为Ra1.6μm,2个∅10.5mm的孔表面粗糙度要求12.5Ramm,2个∅10.5mm孔的内侧面表面粗糙度要求为12.5Ramm,2个∅30孔的外侧面表面粗糙度要求为50Ramm,宽度为4mm的开口槽的表面粗糙度要求为50Ramm。
2.弹簧吊耳零件的技术要求。
吊耳的设计标准
吊耳的设计标准主要包括以下几个方面:
1. 材料选择:吊耳的材料应具有良好的强度和韧性,能够承受吊运过程中的各种应力。
常用的材料有碳钢、合金钢、不锈钢等。
2. 结构设计:吊耳的结构设计应简单、合理,便于制造和安装。
常见的结构形式有圆筒形、椭圆形、矩形等。
吊耳的尺寸应根据被吊物体的重量和形状来确定。
3. 表面处理:为了提高吊耳的耐磨性和抗腐蚀性,通常需要对吊耳进行表面处理,如镀锌、喷涂、热处理等。
4. 安全系数:吊耳的设计应考虑到安全因素,设置足够的安全系数。
安全系数的大小应根据吊运过程中可能出现的最大载荷和最大应力来确定。
5. 连接方式:吊耳的连接方式应与被吊物体的连接方式相匹配,以确保吊装过程的安全和稳定。
常见的连接方式有螺栓连接、焊接连接等。
6. 标识:吊耳上应有清晰的标识,包括型号、规格、生产日期等信息,以便于使用和维护。
7. 检验与验收:吊耳在出厂前应进行严格的检验,确保其质量符合设计要求和相关标准。
在使用过程中,也应定期进行检查和维护,确保其安全可靠。
板式吊耳的设计与施工
Fp=3450/(7+3.8×2) ×15=15.8
Fp=0.9Fy = 31.95KN/cm2
UC=fp/Fp=0.49<1.0
OK
KN/cm2
2.3.2 孔剪应力
Av=4×3.8×(16-7.7)+2×7×(20-7.7)=298.4cm2
fv/Av=11.56KN/cm2
Fv=0.4Fy=14.2KN/cm2
2.3.6 D-D断面拉伸强度
Aa=7×(2×20+38.66×π×16/180)=355.6cm2 θ=+8-1(r/R)=38.66°
fa=P/Aa=3450/355.6=9.7 KN/cm2
Fa=0.6Fy=21.3KN/cm2
UC=fa/Fa=0.46 < 1.0
OK
第20页
二、吊耳的设计算例
cm2 cm2 KN KN KN/cm2 KN/cm2
(3)组合应力
fa=H/A
KN/cm2
Fa=0.6Fy
KN/cm2
UC=fa/Fa < 1.0
第14页
一、吊耳的设计原则、破坏型式和计算方法
(4)组合应力 平面内弯曲 Mz= -H(0.5a-e)+vb fbz=Mz/Sz 平面外弯曲 My=5%pb fby=My/Sy 组合应力 fa/0.6Fy+fby/0.66Fy+fbz/0.66Fy < 1.0
第26页
二、吊耳的设计算例
(3)根据设计经验,吊耳手工计算方法比有限元分析更保 守,吊耳设计建议进行手工计算和软件有限元分析同时进行 ,取得最保守的设计结果。
第27页
三、吊耳的施工与经验教训
3.1 吊耳的施工 主受力方向在进行板材排版要与主轧制方向一致,吊耳 板下料前要进行100%UT检验和材质跟踪。 孔要求机械加工,一般施工顺序是将吊耳板与眼板焊接 在一起后再进行孔的机械加工,对于小直径可以直接钻孔 ,而对于大直径一般下料尺寸为d-10mm作为镗孔余量,在 完成焊接工作后进行镗孔加工。
板式吊耳设计计算书
抚顺石化分公司120万吨/年催化中压加氢精制(改质)装置精制反应器(R-101)反应器吊耳设计参考基本参数:筒体最小壁厚135mm封头最小壁厚:80mm筒体内直径:3613mm封头半径:1834mm注:○1L2公式仅适用于标准椭圆形封头式中:δ—封头名义厚度;h1—封头曲面高度;h2—封头直边高度;对其它形式封头,L2由设计者自定。
吊耳板材质:Q235-A许用应力[σ]:130Mpa许用剪应力[τ]:91Mpa角焊缝系数:Φn:0.7动载综合系数:K=1.65吊耳竖向载荷Q=332235kgFv=332235÷2×K=332235÷2×1.65=274093.8 kg吊角A-A截面拉应力:σ= Fv/S(H-D)= 274093.8/(10-0.13)(53-18)= 274093.8/523.11=523.96kg/cm2σ<[σ],满足要求。
垫板焊缝剪应力:τ= Fv/0.707 a [2(L sp+ H sp )-8×2+2π2]=274093.8/0.707×3.6[2(45.5+93 )-8×2+2π2]=274093.8/696.26=393.66 kg/cm2τ<[τ],满足要求。
吊耳板焊缝剪应力:τ= Fv/0.707 aΦn[2(L sp-G+ L1 )+0.5πF+H-F-8r+2πr]=274093.8/0.707×3.6×0.7[2(45.58+22 )+0.5π15+53-15-8×4+2π×4]=274093.8/368.34=744.13 kg/cm2τ<[τ] ,满足要求。
吊耳受弯状态分析:R A=P/2(2+3λ)R B=-3Pm/2lM A=-PmM B=Pm/2A-C段Q X=-P M X=-PxB-C段Q X=3Pm/2l M X=-Px+R A(x-m)计算吊耳水平状态下受力状态:P=274093kg。
板式吊耳的设计计算
以满 足实 际要求 ( 见图 1 ) 。
F R + r 2 r ]
保证起 吊的平 衡性 和稳定 性 吊 重 量 为 1 5 t , 吊 耳 的 材 质 为
Q 2 3 5 ,与顶罩 的材质一 样 。考虑 到起 吊时 的动载 因 素 、安全 因素 、可靠 因素 、摩 擦 系数等 ,在实 际设
加受 力 面积 ,以此 达 到 作用 力 分 散 、减 小 剪切 力 、
式中, 为 吊耳板 的 长 度 ( m m) ; 为 吊耳板 确保 焊缝 承载 力 的 目的。 吊耳 的最 终 设 计 尺 寸为 :
B=1 7 0 l n n l , a=7 0 l n n l , =6 0 n l n l 。
均具 有较 好 的可 焊性 。根据 不 同材 质 的钢材 板厚取 [ 厂 v ]值 ,只 要 满 足 下式 的要 求 ,吊耳 的 强 度就 可
.
由检修 单位根 据顶罩 的外 形尺 寸 、结构 特点 、起 吊
重量 、 吊耳 受 力 等 情 况 , 自行 设 计 、现 场 焊 接 吊 耳 。已知顶罩 的起 吊重量 为6 0 t , 直 径为 9 . 5 m, 为了
相近 的原则 ,特 殊情况 下 ,也应采 用 比设 备母 材高
一
2. 2 吊耳 的 尺 寸 设 计
某水 电站 的灯泡 贯流式 机组 检修 ,要将顶 罩 吊
移 至上游 流道 前放置 ,由于顶罩 上没有 吊耳 ,需要
个 级 别 的材 料 。水 电 站 一般 都 是 采 用 碳 素 结 构
钢 ,如 Q 2 3 5 ;或是低 合金 高强 度结构 钢 ,如 Q 3 4 5 ,
1 )承压应 力 的最不 利位 置在 1 —2断 面 ,吊耳 孔 壁承 压应 力校 核 :
- 1、下载文档前请自行甄别文档内容的完整性,平台不提供额外的编辑、内容补充、找答案等附加服务。
- 2、"仅部分预览"的文档,不可在线预览部分如存在完整性等问题,可反馈申请退款(可完整预览的文档不适用该条件!)。
- 3、如文档侵犯您的权益,请联系客服反馈,我们会尽快为您处理(人工客服工作时间:9:00-18:30)。
板式吊耳的设计及应用
摘要:本文结合应用实例,对机械设备起重吊装常用板孔式吊耳的设计与校核进行了归纳和总结,弥补了相关规范涵盖范围的不足,为类似板孔式吊耳的设计及应用提供了良好的借鉴。
关键词:板孔式吊耳设计应用
前言在起重吊装工程中经常使用板式吊耳,通常板式吊耳的失效形式以吊耳板与设备本体的焊接强度不够及板孔撕裂为多,易造成不安全因素。
所以吊耳板孔的强度和焊缝强度是板式吊耳设计的最重要环节。
本文仅介绍单板吊耳的设计计算,双板孔吊耳的设计计算参照执行。
1 吊耳板孔的强度计算1.1 拉曼公式
图1板孔式吊耳图2孔壁承压应力分布图3板孔失效形式图1为板式吊耳的基本形式,即单板吊耳。
图2为板式吊耳在受外力作用下孔壁承压应力分布情况。
图3为板式吊耳板孔强度不够吊耳板被撕裂的主要失效形式示意图。
也就是说板孔失效是吊轴与板孔接触所形成的接触压应力过大,不是造成接触处压溃,而是吊耳在外力的作用下对吊耳板进行的剪切作用引起的。
所以吊装工程中常用拉曼公式来对吊耳板孔进行抗剪强度校验。
拉曼公式板孔校核表达式为:(1)式中:k—动载系数,k=1.1;—板孔壁承压应力,MPa;P—吊耳板所受外力,N;δ—板孔壁厚度,mm;d—板孔孔径,mm;R—吊耳板外缘有效半径,mm;r—板孔半径,mm;—吊耳板材料抗剪强度许用值,N/mm2;1.2 吊耳参数确定从(1)式可以看出,当P、d、一定时,取适宜的值可最节省材料,显然,令,则。
从理论而言,较为科学,但使用单板孔吊耳,还应考虑卸扣和绳扣连接时必须预留的间隙,显然R值不宜太大。
笔者认为,较适宜。
通常设计时,应首先按负荷选定使用的卸扣或受力轴的尺寸,则孔径。
首先,确定板厚,使根部焊缝的强度与设备本体局部稳定性满足要求。
必要时,可延长焊缝长度或增加筋板加以解决。
其次,按选定R值。
再次,采取加补强板的措施增加板孔局部的强度。
通常在吊耳孔处焊接单或双面补强板。
(参见图4)通过以上措施可以比较合理的利用材料。
校核时需按照公式(1)中来替换,即补强圈的半径。
2 吊耳板强度计算2.1 吊耳板材料选择吊耳板选择材料时,宜选择与设备的材质相同或相近为好。
施工现场一般选择Q235、Q345等普通材质的材料,且可焊性较好。
按《钢结构设计规范》对应的钢材板厚取值,只要(1)式成立,吊耳板的强度可满足要求。
2.2 吊耳板焊接与焊缝强度校核吊耳板焊接应有焊接工艺评定。
焊缝应为连续焊,不应有夹渣、气孔、裂纹等缺陷。
主受力焊缝应按JB4730-2005进行
渗透检测,Ⅰ级合格。
焊缝强度按《钢结构设计规范》GB50017-2003选定焊缝的值,并进行校核。
焊缝强度计算时,应具体分析。
a.当吊耳受拉伸作用,焊缝不开坡口或小坡口时,属于角焊缝焊接,焊缝强度按《钢结构设计规范》中式7.1.3-1校核,即:(2)式中:—垂直于焊缝方向的应力,MPa;
N—焊缝受力,N=kP=1.4P, 其中k=1.4为可变载荷分项系数,N;—角焊缝的计算厚度,,为焊角尺寸,mm;—角焊缝的计算长度,取角焊缝实际长度减去,mm;—角焊缝的强度设计增大系数,取;—角焊缝的强度设计值,N/mm2;b.当吊耳受拉伸作用,吊耳板采用双面坡口满焊时,可按对接焊缝校核,即:(3)式中:k—动载系数,k=1.1;L—焊缝长度,mm;δ—吊耳板焊接处母材板厚,mm;其他符号意义同上。
c.当焊缝在三向应力状态下受力时,按材料力学第四强度理论校核,即:(4)式中:—焊缝所受轴向应力,MPa;—焊缝所受弯曲应力,MPa;—焊缝所受剪切应力,MPa;应当指出,虽然焊缝的强度计算满足要求,但由于吊耳板与设备焊接处产生的焊接应力及连接面较小产生的应力集中,使用吊耳时也不可能在设计的理想状态下受力等原因,可能造成设备局部变形或将母材撕裂等不良后果。
因此,应有以下有效安全措施:一是对焊缝进行焊后热处理,以消除焊接应力,特别是当吊耳板的厚度达到规范要求焊后热处理的厚度时,必须进行焊后热处理;二是在吊耳板与设备之间焊接连接筋板,增大了焊缝受力面积,同时也加强了局部稳定性。
焊缝强度计算时,应在不考虑连接筋板的作用下强度和局部稳定性同时满足要求。
3 板式吊耳设计校核示例某设备吊装需设计一载荷P=50t的板式吊耳,材质Q235A。
选择55t卸扣,卸扣轴直径70mm,取板孔r=45mm,R=200mm,,,,焊缝长度L=400mm。
Q235A强度设计值,(GB50017-2003)。
参照图4。
拉曼公式校核吊耳板孔强度板孔强度满足要求。
吊耳在受力最大时为拉伸状态,按吊耳受拉伸校核焊缝强度。
由式(2)按角焊缝校核由式(3)按对接焊缝校核,结果与(2)相差不大。
焊缝强度满足要求。
4 结语我公司在煤矿钢结构井架大型起吊安装施工中通过对单板孔吊耳设计计算的规范化,用CAD软件将其按1:1比例绘出满足吊装负载能力的吊耳施工图,可以在较短时间内顺利完成吊耳设计工作并提交到设备加工厂,达到了事半功倍的效果。
注:文章内所有公式及图表请以PDF形式查看。