第6章 粉末冶金特种烧结技术
演示文稿粉末冶金原理烧结课件
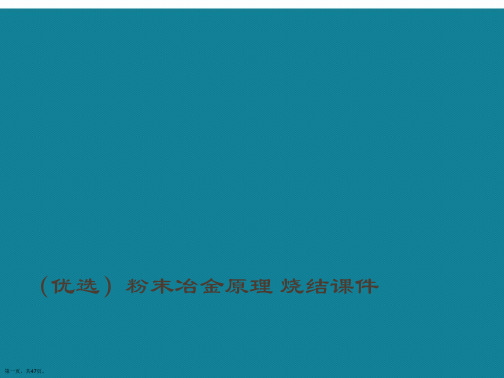
第五页,共47页。
2)有限固溶系 统,如
在合金状态图中有有限固溶区的系 等;
3)完全不互溶系 组元之间既不互相溶解又不形成化 合物或其他中间相的系统,如
等所谓“假合金”。
(3)多元系液相烧结 以超过系统中低熔组分熔点的温度
进行的烧结过程。由于低熔组分同难熔固相之间互相溶解 或形成合金的性质不同,液相可能消失或始终存在于全过 程,故又分为:
√Cabrera:x6/a2 = k/▪t
δ为表面层厚度,采用强烈机械活化可提高有效表面活性的厚度,
从而加快烧结速度。
第三十八页,共47页。
第三十九页,共47页。
烧结铜粉的自扩散系数与 温度的关系
(五)晶界扩散(GB diffusion)
晶界扩散:原子或空位沿晶界进行迁移 晶界是空位的“阱”(Sink),对烧结的贡献体现在: ● 晶界与孔隙连接,易使孔隙消失 ● 晶界扩散激活能仅为体积扩散的一半,D gb》Dv ● 细粉烧结时,在低温起主导作用,并引起体积收缩
第二页,共47页。
2、 烧结也是粉末冶金生产过程的最后一道主要工 序,对最终产品的性能起着决定性作用,因为由烧 结造成的废品是无法通过以后的工序挽救的,烧结 实际上对产品质量起着“把关”的作用。
3、从另一方面看,烧结是高温操作,而且一般要经过 较长的时间,还需要有适当的保护气氛。因此,从经 济角度考虑,烧结工序的消耗是构成产品成本的重要 部分,改进操作与烧结设备,减少物质与能量消耗, 如降低烧结温度,缩短烧结时间等,在经济上的意义
是很大的。
第烧结是粉末或粉末压坯,在适当的温度和气氛 条件下加热所发生的现象或过程。 2、烧结的结果是颗粒之间发生粘结,烧结体的强度
粉末冶金原理-烧结技术详解

铁制品烧结用转化气体标准成分及应用
气体
标准成分
应用举例
吸热型 放热型
40H2,20%CO,1%CH4,Fe-C,Fe-Cu-C等高强度零件;
39%N2
爆炸性极强
8%H2,6%CO,6%CO2,纯铁,Fe-Cu烧结零件;有爆
80%N2
炸性
2020/6/9
School of Materials Science and Engineerin24g
一、烧结前的准备
(一)压坯的检查 ● 目的:去除尺寸、单重不合格或有掉边、掉角、分
层、裂纹等缺陷的压坯,减少烧结废品。
● 方法:抽检、肉眼观察、仪器检测。
2020/6/9
School of Materials Science and Engineerin3g
(二) 装炉(装舟及摆料) 推杆式烧结炉—装舟;网带式烧结炉—-摆料
School of Materials Science and Engineerin26g
2. 无脱碳烧结控制原理
在CH4/H2和CO/CO2气氛中:
1) 图中两线分别为在CO2/CO气氛
2
和CH4/H2气氛中Fe与C反应平衡时
1
气相平衡组成与温度关系
1: Fe + 2CO = (Fe,C) + CO2
③
①
②
④
2020/6/9
School of Materials Science and Engineerin25g
● 要无氧化烧结 ,应在①区;
● >800℃ H2还原区域更大;
● 随温度升高,欲保持CO/CO2 气氛的还原性,需降低CO2%
粉末冶金新技术-烧结

用SPS制取块状纳米晶Fe90Zr7B3软磁的过程是: 先将由非 晶薄带经球磨制成的50~150μm非晶粉末装入WC/Co合金 模具内,并在SPS烧结机上烧结(真空度1×10-2Pa以下、升温 速度0.09~1.7K/s、温度673~873K、压力590MPa), 再把所 得的烧结体在1×10-2Pa真空下、以3 7K/s速度加热到923K、 保温后而制成。材料显示较好的磁性能:最大磁导率29800、 100Hz下的动态磁导率3430, 矫顽力12A/m。
3
双频微波烧结炉 生产用大型微波烧结炉 已烧结成多种材料:如陶瓷和铁氧体等材料。另 外,在日本又开发出相似的毫米波烧结技术,并成功 地在2023K下保温1h烧结成全致密的AlN材料。
4
2.爆炸压制技术 爆炸压制又称冲击波压制是一种有前途的工艺
方法,它在粉末冶金中发挥了很重要的作用, 爆炸压 制时,只是在颗粒的表面产生瞬时的高温,作用时间 短,升温和降温速度极快。适当控制爆炸参数,使得 压制的材料密度可以达到理论密度的90%以上,甚至 达到99%。
3)快速脉冲电流的加入, 无论是粉末内的放电部位还是焦耳 发热部位, 都会快速移动, 使粉末的烧结能够均匀化。
11
与传统的粉末冶金工艺相比,SPS工艺的特点是:
• 粉末原料广泛:各种金属、非金届、合金粉末,特别是 活性大的各种粒度粉末都可以用作SPS 烧结原科。
• 成形压力低:SPS烛结时经充分微放电处理,烧结粉末表 面处于向度活性化状态.为此,其成形压力只需要冷压烧 结的l/10~1/20。
17
SPS制备软磁材料 通常用急冷或喷射方法可得到FeMe(Nb、Zr、Hf)B的非 晶合金,在稍高于晶化温度处理后, 可得到晶粒数10nm,具有 体心立方结构,高Bs 、磁损小的纳米晶材料。但非晶合金目 前只能是带材或粉末, 制作成品还需要将带材重叠和用树脂固 结, 这使得成品的密度和Bs均变低。近年, 日本采用SPS工艺研 究FeMeB块材的成形条件及磁性能。
粉末冶金的烧结技术

粉末冶金的烧结技术粉末冶金是一种通过将金属或非金属粉末在一定条件下,加工成具有一定形状和尺寸的零部件的方法。
烧结技术是粉末冶金中的关键步骤之一,它将粉末颗粒通过加热并施加压力使其质点之间结合得更加牢固,形成一体化的零部件。
本文将对粉末冶金的烧结技术进行深入探讨。
一、烧结技术的基本原理和过程烧结技术是将粉末颗粒通过加热至其熔点以下,但高于材料的再结晶温度,同时施加压力,使粉末颗粒发生结合,形成一体化的零部件。
其基本原理是利用了粉末颗粒与粉末颗粒之间的扩散作用和表面张力降低效应。
烧结过程中,颗粒间的间隙先得到迅速消除,然后颗粒之间产生再结晶,通过扩散使粒间结合更为牢固。
整个烧结过程可以分为初期活化期、再结晶期和液相期三个阶段。
初期活化期是指在烧结过程开始的阶段,颗粒发生活化并形成结合,此时烧结坯体变得更为致密。
再结晶期是指烧结坯体中增强再结晶的发生。
液相期是指在达到受结合的颗粒之间的最小距离后,材料产生液相,并通过液相扩散加快了颗粒间的结合。
在这个过程中,烧结坯体结构的致密度和强度会显著提高。
二、烧结技术的主要参数在进行粉末冶金的烧结过程中,有许多参数需要注意和控制,如温度、压力、时间和气氛等。
这些参数会对烧结过程和烧结产品的质量产生重要影响。
1. 温度:温度是烧结过程的关键参数之一。
合适的温度能够使粉末颗粒迅速熔结,并形成均匀的结构。
过高或过低的温度都会影响烧结效果和质量。
2. 压力:在烧结过程中,施加的压力可以使粉末颗粒更加紧密地结合在一起。
增加压力可以提高烧结物品的致密度和强度。
3. 时间:烧结时间是烧结过程中的一个重要参数。
适当的烧结时间可以使粉末颗粒充分结合并形成致密的结构。
时间过长或过短都会影响产品的质量。
4. 气氛:烧结过程中的气氛对烧结质量和产品性能有很大影响。
不同的气氛可以对不同材料产生不同的效果。
常用的烧结气氛有氢气、氮气、氧气和真空等。
三、烧结技术的应用和优点烧结技术在现代工业中有着广泛的应用,尤其是在金属材料和陶瓷材料的制备过程中。
第6章粉末冶金特种烧结技术
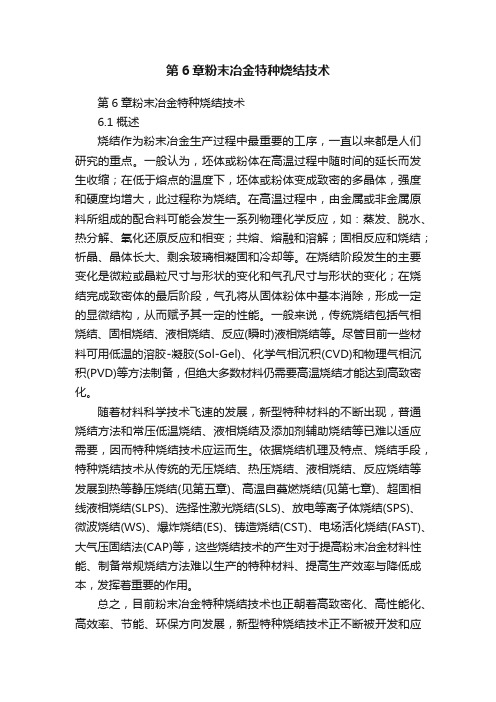
第6章粉末冶金特种烧结技术第6章粉末冶金特种烧结技术6.1 概述烧结作为粉末冶金生产过程中最重要的工序,一直以来都是人们研究的重点。
一般认为,坯体或粉体在高温过程中随时间的延长而发生收缩;在低于熔点的温度下,坯体或粉体变成致密的多晶体,强度和硬度均增大,此过程称为烧结。
在高温过程中,由金属或非金属原料所组成的配合料可能会发生一系列物理化学反应,如:蒸发、脱水、热分解、氧化还原反应和相变;共熔、熔融和溶解;固相反应和烧结;析晶、晶体长大、剩余玻璃相凝固和冷却等。
在烧结阶段发生的主要变化是微粒或晶粒尺寸与形状的变化和气孔尺寸与形状的变化;在烧结完成致密体的最后阶段,气孔将从固体粉体中基本消除,形成一定的显微结构,从而赋予其一定的性能。
一般来说,传统烧结包括气相烧结、固相烧结、液相烧结、反应(瞬时)液相烧结等。
尽管目前一些材料可用低温的溶胶-凝胶(Sol-Gel)、化学气相沉积(CVD)和物理气相沉积(PVD)等方法制备,但绝大多数材料仍需要高温烧结才能达到高致密化。
随着材料科学技术飞速的发展,新型特种材料的不断出现,普通烧结方法和常压低温烧结、液相烧结及添加剂辅助烧结等已难以适应需要,因而特种烧结技术应运而生。
依据烧结机理及特点、烧结手段,特种烧结技术从传统的无压烧结、热压烧结、液相烧结、反应烧结等发展到热等静压烧结(见第五章)、高温自蔓燃烧结(见第七章)、超固相线液相烧结(SLPS)、选择性激光烧结(SLS)、放电等离子体烧结(SPS)、微波烧结(WS)、爆炸烧结(ES)、铸造烧结(CST)、电场活化烧结(FAST)、大气压固结法(CAP)等,这些烧结技术的产生对于提高粉末冶金材料性能、制备常规烧结方法难以生产的特种材料、提高生产效率与降低成本,发挥着重要的作用。
总之,目前粉末冶金特种烧结技术也正朝着高致密化、高性能化、高效率、节能、环保方向发展,新型特种烧结技术正不断被开发和应用。
本章将分别介绍目前国际上流行的特种烧结技术的发展概况、原理、工艺过程及其应用情况。
粉末冶金原理 烧结课件ppt
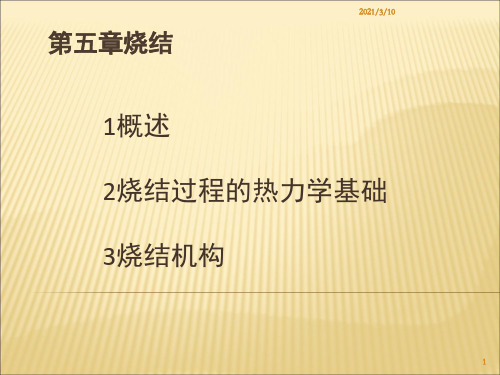
(2)烧结体内孔隙的总体和总表面积减小;
(3)粉末颗粒内晶格畸变的消除。
12
2021/3/10
对烧结过程,特别是早期阶段,作用较大的主要是表 面能。
烧结后颗粒的界面转变为晶界面,由于晶界能更低,故 总的能量仍是降低的。随着烧结的进行,烧结颈处的晶 界可以向两边的颗粒内移动,而且颗粒内原来的晶界也 可能通过再结晶或聚晶长大发生移动并减少。因此晶界 能进一步降低就成为烧结颈形成与长大后烧结继续进行 的主要动力
第五章烧结
2021/3/10
1概述 2烧结过程的热力学基础 3烧结机构
1
1 概述
2021/3/10
一、烧结在粉末冶金生产过程中的重要性
1、烧结是粉末冶金生产过程中最基本的工序之 一。粉末冶金从根本上说,是由粉末成形和粉 末毛坯热处理(烧结)这两道基本工序组成的, 在特殊情况下(如粉末松装烧结),成形工序 并不需要,但是烧结工序,或相当于烧结的高 温工序(如热压或热锻)却是不可缺少的。
1)无限固溶系 如
在合金状态图中有无限固溶区的系统,
5
2)有限固溶系 统,如
2021/3/10
在合金状态图中有有限固溶区的系 等;
3)完全不互溶系 组元之间既不互相溶解又不形成化 合物或其他中间相的系统,如 等所谓“假合金”。
(3)多元系液相烧结 以超过系统中低熔组分熔点的 温度进行的烧结过程。由于低熔组分同难熔固相之间互 相溶解或形成合金的性质不同,液相可能消失或始终存 在于全过程,故又分为:
10
2021/3/10
(a)
(b) (c、d)
图 5-1 球形颗粒的烧结模型 烧结前颗粒的原始接触; 烧结早期的烧结颈长大; 烧结后期的孔隙球化
11
粉末冶金材料的烧结
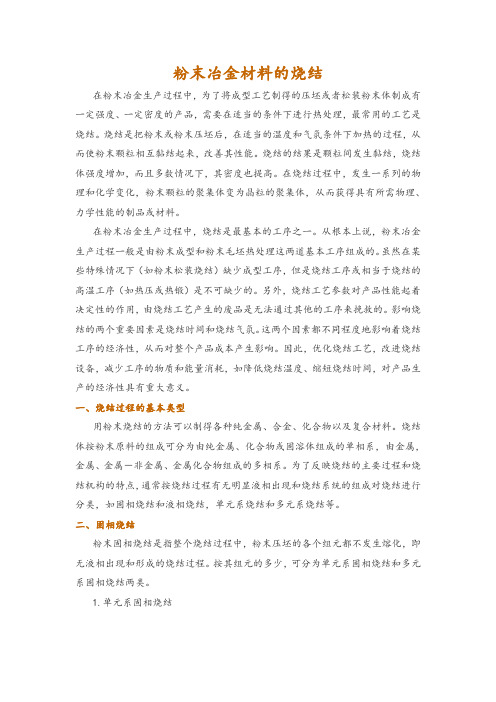
粉末冶金材料的烧结在粉末冶金生产过程中,为了将成型工艺制得的压坯或者松装粉末体制成有一定强度、一定密度的产品,需要在适当的条件下进行热处理,最常用的工艺是烧结。
烧结是把粉末或粉末压坯后,在适当的温度和气氛条件下加热的过程,从而使粉末颗粒相互黏结起来,改善其性能。
烧结的结果是颗粒间发生黏结,烧结体强度增加,而且多数情况下,其密度也提高。
在烧结过程中,发生一系列的物理和化学变化,粉末颗粒的聚集体变为晶粒的聚集体,从而获得具有所需物理、力学性能的制品或材料。
在粉末冶金生产过程中,烧结是最基本的工序之一。
从根本上说,粉末冶金生产过程一般是由粉末成型和粉末毛坯热处理这两道基本工序组成的。
虽然在某些特殊情况下(如粉末松装烧结)缺少成型工序,但是烧结工序或相当于烧结的高温工序(如热压或热锻)是不可缺少的。
另外,烧结工艺参数对产品性能起着决定性的作用,由烧结工艺产生的废品是无法通过其他的工序来挽救的。
影响烧结的两个重要因素是烧结时间和烧结气氛。
这两个因素都不同程度地影响着烧结工序的经济性,从而对整个产品成本产生影响。
因此,优化烧结工艺,改进烧结设备,减少工序的物质和能量消耗,如降低烧结温度、缩短烧结时间,对产品生产的经济性具有重大意义。
一、烧结过程的基本类型用粉末烧结的方法可以制得各种纯金属、合金、化合物以及复合材料。
烧结体按粉末原料的组成可分为由纯金属、化合物或固溶体组成的单相系,由金属,金属、金属-非金属、金属化合物组成的多相系。
为了反映烧结的主要过程和烧结机构的特点,通常按烧结过程有无明显液相出现和烧结系统的组成对烧结进行分类,如固相烧结和液相烧结,单元系烧结和多元系烧结等。
二、固相烧结粉末固相烧结是指整个烧结过程中,粉末压坯的各个组元都不发生熔化,即无液相出现和形成的烧结过程。
按其组元的多少,可分为单元系固相烧结和多元系固相烧结两类。
1.单元系固相烧结单元系固相烧结,即单一粉末成分的烧结。
例如各种纯金属的烧结、预合金化粉末的烧结、固定成分的化合物粉末的烧结等,均为单元系固相烧结。
粉末冶金的烧结技术

粉末冶金的烧结技术粉末冶金是一种重要的金属材料加工技术,其烧结技术是其中的关键环节之一。
烧结是指将金属粉末在高温和压力下进行加工,使其粒子间发生结合,形成致密坚固的材料。
烧结技术主要包括前期制备、烧结过程和后期处理三个阶段。
前期制备主要是选用合适的原料并进行预处理;烧结过程是指将粉末加热至一定温度下,使其颗粒形成熔连和扩散,从而实现颗粒间的结合;后期处理则是通过热处理和机械加工等方式对烧结材料进行改性和加工。
在烧结过程中,主要涉及到的问题包括热传导、粒子熔融和扩散等。
热传导是指热能在颗粒间的传递,它直接影响到烧结过程中的温度分布和物理性质的演化。
热传导主要受到粉末细度、烧结温度和热处理时间等因素的影响。
粒子熔融是指粉末颗粒在高温下发生熔化并与周围颗粒结合。
熔融过程中,粒子表面的氧化物会被还原,同时金属原子也会扩散到颗粒间,从而实现结合。
扩散是指金属原子在颗粒间的迁移和交换,它是烧结过程中颗粒结合的重要机制。
在烧结技术中,常用的烧结方法包括热压烧结、等静压烧结和电子束烧结等。
热压烧结是指将粉末加热至高温后进行压实,它可以在较短时间内获得高致密度的烧结材料。
等静压烧结是指在恒定温度下进行压实,它可以获得均匀的压力分布和高度致密的材料。
电子束烧结则是利用电子束的热效应进行烧结,它具有快速和局部加热的优势。
烧结技术在粉末冶金中具有广泛的应用。
一方面,它可以制备各种金属材料和合金,包括高温合金、硬质合金、不锈钢、铜陶瓷等。
另一方面,它还可以制备复杂形状和微细结构的材料,如蜂窝结构、多孔材料和纳米颗粒等。
此外,烧结技术还可以用于制备金属陶瓷复合材料、金属纤维和金刚石等高性能材料。
总之,粉末冶金的烧结技术是一项重要的金属材料加工技术,它通过热传导、粒子熔融和扩散等机制实现了金属粉末的结合,从而获得高致密度和高强度的材料。
烧结技术在金属材料研究和工业生产中具有广泛的应用前景,将为人们提供更多种类和性能的金属材料。
- 1、下载文档前请自行甄别文档内容的完整性,平台不提供额外的编辑、内容补充、找答案等附加服务。
- 2、"仅部分预览"的文档,不可在线预览部分如存在完整性等问题,可反馈申请退款(可完整预览的文档不适用该条件!)。
- 3、如文档侵犯您的权益,请联系客服反馈,我们会尽快为您处理(人工客服工作时间:9:00-18:30)。
第6章粉末冶金特种烧结技术6.1 概述烧结作为粉末冶金生产过程中最重要的工序,一直以来都是人们研究的重点。
一般认为,坯体或粉体在高温过程中随时间的延长而发生收缩;在低于熔点的温度下,坯体或粉体变成致密的多晶体,强度和硬度均增大,此过程称为烧结。
在高温过程中,由金属或非金属原料所组成的配合料可能会发生一系列物理化学反应,如:蒸发、脱水、热分解、氧化还原反应和相变;共熔、熔融和溶解;固相反应和烧结;析晶、晶体长大、剩余玻璃相凝固和冷却等。
在烧结阶段发生的主要变化是微粒或晶粒尺寸与形状的变化和气孔尺寸与形状的变化;在烧结完成致密体的最后阶段,气孔将从固体粉体中基本消除,形成一定的显微结构,从而赋予其一定的性能。
一般来说,传统烧结包括气相烧结、固相烧结、液相烧结、反应(瞬时)液相烧结等。
尽管目前一些材料可用低温的溶胶-凝胶(Sol-Gel)、化学气相沉积(CVD)和物理气相沉积(PVD)等方法制备,但绝大多数材料仍需要高温烧结才能达到高致密化。
随着材料科学技术飞速的发展,新型特种材料的不断出现,普通烧结方法和常压低温烧结、液相烧结及添加剂辅助烧结等已难以适应需要,因而特种烧结技术应运而生。
依据烧结机理及特点、烧结手段,特种烧结技术从传统的无压烧结、热压烧结、液相烧结、反应烧结等发展到热等静压烧结(见第五章)、高温自蔓燃烧结(见第七章)、超固相线液相烧结(SLPS)、选择性激光烧结(SLS)、放电等离子体烧结(SPS)、微波烧结(WS)、爆炸烧结(ES)、铸造烧结(CST)、电场活化烧结(FAST)、大气压固结法(CAP)等,这些烧结技术的产生对于提高粉末冶金材料性能、制备常规烧结方法难以生产的特种材料、提高生产效率与降低成本,发挥着重要的作用。
总之,目前粉末冶金特种烧结技术也正朝着高致密化、高性能化、高效率、节能、环保方向发展,新型特种烧结技术正不断被开发和应用。
本章将分别介绍目前国际上流行的特种烧结技术的发展概况、原理、工艺过程及其应用情况。
6.2 超固相线液相烧结(SLPS,Supersolidus Liquid Phase Sintering) 6.2.1 SLPS的发展概况超固相烧结(SLPS)由传统液相烧结变化而来,该工艺将粉末坯加热到液相线和固相线之间的温度进行烧结。
SLPS可用于粒度较粗的预合金粉末。
超固相线液相烧结属于液相烧结的范畴,但它又不同于传统混合粉末的液相烧结。
在粉末颗粒相互接触的地方以及晶界处形成液相层。
晶界处的液相层软化粉末颗粒,使粉末在颗粒间毛细管力的作用下致密。
但是,液相层也会降低结构刚度,因为颗粒在重力作用下会下落。
因此,SLPS 的局限就在于致密的必需条件经常会导致变形,液相体积分数高,虽然可以加速致密化过程,但是也会降低尺寸精度。
Westerman于1962年最早描述了镍基高温合金的超固相线液相烧结,他认为SLPS处理后镍基高温合金的力学性能更主要地取决于最高烧结温度,其次才是残余空隙。
70年代初一些学者研究了Fe-0.9%C和Ni-30%Cu的SPLS。
这个阶段仅仅是停留在初步的实验研究水平上,研究的体系十分有限,并且缺乏对工艺和机理的系统研究。
Cambal将近球形的Fe-0.95mass.%C预合金松粉装入氧化铝模中,在1698K 和氢气保护下进行SLPS,Fe-C相图给出了此时的液相量为38%左右,结果在15~60s的时间内便获得了86~91%的相对密度,经过冷轧可将相对密度提高到95%。
随后Lund对Fe- 0.9%C和50%Cu-50%Ni预合金粉末进行了松装SLPS研究,Fe-0.9%C的最初松装密度为3.8~4.0g/cm3,经过1698K、10min的真空烧结,相对密度达到了99%左右,可见真空SLPS 致密化能力优于气体保护烧结。
Cu-Ni合金在1533K烧结10min,产生16~20%的液相量,即可获得93%的相对密度,而在同样的液相量下,Fe-0.9%C只能达到60~70%的相对密度,这说明不同材料体系的最佳致密化所需的液相量不同。
进入上世纪80年代后,关于SLPS的研究十分活跃,先后有许多关于镍基高温合金、不锈钢、工具钢、青铜、陶瓷等方面的SLPS研究。
人们对影响SLPS的各种工艺条件(粉末特性、最高烧结温度、烧结时间、保护气氛、冷却速度、后续处理)作了全面的研究。
German在总结前人工作的基础上,就SLPS的烧结机理、显微组织长大、致密化理论等问题作了全面系统的总结[1],他借助粘性流动理论提出了SLPS的重排致密化机理模型。
目前,SLPS的工业应用已经开始,如制造工具钢和其它一些高合金成分体系的零件。
6.2.2 SLPS的原理及特点SLPS是从烧结机理角度来优化烧结的一种特种烧结技术,它将完全预合金化的粉末加热到合金相图的固相线与液相线之间的某一温度,使每个预合金粉末的晶粒内、晶界处及颗粒表面形成液相,在粉末颗粒间的接触点与颗粒内晶界处形成的液相膜,借助半固态粉末颗粒间的毛细管力使烧结体迅速达到致密化[2,3,4],因此SLPS也属于液相烧结范畴。
在烧结过程中,液相与固相的体积分数基本不变(液相量为30%左右较佳),烧结温度范围比较窄(大多数合金为30K左右),一旦液相形成则迅速达到致密化。
尽管SLPS属于液相烧结范畴,但它又不同于传统混合粉末的液相烧结,二者主要区别在于:SLPS所对应的原料是完全预合金粉末,而普通液相烧结所对应的原料是混合物。
SLPS烧结温度选择在合金相图的固相线与液相线之间,液相在每个粉末颗粒内部形成,因此液相分布相当均匀。
液相的形成,使每个颗粒都经历分离和重排过程。
一旦液相形成,烧结的致密化速率相当快。
由于预合金粉末的生产方法、成分和结构特征不同,SLPS 法烧结时液膜形成位置有所不同(见表6-1 )。
因此,其SLPS致密化的模型也有所不同。
国内有学者[5]采用普通预合金粉的致密化模型[6],给出了WC-Co复合粉空心球颗粒的SLPS的致密化模型如图6-1所示。
SLPS的步骤依次如下:液相形成、WC晶粒滑动(一种蠕变过程)、重排、由溶解—析出所导致的晶粒粗化与孔隙消除。
表6-1 两种预合金粉之间的区别粉末生产方法成分特征结构特征烧结时液膜形成位置A 雾化法/粉碎法非平衡实心颗粒1颗粒间接触处;2晶界;3晶粒内部B SLPS 平衡空心二次颗粒相界(即WC晶粒表面)图6-1 复合粉空心球颗粒内的SLPS模型[5]SLPS不仅具备常规液相烧结的优点,还可以使颗粒尺寸较大的预合金粉末进行快速烧结致密化。
German[7]认为SLPS的特点为:(1)合金的组织结构与性能对烧结温度、工艺参数以及合金成分比较敏感;(2)因颗粒间固态烧结阻碍液相出现时的颗粒重排,液相出现前的固相烧结对合金的最终致密化有不利影响;(3)一旦液相形成,合金的致密化速率相当大,这虽然对获得高的烧结密度有利,但同时也给合金尺寸与微观结构的控制带来了不利影响。
在SLPS时,只有在实际液相数量与消除烧结坯中孔隙所需的液相数量相当接近时,才能获得最佳的合金组织结构与性能。
要满足这种条件,必须严格控制合金的烧结温度与合金成分。
根据SLPS原理,压力烧结有利于在较少液相数量的条件下获得全致密,有利于控制合金晶粒长大。
6.2.3 SLPS中的致密化与变形机理[6]在SLPS的早期阶段,即固相线温度附近,液相首先在晶界与树枝晶处形成,因为这些地方存在着成分偏聚使熔化温度降低。
随着温度的提高,液相量不断增多并沿晶界润湿铺展开来。
随着时间的延长,颗粒内部的液相会溢出颗粒表面,液相的成分将达到平衡。
从微观上看,SLPS 基本过程大致为:液相形成、晶粒重排、接触点平直化、溶解-析出、晶粒形状球化。
在这些过程中残余孔隙被消除。
一般认为,液相形成后晶粒发生重排的阶段是致密化的主要阶段。
当液相量足够时,晶粒之间大约1nm 厚的液相膜在毛细管力的作用下使烧结块内部失去了稳固的结构,从而发生类似粘性流动的晶粒重排,使致密化速率迅速提高。
German 等人[2,6]对SLPS 过程中的致密化与变形机理进行了研究并建立了模型。
SLPS 过程中致密化类似于液相烧结,液相在粉末颗粒间的接触点与颗粒内部的晶界处形成。
晶界的液相膜使颗粒软化,从而使其在毛细管力作用下致密化。
同时,液相膜也降低了结构的刚性使其在重力作用下发生流动。
所以,液相的体积分数越高,致密化速度也就越快,但尺寸精度会降低。
因为SLPS 过程的致密化与变形依赖于液相变形的微观结构变化,为此建立参数通过液相微观结构特征来预知SLPS 过程中的结构刚性,致密化与变形可以依据此参数来进行预测。
图6-2表示SLPS 过程中三个相互接触的粉末颗粒,在粉末颗粒间形成的液相的聚积迫使产生毛细管力,毛细管力通过对组织施加静水压力来驱动结构致密化,而颗粒内部晶界的液相主要降低颗粒的结构刚性。
最初的致密化产生在靠近颈部的局域变形小范围内,它使颈部长大且平直化,但这必须在晶界处被液相膜充分软化后才可能发生。
图 6-2 致密早期阶段的多孔模型[6]。
所以,致密化过程中,烧结体由呈半固态的颗粒和很多孔隙组成。
每个颗粒受到相邻颗粒接触点毛细管力的作用。
当平均毛细管力大于烧结体强度时,毛细管力产生的网状收缩力就会导致烧结体各向同性收缩。
可以用式(6-1)来估算毛细管压力:LV cap 05.2cos ()L D L γθδ∆()= (6-1)D 为颗粒直径,LV γ为液-气表面能,θ为润湿角,0L L ∆为烧结体收缩率。
典型的cap δ初值为几兆帕(γLV 为2 J/m 2,颗粒尺寸为100μm ,毛细管力为10MPa 到1MPa ,线性收缩率为0.01到0.1)。
为得出重力对形变影响的概念,建立烧结体模型,如图6-3所示。
重力作用使各组分在轴向产生偏离。
组分质量的改变产生压力,从而导致形变。
任何一点的张力都依赖于其上面质量的累积,可由hρg 表示,其中h 为从顶部到该点的高度,g 为重力加速度,ρ为密度。
例如一个高度为0.01m 、密度为10g/cm 3的样品底部的张力约为1kPa ,这在数量上比毛细管张力对致密化影响小很多。
从模型可以看出该组织是由固态晶粒以及晶界处的液相(晶内的少量液相)组成。
孔洞和毛细管力都可以忽略。
但是,成分的重量会产生一个轴向力,并且随着高度的增加而增加,且可能导致形状扭曲。
在SLPS 过程中,粉末颗粒呈半固态,每个颗粒都能各自在重力作用下产生变形。
而烧结体的形变主要源于粉末颗粒的整体变形。
由于在致密化过程中,毛细管张力远大于重力,所以重力作用可以忽略不计。
致密化后,烧结体由颗粒边界处充填液相的固态颗粒与少量孔隙组成。
一旦孔隙被液相充填,毛细管力就接近于零,而重力作用是竖直向下的,当这种固-液结构相对于重力作用很小时,烧结体就产生流动。